Open Access
ARTICLE
Optimizing Heat Sink Performance by Replacing Fins from Solid to Porous inside Various Enclosures Filled with a Hybrid Nanofluid
1 Mechanical Engineering Department, University of Babylon, Babylon, 51001, Iraq
2 School of Engineering and Physical Sciences, Heriot Watt University, Edinburgh, EH14 4AS, UK
* Corresponding Author: Ahmed Dhafer Abdulsahib. Email:
Frontiers in Heat and Mass Transfer 2024, 22(6), 1777-1804. https://doi.org/10.32604/fhmt.2024.057209
Received 11 August 2024; Accepted 27 September 2024; Issue published 19 December 2024
Abstract
The current study generally aims to improve heat transfer in heat sinks by presenting a numerical analysis of natural convection of an enclosure with hot right and cool left walls, and thermally insulated top and bottom walls. The cold wall included configurations (half circle/half square) in various sizes (S = 0.1, 0.2, and 0.3), numbers (N = 1, 2, 3, and 4), and locations (C = 0.35, and 0.65). A heat sink is constructed of Aluminum attached to the hot wall, and composed of five fins with protrusions. Fins of the heat sink will be examined in a solid and porous structure. The enclosure is filled with a hybrid nanofluid of Nanoparticles (MWCNT and Fe3O4) and water. The current study utilized COMSOL Multiphysics software due to its efficacy in addressing scientific and technical challenges involving partial differential equations. The solving of the governing equations is achieved using the finite element method with various parameters: Rayleigh number (Ra = 103–106), Darcy number (Da = 10−2, 10−3), solid volume fraction ( = 0–0.06) to determine stream function, isotherms lines, and average Nusselt number (Nu). The results of numerical simulations show that heat sink with solid fins have a 97% higher stream function when Ra is raised from 103 to 105. Whilst with porous fin heat sink, a stream function 96% for Da = 10−3 and 94% for Da = 10−2. Changing solid fins to porous increases stream functions by 9% at Da = 10−3 and 20% at Da = 10−2. It has been found that Ra increases Nu by 44% for solid fins and 50% for porous fins. Making solid fins porous increases Nu by 54% at Ra = 106. The high increase in the percentage of (Nu) indicates the importance of the improvement in heat transfer, and this distinguishes the results of the current study from previous studies. Nu values were found highest for (half square) compared to (half circle), with 2% increases for numbers, 11.6% for sizes, and 11% for location. Solid volume fractions for all Ra at a solid-finned heat sink increased Nu by 23%.Graphic Abstract

Keywords
Cite This Article
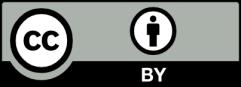
This work is licensed under a Creative Commons Attribution 4.0 International License , which permits unrestricted use, distribution, and reproduction in any medium, provided the original work is properly cited.