Open Access
ARTICLE
Preparation and Application of an Epoxy Soybean Oil-Based Plugging Agent
State Key Laboratory of Oil and Gas Reservoir Geology and Exploitation, Southwest Petroleum University, Chengdu, 610500, China
* Corresponding Author: Dingyuan Zhang. Email:
(This article belongs to the Special Issue: Fluid and Thermal Dynamics in the Development of Unconventional Resources II)
Fluid Dynamics & Materials Processing 2025, 21(2), 261-277. https://doi.org/10.32604/fdmp.2025.060033
Received 22 October 2024; Accepted 14 January 2025; Issue published 06 March 2025
Abstract
Resin plugging agents play a pivotal role in addressing casing damage in oil and gas fields. However, the widespread use of epoxy resin is constrained by its high cost and non-renewable origin, while plant-based resins often suffer from inadequate mechanical properties, which limit their effectiveness in such applications. This study introduces BEOPA, an innovative, renewable, high-strength resin plugging agent derived from epoxidized soybean oil (ESO) and enhanced with bisphenol A-type benzoxazine (BZ). In this study, the synthesis process, reaction mechanism, and application performance of this novel material are systematically presented, explored and optimized. It is shown that the optimal formulation of BEOPA includes 41.4 wt% ESO, 24.8 wt% BZ, 24.8 wt% methylhexahydrophthalic anhydride (MHHPA), 8.2 wt% styrene (ST), and 0.8 wt% N,N-dimethylbenzylamine (BDMA), yielding an impressive compressive strength of 93.7 MPa. The integration of ESO and BZ creates an intricate and robust double crosslinking network, significantly enhancing material strength and durability. BEOPA exhibits a tunable curing time, ranging from 0.5 to 15 h, with viscosities below 300 mPa·s at 25°C and 75 mPa·s at 50°C. Furthermore, it demonstrates exceptional thermal stability within the 100°C–150°C range, even in environments with mineral salt concentrations as high as 43,330 mg/L. Remarkably, BEOPA achieves superior plugging performance, sustaining breakthrough pressures exceeding 29.7 MPa in 1 mm crack cores.Keywords
Casing damage causes a series of problems in oil and gas fields, including oil and gas leakage leading to formation contamination [1], and wellbore pressure imbalance leading to well blowout or lost circulation [2]. Casing damage is attributed to the deformation and breakage of the casing [3] caused by the corrosion of formation fluids [4] and the shear stresses [5], resulting in the formation of micropores and microfractures. Currently, the most prevalent methods for repairing casing damage include physical and chemical plugging. Physical plugging utilizes a solid expandable tubular [6] or casing suspension packer [7] to repair the casing damage. This repair method is costly and exhibits poor plugging efficacy [8]. Chemical plugging is the primary solution for casing damage remediation in oil and gas fields, owing to its excellent injectability, cost-effectiveness, and adaptability [9]. Casing damage repair methods play a crucial role in the safe production of oil and gas fields by mitigating economic costs and risk of environmental damage [10].
Chemical plugging encompasses inorganic material, gel material, and resin material plugging. Inorganic materials include cement-based [11] and gypsum-based composites [12]. However, inorganic materials exhibit an inadequate plugging performance and resistance to penetration. Particles in inorganic materials, such as cement [13], accumulate at the entrance of the crack, making it difficult to penetrate deeper into the crack to plug it. Gel materials comprise polymer gels [14] and water-glass gels [15]. These materials exhibit poor mechanical properties and long-term stability because of their susceptibility to dehydration in high-temperature and saline environments [16,17]. Resin materials, particularly epoxy resins, demonstrate exceptional mechanical properties, long-term plugging effectiveness, and low curing shrinkage rates, indicating significant potential for application in casing damage repair [18–20]. Guo [21] prepared a casing plugging material using epoxy resin, which was characterized by high-pressure resistance and excellent long-term stability. Chen et al. [22] formulated a low curing shrinkage rates and high-strength epoxy resin plugging agent. Alkhamis [23] synthesized a novel epoxy plugging agent, which exhibited superior rheological and plugging properties compared to conventional plugging agents. Despite the exceptional plugging performance and long-term stability of resin materials, their high cost and non-renewability present significant challenges [24].
Epoxidized soybean oil is a vegetable oil derivative synthesized through chemical modification using soybean oil as the raw material [25]. Epoxidized soybean oil is a promising alternative to conventional epoxy resins owing to its sustainability, cost-effectiveness, and abundant availability [26]. The application of epoxidized soybean oil as a raw material is extensive, encompassing polymer synthesis, paints, coatings, agriculture, food packaging, and biomedical industries [27]. Nevertheless, epoxy soybean oil resin exhibits limitations in oil and gas field applications owing to its insufficient hardness, brittleness, and poor toughness properties [28,29]. Researchers have endeavored to enhance epoxy soybean oil resins through the incorporation of reinforcing materials, such as nanoparticles [30], clay [31], and cellulose [32], to improve their mechanical properties. These reinforcing materials enhance the mechanical and toughness properties of the resin through synergistic interactions with the resin matrices. However, the enhancement of the mechanical properties remains suboptimal owing to inadequate interface compatibility.
Researchers have found that blended materials of epoxy or benzoxazine with epoxidized soybean oil exhibit excellent performance [33]. The mechanical properties of these blended materials were enhanced through the incorporation of reactive groups in the network structure formation. However, epoxy resins are limited in their capacity to improve mechanical properties due to their ability to enhance only chain stiffness in the crossover network. Benzoxazines, in contrast, demonstrate greater efficacy in enhancing the mechanical properties of resins compared to epoxy resins. The reaction between benzoxazine and the epoxy group results in ring-opening, forming phenolic hydroxyl groups, which subsequently improve chain rigidity, crosslink density, and crystallinity of the resin. Consequently, resins prepared from blends of benzoxazine and epoxidized soybean oil exhibit exceptional mechanical and thermal properties.
In this study, a novel renewable, high-strength, epoxy soybean oil-based resin plugging agent (BEOPA) was synthesized and optimized from a plant oil, epoxidized soybean oil (ESO), which was modified with bisphenol A-type benzoxazine (BZ). This study analyzed the thermal stability and mechanical properties of the plugging agent, examined the regulation mechanism of the curing time, compressive strength, and injection properties of the epoxy soybean oil-based thermosetting resin, and evaluated its crack-plugging performance and long-term stability performance. The experimental results demonstrate that the BEOPA exhibits excellent injection properties, mechanical properties, long-term temperature, and salt resistance, and can be effectively applied to casing damage management.
Epoxidized soybean oil (purity 99.5%, ESO, Epoxy Value 6.6%), methylhexahydrophthalic anhydride (purity 98%, MHHPA), LTD, styrene (purity 98%, ST) was purchased from Shanghai Maclin Biochemical Technology Co., Ltd. (Shanghai, China) and N, N-dimethylbenzylamine (purity 98%, BDMA) was purchased from Sinopharm Group Chemical Reagent Co., Ltd. (Shanghai, China). Bisphenol A Benzoxazine (BZ) was purchased by Chengdu Coryes Polymer Science & Technology Co., Ltd. (Chengdu, China). All chemicals were used without further purification.
ESO and BZ were added to a beaker and placed in a constant-temperature oil bath at 130°C for 15 min at 400 rpm stirring speed to obtain a mixture solution (BEO). The curing agent, diluent, and initiator were sequentially added to BEO. The mixed solution was stirred for 30 min at 400 rpm to obtain a resin plugging agent reaction solution. The resin plugging agent reaction solution was poured into a mold and placed in a constant-temperature oven at 130°C for 24 h to produce the epoxy soybean oil-based resin plugging agent (BEOPA).
2.2.2 Fourier Transform Infrared Spectroscopy
After the resin plugging agent was ground into a powder and dried in an oven, the infrared characteristics of the resin plugging agent were tested using a Thermo Scientific Nicolet iS20 infrared spectrometer. The FTIR analysis of BEOPA was carried out by preparing slices with potassium bromide (KBr), and the scanning wave number range was 4000−1 to 400−1 cm.
2.2.3 Thermogravimetric Analysis
Thermogravimetric analysis (TGA) of the resin plugging agent was conducted using a Mettler TGA/DSC1 instrument under a nitrogen atmosphere. Thermal analysis was performed in the 30°C–600°C temperature range with a heating rate of 10°C/min.
2.2.4 Differential Scanning Calorimetry
The curing profiles of BEOPA, EOPA, and EPA were examined using a differential scanning calorimetry (DSC) Diamond Analyzer. Approximately 20 mg of the sample was placed in DSC aluminum pans, followed by thermal scanning from 30°C to 300°C at a heating rate of 10°C/min in a nitrogen gas atmosphere. The temperature at which the maximum crosslinking reaction occurred (Peak Temperature) of the resin was determined.
2.2.5 Scanning Electron Microscopy
The BEOPA fracture surface morphology was characterized by scanning electron microscopy (SEM) (SUPRA-55, ZEISS, Oberkochen, Germany). First, the fracture surface of the resin plugging agent was placed on the sample seat, and the surface was sprayed with gold on the fracture surface after vacuum. Photomicrographs were obtained under very high vacuum conditions at 15 kV.
2.2.6 Rheological Properties Determination
The viscosity of the resin plugging agent reaction solution was measured by TAAR2000 rheometer at 300 s−1 shear rate at different temperatures.
2.2.7 Compressive Strength Determination
The resin plugging agent reaction solution was poured into a cylindrical mold (ϕ 25 mm × 30 mm), which was placed in a constant-temperature oven at 130°C for 24 h. The resin-plugging agent was removed from the model and placed on the support plate of the pressure tester. The upper-pressure column was adjusted to fit closely with the surface of the sample; the mode was set as material compression, and the downward pressure speed was set to 2 mm/min. The pressure tester was started and the maximum strength was recorded when the resin plugging agent ruptured.
2.2.8 Curing Time Determination
The resin plugging agent reaction solution was injected into the mold and placed in a constant-temperature oven at 130°C. The mold was removed for observation at 30-min intervals, and the time at which the glass rod could not be inserted into the resin plugging agent was recorded as the curing time of the resin plugging agent.
2.2.9 Plugging Properties Determination
Cracks of varying widths (cracks with a length of 20 mm, width of 1–5 mm, and height of 50 mm) were prefabricated on steel cores to simulate casing damage. Subsequently, the resin plugging agent reaction solution was injected into the steel core at a volume of 1 PV, and the ends of the steel core were sealed. The steel core was placed in a constant-temperature oven for 24 h to evaluate the plugging properties of the BEOPA for cracks of varying widths. In addition, the plugging properties of the epoxidized soybean oil plugging agent (EOPA), epoxy resin plugging agent (EPA), and epoxy soybean oil-based resin plugging agent (BEOPA) were evaluated in 1 mm cracks.
A schematic of the core flooding system used in this study (Fig. 1). The experimental steps were as follows: (1) The steel core was placed into the core holder, and a confining pressure of 2 MPa, which was supplied using a hand pump, was fixed on the steel core to prevent fluid bypassing from the steel core during the experiment; (2) the constant pressure fluid pump was initiated to drive the steel core at a constant water flow rate of 1 mL/min. It was then necessary to continuously adjust the confining pressure so that it was always higher than the inlet end of the steel core at 3 MPa; (3) the pressure at the inlet end of the core sample was monitored using a pressure transducer. The maximum pressure at the inlet of the steel core was recorded as the breakthrough pressure. Once the steel core was breached, the process was continued until the pressure was stabilized for 30 min.
Figure 1: Schematic of the core flooding experimental apparatus
The resin plugging agent reaction solution was poured into a mold and placed in a constant-temperature oven at 130°C for 24 h. Subsequently, the resin plugging agent was demoulded and placed in an aging tank filled with simulated formation water (Table 1). Aging test in a constant-temperature oven at 130°C. At the end of the aging process, surface water was drained using filter paper. The resin was then weighed and its long-term stability was evaluated based on the quality retention rate of BZESO.
To prevent premature curing of the plugging agent during injection and to achieve effective plugging, it is crucial to investigate the factors that influence the curing time of the plugging agent. The experimental results demonstrated that the curing time was influenced by the quantities of the initiator (BDMA) and diluent (St), as well as the curing temperature. By adjusting the quantities of BDMA within a range of 0–1.6 wt% at 100°C–130°C, the plugging agent was cured within a timeframe of 3–15 h (Fig. 2a). At 150°C, the plugging agent was cured within 0.5–1.5 h by adjusting the quantity of BDMA. Thus, by adjusting the quantity of BDMA in the range of 100°C–150°C, the plugging agent can be safely injected into the designated plugging position. Increasing the quantity of BDMA and elevating the reaction temperature can enhance the collision rate of the anhydride group, oxazine ring, and epoxy group, which decreases the activation energies of chemical reactions [34,35]. In summary, increasing the initiator quantity and enhancing the reaction temperature can reduce the curing time of the resin plugging agent. The introduction of diluents decreases the molar concentration of the anhydride and epoxy groups, resulting in a reduction in the collision efficiency and, consequently, a decrease in the reaction rate [36] (Fig. 2b).
Figure 2: (a) Effect of initiator quantity and temperature on curing time of BEOPA; (b) Effect of diluent quantity on curing time of BEOPA
The mechanical properties of the plugging agent are the primary factors that ensure effective plugging in the reservoir. This study was conducted to examine the effects of BZ, MHHPA, and ST on the mechanical properties of BEOPA.
As illustrated in Fig. 3a, the compressive strength of the resin plugging agent exhibited an initial increase, followed by a decrease with increasing BZ quantity. At a BZ quantity of 24.8 wt%, the compressive strength of the resin plugging agent reached 93.7 MPa, which was 41.3% higher than that observed without BZ addition. The enhancement in chain stiffness, crosslink density, and crystallinity of the resin network structure was attributed to the ring-opening polymerisation reaction between BZ and the epoxy group, resulting in the formation of a double-crosslinked network structure [37]. Consequently, the modification of ESO with BZ significantly improved the mechanical properties of the resin plugging agent [38]. However, when an excessive quantity of BZ was employed, phenolic hydroxyl groups were generated due to the ring-opening polymerisation reaction. These groups not only reacted with the epoxy group, but also catalysed the ring-opening polymerisation reaction between ESO and MHHPA. The simultaneous occurrence of the ring-opening polymerisation reactions with MHHPA and BZ decelerated the rate of the ring-opening polymerisation reaction between ESO and BZ. Consequently, an excessive quantity of BZ led to a reduction in the mechanical properties of the resin plugging agent.
Figure 3: Mechanical properties tests. (a) Effect of BZ quantity on the mechanical properties; (b) Effect of MHHPA quantity on the mechanical properties; (c) Effect of ST quantity on the mechanical properties
The MHHPA quantity directly influences the crosslinking density of the plugging agent. As the MHHPA quantity increased, the compressive strength of BEOPA exhibited a trend of initial increase followed by decrease (Fig. 3b). The optimum quantity of MHHPA is 28.9 wt%, which was calculated using Eq. (1) [39]:
(1)
refers to the mass ratio of ESO to MHHPA, refers to the correction coefficient, refers to the relative molecular mass of MHHPA, refers to the anhydride equivalent of MHHPA, refers to the epoxy value of ESO, and refers to the number of anhydride groups. However, experimental results demonstrated that the compressive strength with a 28.9 wt% quantity was lower than that with a 24.8 wt% quantity. This phenomenon occurred because BZ occupied a portion of the reaction sites of the anhydride, resulting in a competitive effect between BZ and the anhydride during the polymerisation process. The quantity of BZ incorporated into the cross-linked network structure was insufficient, leading to inadequate modification of the ESO with BZ [40]. Based on the experimental findings, the mechanical properties of BEOPA were superior to those of EPA and EOPA when the same quantity of MHHPA was added.
To address the issue of increased viscosity in the BEOPA reaction solution resulting from the introduction of BZ, this study employed the addition of diluents to reduce the viscosity. This study investigated the effect of using ST as a diluent on the mechanical properties of resin plugging agents. As illustrated in Fig. 3c, the compressive strength of the resin plugging agent exhibited an inverse relationship with increasing ST concentration. This phenomenon can be attributed to the addition of ST, which reduces the curing reaction concentration between ESO and MHHPA, thereby decreasing the rate of the curing reaction and consequently diminishing the mechanical properties of BEOPA. Experimental results indicate that although the addition of ST influences the compressive strength of BEOPA to some extent, its compressive strength remains sufficient to meet the requirements for plugging. In conclusion, when the quantities of ESO was 41.4 wt%, BZ was 24.8 wt%, MHHPA was 24.8 wt%, BDMA was 0.8 wt%, and ST was 8.2 wt%, the BEOPA demonstrated a compressive strength of 93.7 MPa, which satisfies the strength requirement for casing damage plugging in oil and gas wells.
The resin plugging agent must possess superior rheological properties to ensure efficacious injection into the crack. In this investigation, the influence of temperature and diluent quantity on the viscosity of resin plugging agents was examined. The viscosity was reduced by the addition of ST to enhance the injection properties. Fig. 4a illustrates the influence of ST quantity and temperature on the viscosity of the resin plugging agent. The viscosity of the mixed solution of ESO and BZ exhibited high values at room temperature in the absence of a diluent. This phenomenon is attributable to the rigid ring structure in the BZ molecular configuration and the strong van der Waals forces between the BZ molecules.The viscosity of the resin plugging agent was 13,600 mPa·s when the quantity of BZ was 24.8 wt%. The viscosity of the resin plugging agent rapidly decreased with the addition of ST. When the ST quantity reached 8.2 wt%, the viscosity of the resin plugging agent decreased to 270 mPa·s. This observation demonstrates that ST effectively reduced the viscosity of BEOPA.
Figure 4: (a) Effect of ST quantity on viscosity with different quantity of BZ; (b) Viscosity-temperature curve for 24.8 wt% BZ; (c) Injection performance of BEOPA; (d) Viscosity-temperature curve for 100°C–150°C
Fig. 4b illustrates the viscosity of BEOPA (with a BZ quantity of 24.8 wt% and ST quantity of 8.2 wt%) at various temperatures. Fig. 4c demonstrates that the injection properties of BEOPA were examined using a steel crack core with a width of 1 mm, and the injection stabilization pressure was 0.06 MPa. The experimental results indicate that BEOPA exhibits excellent injection properties with a viscosity of 270 mPa·s at ambient temperature. As the temperature increased, the viscosity of BEOPA decreased rapidly. At 75°C, the viscosity of BEOPA reduced to 25 mPa·s, enabling it to readily penetrate microcracks for plugging purposes.
Fig. 4d illustrates the viscosity-time curve of the BEOPA (with BZ quantity of 24.8 wt%, ST quantity of 8.2 wt%, and BDMA quantity of 4.0 wt%) at various temperatures. The viscosity of BEOPA remained stable for a duration exceeding 20 min at 150°C and for more than 60 min at temperatures of 100°C and 130°C, demonstrating that BEOPA possesses superior flow properties.
The wellbore constitutes a high-temperature and high-humidity saline environment due to the composition of wellbore fluids, which primarily comprise formation water and crude oil. Resin plugging agents must demonstrate excellent long-term thermal stability in high-temperature and high-humidity saline environment to meet the stability requirements of casing damage repair materials.
The cured BEOPA was subjected to a simulated formation water environment at 130°C, and the quality of BEOPA was assessed on different aging days (Fig. 5). The quality retention of BEOPA was 1.05 after 90 d of aging in a high-temperature and high-humidity saline environment. The experimental results indicated that the resin plugging agent demonstrated exceptional thermal stability under high-temperature and high-humidity salinity conditions.
Figure 5: Quality retention of BEOPA in high-temperature and high-humidity salt environments
The BEOPA was subjected to thermogravimetric analysis to characterize the thermal stability of the resin plugging agent (Fig. 6), which was based on the thermal decomposition properties and characteristic thermal temperatures at different temperatures. These results indicate that BEOPA decomposes in the temperature range of 160°C–500°C. The thermal decomposition of BEOPA can be categorized into two stages. According to the TG-DTG curves, the first stage occurred in the temperature range of 160°C–300°C, with a quality loss of less than 10%. This phenomenon can be attributed to the evaporation of a portion of the ST in BEOPA, which is not engaged in the reaction due to the high temperature. The second stage occurred in the temperature interval from 300°C to 500°C with a quality loss of 80%. At this stage, rapid quality loss occurs due to the breakage of a carbon chain that exhibits poor temperature resistance. The temperature interval from 300°C to 500°C corresponds to the decomposition stage of BEOPA. At 500°C, the remaining quality of the plugging agent was 4.2%. At this point, the main and side chains of BEOPA were completely decomposed, the basic structure was destroyed, and BEOPA was degraded. The DG-DTG results demonstrated that the maximum quality loss rate temperatures ranged from 371°C to 386°C, and BEOPA exhibited excellent thermal stability.
Figure 6: Thermal gravity curve of BEOPA
In conclusion, BEOPA demonstrates superior long-term stability performance in high-temperature and high-humidity saline environments, and it effectively meets the long-term plugging requirements for casing damage repair in oil and gas fields under formation conditions of 100°C–150°C.
Fig. 7 shows the polymerization reaction mechanism of ESO/BZ/MHHPA. Fig. 8 shows the infrared spectrum of the BEOPA reaction solution, and aged BEOPA at 130°C for 1 and 30 days. The peaks at 2855, 2927 cm−1 correspond to the methyl and methylene groups on BZ and ESO, respectively. The peak at 3447 cm−1 was attributed to the phenolic hydroxyl group formed by the ring-opening polymerization of BZ and ESO. The absence of the peak associated with the benzoxazine ring at 944 cm−1 and the diminishing area of the epoxy group peak at 822 cm−1 indicated the occurrence of a polymerization reaction between ESO and BZ. The reaction between ESO and MHHPA was evident in the spectra, as demonstrated by the disappearance of the strong characteristic absorption peaks of anhydride groups at 1859, 1785, 898 cm−1. The peaks at 1736 and 1169 cm−1 are characteristic of ester bonds produced by the polymerization reaction, and the increase in the area confirms the polymerization reaction among ESO, MHHPA, and BZ [41].
Figure 7: Polymerization reaction mechanism of ESO/BZ/MHHPA
Figure 8: Infrared spectra of BEOPA reaction solution, BEOPA aging for 1 day, and BEOPA aging for 30 days
A lower glass transition temperature correlates with diminished mechanical properties of the resin at elevated temperatures. Consequently, following the modification of ESO with BZ, the glass transition temperature of BEOPA was substantially higher than those of EPA and EOPA (Fig. 9), thereby ensuring superior mechanical properties at elevated temperatures [42].
Figure 9: DSC heating thermograms of EOPA, EPA, and BEOPA
The fracture surface morphology of the resin plugging agent is depicted in Fig. 10. The fracture surface in Fig. 10a exhibited a rough and uneven texture with a sparse distribution of silver cracks. This observation indicates that subsequent to modification with BZ (Fig. 10b), the fracture surface exhibited a flat and smooth appearance, accompanied by an increased number of silver cracks with a dense and uniform distribution. Following the modification of ESO with BZ, the molecular chains of ESO and BZ became intertwined, resulting in the formation of a robust and dense double-crosslinked network structure. This finding suggests that the incorporation of BZ facilitates the generation of silver cracks shear bands, enabling the material to absorb more energy and undergo a transition from brittle to ductile behavior [43].
Figure 10: SEM spectra of EBOPA: (a) Unmodified; (b) Modified
The plugging properties of the BEOPA in cracks were investigated utilizing core flooding experiments. Fig. 11a illustrates the plugging performance of the BEOPA on steel cores with varying crack widths. The results indicate that the narrower the crack width of the steel core, the higher the plugging strength of the BEOPA. For a crack with a width of 1 mm, the plugging strength is 29.7 MPa, which is approximately 2.02 times that of a 2 mm crack. These findings demonstrate that the BEOPA exhibits excellent plugging performance for microcracks. Fig. 11b depicts the plugging strength of BEOPA, EPA, and EOPA resin plugging for a 1 mm crack. The results reveal that BEOPA demonstrates superior plugging performance compared to EPA and EOPA.
Figure 11: Plugging performance of the BEOPA. (a) Plugging performance for different fracture widths; (b) Plugging performance of different materials
This phenomenon can be attributed to BEOPA’s lower curing shrinkage rates, in contrast to the higher curing shrinkage exhibited by EP and ESO. Consequently, BEOPA demonstrates minimal shrinkage post-curing, resulting in superior sealing strength for cracks compared to EPA and EOPA. The double cross-linked network formed by ESO and BZ exhibited enhanced mechanical properties, and BEOPA demonstrated resistance to cracking due to formation creep or pressure, thus possessing an excellent plugging strength. As a result, BEOPA exhibits superior plugging strength and is suitable for long-term applications in casing damage repair in oil and gas fields.
Well X-3 was produced in the Sichuan Basin over an extended period of time. During the fourth stage of fracturing, the pressure of well X decreased by 20 MPa, and casing damage was suspected to impede the normal progression of the fracturing operation. Through downhole television inspection, noise logging, and well temperature logging, it was determined that the damage point was located at 4615–4627 m, where the formation temperature was 127°C. Initially, a slug was placed below the leakage point. Utilizing a surface cement truck to inject 6 m3 of isolation fluid, 1.35 m3 of BEOPA (41.4 wt% ESO, 24.8 wt% BZ, 24.8 wt% MHHPA, 8.2 wt% ST, and 0.8 wt% BDMA) and 1 m3 of flushing fluid were injected into the casing to plug the damaged section. Upon completion of the sealing operation, the test pressure was 27 MPa with no observed pressure drop. Subsequently, normal production was conducted for 90 d without any casing damage, indicating that the resin plugging agent met the plugging requirements.
Epoxy resin plugging agents are costly and non-renewable, while plant-based resin plugging agents exhibit inferior mechanical properties. In this study, an epoxy soybean oil-based resin plugging agent was synthesized using a bisphenol A-type benzoxazine-modified epoxy soybean oil. The reaction mechanism of BEOPA was elucidated through FTIR and SEM analyses. Subsequently, the rheological, mechanical, stability, and plugging properties of BEOPA were examined. The conclusions of this study are as follows:
(1) The optimum formulation of BEOPA was 41.4 wt% ESO, 24.8 wt% BZ, 24.8 wt% MHHPA, 8.2 wt% ST, and 0.8 wt% BDMA. When the BZ dosage was 24.8 wt%, the compressive strength was 93.7 MPa.
(2) The curing time can be controlled from 3 to 15 h with a BDMA dosage of 0–1.6 wt%. When the amount of ST was 8.2 wt%, the viscosity of the BEOPA was 270 mPa·s at 25°C. As the temperature increased to 75°C, the viscosity decreased to 25 mPa·s.
(3) FTIR and SEM analyses revealed a strong and dense double-cross-linked network structure formed by the ring-opening polymerization reaction of the epoxy group of ESO and the oxazine ring of BZ.
(4) After aging for 90 days in high-temperature and high-humidity saline environment, the BEOPA shape remained intact and did not degrade, with a quality retention of 1.05. The plugging strength of the BEOPA in the 1 mm crack core was 29.7 MPa. The comparative experiments demonstrate that the plugging efficacy of the BEOPA exceeds that of the EPA and EOPA. The BEOPA has demonstrated excellent performance in oilfield applications.
Acknowledgement: The authors would like to thank the reviewers and editors for their useful suggestions for improving the quality of our manuscript.
Funding Statement: This work was supported by the National Natural Science Foundation of China (U23B20156, 52174033).
Author Contributions: The authors confirm contribution to the paper as follows: study conception and design: Dingyuan Zhang; data collection: Yongming Li; analysis and interpretation of results: Yadong Chen; draft manuscript preparation: Jiandu Ye. All authors reviewed the results and approved the final version of the manuscript.
Availability of Data and Materials: The authors confirm that the date supporting the findings of this study are available within the article.
Ethics Approval: Not applicable.
Conflicts of Interest: The authors declare no conflicts of interest to report regarding the present study.
Abbreviations
BEOPA | Benzoxazine-modified epoxidized soybean oil |
BZ | Bisphenol A-type benzoxazine |
ESO | Epoxy Soybean Oil |
MHHPA | Methylhexahydrophthalic anhydride |
ST | Styrene |
BDMA | N, N-dimethylbenzylamine |
EOPA | The epoxidized soybean oil plugging agent |
EPA | The epoxy resin plugging agent |
References
1. Yousuf N, Olayiwola O, Guo B, Liu N. A comprehensive review on the loss of wellbore integrity due to cement failure and available remedial methods. J Pet Sci Eng. 2021;207:109123. doi:10.1016/j.petrol.2021.109123. [Google Scholar] [CrossRef]
2. Michael A, Gupta I. Wellbore integrity after a blowout: stress evolution within the casing-cement sheath-rock formation system. Resul Geophys Sci. 2022;12:100045. doi:10.1016/j.ringps.2022.100045. [Google Scholar] [CrossRef]
3. Tan K, Liu R, Luo J, Zhu Y, Wei W, Liu X. Tannic acid functionalized UV-curable carbon nanotube: effective reinforcement of acrylated epoxidized soybean oil coating. Prog Org Coat. 2019;130:214–20. doi:10.1016/j.porgcoat.2019.01.035. [Google Scholar] [CrossRef]
4. Kutchko BG, Strazisar BR, Lowry GV, Dzombak DA, Thaulow N. Rate of CO2 attack on hydrated class H well cement under geologic sequestration conditions. Environ Sci Technol. 2008;42(16):6237–42. doi:10.1021/es800049r. [Google Scholar] [PubMed] [CrossRef]
5. Yan W, Xu Y, Zhou Y, Wang K. Investigation of stress concentration and casing strength degradation caused by corrosion pits. Int J Corrosion. 2016;2016(1):1–6. doi:10.1155/2016/6930234. [Google Scholar] [CrossRef]
6. Li T. Solid expandable tubular patching technique for high-temperature and high-pressure casing damaged wells. Pet Explor Dev. 2015;42(3):408–13. doi:10.1016/S1876-3804(15)30032-X. [Google Scholar] [CrossRef]
7. Han ZQ, Jiang BQ, Zhou J, Wang YS, Zhang JH, Liu XZ. Application of suspension packing technique in oversea casing repair well. Oil Drill Product Technol/Shiyou Zuancai Gongyi. 2014;36(2):122–5. [Google Scholar]
8. Wang XQ, Jiang JX, Wang BM. Chemical plugging technology for casing damaged wells and its popularization in Changqing Oilfield. Nat Gas Explor Dev. 2007;4:56–9. [Google Scholar]
9. Cao B, Xie K, Lu X, Cao W, He X, Xiao Z et al. Effect and mechanism of combined operation of profile modification and water shutoff with in-depth displacement in high-heterogeneity oil reservoirs. Colloi Surf A: Physicochem Eng Asp. 2021;631(4):127673. doi:10.1016/j.colsurfa.2021.127673. [Google Scholar] [CrossRef]
10. Zhao ZF, Chen MY, Fang H, Zhang NI. Safety evaluation of comprehensive dynamic for the external anti-corrosive system of long-distance pipeline. Paper presented at: Proceedings of the International Petroleum and Petrochemical Technology Conference 2020; 2021 Mar 16; Singapore: Springer. p. 312–26. [Google Scholar]
11. Sun Y, Zhang W, He Y, Kong S, Liu Y, Han R. A novel application of new high-strength plugging agent in baikouquan oilfield. Appl Sci. 2022;12(8150):8150. doi:10.3390/app12168150. [Google Scholar] [CrossRef]
12. Huang Q, Li X, Wu Y. Water-resistant toughening modification of wood fiber-reinforced gypsum-based composites. J Central South Univ Forest Technol. 2024;44(2):174–83. doi:10.14067/j.cnki.1673-923x.2024.02.019. [Google Scholar] [CrossRef]
13. Ramadan MA, Salehi S, Teodoriu C. Robust leakage modeling for plug and abandonment applications. Paper presented at: 38th ASME International Conference on Ocean, Offshore and Arctic Engineering; 2019 Jun 9–14; Glasgow, Scotland, UK. [Google Scholar]
14. Fan X, Zhao P, Zhang Q, Zhang T, Zhu K, Zhou C. A polymer plugging gel for the fractured strata and its application. Materials. 2018;11(5):856. doi:10.3390/ma11050856. [Google Scholar] [PubMed] [CrossRef]
15. Liu H, Guo J, Sun R, Zheng J. Preparation and application of silicate gel plugging agent in water-flooding reservoir. Oilfield Chem. 2018;35(1):64–7. [Google Scholar]
16. Moradi-Araghi A, Doe PH. Hydrolysis and precipitation of polyacrylamides in hard brines at elevated temperatures. SPE Reserv Eng. 1987;2(2):189–98. doi:10.2118/13033-PA. [Google Scholar] [CrossRef]
17. Moradi-Araghi A. A review of thermally stable gels for fluid diversion in petroleum production. J Pet Sci Eng. 2000;26(1):1–10. doi:10.1016/S0920-4105(00)00015-2. [Google Scholar] [CrossRef]
18. Medina NR, Diaz JD, Pachon LF. Application of concentric coiled-tubing and well-vacuuming tool with chemical sand-consolidation resins for controlling sand production in wells with damaged screens or slotted liners: a rigless well-repair alternative. Paper presented at: SPE Latin American and Caribbean Petroleum Engineering Conference; 2010 Dec 1; Lima, Peru. [Google Scholar]
19. Alsaihati ZA, Al-Yami AS, Wagle V, BinAli A, Mukherjee TS, Al-Kubaisi A et al. An overview of polymer resin systems deployed for remedial operations in Saudi Arabia. Paper presented at: SPE Kingdom of Saudi Arabia Annual Technical Symposium and Exhibition; 2017 Apr 24; Dammam, Saudi Arabia. [Google Scholar]
20. Todd L, Cleveland M, Docherty K, Reid J, Cowan K, Yohe C. Big problem-small solution: nanotechnology-based sealing fluid. Paper presented at: SPE Annual Technical Conference and Exhibition; 2018 Sep 24; Dallas, TX, USA. [Google Scholar]
21. Guo G, Li Q, Yang L, Lu W. Development and application of organic resin for controlling loss of borehole fluids in cased hole. Drill Flu Complet Fluid. 2019;36(5):659–62. doi:10.3969/j.issn.1001-5620.2019.05.023. [Google Scholar] [CrossRef]
22. Chen Y, Li Y, Peng Y, Zhang D, Ye J, Jiang Y. Preparation of low-viscosity epoxy resin sealing agent and evaluation of injection, plugging, and degradation properties. ACS Omega. 2024;9(18):19992–20002. doi:10.1021/acsomega.3c10034. [Google Scholar] [PubMed] [CrossRef]
23. Alkhamis MMM. Evaluation of robust epoxy resin sealants for wellbore integrity applications [dissertation]. Rolla, MO, USA: Missouri University of Science and Technology; 2021. 201 p. [Google Scholar]
24. Beharie C, Francis S, Øvestad KHeditors. Resin: an alternative barrier solution material. Paper presented at: SPE Bergen One Day Seminar; 2015 Apr 22; Bergen, Norway. [Google Scholar]
25. Maia DLH, Fernandes FAN. Influence of carboxylic acid in the production of epoxidized soybean oil by conventional and ultrasound-assisted methods. Biomass Convers Biorefinery. 2022;12(12):5861–8. doi:10.1007/s13399-020-01130-0. [Google Scholar] [CrossRef]
26. Chavan VP, Patwardhan AV, Gogate PR. Intensification of epoxidation of soybean oil using sonochemical reactors. Chem Eng Process Process Intensification. 2012;54:22–8. doi:10.1016/j.cep.2012.01.006. [Google Scholar] [CrossRef]
27. Thomas J, Patil R. Enabling green manufacture of polymer products via vegetable oil epoxides. Indust Eng Chem Res. 2023;62(4):1725–35. doi:10.1021/acs.iecr.2c03867. [Google Scholar] [CrossRef]
28. Kumar S, Samal SK, Mohanty S, Nayak SK. Epoxidized soybean oil-based epoxy blend cured with anhydride-based cross-linker: thermal and mechanical characterization. Indust Eng Chem Res. 2017;56(3):687–98. doi:10.1021/acs.iecr.6b03879. [Google Scholar] [CrossRef]
29. Yang Y, Tu Y, Lou Z, Gui X, Kong J, Huang Z. Rapid UV-curable preparation of durable soybean oil-based superhydrophobic anti-icing surfaces with excellent photothermal deicing property. Appl Surf Sci. 2024;653(3):159423. doi:10.1016/j.apsusc.2024.159423. [Google Scholar] [CrossRef]
30. Díez-Pascual AM, Díez-Vicente AL. Epoxidized soybean Oil/ZnO biocomposites for soft tissue applications: preparation and characterization. ACS Appl Mat Interf. 2014;6(19):17277–88. doi:10.1021/am505385n. [Google Scholar] [CrossRef]
31. Zhang J, Hu S, Zhan G, Tang X, Yu Y. Biobased nanocomposites from clay modified blend of epoxidized soybean oil and cyanate ester resin. Prog Org Coat. 2013;76(11):1683–90. doi:10.1016/j.porgcoat.2013.07.017. [Google Scholar] [CrossRef]
32. Dai X, Xiong Z, Na H, Zhu J. How does epoxidized soybean oil improve the toughness of microcrystalline cellulose filled polylactide acid composites? Compos Sci Technol. 2014;90(8):9–15. doi:10.1016/j.compscitech.2013.10.009. [Google Scholar] [CrossRef]
33. Belcher LKA. The development of biocomposites from aligned biofiber and biobased epoxy resin [dissertation]. East Lansing, MI, USA: Michigan State University; 2002. 89 p. [Google Scholar]
34. Hayaty M, Honarkar H, Beheshty MH. Curing behavior of dicyandiamide/epoxy resin system using different accelerators. Iran Polym J. 2013;22(8):591–8. doi:10.1007/s13726-013-0158-y. [Google Scholar] [CrossRef]
35. Khalina M, Beheshty MH, Salimi A. The effect of reactive diluent on mechanical properties and microstructure of epoxy resins. Polym Bull. 2019;76(8):3905–27. doi:10.1007/s00289-018-2577-6. [Google Scholar] [CrossRef]
36. Lakho DA, Yao D, Cho K, Ishaq M, Wang Y. Study of the curing kinetics toward development of fast-curing epoxy resins. Polym Plast Technol Eng. 2017;56(2):161–70. doi:10.1080/03602559.2016.1185623. [Google Scholar] [CrossRef]
37. Jubsilp C, Punson K, Takeichi T, Rimdusit S. Curing kinetics of Benzoxazine-epoxy copolymer investigated by non-isothermal differential scanning calorimetry. Polym Degrad Stab. 2010;95(6):918–24. doi:10.1016/j.polymdegradstab.2010.03.029. [Google Scholar] [CrossRef]
38. Zhang K, Liu Y, Han M, Froimowicz P. Smart and sustainable design of latent catalyst-containing benzoxazine-bio-resins and application studies. Green Chem. 2020;22(4):1209–19. doi:10.1039/C9GC03504D. [Google Scholar] [CrossRef]
39. Hua Z, Liang G, Lv M, Zhu X. Study on the mechanical property of resin-curing agent in EP composite. New Chem Mat. 2022;50(5):180–4. [Google Scholar]
40. Zhang Y, Cao D, Zhang H, Wu X. The study of curing characteristics of epoxy asphalt. Current Tren Develop Indus. 2013;785–786:295–9. doi:10.4028/www.scientific.net/AMR.785-786.295. [Google Scholar] [CrossRef]
41. Wu J, Zhao C, Li Y, Li H, Xiang D, Sun Z, et al. Properties of bio-based thermosetting composites synthesized from epoxidized soybean oil and azo-cardanol benzoxazine. J Polym Res. 2021;28(3):1–12. doi:10.1007/s10965-021-02442-z. [Google Scholar] [CrossRef]
42. Farzi N, Ebrahim M. Mechanical properties and glass transition temperature of metal-organic framework-filled epoxy resin: a molecular dynamics study. Mater Chem Phys. 2024;314:128874. doi:10.1016/j.matchemphys.2023.128874. [Google Scholar] [CrossRef]
43. Bucknall CB, Smith RR. Stress-whitening in high-impact polystyrenes. Polymer. 1965;6(8):437–46. doi:10.1016/0032-3861(65)90028-5. [Google Scholar] [CrossRef]
Cite This Article
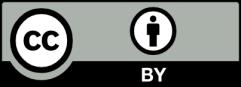
This work is licensed under a Creative Commons Attribution 4.0 International License , which permits unrestricted use, distribution, and reproduction in any medium, provided the original work is properly cited.