Open Access
ARTICLE
Experimental and Numerical Study on the Transient Flow Behavior in Gasoline Refueling System
1 Key Laboratory of Intelligent Manufacturing Quality Big Data Tracing and Analysis of Zhejiang Province, China Jiliang University, Hangzhou, 310018, China
2 School of Aeronautics and Astronautics, Zhejiang University, Hangzhou, 310027, China
3 Ocean College, Zhejiang University, Zhoushan, 316021, China
* Corresponding Authors: Lifang Zeng. Email: ; Lijuan Qian. Email:
Frontiers in Heat and Mass Transfer 2024, 22(1), 107-127. https://doi.org/10.32604/fhmt.2023.044433
Received 30 July 2023; Accepted 26 October 2023; Issue published 21 March 2024
Abstract
Efficient and secure refueling within the vehicle refueling systems exhibits a close correlation with the issues concerning fuel backflow and gasoline evaporation. This paper investigates the transient flow behavior in fuel hose refilling and simplified tank fuel replenishment using the volume of fluid method. The numerical simulation is validated with the simplified hose refilling experiment and the evaporation simulation of Stefan tube. The effects of injection flow rate and injection directions have been discussed in the fuel hose refilling part. For both the experiment and simulation, the pressure at the end of the refueling pipe in the lower located nozzle case is 30% higher than that in the upper located nozzle case at a high flow rate, and the backflow phenomenon occurs at the lower filling mode. The fluid will directly flush into the first pipe elbow, changing the flow pattern from bubble flow to slug flow, which results in low-frequency and high-amplitude flow pressure fluctuations. A hexane refueling system, consisting of a refueling pipe, fuel tank and a vapor return line, is analyzed, in which hexane evaporation is considered. At the early refueling period, a higher refueling rate will lead to more obvious splashing, which leads to a higher average mass of hexane vapor and pressure in the tank. Two optimized fuel tank designs are examined. The lower fuel tank filling port exhibits significantly lower vapor hexane in the fuel tank compared to the other design, resulting in a reduction of 200 Pa in the peak pressure in the tank, which contributes to a substantial reduction of gasoline loss during tank filling.Keywords
Cite This Article
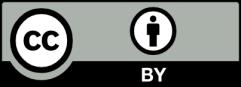
This work is licensed under a Creative Commons Attribution 4.0 International License , which permits unrestricted use, distribution, and reproduction in any medium, provided the original work is properly cited.