Open Access
ARTICLE
Physical-Rheological Properties and Performances of Rejuvenated (Styrene-Butadiene-Styrene) Asphalt with Polymerized-MDI and Aromatic Oil
1 Hubei Regional Management Headquarters, CCCC Asset Management Co., Ltd., Beijing, 101399, China
2 School of Civil Engineering and Architecture, Wuhan Institute of Technology, Wuhan, 430073, China
3 Hubei Provincial Engineering Research Center for Green Civil Engineering Materials and Structures, Wuhan Institute of Technology, Wuhan, 430073, China
* Corresponding Author: Xiong Xu. Email:
(This article belongs to the Special Issue: Advances in Rheological Property Evaluation of Bitumen and Bituminous Mixtures)
Fluid Dynamics & Materials Processing 2024, 20(7), 1633-1646. https://doi.org/10.32604/fdmp.2024.051010
Received 25 February 2024; Accepted 27 May 2024; Issue published 23 July 2024
Abstract
Traditional asphalt rejuvenators, like aromatic oil (AO), are known to be effective in improving the low-temperature properties and fatigue performances of aged SBS (styrene-butadiene-styrene) modified asphalt (SBSMA) binders and mixtures. However, these rejuvenators inevitably compromise their high-temperature properties and deformation resistances because they dilute asphalt binder but do not fix the damaged structures of aged SBS. In this study, a highly-active chemical called polymerized 4,4-diphenylmethane diisocyanate (PMDI) was used to assist the traditional AO asphalt rejuvenator. The physical and rheological characteristics of rejuvenated SBSMA binders and the moisture-induced damage and rut deformation performances of corresponding mixtures were comparatively evaluated. The results showed that the increasing proportion of AO compromises the high-temperature property and hardness of aged SBSMA binder, and an appropriate amount of PMDI works to compensate such losses; 3% rejuvenator at mass ratio of AO:PMDI = 70:30 can have a rejuvenated SBSMA binder with a high-temperature performance similar to that of fresh binder, approximately at 71.4°C; the use of AO can help reduce the viscosity of PMDI rejuvenated SBSMA binder for improving its workability; PMDI can help improve the resistance of AO rejuvenated SBSMA binder to deformation, especially at elevated temperatures, through its chemical reactions with aged SBS; moisture induction can enhance the resistance to damage of rejuvenated mixtures containing AO/PMDI or only PMDI; and the rejuvenator with a mass ratio of AO:PMDI = 70:30 can lead the rejuvenated mixture to meet the application requirement, with a rut depth of only 2.973 mm, although more PMDI can result in a higher resistance of rejuvenated mixtures to high-temperature deformation.Graphic Abstract
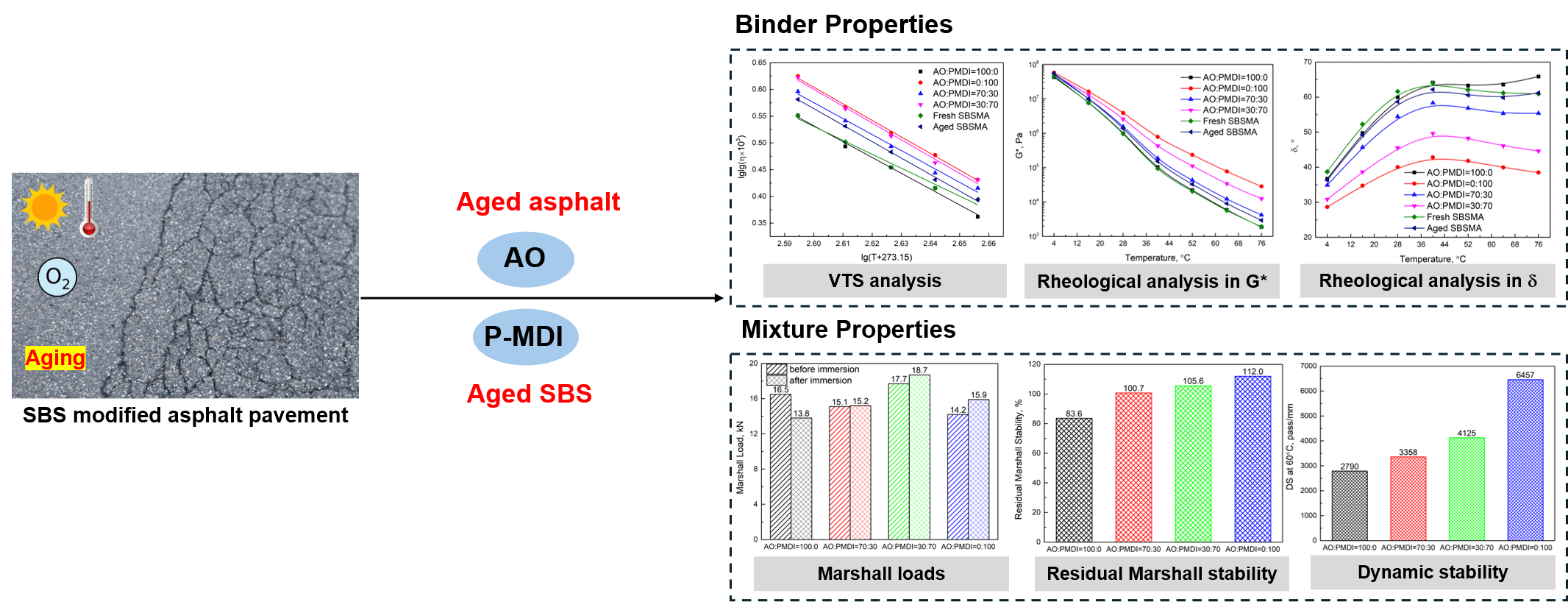
Keywords
The styrene–butadiene–styrene triblock copolymer-modified asphalt (SBSMA) binder is widely used in high-class pavement construction because of its excellent performance under high and low temperatures [1–3]. However, the pavements are prone to deterioration owing to exposure to ultraviolet radiation, heat, oxygen, rainwater, and driving loads. This degradation manifests as road distress in the forms of potholes and cracks [4–6]. Consequently, severely damaged pavement requires milling and rebuilding for safety and driving comfort. The resulting waste mixtures are generally disposed of in landfills and stockpiles, which causes environmental pollution and resource wastage [7,8]. Therefore, it is crucial to thoroughly consider effective and efficient approaches for recycling waste SBSMA mixtures.
Owing to the presence of the styrene–butadiene–styrene (SBS) modifier, the aging process of the SBSMA binder differs significantly from that of virgin bitumen [9,10]. The aging process involves not only the oxidation and polycondensation of the bitumen phase but also the oxidative degradation of SBS [11–13]. Consequently, if the rejuvenation of aged SBSMA binder follows a rehabilitation method similar to that of aged virgin bitumen, the oxidative degradation products of SBS will not, even to a small extent, be activated and reassembled at the molecular level to contribute to the performance of the rejuvenated binder [14,15]. Hence, it is imperative to develop a new rejuvenation system that incorporates reactive chemicals and commonly used asphalt rejuvenators to restore binder performance for high-quality rejuvenation of waste SBSMA mixtures.
Currently, several studies have investigated the engineering properties of rejuvenated SBSMA binders and mixtures through various methods. For example, Cao et al. [16] experimented with cashew shell oil and reactive rejuvenators to rehabilitate the performance of aged SBSMA binders. They discovered significant improvements in the self-healing potential and fatigue resistance of aged binders. Additionally, the fatigue life of the reaction-rejuvenated binder was twice as long as that of commonly rejuvenated binder. Zheng et al. [17] utilized maleic anhydride, epoxidized polybutadiene resin, and epoxidized soybean oil to create composite rejuvenators for aged SBSMA binders. They concluded that these composite rejuvenators, when used in specific amounts, effectively repaired broken structures within the aged SBS, and this resulted in improved physical and rheological properties. These case studies indicated that traditional oil-based rejuvenators were essentially unable to fully enhance the performance properties of aged SBSMA binders and mixtures, because they mainly impact the chemical composition adjustment of aged virgin asphalt binder, with no effect on the structural reassembly of aged SBS. Therefore, there is an urgent need to develop a new composite rejuvenator capable of repairing the molecular structure of aged SBS and addressing aging issues within the chemical composition of virgin asphalt. This development will significantly support the high-quality application of recycled SBSMA mixtures.
Overall, this study explores the use of a highly active chemical called polymerized 4,4-diphenylmethane diisocyanate (PMDI) to enhance the effectiveness of a common asphalt rejuvenator known as aromatic oil (AO) in rejuvenating aged SBSMA binder and mixture. We systematically evaluate the physical and rheological characteristics of PMDI/AO-rejuvenated SBSMA binders, including softening point, penetration, viscosity, complex modulus, and phase angle. Additionally, we analyze key mixture performances of rejuvenated SBSMA mixtures, focusing on high-temperature stability and moisture-induced damage resistance through comparative analysis.
2.1.1 SBS Modified Asphalt Binder
The SBSMA binder used in this study was obtained from a local factory in Wuhan, China. The main physical properties of the binder were tested, and the results are summarized in Table 1.
The asphalt rejuvenators used in this study include AO and PMDI. AO, a commonly used asphalt rejuvenator, is an oily substance with a high aromatic content exceeding 70%. The AO used in this study was obtained from a local oil-refining factory in Wuhan, China. PMDI is a high-performance polyurethane chemical used in various applications such as adhesives, sealants, coatings, and rigid foams. After curing or reaction, PMDI exhibited outstanding mechanical properties and chemical resistance. In this study, PMDI was employed for the rejuvenation of aged SBS in binders, as its highly reactive terminated groups can react with active oxygen-containing groups.
The aggregates used in this study included coarse aggregate, fine aggregate, and mineral powder. The aggregates were all sourced from limestone from a local supplier in Wuhan, China. The main technical indicators of these aggregates were tested, and Table 2 presents the results [18].
2.2.1 Preparation of Aged SBSMA Binder
The aged SBSMA binder was prepared following these procedures: First, the fresh SBSMA binder was heated to a molten state at 170°C and poured into steel aging-use trays, with each tray containing approximately 50 ± 0.5 g of binder. The trays filled with binders were then placed in an aging oven preheated to 163°C for 5 h to conduct the thin film oven test for short-term aging simulation. Subsequently, the binders underwent long-term aging simulation at 100°C for 20 h with a controlled pressure of 2.1 MPa using a pressurized aging vessel aging test. Finally, the aged SBSMA binder was collected for rejuvenation. Table 3 presents the test results of some physical properties.
2.2.2 Preparation of Rejuvenated SBSMA Binders
The rejuvenated SBSMA binders were prepared according to the following procedures: First, the aged SBSMA binder was heated to 170°C to achieve adequate viscosity for uniform mixing. Subsequently, rejuvenators were prepared at different mass ratios of AO:PMDI = 100:0, 70:30, 30:70, and 0:100. AO and PMDI were mixed and stirred for 5 min at room temperature owing to their high reactivity. The rejuvenators were then added to the molten aged binders and mixed at 600–1000 rpm for at least 25 min. Finally, the rejuvenated binders were collected for evaluation.
2.2.3 Preparation of Aged SBSMA Mixture
First, this study selected a commonly used AC-13 type aggregate gradation (Table 4) to prepare fresh SBSMA mixture at 175°C for 90–120 s, with an optimum asphalt content of 4.8% as determined by the Marshall design method. Subsequently, the prepared mixtures were placed into a 135°C oven for 4 h to undergo short-term aging. Finally, they were placed in an 85°C oven for 5 days to undergo long-term aging and prepare an aged SBSMA mixture.
2.2.4 Preparation of Rejuvenated SBSMA Mixtures
Before the preparation of the rejuvenated SBSMA mixtures, the binder content of the aged mixtures was determined as 3.3% through the burning method. According to this determination, rejuvenators were then added to the aged mixtures, following the same AC-13 type gradation. During mixing, the coarse aggregates comprised aged SBSMA concrete particles exceeding 2.36 mm, while the fine aggregates consisted of natural limestone particles below 2.36 mm. Additionally, Pen 70 virgin binder was added to maintain the original optimum binder content at 4.8%. Subsequently, the rejuvenated SBSMA mixtures were prepared at 175°C for 90–120 s.
2.3.1 Physical Properties Test
According to ASTM D36, the softening point was tested to evaluate the high-temperature performance of each rejuvenated SBSMA binder using a combination of AO or PMDI. Additionally, ASTM D5 was used to measure the penetration at 25°C to determine the hardness of the rejuvenated SBSMA binders.
2.3.2 Rotational Rheological Test
According to AASHTO TP48, rotational viscosities were tested at 120°C, 135°C, 150°C, 165°C, and 180°C to assess the viscosity–temperature correlation of the target binders and understand their workability. Furthermore, the viscosity–temperature susceptibility (VTS) was determined through the fitting of the viscosity–temperature curves using the typical Saal equation [19], as outlined using Eq. (1):
where η denotes the binder viscosity, Pa·s; T denotes the test temperature, °C; m denotes the VTS of the binder, of which the higher value means the higher VTS; and n denotes the maximum viscosity.
The temperature-dependent shear rheological test of target binders was conducted using a dynamic shear rheometer (DSR, MCR101, Anton Paar, Austria) to analyze the rheological behaviors of target binders [20]. The test conditions were as follows: a control of 0.1% strain, an angular frequency at 10 rad/s, a test temperature of 4°C–76°C with an interval of 12°C, and a heating rate at 2°C/min. For temperatures below 28°C, a pair of 8 mm-diameter and 25 mm-diameter parallel plates was employed. The gap distance between the plates was controlled at 1 mm. After the test, key rheological data, including complex modulus (G*) and phase angle (δ), were collected for anti-deformation analysis of rejuvenated binders.
The moisture-induced damage was evaluated for each rejuvenated mixture using the Marshall stability test following ASTM D6927 guidelines. Before the test, prefabricated Marshall specimens were preconditioned in a water bath at 60°C for 30 min and 48 h. Subsequently, the specimens were removed from the water bath and subjected to the Marshall stability tester using a controlled loading rate of 50 mm/min. Finally, the data collected were used to calculate the residual Marshall stability for evaluating moisture-induced damage [21]. The calculation was conducted using Eq. (2).
where MS0 denotes the residual Marshall stability after immersion in water, %; MS denotes the Marshall stability after immersion in water at 60°C for 30 min, kN; and MS1 denotes the Marshall stability after immersion in water at 60°C for 48 h, kN.
The rut deformation for each rejuvenated mixture was evaluated using the wheel tracking test according to ASTM D8292 guidelines. Before the test, the rejuvenated mixtures were prefabricated into specimens with dimensions of 300 mm × 300 mm × 50 mm. Subsequently, the specimens were placed in the 60°C test chamber of the rut device for approximately 5 h and then subjected to testing with a back-and-forth rolling speed of 42 cycles/min and a wheel load of 0.7 MPa for 60 min. Finally, the rut depth data were recorded and collected to calculate dynamic stability (DS) to assess the resistance to rut deformation at 60°C. The calculation was conducted using Eq. (3).
where DS denotes dynamic stability, pass/mm; d1 and d2 are the rut depths at 45 and 60 min, mm; and N is the back-and-forth rolling speed of the test wheel, usually 42 cycles/min.
Fig. 1 displays the effect of different rejuvenator contents on the softening point of an aged SBSMA binder. At a rejuvenator AO:PMDI mass ratio of 100:0, the softening point of rejuvenated SBSMA binder gradually decreases from 68.1°C to 60.0°C as the content increases from 1% to 7%. Conversely, at a rejuvenator AO:PMDI mass ratio of 0:100, the softening exhibits a trend of initial increase followed by a decrease, and the maximum peak value reaches 76°C–78°C. These results indicate that increasing the use of AO compromises the high-temperature performance of aged SBSMA binder, whereas incorporating an appropriate amount of PMDI enhances the softening temperature. AO is a traditional oil-type rejuvenator that only works to adjust the chemical components of aged virgin asphalt binder, while the terminal-NCO groups in the PMDI chemically interact with active oxygen-containing groups in the degradation products of SBS to generate new substances with rigid structures for a continuous increase in high-temperature flexibility.
Figure 1: Effect of different rejuvenator contents on softening point of aged SBSMA binder
Additionally, the combined use of AO and PMDI as rejuvenators, regardless of their mixing proportions, generally results in softening point trends characterized by an initial increase followed by a decrease in rejuvenated SBSMA binders. However, at an AO:PMDI mass ratio of 70:30, the rejuvenated SBSMA binder achieves a softening point close to that of fresh SBSMA, specifically 71.4°C before its 3% incorporation. Subsequently, increasing the content from 3% to 7% causes only a slight decrease of within 2°C, similar to the effect observed at an AO:PMDI mass ratio of 30:70. These findings indicate that the addition of 3% rejuvenator with an AO:PMDI mass ratio of 70:30 can rejuvenate SBSMA binder to achieve similar high-temperature performance to that of the fresh binder.
Fig. 2 illustrates the impact of varying rejuvenator contents on the penetration of aged SBSMA binder. The trends of penetration for different rejuvenated SBSMA binders are opposite to the softening point trends. For the rejuvenators at 3%, only the rejuvenator with an AO:PMDI mass ratio of 100:0 causes an increase in penetration from 51 to 58 dmm. Other rejuvenators lead to penetration reductions ranging from 35 to 50 dmm, indicating that the minor utilization of PMDI will increase the hardness of aged SBSMA binders to some extent, regardless of the presence of AO. Similar observations can be drawn from the analysis of softening point trends.
Figure 2: Effect of different rejuvenator contents on penetration of aged SBSMA binder
3.2.1 Viscosity–Temperature Characteristic
Fig. 3 illustrates the viscosity–temperature characteristics of rejuvenated SBSMA binders containing 3% rejuvenator comprised of AO and PMDI. With the use of the rejuvenator with an AO:PMDI mass ratio of 100:0, the viscosity of the rejuvenated binder significantly decreases toward that of fresh SBSMA binder, while the viscosities become high with the addition of the other rejuvenators incorporating PMDI, especially the rejuvenator with an AO:PMDI mass ratio of 0:100. Additionally, the viscosity of the rejuvenated binder rapidly increases as the AO:PMDI mass ratio changes from 70:30 to 30:70, and then increases to a lesser extent as the ratio changes to 0:100. These results demonstrate that the use of PMDI generally leads to increased viscosities of rejuvenated SBSMA binders, regardless of whether AO is present. The combined use of AO, particularly at an AO:PMDI mass ratio of 70:30, helps reduce the viscosity to some extent to improve the applicable workability of the rejuvenated SBSMA binder. A small amount of PMDI can react with functional groups from aged SBS to form new macromolecular structures that are difficult to move even at high temperatures, causing a significant increase in viscosity. Moreover, AO plays a role in diluting the total binder for flowability enhancement. Overall, the rejuvenator with an AO:PMDI mass ratio of 70:30 shows relatively superior performance to the workability of the rejuvenated SBSMA binder for potential engineering applications.
Figure 3: Viscosity-temperature correlation of rejuvenated SBSMA binders with 3% rejuvenator
Fig. 4 and Table 5 display fitted curves and equations to further demonstrate the VTS of the studied binders. Notably, the R2 values of all binders exceed 0.980, which suggests that the fitted results can reveal the correlation between viscosity and temperature. The m-value of fresh SBSMA binder after aging increases slightly from 2.605 to 3.080, indicating that aging makes the fresh binder more susceptible to temperature. Furthermore, the m-value of aged SBSMA binder changes within 0.100 with the addition of different rejuvenators, indicating a close similarity. These variations suggest that the mixing proportion of AO and PMDI is not a key factor affecting the VTS of rejuvenated SBSMA binders.
Figure 4: VTS analysis of rejuvenated SBSMA binders with 3% rejuvenator
3.2.2 Complex Modulus and Phase Angle
Fig. 5 illustrates the rheological analysis in G* for rejuvenated SBSMA binders with a 3% rejuvenator. The G* values of aged SBSMA binder after aging increase notably within the temperature range of 4°C and 76°C. At a rejuvenator AO:PMDI mass ratio of 100:0, the G* curve of the rejuvenated binder closely resembles that of the fresh SBSMA binder. Conversely, increasing the proportion of PMDI results in progressively higher G* values. These results demonstrate that the resistance of rejuvenated binders to deformation at different temperatures weakens with the addition of the physical rejuvenator AO but strengthens with PMDI addition, because PMDI can chemically interact with the active oxygen-containing groups from the degradation products of SBS to form new substances with rigid polymerized structures. AO, being a lighter component, only dissolves and softens some of the unreacted bitumen molecules. Therefore, the composite rejuvenator composed of polymerized MDI and AO can overcome the performance loss of ordinary rejuvenated asphalt binder in terms of high-temperature performance and hardness. The rejuvenated SBSMA binder with the addition of a rejuvenator at an AO:PMDI mass ratio of 70:30 shows slightly higher G* values than the aged SBSMA binder. This suggests that additional PMDI may not be necessary to increase the G* values further to enhance its resistance to deformation at elevated temperatures, considering cost-effectiveness and workability.
Figure 5: Rheological analysis in G* of rejuvenated SBSMA binders with 3% rejuvenator
Fig. 6 presents a rheological analysis of rejuvenated SBSMA binders with a 3% rejuvenator. As temperature increases, the δ value of fresh SBSMA binder initially rises sharply, peaking around 36°C, before gradually decreasing toward a relatively stable state. This demonstrates the typical phase-angle rheological behavior of fresh SBSMA binder, wherein the initial stage primarily reflects the softening performance of virgin bitumen, followed by molecular chain movement after the physical crosslinking structure of SBS is damaged. Subsequently, after aging, the δ value of the fresh binder decreases to varying degrees, with an increasing trend observed after 64°C. This suggests that partial structural damage to SBS occurs during the aging process of the binder, resulting in weakened deformation resistance from the SBS polymeric component at lower temperatures.
Figure 6: Rheological analysis in δ of rejuvenated SBSMA binders with 3% rejuvenator
With the addition of a rejuvenator with an AO:PMDI mass ratio of 100:0, the δ values of the aged binder increase. However, the previously observed slight decreasing trend does not reappear. This indicates that this rejuvenated binder is much more susceptible to softening and deformation, particularly at elevated temperatures. Conversely, the δ values of the rejuvenated binder decrease as the rejuvenator contains more PMDI. Additionally, the previously noted slight decreases at the second stage reappear. This suggests that PMDI can react with the broken molecular structures of SBS in an aged binder to form a new polymeric structure, enhancing resistance to high-temperature deformation, regardless of whether the rejuvenator contains AO. According to these results and viscosity and softening point data, the rejuvenator with an AO:PMDI mass ratio of 70:30 demonstrates superior performance in rejuvenating SBSMA binders with high deformation resistance for engineering applications.
Fig. 7 depicts the Marshall loads of rejuvenated SBSMA mixtures before and after immersion in moisture. The loads of rejuvenated mixtures are 16.5, 15.1, 17.7, and 14.2 kN at rejuvenator AO:PMDI mass ratios of 100:0, 70:30, 30:70, and 0:100, respectively. After immersion, these values change to 13.8, 15.2, 18.7, and 15.9 kN, respectively. Notably, the load decreases for the AO-rejuvenated mixture and increases for the other mixtures after immersion. This indicates that exposure to moisture leads to decreased resistance of AO-rejuvenated mixture to external damage while enhancing the damage resistance of rejuvenated mixtures containing AO/PMDI or only PMDI. However, with increasing PMDI content of rejuvenators, the load of the rejuvenated mixture first increases and then decreases, which indicates that a very high PMDI content may not provide optimal performance in resisting external damage before and after moisture exposure. Hence, the appropriate use of AO and PMDI is crucial for rejuvenating the aged SBSMA mixture.
Figure 7: Marshall loads of rejuvenated SBSMA mixtures before and after moisture immersion
Fig. 8 illustrates the residual Marshall stability of rejuvenated SBSMA mixtures after moisture immersion. Notably, only the rejuvenator with an AO:PMDI mass ratio of 100:0 yields residual stability of <100%, at 83.6%, while others, including PMDI, resulted in values exceeding 100%. As the mass ratio of AO:PMDI changes from 70:30 to 30:70 and then to 0:100, the residual stability of the rejuvenated mixture gradually increases from 100.7% to 105.6% and then to 112.0%. These findings suggest that the resistance of the AO-rejuvenated mixture to moisture-induced damage weakens, a trend that is further exacerbated with higher proportions of PMDI in rejuvenators. This is attributed to water molecules penetrating weak physical interfaces between AO-rejuvenated binders and aggregates, causing moisture-induced damage. However, these molecules can react with residual PMDI to form strong chemical interfaces between AO and PMDI or PMDI-rejuvenated binders and aggregates, enhancing resistance to moisture damage before complete consumption. The rejuvenator with an AO:PMDI mass ratio of 70:30 is recommended for preparing highly moisture-resistant rejuvenated SBSMA mixtures.
Figure 8: Residual Marshall stability of rejuvenated SBSMA mixtures after moisture immersion
Fig. 9 illustrates the DS of rejuvenated SBSMA mixtures with 3% rejuvenator at 60°C. As the proportion of PMDI in rejuvenators increases, the DS value of the rejuvenated mixture also increases. The rejuvenated mixture without a PMDI achieves a DS value of 2790 passes/mm, significantly lower than the value of 6457 passes/mm achieved with only PMDI added. Furthermore, rejuvenators with AO:PMDI mass ratios of 70:30 and 30:70 yield DS values of 3358 passes/mm and 4125 passes/mm, respectively, both meeting the application requirements for highway construction, such as the threshold value of 2800 pass/mm required by JTG F40-2019. These results indicate that the rejuvenator with an AO:PMDI mass ratio of 70:30 can help the rejuvenated mixture meet application requirements, although additional PMDI can further enhance the mixture’s resistance to deformation at high temperatures.
Figure 9: DS of rejuvenated SBSMA mixtures with 3% rejuvenator at 60°C
Fig. 10 displays the 60°C rut depth of rejuvenated SBSMA mixtures with 3% rejuvenator at 60 min. As the AO:PMDI mass ratio in rejuvenators increases from 100:0 to 70:30, 30:70, and 0:100, the rut depth value of the rejuvenated mixture decreases to 3.660, 2.973, 1.914, and 1.622 mm, respectively. These values are all below 4.000 mm, significantly less than the critical rut depth of 10.000 mm required by JTG H20-2015. The findings indicate that although a rejuvenated mixture with a rejuvenator AO:PMDI mass ratio of 100:0 is applicable, higher resistances of rejuvenated mixtures to rut can be achieved through the addition of more proportions of PMDI to the 3% rejuvenator.
Figure 10: The 60°C rut depth of rejuvenated SBSMA mixtures with 3% rejuvenator at 60 min
4 Conclusions and Recommendations
This case study explored the use of PMDI as a rejuvenator component to address shortcomings observed in AO-rejuvenated SBSMA binders and mixtures, particularly regarding decreased high-temperature performance and deformation resistance. Through comparative investigations into the physical and rheological properties of rejuvenated binders and the moisture stability and anti-rut properties of rejuvenated mixtures, the performance of the studied rejuvenators was evaluated. Key findings are as follows:
1) The physical properties results indicated that increasing the proportion of AO compromised the high-temperature property and hardness of aged SBSMA binder. Moreover, the addition of an appropriate dosage of PMDI effectively compensated for these property losses. Furthermore, a 3% rejuvenator with an AO:PMDI mass ratio of 70:30 can rejuvenate the SBSMA binder to achieve a high-temperature performance similar to that of a fresh binder, approximately 71.4°C.
2) The viscosity–temperature correlation results indicated that PMDI addition significantly increased the viscosities of rejuvenated SBSMA binders, whereas the combined use of AO, particularly at an AO:PMDI mass ratio of 70:30, helps reduce viscosity to improve workability. Interestingly, the AO/PMDI mix proportions have minimal influence on the VTS of rejuvenated SBSMA binders.
3) The complex modulus results indicated that PMDI contributed to improving the resistance of the AO-rejuvenated SBSMA binder to deformation, particularly at elevated temperatures. Notably, an AO:PMDI mass ratio of 70:30 resulted in a rejuvenated binder with slightly higher G* values than that of the aged SBSMA binder.
4) The phase angle results indicated that PMDI interacted chemically with the damaged molecular structures of SBS in the aged binder, leading to the reformation of new polymeric structures and enhancing resistance to high-temperature deformation, irrespective of whether the rejuvenator contained AO.
5) The moisture-induced damage results revealed that exposure to moisture reduced the resistance of the AO-rejuvenated mixture to external damage but enhanced the damage resistance in rejuvenated mixtures containing AO/PMDI or only PMDI. Excessive PMDI content in rejuvenators was not optimal for resisting external damage before and after exposure to moisture.
6) The rut deformation results revealed that the rejuvenator with an AO:PMDI mass ratio of 70:30 could economically enhance the rejuvenated mixture to meet the application requirement, with a rut depth of only 2.973 mm, although the addition of more PMDI can further improve the resistance of rejuvenated mixtures to deformation at high temperatures.
Overall, the hybrid use of PMDI and AO showed promise for high-performance recycling of waste SBSMA mixtures. Future research should focus on the cost-effective utilization of PMDI in rejuvenators for different pavement applications and explore its compatibility with other traditional rejuvenators to ensure high-quality rejuvenation of waste SBSMA mixtures and validate their durability.
Acknowledgement: The authors thank to the financial supports from the company for this work.
Funding Statement: This work was supported by the Scientific Technology R&D Project of CCCC Asset Management Co., Ltd. (RP2022015294).
Author Contributions: The authors confirm contribution to the paper as follows: Ao Lu: Conceptualization, Methodology, Resources, Formal analysis, Writing-review & editing; Ming Xiong & Chen Chen: Data curation, Formal analysis, Investigation, Validation, Writing-original draft; Liangjiang Li: Conceptualization, Methodology, Formal analysis, Writing-review & editing; Haibei Tan: Test result analysis; Xiong Xu: Investigation, Testing and testing assistance, Funding acquisition, Manuscript revision & editing. All authors reviewed the results and approved the final version of the manuscript.
Availability of Data and Materials: The datasets generated during and/or analyzed during the current study are not publicly available due to protect data privacy and protect intellectual property, but are available from the corresponding author on reasonable request.
Conflicts of Interest: The authors declare that they have no conflicts of interest to report regarding the present study.
References
1. Cuciniello G, Leandri P, Filippi S, Lo Presti D, Polacco G, Losa M, et al. Microstructure and rheological response of laboratory-aged SBS-modified bitumens. Road Mater Pavement Des. 2021;22:372–96. [Google Scholar]
2. Xu X, Sreeram A, Leng Z, Yu JY, Li R, Peng C. Challenges and opportunities in the high-quality rejuvenation of unmodified and SBS modified asphalt mixtures: state of the art. J Clean Prod. 2022;378:134634. [Google Scholar]
3. Yalcin BF, Bakir E, Yalcin E, Yilmaz M. Composite modifiers to improve the rheological properties of asphalt binders. J Mater Civil Eng. 2024;36(6):04024101. [Google Scholar]
4. Jiang X, Zhu HH, Yan ZG, Zhang FS, Huang X, Leng Z, et al. Fire-retarding asphalt pavement for urban road tunnels: a state-of-the-art review and beyond. Fire Technol. 2024;60(2):1–41. [Google Scholar]
5. Keymanesh MR, Amani S, Omran AT, Karimi MM. Evaluation of the impact of long-term aging on fracture properties of warm mix asphalt (WMA) with high RAP contents. Constr Build Mater. 2023;400:132671. [Google Scholar]
6. Saleh NF, Braswell E, Elwardany M, Yousefi Rad F, Castorena C, Kim YR. Field calibration and validation of a pavement aging model. Int J Pavement Eng. 2023;24(2):2027416. doi:https://doi.org/10.1080/10298436.2022.2027416. [Google Scholar] [CrossRef]
7. Mariyappan R, Palammal JS, Balu S. Sustainable use of reclaimed asphalt pavement (RAP) in pavement applications—a review. Environ Sci Pollut R. 2023;30(16):45587. doi:https://doi.org/10.1007/s11356-023-25847-3. [Google Scholar] [PubMed] [CrossRef]
8. Vijay K, Paluri Y, Reddy MS, Rao IV, John K, Dayanand N. Performance evaluation of reclaimed asphalt pavement (RAP) aggregate in concrete pavements: a state-of-the-art review. J Build Pathol Rehabil. 2023;8(2):90. doi:https://doi.org/10.1007/s41024-023-00335-w. [Google Scholar] [CrossRef]
9. Celauro C, Teresi R, Dintcheva NT. Effect of short-term and UV irradiation aging on the behaviour of SBS-modified bitumen. Sustainability. 2022;14(11):6915. doi:https://doi.org/10.3390/su14116915. [Google Scholar] [CrossRef]
10. Kaya D, Topal A, Gupta J, McNally T. Aging effects on the composition and thermal properties of styrene-butadiene-styrene (SBS) modified bitumen. Constr Build Mater. 2020;235(3):117450. doi:https://doi.org/10.1016/j.conbuildmat.2019.117450. [Google Scholar] [CrossRef]
11. Frolov IN, Okhotnikova ES, Ziganshin MA, Yusupova TN, Firsin AA. The study of bitumen by differential scanning calorimetry: the interpretation of thermal effects. Petrol Sci Technol. 2019;37(4):417–24. doi:https://doi.org/10.1080/10916466.2018.1550499. [Google Scholar] [CrossRef]
12. Kaya D, Topal A, McNally T. Relationship between processing parameters and aging with the rheological behaviour of SBS modified bitumen. Constr Build Mater. 2019;221(1–3):345–50. doi:https://doi.org/10.1016/j.conbuildmat.2019.06.081. [Google Scholar] [CrossRef]
13. Aurilio M, Tavassoti P, Elwardany M, Baaj H. Impact of styrene-butadiene-styrene (SBS) content on asphalt binder’s fatigue resistance at various aging levels using viscoelastic continuum damage and fracture mechanics. Constr Build Mater. 2021;305:124627. doi:https://doi.org/10.1016/j.conbuildmat.2021.124627. [Google Scholar] [CrossRef]
14. Guo M, Liang M, Sreeram A, Bhasin A, Luo D. Characterisation of rejuvenation of various modified asphalt binders based on simplified chromatographic techniques. Int J Pavement Eng. 2022;23(12):4333. doi:https://doi.org/10.1080/10298436.2021.1943743. [Google Scholar] [CrossRef]
15. Lin P, Liu X, Apostolidis P, Erkens S, Zhang Y, Ren S. ESEM observation and rheological analysis of rejuvenated SBS modified bitumen. Mater Des. 2021;204(1983):109639. doi:https://doi.org/10.1016/j.matdes.2021.109639. [Google Scholar] [CrossRef]
16. Cao ZL, Yu JY, Yi J, Sun GQ, Qiu KX, Xu S, et al. Effect of different rejuvenation methods on the fatigue behavior of aged SBS modified asphalt. Constr Build Mater. 2023;407:133494. [Google Scholar]
17. Zheng WZ, Zhang HL, Yang X, Duan HH. Effect of MA-EPR-ESO compound rejuvenator on rheological properties of aged SBS-modified bitumen. J Test Eval. 2023;51(6):20230004. [Google Scholar]
18. Pang H, Lu A, Xiong M, Chen C, Cao X, Xu X, et al. Performance characterization of CR/PU asphalt for potential application in assembled fast-repairing engineering. Fluid Dyn Mater Proc. 2024;20(5):1063–74 doi:https://doi.org/10.32604/fdmp.2023.044000. [Google Scholar] [CrossRef]
19. Xu X, Chu YM, Luo Y, Peng YH, Yang NN, Yan JM, et al. Thermal-and-mechanochemical recycling of waste polypropylene into maleated-epoxided degradation products as warm-mix asphalt modifier: performance improvement and production mechanism analysis. J Clean Prod. 2023;426:139222. [Google Scholar]
20. Xu X, Leng Z, Lan JT, Wang W, Yu JM, Bai YW, et al. Sustainable practice in pavement engineering through value-added collective recycling of waste plastic and waste tyre rubber. Engineering. 2021;7(6):857–67. [Google Scholar]
21. Yang M, Huang T, Lv ST, Zheng JL. Effect and mechanism of acidic aggregate surface silane modification on water stability of asphalt mixture. Road Mater Pavement Des. 2021;22(7):1654–66. doi:https://doi.org/10.1080/14680629.2020.1730229. [Google Scholar] [CrossRef]
Cite This Article
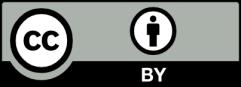
This work is licensed under a Creative Commons Attribution 4.0 International License , which permits unrestricted use, distribution, and reproduction in any medium, provided the original work is properly cited.