Open Access
ARTICLE
Prediction of Erosion Wear in Multi-Size Particulate Flow through a Rotating Channel
CFD Research Leader, GIW Industries Inc., Grovetown, GA - 30813, USA
Asst. Prof., Dept. of Mech. Engg., SISTec, Bhopal, MP, India – 462036 (Corresponding Author)
Fluid Dynamics & Materials Processing 2009, 5(1), 93-122. https://doi.org/10.3970/fdmp.2009.005.093
Abstract
The objective of the present work is to predict erosive wear in multisize dense slurry flow in a rotating channel. The methodology comprises numerical prediction of two-phase flow which is accomplished using the Galerkin finite element method. The wear models for both sliding wear and impact wear mechanisms account for the particle size dependence. The effect of various operating parameters such as rotation rate, solids concentration, flow rate, particle size distribution and so forth has been studied. Results indicate that wear rate in general increases along the pressure-side of the channel with rotation rate, overall solids concentration, flow rates etc. The wear models in the present study are able to capture the particle size distribution fairly well. It is concluded that accurate wear prediction could be obtained by characterizing the particle size distribution into suitable number of size classes, and accounting for the particle-size dependence in the wear model(s).Keywords
Cite This Article
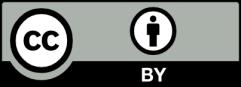
This work is licensed under a Creative Commons Attribution 4.0 International License , which permits unrestricted use, distribution, and reproduction in any medium, provided the original work is properly cited.