Open Access
ARTICLE
Recovery of Solid Oxide Fuel Cell Waste Heat by Thermoelectric Generators and Alkali Metal Thermoelectric Converters
College of Science, Heilongjiang Bayi Agricultural University, Daqing, 163319, China
* Corresponding Author: Wenxia Zhu. Email:
Frontiers in Heat and Mass Transfer 2024, 22(5), 1559-1573. https://doi.org/10.32604/fhmt.2024.047351
Received 03 November 2023; Accepted 21 December 2023; Issue published 30 October 2024
Abstract
A Solid Oxide Fuel Cell (SOFC) is an electrochemical device that converts the chemical energy of a substance into electrical energy through an oxidation-reduction mechanism. The electrochemical reaction of a solid oxide fuel cell (SOFC) generates heat, and this heat can be recovered and put to use in a waste heat recovery system. In addition to preheating the fuel and oxidant, producing steam for industrial use, and heating and cooling enclosed rooms, this waste heat can be used for many more productive uses. The large waste heat produced by SOFCs is a worry that must be managed if they are to be adopted as a viable option in the power generation business. In light of these findings, a novel approach to SOFC waste heat recovery is proposed. The SOFC is combined with a “Thermoelectric Generator and an Alkali Metal Thermoelectric Converter (TG-AMTC)” to transform the excess heat generated by both the SOFC and the TG-AMTC. The proposed TG-AMTC is evaluated using a number of performance indicators including power density, operating temperature, heat recovery rate, exergetic efficiency, energy efficiency, and recovery time. The experimental results state that TG-AMTC has provided an exergetic efficiency, energetic efficiency, and recovery time of 97%, 98%, and 23%, respectively. The study proves that the proposed TG-AMTC for SOFC is an efficient method of recovering waste heat.Keywords
SOFCs are machines that use an electrochemical process to transform chemical energy directly into electrical energy. Hydrogen or hydrocarbon fuels, such as methane, are often used as an energy source in SOFCs. Waste is created during the production of power and takes the forms of heat, carbon dioxide, water vapor, and unreacted fuel. Waste from SOFCs is a major issue since it has the potential to affect both the cost of energy generation as a whole and the fuel cell’s efficiency. Researchers are investigating several approaches for controlling and decreasing solid oxide fuel cell waste, including enhancing the fuel cell’s architecture and creating more effective and affordable recycling and disposal techniques [1]. Thermal waste or chemical waste are two categories that apply to this waste. Thermal waste is the extra heat produced while the fuel cell is operating that may be caught and utilized for other things, like heating or cooling. Carbon dioxide and unreacted fuel that is not turned into electrical energy are examples of chemical waste that has to be appropriately disposed of or recycled. In comparison to other fuel cell designs, SOFCs offer several benefits, including high efficiency, minimal emissions, and the capacity to burn a range of fuels. The decision is, heat recovery and the co-generation of heat and electricity are made possible more effectively. They can also work at extremely high temperatures. For a range of uses, including fixed power production for homes and businesses and portable power sources for military and off-the-grid applications, SOFCs are being developed [2]. Thermoelectric generators (TGs) are machines that produce electricity directly from heat. They make use of the Seebeck effect, which is the formation of an electric potential difference when a temperature differential is applied across two distinct kinds of materials. Thermoelectric generators are normally made up of several thermoelectric modules, which are built of pairs of p and n-type semiconductors that are electrically paired in a thermocouple arrangement. TGs may be used for a variety of useful purposes, including supplying power to spacecraft, operating sensors in distant areas, and recovering waste heat from industrial operations. TGs are advantageous in that they are portable, strong, and dependable, which makes them perfect for uses where conventional power sources would not be practical. The potentials and limitations of each use are briefly discussed at the beginning of each section to make the applications of thermoelectric generators more understandable. The benefits, difficulties, and overall viability of using TGs in various applications are then elaborated on [3]. The chemical energy of fuels like hydrogen or natural gas may be converted into electricity using SOFCs, which have a high conversion efficiency and emit few greenhouse gases in the process. To guarantee optimal operation and avoid system damage, waste heat from SOFCs must be handled, just as it does with any energy conversion process. The use of TGs is one method of controlling the waste heat produced by SOFCs. Temperature-energy generating devices, or TGs, are solid-state components. They work by using the Seebeck phenomenon, which produces a voltage when a temperature gradient is present. As a result, TGs may be used to collect the waste heat produced by SOFCs and transform it into extra electrical power, which can be utilized to raise the system’s overall effectiveness [4]. Multiple studies have concentrated on improving thermoelectric material properties, such as the Seebeck coefficient, electrical resistivity, and thermal conductivity, to increase the efficiency of TGs. As an alternative, TGs may be cascaded into a two-stage configuration, allowing for the further conversion of top-stage TGs’ rejected heat into electricity by the addition of bottom-stage TGs [5]. TGs are superior to other waste heat recovery systems in a variety of ways. They are dependable and low-maintenance since they are absent of any moving components. In addition to being lightweight and simple to install into the SOFC system, they are also small. TGs are excellent for use with SOFCs because they have a long operating lifespan and can function over a broad temperature range. The temperature differential across the device puts a limit on the quantity of electricity that can be produced by TGs, which usually have poor conversion efficiency. This implies that a big temperature differential must exist to create significant quantities of electricity, which may not always be achievable. TGs may also increase the price of the SOFC system, and their complexity and extra parts may reduce the system’s overall efficiency [6]. AMTCs are machines that use the thermoelectric effect to change heat energy into electrical energy. The thermionic emission theory underlies AMTC technology, in which electrons are released from a heated surface and captured by a colder surface. The working fluid for AMTCs is a ceramic tube that is vaporized with an alkali metal, such as sodium or potassium. The alkali metal vapor is heated on one side of the tube, which ionizes it and causes a flow of charged particles. After passing through a sequence of electrodes, the charged particles produce a voltage differential that may be used to generate electrical energy. Since they are so effective, AMTCs can turn up to 50% of the thermal energy they receive into electricity. Numerous applications, including solar power systems, waste heat recovery, and space power systems, are possible for them [7]. Waste heat from SOFCs may be recovered using TGs and AMTCs. The operating temperature of SOFC and needed output power, however, determine which device should be used. TGs are often better suited for applications requiring lower temperatures, while AMTCs are better suited for applications requiring higher temperatures. When waste heat from SOFCs is recovered using TGs and AMTCs, the system’s overall efficiency may be raised while its environmental effect is decreased [8].The process of collecting and using the thermal energy produced as a by-product of SOFC operation is referred to as the recovery of SOFC waste heat. Due to the temperature differential between the hot fuel cell stack and the colder surrounding environment, SOFCs produce waste heat. Thermoelectric generators or alkali metal thermoelectric converters can collect this waste heat and transform it into usable power. The recovery of waste heat from SOFCs using TGs and AMTCs has shown promise, but there are still obstacles to be cleared before these technologies are more efficient, dependable, and cost-effective [9]. The need for the creation of effective and sustainable energy technologies has risen due to global energy and environmental crises. Fuel cells are attractive sources of energy because they can transform fuel chemical energy into electricity effectively and sustainably without the need for intermediate, time-consuming energy conversion procedures. SOFCs, a kind of fuel cell, have generated a great deal of attention because of their fewer emissions, fuel adaptability, inexpensive metal catalysts, and quickly occurring electrochemical reactions. In the review, several SOFC heat recovery methods have been presented and studied; nonetheless. In light of this objective, the present work proposes a unique pairing in which an AMTC and a TG are taken into account as joining an SOFC [10]. SOFCs produce a significant amount of excess heat, which is frequently not fully employed. The efficient retrieval of this waste temperature presents challenges in terms of low conversion efficiency and materials constraints when employing thermoelectric generators (TEGs) and AMTECs. Revolutionary chemical investigation and engineering developments have the potential to improve the performance of TEG and AMTEC. Enhancing the thermal resistance of substances and optimizing the combination of systems can enhance overall efficiency, thereby making the usage of waste thermal from SOFCs more feasible and economically acceptable.
Contribution of the study:
• The industry is still conducting research and development on waste heat recovery, but it is a crucial strategy for improving the sustainability and energy efficiency of SOFC systems.
• In order to reuse the energy that would otherwise be wasted in a cells SOFC, we implemented a TG-AMTC in this investigation.
• The data has been collected from the thermoelectric plants around Beijing.
• Existing technologies such as the Brayton cycle heat engine (BCHE), the “SOFC system equipped with a gas turbine and organic Rankine cycle (SOFC-GT-ORC)”, and the marine diesel engine (MDE) are used to make comparisons in terms of performance metrics such as power density, operating temperature, heat recovery rate, exergetic efficiency, energetic efficiency, and recovery time.
• The findings show that the proposed approach has the potential to greatly boost SOFC system efficiency in general.
2 Application of Solid Oxide Fuel Cell
Reference [11] explored the hybrid system’s overall performance traits and ideal parameter designs, a thorough numerical model of the system is created. The “hybrid system” performs superior to other AFC system-based hybrids that have been previously presented, indicating the TRD has a greater effective capture of the “waste heat” generated by AFC than other traditional combination equipment. Reference [12] has evaluated and addressed the use of NFs in FCs for waste heat recovery and heat management. The effectiveness of NFs as FC coolants has been shown. The thermal efficiency of the FC is almost doubled while the dimensions of the chilling device are reduced when NFs are included. Over the last several years, fuel cells have drawn growing interest as sustainable power conversion technologies. With the great power transformation effectiveness of FC, a significant portion of the generated power is still eliminated as “waste heat”. The goal of the work [13] is to present and conceptually develop a unique energy process based on thermionic and thermoelectric generators and SOFCs.The SOFC converts the chemical energy present in the fuel into electrical energy. The thermoelectric interface (TI) harnesses the waste heat from the SOFC to provide additional electrical power. To generate more power, TE is linked thermally to the TI. As downstream and intermediate cycles, consequently, the TE and TI profit. The concept increases the use of waste heat and improves system effectiveness. In the work [14], a combined structure in the form of an integrated mechanism for electricity, heating, and cooling is explored relative to its energy, exergy, and thermodynamic analysis. The system that is suggested comprises an additional absorption chiller to meet the requirement for cooling as well as an SOFC to give electrical and thermal energy. It also includes steam power turbines to generate extra electrical power. In the work [15], the simulation and evaluation of a cutting-edge integrated co-generation system that produces power while converting heat and includes a biomass gasifier, an SOFC module, and a heat recovery steam generator are performed. The efficiencies and costs of the suggested system have been assessed. It is possible to overcome the multifaceted issues of degradation of the environment, reliability of energy, and depletion of traditional reserves of fossil fuels by using sources of clean energy efficiently. The research [16] compared a stand-alone SOFC system to configurations that include a gas engine, steam generator, and a unique SOFC-mixed cycle powered by a reciprocating engine. Electricity may be produced from natural gas in a tidy and effective manner with the help of SOFC technology. It is fascinating to examine that they stack up because other integration strategies with heat cycles have been suggested to attain even better electrical efficiency. Additionally, it has not yet been sufficiently addressed how the SOFC operating settings affect heat cycles. The goal [17] described was to harness the waste heat and enhance cooling capabilities, a thermoacoustically-driven cryocooler could be connected to an SOFC. The overall effectiveness attributes for such a hybrid system are established from the efficiency indicators measuring a range of irrevocable inefficiencies. The long-term stability of an SOFC during operation is severely impacted by heat build-up. There may be two advantages to using waste heat in further applications. The study [18] developed and examined a novel hybrid system for applications that combine cooling and electricity. The heat created in the PAFC is utilized by TG to get more energy out of the ground, whilst the exhaust heat from the PAFC is used to supply chilling power. Additionally, they discovered that the quality of the presentation is improved when the TG consumes less heat and the AC utilizes the majority of the useable heat. The study [19] presented a “solid oxide fuel cell (SOFC)” with a “graphene-collector thermionic energy converter (GTEC)”. In the framework, GTEC captured the high-quality waste temperature generated by the SOFC and produced additional power. Their investigation offered essential fundamental information on the best configurations and parameterized examination of SOFC-GTEC hybrid systems, hence facilitating the development of high-efficiency SOFC power generation technologies. The study [20] developed MCFC-GCTG, had been to effectively harness the high-quality waste heat generated by MCFC for the simultaneous production of electricity. The MCFC-GCTG exhibits superior performances compared to other hybrid technologies based on MCFCs, indicating that GCTG was more efficient in utilizing the waste heat generated by MCFCs than alternative heat-recovering techniques.
For this study, the data has been collected from thermoelectric plants around Beijing. Recovering waste heat may assist the SOFC system’s dependability and durability. As it enables the recovery of energy that would otherwise be dissipated as heat, it greatly improves the system’s overall efficiency. This may therefore result in less fuel being used and cheaper operational expenses. In consideration of this, we suggested the “thermoelectric generator and an alkali metal thermal electric converter (TG-AMTC)”. Fig. 1 represents the proposed model of this study.
Figure 1: Proposed model
In this system, fuel is fed into the SOFC and transported to the anode electrode, where it undergoes molecular and electrical processes to generate energy. The AMTC is divided into higher-pressure and heat and less-pressure and heat zones using a solid alumina electrolyte (SAE). The SAE, which is defined as having a greater ion conductance than electrical conductance, is crucial to the construction of the AMTC. The AMTC receives the sodium high-pressure vapor from the initial section. The second zone, which has stresses below 90 Pa and heats between 300 and 900 k, also receives low-pressure vapor sodium. The “sodium ions” are sent to the cathode electrode by the pressure change, and the divided electrons are received by the anode electrode. Moreover, isolated electrons are employed in an open circuit to provide electricity power. As a result, the condenser condenses the sodium vapor, which the pump then sends to the topmost portion of the AMTC for recovery. Moreover, the TG is made up of m thermocouples that are serially connected utilizing the bismuth telluride (Bi2Te3) material. These thermocouples are made of two semiconductors P-type and N-type combined together by a thin copper wire.
The source heat of the AMTC is calculated using Eq. (1) per the previously discussed conceptual model. In this, be; AMTC is the electrode region, Dp is the mean precise heat potential of liquid sodium represents the molecular mass of sodium, K represents the heat required for evaporation, z represents the component responsible for radioactive reduction, and Q represents the value of Stefan-Boltzmann.
Qin.AMTC=QG=jBe,AMTCDp(SG−Sh)NE+jBe,AMTECDp(SG−Sh)NK/E+σBe,AMTCσBe,AMTEC(S4G−S4h)/z(1)
After,
UAMTC=1eIn(1+Os(SG)λCQSG)−Uac−UQ(2)
where g and Os define in Eqs. (3) and (4).
e=EQSG(3)
Os(SG)=109.575−5243.1/SG(4)
where C is the SAE’s depth, Vac is the AMTC’s voltage drop, and UR is the SAE voltage of its ions.Uac=−2eIn((12j2SGAOsat(SG)+4)0.5−12(j√SG2AOsat(SG)))(5)
UW=jC(1.53×10−5SGexp(−44.6SG)+1.46×10−7(3655SG))(6)
where A is the temperature-independent interchange power factor, and ΔOcd is the pressure drop, described in Eq. (7).ΔOcd=(1+3H8π)√2πNQSGj2E(7)
H is the geometrical constant. The calculations 8, 9, 10, and 11 are utilized to calculate the “power density (PE)”, efficiency of the “energetic and exergetic (EE)” capacities, and densities of the transpiration proportions of the AMTC.
O∗AMTC=OA,MTCBc,SOFC=IAMTCUAMTCBc,SOFC(8)
ηAMTEC=OA,MTECQin,AMTEC(9)
φAMTEC=OA,MTECQin,AMTEC(1−S0Sg)(10)
ExD∗ΔMTEC=Pin,AMTEC(1−S0Sg)−PAMTECBc,SOFC(11)
Bi2Te3 is chosen as the thermoelectric material, as previously mentioned; its characteristics include the SeeBeck factor (a), thermal conductance (q), electrical resistance (j), and temperature average is defined in Eq. (12).
Savg=Sg−Sc2(12)
The Thomson impact (τ), shown in Eq. (13), may be disregarded while the temperature is fixed.
τ=T∂α∂S(13)
Nevertheless, τ is used as in Eq. (14) with relation to Eqs. (11) and (13).
τ=2×(925.6Savg−1.874S2avg)×10−9(14)
Thus, Eqs. (15) and (16) are used to determine the heat that the Sg receives and the heat that it produces.
Pg=m(∝1ITEGSc−ITEG2Qg/2+L(Sg−Sc)−τ1ITEG(Sg−Sc)−τ1ITEG(Sg−Sc)/2(15)
PD=m(∝2ITEGSc−ITEG2Qg/2+L(Sg−Sc)−τ2ITEG(Sg−Sc)−τ2ITEG(Sg−Sc)/2(16)
where the upper end and bottom end of the Sg are indicated by a1 and s1, and a2 and s2, correspondingly. Hence, Eqs. (17) and (18) are used to determine a thermocouple’s heat conductivity (K) and electrical resistivity (Qg).L=(lOTOKo+ρMkmKM)+Lcont+Lcond(17)
Qh=(ρOTOTo+ρMkMTM)+Qcont+Qcond(18)
As a result, Eq. (19)’s resultant electrical energy for the Sg is as follows:
OTG=Rg−RC(19)
OTG=ITG(∝1Sg−∝2Sc−ITGQg−(Sg−Sc)(τ1+τ2)/2)(20)
The given calculations calculate the PD, efficiency of the EE capacities, and the maximum of the transpiration ratios of the Sg.
O∗TG=OTGBc,SOFC(21)
ηTG=OTGRh,(22)
φTG=OTGTh(1−S0Sc)(23)
ExD∗TG=Rh(1−S0Sc)−OTGBc,SOFC(24)
A technology with tremendous potential for generating power with minimal emissions and high efficiency is the solid oxide fuel cell (SOFC). Unfortunately, they also produce a substantial quantity of waste heat while in use. As a result, we developed a “thermoelectric generator and an alkali metal thermal electric converter (TG-AMTC)” to recover waste heat in SOFC. In this part, many performance indicators, including power density, operating temperature, heat recovery rate, exergetic efficiency, energetic efficiency, and recovery time, are assessed and discussed. Brayton cycle heat engine (BCHE) [21], SOFC system equipped with a gas turbine and organic Rankine cycle (SOFC-GT-ORC), and marine diesel engine (MDE) [22] are used for comparison.
SOFCs produce electricity with high efficiency. However, the excess heat they generate can be utilized by thermoelectric generators (TEGs) to increase the overall power density. In addition, alkali metal thermoelectric converters (AMTECs) provide an alternative method. The system maximizes energy conversion efficiency by utilizing the temperature differential to generate additional power through the integration of TEGs or AMTECs with SOFCs. This combination of synergistic elements optimizes power density, providing a promising pathway for promoting clean energy technologies and enhancing the durability of power generation networks. When compared to the current system, the recommended technique provides a greater range, due to the power densities of SOFCs, which ranged from 0.1 to 1.0 W/cm2. Fig. 2 shows the power density of the proposed methodology and existing techniques. Table 1 shows the outcomes of the power density. In comparison to existing methods, the suggested approach offers a high level of power density.
Figure 2: Power density of the proposed and existing methodologies
Typically, these systems function within a temperature range of 600°C–1000°C, generating waste heat of excellent quality. Thermoelectric generators (TEGs) may effectively utilize this excess heat to produce extra electrical power. Alkali metal thermoelectric converters, which are a form of thermoelectric generator (TEG), are capable of functioning at comparable temperatures. These systems gain advantages from their ability to operate at elevated temperatures, which improves the total energy effectiveness by turning wasted heat into valuable electrical power. As a result, they are considered potential technology for sustainability and effective energy conversion in a wide range of applications. Fig. 3 shows the operating temperature of the proposed methodology and existing techniques. Table 2 shows the outcomes of the operating temperature. In comparison to existing methods, the suggested approach offers a low level of operating temperature.
Figure 3: Operating temperature of the proposed and existing methodologies
The heat recovery rate for waste heat from SOFC using thermoelectric generators and alkali metal thermoelectric converters is a critical factor in achieving high energy productivity. By utilizing these methods, a significant proportion of the excess heat produced in solid oxide fuel cells can be captured and transformed into electrical energy. By employing this dual strategy, the total efficiency of the system is improved, which in turn promotes efficient energy practices and reduces heat losses. The incorporation of thermoelectric generators with alkali metal converters enhances heat consumption, hence facilitating a more efficient and sustainable energy generation process. Fig. 4 shows the heat recovery rate of the proposed and existing techniques. Table 3 shows the outcomes of the heat recovery rate. In comparison to existing methods, the suggested approach offers a high level of heat recovery rate.
Figure 4: Heat recovery rate of the proposed and existing methodologies
The exergetic effectiveness of solid oxide fuel cell waste heat recovery is of essential importance for the sustainability of energy structures, particularly when utilizing thermoelectric generators and alkali metal thermoelectric converters. These technologies strive to optimize the transformation of waste heat into power that may be used, hence improving the total performance of the systems. SOFC produces waste heat at elevated temperatures, which can be utilized by thermoelectric generators or alkali metal thermoelectric converters. This assists optimize energy usage and reduce environmental effect in a consistent method. Fig. 5 shows the exergetic efficiency of the proposed and existing techniques. Table 4 shows the outcomes of the exergetic efficiency. In comparison to existing methods, the suggested approach offers a high level of exergetic efficiency.
Figure 5: Exergetic efficiency of the proposed and existing methodologies
To increase the energy efficiency of solid oxide fuel cells (SOFCs), technologists are investigating into thermoelectric converters and thermoelectric generators made of alkali metals. Converting the normally wasted heat from SOFCs into power is the purpose of these techniques. There is hope for more efficient and ecologically responsible power generation methods in the form of thermoelectric generators and alkali metal converters, which have the potential to maximize energy extraction. Fig. 6 shows the energy efficiency of the proposed and existing techniques. Table 5 shows the outcomes of the energetic efficiency. In comparison to existing methods, the suggested approach offers a stronger energetic efficiency.
Figure 6: Energetic efficiency of the proposed and existing methodologies
The utilization of the waste heat recovery method is significantly enhanced by the implementation of thermoelectric generators and alkali metal thermoelectric converters. The SOFC generates elevated temperatures and waste heat, which is utilized by thermoelectric generators and alkali metal thermoelectric converters to provide extra energy. These devices harness temperature differences to generate electrical power, so increasing the effectiveness of the entire system by collecting and transforming the heat that would otherwise be wasted into usable energy. This maximizes the electricity production of the SOFC systems. Fig. 7 shows the recovery time of the proposed methodology and existing techniques. Table 6 shows the outcomes of the recovery time. In comparison to existing methods, the suggested approach offers a low level of recovery time.
Figure 7: Recovery time of the proposed and existing methodologies
SOFC has the potential to be used in a variety of applications, some of which include the production of electricity for stationary and mobile applications as well as for combined heat and power systems. They are also being researched for their possible use in reversible SOFC-based hydrogen and other fuel generation. Despite their numerous benefits, SOFCs are still somewhat costly and difficult to produce. Ongoing research aims to decrease these costs and increase SOFCs’ cost-effectiveness and durability to make them more competitive with other energy technologies. Waste heat recovery is a key tactic for optimizing the sustainability and energy efficiency of SOFC systems and is still being researched and developed in the industry. As a result, we introduced a thermoelectric generator as well as a TG-AMTC to recover waste heat in SOFC. Performance metrics like power density (0.96 W/cm2), operating temperature (610°C), heat recovery rate (94%), exergetic efficiency (97%), energetic efficiency (98%), and recovery time (23 s) are evaluated and compared with existing technologies like the BCHE, SOFC-GT-ORC and MDE. The results demonstrate that the suggested strategy may significantly increase overall SOFC system efficiency. To improve performance, additional innovative strategies might be applied to the suggested system in further studies.
Acknowledgement: Not applicable.
Funding Statement: Fund Project: Foundation of Heilongjiang Bayi Agricultural University (Grant Nos. ZRCPY201916; ZRCPY201817).
Author Contributions: The authors confirm contribution to the paper as follows: study conception and design: Wenxia Zhu, Baishu Chen, Lexin Wang, Chunxiang Wang; data collection: Lexin Wang; analysis and interpretation of results: Baishu Chen; draft manuscript preparation: Wenxia Zhu. All authors reviewed the results and approved the final version of the manuscript.
Availability of Data and Materials: There is no unavailable data in this study.
Ethics Approval: Not applicable.
Conflicts of Interest: The authors declare that they have no conflicts of interest to report regarding the present study.
References
1. Lin G, Wang X, Rezazadeh A. Electrical energy storage from a combined energy process based on solid oxide fuel cell and use of waste heat. Sustain Energy Technol Assess. 2021;48:101663. doi:10.1016/j.seta.2021.101663. [Google Scholar] [CrossRef]
2. Zoui MA, Bentouba S, Stocholm JG, Bourouis M. A review on thermoelectric generators: progress and applications. Energies. 2020;13(14):3606. doi:10.3390/en13143606. [Google Scholar] [CrossRef]
3. Emadi MA, Chitgar N, Oyewunmi OA, Markides CN. Working-fluid selection and thermoeconomic optimisation of a combined cycle cogeneration dual-loop organic Rankine cycle (ORC) system for solid oxide fuel cell (SOFC) waste-heat recovery. Appl Energy. 2020;261:114384. doi:10.1016/j.apenergy.2019.114384. [Google Scholar] [CrossRef]
4. Tohidi F, Holagh SG, Chitsaz A. Thermoelectric generators: a comprehensive review of characteristics and applications. Appl Therm Eng. 2022;201:117793. doi:10.1016/j.applthermaleng.2021.117793. [Google Scholar] [CrossRef]
5. Olabi AG, Al-Murisi M, Maghrabie HM, Yousef BA, Sayed ET, Alami AH, et al. Potential applications of thermoelectric generators (TEGs) in various waste heat recovery systems. Int J Thermofluids. 2022;16:100249. doi:10.1016/j.ijft.2022.100249. [Google Scholar] [CrossRef]
6. Liu J, Peng W, Zhang H. Performance evaluation of a hybrid alkali metal thermal electric converter-two stage thermoelectric generator system. Appl Therm Eng. 2021;191:116820. doi:10.1016/j.applthermaleng.2021.116820. [Google Scholar] [CrossRef]
7. Chen S, Zhang H, Wang F, Miao H, Zhao J, Zhang C, et al. Maximum power density analyses of a novel hybrid system based upon solid oxide fuel cells, vacuum thermionic generators, and thermoelectric generators. Int J Hydrog Energy. 2021;46(42):22062–78. doi:10.1016/j.ijhydene.2021.04.011. [Google Scholar] [CrossRef]
8. Hadelu LM, Noorpoor A, Boyaghchi FA. Novel hybrid two-stage alkali metal thermoelectric converter and thermally regenerative electrochemical cycle to exploit waste heat of solid oxide fuel cell: performance assessment and optimization. Int J Hydrog Energy. 2022;47(56):23797–817. doi:10.1016/j.ijhydene.2022.05.159. [Google Scholar] [CrossRef]
9. Yang Z, Ren X, Zhang H. A cost-efficient path to utilize coal via solid oxide fuel cells and alkali metal thermoelectric converters. Int J Energy Res. 2022;46(8):11109–22. doi:10.1002/er.7913. [Google Scholar] [CrossRef]
10. Jia Y, Sardari F. Study of employing a thermoelectric generator and an alkali metal thermal electric converter for waste heat recovery of a solid oxide fuel cell. Alex Eng J. 2023;69:403–18. doi:10.1016/j.aej.2023.01.023. [Google Scholar] [CrossRef]
11. Zhang X, Rahman E. Thermodynamic analysis and optimization of a hybrid power system using thermoradiative device to efficiently recover waste heat from alkaline fuel cell. Renew Energy. 2022;200:1240–50. doi:10.1016/j.renene.2022.10.038. [Google Scholar] [CrossRef]
12. Sayed ET, Abdelkareem MA, Mahmoud MS, Baroutaji A, Elsaid K, Wilberforce T, et al. Augmenting performance of fuel cells using nanofluids. Therm Sci Eng Prog. 2021;25:101012. doi:10.1016/j.tsep.2021.101012. [Google Scholar] [CrossRef]
13. Arshad A, Ali HM, Habib A, Bashir MA, Jabbal M, Yan Y. Energy and exergy analysis of fuel cells: a review. Therm Sci Eng Prog. 2019;9:308–21. doi:10.1016/j.tsep.2018.12.008. [Google Scholar] [CrossRef]
14. Peng MYP, Chen C, Peng X, Marefati M. Energy and exergy analysis of a new combined concentrating solar collector, solid oxide fuel cell, and steam turbine CCHP system. Sustain Energy Technol Assess. 2020;39:100713. doi:10.1016/j.seta.2020.100713. [Google Scholar] [CrossRef]
15. Karimi MH, Chitgar N, Emadi MA, Ahmadi P, Rosen MA. Performance assessment and optimization of a biomass-based solid oxide fuel cell and micro gas turbine system integrated with an organic Rankine cycle. Int J Hydrog Energy. 2020;45(11):6262–77. doi:10.1016/j.ijhydene.2019.12.143. [Google Scholar] [CrossRef]
16. Van Biert L, Woudstra T, Godjevac M, Visser K, Aravind PV. A thermodynamic comparison of solid oxide fuel cell-combined cycles. J Power Sources. 2018;397(7):382–96. doi:10.1016/j.jpowsour.2018.07.035. [Google Scholar] [CrossRef]
17. Guo Y, Zhang H, Xu J, Bahrami M. Evaluation on the waste heat recovery potential of thermoacoustically-driven cryocoolers for solid oxide fuel cells. Process Saf Environ Prot. 2023;170:771–82. doi:10.1016/j.psep.2022.12.039. [Google Scholar] [CrossRef]
18. Kiwan S, Radaideh MI. Investigation of a new hybrid fuel cell-ThermoElectric generator-absorption chiller system for combined power and cooling. Int J Refrig. 2020;113(37):103–14. doi:10.1016/j.ijrefrig.2020.02.010. [Google Scholar] [CrossRef]
19. Ding A, Sun H, Zhang S, Dai X, Pan Y, Zhang X, et al. Thermodynamic analysis and parameter optimization of a hybrid system based on SOFC and graphene-collector thermionic energy converter. Energy Convers Manag. 2023;291(1–2):117327. doi:10.1016/j.enconman.2023.117327. [Google Scholar] [CrossRef]
20. Sun H, Ding A, Gao F, Kong Y, Zhang X, Rahman E, et al. Efficient waste heat recovery from molten carbonate fuel cells through graphene-collector thermionic generators. Energy Convers Manag. 2024;299(11):117887. doi:10.1016/j.enconman.2023.117887. [Google Scholar] [CrossRef]
21. Yang Z, Zhang H, Ni M, Lin B. A hybrid system using Brayton cycle to harvest the waste heat from a direct carbon solid oxide fuel cell. Appl Therm Eng. 2019;160(3):113992. doi:10.1016/j.applthermaleng.2019.113992. [Google Scholar] [CrossRef]
22. Wang F, Wang L, Zhang H, Xia L, Miao H, Yuan J. Design and optimization of hydrogen production by solid oxide electrolyzer with marine engine waste heat recovery and ORC cycle. Energy Convers Manag. 2021;229(1–2):113775. doi:10.1016/j.enconman.2020.113775. [Google Scholar] [CrossRef]
Cite This Article
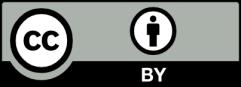
This work is licensed under a Creative Commons Attribution 4.0 International License , which permits unrestricted use, distribution, and reproduction in any medium, provided the original work is properly cited.