Open Access
ARTICLE
Influence of Microwave Power and Heating Time on the Drying Kinetics and Mechanical Properties of Eucalyptus gomphocephala Wood
1 Laboratoire d’Energétique et des Transferts Thermiques et Massiques, Physics Department, Faculty of Science of Tunis, University of Tunis El Manar, Campus Universitaire, El Manar, 2092, Tunisia
2 Physics Department, Faculty of Science, Al-Baha University, Alaqiq, 65779, Saudi Arabia
3 Laboratoire de Gestion et de Valorisation des Ressources Forestières, INRGREF, University of Carthage, City of Hédi EL Karray El Menzah IV, Ariana, 2080, Tunisia
* Corresponding Author: Sahbi Ouertani. Email:
(This article belongs to the Special Issue: Multiscale Heat and Mass Transfer and Energy Conversion)
Frontiers in Heat and Mass Transfer 2025, 23(1), 345-360. https://doi.org/10.32604/fhmt.2024.057387
Received 16 August 2024; Accepted 25 November 2024; Issue published 26 February 2025
Abstract
The aim of this paper was to characterize through experiment the moisture and temperature kinetic behavior of Eucalyptus gomphocephala wood samples using microwave heating (MWH) in two scenarios: intermittently and continuously. The mechanical properties and surface appearance of the heated samples were also investigated. Continuous and intermittent microwave drying kinetic experiments were conducted at a frequency of 2.45 GHz using a microwave laboratory oven at 300, 500, and 1000 watts. Drying rate curves indicated three distinct phases of MWH. Increasing the microwave power with a shorter drying time led to rapid increases in internal temperature and water evaporation rates of the heated samples. Mechanical results indicated that samples heated under continuous MW (Microwave) power at 300 watts had a modulus of rupture (MOR) and modulus of elasticity (MOE) in three static bending tests higher than 29% and 36%, respectively, than samples heated at 1000 watts. Intermittent microwave heating (IMWH) of samples at 300 and 1000 watts produced the highest MOR and MOE values of 31% and 51%, respectively, unlike those heated under continuous microwave heating (CMWH). External qualitative observation showed that samples heated at high microwave power had severe surface checks. These defects were missing when using IMWH. An analysis of variance (ANOVA) showed that mechanical properties were linked to both microwave power level and the heating scenario, except for MOR in axial compression under CMWH.Keywords
Nomenclature
T | Temperature (°C) |
RH | Relative humidity (%) |
P | Microwave power (W) |
MC | Moisture content (%) |
XGreen | mass of initial sample (kg) |
Xwater | Water mass (kg) |
Xd | Oven-dried mass of wood sample (kg) |
DR | Drying rate (kg water/kg DM min) |
MOE | Modulus of elasticity (MPa) |
MOR | Modulus of rupture (MPa) |
MW | Microwave |
MWH | Microwave heating |
e.g., | |
Time | |
Difference between two-time scales | |
Dry | |
Dry matter | |
d.f. | Degree of freedom |
F | F-test ANOVA One way |
Ns | Not significant at p > 0.05 |
* | Significant at p < 0.05 |
** | Significant at p < 0.01 |
The operation of drying is an energy-intensive process on an industrial scale which transforms wood into a value added product that can be used for furniture, decoration, building, thermal insulation, and composite material [1–3]. Drying reduces the moisture content of damp wood, improves its mechanical performance, provides dimensional stability from shrinkage and swelling, and protects it from biological attacks [4–6]. There are currently numerous drying processes, some of which include conventional heat and vent kilns. In these methods, heat penetrates the surface and reaches the product center by means of thermal conductivity [7]. This conventional drying process is slow and energy costly, however, due to low thermal conductivity and resistance to moisture diffusion from the core to the surface of the wood [8]. By using the process of microwave heating (MWH), on the other hand, the MW energy is dissipated instantaneously inside the moist product, thus reducing both drying time and energy consumption by accelerating internal heat and mass transfers [9–13]. In MWH, water molecule dipoles oscillate with respect to the alternative electric field at a frequency of 2.45 GHz. The faster reorientation of the polar water molecules produces friction among the water molecules and generates internal heat [14]. This internally generated heat depends on the microwave power level, frequency, sample size, moisture content, and the dielectric loss factor of the product [15].
In the literature, there have been numerous combinations of MWH with convective air heating and contact vacuum heating investigated to optimize temperature, processing time, and cost and improve the mechanical performance of dried wood samples [16–18]. The MWH process was considered more efficient than conventional heating in terms of operating times, uniform temperature distribution within the product heated, and easily integrated technology. In particular, IMWH consists of a discontinuous microwave energy supply during heating. Several reports have indicated that IMWH homogenizes the moisture content of the wood specimens during the cooling periods, enabling a more gradual release of moisture. The cooling period then reduces the internal vapor pressure peak inside the sample, thus avoiding wood damage and improving the mechanical performance of the end product [19–21]. The intermittency relaxes the stresses of mechanical drying induced within the samples being dried [22]. Hansson and Antti [23] showed that controlled MWH reduces drying time and improves wood resistance. Adjusting to a low microwave power may also provide drying benefits without reducing the wood strength property of Eucalyptus macrorhyncha [24]. Antti et al. [25] demonstrated that controlling microwave power to heat moist Scots pine (Pinussylvestris L.) wood pellets improved their strength over using an oven-drying process. Many studies recommending the use of low microwave power to heat wood have shown that the mechanical properties of the dried samples were not affected compared to conventional drying [11,26,27]. Mascarenhas et al. [28] reported that microwave treatment is efficient for heating Eucalyptus globulus heartwood due to his higher basic density, lower permeability, and the difficulties that this species presents when drying with conventional methods.
In this work, we experimentally investigated MWH of Eucalyptus gomphocephala wood boards freshly sawed from northeast Tunisia using two scenarios: CMWH and IMWH. Optimizing the MW heating parameters such as microwave power, internal temperature, treatment time, and intermittent energy supply was necessary to improve the aesthetic and mechanical quality of the treated samples [9]. However, the influence of IMWH on the drying kinetics and mechanical performance of Eucalyptus gomphocephala wood samples still remains unclear and no data is available in the literature. A better understanding of the temperature profile, the quantity of water released over time, and the MW power level could lead to further optimization of the processing parameters of MW drying of gomphocephala wood. This optimization could improve the quality of dried gomphocephala samples in terms of external appearance as well as mechanical properties for numerous specific applications such as drying, liquid impregnation, and phytosanitary treatment both within Tunisia and internationally. Eucalyptus wood is used as a source of energy and a raw material in the wood industry. This species covers 20 million hectares in more than 90 countries worldwide [29]. Numerous works have demonstrated that eucalyptus wood is extra sensitive during the final stages of drying and may undergo collapse, internal checks, and cracks [30,31]. For this reason, we hope that this study will contribute to a more thorough understanding of the drying behavior of this type of wood by investigating experimentally the potential use of intermittent microwave energy at 2.45 GHz frequency to dry Eucalyptus gomphocephala wood samples, determining the drying kinetics, mechanical axial and flexural properties at 12% moisture content (MC), and examining the external shape of heated samples. An ANOVA test presented the efficiency of MWH on the mechanical properties of treated samples compared to convective drying at 60°C.
2.1 Wood Selection and Sampling
The wood species Eucalyptus gomphocephala was investigated in this study. One freshly cut 50-year-old tree was collected from the Choucha arboretumin the Nabeul governorate of the Hawariya region (36° 95′N, 10° 58′E) of Tunisia. A healthy tree, free of defects or alterations, with an almost perfectly straight trunk was selected as a representative population of the arboretum [32] (tree diameter of 40 cm at 1.25 m from the ground). To limit the natural variability of wood on the drying kinetic experiments, wood samples used in this study were randomly chosen from the heartwood of the log while respecting the directions of wood anisotropy (Longitudinal, Radial, and Tangential). The fresh sample size was 300 × 50 × 20 mm3 (L × R × T). To measure the initial humidity of the tree, a wooden disk 50 mm thick was cut from the selected tree. Then, samples with dimensions of 20 × 20 × 50 mm3 (longitudinal direction) were cut from the wooden disks according to the distribution presented in Fig. 1 [33]. The average initial moisture content and the anhydrous density of the selected samples were 52% and 946 kg/m3, respectively. The dry wood sample mass was obtained after keeping the small samples in the drying oven at a controlled temperature of 103 ± 2°C until a constant mass was reached.
Figure 1: Protocol of sample sawing for the drying kinetic and mechanical characterization experiments
During MWH, the moisture content (kg of water/kg of dry matter) was calculated using the following equation (Eq. (1)):
(1)
The drying rate (DR) was calculated using the following equation (Eq. (2)):
(2)
2.2 Measurement of Microwave Drying Kinetics
Microwave drying kinetics under continuous and intermittent scenarios were carried out using a laboratory microwave oven (BP-301) at a frequency of 2.45 GHz and at various input power levels (300, 500 and 1000 watts). These microwave powers have been those most commonly used in the literature to heat various wood species.
The microwave oven had the following characteristics: 1) output power ranges from 100 to 1000 watts; 2) working chamber dimensions of 340 × 330 × 200 mm3; 3) relative humidity ranging from 10% to 90% without condensation; and 4) equipped with an air extracting fan. During heating, wood samples were placed inside the microwave oven. The temperature was measured at different locations in the wood samples using a fiber optic sensor (OTG-A) such as shown in Fig. 2. The fiber optic sensor used functioned within a temperature range of −40°C to 250°C with an accuracy of 0.1°C. The mass of the samples being dried was periodically measured using a digital balance with an accuracy of ±0.001 g.
Figure 2: (a) Laboratory microwave oven (BP-301); (b) Signal conditioner (TempSens) connected to a computer; (c) Temperature sensor monitoring (fiber optic OTG-A) and locations within samples
2.3 Measurement of Mechanical Properties
The mechanical properties of wood samples heated with different MWH scenarios were determined through three-point static bending and compression tests using a universal testing machine. Modulus of elasticity (MOE) and modulus of rupture (MOR) of MWH and air-dried samples at low temperatures (T = 60°C, RH = 20%) were determined by analyzing the load-deformation data recorded for each sample. Then, the MOE and MOR of samples air-dried at low temperature were chosen as reference values to calculate the change in mechanical properties of samples heated by MWH. Before testing, all samples prepared for the mechanical tests were conditioned at a temperature of 20 ± 2°C and a relative humidity of 65 ± 5% until reaching 12% humidity.
Taking into consideration the limited dimensions of the working cavity of the microwave oven, sample sizes of the ASTM D143-94 [34] protocol were adjusted for the three-point static bending test in order to respect the prescribed L/D (span to depth ratio) of 15 [35]. The sample size was 300 × 20 × 20 mm3 (L × R × T). The moving head speed and span length were 1.2 mm/min and 260 mm, respectively. Axial compression tests of heated samples (30 × 20 × 20 mm3 (L × R × T)) were also carried out according to the specifications of the above standard [34]. The moving head speed was 1.2 mm/min to reach wood sample rupture. Mechanical tests were done ten times on ten samples from different MWH scenarios and convective drying.
Drying kinetics under continuous and intermittent microwave heating of Eucalyptus gomphocephala wood are shown in Figs. 3–5. For both heating methods, an increase in microwave power led to a decrease in drying time and an increase in the internal temperature of the samples. An increase in internal wood temperature increased water vapor pressure which in turn increased moisture migration rates [21]. Under MWH at 2.45 GHz, the electronic dipole of water molecules inside the wood was reoriented around the electromagnetic field. Consequently, internal heat was generated inside the wood samples as a result of the dipolar rotation when water molecules were reoriented [36].
Figure 3: Temporal temperature and moisture content evolution for different levels of microwave power under CMWH
Figure 4: Temporal evolution of moisture content, temperature at center and surfaces of wood samples vs. drying time at 1000 watts under CMWH
Figure 5: Temporal evolution of temperature and moisture content for different microwave power under IMWH
Fig. 4 shows the simultaneous evolution of average moisture content and temperature on the wood sample’s top, bottom, and center during heating at 1000 watts. Analysis of the curves shows three successive drying periods. The first period corresponds to a warm-up phase in which most of the thermal energy, converted from microwave energy, is used for raising the temperature of samples. This period is characterized by a rapid rise in temperature and slow water loss. The second period corresponds to the vaporization phase. This period is characterized by a constant temperature inside the material, where the dissipated microwave energy is associated with moisture evaporation. The third period is the heating-up period. During this period, the temperature of the wood increases gradually. It is characterized by slow water evaporation and rapid temperature increases inside the wood samples. The rise of temperature is due to the excessive heat build-up within the samples as well as the lack of evaporative cooling at the dry core [37]. These three MWH phases were found in previous works for Southern pine wood strands and Eucalyptus urophylla wood [38,39].
The IMWH scenario was conducted using an on/off cycle with the microwave heating and not heating, respectively. The time interval of on/off was established based on preliminary MWH experiments when the internal wood temperature did not exceed 110°C at 300, 500, and 1000 watts.
Fig. 5 shows the temporal evolution of internal wood temperature and moisture content under the IMWH scenario. At the beginning, the internal wood temperature rapidly reached 70°C, then increased slowly to reach 110°C in the end. We can see that the internal wood temperature oscillated due to the intermittency of microwave power. The period of increasing temperature corresponds to the MWH phase while the decreasing period corresponds to the phase without MWH. At the beginning of the scenario, the internal wood temperature oscillated 5°C or 6°C while at the end it oscillated around 3°C. This can be explained by the reduced moisture content at the end of the drying operation. Lower moisture content means reduced absorption of microwave energy, thus resulting in less internal heat being generated. The results show that increased microwave power reduces the time required for the internal temperature to reach 110°C, thereby reducing the drying time necessary to reach 12% moisture content.
Fig. 6 shows that increasing microwave power increased the drying rate. The maximum drying rates found are 0.0006, 0.0008, and 0.0012 (kg water/kg DM min) at 300, 500, and 1000 watts, respectively. At the beginning of IMWH, the drying rate increased until it reached 31% moisture content and then decreased until the end of the drying operation. The moisture content of 30% must therefore represent the fiber saturation point (FSP) of Eucalyptus gomphocephala wood. The phase where the drying rate was increasing corresponds to the evaporation of liquid water above the FSP, while the phase of decreasing rate corresponds to the evaporation of bound water below the FSP. These trends are similar to those found for Canadian jack pine wood [4,8]. The drying rate of Eucalyptus wood under IMWH can be described by a second-order polynomial law of moisture content. We can see that the parameters of polynomial laws of drying rate with moisture content are affected by microwave power levels as follows:
(3)
(4)
(5)
Figure 6: Drying rate of Eucalyptus gomphocephala wood samples under IMWH scenario
3.2 Influence of CMWH and IMWH on the Surface Appearance of Heated Samples
Fig. 7 shows the external surface of samples heated at 300, 500, and 1000 watts under the CMWH scenario. In Fig. 4, we see that the temperature at the center and peripheral region of the samples reached 178°C and 160°C at 1000 watts, respectively. Results show that samples treated at 1000 watts present carbonized regions of ligneous wood matter. The degradation occurring in wood heated at high temperatures indicates some chemical and structural modifications [40]. Arshanitsa et al. [41] found chemical changes in samples treated with microwave heating above 150°C. The carbonization reaction was located at the sample center, making it clear that internal heat is being generated in MWH [42].
Figure 7: External shape of wood samples heated under CMWH scenario (Left at 300 watts; Center at 500 watts; Right at 1000 watts)
Fig. 7 demonstrates that drying defects (coloration, cracking, etc.) of samples increase with increased microwave power. Applying intense microwave power to moist wood generates internal steam pressure within the wood cells that breaks some cell walls creating internal cracks and checks at the macroscopic wood scale [43–46]. According to Liu et al. [47], the high-intensity microwave treatment opens up channels in the pits and generates cracks in larch wood. Poonia et al. [48] mentioned that when applying higher microwave energy to heat Eucalyptus tereticornis wood, the high internal steam pressure causes the pit membranes in the cell walls to rupture, produces tyloses in the vessels, and weakens the ray cells, creating new pathways for transporting liquid and vapor. Similar findings were reported by Li et al. [39] for Eucalyptus urophylla wood, and by other papers [44,49] for various eucalyptus wood species. Yang et al. [50] said that eucalyptus wood is difficult to dry without degradation and indicated that most drying defects are more severe when increasing drying rates and temperature.
To avoid these problems related to internal gas overpressure and carbonization of the end quality of wood samples due to the high temperatures under CMWH, we investigated the IMWH scenario in the next part of the study.
Fig. 8 shows the external shape of samples heated under IMWH. Intermittent microwave energy reduces heat supply, temperature, over-gas pressure, and drying rate. This heating intermittency allows time for the water to migrate from the center to the sample surface. This scenario offers more uniform moisture content distribution and stress relaxation of the wood board [31]. Fig. 8 demonstrates that drying defects are reduced when using IMWH at 300, 500, and 1000 watts. This phenomenon can be explained by the decrease in internal temperature and over-gas pressure inside the samples, resulting in mechanical stress relaxation.
Figure 8: External shape of samples heated under IMWH (Left: at 300 watts; Center at 500 watts; Right at 1000 watts)
According to our results, CMWH presents the lowest drying time. However, the dried samples are of poor quality compared to the IMWH. On the other hand, IMWH, even though it has a higher drying time, leads to fewer drying defects and therefore does less harm to the external shape, particularly at low microwave power levels.
To determine the best MWH scenario for drying eucalyptus wood without degradation, we propose measuring the mechanical properties of the heated samples in the next part of the study.
3.3 Influence of Microwave Heating on Mechanical Properties
The MOE and MOR of Eucalyptus gomphocephala wood in three-point static bending and axial compression are presented in Table 1. Results show that the mechanical properties of eucalyptus wood samples heated under IMWH and CMWH scenarios decrease with increased microwave power. Similar results were reported in the literature for jack pinewood [4,8]. Oloyede et al. [14] revealed that Caribbean pine samples dried at 100% microwave power presented the least strength and stiffness compared with samples dried at 50% power level.
This study found that values for MOR and MOE in static bending and MOR in axial compression were all higher when the samples were dried under IMWH than when dried under CMWH. The MOR values in static bending tests were higher by 38%, 41%, and 49% at 300, 500, and 1000 watts, respectively (Fig. 9). The MOE values in static bending tests were greater by 29%, 31% and 48% at 300, 500 and 1000 watts, respectively (Fig. 10). The MOR values in axial compression were higher by 10%, 11% and 11% at 300, 500 and 1000 watts, respectively (Fig. 11). Therefore, we concluded that CMWH has a negative impact on the mechanical properties of eucalyptus wood samples compared to IMWH. In addition, the CMWH scenario had a more destructive effect on the MOR and MOE in static bending than on the axial compression properties. This effect was due to the high intensity of treatment during CMWH, where the internal temperature of samples exceeded 140°C. Liu et al. [47] demonstrated that high-intensity microwave treatment of larch wood changes its microstructure and affects its mechanical properties. Torgovnikov et al. [51] found reductions of 60% in MOR and 43% in MOE of Eucalyptus globules treated at high microwave levels. Hansson and et al. [36] reported that MWH of Norway spruce wood at temperatures of 60°C, 100°C, and 110°C during drying had no significant influence on hardness.
Figure 9: Effect of intermittent, continuous, and convective scenarios on MOR in static bending
Figure 10: Effect of intermittent, continuous, and convective scenarios on MOE in static bending
Figure 11: Effect of intermittent, continuous, and convective drying at 60°C on MOR in axial compression
The analysis of variance (ANOVA) showed that all mechanical properties of eucalyptus samples were affected by microwave power level (Table 2), except for MOR in axial compression from CMWH which was not significantly affected. Those properties did not meet the 0.05 significance level.
Indeed, there was a weak change of 16.16%, 11.75% and 0.79% on MOR and MOE in static bending and MOR in axial compression tests between mechanical properties of heated wood under intermittent and low microwave power level and those dried under a convective process at 60°C. Furthermore, eucalyptus wood samples dried under continuous and intermittent microwave treatment presented lower mechanical properties than those conventionally dried at 60°C (Table 3).
From this study, we recommend the use of IMWH at low microwave power that does not exceed an internal wood temperature of 110°C to heat Eucalyptus gomphocephala wood.
The MWH kinetics of Eucalyptus gomphocephala wood have been studied under various microwave powers, and a comparative study between continuous and intermittent heating scenarios was discussed in terms of end mechanical quality and appearance of heated samples and drying efficiency. The following conclusions have been drawn:
- Results indicated that an increase in microwave power decreased drying time and increased internal wood temperature;
- Internal heat was generated in the MWH of the sample, verified through the temporal evolution of internal wood temperature and drying rate curves;
- A qualitative analysis of the heated samples’ surface showed that the IMWH method reduced the drying defects and did not hurt the mechanical properties as much as those treated under CMWH;
- Comparison of mechanical properties showed that wood treated under IMWH had significantly higher bending and axial compressive strength compared to those samples treated under CMWH; and
- An ANOVA analysis demonstrated that the overall mechanical properties of eucalyptus wood were significantly affected by microwave power intensity and heating scenarios.
Acknowledgement: The authors would like to thank Madam Christie Chaar for correcting the English language of the manuscript.
Funding Statement: The authors received no specific funding for this study.
Author Contributions: The authors contributed to the paper as follows: study conception and design: Soufien Azzouz; data collection: Mariam Habouria; analysis and interpretation of results: Mariam Habouria, Sahbi Ouertani, Soufien Azzouz and Noura Ben Mansour; critical revision of the article: Sahbi Ouertani, Mohamed Taher Elaieb; drafting the article and English corrections: Sahbi Ouertani, Noura Ben Mansour; providing samples: Mohamed Taher Elaieb. All authors reviewed the results and approved the final version of the manuscript.
Availability of Data and Materials: Data available on a request from corresponding author.
Ethics Approval: Not applicable.
Conflicts of Interest: The authors declare no conflicts of interest to report regarding the present study.
References
1. Hietala M. Extrusion processing of wood raw materials for use in wood-polymer composites (Ph.D. Thesis). Luleå University of Technology, Luleå, Sweden, University of Oulu, Oulu, Finland; 2011. [Google Scholar]
2. Veitmans K, Grinfelds U. Wood fiber insulation material. In: Proceedings of the 22 nd Annual International Scientific Conference, 2016 May 18–20; Latvia University of Agriculture, Research for Rural Development; vol. 2, p. 91–8. [Google Scholar]
3. Ramage MH, Burridge H, Busse-Wicher M, Fereday G, Reynolds T, Shah DU, et al. The wood from the trees: the use of timber in construction. Renew Sustain Energy Rev. 2017;68(3):333–59. doi:10.1016/j.rser.2016.09.107. [Google Scholar] [CrossRef]
4. Ouertani S, Koubaa A, Azzouz S, Bahar R, Hassini L, Belghith A. Microwave drying kinetics of jack pine wood: determination of phytosanitary efficacy, energy consumption, and mechanical properties. Eur J Wood Wood Prod. 2018;76(4):1101–11. doi:10.1007/s00107-018-1316-x. [Google Scholar] [CrossRef]
5. Penvern H, Zhou M, Maillet B, Courtier-Murias D, Scheel M, Perrin J, et al. How bound water regulates wood drying. Phys Rev Appl. 2020;14(5):1–20. doi:10.1103/PhysRevApplied.14.054051. [Google Scholar] [CrossRef]
6. Leggate W, Kumar C, McGavin RL, Faircloth A, Knackstedt M. The effects of drying method on the wood permeability, wettability, treatability, and gluability of southern pine from Australia. BioResources. 2021;16(1):698–720. doi:10.15376/biores.16.1.698-720. [Google Scholar] [CrossRef]
7. Bahar R, Ouertani S, Azzouz S, Naili H, El Ayeb MT, El Cafci A. Mechanical properties changes in oak (Quersus canariensis) and stone pine (Pinus pinea) wood subjected to various convective drying conditions. Eur J Environ Civ En. 2019;24(13):2117–29. doi:10.1080/19648189.2018.1500308. [Google Scholar] [CrossRef]
8. Ouertani S, Hassini L, Azzouz S, Torres SS, Belghith A, Koubaa A. Modeling of combined microwave and convective drying of wood: prediction of mechanical behavior via internal gas pressure. Dry Technol. 2015;33(10):1234–42. doi:10.1080/07373937.2015.1022828. [Google Scholar] [CrossRef]
9. Mascarenhas FJR, Dias AMPG, Christoforo AL. State of the art of microwave treatment of wood: literature review. Forests. 2021;12(6):745. doi:10.3390/f12060745. [Google Scholar] [CrossRef]
10. Ritter E, Kismereshkin V, Cieslik J, Savostin A, Ritter D, Aytulina A, et al. Uniform large-sized lumber drying system using MW radiation and basing on a single-wire E00 wave energy transmission line. East-Eur J Enterp Technol. 2020;4/8(106)):21–8. doi:10.15587/1729-4061.2020.210752. [Google Scholar] [CrossRef]
11. Aksenov AA, Malyukov SV. Microwave modification of wood: determination of mechanical properties of softwood. IOP Conf Ser: Earth Environ Sci. 2020;595(1):012012. doi:10.1088/1755-1315/595/1/012012. [Google Scholar] [CrossRef]
12. Aniszewska M, Gendek A, Malaťák J, Tamelová B, Smyl S. Effects of microwave drying on moisture content depending on wood chip size distribution. Environ Sci Proc. 2021;3(1):54. doi:10.3390/IECF2020-07765. [Google Scholar] [CrossRef]
13. Weng X, Zhou Y, Fu Z, Gao X, Zhou F, Jiang J. Efects of microwave pretreatment on drying of 50 mm-thickness Chinese fir lumber. J Wood Sci. 2021;67(1):13. doi:10.1186/s10086-021-01942-2. [Google Scholar] [CrossRef]
14. Oloyede A. The influence of microwave heating on the mechanical properties of wood. J Mater Process Technol. 2000;100(1):67–73. doi:10.1016/S0924-0136(99)00454-9. [Google Scholar] [CrossRef]
15. Erchiqui F. 3D numerical simulation of thawing frozen wood using microwave energy: frequency effect on the applicability of the beer-lambert law. Dry Technol. 2013;31(11):1219–33. doi:10.1080/07373937.2013.784327. [Google Scholar] [CrossRef]
16. Vongpradubchai S, Makul N, Rattanadecho P. Influence of the microwave-accelerated process on the drying kinetics, mechanical properties and surface appearance of rubberwood (Heavea brasiliensis). Eur J Wood Prod. 2022;80(12):395–407. doi:10.1007/s00107-021-01766-3. [Google Scholar] [CrossRef]
17. Huang D, Shen H, Zhang J, Zhuo X, Dong L. Effects of hydrothermal-microwave treatment on bending properties of teak in plantation. Front Mater. 2024;11:1278707. doi:10.3389/fmats.2024.1278707. [Google Scholar] [CrossRef]
18. Kumar S. Studies on microwave vacuum drying of round Bambusa tulda. Adv Bamboo Sci. 2024;6(2):100053. doi:10.1016/j.bamboo.2023.100053. [Google Scholar] [CrossRef]
19. Kol HŞ, Çayır B. Increasing the impregnability of oriental spruce wood via microwave pretreatment. BioResources. 2021;16(2):2513–23. doi:10.15376/biores.16.2.2513-2523. [Google Scholar] [CrossRef]
20. Kol HŞ, Çayır B. The effects of increasing preservative uptake by microwave pre-treatment on the microstructure and mechanical properties of Oriental spruce wood. Wood Mater Sci Eng. 2022;18(2):732–8. doi:10.1080/17480272.2022.2077656. [Google Scholar] [CrossRef]
21. Mascarenhas FJR, Simões RMS, Dias AMPG, Christoforo AL, Cunha AEP. Moisture and temperature profiles of heartwood pinus pinaster ait. Wood specimens during microwave drying. Forests. 2024;15(6):944. doi:10.3390/f15060944. [Google Scholar] [CrossRef]
22. Yuniarti K, Ozarska B, Brodie G, Harris G, Waugh G. The drying performance and post-drying qualities of eucalyptus saligna exposed to intermittent and continuous drying. Indones J For Res. 2020;7(2):43–57. doi:10.20886/ijfr.2020.7.1.43-57. [Google Scholar] [CrossRef]
23. Hansson L, Antti A. The effect of microwave drying on Norway spruce woods strength: a comparison with conventional drying. J Mater Process Technol. 2003;141(1):41–50. doi:10.1016/S0924-0136(02)01102-0. [Google Scholar] [CrossRef]
24. Balboni BM, Ozarska B, Garcia JN, Torgovnikov G. Microwave treatment of Eucalyptus macrorhyncha timber for reducing drying defects and its impact on physical and mechanical wood properties. Eur J Wood Wood Prod. 2017;76(3):861–70. doi:10.1007/s00107-017-1260-1. [Google Scholar] [CrossRef]
25. Antti L, Finell M, Arshadi M, Lestander TA. Effects of microwave drying on biomass fatty acid composition and fuel pellet quality. Wood Mater Sci Eng. 2011;6(1–2):34–40. doi:10.1080/17480272.2010.516369. [Google Scholar] [CrossRef]
26. Liu H-H, Wang Q-W, Yang L, Jiang T, Cai Y-C. Modification of larch wood by intensive microwave irradiation. J For Res. 2005;16(3):237–40. doi:10.1007/BF02856823. [Google Scholar] [CrossRef]
27. Rajewska K, Smoczkiewicz-Wojciechowska A, Majka J. Intensification of beech wood drying process using microwaves. Chem Process Eng. 2019;40(2):179–87. doi:10.24425/cpe.2019.126110. [Google Scholar] [CrossRef]
28. Mascarenhas FJR, Dias AMPG, Christoforo AL, Simões RMS, Cunha AEP. Effect of microwave treatment on drying and water impregnability of Pinus pinaster and Eucalyptus globulus. Maderas Cienc Tecnol. 2023;25(6):1–14. doi:10.4067/s0718-221x2023000100406. [Google Scholar] [CrossRef]
29. Booth TH. Eucalypt plantations and climate change. For Ecol Manag. 2013;301:28–34. doi:10.1016/j.foreco.2012.04.004. [Google Scholar] [CrossRef]
30. Yuniarti K, Ozarska B, Brodie G, Harris G, Waugh G. Collapse development of eucalyptus saligna under different drying temperatures. J Trop For Sci. 2015;27(4):462–71. Available from: http://www.jstor.org/stable/43596223. [Google Scholar]
31. Yang L, Liu H. A review of eucalyptus wood collapse and its control during drying. BioResources. 2018;13(1):2171–81. doi:10.15376/biores.13.1.Yang. [Google Scholar] [CrossRef]
32. Elaieb MT, Ben Ayed S, Ouellani S, Khouja ML, Touhami I, Candelier K. Collapse and physical properties of native and pre-steaming eucalyptus camaldulensis and eucalyptus saligna woods from Tunisia. J Trop For Sci. 2019;31(2):162–47. doi:10.26525/jtfs2019.31.2.162174. [Google Scholar] [CrossRef]
33. Habouria M, Ouertani S, Azzouz S, Hermassi I, Elaieb MT. Analysis of thermodynamic properties of moisture-desorption isotherms of Eucalyptus gomphocepha wood. Wood Mater Sci Eng. 2022;18(3):1094–104. doi:10.1080/17480272.2022.2108336. [Google Scholar] [CrossRef]
34. ASTM D143-94. Standard test methods for small clear specimens of timber. Available from: https://www.astm.org/DATABASE.CART/HISTORICAL/D143-94R00E1.htm. [Accessed 2024]. [Google Scholar]
35. Yemele MCN, Koubaa A, Cloutier A, Soulounganga P, Stevanovic T, Wolcott MP. Effects of hot water treatment of raw bark, coupling agent, and lubricants on properties of bark/HDPE composites. Ind Crops Prod. 2013;42(1):50–6. doi:10.1016/j.indcrop.2012.05.012. [Google Scholar] [CrossRef]
36. Hansson L, Antti AL. The effect of drying method and temperature level on the hardness of wood. J Mater Process Technol. 2006;171(3):467–70. doi:10.1016/j.jmatprotec.2005.08.007. [Google Scholar] [CrossRef]
37. Bartholme M, Avramidis G, Viöl W, Kharazipour A. Microwave drying of wet processed wood fibre insulating boards. Eur J Wood Wood Prod. 2009;67(3):357–60. doi:10.1007/s00107-008-0306-9. [Google Scholar] [CrossRef]
38. Du G, Wang S, Cai Z. Microwave drying of wood strands. Dry Technol. 2005;23(12):2421–36. doi:10.1080/07373930500340494. [Google Scholar] [CrossRef]
39. Li X, Lu K, Lin L, Zhou Y, Cai Z, Fu F. Fundamental characteristics of microwave explosion pretreatment of wood I. Properties of temperature development. For Stud China. 2010;12(1):9–13. doi:10.1007/s11632-010-0004-7. [Google Scholar] [CrossRef]
40. Saporiti J. Effect of microwave treatment on oak compression strength. Silva Lus. 2006;14(1):51–8. [Google Scholar]
41. Arshanitsa A, Dizhbite T, Bikovens O, Pavlovich G, Andersone A, Telysheva G. Effects of microwave treatment on the chemical structure of lignocarbohydrate matrix of softwood and hardwood. Energy Fuels. 2016;30(1):457–64. doi:10.1021/acs.energyfuels.5b02462. [Google Scholar] [CrossRef]
42. Hansson L. Microwave treatment of wood (Ph.D. Thesis). Luleå University of Technology: Luleå, Sweden; 2007. [Google Scholar]
43. Perré P, Keey R. Drying of wood: principles and practices. In: Arun S, Mujumdar, editors. Handbook of industrial drying. 4th ed. Boca Raton: CRC Press; 2014. p. 797–846. doi:10.1201/b17208. [Google Scholar] [CrossRef]
44. Torgovnikov G, Vinden P. High-intensity microwave wood modification for increasing permeability. For Prod J. 2009;59(4):84–92. [Google Scholar]
45. Terziev N, Daniel G, Torgovnikov G, Vinden P. Effect of microwave treatment on the wood structure of Norway spruce and radiata pine. BioResources. 2020;15(3):5616–26. doi:10.15376/biores.15.3.5616-5626. [Google Scholar] [CrossRef]
46. Ganguly S, Balzano A, Petrič M, Kržišnik D, Tripathi S, Žigon J, et al. Effects of different energy intensities of microwave treatment on heartwood and sapwood microstructures in Norway spruce. Forests. 2021;12(5):598. doi:10.3390/f12050598. [Google Scholar] [CrossRef]
47. Liu M, Li C, Wang Q. Microstructural characteristics of Larch wood treated by high-intensity microwave. BioResources. 2010;14(1):1174–84. doi:10.15376/biores.14.1.1174-1184. [Google Scholar] [CrossRef]
48. Poonia PK, Tripathi S, Sihag K, Kumar S. Effect of microwave treatment on air permeability and preservative impregnation of Eucalyptus Tereticornis wood. J Indian Acad Wood Sci. 2015;12(2):89–93. doi:10.1007/s13196-015-0148-0. [Google Scholar] [CrossRef]
49. Hermoso E, Vega A. Effect of microwave treatment on the impregnability and mechanical properties of Eucalyptus globulus wood. Maderas Cienc Tecnol. 2016;18(1). doi:10.4067/S0718-221X2016005000006. [Google Scholar] [CrossRef]
50. Yang L, Liu H, Cai Y, Wu Z. A novel method of studying the collapsed cell of eucalyptus wood using X-ray CT scanning. Dry Technol. 2019;37(12):1597–604. doi:10.1080/07373937.2018.1519572. [Google Scholar] [CrossRef]
51. Torgovnikov G, Vinden P, Balboni BM. Microwave conversion of plantation grown blue gum (Eucalyptus globulues L’Herit) wood to Torgvin and impregnation with a metal alloy. J Mater Sci Eng Adv Technol. 2015;11(1):1–19. doi:10.18642/jmseat_7100121430. [Google Scholar] [CrossRef]
Cite This Article
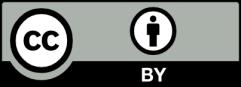
This work is licensed under a Creative Commons Attribution 4.0 International License , which permits unrestricted use, distribution, and reproduction in any medium, provided the original work is properly cited.