Open Access
ARTICLE
Effect of Lightweight Aggregates Incorporation on the Mechanical Properties and Shrinkage Compensation of a Cement-Ground Granulated Blast Furnace Slag-Phosphogypsum Ternary System
1 State Key Laboratory of Bridge Intelligent and Green Construction, China Railway Major Bridge Engineering Group Co., Ltd., Wuhan, 430034, China
2 China Railway Bridge Science Research Institute., Ltd., Wuhan, 430034, China
* Corresponding Author: Mengyang Ma. Email:
(This article belongs to the Special Issue: Advances in Solid Waste Processing and Recycling Technologies for Civil Engineering Materials)
Fluid Dynamics & Materials Processing 2024, 20(8), 1773-1784. https://doi.org/10.32604/fdmp.2024.048695
Received 15 December 2023; Accepted 22 February 2024; Issue published 06 August 2024
Abstract
Shrinkage-induced cracking is a common issue in concrete structures, where the formation of cracks not only affects the aesthetic appearance of concrete but also potentially reduces its durability and strength. In this study, the effect of ceramsite sand addition on the properties of a ternary system of cement-ground granulated blast furnace slag (GGBFS)-phosphogypsum (PG) is investigated. In particular, the fluidity, rheology, hydration heat, compressive strength, autogenous shrinkage, and drying shrinkage of the considered mortar specimens are analyzed. The results indicate that an increase in PG content leads to a decrease in fluidity, higher viscosity, lower exothermic peak, and lower compressive strength. However, the shrinkage of the mortar specimens is effectively compensated. The incorporation of internal curing water from ceramsite sand improves fluidity, decreases both yield stress and viscosity, enhances the degree of hydration, and induces mortar expansion. However, the inferior mechanical properties of the ceramsite sand generally produce a decrease in the compressive strength.Keywords
The durability of concrete structures is seriously affected by the presence of cracking, a common issue in modern construction engineering. This issue is often a consequence of shrinkage which causes shallow cracks in concrete at an early stage [1–4], not only facilitating the invasion of harmful ions but also accelerating the deterioration of concrete [5–8]. Therefore, it is particularly important to maintain the volume stability of concrete.
Materials such as expansive agents or hydration heat inhibitors are usually used to offset shrinkage or reduce heat release of concrete to improve the volume stability of concrete. Although these methods can be effective to a certain extent, there are still shortcomings. To solve the problem of cracks caused by serious shrinkage of high-strength concrete, Xi et al. [9] studied the effect of expansive agents on the performance of concrete. The results showed that the compressive strength can be improved by expansive agents, but cracks occurred due to excessive and delayed expansion in the later stage. Liang et al. [10] found that hydration heat inhibitors led to a decline in the early hydration degree of concrete, which significantly reduced the early compressive strength of concrete, and with the increase of hydration heat inhibitors content, the strength of concrete decreased. Zhang [11] and Li et al. [12] respectively discussed the preparation of MgO expansive agents and butyl acrylate copolymer emulsion and found that the preparation of expansive agents and hydration heat inhibitors was complicated and easy to cause environmental pollution.
PG is a solid waste discharged in wet-process of phosphoric acid production, which contains 90% calcium sulfate, and a small amount of impurities such as phosphoric acid residuals, fluorides and heavy metals. The common disposal method of PG is stacked in landfill fields, where PG is harmful to the surrounding environment and human health once the impurities and heavy metals are leaked into the soil. It is estimated that the annual production of PG will reach 250 million tons within the next decade, but only 15% of PG can be utilized [13]. Hence, many researchers are exploring effective utilization ways for PG to serve as an alternative cementitious material in concrete. PG was tried to prepare high-content PG concrete, and although its mechanical properties were reduced, the permeability resistance of concrete was qualified [14–17]. This approach not only reduces the reserves of PG, but also reduces the production and consumption of cement, promoting environmental sustainability and conserving natural resources. Dong et al. [16] found that PG could improve the working performance and hydration process of concrete, and the sulfate in PG would generate the expansion product (ettringite) in concrete. Djayaprabha et al. [18] found that when PG content reached an optimal amount, both the compressive strength and bending strength of mortar were increased, which was also attributed to the formation of ettringite. Costa et al. [19] and Zeng et al. [20] indicated that the addition of PG would significantly reduce water content on the matrix and directly affect the hydration degree. The reason is that the water consumption of ettringite formation is larger [21], resulting in incomplete hydration of cement, increased residual PG, and reduced amount of hydration products that provide strength so that the mechanical properties of concrete decreased and the volume stability became worse.
Lightweight aggregates with water absorption ability can be incorporated into concrete to play the role of reservoir. When the water in the hydration process is insufficient, lightweight aggregates could release water to form an internal curing environment to increase the internal relative humidity of concrete, so that the hydration of cementitious materials could continue and autogenous shrinkage could be compensated. Afifi et al. [22] found that the introduction of internal curing water by perlites could enhance the hydration degree, and reduce the shrinkage and the possibility of cracking. Similarly, Hammam et al. [23] found that the internal humidity of concrete could be improved by pre-wetted perlites and recycled aggregates, and the working performance, durability, and cracking resistance of concrete were all promoted. Zhao et al. [24] indicated that the expansion effect of CaO expansive agent could be improved by the addition of pre-wetted ceramsite sand to reduce the autogenous shrinkage of concrete.
In this study, a cement-GGBFS-PG ternary system was studied, with ceramsite sand partially replacing the sand as an internal curing material. The utilization of internal curing materials could maintain internal relative humidity, providing the necessary water for the reaction of PG, thereby further compensating for shrinkage, and enhancing volume stability.
2 Materials and Experiment Methods
The cement used in this study is P. II 52.5 cement with a density of 3.16 g/cm³, a specific surface area of 340 m²/kg, a 28-day bending strength of 10.1 MPa, and a 28-day compressive strength of 59.8 MPa. The PG used in this study primarily consists of dihydrate gypsum (CaSO4·2H2O) with D50 = 31.58 μm. The S95 grade GGBFS is used in this study with a density of 2910 kg/m³, a specific surface area of 411 m²/kg, and a fluidity ratio of 101%, the 7-day and 28-day activity index are 77% and 98%, respectively. The chemical compositions of cement, GGBFS, and PG are shown in Table 1. Ceramsite sand has a 24-h water absorption rate of 27%, with an apparent density of 1123 kg/m³, the microtopography of ceramsite sand is shown in Fig. 1. The sand used is medium sand with a fineness modulus of 2.8 and an apparent density of 2530 kg/m³. The solid content of the polycarboxylate water-reducing agent is 45%. The mixing water is tapping water.
Figure 1: The microtopography of ceramsite sand
2.2.1 Preparation of Mortar Specimens
The mixture proportions of specimens are shown in Table 2. The 24-h water absorption rate of ceramsite sand was tested, and the corresponding extra water was added into the mixing water to pre-wet the ceramsite sand 24 h in advance. The raw materials were weighed according to Table 2, and the replacement of sand by ceramsite sand was calculated by volume according to the apparent densities. The 40 mm × 40 mm × 40 mm steel molds were used to cast mortar. The dosage of the water-reducing agent was adjusted to maintain the fluidity of the mortar at 190 ± 5 mm. The specimens were cured in standard curing conditions (RH ≥ 95%, 20°C).
The fluidity test of the specimens was conducted in accordance with GB/T 2419-2005 by a flow table.
The rheological test of mortar is conducted by a MARS40 rheometer (Fig. 2). The shear process is shown in Fig. 3. The shear rate and shear stress in the process from 210 to 270 s are used as the data to analyze the rheological properties of mortar. The Bingham model (
Figure 2: Rheometer
Figure 3: Shear process
The hydration heat is measured by a TAM AIR isothermal calorimeter with 8 channels at 20°C. 30 g mortar is put into each channel, and the instrument starts after 15 min. The test duration is 72 h.
The compressive strength test of the mortar is conducted by a microcomputer servo flexural-compressive tester in accordance with GB/T 17671-2021. The compressive strength test is tested at 3, 7, 28, and 60 d, the average value of three specimens is taken as the final compressive strength.
Autogenous shrinkage is recorded by a digital display comparator according to JC/T 603-2004. The mortar specimens are cast in 25 mm × 25 mm × 280 mm molds and demolded after 24 h curing. The mortar specimens are wrapped in plastic films to isolate the exchange of moisture with air. The test is conducted in the curing room (RH = 60 ± 5%, 20 ± 2°C). The test duration is 7 d, and the average autogenous shrinkage of three specimens is taken as the final autogenous shrinkage.
Drying shrinkage is recorded by a digital display comparator according to JC/T 603-2004. The mortar specimens are cast in 25 mm × 25 mm × 280 mm molds and demolded after 24 h curing. The test is conducted in a curing room (RH = 60 ± 5%, 20 ± 2°C). The drying shrinkage is recorded at 1, 3, 7, 14 and 28 d, and the average drying shrinkage of three specimens is taken as the final drying shrinkage.
3.1 Fluidity of Fresh Mortar Mixture
The fluidity and water-reducing agent dosage are shown in Fig. 4. To avoid the results of subsequent tests being affected by the fluidity of mortar specimens, the fluidity of mortar specimens is maintained at 190 ± 5 mm during the preparation. The influence of PG and ceramsite sand on the fluidity of mortar specimens is represented through the dosage of water-reducing agent. The result shows that the dosage of water-reducing agent gradually increases with the increased content of PG. However, the influence of ceramsite sand shows a contrary effect. The reason is that the monoclinic structure of PG hinders the fluidity of mortars [25], but the part of internal water released from ceramsite sand increases the free water of mortar specimens, resulting in a decrease of water-reducing agent [26].
Figure 4: The fluidity and water-reducing agent dosage of mortar specimens
3.2 Rheology of Fresh Mortar Mixture
The rheological curves of mortar specimens are shown in Fig. 5. The yield stress (τ0) and viscosity (μ) are calculated according to the Bingham model. It can be observed that the yield stress and viscosity of 0.4S20 are 59.48 Pa and 3.22 Pa·s, respectively. With the incorporation of PG, the yield stress and viscosity of 0.4S12 is 56.77 Pa and 4.44 Pa·s. The yield stress of 0.4S12 shows little difference with 0.4S20 but the viscosity is increased significantly, which indicates higher energy is needed to keep its moving status due to the monoclinic structure of PG. However, the addition of internal curing water makes 0.4S12L20 show significantly lower yield stress and viscosity, which are 37.84 Pa and 2.95 Pa·s, respectively. The pre-wet ceramsite sand releases water during the mixing process, the increase of free water significantly reduces the solid phase volume fraction of mortar, which is the main reason for the decrease of yield stress and plastic viscosity of mortar.
Figure 5: The rheological curves of mortar specimens
The hydration heat of mortar specimens is shown in Fig. 6, the exothermic process can be divided into 5 periods: Early induction period, induction period, acceleration period, deceleration period and stable period. It can be found there are two main exothermic peaks: the first exothermic peak is mainly caused by the heat release of the surface wetting of cement particles and the heat release of C3A [27], and the second exothermic peak is the heat release peak of C3S. Comparing the hydration heat curves of three specimens, it can be found that the total heat release is increased with the PG content before 4 h, which indicates a higher first exothermic peak. This is because the increase of PG increases the content of SO42− in the liquid phase and promotes the formation of ettringite [25]. The addition of PG greatly delays the second exothermic peak by about 14 h. The soluble phosphorus in PG can form calcium phosphate precipitation on the surface of C3S to reduce the activation points, and seriously hinder further hydration [28,29]. Although SO42− can promote the hydration of C3S [30,31], this positive effect is weaker than the negative effect of soluble phosphorus. Therefore, the second exothermic peaks of 0.4S12 and 0.4S12L20 are delayed than that of 0.4S20, and the peak intensity is also weaker. With the incorporation of ceramsite sand, it can be found that the exothermic peak occurred in advance slightly and the total heat release of 0.4S12L20 is higher than that of 0.4S20 and 0.4S12, indicating the hydration is accelerated by internal curing [27]. It is worth noting that although the total heat release of 0.4S12 and 0.4S12L20 show higher compared to 0.4S20, the intensity of the exothermic peaks is much lower, which is beneficial for preventing temperature-induced cracking [32].
Figure 6: The hydration heat of mortar specimens
The compressive strength of mortar specimens is shown in Fig. 7. It can be found that with the increased content of PG and ceramsite sand, the compressive strength of mortar specimens shows a decreased trend. Since harmful impurities, the free phosphorus and fluoride ions can react with calcium ions to produce calcium phosphate, hydroxyapatite, and calcium fluoride to hinder the hydration, so that the compressive strength is affected negatively at an early stage [19,28,29]. Moreover, the replacement of GGBFS (which has been proven to be highly beneficial to later strength [33,34]) by PG, also leads to a decline in strength in the later stage. It is worth noting that the compressive strength of 0.4S12 at 60 d is lower than that at 28 d, which indicates an overmuch PG content is harmful to the mechanical properties of mortar at later stage. This is because the addition of PG promotes the formation of ettringite which gradually fills the pores of mortar and exerts certain compressive stress on the surrounding area. When the PG content is high, the unreacted PG could generate ettringite to make the compressive stress on the surrounding area over high, leading to the expansion of the matrix and the formation of micro-cracks at a later stage [15,35,36]. With the incorporation of internal curing water, the compressive strength of 0.4S12L10 shows higher than that of 0.4S12 which suggests a positive internal curing effect can endow mortar with a higher hydration degree and compensate for the strength loss brought by PG [37,38]. However, due to the porous structure of ceramsite sand, the increasing content of ceramsite sand decreases the compressive strength of mortar [39,40].
Figure 7: The compressive strength of mortar specimens
The autogenous shrinkage curves of mortars are shown in Fig. 8. It can be found that the incorporation of PG and ceramsite sand can reduce the autogenous shrinkage of mortar specimens. Compared with 0.4S20, the autogenous shrinkage of 0.4S16 and 0.4S12 are reduced by 13.6% and 24.1%, respectively, suggesting a higher ability of shrinkage resistance. The reason is that the incorporation of PG produces ettringite in the mortar specimens to compensate for shrinkage [41,42]. In addition, the incorporation of internal curing water makes autogenous shrinkage of mortar specimens fall further, and 0.4S12L15 and 0.4S12L20 show expansion at 2 d. It is well known that the larger water-to-cement ratio presents lower autogenous shrinkage [43]. Compared with 0.4S12, it can be found that the total water-to-cement ratio of 0.4S12L10, 0.4S12L15, and 0.4S12L20 is higher. The internal curing effect can provide extra water to increase the water-to-cement ratio which has been proven to reduce the self-desiccation effect so that the autogenous shrinkage can be reduced [44]. Moreover, the addition of water to the mortar specimens also promotes the production of ettringite [20].
Figure 8: The autogenous shrinkage of mortar specimens
The drying shrinkage curves of mortar specimens are shown in Fig. 9. Similar to the result of autogenous shrinkage, the incorporation of PG and ceramsite sand can reduce the drying shrinkage of mortar. However, although the drying shrinkage is decreased with the addition of PG and ceramsite sand, only 0.4S20 shows a significant difference compared with other specimens. The internal curing water seems to play a negative role in the shrinkage process by providing more water to be lost to aggravate drying shrinkage in an exposed environment [44].
Figure 9: The drying shrinkage of mortar specimens
With the study of this research, the conclusions are drawn as follows:
(1) The fluidity of specimens is represented by the dosage of water-reducing agent. The incorporation of PG increases the dosage of water-reducing agent, but the incorporation of internal curing water shows the contrary.
(2) The addition of PG makes specimens show higher viscosity, the yield stress and viscosity are decreased due to the release of internal curing water during the mixing process.
(3) The occurred time of exothermic peak is delayed significantly by the addition of PG, and the intensity of exothermic peaks of 0.4S12 and 0.4S12L20 is much lower compared to 0.4S20, which is beneficial to prevent temperature-induced cracking of concrete.
(4) The addition of internal curing water can promote compressive strength and compensate for the harmful effect brought by PG at a later stage, but the content of ceramsite sand needs to be limited due to its weak porous structure.
(5) The synergistic effect of PG and internal curing can endow specimens with autogenous expansive deformation, but the internal curing effect seems to be a negative factor in restraining the decrease of drying shrinkage due to more water being lost in the air.
(6) A small amount of PG combined with internal curing can significantly improve the shrinkage properties of cementitious materials. For future research, several lines of study are suggested: the influence of different qualities of PG on concrete performance; the development of the long-term performance of concrete doped with PG; the formation, transformation, and decomposition of hydration products in large-volume concrete doped with PG; and the application of PG and internal curing in high-strength structural concrete.
Acknowledgement: Thanks for the help from the leaders and colleagues of the National Key Laboratory of Bridge Intelligent and Green Construction.
Funding Statement: This study is funded by the China Railway Major Bridge Engineering Group Co., Ltd., Project (2023-48-Key Project).
Author Contributions: Yu Wang: Experiment, writing original drawing. Mengyang Ma: Analysis, writing final manuscript, review, and editing. Yu Long: Investigation. Qingxiang Zhao: Experiment. Zhifei Cheng: Experiment.
Availability of Data and Materials: The datasets used or analyzed during the current study are available from the corresponding author upon reasonable request.
Conflicts of Interest: The authors declare that they have no conflicts of interest to report regarding the present study.
References
1. Hassan AL, Billah AM. Superabsorbent cellulose fibers for reducing shrinkage and microcracking in concrete. Can J Civ Eng. 2022;49(8):1379–91. [Google Scholar]
2. Meyer DM, Combrinck R. Utilising microCT scanning technology as a method for testing and analysing plastic shrinkage cracks in concrete. Constr Build Mater. 2022;317:125895. [Google Scholar]
3. Afroz S, Nguyen QD, Zhang Y, Kim T, Castel A. Cracking of limestone calcined clay blended concrete and mortar under restrained shrinkage. Constr Build Mater. 2023;386:131599. [Google Scholar]
4. Deysel RC, Boshoff WP, Smit MS. Implementing capillary pressure control measures to prevent plastic shrinkage cracking in concrete. Constr Build Mater. 2023;397:132407. [Google Scholar]
5. Srinivasan SS, Ferron RD. Effect of crack width, density, and depth on strength and durability of concrete-equivalent mortar. Aci Mater J. 2021;118(4):65–78. [Google Scholar]
6. Meyer DM, Boshoff WP, Combrinck R. Utilising super absorbent polymers as alternative method to test plastic shrinkage cracks in concrete. Constr Build Mater. 2020;248:118666. [Google Scholar]
7. Arya EK, James JS, John E. Study on the effectiveness of shrinkage reducing admixtures on plastic shrinkage of concrete. In: Proceedings of SECON’19: Structural Engineering and Construction Management 3. Angamaly, Kerala, India: Springer International Publishing; 2020; p. 147–54. [Google Scholar]
8. Sayahi F, Emborg M, Hedlund H, Cwirzen A. Effect of admixtures on mechanism of plastic shrinkage cracking in self-consolidating concrete. Aci Mater J. 2020;117(5):51–9. [Google Scholar]
9. Xi YF, Lee J, Chen BL, Yang B, Yu MZ, Yan XZ, et al. Impact of high-performance expansion and shrinkage-reducing agents on the mechanical properties and shrinkage compensation of high-strength concrete. Buildings. 2023;13(3):717. [Google Scholar]
10. Liang T, Luo P, Mao Z, Huang X, Deng M, Tang M. Effect of hydration temperature rise inhibitor on the temperature rise of concrete and its mechanism. Mater. 2023;16(8):2992. [Google Scholar]
11. Zhang J. Recent advance of MgO expansive agent in cement and concrete. J Build Eng. 2022;45:103633. [Google Scholar]
12. Li S, Mao Z, Deng M. Preparation of butyl acrylate copolymer emulsion and its regulation effect on cement hydration. Mater. 2023;16(7):2887. [Google Scholar]
13. Zhang L, Kim HM, Soon PY, Gencel O, Ling T. Mechanical strength, water resistance and drying shrinkage of lightweight hemihydrate phosphogypsum-cement composite with ground granulated blast furnace slag and recycled waste glass. Constr Build Mater. 2022;345:128232. [Google Scholar]
14. Sun T, Li W, Xu F, Yu Z, Wang Z, Ouyang G, et al. A new eco-friendly concrete made of high content phosphogypsum based aggregates and binder: mechanical properties and environmental benefits. J Clean Prod. 2023;400:136555. [Google Scholar]
15. Ma F, Chen L, Lin Z, Liu Z, Zhang W, Guo R. Microstructure and key properties of phosphogypsum-red mud-slag composite cementitious materials. Mater. 2022;15(17):6096. [Google Scholar]
16. Dong E, Fu S, Wu C, Lv W, Zhang L, Feng Y, et al. Value-added utilization of phosphogypsum industrial by-products in producing green ultra-high performance concrete: detailed reaction kinetics and microstructure evolution mechanism. Constr Build Mater. 2023;389:131726. [Google Scholar]
17. Calderón-Morales BR, García-Martínez A, Pineda P, García-Tenório R. Valorization of phosphogypsum in cement-based materials: limits and potential in eco-efficient construction. J Build Eng. 2021;44:102506. [Google Scholar]
18. Djayaprabha HS, Nguyen HA. Utilizing phosphogypsum waste to improve the mechanical and durability performances of cement-free structural mortar containing ground granulated blast furnace slag and calcium oxide. J Build Eng. 2023;72:106557. [Google Scholar]
19. Costa RP, de Medeiros MHG, Martinez EDR, Quarcioni VA, Suzuki S, Kirchheim AP. Effect of soluble phosphate, fluoride, and pH in Brazilian phosphogypsum used as setting retarder on Portland cement hydration. Case Stud Constr Mat. 2022;17:e01413. [Google Scholar]
20. Zeng LL, Bian X, Zhao L, Wang YJ, Hong ZS. Effect of phosphogypsum on physiochemical and mechanical behaviour of cement stabilized dredged soil from Fuzhou, China. Geomech Energy Envir. 2021;25:100195. [Google Scholar]
21. Du YJ, Jiang NJ, Liu SY, Xi F, Singh DN, Puppala AJ. Engineering properties and microstructural characteristics of cement-stabilized zinc-contaminated kaolin. Can Geotech J. 2014;51(3):289–302. [Google Scholar]
22. Afifi M, Nagib Abou-Zeid M, Ahmed R. Internal curing of structural concrete: a closer look. J Mater Civil Eng. 2022;34(2):04021416. [Google Scholar]
23. Hammam A, Ismail M, Roushdy M, El Ghonemy M, Abdel Raouf M, El Maghraby Y, et al. Incorporation of perlite and recycled aggregates for internal concrete curing. In: International Conference on Transportation and Development 2021, 2021. [Google Scholar]
24. Zhao H, Liu H, Wan Y, Ghantous RM, Li J, Liu Y, et al. Mechanical properties and autogenous deformation behavior of early-age concrete containing pre-wetted ceramsite and CaO-based expansive agent. Constr Build Mater. 2021;267:120992. [Google Scholar]
25. Li Z, Zhang J, Li S, Gao Y, Liu C, Qi Y. Effect of different gypsums on the workability and mechanical properties of red mud-slag based grouting materials. J Clean Prod. 2020;245:118759. [Google Scholar]
26. Zou D, Que Z, Su D, Liu T, Zhou A, Li Y. Sustainable use of recycled autoclaved aerated concrete waste as internal curing materials in ultra-high performance concrete. J Clean Prod. 2022;245:133910. [Google Scholar]
27. Taylor HF. Cement chemistry. London: Thomas Telford; 1997. [Google Scholar]
28. Cao W, Yi W, Peng J, Yin S. Upcycling of phosphogypsum as anhydrite plaster: the positive effect of soluble phosphorus impurities. Constr Build Mater. 2023;372:130824. [Google Scholar]
29. Gijbels K, Nguyen H, Kinnunen P, Schroeyers W, Pontikes Y, Schreur S, et al. Feasibility of incorporating phosphogypsum in ettringite-based binder from ladle slag. J Clean Prod. 2019;237:117793. [Google Scholar]
30. Huang L, Yang Z. Early hydration of tricalcium silicate with potassium hydroxide and sulfate from pore solution and solid view. Constr Build Mater. 2020;230:116988. [Google Scholar]
31. Yaseen SA, Yiseen GA, Poon CS, Li Z. Influence of seawater on the morphological evolution and the microchemistry of hydration products of tricalcium silicates (C3S). Acs Sustain Chem Eng. 2020;8(42):15875–887. [Google Scholar]
32. Do TA, Hoang TT, Bui-Tien T, Hoang HV, Do TD, Nguyen PA. Evaluation of heat of hydration, temperature evolution and thermal cracking risk in high-strength concrete at early ages. Case Stud Therm Eng. 2020;21:100658. [Google Scholar]
33. Patil A, Dwivedi AK. Mechanical strength and durability performance of sea water concrete incorporating supplementary cementitious materials in different curing conditions. Mater Today: Proc. 2022;65:969–74. [Google Scholar]
34. Lee SH, Cho SJ, Kwon SJ. Evaluation of durability performance in concrete incorporating low fineness of GGBFS (3000 Grade). JKSMI. 2019;23(4):96–102. [Google Scholar]
35. Yang X, Jia Y, Yang C, He X, Jia Y, Xu L. Research on formulation optimization and hydration mechanism of phosphogypsum-based filling cementitious materials. Front Env Sci. 2022;10:1012057. [Google Scholar]
36. Liu X, Liu E. The synergistic mechanism and stability evaluation of phosphogypsum and recycled fine powder-based multi-source solid waste geopolymer. Polymers. 2023;15(12):2696. [Google Scholar] [PubMed]
37. Kazemian M, Shafei B. Internal curing capabilities of natural zeolite to improve the hydration of ultra-high performance concrete. Constr Build Mater. 2022;340:127452. [Google Scholar]
38. Shen P, Lu JX, Lu L, He Y, Wang F, Hu S. An alternative method for performance improvement of ultra-high performance concrete by internal curing: role of physicochemical properties of saturated lightweight fine aggregate. Constr Build Mater. 2021;312:125373. [Google Scholar]
39. Li M, Zhou D, Jiang Y. Preparation and thermal storage performance of phase change ceramsite sand and thermal storage light-weight concrete. Renew Energ. 2021;175:143–52. [Google Scholar]
40. Fan LF, Wang H, Zhong WL. Development of lightweight aggregate geopolymer concrete with shale ceramsite. Ceram Int. 2023;49(10):15422–33. [Google Scholar]
41. Harrou A, Gharibi EK, Taha Y, Fagel N, El Ouahabi M. Phosphogypsum and black steel slag as additives for ecological bentonite-based materials: microstructure and characterization. Minerals. 2020;10(12):1067. [Google Scholar]
42. Hanjitsuwan S, Injorhor B, Phoo-ngernkham T, Damrongwiriyanupap N, Li LY, Sukontasukkul P, et al. Drying shrinkage, strength and microstructure of alkali-activated high-calcium fly ash using FGD-gypsum and dolomite as expansive additive. Cement Concrete Comp. 2020;114:103760. [Google Scholar]
43. Yang J, Wang F, He X, Su Y, Wang T, Ma M. Potential usage of porous autoclaved aerated concrete waste as eco-friendly internal curing agent for shrinkage compensation. J Clean Prod. 2021;320:128894. [Google Scholar]
44. Tutkun B, Barlay ES, Yalçınkaya C, Yazıcı H. Effect of internal curing on shrinkage and cracking potential under autogenous and drying conditions. Constr Build Mater. 2023;409:134078. [Google Scholar]
Cite This Article
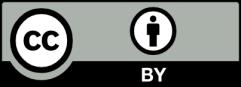
This work is licensed under a Creative Commons Attribution 4.0 International License , which permits unrestricted use, distribution, and reproduction in any medium, provided the original work is properly cited.