Open Access
ARTICLE
Hybrid Multi-Object Optimization Method for Tapping Center Machines
1 Department of Electrical Engineering, National Kaohsiung University of Science and Technology, Kaohsiung, 807, Taiwan
2 Department of Intelligent Robotics, National Pingtung University, Pingtung, 900, Taiwan
3 Graduate Institute of Precision Manufacturing, National Chin-Yi University of Technology, Taichung, 411, Taiwan
* Corresponding Author: Po-Yuan Yang. Email:
Intelligent Automation & Soft Computing 2023, 36(1), 23-38. https://doi.org/10.32604/iasc.2023.031609
Received 22 April 2022; Accepted 12 July 2022; Issue published 29 September 2022
Abstract
This paper proposes a hybrid multi-object optimization method integrating a uniform design, an adaptive network-based fuzzy inference system (ANFIS), and a multi-objective particle swarm optimizer (MOPSO) to optimize the rigid tapping parameters and minimize the synchronization errors and cycle times of computer numerical control (CNC) machines. First, rigid tapping parameters and uniform (including 41-level and 19-level) layouts were adopted to collect representative data for modeling. Next, ANFIS was used to build the model for the collected 41-level and 19-level uniform layout experiment data. In tapping center machines, the synchronization errors and cycle times are important considerations, so these two objects were used to build the ANFIS models. Then, a MOPSO algorithm was used to search for the optimal parameter combinations for the two ANFIS models simultaneously. The experimental results showed that the proposed method obtains suitable parameter values and optimal parameter combinations compared with the non-systematic method. Additionally, the optimal parameter combination was used to optimize existing CNC tools during the commissioning process. Adjusting the proportional and integral gains of the spindle could improve resistance to deformation during rigid tapping. The position gain and pre-feedback coefficient can reduce the synchronization errors significantly, and the acceleration and deceleration times of the spindle affect both the machining time and synchronization errors. The proposed method can quickly and accurately minimize synchronization errors from 107 to 19.5 pulses as well as the processing time from 3,600 to 3,248 ms; it can also shorten the machining time significantly and reduce simultaneous errors to improve tapping yield, thereby helping factories achieve carbon reduction.Keywords
Cite This Article
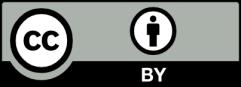
This work is licensed under a Creative Commons Attribution 4.0 International License , which permits unrestricted use, distribution, and reproduction in any medium, provided the original work is properly cited.