Open Access
ARTICLE
Numerical Simulation of the Flow and Heat Transfer in Novel Circumfluent Cyclone Separator during High-Temperature Converter Gas Recovery
1 State Key Laboratory of High Temperature Gas Dynamics, Institute of Mechanics, Chinese Academy of Sciences, Beijing, 100190, China
2 School of Engineering Science, University of Chinese Academy of Sciences, Beijing, 100049, China
* Corresponding Author: Sen Li. Email:
Frontiers in Heat and Mass Transfer 2025, 23(1), 163-184. https://doi.org/10.32604/fhmt.2024.059740
Received 15 October 2024; Accepted 26 November 2024; Issue published 26 February 2025
Abstract
In the novel fully dry converter gas recovery process, a novel circumfluent cyclone separator with an evaporation heating surface can simultaneously realize the dust removal and sensible heat recovery of converter gas. For this equipment, the distributions of internal flow and wall heat transfer affect the efficiency of dust removal and sensible heat recovery. In this study, based on on-site operation tests, the distributions of internal flow and wall heat transfer in the circumfluent cyclone separator are studied by numerical simulation. The results indicate that the flow rate proportions in different regions of the circumfluent cyclone separator remain constant during the steelmaking process, approximately 80.1% of the converter gas flows through the cone chamber, and 15.4% of the converter gas flows through the annular chamber. The heat transfer rate proportions on the walls of different regions of the circumfluent cyclone separator remain constant during the steelmaking process, and the heat transfer rate proportions on the walls of the cone chamber, straight shell, shell head and outlet pipe are 40.2%, 27.0%, 17.6% and 15.2%, respectively.Keywords
Cite This Article
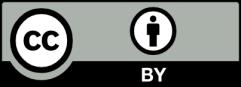
This work is licensed under a Creative Commons Attribution 4.0 International License , which permits unrestricted use, distribution, and reproduction in any medium, provided the original work is properly cited.