Open Access
ARTICLE
Impacts of Using Al2O3 Nano Particle to Compressor Oil on Performance of Automobile Air Conditioning System
1 Engineering Technical College of Mosul, Cultural Group, Northern Technical University, Mosul, 41002, Iraq
2 College of Engineering, AlNoor University, Mosul, 41002, Iraq
* Corresponding Author: Omar Rafae Alomar. Email:
Frontiers in Heat and Mass Transfer 2024, 22(3), 839-854. https://doi.org/10.32604/fhmt.2024.052671
Received 10 April 2024; Accepted 31 May 2024; Issue published 11 July 2024
Abstract
This work involves an experimental study on the performance of automobile air-conditioning systems by adding Al2O3 nanoparticles to oil compressors to investigate their impacts on the enhancement of the speed cooling of refrigeration systems and to compare it with the system operated using only oil. The Al2O3 nanoparticles have been added to the oil compressor for different ranges of mass concentration (Ø = 0.1%, Ø = 0.15% and Ø = 0.2%). The stability of Al2O3 nanoparticles has been tested by direct observation for different time periods. The results indicated that the air conditioning system that operated by using Al2O3-oil was better than the system that operated with pure oil. For Ø = 0.2%, the results indicated that the cooling speed and the efficiency of the system operated with Al2O3-oil are increased by 13% and 18%, respectively, as compared to the pure oil system. This study shows that the thermos-physical properties of refrigerant oil are enhanced by 15% when Ø is increased.Keywords
Nomenclature
ρp | Density of Nano atoms (kg/m3) |
ρf | Pure oil density (kg/m3) |
M | Weight (kg) |
mp | The nanoparticles weight (kg) |
Mf | Weight of oil (kg) |
m | Mass flow rate of the refrigerant (kg/s) |
Cp | Specific heat capacity of the refrigerant (J/kg.°C) |
Th | High temperature or heat source temperature (°C) |
Tc | Low temperature or heat sink temperature (°C) |
I | Input Amber to the system (Amber) |
V | Input voltage (Volt) |
K | Thermal conductivity (W/m.K) |
kn | Thermal conductivity of Nano-oil (W/m.K) |
kf | Pure oil thermal conductivity (W/m.K) |
μnf | The viscosity of the Nano-oil (Pa.s) |
μbf | The viscosity of the pure oil (Pa.s) |
Ø | Mass friction (%) |
Car air conditioning (AC) systems keep the interior of the vehicle at a pleasant temperature by absorbing heat and expelling it outside. They are common in the automotive industry for luxury, safety, and health reasons [1]. AC systems in cars have various applications in industry and academia. They are essential for providing a pleasant environment for drivers and passengers, transporting temperature-sensitive goods, and studying thermodynamic properties [2]. The utilization of AC systems has influenced climate change because of the refrigerants such as hydrofluorocarbons (HFCs) utilized, which add to the greenhouse effect. Advancements have led to the creation of environmentally friendly refrigerants such as hydrofluoric olefins (HFOs) [3]. AC Systems Using Water as a Working Fluid: Some AC systems use water as a working fluid, offering advantages like efficient heat transfer, high specific heat capacity, and environmental friendliness [4,5]. The use of monotype nanofluids in AC systems has attracted interest in boosting thermal conductivity and heat transfer characteristics, leading to enhanced cooling efficiency [6,7].
So, nanofluids have been proposed as potential working fluids in refrigeration systems due to their enhanced thermal conductivity and heat transfer properties. In recent years, several studies have been conducted to investigate the use of nanofluids in refrigeration systems. Okonkwo et al. [8] provided a comprehensive overview of the use of nanofluids in refrigeration systems. The investigation has discussed the different types of nano-particles used in refrigeration systems, their effects on the thermo-physical properties of the nanofluids and the performance of refrigeration systems using nanofluids. They concluded that the use of nano-fluids can significantly improve the performance of refrigeration systems. Utilizing Al2O3 as a coolant addition in automobiles in much their impact on the environment. It has been proven that the nano-sized Al2O3 particles increase the effectiveness of radiators that are used as heat exchangers. This results in an overall increment in heat transfer coefficients and the thermal efficiency of the engines [9–11]. The Al2O3 compound imposed in compressor oil amplifies the power of the air conditioning (AAC) cooling systems in vehicles. Increasing the Al2O3-SiO2/PAG composite nano-lubricant in the AAC system leads to better cooling, higher COP, easy compressor work, and, ultimately, less power requirement [12,13]. Hybrid nano-lubricants with Al2O3-SiO2/PAG at specific composition ratio, e.g., 60:40 over the investigation period of 40 h, the COP has been enhanced to a maximum of 16.31% and the compressor work has been decreased by 18.65%. Additionally, applying composite nano-lubricants and fuzzy modelling optimization also yields as much as an 88% increase in the AAC systems performance which is better than single-component nano-lubricants [14]. The use of Al2O3 nano-particles as a refrigerant additive showed a high efficiency improvement along with reducing the power consumption making Al2O3 a promising additive in improving the AAC system [15].
Husainy et al. [16] investigated the performance of a domestic refrigerator using R600a refrigerant and nanofluids containing copper oxide (CuO) and alumina (Al2O3) nano-particles. The results showed that the use of nanofluids improved the coefficient of performance (COP) of the refrigerator by up to 13%. Afolalu et al. [17] presented the performance of a vapour compression refrigeration system using carbon nano-tube-based nanofluids. The results showed that the use of nanofluids improved the COP of the system by up to 5.5% compared to the use of conventional refrigerants. Said et al. [18] investigated the effects of using alumina nanofluids in a domestic refrigerator. The results showed that the use of nanofluids improved the COP of the refrigerator by up to 8%. The study also reported that the use of nanofluids reduced the compressor power consumption by up to 12%. Sözen et al. [19] presented the effects of using nano refrigerants containing alumina and titanium dioxide nanoparticles on the performance of a domestic refrigerator. The results showed that the use of nano-refrigerants improved the COP of the refrigerator by up to 18%. Moreover, the use of nano-refrigerants reduced the compressor power consumption by up to 16%. Sanukrishna et al. [20] provided an overview of the use of nanofluids as refrigerants for low-temperature applications. The investigation has discussed the different types of nano-particles used in refrigeration systems, their effects on the thermo-physical properties of the nanofluids and the performance of refrigeration systems using nanofluids. The findings show that the use of nanofluids as refrigerants has the potential to significantly improve the performance of refrigeration systems. Jiang et al. [21] experimentally analyzed the performance of a vapour compression refrigeration system using Al2O3-R134a nanofluid. The results showed that the use of nano-fluids improved the performance of the refrigeration system by reducing compressor work by up to 13% and increasing the COP by up to 22%. Ajayi et al. [22] experimentally investigated the performance of a vapour compression refrigeration system using a nano-refrigerant consisting of R600a and copper oxide nanoparticles. The results showed that the use of nano-refrigerant improved the COP of the refrigeration system by up to 11.4%. Raja et al. [23] experimentally investigated the performance of a vapour compression refrigeration system using SiO2-R134a nano-refrigerant. The results showed that the use of nano-refrigerant improved the COP of the refrigeration system by up to 20% compared to the use of R134a. Adelekan et al. [24] experimentally evaluated the performance of a domestic refrigerator using nano-refrigerants containing aluminium oxide nanoparticles. The results showed that the use of nano-refrigerant improved the COP of the refrigerator by up to 8%. Nano-scale alumina oxide particles have demonstrated the potential as a coolant additive in the automobile air conditioning system, which can reduce energy consumption. Researchers have shown that when the Al2O3 nano-crystals are used in oil nano-composite, the heat transfer coefficient and the efficiency of the AAC system can considerably be increased [25,26]. On top of that, the nano refrigerants that contain Al2O3 nano-particles accelerate the heat transfer being far more efficient than existing technologies. That has the potential to decrease the amount of energy needed for operation [27,28]. Meanwhile, the use of Al2O3 nano-particles with suitable refrigerants was recorded to have better COP and energy savings as compared to the earlier results, which signifies strong positive impacts on energy efficiency [29]. Thus, applying that Al2O3 compound as a coolant additive gives clear evidence of the efficacy of the coolant system of the car air conditioner.
A full check in the open literature investigations reveal that there are some experimental and numerical investigations deal with refrigerating systems of car to improve their performances by modifying the system through using e.g., indirect evaporator cooler, evaporative water and heat pipe. The review on previous studies show that the studies that assumes the improving the performance of refrigerating system by using nano particles are very limited. Moreover, the survey on the literature reveal that there is no experimental investigation deal with enhancing the speed cooling of refrigerating systems of car by adding nano-particles to the compressor oil. The employed of nano-particles to the oil compressor objected to enhance the speed cooling through improving the heat exchange and thus, this issue can improve the refrigerating system performance. To have a better insight on the actions of using nano particles to the compressor oil on the performance of refrigerating system, an experimental investigation is required. So, the main target of this investigation is to experimentally perform and compare the performance of refrigerating systems of car without and with adding Al2O3 nano-particles to oil under different operating conditions. The temperature difference, speed cooling and COP are presented for the tested parameters with different values of mass concentration. The present research offers empirical proof of the effect of Al2O3 nanoparticles on cooling rate, effectiveness, and thermo-physical attributes, supplementing the existing body of knowledge and addressing the voids in the comprehension of nanofluids in AC systems.
The cooling system in an automobile plays a critical role in maintaining the engine’s temperature and preventing it from overheating. Fig. 1 indicates the main feature of the test rig consisting of the:
Figure 1: Photograph and schematic of the experimental system
1-The compressor is the power unit of the air-conditioning system that puts the refrigerant under high pressure before it pumps it into the condenser, where it changes from a gas to a liquid. A fully functioning compressor is necessary for the air-conditioning system to provide peak performance. On most cars, A/C compressors are driven by an engine-accessory belt.
2-The air-conditioning condenser is a radiator positioned between the car’s grille and the engine-cooling radiator in which the gaseous refrigerant sheds heat and returns to a liquid state. The liquid refrigerant flows to the evaporator inside the dashboard, where it cools the cabin.
3-A standard sight glass with indicator also usually has a dual function. it monitors whether the moisture content of the refrigerant is within acceptable limits and whether liquid refrigerant is always present at the expansion valve.
4-The air-conditioning evaporator is a small radiator inside the dashboard that provides cold air for the air-conditioning system. It is called the evaporator because it is where the freezing liquid refrigerant takes on any heat from the air blown through it and changes into a gaseous state (evaporating it) before returning it to the air-conditioning condenser to shed the heat; the process is constantly repeated. The air that emerges from the air conditioner is cold as a result. The evaporator is typically hidden inside the vehicle’s dashboard and can be labor-intensive to replace, which then requires a full system recharge.
5-Refrigerant is a substance that carries out the “transfer of heat process” by cycling through the air conditioning system and absorbing heat when becoming a gas, and giving off heat when becoming a liquid. HFC-134a (R134a) is used in air conditioners because it evaporates and liquefies easily, and has chemically stable and non-degenerative properties.
6-The primary function of a thermostat is to maintain a minimum operating temperature in the car’s engine. When the engine is started, the antifreeze and coolant mixture is kept within the engine by the thermostat. It opens upon reaching a specified temperature.
The test was conducted under laboratory conditions, with half an hour between stages, and at the same ambient temperature. The system was cleaned using R-11 after testing. All of the components in Fig. 1 work together to maintain the engine’s temperature and prevent it from overheating, which can cause damage and reduce the engine’s lifespan. It is important to regularly maintain and replace these components as needed to ensure the cooling system is functioning properly.
Nanofluids are a class of engineered fluids that consist of a base fluid (usually a liquid) and nano-particles with diameters in the range of 1–100 nm. Due to the unique properties of nano-particles, nanofluids exhibit several enhanced physical properties compared to their base fluids. Thermal conductivity is commonly measured using the hot-wire method, KD2 Pro Analyzer, and coaxial cylinders method. Rotational viscometers like Brookfield LVDV-III Rheometer are used for viscosity measurements. Both properties increase with nanoparticle concentration, but viscosity decreases with temperature. The two-step preparation method ensures the stability and dispersion of nanoparticles [30–33]. Some of these properties are calculated as [34–37].
Density:
ρn=(1−∅)ρf+∅ρp(1)
Thermal conductivity:
kn=kf(ks+2kf−2∅(kf−ks)ks+2kf+∅(kf−ks))(2)
Viscosity:
μnf=μbf(1+2.5∅)(3)
Specific heat transfer:
CPnf=(1−∅)CPbf×ρbf+∅×ρp×Cppρnf(4)
Nano-oil was prepared, which is solid nano-particles of (Al2O3) suspended in (Suniso 4GS) refrigerant oil it represents performance lubricants that are highly stable, wax-free, and suitable for use in refrigeration compressors and heat pumps. They are compatible with both H-CFC and natural refrigerants and are approved by major air-conditioner manufacturers worldwide. These oils are ideal for various installations and are miscible with various refrigerants, ensuring long service life. In the beginning, the amount of oil to be used in the device was calculated and the amount of solid nano-particles was calculated by using the equation below:
mp=∅×ρp×(mfρf)(1−∅)(5)
After calculating the amount of solid nano-particles, they are combined with the refrigerant oil in two ways:
A. Mechanical method
An electric mixer, as shown in Fig. 2, was used to mix the oil with the solid nano-particles in the quantities that were calculated according to the above equation, by running the mixer for a certain period of time ranging between (25–40) min until it appears completely homogeneous, where their specification are (1 L, 220 V, 50 Hz) and (7000 RPM).
Figure 2: Photographs of the mechanical and ultrasonic mixing processes for nano-particles
B. Using an ultrasound machine
The oil mixed with the nano-fluids in the mechanical way is placed in a beaker, as shown in Fig. 2, and the device is operated for a certain period of time ranging from (30–45) min, where their specification are (400 W, 220 V, 50 Hz) and (LUC-410).
The experimental error analysis is conducted based on the content provided by Ahmad [38]. The Root Sum Square (RSS) method is used to calculate the uncertainty ratio for the measured physical quantities and the calculated physical quantities. For independent variables and dependent variables, the bias error is calculated from the following equation [39]:
B=±[(12Resolution)2+(Accuracy)2]1/2(6)
The average measured value is calculated as follows:
¯χ=1n∑ni=1χi(7)
The standard deviation (σ) of the sampling distribution is calculated as follows:
σχ=[1n−1∑ni=1(χi−¯χ)2]1/2(8)
Thus, the average standard deviation (σ¯χ) of the values can be deduced using the following relationship:
σ¯χ=σχ√N(9)
Using the student-t distribution at the 95% confidence limit with degrees of freedom N–1. Accordingly, the total accuracy limits are as follows:
Pχ=t(N−1),95%×σ¯χ(10)
By integrating the initial error terms at 95%, since it is an absolute value, the following relationship is used as [39]:
Uχ=±[B2+Pχ2]1/2(11)
Accordingly, the experimental error rate (percentage) is calculated from the following relationship:
Uχχ%=±(Uχχ)×100(12)
In Eqs. (6)–(12), χ is any independent coefficient. Table 1 shows the uncertainties values of the independent variables and physical properties.
A standard error analysis is employed to perform an uncertainty assessment, assessing the precision of the current experimental method. The maximum uncertainty of the thermocouples is found to be 0.5% (Manufacturer: omega, Bridgeport, NY, USA), while uncertainties for different values are calculated as follows [40].
Analyzing the error rate for temperatures, it should be noted that the design specifications of the device used in temperature measurement are (Accuracy = ±0.2% + 0.1°C, Resolution = 0.1°C).
PT,ave.=t(N−1),95%∗σ¯T, ave.(13)
ΔTave.=[BTemp2+PTave.2]0.5(14)
ΔTave.Tave.%=±(ΔTave.¯Tave.)×100(15)
The uncertainty ratio of the physical properties was also calculated based on the temperature rate, in addition, the power was calculated based on the following information from the voltage and current supplied to the system:
BV=±[(12Resolution)2+(Accuracy)2]0.5(16)
Pv=t(25−1),95%∗σ¯v(17)
ΔV=±[(BV)2+(PV)2]0.5(18)
ΔVV%=±(ΔV¯V)×100(19)
Note that the design specifications of the voltage regulator used (Accuracy = (±1.2% + 3%) V, Resolution = 0.01 V), and the design specifications of the digital electric current intensity reader device used are (Accuracy = (±2.5% + 5%) A, Resolution = 0.01 A), as shown in the following equations:
BIc=±((12Resolution)2+(Accuracy)2)0.5(20)
PIc=t(25−1),95%∗σ¯Ic(21)
ΔIc=±[(BIc)2+(PIc)2]0.5(22)
ΔIcIc%=±(ΔIc¯Ic)×100(23)
Nanofluids are colloidal suspensions consisting of nanoparticles dispersed in a base fluid, and they have gained much attention due to their enhanced thermal conductivity and heat transfer properties. However, their stability is an important factor that must be taken into account for practical applications. The stability of nanofluids can be influenced by several factors such as particle size, concentration, surface charge, and surface chemistry. Overall, the stability of nanofluids is a complex phenomenon that depends on multiple factors. Further research is required to fully understand the mechanisms involved in nanofluid stability and to develop strategies for improving the stability of nanofluids for practical applications [41–44]. From Fig. 3, it can be observed that the nanoparticles remain stable in the oil around 15 h. After that, the nanoparticles begin to separate from the oil. If the system is stopped for a short period of time and then re-operated, the nanoparticles can be mixed once again with the oil due to the oil circulation process and rising temperature by taking into consideration there is a possibility to deposit some parts of nanoparticles within the system.
Figure 3: Photograph of the process of stability Al2O3-oil
The performance of the system (COP) is a critical metric used to evaluate the efficiency of an automotive air conditioning system. It is affected by different factors including compressor speed, ambient temperature, refrigerant charge, and the efficiency of heat exchangers. The COP is calculated as the ratio of useful heating or cooling provided by any system divided by the amount of energy consumed by the system as follows [45,46]:
Coefficient of Performance:
COP=Cooling OutputElectrical Energy Input(24)
where the cooling output is the amount of heat withdrawn from an area by an air conditioning system, indicating its ability to reduce indoor temperature. On the other hand, the electrical energy input displays the amount of electricity used by an air conditioning unit to power the system, enabling efficient operation and control of indoor air temperature and humidity.
Fig. 4 shows the comparison of density, viscosity and thermal conductivity between pure oil and Al2O3-oil with a mass concentration range of 0.1%, 0.15% and 0.2%. From Fig. 4, the results show that the conventional oils with Al2O3 nanoparticles lead to improved physical thermal properties further validated by the work of Husainy et al. [16] and Ajayi et al. [22]. These improvements have manifested themselves in an enhanced fluid behaviour that highlights the high potential for the use of nanofluids to outperform traditional fluids across numerous application areas, with heightened value placed on efficient heat transfer and superior heat capacity.
Figure 4: Comparison of density, viscosity and thermal conductivity between pure oil and Al2O3-oil
Fig. 5 shows the temperature inside the cabin along with speed cooling with and without adding Al2O3 nanoparticles with a mass concentration range of 0.1%, 0.15% and 0.2%. In particular, the addition of Al2O3 nanoparticles to the oil aligns with the work of Li et al. [26] and Daniel et al. [27], who reported that Al2O3 nanoparticles in oil-nano leads to improved performance of heat transfer and hence, the speed cooling has been raised about 9%, 10% and 13% for mass concentrations of 0.1%, 0.15% and 0.2%, respectively, as compared to the pure oil. The test was conducted under laboratory conditions, with half an hour between stages, and at the same ambient temperature. The system was cleaned using R-11 after testing as may be seen in Fig. 5. This finding emphasizes the features of thermal properties of Al2O3 nanoparticles for improving the heat dissipation systems. The increment is due to the increase in the physical properties of the nano-oil.
Figure 5: Temperature inside the cabin testing over time with and without the addition of Al2O3 nanoparticles to oil
Fig. 6 shows the comparison between the thermal performance coefficient (COP) with and without adding Al2O3 nanoparticles to oil under different values of mass concentration. The results indicated that the thermal performance coefficient of the nano-oil system has been increased by 13%, 15% and 18% for mass concentrations 0.1%, 0.15% and 0.2%, respectively, as compared to the system that used pure oil. This indication demonstrated that the use of Al2O3 nano-particles significantly improved the heat transfer performance and enhanced the cooling rate under the same operating and surrounding conditions resulting from increasing the physical properties of nano-oil. This relationship between nanoparticle concentration and thermal properties is supported by the findings of Mert et al. [10], Afolalu et al. [17], Said et al. [18], Sharif et al. [28], and Babarinde et al. [29], Their results demonstrated improvements in thermophysical properties and coefficient of performance (COP) in system, which aligns with the enhanced COP observed in our study when using Al2O3 nanoparticles.
Figure 6: Comparison of thermal performance comparison (COP) between pure oil system and modifiying system (nano + oil) under different values of mass concentration of nano-particles
From the current investigation, the following findings are listed in brief:
1. The comparison between the system operated by only oil and the system operated by Al2O3-oil shows that the using of Al2O3 nanoparticles leads to a rise in the speed cooling by 13% for Ø = 0.2%. This increase implies that the using of Al2O3 nanoparticles has a great impact on hastening cooling within the setup and thus, this helps to improve the thermal management.
2. The findings display that the value of COP increases by 18% when using Al2O3-oil with Ø = 0.2% as compared to the pure oil case. This means that the addition of Al2O3 nanoparticles to oil has a high influence on the rate of heat transfer. Thus, it can be ideally used for any application, where heat control is paramount.
3. The findings show that the increase Ø leads to enhancing the thermo-physical characteristics of nanofluid by 15% for Ø = 0.2% and hence, this value represents the maximum improvement. Also, the results display that there is a direct relationship between Ø and thermal properties of nanofluid, such as thermal conductivity, viscosity, and density. This enhancement shows that there is room for optimizing the characteristics of nanofluids toward tailored thermal management demands.
4. The use of Al2O3 nanoparticles to compressor oil significantly enhanced the cooling system, the heat dissipation rate, and the thermal efficiency highlighting the versatility and benefits of nanofluids in various applications that require efficient heat conduction and enhancing the thermo-mechanical performance.
To progress the present investigation, the next investigations are listed as follows:
1. Extend the nano-oil stability testing beyond 15 h for practical use.
2. Investigate the actions of using CuO or SiO2 nanoparticles instead of Al2O3 on the performance of all components.
3. The study may be improved in the future by assessing the cooling system performance under real-world conditions for practical insights.
Acknowledgement: We would humbly like to express our appreciation to the Northern Technical University for their laboratory support for this study.
Funding Statement: The authors received no specific funding for this study.
Author Contributions: The authors confirm contribution to the paper as follows: study conception and design: Karam H. Mohammed, Ashraf E. Al-Mirani; data collection: Bashar Mahmood Ali; analysis and interpretation of results: Omar Rafae Alomar; draft manuscript preparation: Omar Rafae Alomar. All authors reviewed the results and approved the final version of the manuscript.
Availability of Data and Materials: All data is available on request.
Conflicts of Interest: The authors declare that they have no conflicts of interest to report regarding the present study.
References
1. Setiyo, M., Mohd, S. (2022). Vehicle air conditioner (vac) control system based on passenger comfort: A proof of concept. IIUM Engineering Journal, 23, 370–383. https://doi.org/10.31436/iiumej.v23i1.1812 [Google Scholar] [CrossRef]
2. Zhang, Z., Wang, J., Feng, X., Chang, L., Chen, Y. et al. (2018). The solutions to electric vehicle air conditioning systems: A review. Renewable & Sustainable Energy Reviews, 91, 443–463. https://doi.org/10.1016/J.RSER.2018.04.005 [Google Scholar] [CrossRef]
3. Francesco, P. C., Ian, S. W., Enrica, D. C. (2023). Air-conditioning adoption and electricity demand highlight climate change mitigation–adaptation tradeoffs. Dental Science Reports. https://doi.org/10.1038/s41598-023-31469-z [Google Scholar] [CrossRef]
4. Ramasamy, K., Manasij, S. R., Sai, H. (2020). Artificial intelligence based air conditioner energy saving using a novel preference map. IEEE Access. https://doi.org/10.1109/ACCESS.2020.3037970 [Google Scholar] [CrossRef]
5. Qian, Z., Xu, C., Ren, J. (2022). Thermal analysis of a novel single-effect absorption refrigeration system using water/ionic liquid as working fluids. Thermal Science, 26, 3107–3118. https://doi.org/10.2298/tsci201026038q [Google Scholar] [CrossRef]
6. Pazarlıoğlu, H. K., Ekiciler, R., Arslan, K., Mohammed, N. A. M. (2023). Exergetic, energetic, and entropy production evaluations of parabolic trough collector retrofitted with elliptical dimpled receiver tube filled with hybrid nanofluid. Applied Thermal Engineering, 223, 120004. https://doi.org/10.1016/j.applthermaleng.2023.120004 [Google Scholar] [CrossRef]
7. Pazarlıoğlu, H. K., Tepe, A. Ü., Tekir, M., Arslan, K. (2022). Effect of new design of elongated jet hole on thermal efficiency of solar air heater. Thermal Science and Engineering Progress, 36, 101483. https://doi.org/10.1016/j.tsep.2022.101483 [Google Scholar] [CrossRef]
8. Okonkwo, E. C., Wole-Osho, I., Almanassra, I. W., Abdullatif, Y. M., Al-Ansari, T. (2020). An updated review of nanofluids in various heat transfer devices. Journal of Thermal Analysis and Calorimetry, 145(6), 2817–2872. https://doi.org/10.1007/s10973-020-09760-2 [Google Scholar] [CrossRef]
9. Redhwan, A. A. M., Azmi, W. H., Sharif, M. Z., Mamat, R., Samykano, M. et al. (2018). Performance improvement in mobile air conditioning system using Al2O3/PAG nanolubricant. Journal of Thermal Analysis and Calorimetry, 135(2), 1299–1310. https://doi.org/10.1007/s10973-018-7656-2 [Google Scholar] [CrossRef]
10. Mert, S., Yaşar, H., Durmaz, U., Topuz, A., Yeter, A. et al. (2021). An experimental study on cooling performance of a car radiator using Al2O3-ethylene glycol/water nanofluid. Thermal Science, 25(1 Part B), 801–809. https://doi.org/10.2298/TSCI190630179M [Google Scholar] [CrossRef]
11. Dilawar, M., Qayoum, A. (2022). Performance study of aluminium oxide based nanorefrigerant in an air-conditioning system. Research on Engineering Structures & Materials. https://doi.org/10.17515/resm2022.459ma0701 [Google Scholar] [CrossRef]
12. Azmi, W. H., Zawawi, N. N. M., Redhwan, A. A. M., Ramadhan, A. I., Ali, H. M. (2022). Optimization of air conditioning performance with Al2O3-SiO2/PAG composite nanolubricants using the response surface method. Lubricants, 10(10), 243. https://doi.org/10.3390/lubricants10100243 [Google Scholar] [CrossRef]
13. Zawawi, N. N. M., Azmi, W. H., Ghazali, M. F., Ali, H. M. (2022). Performance of air-conditioning system with different nanoparticle composition ratio of hybrid nanolubricant. Micromachines, 13(11), 1871. https://doi.org/10.3390/mi13111871. [Google Scholar] [PubMed] [CrossRef]
14. Alahmer, A., Ghoniem, R. M. (2023). Improving automotive air conditioning system performance using composite nano-lubricants and fuzzy modeling optimization. Sustainability, 15(12), 9481. https://doi.org/10.3390/su15129481 [Google Scholar] [CrossRef]
15. Zawawi, N. N. M., Azmi, W. H., Ghazali, M. F., Ramadhan, A. I. (2022). Performance optimization of automotive air-conditioning system operating with Al2O3-SiO2/PAG composite nanolubricants using taguchi method. Automotive Experiences, 5(2), 121–136. https://doi.org/10.31603/ae.6215 [Google Scholar] [CrossRef]
16. Husainy, A., Gurav, A. R., Pawar, A. N., Kate, S. S., Daphale, D. D. et al. (2019). Performance study of ducted air-conditioning system with different mass fraction of Al2O3 nanofluids. Asian Review of Mechanical Engineering, 8(1), 48–51. https://doi.org/10.51983/arme-2019.8.1.2459 [Google Scholar] [CrossRef]
17. Afolalu, S. A., Ikumapayi, O. M., Adeoye, A. O. M., Bello, K. A., Ogundipe, A. T. et al. (2022). Performance assessment of varying nanoparticles in a base mineral oil for domestic refrigeration system. Materials Today: Proceedings, 62, 3350–3354. https://doi.org/10.1016/j.matpr.2022.04.246 [Google Scholar] [CrossRef]
18. Said, Z., Rahman, S. M. A., Sohail, M. A., Bibin, B. S. (2023). Analysis of thermophysical properties and performance of nanorefrigerants and nanolubricant-refrigerant mixtures in refrigeration systems. Case Studies in Thermal Engineering, 49, 103274. https://doi.org/10.1016/j.csite.2023.103274 [Google Scholar] [CrossRef]
19. Sözen, A., Özbaş, E., Menlik, T., Çakir, M. T., Gürü, M. et al. (2014). Improving the thermal performance of diffusion absorption refrigeration system with alumina nanofluids: An experimental study. International Journal of Refrigeration, 44, 73–80. https://doi.org/10.1016/j.ijrefrig.2014.04.018 [Google Scholar] [CrossRef]
20. Sanukrishna, S. S., Murukan, M., Jose, P. M. (2018). An overview of experimental studies on nanorefrigerants: Recent research, development and applications. International Journal of Refrigeration, 88, 552–577. https://doi.org/10.1016/j.ijrefrig.2018.03.013 [Google Scholar] [CrossRef]
21. Jiang, W., Song, J., Jia, T., Yang, L., Li, S. et al. (2022). A comprehensive review on the pre-research of nanofluids in absorption refrigeration systems. Energy Reports, 8, 3437–3464. https://doi.org/10.1016/j.egyr.2022.02.087 [Google Scholar] [CrossRef]
22. Ajayi, O. O., Ukasoanya, D. E., Ogbonnaya, M., Salawu, E. Y., Okokpujie, I. P. et al. (2019). Investigation of the effect of R134A/Al2O3–Nanofluid on the performance of a domestic vapour compression refrigeration system. Procedia Manufacturing, 35, 112–117. https://doi.org/10.1016/j.promfg.2019.05.012 [Google Scholar] [CrossRef]
23. Raja, N. N., Khanderao, A. D. (2020). Experimental investigation on performance of vapor compression refrigeration system using nanorefrigerant (R134a + Al2O3) with evaporative condenser. Asian Review of Mechanical Engineering, 9(1), 45–49. https://doi.org/10.51983/arme-2020.9.1.2471 [Google Scholar] [CrossRef]
24. Adelekan, D. S., Ohunakin, O. S., Gill, J., Atiba, O. E., Okokpujie, I. P. et al. (2019). Experimental investigation of a vapour compression refrigeration system with 15 nm TiO2-R600a nano-refrigerant as the working fluid. Procedia Manufacturing, 35, 1222–1227. https://doi.org/10.1016/j.promfg.2019.06.079 [Google Scholar] [CrossRef]
25. Mohamed, H., Çamdalı, Ü., Bıyıkoğlu, A., Aktaş, M. (2022). Enhancing the performance of a vapour compression refrigerator system using R134a with a CuO/CeO2 nano-refrigerant. StrojnišKi Vestnik, 68(6), 395–410. https://doi.org/10.5545/sv-jme.2021.7454 [Google Scholar] [CrossRef]
26. Li, S., Lu, J. (2022). A theoretical comparative study of vapor-compression refrigeration cycle using Al2O3 nanoparticle with low-GWP refrigerants. Entropy, 24(12), 1820. https://doi.org/10.3390/e24121820. [Google Scholar] [PubMed] [CrossRef]
27. Daniel, V. B., Prakash, N., Prasad, C., John, J. G., Hariram, V. (2022). Effect of nanofluids as coolant in automotive radiator—A numerical approach. International Journal of Vehicle Structures and Systems, 14(5). https://doi.org/10.4273/ijvss.14.5.21 [Google Scholar] [CrossRef]
28. Sharif, M. Z., Azmi, W. H., Ghazali, M. F., Zawawi, N. N. M., Ali, H. M. (2023). Numerical and thermo-energy analysis of cycling in automotive air-conditioning operating with hybrid nanolubricants and R1234yf. Numerical Heat Transfer, Part A: Applications, 83(9), 935–957. https://doi.org/10.1080/10407782.2022.2155277 [Google Scholar] [CrossRef]
29. Babarinde, T. O., Madyira, D. M. (2023). Assessment of TiO2, Al2O3, and SiO2 nanolubricant with eco-friendly refrigerant as substitute for R134a in a vapour compression system: An experimental approach. Energy Reports, 9, 326–331. https://doi.org/10.1016/j.egyr.2023.10.005 [Google Scholar] [CrossRef]
30. Ramadhan, A. I., Azmi, W. H., Mamat, R., Diniardi, E., Hendrawati, T. Y. (2021). Experimental investigation of cooling performance in automotive radiator using Al2O3-TiO2-SiO2 nanofluids. Automotive Experiences, 5(1), 28–39. https://doi.org/10.31603/ae.6111 [Google Scholar] [CrossRef]
31. Chiam, H., Azmi, W., Usri, N., Mamat, R., Adam, N. (2017). Thermal conductivity and viscosity of Al2O3 nanofluids for different based ratio of water and ethylene glycol mixture. Experimental Thermal and Fluid Science, 81, 420–429. https://doi.org/10.1016/j.expthermflusci.2016.09.013 [Google Scholar] [CrossRef]
32. Wang, R., Wang, J. (2017). Intelligent dimensional and thermal performance analysis of Al2O3 nanofluid. Energy Conversion and Management, 138, 686–697. https://doi.org/10.1016/j.enconman.2017.02.010 [Google Scholar] [CrossRef]
33. Hussein, A., Bakar, R., Kadirgama, K., Sharma, K. (2013). Experimental measurements of nanofluids thermal properties. International Journal of Automotive and Mechanical Engineering, 7, 850–863. https://doi.org/10.15282/ijame.7.2012.5.0070 [Google Scholar] [CrossRef]
34. Ramachandran, K., Hussein, A., Kadirgama, K., Ramasamy, D., Azmi, W. H. et al. (2017). Thermophysical properties measurement of nano cellulose in ethylene glycol/water. Applied Thermal Engineering, 123, 1158–1165. https://doi.org/10.1016/j.applthermaleng.2017.05.067 [Google Scholar] [CrossRef]
35. Hussein, A., Sharma, K. V., Bakar, R. A., Kadirgama, K. (2013). The effect of nanofluid volume concentration on heat transfer and friction factor inside a horizontal tube. Journal of Nanomaterials, 2013, 1–12. https://doi.org/10.1155/2013/859563 [Google Scholar] [CrossRef]
36. Rajput, R. K. (1998). Fluid mechanics and hydraulic machines. https://www.amazon.com/Fluid-Mechanics-Hydraulic-Machines-Rajput/dp/8121916666 (accessed on 10/05/2024). [Google Scholar]
37. Abedalh, A. S., Shaalan, Z. A., Yassien, H. N. S. (2021). Mixed convective of hybrid nanofluids flow in a backward-facing step. Case Studies in Thermal Engineering, 25, 100868. https://doi.org/10.1016/j.csite.2021.100868 [Google Scholar] [CrossRef]
38. Ahmad, T. T. (2014). Optimal geometric arrangement of unfinned and finned flat tube heat exchangers under laminar forced convection. http://umpir.ump.edu.my/id/eprint/13175/ (accessed on 10/05/2024). [Google Scholar]
39. Beasley, D. E., Figliola, R. S. (2001). Theory and design for mechanical measurements, third edition. Measurement Science & Technology, 12(10), 1743. https://doi.org/10.1088/0957-0233/12/10/701 [Google Scholar] [CrossRef]
40. Taylor, J. (1997). Introduction to error analysis, the study of uncertainties in physical measurements, 2nd edition. University Science Books. http://ui.adsabs.harvard.edu/abs/1997ieas.book (accessed on 10/05/2024). [Google Scholar]
41. Holman, J. P. (2012). Experimental methods for engineers, 8th edition. New York: McGraw-Hill. [Google Scholar]
42. Mehta, B., Subhedar, D., Panchal, H., Said, Z. (2022). Synthesis, stability, thermophysical properties and heat transfer applications of nanofluid—A review. Journal of Molecular Liquids, 364, 120034. https://doi.org/10.1016/j.molliq.2022.120034 [Google Scholar] [CrossRef]
43. Mukherjee, S., Paria, S. (2013). Preparation and stability of nanofluids—A review. IOSR Journal of Mechanical and Civil Engineering, 9(2), 63–69. https://doi.org/10.9790/1684-0926369 [Google Scholar] [CrossRef]
44. Setia, H., Gupta, R., Wanchoo, R. K. (2013). Stability of nanofluids. Materials Science Forum, 757, 139–149. https://doi.org/10.4028/www.scientific.net/MSF.757.139 [Google Scholar] [CrossRef]
45. Datta, S., Das, P., Mukhopadhyay, S. (2019). An optimized ANN for the performance prediction of an automotive air conditioning system. Science and Technology for the Built Environment, 25, 282–296. https://doi.org/10.1080/23744731.2018.1526014 [Google Scholar] [CrossRef]
46. Ibrahim, M. (2020). A comparative experimental study on the performance of the air-conditioning system through effective condenser cooling and preheating the refrigerant. Environmental Progress & Sustainable Energy, 40, 521. https://doi.org/10.1002/ep.13468 [Google Scholar] [CrossRef]
Cite This Article
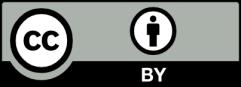
This work is licensed under a Creative Commons Attribution 4.0 International License , which permits unrestricted use, distribution, and reproduction in any medium, provided the original work is properly cited.