Open Access
ARTICLE
Numerical and Experimental Analysis of the Aerodynamic Torque for Axle-Mounted Train Brake Discs
1 Brake System Laboratory, CRCC (Qingdao) Vehicle Inspection Station Co., Ltd., Qingdao, 266031, China
2 Brake System Laboratory, CRRC Qingdao Sifang Rolling Stock Research Institute Co., Ltd., Qingdao, 266031, China
3 The State Key Laboratory of Heavy-Duty and Express High-Power Electric Locomotive, Central South University, Changsha, 410075, China
4 Key Laboratory of Traffic Safety on Track of Ministry of Education, School of Traffic & Transportation Engineering, Central South University, Changsha, 410075, China
5 National & Local Joint Engineering Research Center of Safety Technology for Rail Vehicle, Changsha, 410075, China
* Corresponding Author: Chen Jiang. Email:
Fluid Dynamics & Materials Processing 2024, 20(8), 1867-1882. https://doi.org/10.32604/fdmp.2024.047427
Received 05 November 2023; Accepted 25 March 2024; Issue published 06 August 2024
Abstract
As the velocity of a train increases, the corresponding air pumping power consumption of the brake discs increases proportionally. In the present experimental study, a standard axle-mounted brake disc with circumferential pillars was analyzed using a 1:1 scale model and a test rig in a wind tunnel. In particular, three upstream velocities were selected on the basis of earlier investigations of trains operating at 160, 250, and 400 km/h, respectively. Moreover, 3D steady computational fluid dynamics (CFD) simulations of the flow field were conducted to compare with the wind tunnel test outcomes. The results for a 3-car train at 180 km/h demonstrated: (1) good agreement between the air resistance torques obtained from the wind tunnel tests and the related numerical results, with differences ranging from 0.95% to 5.88%; (2) discrepancies ranging from 3.2 to 3.8 N · m; (3) cooling ribs contributing more than 60% of the air resistance torque; (4) the fast rotation of brake discs causing a significantly different flow field near the bogie area, resulting in 25 times more air pumping power loss than that obtained in the stationary brake-disc case.Keywords
Cite This Article
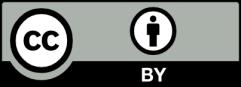
This work is licensed under a Creative Commons Attribution 4.0 International License , which permits unrestricted use, distribution, and reproduction in any medium, provided the original work is properly cited.