Open Access
ARTICLE
Up-Sampled Cross-Correlation Based Object Tracking & Vibration Measurement in Agriculture Tractor System
1 Department of Mechanical Engineering, Sathyabama Institute of Science and Technology, Chennai, 600119, India
2 Department of Mechanical Engineering, CEGC, Anna University, Chennai, 600025, India
* Corresponding Author: R. Ganesan. Email:
Intelligent Automation & Soft Computing 2023, 36(1), 667-681. https://doi.org/10.32604/iasc.2023.031932
Received 30 April 2022; Accepted 01 July 2022; Issue published 29 September 2022
Abstract
This research introduces a challenge in integrating and cleaning the data, which is a crucial task in object matching. While the object is detected and then measured, the vibration at different light intensities may influence the durability and reliability of mechanical systems or structures and cause problems such as damage, abnormal stopping, and disaster. Recent research failed to improve the accuracy rate and the computation time in tracking an object and in the vibration measurement. To solve all these problems, this proposed research simplifies the scaling factor determination by assigning a known real-world dimension to a predetermined portion of the image. A novel white color sticker of the known dimensions marked with a color dot is pasted on the surface of an object for the best result in the template matching using the Improved Up-Sampled Cross-Correlation (UCC) algorithm. The vibration measurement is calculated using the Finite-Difference Algorithm (FDA), a machine vision system fitted with a macro lens sensor that is capable of capturing the image at a closer range, which does not affect the quality of displacement measurement from the video frames. The field test was conducted on the TAFE (Tractors and Farm Equipment Limited) tractor parts, and the percentage of error was recorded between 30% and 50% at very low vibration values close to zero, whereas it was recorded between 5% and 10% error in most high-accelerations, the essential range for vibration analysis. Finally, the suggested system is more suitable for measuring the vibration of stationary machinery having low frequency ranges. The use of a macro lens enables to capture of image frames at very close-ups. A 30% to 50% error percentage has been reported when the vibration amplitude is very small. Therefore, this study is not suitable for Nano vibration analysis.Keywords
Cite This Article
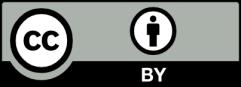
This work is licensed under a Creative Commons Attribution 4.0 International License , which permits unrestricted use, distribution, and reproduction in any medium, provided the original work is properly cited.