Open Access
ARTICLE
Study on Rotational Effects of Modern Turbine Blade on Coolant Injecting Nozzle Position with Film Cooling and Vortex Composite Performance
1 School of Energy and Power Engineering, Xi’an Jiaotong University, Xi’an, 710049, China
2 School of Mechanical and Aerospace Engineering, College of Engineering, Nanyang Technological University, 639798, Singapore
3 Shaanxi Engineering Laboratory of Turbomachinery and Power Equipment, Xi’an, 710049, China
* Corresponding Authors: Eddie Yin Kwee Ng. Email: ; Liang Li. Email:
Frontiers in Heat and Mass Transfer 2023, 21, 1-31. https://doi.org/10.32604/fhmt.2023.045510
Received 29 August 2023; Accepted 23 October 2023; Issue published 30 November 2023
Abstract
The flow structure of the vortex cooling is asymmetrical compared to the traditional gas turbine leading edge cooling, such as the impingement cooling and the axial flow cooling. This asymmetrical property will affect the cooling performance in the blade leading edge, whereas such effects are not found in most of the studies on vortex cooling due to the neglect of the mainstream flow in the airfoil channel. This study involves the mainstream flow field and the rotational effects based on the profile of the GE E3 blade to reveal the mechanism of the asymmetrical flow structure effects. The nozzle position on the characteristics of the vortex and film composite cooling in the turbine rotating blade leading edge is numerically investigated. The cool-ant injecting nozzles are set at the side of the pressure surface (PS-side-in) vs. that is set at the side of the suction surface (SS-side-in) to compare the cooling characteristics at the rotating speed range of 0–4000 rpm with fluid and thermal conjugate approach. Results show that the nozzle position presents different influences under low and higher rotational speeds. As for the mainstream flow, rotation makes the stagnation line move from the pressure surface side to the suction surface side, which changes the coolant film attachment on the blade leading edge surface. The position of nozzles, however, indicates limited influence on the coolant film flow. As for the internal channel vortex flow characteristics, the coolant injected from the nozzles forms a high-velocity region near the target wall, which brings about enhancing convective heat transfer. The flow direction of the vortex flow near the internal channel wall is opposite and aligns with the direction of Coriolis force in both the PS-side-in and SS-side-in, respectively. Therefore, the Coriolis force augments the convective heat transfer intensity of the vortex cooling in the internal channel in SS-side-in while weakening the internal heat transfer in PS-side-in. Such effects become more intense with higher rotational speed. The blade surface temperature decreases as the Coriolis force increases the internal heat transfer intensity. The SS-side-in suggests a superior composite cooling performance under the relatively higher rotating speed. The SS-side-in structure is recommended in the gas turbine blade leading edge running at a higher rotating speed.Graphic Abstract
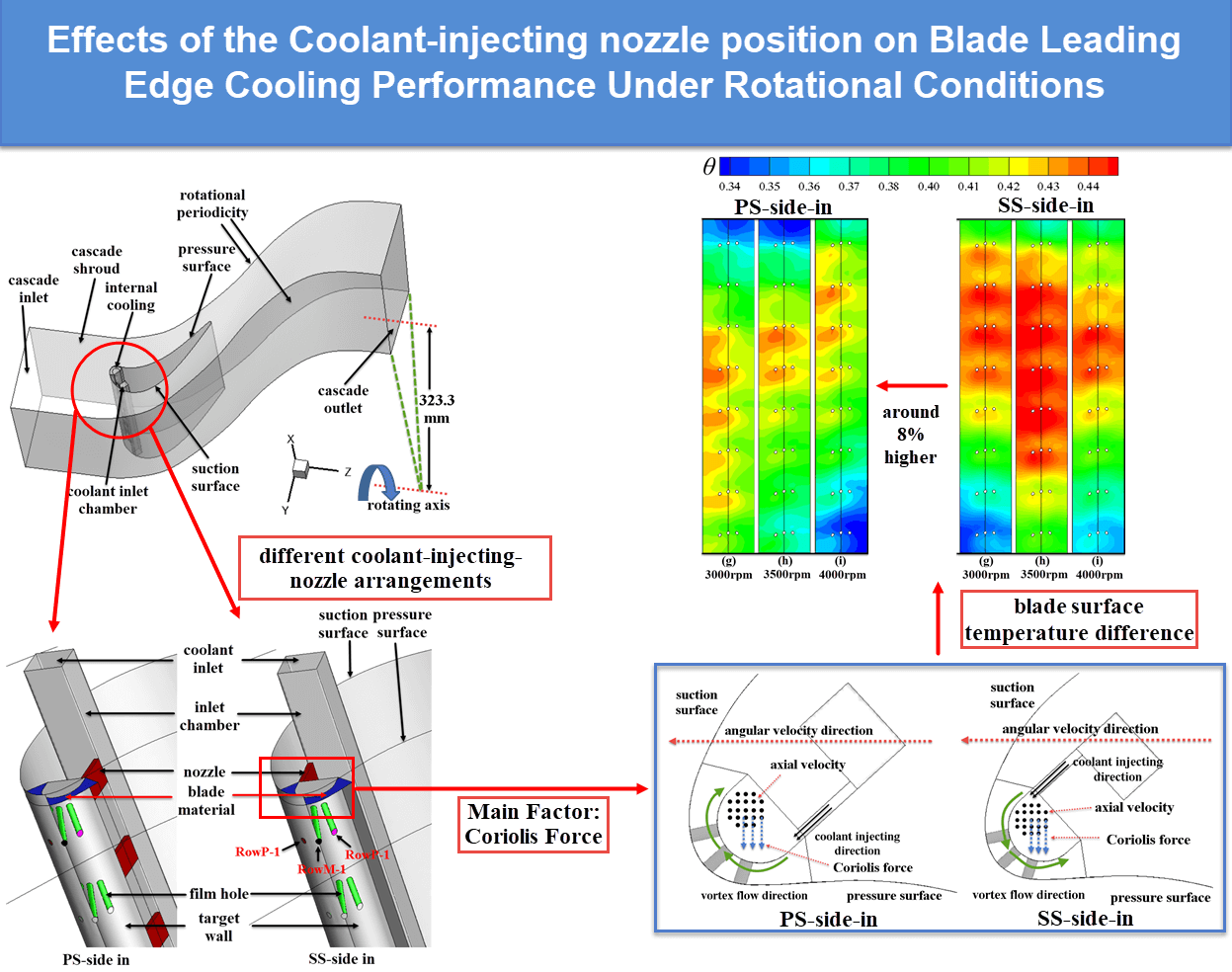
Keywords
Cite This Article
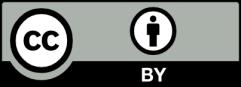
This work is licensed under a Creative Commons Attribution 4.0 International License , which permits unrestricted use, distribution, and reproduction in any medium, provided the original work is properly cited.