Open Access
ARTICLE
Optimization of Finned-Tube Heat Exchanger in a Gravity-Assisted Separated Heat Pipe
1 Huadong Engineering Corporation Limited, Power Construction Corporation of China, Hangzhou, 310014, China
2 Institute of Refrigeration and Cryogenics, Zhejiang University, Hangzhou, 310027, China
* Corresponding Author: Shaozhi Zhang. Email:
(This article belongs to the Special Issue: Computational and Numerical Advances in Heat Transfer: Models and Methods II)
Frontiers in Heat and Mass Transfer 2024, 22(4), 1209-1229. https://doi.org/10.32604/fhmt.2024.052415
Received 01 April 2024; Accepted 06 June 2024; Issue published 30 August 2024
Abstract
Finned-tube heat exchanger (FTHE) is often used as an evaporator in commercial products of separated heat pipe (SHP). The working conditions of FTHE in gravity-assisted SHP are significantly different from those working in refrigerators and air conditioners. Although FTHE is widely used in commercial products of SHP, previous research on its characteristics is very limited. In this paper, a mathematical model for a SHP with FTHE as the evaporator and plate heat exchanger as the condenser is established and verified with experiments. Parametric analyses are carried out to investigate the influences of evaporator design parameters: air inlet velocity, number of tube rows, tube diameter, and fin pitch. With the increasing of air velocity, number of tube rows and tube diameter, and the decreasing of fin pitch, the heat transfer rate increases, while the energy efficiency ratio (EER) decreases monotonically. Using the total cost of the ten-year life cycle as the performance index, the structure parameters of the evaporator with a given heat transfer rate are optimized by the method of orthogonal experimental design. It is found that the total cost can differ as large as nearly ten times between groups. Among the three factors investigated, the number of tube rows has a significant impact on the total cost of the evaporator. With more tube rows, the total cost will be less. The impacts of fin pitch and tube diameter are insignificant. These results are of practical importance for the engineering design of FTHE in gravity-assisted SHP.Keywords
Cite This Article
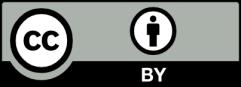
This work is licensed under a Creative Commons Attribution 4.0 International License , which permits unrestricted use, distribution, and reproduction in any medium, provided the original work is properly cited.