Open Access
ARTICLE
Production and Characterization of a Composite Based on Plaster and Juncus Maritimus Plant Fibers
1 Laboratory of Thermodynamics and Energetics, Faculty of Science, University of Ibn Zohr, Dakhla, Agadir, 80000, Morocco
2 National School of Architecture Agadir, New Complex, University of Ibn Zohr, Dakhla, Agadir, 80000, Morocco
* Corresponding Author: Mina Amazal. Email:
(This article belongs to the Special Issue: Materials and Energy an Updated Image for 2023)
Fluid Dynamics & Materials Processing 2024, 20(9), 2059-2076. https://doi.org/10.32604/fdmp.2024.050613
Received 12 February 2024; Accepted 13 June 2024; Issue published 23 August 2024
Abstract
Nowadays, materials with a limited impact on the environment are required in the construction sector. Considering the interesting properties of natural elements such as natural fibers, it seems advantageous to use them to reinforce materials while protecting the environment and guaranteeing economic gain. Along these lines, this research was devoted to studying the effect of untreated natural fibers extracted from the Juncus maritimus plant (from Southern Morocco) on plaster. First, the effect of the percentage of added fibers on the fluidity of the plaster was evaluated by means of the Marsh’s cone method, that is, by measuring the time taken by a known volume of plaster to flow from a cone through a short tube. Then, the highly porous microstructure of the plaster was observed using a scanning electron microscope (SEM). The diffractogram of Juncus maritimus fibers was built by means of a X-ray diffraction (XRD) method. The values obtained for the wet thermal conductivity of the composites decreased from 0.4853 W/m.K for the reference specimen to 0.4324 W/m K for a fiber volume content of 40%. The densities were calculated to determine the lightness of each composite. The mechanical strengths [flexural and compressive] were evaluated for different percentages of rush fibers. The addition of 20% volume fiber was found to improve the flexural strength to 3.63 MPa compared to the sample without fiber (3.36 MPa), thereby ensuring good toughness of the considered material. Nevertheless, a reduction in compressive strength was observed, due to the poor adhesion between the fibers and the plaster matrix.Keywords
Nomenclature
T | Temperature |
JM | Juncus Maritimus |
Gypsum plasterboard is frequently used in construction for wall cladding, false ceilings and home decoration. Its composition ensures fire-retardant performance, depending on thickness and good thermal insulation, which is why it is used in smoke extraction ducts and public areas requiring sufficient fire-retardant time to evacuate residents [1,2]. It also has a number of advantages, in particular, its wide availability, low cost and very short setting time with rapid drying [3]. But despite these many advantages, the use of this material remains restricted, as it has undesirable characteristics, namely brittleness, poor resistance to bending and tension, and deterioration in damp locations, which precludes its application outdoors [4].
Incorporating a binder with natural fibers improves the thermomechanical properties of the composite material, particularly its post-cracking behavior [2,5,6]. In fact, combining plaster with plant fibers can reduce its brittleness. The use of natural fibers combines two expectations demanded by the construction industry, their ecological behavior and, therefore low environmental impact and socio-economic advantages [7]. Natural fibers are characterized by low cost, low thermal conductivity (because they have a porous microstructure), low density and good mechanical properties, particularly tensile strength [8], these interesting properties of natural fibers make them a competitor to synthetic fibers in the construction sector [7].
Recent scientific research has attempted to estimate the thermal, mechanical and acoustic behavior of natural fibers reinforced plaster. Mehrez et al. [9] studied the thermophysical behavior of plaster reinforced with straw and wood fibers; they concluded that reinforcing composites with wood fibers enhanced their thermal characteristics compared with straw fibers, thanks to their lower thermal conductivity. Recently, Charai et al. [10] examined the thermal behavior of plaster incorporated with Moroccan hemp fibers, and showed that partial replacement of plaster by hemp stalks can improve thermal comfort for residents. Iucolano et al. [4] compared the impact of three chemical treatments, NaOH, distilled water and EDTA of abaca fibers on the mechanical behavior of the plaster matrix and concluded that treating abaca fibers with distilled water improved the mechanical characteristics of biocomposites compared to the other chemical treatments used. Further research by Iucolano et al. [5] compared the impact of glass fibers and hemp fibers on the mechanical behavior of plaster and highlighted the competition between glass fibers and hemp fibers. The acoustic effect of alfa and wood fibers was investigated by Cherradi et al. [11], who deduced from the sound absorption coefficient values of biocomposites that these developed materials can be used as a replacement for commercial synthetic materials. All this scientific research has demonstrated the thermal, mechanical and acoustic advantages of natural fibers over plaster, with the aim of meeting socio-economic expectations and reducing energy consumption.
Juncus maritimus is a new plant used in the construction. It is a widespread member of the Juncaceae family, which numbers around 200 species; it can easily adapt to different environmental conditions, particularly in places characterized by the presence of water, generally wetlands and aquatic environments [12]. New scientific research has investigated the feasibility of using Juncaceae family fibers as reinforcing materials for various matrices. For example, Saghrouni et al. [13] examined the effect of Juncus maritimus on the thermal behavior of cement mortar and found that the porosity of composites increased as the amount of fiber increased, consequently improving the thermal characteristics of composites. Saghrouni et al. [14] have used chemical treatment of JM fibers to enhance the mechanical behavior of cement mortars and showed the mechanical characteristics of cement mortar incorporated with treated Juncus maritimus fibers were improved over those incorporated with untreated Juncus maritimus fibers. Another type of Juncussae fiber, Juncus acutus, has been treated with a clay matrix. Maaloufa et al. [15] examined the impact of Juncus acutus on the thermomechanical behavior of a clay mortar composed of 60% clay and 40% sand and showed that these Juncus acutus fibers improved thermal conductivity and the density of the composites developed, but a significant reduction in mechanical properties was observed. Recently, Sadouri et al. [16] studied the behavior of compressed brick incorporated with Juncus acutus fibers and found that the thermal conductivity and bulk density of the bricks produced were improved, with a favorable impact on the ultrasonic pulse velocity, which will improve acoustic insulation, but compressive strength of the bricks has been dropped. All this new research has focused on the impact of the addition of Juncus fibers on the thermophysical and mechanical behavior of cement-based and clay-based materials. Thanks to their encouraging results regarding the characteristics of these fibers, this study aims to verify the feasibility of a new plaster material reinforced with Juncus maritimus fibers.
The aim of this research is to study the impact of incorporating Juncus maritimus fibers on the thermophysical and mechanical characteristics of plaster using different fiber volume contents (0%, 10%, 20%, 30% and 40%). With the aim of using these Juncus maritimus as a sustainable variant for the production of gypsum plasterboard with improved thermal and mechanical performance.
2.1 Description of Raw Materials
The Juncus maritimus plant, illustrated in Fig. 1a, from the Tamri area (30°41′42″ North, 9°49′30″ West) (Fig. 1b), was used to develop a new composite of plaster and Juncus maritimus. This plant is widespread in this region; it has the shape of a tuft of grass composed of a white spongy substance, surrounded by a cylindrical stem with an average length of around 1 m and a diameter of 4–8 mm [12], it grows particularly in humid and saline areas [15].
Figure 1: (a) Juncus maritimus plant, (b) location of Juncus maritimus plant on aerial map
The plaster used (Fig. 2) is NAKCH ASRI [17] semi-hydrated coarse building gypsum (CaSO4, 1/2 H2O), produced by calcining natural gypsum at around 150°C according to Eq. (1).
(1)
Figure 2: Plaster powder
2.2 Thermophysical Properties of Plaster and JM Fibers
The thermophysical properties of the plaster and JM fibers studied are presented in Table 1. The apparent density of plaster and cruched JM fibers is the quotient obtained by dividing their dry masses filling a specified container without compaction by the volume of the container [18]. The thermal diffusivity and conductivity of ground Juncus maritimus fibers and plaster powder were measured using the HOT DISK TPS 1500 in accordance with ISO 22007-2 [19]. Ground Juncus maritimus fibers and plaster powder were placed in a cylindrical sample holder, and the HOT DISK sensor was placed in the center of the two-part cylinder, with the powder added first to the lower compartment and then to the upper face of the sensor. Once the sample had been placed in the sample holder, mechanical pressure was applied using pistons.
2.3 Characterization of Raw Materials
2.3.1 Mineralogical Composition of Juncus Maritimus Fibers
The crystalline nature of Juncus maritimus fiber powder was determined by X-ray diffraction (XRD) using a Bruker D8 Advance Twin diffractometer. The diffractogram of Juncus maritimus fibers is shown in Fig. 3. This analysis provides qualitative information on the quantity of cellulose contained in the fibers studied, in order to assess the thermal and mechanical insulation efficiency of plant fibers in the production of construction materials [20]. Fig. 3 shows 3 major reflection peaks (2 θ = 15.6°, 22.19° and 34.7°) corresponding to cellulose I (C6H10O5), determined from XRD reference patterns. The crystallinity index was calculated with the Eq. (2) below [21]:
(2)
With:
corresponds to the maximum intensity of the crystalline zone,
is the intensity of the peak corresponding to the amorphous zone.
Figure 3: X-ray diffraction peaks of JM fibers
The value of the crystallinity index of Juncus maritimus fibers is 42.45%, this value shows that Juncus maritimus fibers have a high cellulose content, which can improve the thermomechanical characteristics of construction materials. The crystallinity index value of Juncus maritimus fibers found is lower than that of Cissus quadrangularis stem fibers (47.15%) [22], and higher than that of untreated date palm (19.9%) [23].
2.3.2 Microstructural Characterization of Plaster and JM Fibers
The microstructure of Juncus maritimus stem and plaster was determined by JEOL JSM IT-100 scanning electron microscopy (SEM), and semi-quantitative chemical element analysis was performed using an energy-dispersive X-ray spectrometer (EDS). The microstructure of the outer surface of the Juncus maritimus stem presented in Fig. 4a shows the rough outer appearance of the fibers and veins parallel to the fiber axis. This grooved structure of the fibers can improve the mechanical coupling of the fibers with the plaster, which can influence the post-peak behavior of the composite material. SEM observations of the cross-section of the Juncus maritimus stem show a porous structure that effectively improves the thermal performance and lightness of the composites (Fig. 4c). Fig. 4b,d shows the curves obtained from the EDS analysis spectrum of the outer surface and cross-section of Juncus maritimus, revealing a significant amount of oxygen and carbon as constituents of these fibers, the other components are observed in the cross-section of Juncus maritimus (chlorine and potassium) which may be contaminations. Fig. 4e shows the morphology of the plaster studied, which is considered microporous, consisting of an assembly of microcrystals. Fig. 4f shows the main elements in the plaster studied: Ca, S, O and a trace of C.
Figure 4: SEM analysis of the studied stem and plaster: (a) external face of stem, (c) cross-section of stem and (e) plaster. EDS analysis of studied stem and plaster: (b) outer face stem, (d) cross-section of stem and (f) plaster
The elaboration procedure followed consists in reinforcing the plaster sample with Juncus maritimus fibers as an ecological additive by varying the percentages in volume of the fibers starting with a reference sample without fibers (0%) incrementing by a step of 10% until reaching 40%.
The method of incorporating fibers varies according to the author and the type of fiber. There are several methods of distributing fibers in either random or structured form that can affect the mechanical behavior of composites [24,25]. In our case, we mixed the ground fibers randomly with the plaster matrix since the Juncus surface is rather smooth and cannot be used directly due to its cylindrical shape (Fig. 5a). The samples were elaborated by mixing plaster and fibers until a homogeneous mixture was obtained. After drying and grinding, the fibers were sieved to a mesh size of between 0.315 and 2 mm as shown in Fig. 5b. When the quantity of fibers is increased in the plaster, we observe that the workability of the mixture during processing decreases with the addition of fibers, this may be explained by the hydrophilic nature of the fibers, which also increases the time required to harden the samples, as the fibers retain water and require time for the water to escape from the sample. Solids/Water = 1.33 is the ratio used in the manufacture of all samples [17]. The resulting mixtures were placed in 4 × 4 × 16 cm3 according to EN 13279-2 [26] and 10 × 10 × 2.5 cm3 molds [19] for mechanical and thermal testing, respectively. After demolding, the specimens were dried under laboratory conditions (20°C ± 2°C, 65% ± 2% RH) for 28 days until the mass of the samples is obtained constant. Fig. 6a shows the mixing of JM fibers with plaster and Fig. 6b shows the shapes of the samples after demolding. We prepared three specimens of each mixture for mechanical testing, and two specimens for thermal testing. The results obtained are presented as average values of the results of the various analyses carried out.
Figure 5: (a) Dry stems of JM, (b) fibers after the operation of grinding and sieving
Figure 6: (a) Mixing of fibers with plaster, (b) shapes of demolded composites
2.5 Rheological Behavior of Plaster Pastes
Rheology, as a science concerned with the characterization of fluids and their ability to deform under external shear stress, is more exact than conventional workability tests, which are in large part based on empirical investigations [27]. It is an effective tool for controlling flowability and workability, as well as for predicting their stability (avoiding segregation), injectability and pumpability. The term “rheology” was introduced by Bingham in 1920. Rheological parameters are useful for quantifying and assessing the fresh physical characteristics of a material [28].
Rheological behavior can be studied using a laboratory Rheometer. Gutiérrez-González et al. [29] have recapitulated the results of plastic viscosity, fluidity and shear stress tests for gypsum samples, as shown in Table 2.
There are a number of in-situ techniques that are often used, as they require only simple tools that enable rapid but global measurements of grout fluidity. Among these, the Marsh cone is frequently used to characterize the global fluidity of grouts. This is linked to their rheological behavior [30].
The Marsh cone is a simple tool in accordance with NF P 18-358 [31]. It consists of a truncated cone with a removable cylindrical nozzle at the bottom. To measure the flowability of grout using the Marsh cone, the time taken for a given volume of grout (1 liter) to flow through the nozzle is measured. The shorter the flow time, the greater the flowability of the grout. Fig. 7 shows the Marsh cone used in this manipulation.
Figure 7: Manipulation of Marsh cone on the plaster paste incorporated by JM fibers
Fig. 8 shows the impact of adding JM fibers on the flow time. We can observe from Marsh’s cone manipulation that adding fibers increases the paste flow time and decreases their fluidity, thus impacting directly on the composites viscosity [29].
Figure 8: Impact of adding JM fibers on the flow time of plaster paste using the Marsh cone
2.6.1 Measurement of Apparent Density
The apparent density of wet composites is calculated from the ratio between the two quantities representing the weight and volume characterizing the sample. The mass of the latter was measured using a Kern PCB electronic balance accurate to 0.01 g, and the volume was measured using the actual dimensions of each prototype.
2.6.2 Measurement of Thermal Properties
Determination of the thermal diffusivity and conductivity of prepared specimens, was carried out using the HOT DISK TPS 1500 [19]. The measurement technique is based on the use of a double spiral probe, which acts both as a temperature sensor and a heat source. This probe is inserted between the two identical samples to be characterized, as shown in Fig. 9. Details of the handling and equations governing the method are referred to in previous studies [32,33]. The diffusivity and thermal conductivity of processed samples were measured in the wet state under laboratory conditions (20°C ± 2°C, 65% ± 2% RH) after a 28-day curing period.
Figure 9: Measurement of thermal properties
Three-point bending and compressive tests were performed using a Controls Automax5 machine and Microdata Auto-driver software on prismatic specimens measuring 4 × 4 × 16 cm3, which were prepared for the bending test (Fig. 10a), and the half specimens obtained with dimensions 4 × 4 × 8 cm3 were reserved for the compressive test (Fig. 10b) in accordance with standard NF EN 196-1 [34]. To determine flexural strength, the sample is placed on two steel support rollers, spaced (10.0 ± 0.05) cm apart, and the load is applied vertically to the side face, increasing it regularly up to 10 kN with a precision equal to ± 1.0% of the load recorded at a speed of (50 ± 10) N/s, until breaking occurs. The flexural strength obtained is the average of the strength values of the three specimens for each mixture, and it is expressed as follows:
(3)
With:
(MPa) represents the bending strength,
(N) is the maximum load applied to the middle of the prism at the moment of failure,
l (mm) is the distance between the supports,
b (mm) is the side of the square section of the prism.
Figure 10: (a) Three-point bending tests, (b) compressive tests
To determine compressive strength, load was applied to the side faces of both halves of the broken prism, measuring 4 × 4 × 8 cm3, steadily increasing the load at a rate (2400 ± 200) N/s until failure. The compressive resistance is calculated using the following formula:
(4)
where:
(MPa) represents the compressive strength,
(N) represents the maximum breaking load,
1600 (mm2) is the lateral surface area of the 40 × 40 mm2 section.
In recent years, lightweight building materials have become essential for reducing construction times and greenhouse gas emissions. Indeed, the aim is to develop low-density building materials using plant fibers, which can also positively affect thermal and acoustic insulation properties [11,35]. This section is devoted to studying the effect of fiber incorporation on plaster lightness with the aim of testing their feasibility in the manufacture of lightweight boards.
Fig. 11 shows the evolution of the bulk density of different composites studied, and their errors determined by the difference between the maximum and average value of each composition. The wet apparent density of composites decreases with increasing volume of Juncus maritimus fiber additive, varying from 1009.75 kg/m3 for the reference sample to 944.54 kg/m3 for a 40% fiber volume. These results show that Juncus maritimus fibers act as pore-formers in the plaster matrix, resulting in low-density composites. These results are also due to the low density of Juncus maritimus fibers (216.45 kg/m3) compared to the density of plaster (852.35 kg/m3) (Table 1). These variations in apparent density were obtained by Mehrez et al. [9], who showed that the bulk density of dried plaster composites decreased as the addition of cereal straw and wood fiber increased. Other research has shown the same trend of variation in the density of plaster composites incorporated with fibers studied by Maaloufa et al. [15], and Bouzit et al. [16].
Figure 11: Bulk density of different composites
Fig. 12a shows the evolution of the thermal conductivity of composites in the wet state for different fiber contents. The thermal conductivity of composites decreases with increasing JM fiber content in the plaster matrix, from a value of 0.4853 W/m.K for the sample without reinforcement to 0.4324 W/m.K for the composite with 40% volume content, by a rate of decrease of 10.9%. This reduction in the thermal conductivity of the biocomposite is due to the fact that the thermal conductivity of the Juncus maritimus fibers (0.084 W/m.K) was lower than that of plaster (0.24 W/m.K) (Table 1), results show that less conductive composites can be produced from embedding materials with low thermal conductivity. Furthermore, the thermal conductivity of biocomposites depends not only on the low thermal conductivity of fibers but also on the decrease in the apparent density of the biocomposites when the quantity of fibers increases in the plaster matrix (Fig. 11), which translates into the creation of pores inside the biocomposites due essentially to the porous structure of the JM fibers observed by SEM (Fig. 4c), and also to the high cellulose content of these fibers (Fig. 3) [36]. The creation of these pores may also be due to the disruption of the plaster mineral skeleton, leading to the creation of voids inside which are filled essentially by air, which is considered an insulating material. Several authors have observed a decrease in thermal conductivity as porosity increases in the material studied [2,10,37]. Consequently, the lower the density of the sample, the lower its thermal conductivity. This relationship between density and thermal conductivity has been confirmed by a number of studies [15,37], which have revealed that it is still true for mineral matrix materials incorporated with plant fibers.
Figure 12: (a) Wet thermal conductivity of composites, (b) correlation between density and thermal conductivity, (c) thermal diffusivity at different fiber volume contents
The relationship between bulk density and thermal conductivity of composites with different fiber contents is shown in Fig. 12b. Composite thermal conductivity decreases as composite apparent density increases. A correlation is obtained between these two values expressed by the following formula: y = Â 0.0007x–0.1817, which corresponds to a correlation coefficient R2 = 0.8762. These results are similar to several previous studies [38,39].
Thermal diffusivity characterizes the rate at which heat is transmitted by conduction through the body. Fig. 12c shows that the thermal diffusivity of composites decreases as the additive content increases, corresponding to a reduction rate of 14.88% at 40% additives compared with the reference sample. This decrease in thermal diffusivity is explained by the low diffusivity of JM fibers compared with plaster (Table 1), so the addition of these fibers allows the heat front to take longer to penetrate the composite thickness.
Fig. 13 shows the variations in three-point flexural strength of composites with different volume contents of Juncus maritimus fibers. The flexural strength of the 10% fiber-reinforced sample is lower than that of the reference sample, showing that the addition of this percentage does not improve the material’s flexural strength. While the addition of 20% fibers improves the flexural strength by 7.44% compared to the reference specimen. According to scientific research, the increase in flexural strength is the result of the high tensile strength of the fibers and also the good adhesion between the fibers and the matrix [40]. We observe that for the percentages 30% and 40% of the fibers, the flexural strength decreases, which may be due to the increased number of fibers in the plaster matrix and, consequently, to the poor adhesion between the matrix and the fibers. Nevertheless, all composite flexural strength values exceed the minimum 1 MPa defined by EN 13279-2 [26], Which means that the added percentages of fibres in the plaster matrix result in mixtures that perform well in accordance with the requirements of the standard. There is a similarity between the results obtained and those of Iucolano et al. [4], who found an improvement in the flexural strength of a biocomposite incorporated with 2% mass of abaca fibers, and a reduction in flexural strength for a fiber percentage of 3%. Similarly, Romero-Gomez et al. [41] compared the effect of incorporating recycled nylon fibers and commercial glass fibers into the plaster matrix, using different percentages by mass (1%, 2%, 2.5%, 3%), and found that the maximum flexural strength of the composites is achieved at a fiber percentage of 2% by mass and decreases at 2.5% and 3% of the fibers due to composite heterogeneity when these percentages are added.
Figure 13: Flexural strength of composites
The evolution of compressive strength with increasing Juncus maritimus fiber content is shown in Fig. 14. We note that increasing the amount of fiber in the composite has a negative effect on compressive strength, varying from 9.2 MPa for the unreinforced sample to 6.18 MPa for the reinforced composite with a fiber content of 40% by volume, with a reduction rate of 32.82%. These results are mainly due to the pores created in the plaster matrix when the fiber content increases and, consequently the creation of interfacial bonding defects between the plaster and the Juncus maritimus fibers, which reduces compressive strength. Similar results of decreasing compressive strength with increasing porosity in different matrices have been obtained in other studies [3,15,42,43]. Furthermore, the plaster incorporated by the fibers, through the adoption of a random mixing method, provides a less homogeneous distribution of matrix components, and the sample subjected to compressive loads results in cracks in the zones adjacent to the fibers, resulting in the failure of these elements at a lower load than that applied to the sample without fibers. Nevertheless, in accordance with the standard [26], the minimum requirement for the compressive strength of plaster is 2 MPa, and all the compressive strengths of plaster composites incorporated by JM fibers have been above this limit, underlining the feasibility of using these composites in the construction field.
Figure 14: Compressive strength of composites
3.4 Microstructures of Composites
Fig. 15 shows the morphology of plaster and composites incorporated by 20% and 40% of JM fibers. A number of authors have already analyzed the morphology of the plaster matrix illustrated in Fig. 15a [3,41,44]; this figure shows that plaster consists of interlocking needle-or plate-shaped crystals. After the three-point bending test, the morphology of the matrix-fiber interface was analyzed to obtain further information on the role of Juncus maritimus fibers within the plaster matrix. The morphology of the composite incorporated by 20% of the JM fibers (Fig. 15b) shows a fiber surface that seems almost covered with plaster crystals, thus confirming the improved matrix-fiber adhesion. The JM fibers are also observed to overflow the plaster matrix after the flexural test, sewing the plaster matrix components together, which explains the improved flexural strength and anti-cracking ability of this percentage (Fig. 13). But when the percentage of JM fibers increases to 40% as shown in Fig. 15c, we notice that the fiber matrix surface appears heterogeneous and the JM fibers added to the plaster matrix are not completely covered by the plaster matrix, there are air pores between the fibers and the plaster paste. This can be explained by the hydrophilic nature of the fibers and their ability to absorb water. This leads to swelling of the fibers during sample manufacture and consequent detachment of the fibers from the plaster matrix after the composites have dried [15]. These observations explain the reduction in mechanical properties, particularly compressive strength (Fig. 14), which depends essentially on the porosity of the composite. The greater the number of pores in the composite, the greater the rate of reduction in compressive strength [40]. The increase in pores as the percentage of fibers in the plaster matrix increases, as observed in these SEM images, also justifies the decrease in apparent density, and the thermal properties of the composites obtained in Sections 3.1 and 3.2.
Figure 15: Secondary electron SEM images of the fracture face, (a) plaster, (b) plaster composite incorporated with 20% JM fibers, (c) plaster composite incorporated with 40% JM fibers
This research focuses on guiding the use of Juncus maritimus fibers in construction materials by studying the impact of these Juncus maritimus fibers as reinforcing materials on the thermomechanical behavior of plaster. The mineralogical composition and microstructure of Juncus maritimus fibers were analyzed, and it was found that these fibers possess interesting properties for application as insulating materials due to their high crystallinity index (42.45%) and porous structure. Different percentages of Juncus maritimus fibers have been used in the fabrication of plaser-based composites to assess the thermal and mechanical impact of adding these fibers to the plaster matrix. Physical and thermal characterization of the composites showed that reinforcing the plaster with Juncus maritimus fibers made the composite lighter, with improved thermal resistance. A 40% fiber content added to the plaster reduced the thermal diffusivity and thermal conductivity of the composites from 0.457 to 0.389 mm2/s and from 0.4853 to 0.4324 W/m.K, respectively, highlighting the potential use of JM fibers as an additive to the plaster matrix to improve thermal comfort and energy efficiency inside buildings to reduce greenhouse gas emissions and energy consumption. Concerning the mechanical behavior of composites, the addition of 20% by volume of Juncus maritimus fibers improved the bending strength of plaster thanks to the high tensile strength of the fibers and the good adhesion between matrix and fibers, as confirmed by the microstructure of the fiber-matrix surface. The results, therefore, demonstrate the effective use of Juncus maritimus fibers to manufacture plaster boards with improved mechanical strength.
Overall, the incorporation of fibers into the plaster matrix is considered an effective technique for improving plaster’s mechanical properties and thermal insulation. Future orientations in the construction sector should focus on optimizing the incorporation of Juncus maritimus fiber, and studying the durability of the reinforcements studied, as well as the acoustic effect of Juncus maritimus fibers on the plaster matrix.
Acknowledgement: This research was carried out at the Thermodynamics and Energy Laboratory (LTE). Authors present special thanks to Renewable Energy Laboratory (LMER), the Ibn Zohr University Research Center, and the Public Testing and Research Laboratory (LPEE) for their help so as to realize this work.
Funding Statement: The authors received no specific funding for this study.
Author Contributions: The authors confirm contribution to the paper as follows: study conception and design: Mina Amazal, Soumia Mounir, Asma Souidi; data collection: Mina Amazal, Asma Souidi, Malika Atigui, Slimane Oubeddou; analysis and interpretation of results: Mina Amazal, Slimane Oubeddou, Asma Souidi, Soumia Mounir, Malika Atigui; draft manuscript preparation: Mina Amazal, Malika Atigui, Soumia Mounir, Youssef Maaloufa, Ahmed Aharoune. All authors reviewed the results and approved the final version of the manuscript.
Availability of Data and Materials: The authors confirm that the data supporting the findings of this study are available within article.
Conflicts of Interest: The authors declare that they have no conflicts of interest to report regarding the present study.
References
1. Martias C, Joliff Y, Favotto C. Effects of the addition of glass fibers, mica and vermiculite on the mechanical properties of a gypsum-based composite at room temperature and during a fire test. Compos Part B Eng. 2014;62:37–53. [Google Scholar]
2. Ouakarrouch M, El Azhary K, Laaroussi N, Garoum M, Kifani-Sahban F. Thermal performances and environmental analysis of a new composite building material based on gypsum plaster and chicken feathers waste. Therm Sci Eng Prog. 2020;19:100642. [Google Scholar]
3. Souidi A, Maaloufa Y, Amazal M, Atigui M, Oubeddou S, Mounir S, et al. The effect of mussel shell powder on the thermal and mechanical properties of plaster. Constr Build Mater. 2024;416:135142. [Google Scholar]
4. Iucolano F, Caputo D, Leboffe F, Liguori B. Mechanical behavior of plaster reinforced with abaca fibers. Constr Build Mater. 2015;99:184–91. [Google Scholar]
5. Iucolano F, Boccarusso L, Langella A. Hemp as eco-friendly substitute of glass fibres for gypsum reinforcement: impact and flexural behaviour. Compos Part B Eng. 2019;175:107073. [Google Scholar]
6. Boccarusso L, Durante M, Iucolano F, Mocerino D, Langella A. Production of hemp-gypsum composites with enhanced flexural and impact resistance. Constr Build Mater. 2020;260:120476. [Google Scholar]
7. Ahmad F, Choi HS, Park MK. A review: natural fiber composites selection in view of mechanical, light weight, and economic properties. Macromol Mater Eng. 2015;300(1):10–24. [Google Scholar]
8. Millogo Y, Morel JC, Aubert JE, Ghavami K. Experimental analysis of pressed adobe blocks reinforced with Hibiscus cannabinus fibers. Constr Build Mater. 2014;52:71–8. [Google Scholar]
9. Mehrez I, Hachem H, Jemni A. Thermal insulation potential of wood-cereal straws/plaster composite. Case Stud Constr Mater. 2022;17:e01353. [Google Scholar]
10. Charai M, Sghiouri H, Mezrhab A, Karkri M. Thermal insulation potential of non-industrial hemp (Moroccan cannabis sativa L.) fibers for green plaster-based building materials. J Clean Prod. 2021;292:126064. [Google Scholar]
11. Cherradi Y, Rosca IC, Cerbu C, Kebir H, Guendouz A, Benyoucef M. Acoustic properties for composite materials based on alfa and wood fibers. Appl Acoust. 2021;174(9):107759. doi:10.1016/j.apacoust.2020.107759. [Google Scholar] [CrossRef]
12. Kassab Z, Syafri E, Tamraoui Y, Hannache H, Qaiss AEK, El Achaby M. Characteristics of sulfated and carboxylated cellulose nanocrystals extracted from Juncus plant stems. Int J Biol Macromol. 2020;154:1419–25. doi:10.1016/j.ijbiomac.2019.11.023. [Google Scholar] [PubMed] [CrossRef]
13. Saghrouni Z, Baillis D, Naouar N, Blal N, Jemni A. Thermal properties of new insulating juncus maritimus fibrous mortar composites/experimental results and analytical laws. Appl Sci. 2019;9(5):981. doi:10.3390/app9050981. [Google Scholar] [CrossRef]
14. Saghrouni Z, Baillis D, Jemni A. Composites based on Juncus maritimus fibers for building insulation. Cem Concr Compos. 2017;8(7):1026–40. doi:10.1016/j.cemconcomp.2019.103474. [Google Scholar] [CrossRef]
15. Maaloufa Y, Mounir S, Khabbazi A, Kettar J. Thermal and mechanical behavior of the plaster reinforced by fiber alpha or granular cork. Int J Civ Eng. 2020;238(10):117712. doi:10.1016/j.conbuildmat.2019.117712. [Google Scholar] [CrossRef]
16. Bouzit S, Laasri S, Taha M, Laghzizil A, Hajjaji A, Merli F, et al. Characterization of natural gypsum materials and their composites for building applications. Appl Sci. 2019;9(12):2443. [Google Scholar]
17. Nakch A. Wholesale construction plaster (PGC) (In French). Available from: https://www.centralegypse.com/wp-content/uploads/2020/02/Nakch-Asri-Fiche-technique-Fr.pdf. [Accessed 2020]. [Google Scholar]
18. AFNOR. NF EN 1097-6: tests to determine the mechanical and physical characteristics of aggregates. Part 6: determination of actual density and water absorption coefficient; 2014 (In French). Available from: https://www.boutique.afnor.org/en-gb/standard/nf-en-10976/tests-for-mechanical-and-physical-properties-of-aggregates-part-6-determina/fa163899/42536 [Accessed 2014]. [Google Scholar]
19. Hot Disk AB. Hot disk thermal constants analyser instruction manual; 2015. Available from: https://www.thermoconcept-sarl.com/wp-content/uploads/2017/03/Hot-Disk-TPS-1500.pdf [Accessed 2024]. [Google Scholar]
20. Millogo Y, Aubert JE, Séré AD, Fabbri A, Morel JC. Earth blocks stabilized by cow-dung. Mater Struct. 2016;49(11):4583–94. [Google Scholar]
21. Segal L, Creely JJ, Martin AE, Conrad CM. An empirical method for estimating the degree of crystallinity of native cellulose using the X-ray diffractometer. Text Res J. 1959;29(10):786–94. [Google Scholar]
22. Indran S, Raj RE. Characterization of new natural cellulosic fiber from Cissus quadrangularis stem. Carbohydr Polym. 2015;117:392–9. [Google Scholar] [PubMed]
23. Abdal-hay A, Suardana NPG, Jung DY, Choi KS, Lim JK. Effect of diameters and alkali treatment on the tensile properties of date palm fiber reinforced epoxy composites. Int J Precis Eng Manuf. 2012;13(7):1199–206. [Google Scholar]
24. Vandeurzen P, Ivens J, Verpoest I. A three-dimensional micromechanical analysis of woven-fabric composites: I. Geometric analysis. Compos Sci Technol. 1996;56(11):1303–15. [Google Scholar]
25. Kabir H, Aghdam MM. A robust Bézier based solution for nonlinear vibration and post-buckling of random checkerboard graphene nano-platelets reinforced composite beams. Compos Struct. 2019;212:184–98. [Google Scholar]
26. AFNOR. EN 13279-2: gypsum binders and gypsum plasters–part 2: test methods; 2014 (In French). Available from: https://www.boutique.afnor.org/fr-fr/norme/nf-en-132792/liantsplatres-et-enduits-a-base-de-platre-pour-le-batiment-partie-2-methode/fa180332/42823 [Accessed 2024]. [Google Scholar]
27. Boulekbache B, Hamrat M, Chemrouk M, Amziane S. Flowability of fibre-reinforced concrete and its effect on the mechanical properties of the material. Constr Build Mater. 2010;24(9):1664–71. [Google Scholar]
28. Jiao D, Shi C, Yuan Q, An X, Liu Y, Li H. Effect of constituents on rheological properties of fresh concrete-A review. Cem Concr Compos. 2017;83:146–59. [Google Scholar]
29. Gutiérrez-González S, Alonso MM, Gadea J, Rodríguez A, Calderón V. Rheological behaviour of gypsum plaster pastes with polyamide powder wastes. Constr Build Mater. 2013;38(509):407–12. doi:10.1016/j.conbuildmat.2012.08.034. [Google Scholar] [CrossRef]
30. Almahdawi FHM, Zarzor Al-Yaseri A, Jasim N. Apparent viscosity direct from marsh funnel test. Iraqi J Chem Pet Eng. 2014;15(1):51–7. doi:10.31699/IJCPE.2014.1.6. [Google Scholar] [CrossRef]
31. AFNOR. EN P18-358: admixtures for concrete, mortar and grout-Common injection grouts for prestressing-Measuring fluidity and water reduction; 1985 (In French). Available from: https://www.boutique.afnor.org/fr-fr/norme/p18358/adjuvants-pour-betons-mortiers-et-coulis-coulis-courants-dinjection-pour-pr/fa033637/11583 [Accessed 2024]. [Google Scholar]
32. Tiskatine R, Bougdour N, Oaddi R, Gourdo L, Rahib Y, Bouzit S, et al. Thermo-physical analysis of low-cost ecological composites for building construction. J Build Eng. 2018;20(2):762–75. doi:10.1016/j.jobe.2018.09.015. [Google Scholar] [CrossRef]
33. Mihiretie B, Cederkrantz D, Rosén A, Otterberg H, Sundin M, Gustafsson S, et al. Finite element modeling of the Hot Disc method. Int J Heat Mass Transf. 2017;115:216–23. doi:10.1016/j.ijheatmasstransfer.2017.08.036. [Google Scholar] [CrossRef]
34. AFNOR. NF EN 196-1: methods bof testing cement. Determination of strength; 2016 (In French). Available from: https://www.boutique.afnor.org/fr-fr/norme/nf-en-1961/methodes-dessais-des-ciments-partie-1-determination-des-resistances/fa184622/57803 [Accessed 2024]. [Google Scholar]
35. Liuzzi S, Rubino C, Stefanizzi P, Petrella A, Boghetich A, Casavola C, et al. Hygrothermal properties of clayey plasters with olive fibers. Constr Build Mater. 2018;158:24–32. doi:10.1016/j.conbuildmat.2017.10.013. [Google Scholar] [CrossRef]
36. Fernea R, Manea DL, Tămaş-Gavrea DR, Roşca IC. Hemp-clay building materials-An investigation on acoustic, thermal and mechanical properties. Procedia Manuf. 2019;32:216–23. [Google Scholar]
37. Charai M, Mghazli MO, Channouf S, El Hammouti A, Jagadesh P, Moga L, et al. Lightweight waste-based gypsum composites for building temperature and moisture control using coal fly ash and plant fibers. Constr Build Mater. 2023;393:132092. [Google Scholar]
38. Laibi B. Hygro-thermo-mechanical behavior of structural materials for the construction associating kenaff fibers with clayed lands (Ph.D. Thesis). Normandie Université: France; 2017 (In French). [Google Scholar]
39. Pacheco-Torgal F, Jalali S. Cementitious building materials reinforced with vegetable fibres: a review. Constr Build Mater. 2011;25(2):575–81. [Google Scholar]
40. Babé C, Kidmo DK, Tom A, Mvondo RRN, Kola B, Djongyang N. Effect of neem (Azadirachta Indica) fibers on mechanical, thermal and durability properties of adobe bricks. Energy Rep. 2021;7:686–98. [Google Scholar]
41. Romero-Gómez MI, Silva RV, Flores-Colen I, Rubio-de-Hita P. Mechanical performance of waste fishing net fibre-reinforced gypsum composites. Constr Build Mater. 2023;387:131675. [Google Scholar]
42. Khoudja D, Taallah B, Izemmouren O, Aggoun S, Herihiri O, Guettala A. Mechanical and thermophysical properties of raw earth bricks incorporating date palm waste. Constr Build Mater. 2021;270(6):121824. doi:10.1016/j.conbuildmat.2020.121824. [Google Scholar] [CrossRef]
43. Ouedraogo M, Dao K, Millogo Y, Aubert JE, Messan A, Seynou M, et al. Physical, thermal and mechanical properties of adobes stabilized with fonio (Digitaria exilis) straw. J Build Eng. 2019;23(12):250–8. doi:10.1016/j.jobe.2019.02.005. [Google Scholar] [CrossRef]
44. Atigui M, Maaloufa Y, Souidi A, Amazal M, Oubeddou S, Demrati H, et al. Enhanced thermo-physical properties of gypsum composites using olive pomace waste reinforcement. Rev Compos Matér Avancés. 2024;34(1):67–75. doi:10.18280/rcma.340109. [Google Scholar] [CrossRef]
Cite This Article
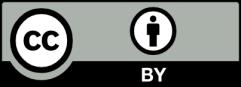
This work is licensed under a Creative Commons Attribution 4.0 International License , which permits unrestricted use, distribution, and reproduction in any medium, provided the original work is properly cited.