Open Access
ARTICLE
Heat Recovery from Automotive Exhaust Using Heat Pipes with Limited Fluid Charge
Department of Engineering Technology, Texas State University, San Marcos, 78666, USA
* Corresponding Author: Bin Xiao. Email:
(This article belongs to the Special Issue: Passive Heat Transfer Enhancement for Single Phase and Multi-Phase Flows)
Frontiers in Heat and Mass Transfer 2024, 22(1), 35-48. https://doi.org/10.32604/fhmt.2024.048039
Received 26 November 2023; Accepted 25 January 2024; Issue published 21 March 2024
Abstract
Experiments were conducted in this study to examine the thermal performance of a thermosyphon, made from Inconel alloy 625, could recover waste heat from automobile exhaust using a limited amount of fluid. The thermosyphon has an outer diameter of 27 mm, a thickness of 2.6 mm, and an overall length of 483 mm. The study involved directing exhaust gas onto the evaporator. This length includes a 180-mm evaporator, a 70-mm adiabatic section, a 223-mm condenser, and a 97-mm finned exchanger. The study examined the thermal performance of the thermosyphon under exhaust flow rates ranging from 0–10 g/sec and temperatures varying from 300°C–900°C. The influence of three parameters—inclination angle (5°–45°), water mass (2–5.3 g), and the quantity of non-condensable gas Argon (0–0.6 g)—was investigated to assess their impacts on the thermosyphon’s thermal efficiency. The experimental findings revealed that with 3 g of water and 0.0564 g of argon in the thermosyphon, the condenser reached its highest temperature at around 200°C. The ideal fuel loading rate for the thermosyphon falls between 0.2 and 0.7 g/s. Moreover, as inclination angles rise, outer wall temperatures of the thermosyphon increase. This is attributed to the explicit expansion of the effective heating area within the evaporation section, coupled with an amplified gravitational component of the water flux. Additionally, an upsurge in the quantity of non-condensable gas (NCG) can mitigate temperature gradients on the outer wall, resulting in a decline in the thermosyphon’s performance. The insulation applied to the adiabatic section demonstrated efficacy in augmenting temperature gradients on the outer wall, thereby improving the overall performance of the thermosyphon. As the water charge within the thermosyphon increases, there is a corresponding rise in heat transfer rates both from the exhaust to the thermosyphon and from the thermosyphon to the fuel.Keywords
Cite This Article
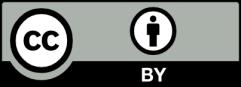
This work is licensed under a Creative Commons Attribution 4.0 International License , which permits unrestricted use, distribution, and reproduction in any medium, provided the original work is properly cited.