Open Access
REVIEW
Progress in the Understanding and Modeling of Cavitation and Related Applications
1 Key Laboratory of Advanced Manufacturing Intelligent Technology, Ministry of Education, Harbin University of Science and Technology, Harbin, 150080, China
2 School of Mechanica and Power Engineering, Harbin University of Science and Technology, Harbin, 150080, China
* Corresponding Author: Jianying Li. Email:
Fluid Dynamics & Materials Processing 2025, 21(3), 445-470. https://doi.org/10.32604/fdmp.2025.062337
Received 16 December 2024; Accepted 26 February 2025; Issue published 01 April 2025
Abstract
Hydrodynamic cavitation, as an efficient technique applied in many physical and chemical treatment methods, has been widely used by various industries and in several technological fields. Relevant generators, designed with specific structures and parameters, can produce cavitation effects, thereby enabling effective treatment and reasonable transformation of substances. This paper reviews the design principles, performance, and practical applications associated with different types of cavitation generators, aiming to provide theoretical support for the optimization of these systems. It systematically analyzes the underpinning mechanisms and the various factors influencing the cavitation phenomena, also conducting a comparative analysis of the performance of different types of generators. Specific applications dealing with wastewater treatment, chemical reaction acceleration, and other fields are discussed together with the advantages, disadvantages, and applicability of each type of cavitation generator. We also explore research progress in areas such as cavitation stability, energy efficiency, and equipment design upgrades. The study concludes by forecasting the application prospects of intelligent design and computational fluid dynamics (CFD) in optimizing and advancing cavitation generators. It proposes new ideas for the further development of cavitation technology and highlights directions for its widespread future application.Graphic Abstract
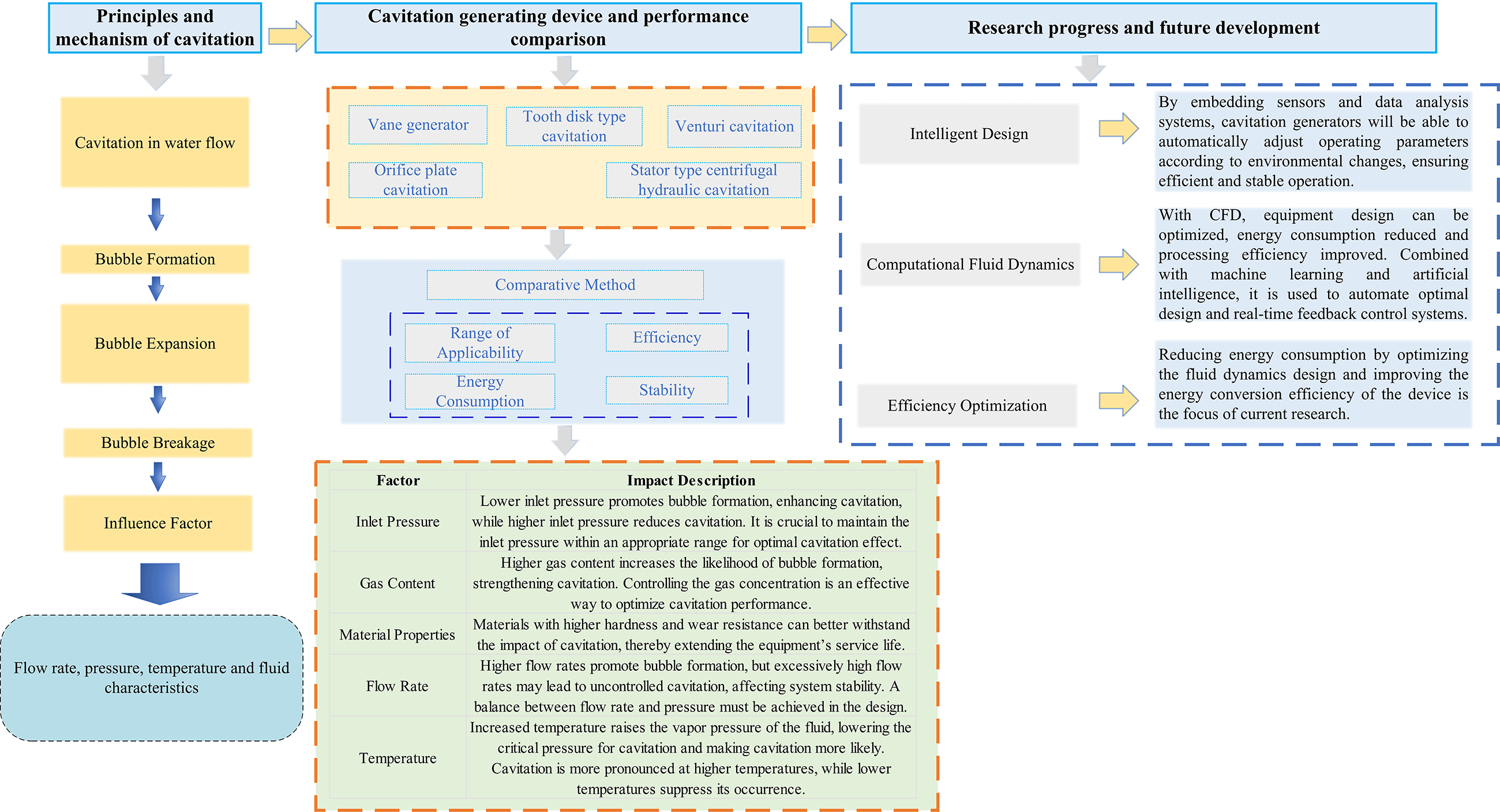
Keywords
Cavitation is a phenomenon where bubbles form when the local pressure in a liquid rapidly drops and collapse quickly when the pressure is restored. The collapse of these bubbles generates extremely high temperatures, localized pressures, high-speed microjets, and intense shear forces. These characteristics make cavitation effects of great significance in various industries, including wastewater treatment, nanomaterial synthesis, food processing, and energy utilization [1]. The unique physical properties of cavitation effects provide new possibilities for the enhancement of various physicochemical processes and are widely applied across multiple fields.
Initially, research on cavitation effects mainly focused on their destructive impacts on equipment, particularly cavitation corrosion in devices such as valves, pumps, and ship propellers [2]. During cavitation, the formation and collapse of bubbles generate intense shock waves and microjets. These high-energy microjets create localized high stresses on equipment surfaces, leading to material fatigue and damage. Prolonged cavitation corrosion not only significantly shortens the lifespan of equipment but also increases maintenance costs and downtime. Cavitation also increases noise and reduces flow efficiency, which in turn affects the stability and reliability of the system. In recent years, researchers have gradually recognized the beneficial properties of cavitation. The extreme high temperatures, high pressures, and intense shear forces generated by cavitation can play an important role in improving industrial process efficiency. In wastewater treatment, the free radicals generated by cavitation can efficiently degrade organic pollutants, significantly improving treatment efficiency [3,4]. In nanomaterial synthesis, cavitation accelerates the reaction process and promotes the uniform dispersion of particles [5–7]. In the food processing sector, cavitation technology is used for disinfection and homogenization, enhancing food quality and safety [8]. Additionally, cavitation effects are applied to improve the conversion efficiency of biomass energy.
Cavitation effects show significant advantages in various applications, but their effective utilization depends on the performance of cavitation generators. The design and operation of cavitation generators directly determine the intensity, stability, and controllability of the cavitation effect. Cavitation generators, such as orifice, acoustic, vortex, and Venturi types, each have unique structural and application advantages, making them suitable for different industrial needs [9,10]. Therefore, a deep understanding and optimization of the working principles of cavitation generators are crucial for enhancing the efficiency of cavitation effect applications.
This review aims to comprehensively analyze cavitation effects and their applications in different cavitation generators, with a focus on comparing the performance of various cavitation generators in practical applications. The paper will explore the structure and working principles of cavitation generators such as orifice, acoustic, vortex, and Venturi types, review the latest advancements in cavitation technology, and propose strategies to enhance the efficiency of cavitation effect utilization, providing valuable insights for researchers in related fields.
2 Cavitation Theory, Influencing Factors and Application Progress
Cavitation is a unique physical phenomenon that occurs in fluid media. When the local pressure of a fluid drops below a certain threshold, specifically its saturated vapor pressure, soluble gases in the fluid are released, forming gas nuclei. These gas nuclei grow and form cavitation bubbles. When the fluid flows through a high-pressure region, the gas nuclei begin to collapse as the pressure increases, a process known as cavitation [11,12]. This process consists of three stages: nucleation of gas bubbles, bubble growth, and collapse. Fig. 1 illustrates the bubble growth cycle. The key to bubble formation is the reduction of local pressure below the fluid’s saturated vapor pressure [13], causing the fluid to vaporize and generate bubbles. This phenomenon commonly occurs when the fluid temperature is high or the local flow velocity is large. When the local pressure decreases, the bubbles grow rapidly. As the bubbles enter a high-pressure area, they shrink quickly, undergoing a collapse process. The gas inside the bubble is compressed, and upon bursting, it releases a large amount of energy, accompanied by phenomena such as local high temperature, high pressure, and micro-jets.
Figure 1: Bubble growth cycle diagram
The high temperatures generated during cavitation can reach up to 5000 K, with jet velocities as high as 400 km/h and pressures up to 50 MPa. While cavitation can cause significant damage to materials and structures, it also releases a large amount of energy that can be harnessed. This process has wide applications in areas such as wastewater treatment, industrial equipment descaling, sterilization, deodorization, and the degradation of organic pollutants.
2.1 Main Factors Affecting Cavitation Occurrence
2.1.1 Influence of Fluid Flow Velocity and Temperature
Liu et al. [14] considered the significant impact of fluid viscosity on bubble pulsation, and obtained the expansion and contraction pulsation patterns of bubbles in glycerin-water solutions with different viscosities. Nazari-Mahroo et al. [15] analyzed the effects on individual bubbles at different densities and found that when using non-constant fluid density, the pressure and temperature inside the bubbles significantly increase during the collapse phase. Yan et al. [13], in his study on the cavitation characteristics of viscous oil liquids, pointed out that due to their low saturated vapor pressure and high gas content, the cavitation mechanism and evolution process in viscous oil liquids differ significantly from vapor-type cavitation in water. Fig. 2 illustrates the development process of cavitation bubbles in pure water.
Figure 2: Development process of cavitation bubbles in pure water. Reference [13], Copyright © 2024, Journal of Mechanical Engineering
As the fluid flow velocity increases, the local pressure decreases during the flow, leading to cavitation in regions with rapid changes in flow velocity. In a Venturi tube, the reduction in cross-sectional area at the throat causes an increase in flow velocity, and when the fluid pressure drops to the saturated vapor pressure, a cavity is formed. When the fluid exits the throat, the local pressure recovers, causing the bubbles to collapse [16].
As the fluid temperature increases, the saturation vapor pressure rises, leading to the occurrence of cavitation. Peng et al. [17] analyzed the impact of fluid temperature on cavitation intensity and found that the bubble rupture strength increases at higher fluid temperatures. Ge et al. [18] conducted experiments in a Venturi-type cross-sectional closed-loop cavitation tunnel, where fluid temperature ranged from 24°C to 55°C. With increasing temperature, the cavitation bubble volume increased, but further temperature rise led to the opposite effect. Zheng et al. [19] studied the temperature effects on the characteristics of a seawater desalination rotating supercavitation evaporator and found that the cavitation evolution pattern was similar across different temperatures, with cavitation intensity increasing as the temperature rose. Wang et al. [20] studied the effects of varying fluid temperatures on long-pulse laser-induced cavitation and used the adiabatic expansion theory to predict the maximum length and width of cavitation bubbles at different fluid temperatures.
2.1.2 Influence of Fluid Flow Velocity and Temperature
When a large amount of gas is dissolved in a fluid, the gases can form bubbles as local pressure decreases, potentially triggering cavitation. Both the type and concentration of dissolved gases influence cavitation occurrence. The gas content plays a crucial role in the formation and collapse of cavitation nuclei, thereby significantly affecting cavitation intensity. Shi et al. [21] studied the impact of dissolved carbon dioxide on the cavitation intensity of underwater water jets. At low concentrations, dissolved CO2 primarily influences cavitation intensity by altering the pH of the water. However, as the CO2 concentration increases, it suppresses cavitation formation. The effect of dissolved salts in seawater, which reduces vapor pressure and increases surface tension to promote cavitation, was demonstrated in a study by Song et al. [22] on nitrogen removal using NaClO₂ in seawater under strong cavitation conditions. The results showed that intense cavitation effectively removes NOx from the seawater solution.
2.1.3 Cavitation Device Design and Operating Conditions
The structure of cavitation devices—such as wall roughness, pipe diameter, and the presence of elbows—along with operating conditions like flow rate, rotational speed, and pressure settings, directly influence cavitation occurrence. Improper structural design can cause local pressure to drop excessively, triggering cavitation effects. Li et al. [23] proposed a method combining Venturi tubes and orifice plates to investigate how parameter variations impact cavitation. As the cross-sectional area of the hole increased, the cavitation effect of the Venturi-type orifice plate was enhanced, and the number of holes further amplified the cavitation effect by altering the cross-sectional area.
Li et al. [24] explored the influence of wall roughness on the cavitation flow field inside a Venturi tube and found that roughness intensifies cavitation effects by increasing the number of micro gas nuclei attached to the inner wall. Ding et al. [16] introduced a semicircular ring protrusion into a Venturi tube to improve cavitation efficiency, concluding that the semicircular shape outperformed triangular and rectangular shapes. Lyu et al. [25] examined the impact of structural parameters in shear-type hydrodynamic cavitation generators on cavitation intensity, finding that an appropriate selection of tooth row numbers increased steam and velocity flow fields. Ren et al. [26] investigated how changes in surface microstructure size affect cavitation erosion, showing that compared to smooth surfaces, microstructured surfaces significantly reduce cavitation damage in martensitic stainless steel. When the width-to-depth ratio is small and the occupancy ratio is large, the gas content on the material surface remains low, helping to mitigate cavitation erosion damage.
Zhang et al. [27] analyzed the effects of pressure and flow on the cavitation behavior of throttling valves, noting that the pressure difference between the valve’s inlet and outlet significantly influences cavitation intensity. A larger pressure difference increases the likelihood of cavitation formation. Flow rate also affects cavitation intensity; as the inlet flow decreases, the cavitation effect weakens [28]. Fang et al. [29] assessed how different driving pressure fields impact the accuracy of cavitation erosion predictions. By using a time-averaged pressure field as the driving pressure, transient erosion strength on the wall during bubble evolution could be captured. Accumulating the transient erosion strength led to a better match between easily eroded areas and experimental erosion results.
2.2 Physical and Chemical Effects of Cavitation on Fluids and Materials
When a cavitation bubble collapses, it generates a local high-temperature and high-pressure environment, accompanied by microjets and shock waves, releasing a significant amount of energy. Leveraging these energy characteristics, hydraulic cavitation has become a commonly used enhancement technique in many industrial processes, with widespread applications in emulsification, advanced oxidation reactions, and nanomaterial synthesis [30]. Cao et al. [31] conducted experiments on the oxidation and decolorization of sugar juice in cavitation and jet cavitation devices. The study found that the interaction between cavitation and oxidation effectively promotes the degradation of sugar juice pigments. Wang et al. [32] proposed a cavitation device based on vortex cavitation, as shown in Fig. 3. The results indicated that the degradation of tetracycline primarily occurs under the strong oxidative action of hydroxyl radicals generated by the cavitation device. During hydraulic cavitation, the collapse of bubbles generates high temperature and pressure, which causes the O-H bonds between water molecules to break, leading to an increase in the conductivity of the aqueous solution. This effect was also used as an indicator to assess cavitation intensity in experiments exploring the impact of parameter changes in Venturi-type orifice plates on cavitation performance. Cavitation can cause surface wear, corrosion, fatigue, and crack propagation, particularly on metal and composite material surfaces. Li et al. [33] investigated the impact of cavitation on WC-Co-Cr coatings in marine environments and found that pure cavitation erosion was the primary cause of coating damage, followed by corrosion-induced cavitation erosion. Wang et al. [34] explored the severe cavitation phenomena typically associated with submerged high-pressure water jets, and studied the cavitation behavior of underwater high-pressure jets using different nozzle outlet shapes, such as the bellows tube nozzle. Zhao Weiguo et al. [35] conducted a numerical analysis of the cavitation suppression effects of bio-inspired hydrofoil structures and identified their optimal structural parameters.
Figure 3: 3D Structure of the vortex cavitation device components. Reference [35], Copyright © 2024, Journal of Drainage and Irrigation Machinery Engineering
Hong et al. [36] and colleagues prepared ceramic-metal coatings, assessed the relationship between the coating microstructure, flow velocity, and cavitation erosion behavior, and discussed the cavitation erosion mechanisms at different flow velocities to mitigate the impacts of cavitation erosion.
2.3 Experimental Methods Exploring Cavitation Evolution
Common experimental methods for cavitation evolution include high-speed photography, optical imaging, and laser particle image velocimetry (PIV). Hu et al. [37] used a high-speed camera to capture the dynamics of cavitation bubble evolution under multiple boundary conditions, as shown in Fig. 4. In the experiment, a capacitor discharges to melt a copper wire, which generates bubbles. The wire’s melting may interfere with the bubble surface, but since the wire diameter is much smaller than the bubble radius, the effect is negligible. All experiments were conducted at room temperature and pressure.
Figure 4: Influence of free surface on jet flow inside bubbles (Yb1 = 1.20, Yb2-1.20). Reference [37], Copyright © 2023, Journal of Drainage and Irrigation Machinery Engineering
3 Cavitator Types and Their Performance Analysis
The working principle of a cavitator relies on the occurrence of cavitation when fluid passes through a specific region where pressure experiences a sudden drop. As the local pressure of the fluid falls below its vapor pressure, bubbles begin to form within the fluid. These bubbles expand and collapse as the fluid flows, with shear forces, turbulence, and flow velocity further contributing to their generation and development. When the bubbles move into regions of higher pressure, they collapse rapidly, releasing energy and creating a local environment of high temperature and pressure. The generation and stability of cavitation are influenced by various factors, including operational parameters such as flow velocity, pressure, and temperature, which directly affect the formation and behavior of cavitation bubbles.
The design of hydrodynamic cavitation generators, including the geometry, hole diameter, and spacing of perforated plates, plays a critical role in determining the intensity and stability of the cavitation effect. A well-designed system can promote efficient bubble generation and collapse, maximizing energy release and improving reaction efficiency. The energy released during bubble collapse can drive chemical reactions, redox processes, and generate free radicals, which are particularly important in applications like water treatment and pollutant degradation. Furthermore, the collapse of cavitation bubbles generates intense mechanical shock waves and localized high temperatures, which enhance the solubility of substances and accelerate reaction rates [38−42].
3.1.1 Fundamental Research and Mechanism Exploration of Cavitation
Zheng et al. [43] studied the optical characteristics of hydrodynamic cavitation within a Venturi tube and found that the collapse of cavitation bubbles is closely related to light intensity. He proposed a method for estimating light intensity based on changes in sound velocity. Soyama [44] conducted experimental research on the sludge degradation performance of a rotor-stator type hydrodynamic cavitation generator and analyzed the effects of shear stress and thermal effects on sludge degradation. The rotor with concave pits significantly improved the reduction rate of sludge particles, and as the rotational speed increased, the sludge degradation effect was further enhanced. Higher inlet pressure and rotational speed were found to have a significant impact on sludge degradation, providing insights for optimizing sludge degradation performance. Fu et al. [45] proposed a new wastewater treatment device based on a rotary hydrodynamic cavitation generator. As the treatment capacity increased, the hydroxyl concentration also significantly increased, and the cavitation intensity of the HLAC (Hydraulic Cavitation Generator) was 54% higher than that of WLAC (Water Liquid Cavitation Generator). Additionally, as the Reynolds number increased, cavitation production capacity decreased, but HLAC, due to its strong cavitation cloud generation ability and better flow characteristics, exhibited higher cavitation production capacity.
3.1.2 Applications of Hydrodynamic Cavitation in Pollutant Removal
Hydrodynamic cavitation technology plays a crucial role in wastewater treatment and the degradation of organic pollutants. Taşdemir et al. [46] improved ammonia removal efficiency in an HDC generator by adjusting factors such as cavitation number, airflow rate, temperature, and initial concentration, achieving significant removal efficiency without the need for air. Sun et al. [47] explored the application of a rotary hydrodynamic cavitation generator in water treatment, particularly in wastewater treatment. The generator was able to effectively remove harmful substances from water in a short period, achieving higher removal efficiency.
3.1.3 Shear-Type Cavitation Generator
Yuan et al. [48] studied a toothed-disc mechanical shear cavitation generator and found that vortex flow between the teeth and mechanical shear are the primary mechanisms for cavitation bubble formation, with the longitudinal profile of the shear disc shown in Fig. 5. As rotational speed, feed flow rate, and processing time increased, cavitation rate significantly improved. Moreover, the hydroxyl concentration generated by the toothed-disc cavitation generator was higher than that of the Venturi tube, demonstrating its superior cavitation performance.
Figure 5: Longitudinal section of the shear disc. Reference [48], Copyright © 2021, Chemical Engineering.
Wang et al. [49] conducted a cavitation mechanism analysis on rotor-stator centrifugal hydrodynamic cavitation generators and identified three types of cavitation mechanisms inside the cavitation generator: blunt-body flow cavitation, trailing vortex cavitation, and wedge-shaped groove cavitation. In the study of rotating hydrodynamic cavitation generators, Wang et al. [50] optimized the cavitation performance of the generator by improving the rotor blade design. The curved rotor significantly increased cavitation intensity and cavitation rate. Additionally, adjusting the rotor blade inlet angle further enhanced cavitation performance, and increasing the inlet angle of the blades led to a substantial improvement in both cavitation intensity and overall generator performance.
3.2 Orifice Plate Cavitation Generator
The orifice plate cavitation generator utilizes the flow restriction effect of the orifice plate to induce cavitation phenomena near the plate. Its operating principle and design rely on the sharp drop in pressure as fluid passes through the orifice plate. The formation and collapse of cavitation bubbles under certain operating conditions can effectively trigger a series of changes in flow characteristics and energy release. Orifice plate cavitation generators play an important role not only in fluid flow control but also in various applications such as wastewater treatment, chemical reactions, and mineral processing. The following discussion will focus on the design optimization, cavitation flow characteristics, and applications of orifice plate cavitation generators [51−53].
3.2.1 Working Principle and Design of Orifice Plate Cavitation Generator
The orifice plate cavitation generator regulates cavitation phenomena by altering the geometric shape of the orifice plate and the operational conditions of the fluid. The fundamental principle is that the orifice plate, or a porous plate, creates resistance to fluid flow, causing a sharp drop in pressure as the fluid passes through the plate. When the fluid pressure drops below the vaporization pressure, cavitation bubbles form. The formation and collapse of these cavitation bubbles release substantial energy, which affects the stability and efficiency of the system. Therefore, optimizing the orifice plate design, minimizing cavitation, and controlling cavitation intensity are crucial for improving system performance and extending equipment life.
Zhang et al. [54] proposed an optimized design for single-hole orifice plates by adopting a converging plane with a diffused hole shape and optimizing its geometry using a multi-objective optimization method. Through numerical simulations, the effect of different converging angles on cavitation behavior was studied. The converging angle plays a dominant role in cavitation control. The optimized orifice plate design significantly reduced the occurrence of cavitation and minimized the downstream jetting area, thereby reducing pipeline vibration and energy losses caused by cavitation.
Li et al. [55] proposed an improved cavitation model for high-pressure environments such as nuclear power plant and aircraft engine fuel pipelines, combining local flow characteristics, supervised learning, and genetic algorithms. The diameter ratio of the orifice plate and the pressure drop have significant effects on flow rate and cavitation characteristics. The cavitation prediction model was optimized using genetic algorithms, and empirical formulas based on the diameter ratio and pressure drop were derived to effectively control cavitation phenomena [56].
Han et al. [57] studied the effects of the number of holes and plate thickness of the orifice plate on the hydraulic cavitation effect. The number of holes and plate thickness significantly influenced cavitation intensity under different pressure differentials. As the inlet pressure increased, cavitation intensity gradually increased, stabilizing after reaching a certain pressure level. The number of holes, hole shape, and plate thickness of the orifice plate have a significant impact on the cavitation effect [58]. A five-hole orifice plate showed the best cavitation effect within a pressure differential range of 0.2 to 0.6 MPa, while a three-hole orifice plate performed best within a 0.6 to 1 MPa pressure differential range. Additionally, the hole shape had a minor effect on cavitation intensity, with the overall circular orifice plate exhibiting the best cavitation performance.
The key to optimizing the design of the orifice plate cavitation generator lies in the precise control of the geometric parameters of the orifice plate and the fluid flow conditions. Factors such as the number of holes in the plate, plate thickness, hole shape, and pressure drop directly affect the intensity of cavitation and the flow characteristics. By using a multi-objective optimization approach, the orifice plate design can be optimized to reduce cavitation phenomena and improve cavitation performance.
3.2.2 Orifice Plate Cavitation Flow Characteristics
The cavitation flow characteristics of an orifice plate cavitation generator are influenced by multiple factors, including the geometry of the orifice plate, pressure conditions, and the flow velocity of the fluid. Yue et al. [59] investigated the critical pressure ratio for orifice plate cavitation and examined the impact of surface pits on the critical cavitation pressure ratio. Cavitation occurs only when the outlet-to-inlet pressure ratio is less than 0.5. Further experiments revealed that surface pits on the orifice plate can promote the formation and development of cavitation bubbles [60], particularly when the pressure ratio approaches the critical cavitation pressure ratio, at which point the effect of pit defects on cavitation behavior becomes more pronounced. These findings provide a theoretical foundation for mitigating cavitation damage caused by pits in orifice plate design.
Mai et al. [61] analyzed the vibration characteristics of porous orifice plates at various stages of cavitation. As cavitation intensity increased, the vibration acceleration downstream of the orifice plate significantly rose, with the vibration exhibiting a broad frequency range. A study on the effect of porosity on the critical cavitation number indicated that orifice plates with lower porosity experienced cavitation earlier as the critical cavitation number was approached. Conversely, increasing the porosity delayed the onset of cavitation. Based on cavitation flow resistance curves, plates with higher porosity exhibited greater flow resistance, which increased significantly as the cavitation number rose. Optimizing the porosity design of the orifice plate helps delay cavitation onset and reduces the negative impact of cavitation on system performance.
The application of orifice plate cavitation generators in water treatment and organic pollutant degradation has become increasingly widespread. Qin et al. [62] investigated the experimental process of enhancing degradation effects using an orifice plate cavitation generator in aqueous solutions. By adjusting parameters such as the number of holes in the orifice plate, inlet pressure, and solution temperature, a negative pressure-assisted hydrodynamic cavitation (NPA-HC) system significantly improved the degradation and mineralization rates of methylene blue (MB). Under low temperatures, high inlet pressures, and moderate dye concentrations, the NPA-HC system achieved superior degradation results. Mali et al. [63] studied the cavitation characteristics of orifice plates in flow control devices used in nuclear power plants, focusing on the role of honeycomb-shaped orifice plates in flow and cavitation. Parameters such as flow area, plate spacing, and the number of orifice plates significantly affect cavitation phenomena and pressure drop. Increasing the number of orifice plates can reduce cavitation occurrence, while decreasing the flow area of the plates increases the likelihood of cavitation and pressure drop.
3.2.3 Optimization and Improvement of Orifice Plate Cavitation Generators
As research on orifice plate cavitation generators has deepened, many scholars have focused on optimizing the design of orifice plates and experimental conditions to improve cavitation performance and reduce the damage caused by cavitation to equipment. Zhang et al. [64] proposed an improved backpropagation neural network prediction model for efficiently obtaining the cavitation characteristics near throttling orifice plates in nuclear-grade pipelines. By combining the Latin Hypercube Sampling (LHS) method with CFD simulations, the study investigated the influence of geometric parameters, such as orifice diameter and inlet opening angle, on the minimum cavitation number. The prediction model’s accuracy was optimized through genetic algorithms. The orifice diameter and inlet opening angle showed strong global sensitivity to the cavitation number, and the root mean square error of the model’s predictions was reduced by approximately 36.4%.
Osman et al. [65] studied the application of porous orifice plates in cavitation and used CFD simulations to analyze the interactions between adjacent holes and their impact on bubble formation and downstream flow turbulence. Increasing the number of holes in the orifice plate, rather than the hole size, was found to be more effective in optimizing cavitation performance. Additionally, the thickness of the orifice plate significantly influenced the direction of the jet flow, highlighting the crucial role that the geometry and hole distribution of the orifice plate play in flow characteristics and cavitation intensity.
Xu et al. [66] conducted research on the cavitation characteristics of orifice plate cavitation generators under high-temperature and high-pressure environments and proposed an adaptive variational modal decomposition algorithm based on genetic algorithms to analyze the relationship between pressure pulsation signals and cavitation phenomena in orifice plate cavitation generators. Increasing the cross-sectional area of the orifice plate significantly improved cavitation performance, and under the same cross-sectional area, multi-channel orifice plates exhibited better cavitation effects than single-channel plates. Further studies explored the impact of orifice plate channel structure parameters on cavitation performance. The analysis of the effects of channel cross-sectional area, hole distribution, hole dispersion, and surface roughness on cavitation performance showed that, under the same channel cross-sectional area, multi-channel orifice plates performed better than single-channel plates. Increasing the channel cross-sectional area effectively enhanced cavitation performance. Additionally, lower surface roughness of the orifice plate channels promoted cavitation, and orifice plates with smaller hole spacing exhibited better cavitation effects.
3.3 Venturi Cavitation Generator
The Venturi cavitation generator is a device that utilizes the principle of accelerating fluid flow in a constricted pipeline, leading to a pressure drop, thereby inducing cavitation. The design of the Venturi cavitation generator typically consists of two main sections: the converging section and the diverging section. The purpose of the converging section is to accelerate the fluid flow, reduce the pressure, and promote cavitation, while the diverging section serves to decrease the flow velocity and restore the fluid pressure [67,68]. The geometry, length, and minimum diameter of the pipeline in both the converging and diverging sections directly affect the intensity of the cavitation effect, the size of the bubbles, and the distribution of cavitation bubbles. Precise structural design and flow field optimization are crucial for achieving effective cavitation [69,70].
3.3.1 Numerical Simulation and Study of Venturi Cavitation Flow
In recent years, research on Venturi cavitation generators has primarily focused on the simulation and experimental analysis of cavitation flow, with particular attention to the effects of cavitation phenomena on pressure fluctuations, flow characteristics, and cavitation intensity. Korneev et al. [71] proposed a mathematical model based on the continuity equation and the Navier-Stokes equation to describe unsteady turbulent cavitating flow in a Venturi pipe. He combined this with a comprehensive cavitation model to study the amplitude-frequency characteristics of pressure self-oscillations.
Wang et al. [72] conducted a numerical simulation of cavitation flow in a Venturi pipe using Large Eddy Simulation (LES) methods. He developed a modified prediction model to quantitatively describe the relationship between cavitation evolution and induced pressure fluctuations. This model improves the prediction accuracy of pressure fluctuations, particularly in narrow channels, by considering the “blocking effect” of cavitating flow, which enhances the model’s ability to predict pressure fluctuations in Venturi pipes.
In nuclear power plant applications, Venturi flow meters are commonly used for cavitation flow limitation protection under overflow conditions. Zhou et al. [73] combined FLUENT numerical simulations with high-speed camera experiments to investigate the simulation effects of various cavitation models on the cavitation flow limitation phenomenon in Venturi pipes. The Zwart-Gerber-Belamri cavitation model, coupled with the shear stress k-ω turbulence model, was found to accurately simulate the cavitation flow limitation phenomenon, capturing both periodic cavitation and microscopic flow behavior.
Liang et al. [74] employed LES and the Zwart-Gerber-Belamri cavitation model to numerically simulate the flow in a Venturi pipe under different cavitation numbers. The steam volume fraction contour map is shown in Fig. 6. He analyzed the discrepancies between the simulation results and experimental data, noting that the pressure ratio at the inlet and outlet, as well as the pressure coefficient at monitoring points, exhibited low uncertainty across various operating conditions, thus validating the applicability of this method for LES simulations of internal flow in Venturi pipes.
Figure 6: Steam volume fraction contour. Reference [74], Copyright © 2022, Journal of Chinese Ship Research
Hong et al. [75] studied the cavitation energy characteristics within a Venturi cavitation generator and proposed a physical model for assessing cavitation energy. Numerical analysis was conducted using the LES-WALE turbulence model and the Schnerr-Sauer cavitation model. As the cavitation number decreases, cavitation energy gradually increases, with the peak energy observed at the tip of the sheet-like cavity. The highest cavitation energy is found at the junction between the throat and the diffuser section. This study provides an effective computational method for evaluating cavitation energy.
3.3.2 Influence of Fluid Medium on Venturi Cavitation Intensity
In addition to the fluid itself, the presence of solid particles also has a significant impact on cavitation phenomena. Shi et al. [76] investigated the effect of solid particle concentration on cavitation effects within a Venturi tube. As the concentration of solid particles increased, the cavitation intensity significantly increased, particularly at higher solid mass concentrations, where the generation of cavitation bubbles became more intense. The presence of solid particles facilitates the collapse of bubbles and exacerbates the formation of local high-temperature and high-pressure environments.
Li et al. [77] proposed a novel internal Venturi tube design that addresses the poor cavitation performance of series-connected Venturi tubes and the large footprint of parallel-connected Venturi tubes. The study investigated the effects of inlet pressure and structural parameters on cavitation performance. As shown in Fig. 7, the gas content distribution contour maps at different inlet pressures revealed that the cavitation performance of the Venturi tube was optimal when the inlet pressure reached 0.7 MPa, and the optimized structural parameters significantly improved cavitation performance.
Figure 7: Gas content distribution contour map at different inlet pressures. Reference [77], Copyright © 2024, Science Technology and Engineering
3.3.3 Applications and Challenges of Venturi Cavitation Devices
The Venturi cavitation device has been widely applied in various fields, especially in the preparation of graphene, wastewater treatment, fluid dispersion, and surface cleaning, achieving significant progress. In the preparation of graphene, the cavitation effect, through the high-temperature and high-pressure environment generated by bubble collapse, promotes the exfoliation and dispersion of graphene, significantly improving yield and quality. This process not only reduces the cost of traditional preparation methods but also effectively controls the quality of graphene, avoiding the common contamination and instability issues found in traditional chemical methods.
Despite its good performance in various applications, the Venturi cavitation device still faces multiple challenges under high-load conditions. Cavitation devices often experience stability issues under high-load conditions, leading to instability during bubble formation and collapse. The noise and vibration generated during cavitation are also relatively strong, affecting the equipment and operating environment, hindering precise process control. In high-pressure environments, the repeated generation and collapse of cavitation bubbles can impact the equipment surface, causing material wear and fatigue, thus shortening the device’s lifespan. To address these issues, researchers have begun optimizing the design of Venturi cavitation devices to reduce the adverse effects of cavitation on equipment. The use of porous materials and coating technologies has been proven to effectively mitigate the impact of bubble collapse on the equipment surface, thereby extending the device’s lifespan [78]. Meanwhile, improvements in fluid dynamics design and optimization of operational parameters are key areas of current research. By controlling the generation and collapse of cavitation bubbles, the stability and controllability of the cavitation effect can be enhanced.
3.4 Acoustic and Vortex Cavitation Generators
Common acoustic cavitation generators include ultrasonic cavitation generators, as well as low-frequency and high-frequency acoustic cavitation. The ultrasonic cavitation effect refers to a series of dynamic processes where sound pressure alternates periodically as sound waves propagate through the liquid. This creates compression and expansion phases. Small gas bubbles in the liquid grow during expansion and collapse during compression [79]. Wang et al. [80] studied the effects of swirling jet cavitation, ultrasonic cavitation, and their combination with H2O2 on the degradation of the reactive dye Brilliant Red K-2BP. The results showed that the combination of hydraulic cavitation and H2O2 has a clear synergistic effect. The degradation process follows pseudo-first-order kinetics. Higher temperature, pressure, and H2O2 concentration help improve degradation efficiency. Chuai et al. [81] used a dual-frequency ultrasonic cavitation structure. The synergistic effect of dual-frequency ultrasound greatly enhanced the collapse effect of cavitation bubbles, thus improving cavitation intensity. Compared to single-frequency ultrasound, dual-frequency ultrasound reduces cavitation shielding, lowers the cavitation threshold, and produces a stronger cavitation effect. A vortex cavitation generator lowers local pressure by generating vortex flow, which forms bubbles in the liquid. Vortex cavitation technology shows great potential in treating tetracycline wastewater. The designed vortex cavitator, through CFD simulation and experimental validation, successfully generated a significant vortex cavitation effect. This mainly degrades tetracycline through the oxidation of hydroxyl radicals. At pH 7.0, the degradation efficiency of a 2.0 mg/L tetracycline solution reached 76.45% in 50 min [82].
3.5 Cavitation Effect Stability
The stability of cavitation effects is a key issue in fluid dynamics and engineering applications. It mainly involves cavitation instability, noise, vibration, erosion, and surface damage. To address these challenges, researchers adjust operational parameters using active control systems or apply surface modification techniques, such as microstructured surfaces, to control bubble formation and collapse. Noise and vibration caused by cavitation can be reduced by using damping materials, vibration isolation techniques, or pressure pulsation control to stabilize the flow in the cavitation region. To address erosion, erosion-resistant materials, coatings, or optimized surface designs are used to increase hardness and reduce damage. Advanced computational fluid dynamics models and machine learning techniques can accurately predict cavitation occurrence and intensity, helping optimize designs and avoid potential risks. By combining materials engineering, simulation technology, real-time control systems, and design optimization, cavitation stability issues are effectively addressed, improving system reliability and efficiency.
3.6 Potential Issues Related to the Phenomenon of Cavitation
Various suppression techniques can be used to address the potential issues caused by cavitation. Surface modification techniques, such as microstructured surfaces or shot peening, can effectively improve the material’s resistance to cavitation erosion. Active control systems monitor the fluid state in real-time and dynamically adjust operational parameters, such as flow rate and pressure, to reduce cavitation occurrence and improve system stability. Flow path optimization design suppresses bubble formation by altering geometry or adding guide vanes, thus controlling cavitation. Additionally, using low surface tension fluids or additives can reduce the formation and collapse speed of bubbles, thereby enhancing the cavitation resistance of the fluid. Flow stabilization technologies, such as flow control valves and pressure regulators, help reduce cavitation issues caused by pressure fluctuations. To reduce noise and vibration caused by cavitation, damping materials and vibration isolation devices can significantly improve system stability. CFD simulation technology can accurately model the cavitation process, helping to predict the occurrence and intensity of cavitation, optimizing the design, and avoiding potential risks.
The effects of cavitation in different scenarios include equipment damage, efficiency loss, noise and vibration, and energy loss. The intense pressure shock generated by cavitation bubble collapse causes corrosion, fatigue, and damage to equipment surfaces, especially in pumps, turbines, and valves. At the same time, cavitation can cause flow instability, increased noise, and efficiency loss, affecting pump and turbine performance, and may even prevent proper fluid flow. Bubble collapse not only affects equipment operation but also generates noise and vibration, impacting the system’s working environment and service life. Energy loss caused by cavitation reduces the overall system efficiency, especially in fluid transmission systems, where cavitation decreases hydraulic power transmission efficiency, affecting overall performance.
High-speed operation of hydraulic pumps can reduce pump volume, lower power source costs, and achieve energy savings while meeting the same flow requirements. However, the suction cavitation issue during high-speed operation is a major challenge in the high-speed operation of hydraulic pumps. Yang et al. [83] studied the suction cavitation issue of high-power dual gear pumps at high rotational speeds through theoretical analysis and simulation. He identified the critical speed for noticeable cavitation and the critical suction pressure for suppressing flow pulsation rise, and proposed a new type of centrifugal impeller supercharged oil pump. The use of a pressurization device to increase the pump’s inlet pressure significantly improved the cavitation suppression effect and enhanced the effective flow of the gear pump.
4 Comparison of Performance among Different Cavitation Devices
4.1 Performance of Venturi Cavitation Devices
The design of Venturi cavitation devices typically consists of a contraction section, a throat section, and an expansion section. The contraction section rapidly increases the fluid velocity and sharply decreases the pressure, which promotes the occurrence of cavitation [84]. The design of the throat section is crucial for the formation of cavitation bubbles, as the sudden drop in local pressure causes the fluid to reach its vaporization pressure, leading to the formation of cavitation bubbles. As the fluid enters the expansion section, the velocity gradually decreases, and the pressure gradually recovers. During this process, cavitation bubbles gradually collapse and release a large amount of energy, creating intense local high-temperature and high-pressure conditions, which further enhance the cavitation effect. Effective control of this process not only improves the reaction rate but also facilitates the removal of pollutants and the dispersion of substances.
In terms of cavitation intensity, Venturi cavitation devices can generate uniform and stable cavitation phenomena over a wide range by precise design and appropriate control of operating conditions. The formation and collapse of cavitation bubbles, along with the energy released, can be enhanced by adjusting parameters such as the geometry of the contraction section, the fluid velocity, and the minimum diameter of the pipe, thereby improving the efficiency of the cavitation device. Studies have shown that optimizing the geometric structure of the Venturi cavitation device significantly enhances cavitation intensity, which in turn improves the efficiency of the device in wastewater treatment, chemical reactions, and other applications.
Regarding energy conversion efficiency, Venturi cavitation devices typically exhibit high energy conversion efficiency [85]. However, factors such as fluid temperature, viscosity, and pressure may influence the cavitation effect, particularly in high-viscosity fluids or high-temperature environments, where the cavitation effect may be weakened. Therefore, to ensure optimal cavitation performance, careful control of operating conditions is required. Proper control of fluid velocity and pressure changes can maximize the cavitation effect while minimizing unnecessary energy losses.
Venturi cavitation devices, due to their simple design and stable operation, are widely used in various fields, including wastewater treatment, bubble generation, material degradation, surface cleaning, and chemical reaction acceleration. In the field of wastewater treatment, Venturi cavitation devices are highly efficient at breaking down organic pollutants, showing excellent adaptability, especially in handling high-concentration wastewater [86]. They perform exceptionally well in treating organic pollutants and industrial wastewater, significantly improving treatment efficiency. However, the cavitation effect in Venturi devices may become unstable under high-load or high-temperature conditions, which requires optimizing operational conditions to maintain stable performance.
4.2 Performance of Orifice Cavitation Devices
The performance of orifice cavitation devices is highly influenced by the geometric design of the orifice plate, fluid velocity, pressure, and other operational conditions. Parameters such as the orifice diameter, the number of orifices, and the spacing between orifices directly affect cavitation occurrence, the formation and collapse of cavitation bubbles, and the release of cavitation energy [87]. Research has shown that smaller orifice diameters result in a greater local pressure drop as fluid passes through the orifice plate, thereby enhancing the cavitation effect. However, excessively small orifice diameters may increase flow resistance, negatively impacting overall cavitation performance. Consequently, it is essential to carefully select the orifice diameter and number of orifices. Increasing the number of orifices can further enhance the local pressure drop, thereby improving cavitation intensity [88].
The spacing between orifices and the shape of the orifices also significantly influence cavitation performance. Smaller orifice spacing tends to generate more turbulence in the fluid, promoting cavitation. Regarding orifice shape, studies indicate that circular orifices are more effective in generating cavitation bubbles than square or triangular orifices under identical operating conditions. This is because the circular orifice design facilitates a more uniform pressure drop across the fluid, promoting stable cavitation bubble formation and enhancing the cavitation effect.
Fluid velocity and pressure also play critical roles in the performance of orifice cavitation devices [89]. As fluid velocity increases, the local pressure drop across the orifice plate becomes more pronounced, thereby intensifying the cavitation effect. Higher velocity not only enhances cavitation bubble formation but also amplifies the energy released during bubble collapse, further increasing cavitation intensity. Pressure regulation is another key factor influencing cavitation performance. Within a certain pressure range, increasing pressure strengthens the cavitation effect; however, excessively high pressure can destabilize cavitation bubbles, thus reducing system efficiency [90]. Therefore, proper control of fluid velocity and pressure is essential for maintaining the efficient operation of orifice cavitation devices.
The stability of cavitation phenomena is crucial for sustaining a high-efficiency cavitation effect. To ensure this stability, it is important to design the orifice plate geometry effectively and adjust operational conditions, such as fluid velocity and pressure, to enable stable formation and collapse of cavitation bubbles. This, in turn, ensures long-term efficient operation.
Orifice cavitation devices, due to their simple structure, low cost, and high cavitation efficiency, have found widespread applications across various industrial fields, including wastewater treatment, chemical reaction acceleration, bubble generation, and material degradation. In wastewater treatment, orifice cavitation devices are highly effective in breaking down organic pollutants, showing excellent adaptability, especially when handling high-flow and high-concentration wastewater. These devices not only improve wastewater treatment efficiency but also reduce energy consumption, making them suitable for large-scale industrial applications [91]. Additionally, in the field of chemical reaction acceleration, orifice cavitation devices significantly increase reaction rates, optimize the reaction process, and are widely used in catalytic and oxidation reactions, among others.
4.3 Performance of Disc-Type Mechanical Shear Cavitation Devices
The cavitation intensity of disc-type cavitation devices is closely related to their operating parameters. Higher rotational speeds result in stronger shear forces within the cavitation device, making bubble generation and cavitation phenomena more pronounced. As the feed flow rate increases, the residence time of the fluid within the cavitation device also increases, providing more opportunities for cavitation to occur and thus enhancing the cavitation effect [92]. Extending the processing time allows the fluid to be exposed to cavitation conditions for longer periods, providing more favorable conditions for cavitation reactions.
The cavitation performance of disc-type mechanical shear cavitation devices is also significantly influenced by the geometric design of the discs. Factors such as the tooth design, the spacing between teeth, and rotational speed affect bubble formation and collapse. Experimental studies have shown that smaller tooth gaps generate stronger shear forces, thereby enhancing the cavitation effect [93,94]. Additionally, optimized tooth designs can help distribute shear forces more evenly across the fluid, promoting uniform bubble generation and stable collapse. Further optimization, such as precise adjustments of tooth shape, tooth gap spacing, and the design of fluid flow paths within the disc, can significantly improve the device’s performance.
Disc-type mechanical shear cavitation devices demonstrate significant advantages in wastewater treatment [95]. They exhibit high cavitation intensity, effectively decomposing organic pollutants and removing bacteria. When treating high-concentration organic wastewater, disc-type cavitation devices show excellent adaptability and efficiency. The energy released during bubble formation and collapse not only disrupts the molecular structure of pollutants but also promotes microbial degradation. Compared to traditional hydrodynamic cavitation devices, disc-type mechanical shear cavitation devices generate more bubbles in a shorter time and enhance cavitation intensity through stronger shear forces, significantly improving wastewater treatment efficiency [96]. Moreover, these devices can achieve efficient pollutant removal with lower energy consumption, reducing operational costs.
In the field of chemical reaction acceleration, disc-type cavitation devices also find extensive applications. The extreme localized temperatures and pressures generated by cavitation phenomena accelerate chemical reactions, particularly those requiring high-temperature and high-pressure conditions. The energy released during bubble collapse provides an ideal reaction environment. Additionally, this energy promotes intense collisions between reactants, further accelerating the reaction process. Disc-type cavitation devices maintain stable cavitation effects even under high-load operating conditions, making them highly reliable and durable for industrial applications [97,98]. Furthermore, these devices are well-suited for processing high-viscosity fluids. While many traditional cavitation devices perform poorly with high-viscosity fluids, disc-type cavitation devices overcome this limitation by enhancing shear forces, ensuring the smooth progression of cavitation reactions. Table 1 shows the influence of various factors on cavitation performance.
4.4 Performance of Hydrodynamic Cavitation Generators
The performance of hydrodynamic cavitation generators is influenced by multiple factors, primarily including flow rate, pressure, generator geometry, and operating parameters. Firstly, a higher flow rate accelerates the fluid through the throttling device, resulting in a stronger cavitation effect, increasing both the frequency and intensity of cavitation bubble formation. The flow rate inside the generator must be precisely controlled to meet cavitation requirements while avoiding excessive flow rates that could lead to energy waste or instability in the cavitation phenomenon [99]. Secondly, the pressure conditions inside the generator directly affect cavitation intensity. When the fluid passes through the throttling device, the pressure drops to a certain level, and bubbles begin to form within the fluid. Appropriate pressure regulation helps improve cavitation effects and optimize chemical reaction processes.
The geometric design of the generator also plays a crucial role in cavitation performance. The design of the flow path, the geometry of the throttling device, and factors such as aperture size directly determine the bubble generation and collapse processes. A well-designed generator structure ensures more uniform flow of the fluid inside the generator, preventing cavitation from becoming overly concentrated or unstable in localized areas [100]. Additionally, factors such as the cross-sectional area of the generator, the arrangement of throttling devices, and the shape of the flow channels influence the flow velocity and pressure distribution, thereby affecting bubble formation and cavitation effects.
Energy consumption in hydrodynamic cavitation generators is one of the key indicators for performance evaluation. As cavitation involves the rapid flow of fluid under high pressure, energy consumption is inevitable. The primary sources of energy consumption in hydrodynamic cavitation generators are the high-pressure pumping of the fluid and the bubble generation process. By improving generator design—such as optimizing throttling devices, flow channel shapes, and generator geometry—energy consumption can be effectively reduced while enhancing energy conversion efficiency. Furthermore, optimizing operating parameters such as flow rate, pressure, and reaction time can significantly enhance cavitation effects without increasing energy consumption, thus improving the overall operational efficiency and economics of the generator.
The high temperature and pressure environment created by cavitation may cause wear on generator materials and structures, so it is essential to use wear-resistant and corrosion-resistant materials to ensure the long-term durability of the generator. Maintaining cavitation stability over extended operating periods and preventing excessive fluctuations in cavitation bubble formation is also a challenge. By optimizing the internal flow path of the generator and strengthening the stability control of the cavitation phenomenon, irregular bubble formation can be avoided, ensuring the long-term stable operation of the equipment. For the treatment of high-load, high-viscosity fluids, hydrodynamic cavitation generators demonstrate strong adaptability, effectively overcoming the flow resistance of high-viscosity fluids and ensuring smooth cavitation processes.
Different types of cavitation devices each offer unique advantages for industrial applications. Selecting the appropriate cavitation device is crucial for enhancing treatment efficiency and reducing costs. Table 2 provides a comparative summary of the performance and applications of various types of cavitation devices.
4.5 Optimizing Cavitation Generators through the Integration of Different Approaches
4.5.1 Strategies and Approaches for Enhancing Energy Conversion Efficiency in Cavitation Generators
To improve the energy conversion efficiency of cavitation generators, optimization can be carried out from multiple aspects. The geometric design of cavitation generators is crucial to the bubble formation and collapse process. Optimizing the shape of the fluid passage can more efficiently generate cavitation bubbles. Optimizing the geometry through computational fluid dynamics simulations can reduce energy loss and improve the stability of the cavitation effect. At the same time, optimizing the design of the fluid supply system to ensure uniform fluid flow and provide sufficient pressure helps reduce energy waste and avoid cavitation instability caused by uneven flow or pressure fluctuations. The choice of fluid also has a significant impact on energy conversion efficiency. The physical properties of the fluid, such as viscosity, surface tension, and density, directly affect cavitation phenomena and the stability of bubbles. Choosing liquids with low surface tension and high vaporization potential can enhance the energy utilization in the cavitation effect. Multi-frequency cavitation excitation technology can enhance cavitation energy density by exciting cavitation at multiple frequencies, optimizing bubble generation and collapse, thereby improving overall efficiency.
Precisely controlling the micro characteristics of cavitation bubbles can also significantly improve energy conversion efficiency. By adjusting the operating conditions of the cavitation generator, such as pressure, temperature, and flow rate, bubble generation, size, and collapse can be optimized, enhancing the cavitation effect. Combining real-time monitoring with a dynamically adjusted intelligent control system ensures the equipment operates at its optimal working state, thereby improving energy efficiency. Reducing noise and vibration during the cavitation process is key to improving energy conversion efficiency. By applying technologies such as acoustic isolation, vibration dampers, and active noise control, energy loss and mechanical vibration caused by cavitation can be effectively reduced, improving the overall system efficiency.
4.5.2 The Optimization of Cavitation Generators through Interdisciplinary Approaches
By combining machine learning and artificial intelligence, intelligent design significantly improves the design efficiency of cavitation generators. This system automatically optimizes the geometry and operating conditions based on simulation results, enhancing cavitation performance while reducing adverse effects such as noise, vibration, and erosion. Identifying the optimal geometric configuration and material selection, even small changes in geometry, can have a significant impact on cavitation behavior. Intelligent design also enables multi-objective optimization, maximizing cavitation intensity while minimizing erosion, thus balancing performance and durability. The intelligent design system can adaptively adjust based on real-time operational feedback, continuously optimizing the design of the cavitation generator to improve its performance and reliability.
Computational fluid dynamics plays a crucial role in cavitation prediction and control. Through simulations, the cavitation process can be comprehensively modeled, including bubble formation, growth, collapse, and interaction with solid surfaces. This allows designers to intuitively understand cavitation behavior, identify pressure fluctuations and erosion issues caused by cavitation, and optimize the flow field to avoid the formation of low-pressure regions, thereby improving the stability and controllability of the cavitation generator. CFD can also be combined with other simulation tools to provide a more comprehensive design optimization approach. In particular, in cavitation generator design, cavitation may cause mechanical and thermal stresses, and combining structural analysis and thermal simulations effectively evaluates and optimizes the design.
By combining intelligent design with computational fluid dynamics simulations, it is possible to not only predict the immediate performance of the cavitation generator but also assess its long-term performance and durability. CFD can predict the impact of cavitation bubble collapse on surfaces, helping to identify areas that are susceptible to cavitation erosion, providing a basis for developing materials or coatings resistant to cavitation erosion. CFD also helps select appropriate materials and surface treatments by simulating the interaction between different materials and cavitation bubbles, optimizing material cavitation resistance and extending the service life of the cavitation generator.
Machine learning algorithms train surrogate models based on simulation data, enabling quick and accurate prediction of new design parameters, thereby improving design efficiency and avoiding complex calculations. By combining CFD simulations with machine learning, hybrid systems can also perform real-time optimization during actual operations, adjusting the cavitation generator’s working state based on real-time data, achieving adaptive control, and further improving system efficiency and reliability.
Through intelligent design and CFD technology, the design of the cavitation generator can be optimized to achieve the desired effect while reducing damage to the system. In energy production systems such as hydropower, cavitation affects turbine performance. Optimized design helps improve turbine design, reduce cavitation damage, and enhance efficiency and equipment lifespan. Cavitation generators are also widely used in processes such as ultrasonic cleaning, material surface treatment, and graphene production. The optimization of intelligent design and CFD technology can improve the efficiency, economics, and environmental friendliness of these processes.
4.6 Evaluate the Performance of Different Cavitation Generators
This paper evaluates the performance of different cavitation generators and analyzes the impact of various types of cavitation generators on cavitation intensity and stability. The experiment uses a closed-loop flow system, including a liquid reservoir, pump, flowmeter, and cavitation generator. The pump flow rate is adjustable to simulate different operating conditions. Pressure sensors are installed at multiple positions in the loop to monitor pressure changes in real-time and detect cavitation occurrence. Flow rate is controlled by adjustable valves, and the electromagnetic flowmeter measures it precisely. To observe the dynamic behavior of bubbles, high-speed cameras and laser-induced fluorescence technology are used to capture the formation process of bubble clouds.
Pure water is used as the base fluid in the experiment due to its simple thermodynamic properties and its common use in cavitation research. The flow range is adjusted based on different cavitation generators and experimental requirements, and the inlet pressure range simulates different operating conditions. Pressure drop across the cavitation generator is precisely monitored to determine the cavitation threshold. Cavitation performance is evaluated using the cavitation number, which is an important parameter for assessing cavitation intensity. It is defined as the ratio of the difference between inlet pressure and fluid vapor pressure to the square of flow velocity. The specific Formula (1) is as follows [100]:
σ=Pinlet−Pvapor12ρv2(1)
Here, Pinlet represents the inlet pressure, Pvapor is the vapor pressure of the fluid, ρ is the fluid density, and v is the flow velocity. The cavitation number characterizes the relationship between the local pressure in the fluid and the vapor pressure, as well as the flow energy. When the cavitation number is low, the local pressure in the fluid is below the vapor pressure, making cavitation more likely to occur. On the other hand, when the cavitation number is high, cavitation is less likely to occur. The value of the cavitation number directly affects the bubble formation and collapse process. A low cavitation number helps enhance the cavitation effect, promoting bubble generation and intense collapse, thereby increasing cavitation intensity. By adjusting the inlet pressure, flow velocity, and fluid vapor pressure, the cavitation number can be effectively regulated, thereby controlling the occurrence and intensity of cavitation.
Hydraulic cavitation technology has been widely applied in various industrial fields, such as wastewater treatment, chemical reaction acceleration, and water purification, demonstrating exceptional efficiency. Different types of cavitation devices play a crucial role in controlling cavitation phenomena and improving processing efficiency. Although significant achievements have been made with existing cavitation devices in practical applications, the stability of the cavitation effect, energy efficiency improvements, and optimization of operating parameters remain central issues in current research. Advances in CFD technology and optimization design tools have provided strong support for the precise design of cavitation devices. With these technologies, the control of cavitation phenomena has become more precise, significantly enhancing the stability of cavitation effects, reducing energy consumption, and improving overall performance.
The multifunctionality and integrated design of cavitation devices are becoming hot topics in research, offering more possibilities for efficient application in complex working conditions. However, the further development of cavitation technology faces significant challenges in energy efficiency optimization, equipment durability, and long-term stability. Cavitation intensity and stability are influenced by fluid properties, equipment structure, and operating conditions. Therefore, improving the long-term operational efficiency of cavitation devices, reducing maintenance costs, and ensuring system stability remain urgent problems to be solved.
This study provides a comprehensive comparison of different types of cavitation devices in terms of performance, advantages, and disadvantages, and discusses their current state of development and future optimization directions. The development of intelligent and automated technologies provides new opportunities for the design, operation, and maintenance of cavitation devices. With the help of advanced technologies such as machine learning and artificial intelligence, real-time monitoring of cavitation device performance and dynamic optimization can be achieved, enhancing their ability to adapt to different industrial demands. The wide application prospects of hydraulic cavitation technology in industrial fields are vast. Through continuous technological innovation, the performance of cavitation devices will continue to improve, driving the deeper application of cavitation technology in water treatment, chemical processes, environmental protection, and contributing positively to the development of green industries and sustainable environmental management.
Acknowledgement: This research was supported by Harbin University of Science and Technology.
Funding Statement: The authors received no specific funding for this study.
Author Contributions: Jianying Li provided significant insights in the discussion section, supervised and guided the entire research process, offering valuable professional opinions, made important revisions and additions in the literature review and conclusion sections. Donglai Li designed and led the research project, responsible for overall project planning, contributed important ideas and theoretical support in paper writing. Tiefeng Li was responsible for data collection and preprocessing, provided detailed descriptions and analysis of the experimental section for paper writing, conducted data analysis and statistical processing, offering strong support for interpreting the paper’s results. All authors reviewed the results and approved the final version of the manuscript.
Availability of Data and Materials: The datasets used and analysed during the current study are provided within the manuscript, and there is no supplementary information files.
Ethics Approval: Not applicable.
Conflicts of Interest: The authors declare that during the process of writing and submitting this paper, we have no financial or non-financial competing interests. We do not have any direct or indirect financial relationships or other interests that could potentially lead to conflicts of competing interests with any institutions, organizations, or individuals. The design, data collection, analysis, and interpretation of results for this study have been conducted with objectivity and integrity, unaffected by any competing interests.
References
1. Zhang Y, Li J. Study on hydraulic cavitation occurrence characteristics of adjustable Venturi tube. Fluid Mach. 2022;50(4):85–91, 98. (In Chinese). doi:10.3969/j.issn.1005-0329.2022.04.013. [Google Scholar] [CrossRef]
2. Li MY, Zhu Y, Zhang WB, Yu Z, Kang C. Cavitation phenomenon and induced pressure pulsation characteristics of NaOH solution in a Venturi tube. J Jiangsu Univ (Nat Sci Ed). 2023;44(1):104–11. (In Chinese). [Google Scholar]
3. Han GH, Liu YN, Shao JP, Zhang CJ. Research on cavitation evolution model in venturi tube. J Syst Simul. 2020;32(2):164–71. (In Chinese). doi:10.16182/j.issn1004731x.joss.17-9174. [Google Scholar] [CrossRef]
4. Mishra C, Peles Y. An experimental investigation of hydrodynamic cavitation in micro-Venturis. Phys Fluids. 2006;18(10):103603. doi:10.1063/1.2360996. [Google Scholar] [CrossRef]
5. Li DW, Zhao MS, Zeng QF, Zheng HY, Pei Y, Yao SY, et al. Numerical simulation analysis of the hydrodynamic characteristics of an improved wedge-shaped blade rotating cavitator. J Chin Ship Res. 2023;18(1):181–8. [Google Scholar]
6. Dong B, Luo JQ, Zhang JH, Wang YW, Liu AX, Guo XQ. Numerical simulation on influence of the length of straight tube section on cavitation flow field of venturi tube. Fluid Mach. 2022;50(5):62–7. (In Chinese). doi:10.3969/j.issn.1005-0329.2022.05.009. [Google Scholar] [CrossRef]
7. Yasuda K, Ako D. Effect of venturi tube shape on reaction performance by hydrodynamic cavitation. J Chem Eng Jpn. 2019;52(3):280–2. doi:10.1252/jcej.18we183. [Google Scholar] [PubMed] [CrossRef]
8. Ren XE, Li CZ, Yang F, Huang YC, Yan LJ. Intermolecular interaction mechanism for improvement in solubility of soy protein isolate by swirling cavitation. Food Sci. 2020;41(3):93–8. (In Chinese). doi:10.7506/spkx1002-6630-20190306-078. [Google Scholar] [CrossRef]
9. Folden TS, Aschmoneit FJ. A classification and review of cavitation models with an emphasis on physical aspects of cavitation. Phys Fluids. 2023;35(8):081301. doi:10.1063/5.0157926. [Google Scholar] [CrossRef]
10. Shao JP, Liu YN. Study on factors affecting cavitation effect in venturi tube. J Harbin Univ Sci Technol. 2020;25(3):122–30. (In Chinese). doi:10.15938/j.jhust.2020.03.019. [Google Scholar] [CrossRef]
11. Han GH, Zhu YP, Hong J, Li DW. Influence of endocavitating rotary cavitator parameters on cavitation effect. J Harbin Univ Sci Technol. 2024;29(1):44–9. (In Chinese). doi:10.15938/j.jhust.2024.01.005. [Google Scholar] [CrossRef]
12. Han GH, Yang XD, Chen DY, Li DW, Zhao MS, Pei Y, et al. Research on cavitation characteristics of series venturi. J Harbin Univ Sci Technol. 2022;27(2):55–62. (In Chinese). doi:10.15938/j.jhust.2022.02.007. [Google Scholar] [CrossRef]
13. Yan QD, Liu SQ, Guo M, Liu C, Wang HY, Xie XY, et al. Research on the cavitation characteristics in viscous oil around parameterized hydrofoils. Ocean Engineering. 2024; 313(3):119620. [Google Scholar]
14. Liu XM, He J, Lu J, Ni XW. Experimental study on the cavitation bubble pulsation characteristics in fluids with different viscosities. Optoelectron Lasers. 2008;2008(7):985–8. [Google Scholar]
15. Nazari-Mahroo H, Pasandideh K, Navid HA, Sadighi-Bonabi R. Influence of liquid density variation on the bubble and gas dynamics of a single acoustic cavitation bubble. Ultrasonics. 2020;102(10):106034. doi:10.1016/j.ultras.2019.106034. [Google Scholar] [PubMed] [CrossRef]
16. Ding W, Hong F, Ying D, Huang Y, Khan SN, Jia J. A comprehensive study on the effects of annular protrusion for cavitation intensification in Venturi tubes. Chem Eng J. 2024;498(6):155306. doi:10.1016/j.cej.2024.155306. [Google Scholar] [CrossRef]
17. Peng K, Qin FGF, Jiang R, Kang S. Interpreting the influence of liquid temperature on cavitation collapse intensity through bubble dynamic analysis. Ultrason Sonochem. 2020;69:105253. doi:10.1016/j.ultsonch.2020.105253. [Google Scholar] [PubMed] [CrossRef]
18. Ge M, Petkovšek M, Zhang G, Jacobs D, Coutier-Delgosha O. Cavitation dynamics and thermodynamic effects at elevated temperatures in a small Venturi channel. Int J Heat Mass Transf. 2021;170(39):120970. doi:10.1016/j.ijheatmasstransfer.2021.120970. [Google Scholar] [CrossRef]
19. Zheng ZY, Wang L, Wei TZ, Cai WH, Li H, Yao LM, et al. Experimental investigation of temperature effect on hydrodynamic characteristics of natural cavitation in rotational supercavitating evaporator for desalination. Renew Energy. 2021;174:278–92. doi:10.1016/j.renene.2021.04.038. [Google Scholar] [CrossRef]
20. Wang D, Bi Y. Investigation of the influence of different liquid temperatures on the dynamics of long-pulse laser-induced cavitation bubbles. AIP Adv. 2024;14(2):025013. doi:10.1063/5.0185608. [Google Scholar] [CrossRef]
21. Shi H, Kang Y, Zeng D, Li D, Hu Y, Liu Q. Experimental study on the effect of dissolved CO2 on cavitation erosion intensity by submerged waterjet. Wear. 2022;504(11):204418. doi:10.1016/j.wear.2022.204418. [Google Scholar] [CrossRef]
22. Song L, Meng L, Sui H, Yang J, Guo F, Zhao X, et al. Study on DeNOx of NaClO2 in simulated seawater solution enhanced by hydrodynamic cavitation. Sep Purif Technol. 2024;330:125190. doi:10.1016/j.seppur.2023.125190. [Google Scholar] [CrossRef]
23. Li DW, Gu SJ, Han GH, Yang XD. Investigation of the effect of orifice plate parameters in Venturi tubes on cavitation performance. J Harbin Univ Sci Technol. 2023;8:1007–2683. [Google Scholar]
24. Li Q, Zhang J, Ming DZ, Wu MJ, Yuan Y. Effect of wall roughness on cavitation flow field in venturi tube. Chem React Eng Technol. 2020;36(3):193–202. (In Chinese). doi:10.11730/j.issn.1001-7631.2020.03.0193.10. [Google Scholar] [CrossRef]
25. Lyu F, Tang M, Zhou F, Zhang X, Han S, Zhang S. Research on the effect of structural parameters on cavitation performance of shear hydrodynamic cavitation generator. Appl Sci. 2024;14(9):3676. doi:10.3390/app14093676. [Google Scholar] [CrossRef]
26. Ren QN, Hu HX, Zheng YG. Effect of width-to-depth ratio and duty cycle of surface microstructure on cavitation and cavitation erosion on martensitic stainless steels. Surf Technol. 2024;53(11):67–79. (In Chinese). doi:10.16490/j.cnki.issn.1001-3660.2024.11.006. [Google Scholar] [CrossRef]
27. Zhang J, Luo T. Experimental study on the effect of pressure and flow rate on cavitation in a poppet throttle valve. Ind Lubr Tribol. 2019;72(5):629–36. doi:10.1108/ILT-04-2019-0152. [Google Scholar] [CrossRef]
28. Wang Y, Li M, Chen J, Liu F, Huang Y, Wang X, et al. Experimental investigation on cavitation performance of the annular-slit rotational hydrodynamic cavitation reactor. J Braz Soc Mech Sci Eng. 2024;46(9):567. doi:10.1007/s40430-024-05153-w. [Google Scholar] [CrossRef]
29. Fang HY, Zhang RJ, Cao YT, Zheng EH, Zhang CH, Geng LL. Analysis of the influence of different driving pressure fields on numerical cavitation prediction. J Hydrodynam, Series A. 2024;39(5):696–705. [Google Scholar]
30. Dastane GG, Thakkar H, Shah R, Perala S, Raut J, Pandit AB. Single and multiphase CFD simulations for designing cavitating venturi. Chem Eng Res Des. 2019;149:1–12. doi:10.1016/j.cherd.2019.06.036. [Google Scholar] [CrossRef]
31. Cao Y, Huang WX, Huang YC, Huang CD. Study on the effects of oxidative decolorization of sugar juice in impact-jet hydrodynamic cavitator. Food Mach. 2024;40(9):179–85. (In Chinese). doi:10.13652/j.spjx.1003.5788.2023.80877. [Google Scholar] [CrossRef]
32. Wang B, Zhang RH, Li YY, Lian XM, She ZP. Flow field simulation of a new type of vortex-flow cavitator and its removal effect on tetracycline from wastewater. J Environ Eng. 2022;16(5):1490–6. [Google Scholar]
33. Li Y, Feng M, Lian Y, Wu Y. Behaviors and mechanism of HVOF/HVAF sprayed WC-co-Cr coatings subjected to cavitation in marine environments. J Mater Eng Perform. 2024;31(1):1. doi:10.1007/s11665-024-09968-5. [Google Scholar] [CrossRef]
34. Wang G, Yang Y, Wang C, Shi W, Li W, Pan B. Effect of nozzle outlet shape on cavitation behavior of submerged high-pressure jet. Machines. 2022;10(1):4. doi:10.3390/machines10010004. [Google Scholar] [CrossRef]
35. Zhao WG, Liu JJ, Zhang JY, Qin JW. Numerical analysis of effect of bionic hydrofoil structure on cavitation suspension. J Drain Irrig Mach Eng. 2024;42(7):685–92, 700. (In Chinese). [Google Scholar]
36. Hong S, Wu Y, Wu J, Zhang Y, Zheng Y, Li J, et al. Microstructure and cavitation erosion behavior of HVOF sprayed ceramic-metal composite coatings for application in hydro-turbines. Renew Energy. 2021;164(3):1089–99. doi:10.1016/j.renene.2020.08.099. [Google Scholar] [CrossRef]
37. Hu JM, Wang ZM, Li ZS. Experimental study on evolution characteristics of cavitation bubble under multiple boundary conditions. J Drain Irrig Mach Eng. 2023;41(4):393–9, 416. (In Chinese). doi:10.3969/j.issn.1674-8530.21.0106. [Google Scholar] [CrossRef]
38. Brennen CE. Hydrodynamics and cavitation of pumps. Vienna: Springer; 2007. [Google Scholar]
39. Zhang ZR. Research on experimental technique of cavitational hydrodynamics performance of semi-submerged propellers in depressurized towing tank. J Ship Mech. 2001;5(1):25–31. [Google Scholar]
40. Golash N, Gogate PR. Degradation of dichlorvos containing wastewaters using sonochemical reactors. Ultrason Sonochem. 2012;19(5):1051–60. doi:10.1016/j.ultsonch.2012.02.011. [Google Scholar] [PubMed] [CrossRef]
41. Mishra KP, Gogate PR. Intensification of degradation of aqueous solutions of rhodamine B using sonochemical reactors at operating capacity of 7 L. J Environ Manage. 2011;92(8):1972–7. doi:10.1016/j.jenvman.2011.03.046. [Google Scholar] [PubMed] [CrossRef]
42. Abu-Nab AK, Mamdouh HO, Mohamed KG, Abu-Bakr AF. Hydrodynamics and heat transfer of cavitation bubble in nanoparticles/water nanofluids based on the effects of variable surface tension and viscous forces. J Nanofluids. 2023;12(8):2044–55. doi:10.1166/jon.2023.2067. [Google Scholar] [CrossRef]
43. Zheng H, Zheng Y, Zhu J. Recent developments in hydrodynamic cavitation reactors: cavitation mechanism, reactor design, and applications. Engineering. 2022;19(4949):180–98. doi:10.1016/j.eng.2022.04.027. [Google Scholar] [CrossRef]
44. Soyama H. Luminescence intensity of vortex cavitation in a Venturi tube changing with cavitation number. Ultrason Sonochem. 2021;71:105389. doi:10.1016/j.ultsonch.2020.105389. [Google Scholar] [PubMed] [CrossRef]
45. Fu S, Lu J, Zhou F, Yuan H, Wang Y, Dai C. Study on the performance of a novel hydrodynamic cavitation device for treatment of wastewater. Asia-Pacific J Chem Eng. 2022;17(2):e2752. doi:10.1002/apj.2752. [Google Scholar] [CrossRef]
46. Taşdemir A, Cengiz İ., Yildiz E, Bayhan YK. Investigation of ammonia stripping with a hydrodynamic cavitation reactor. Ultrason Sonochem. 2020;60:104741. doi:10.1016/j.ultsonch.2019.104741. [Google Scholar] [PubMed] [CrossRef]
47. Sun X, Kang CH, Park JJ, Kim HS, Om AS, Yoon JY. An experimental study on the thermal performance of a novel hydrodynamic cavitation reactor. Exp Therm Fluid Sci. 2018;99:200–10. doi:10.1016/j.expthermflusci.2018.02.034. [Google Scholar] [CrossRef]
48. Yuan HX, Lu J, Zhou LY, Fu SC, Wang YB. Cavitation performance of tooth-disk cavitator. Chem Eng. 2021;49(7):48–55. [Google Scholar]
49. Wang Y, Yan J, Wang J, Liu HL, Dular M. Unsteady cavitation patterns in a rotor-Stator centrifugal hydrodynamic cavitation generator. J Harbin Eng Univ. 2018;39(12):1887–93. (In Chinese). doi:10.11990/jheu.201707108. [Google Scholar] [CrossRef]
50. Wang L, Liu ZY, Wang ZW, Song YX, Zhang LH. Cavitation performance optimization of rotor-gap hydraulic cavitation generator. J Vac Sci Technol. 2024;44(2):176–83. [Google Scholar]
51. Bhukya J, Naik R, Mohapatra D, Sinha LK, Rao KVR. Orifice based hydrodynamic cavitation of sugarcane juice: changes in Physico-chemical parameters and Microbiological load. LWT. 2021;150(1):111909. doi:10.1016/j.lwt.2021.111909. [Google Scholar] [CrossRef]
52. Yi L, Qin J, Sun H, Ruan Y, Zhao L, Xiong Y, et al. Improved hydrodynamic cavitation device with expanded orifice plate for effective chlorotetracycline degradation: optimization of device and operation parameters. Sep Purif Technol. 2022;280(17):119840. doi:10.1016/j.seppur.2021.119840. [Google Scholar] [CrossRef]
53. Wang S, Zhao L, Ruan Y, Qin J, Yi L, Zhang Z, et al. Investigation on series-wound orifice plate hydrodynamic cavitation (HC) degradation of Rhodamine B (RhB) assisted by several by-pass line orifice plates. J Water Process Eng. 2023;51(5):103404. doi:10.1016/j.jwpe.2022.103404. [Google Scholar] [CrossRef]
54. Zhang Y, Lai J, He C, Yang S. Cavitation optimization of single-orifice plate using CFD method and neighborhood cultivation genetic algorithm. Nucl Eng Technol. 2022;54(5):1835–44. doi:10.1016/j.net.2021.10.043. [Google Scholar] [CrossRef]
55. Li Q, Zong C, Liu F, Xue T, Zhang A, Song X. Numerical and experimental analysis of the cavitation characteristics of orifice plates under high-pressure conditions based on a modified cavitation model. Int J Heat Mass Transf. 2023;203(19–20):123782. doi:10.1016/j.ijheatmasstransfer.2022.123782. [Google Scholar] [CrossRef]
56. Han GH, Chen LQ, Li DW, Zhao ZW, Zhao EY. Numerical simulation and experiment of orifice plate cavitator parameters. J Harbin Univ Sci Technol. 2023;28(4):86–94. (In Chinese). doi:10.15938/j.jhust.2023.04.010. [Google Scholar] [CrossRef]
57. Han GH, Zhao EY, Li DW, Zhao ZW, Chen LQ, Zhu YP. Cavitation effect of pure water on orifice plate. J Harbin Univ Sci Technol. 2023;28(5):110–7. (In Chinese). doi:10.15938/j.jhust.2023.05.014. [Google Scholar] [CrossRef]
58. Han GH, Ge N, Hou JJ, Li DW, Zhao MS, Pei Y, et al. Cavitation characteristics of fluid in orifice cavitator. J Harbin Univ Sci Technol. 2022;27(3):22–9. (In Chinese). doi:10.15938/j.jhust.2022.03.003. [Google Scholar] [CrossRef]
59. Yue LJ, Liao YH, Xue Y, Li XJ, Li YX, Liu CW. Study on the effect of pit defects on cavitating flow characteristics at the throat of a thick orifice plate. Chem Eng J. 2023;74(8):3292–308. [Google Scholar]
60. Li B, Li S, Yi L, Sun H, Qin J, Wang J, et al. Degradation of organophosphorus pesticide diazinon by hydrodynamic cavitation: parameters optimization and mechanism investigation. Process Saf Environ Prot. 2021;153:257–67. doi:10.1016/j.psep.2021.07.026. [Google Scholar] [CrossRef]
61. Mai CL, Chang ZB, Zhao L, Peng Y, Jiang J. Experimental study on cavitation flow characteristics of porous orifice plate. China Rural Water Hydropower. 2024;2024(4):132–40. (In Chinese). [Google Scholar]
62. Qin J, Sun H, Zhang S, Yi L, Ruan Y, Wang S, et al. Investigation on the by-pass line orifice plate assisted hydrodynamic cavitation (B-PLOPA HC) degradation of basic fuchsin (BF) in wastewater. Sep Purif Technol. 2022;287(3):120501. doi:10.1016/j.seppur.2022.120501. [Google Scholar] [CrossRef]
63. Mali CR, Patwardhan AW, Pandey GK, Banerjee I, Vinod V. CFD study on the effect of various geometrical parameters of honeycomb type orifices on pressure drop and cavitation characteristics. Nucl Eng Des. 2020;370:110880. doi:10.1016/j.nucengdes.2020.110880. [Google Scholar] [CrossRef]
64. Zhang Y, Sun L, He C, Yuan SB. Prediction of cavitation characteristics of throttle orifice plate based on improved BP neural network. Nucl Power Eng. 2021;42(6):135–40. (In Chinese). doi:10.13832/j.jnpe.2021.06.0135. [Google Scholar] [CrossRef]
65. Osman H, Sedrak M, Hosseini SH, Elsayed K. A comprehensive study of hole-to-hole interaction for multi-hole orifice (MHO) in hydrodynamic cavitation process. Flow Meas Instrum. 2022;85:102163. doi:10.1016/j.flowmeasinst.2022.102163. [Google Scholar] [CrossRef]
66. Xu B, Hu HF, Wang HJ. Application of adaptive variational mode decomposition algorithm in the analysis of cavitation characteristics in high-temperature and high-pressure water. J Xi’an Jiaotong Univ. 2024;12(1):1–12. [Google Scholar]
67. Xu S, Long X, Wang J, Cheng H, Zhang Z. Experiment on flow dynamics and cavitation structure in an axisymmetric venturi tube based on x-t diagrams and proper orthogonal decomposition. Exp Therm Fluid Sci. 2022;136(12):110648. doi:10.1016/j.expthermflusci.2022.110648. [Google Scholar] [CrossRef]
68. Bimestre TA, Júnior JAM, Botura CA, Canettieri E, Tuna CE. Theoretical modeling and experimental validation of hydrodynamic cavitation generator with a Venturi tube for sugarcane bagasse pretreatment. Bioresour Technol. 2020 Sep;311(4):123540. doi:10.1016/j.biortech.2020.123540. [Google Scholar] [PubMed] [CrossRef]
69. Chen Q, Liu Y, Wu Q, Wang Y, Liu T, Wang G. Global cavitation patterns and corresponding hydrodynamics of the hydrofoil with leading edge roughness. Acta Mech Sin. 2020;36(6):1202–14. doi:10.1007/s10409-020-00992-x. [Google Scholar] [CrossRef]
70. Gayathri G, Reddy D. Degradation and decolourisation of azodyes in wastewater by using hydrodynamic cavitation technique. Oxidat Commun. 2021;2021(4):44. [Google Scholar]
71. Korneev AS, Zhebynev DA, Fel’dman AM. Calculation and experimental investigations of the venturi tube as a hydrodynamic oscillator. J Eng Phys Thermophys. 2020;93(2):428–35. doi:10.1007/s10891-020-02137-0. [Google Scholar] [CrossRef]
72. Wang L, Ji B, Cheng H, Wang J, Long X. One-dimensional/three-dimensional analysis of transient cavitating flow in a venturi tube with special emphasis on cavitation excited pressure fluctuation prediction. Sci China Technol Sci. 2020;63(2):223–33. doi:10.1007/s11431-019-9556-6. [Google Scholar] [CrossRef]
73. Zhou JJ, Song YC, Wang DZ, Yin JL. Experimental and numerical investigation of cavitation-induced choked flow in venturi tube. Nucl Power Eng. 2021;42(3):25–31. (In Chinese). doi:10.13832/j.jnpe.2021.03.0025. [Google Scholar] [CrossRef]
74. Liang YZ, Long Y, Long XP, Cheng HY. Verification and confirmation of large eddy simulation of cavitating flow inside a Venturi tube. J Chin Ship Res. 2022;17(3):196–204. [Google Scholar]
75. Hong F, Deng YY, Shao ZW, Liu SC, Xiang KX, Lei EH, et al. Development and analysis of energy index for unsteady cavitation flow in a Venturi cavitator. J Drain Irrig Mach Eng. 2024;42(10):1018–23, 1030. (In Chinese). [Google Scholar]
76. Shi H, Li M, Liu Q, Nikrityuk P. Experimental and numerical study of cavitating particulate flows in a Venturi tube. Chem Eng Sci. 2020;219(4):115598. doi:10.1016/j.ces.2020.115598. [Google Scholar] [CrossRef]
77. Li MQ, Peng HL. Cavitation characteristics of a new type of built-in venturi tube cavitation generator. Sci Technol Eng. 2024;24(21):9061–8. (In Chinese). doi:10.12404/j.issn.1671-1815.2306065. [Google Scholar] [CrossRef]
78. Wu M, Yuan S, Song H, Li X. Micro-nano bubbles production using a swirling-type venturi bubble generator. Chem Eng Process Process Intensif. 2022;170:108697. doi:10.1016/j.cep.2021.108697. [Google Scholar] [CrossRef]
79. Sun SQ, Liu B, Fu M, Wu X, Wang J. Study on the distribution of ultrasonic cavitation bubbles under acoustic flow conditions. Acoustic Technol. 2022;41(4):526–33. [Google Scholar]
80. Wang J, Wang X, Guo P, Yu J. Degradation of reactive brilliant red K-2BP in aqueous solution using swirling jet-induced cavitation combined with H2O2. Ultrason Sonochem. 2011;18(2):494–500. doi:10.1016/j.ultsonch.2010.08.006. [Google Scholar] [PubMed] [CrossRef]
81. Chuai S, Ye L, Ma N, Zhu X, Lv B. Quantitative characterization and influencing factors analysis of dual-frequency ultrasonic cavitation intensity based on fluorescence analysis. Chem Eng Process Process Intensif. 2023;191:109470. doi:10.1016/j.cep.2023.109470. [Google Scholar] [CrossRef]
82. Wang B, Zhang R, Li Y, Lian X. CFD simulation of a swirling Vortex cavitator and its degradation performance and pathway of tetracycline in aqueous solution. Int J Chem React Eng. 2022;20(9):955–63. doi:10.1515/ijcre-2021-0243. [Google Scholar] [CrossRef]
83. Yang SQ, Ji H, Li C, Wang SY, Tang RF. Suction cavitation and suppression of high-speed gear pump. Chin Hydraul Pneum. 2024;48(8):18–28. (In Chinese). doi:10.11832/j.issn.1000-4858.2024.08.003. [Google Scholar] [CrossRef]
84. Zhi C, Watanabe S, Fujiwara T. Venturi nozzle and fuel supply device equipped with this Venturi nozzle. Japan: CN201911145067.3; 2020 Feb 11. [Google Scholar]
85. Wu D, Wu DY. A Venturi system for bubble drag reduction in hulls. Shaanxi, China: CN201911043820.8; 2020 Feb 07. [Google Scholar]
86. Larsen F, Mortensen HH, Jensen PB. Venturi mixer with adjustable flow restrictor and its operating method. Switzerland: CN201880040235.X; 2020 Feb 11. [Google Scholar]
87. Zhang XJ, Wang X, Qu DL, Sang XY, Li QF, Zhang NN, et al. System for hydraulic cavitation and ozone combined treatment of sulfur-containing wastewater. Beijing, China: CN201910487250.5; 2024 Apr 12. [Google Scholar]
88. Zhang D, Wang ZG, Liu ZP, Wu YH, Zhang JX, Zhang WY, et al. Anti-cavitation design method for multi-stage orifice energy dissipators. Beijing, China: CN202110527451.0; 2023 Sep 22. [Google Scholar]
89. Fang DW, Sun HS, Wang J, Zhang CH. Hydraulic cavitation device based on parallel orifices and its application in the degradation of dye-containing wastewater. Liaoning, China: CN202210384026.5; 2022 Aug 12. [Google Scholar]
90. Wang J, Dong YR, Zhang ZH, Fang DW. Method for degrading tetracycline antibiotics in wastewater using a hydraulic cavitation system based on an enlarged orifice plate. Liaoning, China: CN202110118215.3; 2021 Jun 11. [Google Scholar]
91. Tao ML, Deng YJ, Liu JY, You HN, Wang Z. Hydraulic cavitation treatment system suitable for mixed wastewater. Hube, China: CN202220722091.X; 2022 Jul 26. [Google Scholar]
92. Tao ML, Wang Z, You HN, Deng YJ, Liu JY, Xie ZJ, et al. Circulating sterilization wastewater treatment system combining tooth-disk cavitator and aeration tank. Hube, China: CN202220712843.4; 2022 Jul 19. [Google Scholar]
93. Yuan HX, Zhou LY, Fu SC. A cavitator. Jiangsu, China: CN201711247510.9; 2018 Jun 05. [Google Scholar]
94. Wang SY. A multi-stage friction shear cavitation water jet nozzle. Huna, China: CN202322820907.X; 2024 Jul 23. [Google Scholar]
95. Long XP, Wang J. Strong shear-type central jet cavitation generator. Hubei, China: CN201611193216.X; 2022 Aug 30. [Google Scholar]
96. Yao LM, Li DW, Jing T, Zhao MS, Pei Y, Yao SY, et al. High shear machine with cavitation effect. Heilongjiang, China: CN202220834814.5; 2022 Jul 22. [Google Scholar]
97. Li D, Yao ZY, Wu SJ, Kang Y, Luo WR. Rotating shear cavitation nozzle. Hubei, China: CN202110604992.9; 2022 Jul 05. [Google Scholar]
98. Yuan HX, Wang YB, Fu SC, Lu J, Zhang YL, Zhou LY. Rotating tooth cylinder-type hydraulic cavitator. Jiangsu, China: CN202010017555.2; 2022 Mar 25. [Google Scholar]
99. Song YX, Wang L, Zhang LB, Liu Q, Guan ST, Liu JT, et al. Counter-rotating hydraulic cavitation generator. Shandon, China: CN202411028780.0; 2024 Aug 27. [Google Scholar]
100. Zhang WJ, Yao LM, Zhang XC, Wei J, Li DW, Zhao MS, et al. Hydraulic cavitation generator and reaction method. Heilongjian, China: CN201510940088.X; 2018 Apr 17. [Google Scholar]
Cite This Article
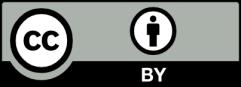
This work is licensed under a Creative Commons Attribution 4.0 International License , which permits unrestricted use, distribution, and reproduction in any medium, provided the original work is properly cited.