Open Access
ARTICLE
Numerical Investigations on Fluid Flow and Heat Transfer Characteristics of an Ultra-Thin Heat Pipe with Separated Wick Structures
1 Division of Industrial Fundamentals, Faculty of Advanced Science and Technology, Kumamoto University, Kumamoto, 860-8555, Japan
2 Department of Mechanical and Mathematical Engineering, Graduate School of Science and Technology, Kumamoto University, Kumamoto, 860-8555, Japan
* Corresponding Author: Yasushi Koito. Email: -u.ac.jp
Frontiers in Heat and Mass Transfer 2024, 22(3), 869-887. https://doi.org/10.32604/fhmt.2024.050910
Received 22 February 2024; Accepted 15 May 2024; Issue published 11 July 2024
Abstract
Thermal and fluid-flow characteristics were numerically analyzed for ultra-thin heat pipes. Many studies have been conducted for ultra-thin heat pipes with a centered wick structure, but this study focused on separated wick structures to increase the evaporation/condensation surface areas within the heat pipe and to reduce the concentration of heat flux within the wick structure. A mathematical heat-pipe model was made in the three-dimensional coordinate system, and the model consisted of three regions: a vapor channel, liquid-wick, and container wall regions. The conservation equations for mass, momentum, and energy were solved numerically with boundary conditions by using a code developed by one of the authors. The numerical results with the separated wick structures were compared with those with the centered, which confirmed the effectiveness of the separation of the wick structure. However, the effectiveness of the separation was affected by the position of the separated wick structure. A simple equation was presented to determine the optimum position of the separated wick structures. Numerical analyses were also conducted when the width of the heat pipe was increased with the cooled section, which clarified that the increase in the cooled-section width with the addition of wick structures was more effective than the increase in the cooled-section length. A 44% reduction in the total temperature difference of the heat pipe was obtained under the present numerical conditions. Furthermore, a comparison was made between experimental results and numerical results.Keywords
Cite This Article
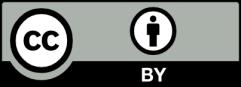
This work is licensed under a Creative Commons Attribution 4.0 International License , which permits unrestricted use, distribution, and reproduction in any medium, provided the original work is properly cited.