Open Access
ARTICLE
A Novel Integrated Photovoltaic System with a Three-Dimensional Pulsating Heat Pipe
Department of Mechanical Engineering, Mashhad Branch, Islamic Azad University, Mashhad, 9187147578, Iran
* Corresponding Author: Mahyar Kargaran. Email:
(This article belongs to the Special Issue: Multiscale Heat and Mass Transfer and Energy Conversion)
Frontiers in Heat and Mass Transfer 2024, 22(5), 1461-1476. https://doi.org/10.32604/fhmt.2024.056284
Received 19 July 2024; Accepted 14 August 2024; Issue published 30 October 2024
Abstract
Solar energy is a valuable renewable energy source, and photovoltaic (PV) systems are a practical approach to harnessing this energy. Nevertheless, low energy efficiency is considered a major setback of the system. Moreover, high cell temperature and reflection of solar irradiance from the panel are considered chief culprits in this regard. Employing pulsating heat pipes (PHPs) is an innovative and useful approach to improving solar panel performance. This study presents the results of the power performance of a PV panel attached to a newly designed spiral pulsating heat pipe, while graphene oxide nanofluid with three different concentrations was used as a working fluid to maximize the efficacy of the solar panel. The study proved that the cooling method delivered high efficiency by reducing the temperature, especially in the middle of the day. Using nanofluid graphene oxide at concentrations of 0.2, 0.4, and 0.8 gr/lit as the working fluid can reduce the thermal resistance of PHPs by over 30%, 24%, and 15%, respectively. This, in turn, enhances the system’s electrical power output by approximately 9%, 7%, and 6%, respectively.Keywords
Nomenclature
A | Panel aperture area (m2) |
Cp | Heat capacity of flowing medium (J/kg.k) |
G | Incident solar radiation (W/m2) |
I | Electric current (A) |
˙m | Mass flow rate (kg/s) |
Q | Heating power (W) |
P | Power (W) |
T | Temperature (°C) |
R | Thermal resistance (°C W-1) |
V | Voltage (V) |
η | Efficiency (%) |
Acronyms | |
OHP | Oscillating heat pipe |
PHP | Pulsating heat pipe |
PV | Photovoltaic |
S | Speed |
Subscripts | |
a | Ambient |
b | Improvement |
c | Condenser |
el | Electrical |
e | Evaporator |
in | Input |
mp | Maximum power point |
oc | Open-circuit |
out | Output |
s | Solar panel |
sc | Short-circuit |
w | Wind |
The depletion of fossil resources has become a highly controversial issue. Conventional energy resources such as oil and natural gas will be drained in less than 70 years [1]. Developing reliable and sustainable sources is identified as one of the most pragmatic approaches to resolving this issue. Renewable energy technology has been considered a viable and attractive option to tackle the energy crisis [2]. However, the application of this technology faces two grave problems, namely low efficiency and manufacturing cost [3]. Photovoltaic (PV) technology has caught considerable attention due to its cost-effectiveness, durability, and simple structure [4,5]. Generally, the efficiency of PV panels varies from 10% to 23% [6]. On the other hand, increasing cell temperature produces an adverse effect on PV efficiency [7]. Solar radiation intensity and ambient temperature are considered two decisive factors that dramatically affect photovoltaic efficiency [8]. PV cell efficiency is lowest at the highest solar intensity and lowest wind speed, leading to cell overheating [9]. Therefore, to enhance PV efficiency, the generated heat should be dissipated. A large number of methods have been implemented to cool PV cell temperature, and the major ones are the active methods (air cooling [10] and water cooling [11,12]) and passive methods (heat pipe [13], PCM [14], and nanofluid [15]) listed in Fig. 1.
Figure 1: Cooling approaches of solar panels
On the other hand, there are major disadvantages related to air cooling and water cooling, such as low efficiency and freezing problems [16]. Heat pipes are considered a viable solution to address these problems, making a significant contribution to improving photovoltaic efficiency [17]. Heat pipes are divided into five types (cylindrical heat pipe, loop heat pipe, rotating heat pipe, variable conductance heat pipe, and pulsating heat pipe (PHP) [18]), which offer high performance in terms of heat transfer [19]. Heat pipes are highly advantageous due to their low weight, cost-efficiency, reliability, and easy-to-manufacture structure [20]. Heat pipe performance is vulnerable to some factors, such as the heat input [21], filling ratio [22], tube diameter [23], inclination angle [24,25], and the length of tubes [26]. Xu et al. [27] designed a new type of PV connected with an oscillating (pulsating) heat pipe. It was observed that the thermal resistance of the PHP absorber diminishes with increasing evaporation temperature, and they also showed that the system can offer promising efficiency. Ersoz [28] applied acetone, hexane, ethanol, petroleum ether, methanol, and chloroform as coolants and investigated their impact on the thermal behavior of a heat pipe solar collector in Turkey. When the air velocity was between 2–4 m/s, acetone and chloroform offered the most optimal performance.
The emergence of pulsating heat pipes (PHPs) in the early 1990s [29] as one of the most efficient, innovative pieces of equipment has drawn a lot of attention, thanks to their impressive performance in terms of heat transfer and unique design [30]. Patel et al. [31] investigated the effect of eleven coolants on a pulsating heat pipe solar water heater. Pure fluids (DI water, acetone, methanol, and ethanol) and binary fluids (a mixture of water with the mentioned coolants) were used. It was observed that acetone was the best pure working fluid, and concerning binary fluids, water-acetone provided greater performance.
Nanofluid, which comprises a base fluid and solid nanometer particles, has broadened perspectives to promote the performance of thermal control devices [32]. It has proven that adding nanoparticles significantly contributes to improving the thermal performance of the coolant [33]. Pulsating heat pipes achieve remarkable performance when nanofluids are utilized as the coolant [34]. Dehaj et al. [35] studied the efficiency of a heat pipe solar panel using Al₂O₃, and CuO nanofluids. Their findings showed that the nanofluids enhanced the panel’s efficiency by over 9%.
The research conducted by Alizadeh et al. [36] highlights the effectiveness of single-turn pulsating heat pipes in improving the thermal management of photovoltaic (PV) panels. Their numerical simulations offer valuable insights into optimizing PHP designs to maximize cooling efficiency, resulting in an 18% enhancement in the overall performance of PV systems.
Graphene oxide (GO) nanofluids have the potential to significantly enhance the performance of heat pipes through improved thermal conductivity and heat transfer efficiency [37,38]. GO nanofluids typically demonstrate good stability and dispersion in the base fluid, which is crucial for maintaining consistent thermal performance [39].
Both 2D and 3D pulsating heat pipes (PHPs) are effective for thermal management, but 3D PHPs, with their superior thermal performance and intricate fluid dynamics, are better suited for high-power, multi-dimensional applications requiring excellent heat dissipation and operational stability [40]. Thompson et al. [41] investigated three-dimensional flat-plate oscillating heat pipes (3D FP-OHPs) filled with water or acetone, noting that the lowest thermal resistance achieved was 0.08°C/W with water. Additionally, Ling et al. [42] demonstrated that a PCM/3D-PHP cooling system for electronic devices could reduce thermal resistance by up to 36.3% by efficiently transferring heat to the environment.
Jung et al. [43] compared a 3D pulsating heat pipe (PHP) with a conventional PHP, finding that the 3D-PHP had enhanced heat transfer due to additional flow, leading to reductions of up to 14.7% in thermal resistance and 6.7°C in evaporator temperature under uniform heating conditions. Dia et al. [44] designed a new 3D-PHP and studied the effects of geometric parameters and operating conditions on its performance, noting that a uniform distribution of vapor-liquid plugs significantly improved the PHP’s performance.
The review reveals a noticeable gap in experimental research aimed at optimizing PV panel efficiency using 3D-PHPs, with most studies focusing solely on 2D-PHP designs. In response, this study involves modeling PV panels equipped with innovative 3D-PHPs using various working fluids to determine the optimal configuration for maximizing electrical efficiency. The goal of this research is to introduce a new 3D-PHP design that is both practical for real-world applications and capable of handling higher heat flux compared to previous designs. This research is exceptional and presents significant findings by introducing a practical and innovative cooling method for lowering solar panel temperatures. Additionally, the proposed system demonstrated high efficiency, as it could dissipate heat from the solar panels without relying on an external power, thereby enhancing its cost-effectiveness.
This section provides an in-depth explanation of the experimental setup and the formulas used for calculating the results.
An experimental setup was tested in Iran (Mashhad). It should be mentioned that in this study, two monocrystalline solar panels were used. One of them was considered the cooled panel equipped with a spiral 3D-PHP, and the other served as the reference panel. Fig. 2 displays the electrical features of the solar panel.
Figure 2: Electrical features of the solar panel
Fig. 3 depicts the new three-dimensional PHP fabricated with the copper. While in Table 1, detailed design of 3D-PHP is demonstrated.
Figure 3: Configuration of PHP from different views
Research has demonstrated that a 50% filling ratio yields the best performance for PHPs [45,46]. Consequently, all tests were conducted using this ratio. A vacuum was provided by a vacuum pump before the PHP was loaded with coolant. The experimental setup is shown in Fig. 4, while a schematic of the experiment is depicted in Fig. 5.
Figure 4: Picture of experiment setup
Figure 5: Schematic diagram of experiment
Despite many studies that have used the lamination technique to attach the evaporator to solar panels [47], in this study, a copper sheet was attached to the solar panel with thermal paste, which contributed to lowering the operation costs and simplifying the system. Graphene oxide nanofluid with three different concentrations (0.2, 0.4, 0.8 gr/lit) was prepared, with distilled water as the base fluid, to be used as a coolant. The graphene oxide used in this study was sourced from US Research Nanomaterials, Inc. As mentioned earlier, nanofluids improve the base fluid’s overall thermal conductivity, but they also need to be stable and durable [48]. Thus, the surfactant sodium dodecyl sulfate was added. The scanning electron microscopy image of GO is shown in Fig. 6.
Figure 6: Scanning electron microscopy image of GO
Raman spectroscopy analysis of GO is illustrated in Fig. 7. Characteristic peaks are demonstrated, specifically at around 1400 cm-1 for the D band and 1600 cm-1 for the G band of graphene oxide.
Figure 7: Raman spectroscopy analysis of GO
Table 2 illustrates thermal conductivity of and GO with three different concentrations used in this investigation.
In this study, to measure temperature, four K-type thermocouples were installed in the condenser section, and four were placed in the evaporator section. Their values were calculated as follows:
Tc=Tc1+Tc2+Tc3+Tc44(1)
Te=Te1+Te2+Te3+Te44(2)
The thermal resistance is defined as:
R=ΔTQ(3)
And Q is defined as heat which PHP receives [49], while ΔT is calculated as:
ΔT=Te−Tc(4)
Thermal efficiency of a solar panel is demonstrated as [50]:
ηx=˙mCp∫t2t1(To−Tx)dtA∫t2t1Gdt(5)
Hence, the electrical efficiency of solar panel is defined as the percentage of sunlight that a solar cell converts into usable electricity, calculated by Eq. (6) [51].
ηel=PoutPin=VmpImpAG(6)
The amount of improvement of proposed system in terms of efficiency is defined as [52]:
ηb=ηPHP−PVηPV−1(7)
In experimental investigations, the accuracy of the gathered data is essential. Therefore, to evaluate this accuracy, an uncertainty analysis must be conducted. The uncertainty in the calculation of values is measured based on both direct and indirect data [53]. Measurement errors of the instruments and data acquisition errors are calculated and listed in Table 3.
The temperature, power output, and efficiency of the solar panels were assessed. Tests were conducted on clear days, reflecting the climate of Mashhad, Iran. Additionally, two panels were used in the study: one was equipped with a 3D-PHP, while the other served as a reference panel.
Fig. 8 illustrates that both the ambient temperature and the solar panel temperature rise steadily until reaching their highest point at midday. After this peak, both temperatures begin to decline. Similarly, solar intensity follows a comparable trend, peaking at over 1120 W/m2 around 11:30 local time, and dropping to a minimum of 750 W/m2 (as shown in Fig. 9).
Figure 8: Ambient temperature and solar panel temperature
Figure 9: Solar intensity and wind speed
Wind speed is a parameter that affects solar panel efficiency and PHP performance. Over time, the average value (as shown in Fig. 9) increases, reaching over 9 km/h by the end of the test.
Electrical efficiency is influenced by solar irradiance and panel temperature [54]. The more irradiance the panel receives, the higher its efficiency. Nonetheless, Isc and VOC exhibit quite the opposite behavior as the panel temperature changes (Fig. 10).
Figure 10: Isc and VOC behavior during the test
Solar panels are responsible for capturing sunlight and converting it into electricity. The larger the area covered by solar panels, the better the chance of capturing the sun’s energy. One of the parameters that strongly influences the efficiency of a solar panel is its angle of tilt with the horizon, which consequently affects the amount of solar radiation received; therefore, they need to be tilted at the optimal angle to achieve maximum efficiency [55]. The system was tested at a 30° tilt angle, which is the best angle for solar panels in Mashhad [56].
The amount of thermal resistance of the 3D-PHP for different coolants has been calculated. At lower heat transfer rates, conduction is the primary mode of heat transfer. However, at higher temperatures, the presence of nanoparticles increases the number of active nucleation sites in the evaporator, facilitating the boiling process in the PHP, which leads to better PHP performance. Using graphene oxide helps reduce the thermal resistance of the PHP; however, as the concentration increases, dynamic viscosity also increases, which impedes fluid movement in the tube and, as a result, deteriorates thermal performance. On the other hand, at higher temperatures, the working fluid moves more easily, which mitigates the impact of high dynamic viscosity. As demonstrated in Fig. 11, graphene oxide with a concentration of 0.2 gr/lit produces the best performance.
Figure 11: Thermal resistance vs. received heat
The maximum solar panel performance occurs at 25°C and above that it suffers loss due to high temperature which strongly affects it. As mentioned earlier, by increasing temperature (more than 25°C), PV power output decreases. The higher the PV cell temperature gets, the more it suffers in terms of performance. On the other hand, the difference in solar irradiance (SI) is not significant enough to compensate for the negative effect of rising temperature. In other words, the negative impact of temperature rise outweighs the benefit of increased solar irradiance received by the cells. In this experiment maximum Pout is over 46 W, which is quite noticeable, when graphene oxide with the concentration of 0.2 gr/lit was employed as a coolant (Fig. 12).
Figure 12: Effect of coolants on Pout
Since PV efficiency is highly sensitive to cell’s temperature, in other words, negative impact of temperature rise outweighs solar irradiance the cells receive. On the other hand, using a PHP can significantly contribute to minimizing the loss, especially at higher temperatures. Furthermore, at the hottest time of the test, PHPs with different graphene oxide concentrations showed similar performance (Fig. 13).
Figure 13: Effect of coolants on electrical efficiency
Fig. 14 demonstrates how varying concentrations of graphene oxide influence the enhancement of a solar panel’s electrical efficiency. The data clearly show that the system reached peak performance with a coolant concentration of 0.2 gr/lit, particularly during the hottest part of the day.
Figure 14: Electrical efficiency improvement with different coolants
The power output of solar panels is significantly influenced by the temperature of the cells, which decreases as the temperature increases. In this study, a new cooling method was implemented to improve the electrical efficiency of the solar panel. It was observed that at higher temperatures, nanoparticles increase the number of active nucleation sites in the evaporator, enhancing the boiling process and improving PHP performance. The experimental results reveal that using graphene oxide nanofluids at various concentrations effectively reduces thermal resistance, with the most notable reduction observed at a concentration of 0.2 gr/lit. This reduction in thermal resistance directly translates into increased electrical power output, thereby validating the efficacy of this cooling method. Furthermore, using a 3D pulsating heat pipe with nanofluid effectively lowered the temperature, leading to improvements in maximum power output of over 9%, 7%, and 6% for graphene oxide concentrations of 0.2, 0.4, and 0.8 gr/lit, respectively. The proposed cooling system is simple and cost-effective, requiring no external power sources like pumps, making it promising for industrial and residential rooftop applications. However, despite numerous studies, PV systems integrated with heat pipes, especially PHPs, have not yet been commercialized. Further investigation is needed to ensure the long-term reliability and performance of these systems in real-world conditions.
Acknowledgement: The authors acknowledge Islamic Azad University Mashhad Branch.
Funding Statement: The authors received no specific funding for this study.
Author Contributions: The authors confirm contribution to the paper as follows: study conception and design: Mahyar Kargaran; data collection: Mahyar Kargaran, Hamid Reza Goshayeshi; analysis and interpretation of results: Mahyar Kargaran, Hamid Reza Goshayeshi, Ali Reza Alizadeh Jajarm; draft manuscript preparation: Mahyar Kargaran. All authors reviewed the results and approved the final version of the manuscript.
Availability of Data and Materials: The data are available from the corresponding author upon reasonable request.
Ethics Approval: Not applicable.
Conflicts of Interest: The authors declare that they have no conflicts of interest to report regarding the present study.
References
1. Yousaf S, Akhtar T, AlMasoud N, Ayub K, Rauf S, Tariq M, et al. Porphyrin-anhydride co-sensitization strategy for enhanced photovoltaic performance in DSSC: a combined experimental and theoretical approach. Polyhedron. 2023 Dec 1;246(5):116675. doi:10.1016/j.poly.2023.116675. [Google Scholar] [CrossRef]
2. Gholikhani M, Roshani H, Dessouky S, Papagiannakis AT. A critical review of roadway energy harvesting technologies. Appl Energy. 2020 Mar 1;261(1):114388. doi:10.1016/j.apenergy.2019.114388. [Google Scholar] [CrossRef]
3. Saif OM, Elogail Y, Abdolkader TM, Shaker A, Zekry A, Abouelatta M, et al. Comprehensive review on thin film homojunction solar cells: technologies, progress and challenges. Energies. 2023 May 30;16(11):4402. doi:10.3390/en16114402. [Google Scholar] [CrossRef]
4. Mogren MMAl, Ahmed NM, Hasanein AA. Molecular modeling and photovoltaic applications of porphyrin-based dyes: a review. J Saudi Chem Soc. 2020 Mar 1;24(3):303–20. doi:10.1016/j.jscs.2020.01.005. [Google Scholar] [CrossRef]
5. Allouhi, Rehman S, Buker MS, Said Z. Recent technical approaches for improving energy efficiency and sustainability of PV and PV-T systems: a comprehensive review. Sustain Energy Technol Assess. 2023 Mar 1;56:103026. doi:10.1016/j.seta.2023.103026. [Google Scholar] [CrossRef]
6. Du D, Darkwa J, Kokogiannakis G. Thermal management systems for photovoltaics (PV) installations: a critical review. Sol Energy. 2013 Nov 1;97:238–54. doi:10.1016/j.solener.2013.08.018. [Google Scholar] [CrossRef]
7. Patil M, Sidramappa A, Shetty SK, Hebbale AM. Experimental study of solar PV/T panel to increase the energy conversion efficiency by air cooling. Mater Today: Proc. 2023 Jan 1;92(3):309–13. doi:10.1016/j.matpr.2023.05.007. [Google Scholar] [CrossRef]
8. Talwar P, Verma N, Khatri H, Ahire PD, Chaudhary G, Lindenberger C, et al. A systematic review of photovoltaic-green roof systems in different climatic conditions focusing on sustainable cities and societies. Sustain Cities Soc. 2023 Jul 20;104813. doi:10.1016/j.scs.2023.104813. [Google Scholar] [CrossRef]
9. Ebhota WS, Tabakov PY. Influence of photovoltaic cell technologies and elevated temperature on photovoltaic system performance. Ain Shams Eng J. 2023 Jul 1;14(7):101984. doi:10.1016/j.asej.2022.101984. [Google Scholar] [CrossRef]
10. Choubineh N, Jannesari H, Kasaeian A. Experimental study of the effect of using phase change materials on the performance of an air-cooled photovoltaic system. Renew Sustain Energ Rev. 2019;101(1):103–11. doi:10.1016/j.rser.2018.11.001. [Google Scholar] [CrossRef]
11. Schiro F, Benato A, Stoppato A, Destro N. Improving photovoltaics efficiency by water cooling: modelling and experimental approach. Energy. 2017;137(7):798–810. doi:10.1016/j.energy.2017.04.164. [Google Scholar] [CrossRef]
12. Bahaidarah H, Subhan A, Gandhidasan P, Rehman S. Performance evaluation of a PV (photovoltaic) module by back surface water cooling for hot climatic conditions. Energy. 2013;59(6):445–53. doi:10.1016/j.energy.2013.07.050. [Google Scholar] [CrossRef]
13. Fu HD, Pei G, Ji J, Long H, Zhang T, Chow TT. Experimental study of a photovoltaic solar-assisted heat-pump/heat-pipe system. Appl Therm Eng. 2012;40:343–50. doi:10.1016/j.applthermaleng.2012.02.036. [Google Scholar] [CrossRef]
14. Chandel SS, Agarwal T. Review of cooling techniques using phase change materials for enhancing efficiency of photovoltaic power systems. Renew Sustain Energ Rev. 2017;73:1342–51. doi:10.1016/j.rser.2017.02.001. [Google Scholar] [CrossRef]
15. Ali HM, Shah TR, Babar H, Khan ZA. Application of nanofluids for thermal management of photovoltaic modules: a review. Microfluid Nanofluid. 2018;10. doi:10.5772/intechopen.74967. [Google Scholar] [CrossRef]
16. Pei G, Fu H, Zhang T, Ji J. A numerical and experimental study on a heat pipe PV/T system. Sol Energy. 2011;85(5):911–21. doi:10.1016/j.solener.2011.02.006. [Google Scholar] [CrossRef]
17. Gao Y, Wu D, Dai Z, Wang C, Chen B, Zhang X. A comprehensive review of the current status, developments, and outlooks of heat pipe photovoltaic and photovoltaic/thermal systems. Renew Energy. 2023 May 1;207(10):539–74. doi:10.1016/j.renene.2023.03.039. [Google Scholar] [CrossRef]
18. Jose J, Hotta TK. A comprehensive review of heat pipe: its types, incorporation techniques, methods of analysis and applications. Thermal Sci Eng Progress. 2023 Jul 1;42:101860. doi:10.1016/j.tsep.2023.101860. [Google Scholar] [CrossRef]
19. Wang X, Wen Q, Yang J, Xiang J, Wang Z, Weng C, et al. A review on data centre cooling system using heat pipe technology. Sustain Comput: Inform Syst. 2022 Sep 1;35:100774. doi:10.1016/j.suscom.2022.100774. [Google Scholar] [CrossRef]
20. Alshukri MJ, Hussein AK, Eidan AA, Alsabery AI. A review on applications and techniques of improving the performance of heat pipe-solar collector systems. Sol Energy. 2022 Apr 1;236(8):417–33. doi:10.1016/j.solener.2022.03.022. [Google Scholar] [CrossRef]
21. Pagliarini L, Iwata N, Bozzoli F. Pulsating heat pipes: critical review on different experimental techniques. Exp Therm Fluid Sci. 2023 Oct 1;148(23):110980. doi:10.1016/j.expthermflusci.2023.110980. [Google Scholar] [CrossRef]
22. Ahmadian-Elmi M, Hajmohammadi MR, Nourazar SS, Vafai K, Shafii MB. Effect of filling ratio, number of loops, and transverse distance on the performance of pulsating heat pipe in a microchannel heat sink. Numer Heat Transf A: Appl. 2024 Apr 17;85(8):1278–99. doi:10.1080/10407782.2023.2200217. [Google Scholar] [CrossRef]
23. Su Z, Hu Y, Zheng S, Wu T, Liu K, Zhu M, et al. Recent advances in visualization of pulsating heat pipes: a review. Appl Therm Eng. 2023 Feb 25;221(7):119867. doi:10.1016/j.applthermaleng.2022.119867. [Google Scholar] [CrossRef]
24. Kargaran M, Goshayeshi HR, Saleh SR, Zahmatkesh I, Chaer I. Novel cooling system for free-standing photovoltaic panels. Energy Sources A: Recov Util Environ Effects. 2024;46(1):8155–70. doi:10.1080/15567036.2024.2368492. [Google Scholar] [CrossRef]
25. Xu H, Yang Y, Gan K, Zhang H, Gao Y, Li R, et al. Heat transfer performance of novel high temperature flat heat pipe (HTFHP) with heating power and inclination angles. Appl Therm Eng. 2023;220:119679. doi:10.1016/j.applthermaleng.2022.119679. [Google Scholar] [CrossRef]
26. Zhan J, Chen X, Ji Y, Zheng P, Duan W. Experimental study of ethane pulsating heat pipe with varying evaporator lengths based on pulse tube refrigerator. Int J Refrig. 2023;145:40–9. doi:10.1016/j.ijrefrig.2022.09.010. [Google Scholar] [CrossRef]
27. Xu R, Zhang X, Wang R, Xu S, Wang H. Experimental investigation of a solar collector integrated with a pulsating heat pipe and a compound parabolic concentrator. Energy Convers Manag. 2017;148:68–77. doi:10.1016/j.enconman.2017.04.045. [Google Scholar] [CrossRef]
28. Ersöz MA. Effects of different working fluid use on the energy and exergy performance for evacuated tube solar collector with thermosyphon heat pipe. Renew Energy. 2016;96:244–56. doi:10.1016/j.renene.2016.04.058. [Google Scholar] [CrossRef]
29. Mameli M, Besagni G, Bansal PK, Markides CN. Innovations in pulsating heat pipes: from origins to future perspectives. Appl Therm Eng. 2022;203(4):117921. doi:10.1016/j.applthermaleng.2021.117921. [Google Scholar] [CrossRef]
30. Salarnia M, Toghraie D, Fazilati MA, Mehmandoust B, Pirmoradian M. Pirmoradian The effects of different nanoparticles on physical and thermal properties of water in a copper oscillating heat pipe via molecular dynamics simulation. J Taiwan Inst Chem Eng. 2023;143(1):104721. doi:10.1016/j.jtice.2023.104721. [Google Scholar] [CrossRef]
31. Patel VM, Gaurav, Mehta. HB. Influence of working fluids on startup mechanism and thermal performance of a closed loop pulsating heat pipe. Appl Therm Eng. 2017;110(1):1568–77. doi:10.1016/j.applthermaleng.2016.09.017. [Google Scholar] [CrossRef]
32. Qu J, Wu HY, Cheng P. Thermal performance of an oscillating heat pipe with Al2O3-water nanofluids. Int Commun Heat Mass Transf. 2010;37(2):111–5. doi:10.1016/j.icheatmasstransfer.2009.10.001. [Google Scholar] [CrossRef]
33. Chang C, Pei L, Li B, Han Z, Ji Y. Fabrication and thermal performance of a solar-driven heat pipe filled with reduced graphene oxide nanofluids. Sol Energy. 2023;264(10):112007. doi:10.1016/j.solener.2023.112007. [Google Scholar] [CrossRef]
34. Riehl RR, Murshed SMS. Performance evaluation of nanofluids in loop heat pipes and oscillating heat pipes. Int J Thermofluids. 2022;14(1):100147. doi:10.1016/j.ijft.2022.100147. [Google Scholar] [CrossRef]
35. Dehaj MS, Ahmadi M, Mohiabadi MZ. Assessment of a heat pipe solar collector with nanofluids. Environ Sci Pollut Res. 2021;28(5):5316–31. doi:10.1007/s11356-020-10797-x [Google Scholar] [PubMed] [CrossRef]
36. Alizadeh H, Ghasempour R, Shafii MB, Ahmadi MH, Yan W, Nazari MA. Numerical simulation of PV cooling by using single turn pulsating heat pipe. Int J Heat Mass Transf. 2018;127:203–8. doi:10.1016/j.ijheatmasstransfer.2018.06.108. [Google Scholar] [CrossRef]
37. Novoselov KS, Blake P, Katsnelson MI. Graphene: electronic properties. Encyclopedia Mater Sci Technol. 2008; 1–6. [Google Scholar]
38. Huang P, Li Y, Yang G, Li Z, Li Y, Hu N, et al. Graphene film for thermal management: a review. Nano Mater Sci. 2021;3(1):1–16. doi:10.1016/j.nanoms.2020.09.001. [Google Scholar] [CrossRef]
39. Natesan K, Karinka S. A comprehensive review of heat transfer enhancement of heat exchanger, heat pipe and electronic components using graphene. Case Stud Therm Eng. 2023;45(7):102874. doi:10.1016/j.csite.2023.102874. [Google Scholar] [CrossRef]
40. Qu J, Zhao J, Rao Z. Experimental investigation on thermal performance of multi-layers three-dimensional oscillating heat pipes. Int J Heat Mass Transf. 2017;115:810–9. doi:10.1016/j.ijheatmasstransfer.2017.08.082. [Google Scholar] [CrossRef]
41. Thompson SM, Cheng P, Ma HB. An experimental investigation of a three-dimensional flat-plate oscillating heat pipe with staggered microchannels. Int J Heat Mass Transf. 2011;54(17–18):3951–9. doi:10.1016/j.ijheatmasstransfer.2011.04.030. [Google Scholar] [CrossRef]
42. Ling Y, Zhang X, Wang F, She X. Performance study of phase change materials coupled with three-dimensional oscillating heat pipes with different structures for electronic cooling. Renew Energy. 2020;154(5):636–49. doi:10.1016/j.renene.2020.03.008. [Google Scholar] [CrossRef]
43. Jung J, Jeon Y. Numerical study on the heat transfer characteristics of three-dimensional pulsating heat pipe. J Mech Sci Technol. 2023;37(9):4869–76. doi:10.1007/s12206-023-0839-1. [Google Scholar] [CrossRef]
44. Dai Y, Zhang R, Qin Z, Liu K, Liu C, Zhao J. Research on heat transfer performance and optimization of three-dimensional array pulsating heat pipe. 2023. doi:10.2139/ssrn.4478684. [Google Scholar] [CrossRef]
45. Kargaran M, Goshayeshi HR, Pourpasha H, Chaer I, Heris SZ. An extensive review on the latest developments of using oscillating heat pipe on cooling of photovoltaic thermal system. Therm Sci Eng Progress. 2022;36(6):101489. doi:10.1016/j.tsep.2022.101489. [Google Scholar] [CrossRef]
46. Zhang D, He Z, Guan J, Tang S, Shen C. Heat transfer and flow visualization of pulsating heat pipe with silica nanofluid: an experimental study. Int J Heat Mass Transf. 2022;183(5):122100. doi:10.1016/j.ijheatmasstransfer.2021.122100. [Google Scholar] [CrossRef]
47. Chen FC, Hu ML, Badiei A, Yu M, Huang ZC, Wang ZY, et al. Experimental and numerical investigation of a novel photovoltaic/thermal system using micro-channel flat loop heat pipe (PV/T-MCFLHP). Int J Low Carbon Technol. 2020;15(4):513–27. doi:10.1093/ijlct/ctaa019. [Google Scholar] [CrossRef]
48. Alexander K, Gajghate SS, Katarkar AS, Majumder A, Bhaumik S. Role of nanomaterials and surfactants for the preparation of graphene nanofluid: a review. Mater Today: Proc. 2021;44:1136–43. doi:10.1016/j.matpr.2020.11.231. [Google Scholar] [CrossRef]
49. Praveenkumar S, Gulakhmadov A, Agyekum EB, Alwan NT, Velkin VI, Sharipov P, et al. Experimental study on performance enhancement of a photovoltaic module incorporated with CPU heat pipe—a 5E analysis. Sensors. 2022;22(17):6367. doi:10.3390/s22176367 [Google Scholar] [PubMed] [CrossRef]
50. Zhang XX, Zhao XD, Smith S, Xu JH, Yu XT. Review of R&D progress and practical application of the solar photovoltaic/thermal (PV/T) technologies. Renew Sustain Energ Rev. 2012;16(1):599–617. doi:10.1016/j.rser.2011.08.026. [Google Scholar] [CrossRef]
51. Chandrika VS, Karthick A, Kumar NM, Kumar PM, Stalin B, Ravichandran M. Experimental analysis of solar concrete collector for residential buildings. Int J Green Energy. 2021;18(6):615–23. doi:10.1080/15435075.2021.1875468. [Google Scholar] [CrossRef]
52. Agyekum EB, PraveenKumar S, Alwan NT, Velkin VI, Shcheklein SE, Yaqoob SJ. Experimental investigation of the effect of a combination of active and passive cooling mechanism on the thermal characteristics and efficiency of solar PV module. Inventions. 2021;6(4):63. doi:10.3390/inventions6040063. [Google Scholar] [CrossRef]
53. Hassan A, Abbas S, Yousuf S, Abbas F, Amin NM, Ali S, et al. An experimental and numerical study on the impact of various parameters in improving the heat transfer performance characteristics of a water based photovoltaic thermal system. Renew Energy. 2023;202:499–512. doi:10.1016/j.renene.2022.11.087. [Google Scholar] [CrossRef]
54. Fouad MM, Shihata LA, Morgan EI. An integrated review of factors influencing the perfomance of photovoltaic panels. Renew Sustain Energ Rev. 2017;80(1):1499–1511. doi:10.1016/j.rser.2017.05.141. [Google Scholar] [CrossRef]
55. Xu RD, Ni K, Hu YH, Si JK, Wen HQ, Yu DS. Analysis of the optimum tilt angle for a soiled PV panel. Energy Convers Manag. 2017;148(9):100–9. doi:10.1016/j.enconman.2017.05.058. [Google Scholar] [CrossRef]
56. Kargaran M, Goshayeshi HR, Saleh SR, Zahmatkesh I, Chaer I. Cooling effect of 3D oscillating heat pipe with nanofluid on photovoltaic panel in hot climates. Multiscale Multi Mod. 2024;7(4):1–11. doi:10.1007/s41939-024-00394-7. [Google Scholar] [CrossRef]
Cite This Article
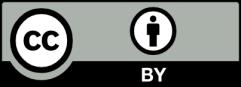
This work is licensed under a Creative Commons Attribution 4.0 International License , which permits unrestricted use, distribution, and reproduction in any medium, provided the original work is properly cited.