Open Access
ARTICLE
Preparation and Analysis of Carbon Fiber-Silicon Carbide Thermally Conductive Asphalt Concrete
School of Civil Engineering and Environment, Hubei University of Technology, Wuhan, 430068, China
* Corresponding Author: Zhi Chen. Email:
(This article belongs to the Special Issue: Advances in Solid Waste Processing and Recycling Technologies for Civil Engineering Materials)
Fluid Dynamics & Materials Processing 2024, 20(4), 705-723. https://doi.org/10.32604/fdmp.2023.044030
Received 19 July 2023; Accepted 02 November 2023; Issue published 28 March 2024
Abstract
An experimental investigation into the thermal conductivity of CF-SiC two-phase composite asphalt concrete is presented. The main objective of this study was to verify the possibility of using SiC powder instead of mineral powder as the thermal conductive filler to prepare a new type of asphalt concrete and improve the efficiency of electrothermal snow and ice melting systems accordingly. The thermal conductivity of asphalt concrete prepared with different thermally conductive fillers was tested by a transient plane source method, and the related performances were measured. Then the temperature rise rate and surface temperature were studied through field heating tests. Finally, the actual ice melting efficiency of the thermally conductive asphalt concrete was evaluated using an effective electrothermal system. As shown by the experimental results, the composite made of SiC powder and carbon fiber has a high thermal conductivity. When SiC replaces mineral powder, the thermal conductivity of the asphalt mixture increases first and then decreases with the increase of carbon fiber content. In the present study, in particular, the thermal conductivity attained a peak when the carbon fiber content was 0.2% of the aggregate mass.Keywords
Compared with traditional cement concrete pavement, asphalt concrete has become a necessary material for road engineers due to its advantages of bearing comfort, durability, and simple maintenance [1,2]. However, with the increasingly complex environmental conditions, the service life and traffic safety of asphalt concrete pavement have been seriously affected. Particularly, in winter, when the ambient temperature is low, snow and ice on road surfaces reduce the adhesion coefficient between the road and vehicle wheels by more than 75%, which seriously affects driving safety and causes a series of problems, such as traffic accidents, traffic delays, and economic losses [3]. To cope with the negative impact of snow and ice on asphalt concrete pavements during the cold season, snow and ice suppression technology has become an increasingly important field in many countries.
Up to now, the traditional methods of inhibiting road icing and removing snow in winter are mainly mechanical deicing and salting. These methods cause different levels of damage to asphalt concrete pavement in the pavement structure and ancillary facilities, corrosion of steel bars, and affect the soil and water environments [4]. In addition, other problems such as low efficiency and incomplete snow removal cannot be ignored [5,6]. Therefore, it is necessary to develop more efficient and environmentally friendly snow-melting and ice-melting solutions.
To mitigate the impact of extreme temperatures during cold seasons on traffic safety, researchers have developed many new and practical de-icing technologies, such as the geothermal method [7,8], electric heating method [9,10], and roads with high thermal conductivity [11,12]. Roads with high thermal conductivity are achieved by adding thermally conductive materials to asphalt concrete, or using thermally conductive materials to modify asphalt binders [13]. The thermal conductivity of asphalt concrete has a very important influence on the temperature distribution of the asphalt pavement, including gradient thermal conductivity, bidirectional thermal conductivity, and the heat-resistant wear layer [14,15]. The main goal of this study was to improve the energy transmission and energy utilization efficiency by incorporating some thermal conductive materials into the asphalt mixture. This would allow the asphalt concrete to more effectively transfer heat from the heat source to the pavement direction during the colder months and quickly raise pavement temperature. In addition, it would reduce the time it takes for snow and ice to melt. In the literature, carbon fiber (CF), steel fiber, and graphite are usually used as thermally conductive materials in cement and asphalt mixtures [16]. Compared with other thermally conductive materials, silicon carbide (SiC) micropowder has the characteristics of low cost, corrosion resistance, stable chemical properties, high strength, and good adhesion to asphalt [17]. Therefore, there is high research value and application prospects to replace mineral powder with SiC powder as the thermally conductive aggregate in asphalt concrete pavements.
To prevent snow and ice from forming on road surfaces or to quickly melt and deice the surface, the goal of this study was to create thermally conductive asphalt concrete (TCAC) with a high thermal conductivity. This would help to solve the wintertime problem of poor road traffic safety.
The thermal properties of TCAC made of SiC powder, in replacement of mineral powder, mixed with carbon fiber (CF) as the thermally conductive filler were evaluated in the laboratory. Firstly, the thermal conductivity of TCAC prepared by adding different contents of CF and SiC powder was tested to determine the appropriate SiC and CF contents. Then, the engineering performance of the resulting TCAC was tested and analyzed against that of ordinary asphalt concrete (OAC) to ensure that the TCAC met the requirements of actual engineering specifications. Finally, the snow melting efficiency of the TCAC was evaluated using an electric heating system. The sequence of steps is summarized in Fig. 1.
Figure 1: Technical roadmap of the study
The TCAC specimens prepared in this study were composed of asphalt binder, conventional aggregate, and thermally conductive aggregate. The asphalt binder was a 70# matrix asphalt, and the test was carried out according to the ‘Standard Test Methods of Bitumen and Bituminous Mixtures for Highway Engineering’ (JTG E20-2011). Table 1 lists the basic properties of the 70# matrix asphalt. The conventional aggregate was basalt, and its basic properties were measured according to the ‘Test Methods of Aggregate for Highway Engineering’ (JTG E42-2005). The results are presented in Table 2. The thermally conductive aggregates were 3–6 mm chopped CF and 8000 mesh SiC, respectively. The basic parameters are listed in Table 3.
Thermally conductive materials are an important factor affecting the thermal conductivity of asphalt concrete. The differences in thermally conductive materials can directly affect the thermal conductivity of asphalt concrete, especially when a variety of different types of thermally conductive materials exist in asphalt concrete, and even produce a superposition effect. The superposition effect can make up for the characteristic defects of using a single material as the thermally conductive material. The main thermally conductive materials used in this study were CF and SiC micropowder. The CF-SiC asphalt concrete with good thermal conductivity was designed considering appropriate test amount and thermally conductive material conditions. A dense asphalt concrete with a maximum aggregate diameter of 16 mm and a gradation of AC-13 was used. The gradation was designed according to the requirements of the ‘Highway Asphalt Pavement Design Specification’ (JTG D50-2017) [18]. The aggregate gradation is shown in Fig. 2.
Figure 2: Distribution of aggregate gradation
Considering that the densities of mineral powder and SiC are similar, the mass fraction was used as a control index to ensure that the volume index of the mixture was not significantly different. Using the direct casting method, CF was added to the asphalt mixture as a thermally conductive filler. In the experiment, 0.1%, 0.2%, 0.3%, 0.4%, and 0.5% CF of the aggregate mass and 100% SiC micropowder replacing the mineral powder mass were added as thermal conductive fillers to Marshall specimens, and the specimens were grouped as presented in Table 4. The Marshall Specimen (MS) was designed according to the standard Marshall Design Method (ASTM D 6926-04).
2.3.1 Thermal Conductivity Test of Marshall Specimens
Thermal conductivity is an extremely important parameter used in evaluating the thermal performance of asphalt concrete. Previous studies on the thermal conductivity of asphalt mixtures have found that it was affected by many factors, including aggregate type, mixture gradation, particle size, compaction method, porosity, and density [19]. Based on these considerations, as shown in Fig. 3, the transient plane source (TPS) method was used to measure the thermal conductivity of the Marshall specimen using a thermal conductivity device (DRE-III) to determine the appropriate amount of thermally conductive material. Accordingly, 12 groups of tests were selected to test the thermal conductivity. To ensure consistency during the test, the test was carried out at constant room temperature. To keep the probe in continuous close contact with the sample, the surface of the Marshall specimen was first smoothed, and then the probe was placed between two identical samples and fixed on the test bench. Finally, the thermal conductivity was obtained directly from the computer under the conditions of output power of 0.5 W, test time of 60 s, and sampling interval of 200 ms. To improve the accuracy of the test results, three samples were selected for each group of tests, and the results were averaged.
Figure 3: Thermal conductivity testing of TCAC
2.3.2 Engineering Properties of TCAC
The water stability, low temperature crack resistance, and permanent deformation of asphalt concrete were tested by the Marshall test, bending test, and rutting test respectively according to the requirements of Chinese specifications (JTG E20-2011) [20].
(1) Marshall Test
Water stability mainly studies the damaging effect of pavement water on asphalt concrete in the process of freeze-thaw cycles. At present, the commonly used water stability evaluation methods include the immersion Marshall test, freeze-thaw splitting test, asphalt pavement analyzer immersion rutting test, boiling method, immersion compression method, and so on [21]. The water stability of the asphalt concrete was tested by the immersion Marshall test and freeze-thaw splitting test. The sample size was a standard Marshall specimen with a height of 63.5 mm and a diameter of 101 mm. To ensure the accuracy of the test, four specimens from each group were selected for the test.
(2) Bending Test
Current methods for evaluating the low temperature performance of asphalt concrete include the low temperature direct tensile test, low temperature bending test, low temperature bending tensile creep test, and temperature stress test of confined specimens. To test the low temperature performance of the asphalt mixture, the mechanical properties of bending failure of asphalt concrete at a specified temperature and loading rate were determined by the low temperature bending test. The sample size was a 250 mm × 30 mm × 35 mm beam.
(3) Rutting Test
The rutting test machine was used to conduct the rutting test in accordance with the requirements of the specification to evaluate the asphalt mixture’s high temperature anti-rutting performance. The detected rutting deformation was used to determine the dynamic stability, which is a measure of the asphalt mixture’s high temperature stability. The sample was 300 mm × 300 mm × 50 mm in size. Through experimental study, Guo et al. [22] discovered that temperature has a significant impact on the high temperature stability of asphalt mixtures, and that temperature should be closely regulated in experimental operations.
2.3.3 Melting Snow and Ice Test
After the asphalt mixture was stirred according to the specification requirements, the sample was prepared in a mold with a size of 30 cm × 30 cm × 10 cm. The lower layer was plain asphalt concrete (without CF and SiC, 5 cm), and the upper layer was thermally conductive asphalt concrete (with CF and SiC, 5 cm) or plain asphalt concrete. A carbon fiber heating cable was then placed at the bottom of the upper layer of asphalt concrete. At the initial conditions of ambient temperature of −5°C, no solar radiation, and no wind, in the low temperature test chamber, the initial ice thickness was 30 mm. During the snow melting process, the carbon fiber heating cable was connected to a 220 V power supply and five K-type thermocouples were placed at equal intervals on the sample surface to record the temperature changes during the snow melting and ice melting process. Changes in the ice thickness were recorded in real-time with a video camera. The snow-melting and icing specimens are shown in Fig. 4.
Figure 4: Schematic of the ice/snow melting test
3.1 Thermal Conductivity of the TCAC
Due to the use of different thermally conductive fillers, the overall structure of the resulting concrete can be affected to varying degrees, and the thermal conductivity can also be changed due to the method of mixing of the asphalt concrete. The increase in thermal conductivity serves to reduce the loss of heat in the heat transfer process. Under the condition of oil-stone ratio of 4.75%, the test results of the thermal conductivity of the Marshall specimens made with different contents of thermally conductive filler are presented in Table 5.
When the Marshall specimen was made with only CF as the thermal conductive filler, the resulting variation of the thermal conductivity is represented by the point line diagram shown in Fig. 5.
Figure 5: Thermal conductivity of CF as filler
When CF was incorporated into asphalt concrete as a thermally conductive filler, the thermal conductivity of the test block was markedly increased, and the thermal conductivity increased with the increase of CF content. When the CF content increased from 0.1% to 0.5%, the thermal conductivity of the test block increased from 0.906 to 1.117 W/(m·K). Compared with OAC without thermal conductive filler, the increase in thermal conductivity ranged from 9.58% to 30.7%. It showed that the incorporation of CF can greatly improve the thermal conductivity of the test block. The main reason was that CF has excellent thermal conductivity. After being incorporated into asphalt concrete, CF filaments remained in contact each other, thus forming a complete thermally conductive network and path on the inside, thereby improving the thermal conductivity of the test block.
The increase in rate of thermal conductivity was the fastest when the CF content ranged from 0% to 0.2%. With the further increase of CF content, the increase in rate of thermal conductivity slowed down when the CF content ranged from 0.2% to 0.4%. Finally, when the content of CF was 0.4% to 0.5%, the increase in rate of thermal conductivity was the slowest. When the CF content was from 0% to 0.5%, the thermal conductivity increased by 0.079, 0.087, 0.039, 0.032, and 0.017 W/(m·K), respectively, representing an increase of 9.58%, 9.63%, 3.92%, 3.14% and 1.57%, respectively. This indicated that the addition of an appropriate amount of CF effectively improved the thermal conductivity of asphalt concrete, and when the CF content exceeded 0.4% of the aggregate mass, the thermal conductivity of asphalt concrete was not further improved.
3.1.2 Effect of Different Content of CF in Combination with SiC
Previous studies [23] have shown that a single thermal conductive filler can improve the thermal conductivity of asphalt concrete pavement by adjusting the content and mix ratio. However, many problems were also reported, such as the need for a large quantity of thermally conductive filler, low thermal conductivity, insufficient long-term effect, negative impact on road performance, etc. These problems have hindered the promotion and use of thermally conductive asphalt concrete. Therefore, on the basis of CF thermal conductive asphalt concrete, a thermally conductive asphalt concrete with CF-SiC two-phase composite thermal conductive filler was prepared by replacing the slag powder with SiC micropowder with better heat transfer characteristics that could potentially improve the thermal conductivity of the concrete. The results of the thermal conductivity tests are shown in Fig. 6.
Figure 6: Thermal conductivity of CF-SiC composite asphalt concrete
When SiC powder was used in combination with CF as the thermally conductive filler and mixed to make Marshall specimens, the thermal conductivity first increased and then decreased with the increase of CF content. As is evident when comparing Figs. 5 and 6, when the SiC powder replaced the mineral powder and the CF content was 0.1%–0.4%, the thermal conductivity at the same CF content was higher than that of the Marshall specimen made of CF alone. This indicated that using SiC powder in place of mineral powder to make asphalt concrete improved the thermal conductivity of the test block. When the mass of SiC was 100% and the CF content was 0.2%, the highest thermal conductivity of 1.368 W/(m·K) was obtained. The thermal conductivity rose by 65.4% when compared to OAC. With the further increase of CF content, the thermal conductivity began to decline. This indicated that while the addition of an appropriate amount of CF markedly improved the thermal conductivity of the test block, however, the addition of excessive CF reduced the thermal conductivity of the asphalt concrete. The reason for this phenomenon was that the adsorption of free asphalt by SiC micropowder was stronger than that of limestone powder. When SiC micropowder replaced mineral powder, a part of free asphalt was adsorbed, and an appropriate amount of CF also adsorbed a part of free asphalt to make it denser in the condensation process. This effectively maintained the thermal conductivity path and improved the thermal conductivity of asphalt concrete, while, the continued addition of CF led to the excessive adsorption of free asphalt, resulting in an increase in the internal porosity of asphalt concrete, and with the voids not being conducive to the effective propagation of heat in asphalt concrete, resulted in a decrease in thermal conductivity. Compared with OAC, the thermal conductivities of single-doped CF, and CF-SiC composite had different degrees of improvement. However, the thermally conductive filler in the ratio of the A9 group showed the highest increase in thermal conductivity.
3.2 Engineering Performance of Asphalt Mixture
The A3 and A9 groups which gave the highest thermal conductivity among the single thermally conductive filler groups and two-phase composite thermally conductive filler groups, respectively, were selected for the test of the engineering performance of asphalt concrete, considering the influence of actual thermal conductivity. The OAC of A1 group was used as the control for the test.
3.2.1 Water Stability of Asphalt Concrete
The Marshall specimen was made by the Marshall compactor, and the immersion Marshall test and freeze-thaw splitting test were carried out. The immersion residual stability and freeze-thaw splitting strength obtained from the test results are shown in Fig. 7.
Figure 7: Water stability of different asphalt concretes
Compared with OAC, the immersion residual stability of the asphalt mixture was improved whether CF or CF-SiC was used as the thermally conductive filler, with the latter yielding a more marked improvement. The main reason was that the CF was dispersed in the concrete to form a network structure, which not only improved the crack resistance of the asphalt concrete, but also facilitated overall stability. Further, because the hardness of SiC powder was stronger than that of the limestone powder which it replaced, the stability of the asphalt mixture was further enhanced.
The specification recommended that the freeze-thaw splitting strength ratio of asphalt concrete with gradation AC-13 should not be less than 80% to avoid moisture damage [20]. The results showed that when CF was added to asphalt concrete as the thermally conductive filler, the freeze-thaw splitting strength ratio decreased with the addition of CF. While the freeze-thaw splitting strength ratio of OAC was 96.5%, after adding CF alone, the freeze-thaw splitting strength ratio decreased to 92.3%. When CF-SiC composite was used as the thermally conductive filler, the freeze-thaw splitting strength ratio was 93.5%. Although this was still lower than that of OAC, it was higher than that of single CF. The reason may be that under the freeze-thaw cycle, water expands during the process of freezing, causing voids inside, resulting in a decrease in the freeze-thaw splitting strength ratio. As the particle size of the SiC powder was smaller than that of limestone powder, it better filled the gap generated in the interior, and the freeze-thaw splitting strength was improved compared with that of single-doped CF. Therefore, the use of a CF-SiC two-phase composite thermally conductive filler could retain the water stability of asphalt concrete.
3.2.2 Low-Temperature Crack Resistance of Asphalt Concrete
Three groups of rutting plate specimens were made by a rutting forming instrument. After cooling and forming, they were cut into trabecular specimens for the low-temperature crack resistance test. The test results are shown in Fig. 8.
Figure 8: Low-temperature stability of different asphalt concretes
With the addition of CF, the low-temperature cracking performance of asphalt concrete was obviously enhanced, indicating that the asphalt mixture prepared by adding CF had better bond strength and could withstand greater strain than OAC. This showed that in the same environment, the addition of CF can significantly improve the crack resistance of asphalt concrete. The CF dispersed in the asphalt mixture was similar to the role of steel bars in cement concrete, which can enhance the deformation resistance and tensile strength of the mixture. With the replacement of limestone powder by SiC powder, the mixing stiffness modulus of asphalt mixture had a stronger performance. The reason was that on the one hand, the surface of the CF was rough, which could not only adsorb effective asphalt, but also had higher friction and better interlocking effect, such that the stress dispersion was more uniform. On the other hand, SiC micropowder, as a material with a large specific surface area, could adsorb effective asphalt and excessive asphalt at the same time with CF, enhancing the adhesion between asphalt and aggregate. Therefore, both filler types improved the low-temperature crack resistance of the asphalt mixture.
3.2.3 High-Temperature Stability of Asphalt Concrete
The dynamic stability of the specimens was tested by a rutting test machine, and the high-temperature stability of TCAC was evaluated using this data. The test results are shown in Fig. 9.
Figure 9: High-temperature stability of different asphalt concretes
Compared with OAC, single-doped CF and CF-SiC two-phase composites as thermally conductive fillers had a marked effect on the dynamic stability of the asphalt mixtures, and the dynamic stability showed a downward trend. The dynamic stability of the two groups fell by 10.8% and 19.7%, respectively, when compared with the blank control group. This was because before the wheel tracking test, the asphalt mixture was kept at an ambient temperature of 60°C for a period. Because the thermal conductivities of CF and SiC were much higher than that of aggregate and limestone powder, CF was heated first, then the heat was transferred to SiC through asphalt, and finally the basalt aggregate began to heat. The heat gradually accumulated over time, and the temperature difference between CF, SiC, and basalt gradually decreased until the temperature was stable. Compared with OAC without thermally conductive filler and TCAC with CF alone, the asphalt mixture made of CF-SiC two-phase composite thermal conductive filler had the fastest heat transfer, took a shorter time to reach constant temperature, and thus rutting was more likely to occur, resulting in lower dynamic stability. However, it still met the requirements of the specification for the rutting resistance of AC-13 asphalt concrete.
In summary, when the A9 group mixture was used as the thermally conductive filler, the thermal conductivity of asphalt concrete was the best, and its engineering performance was better than that of OAC and single-doped CF as thermally conductive filler, and met the requirements of the specification. Therefore, when studying the thermal conductivity of asphalt concrete and conducting snow melting and ice melting tests, it is recommended that the A9 group mix ratio be used as the thermally conductive filler to make TCAC.
3.3 Thermal Conductivity of Asphalt Concrete
Whether it has excellent work efficiency is an important basis for the application of TCAC to practical engineering. This meant that the road surface temperature be raised above the ice melting temperature in the shortest possible time. Therefore, the heating rate and horizontal temperature distribution of TCAC were studied in a low-temperature laboratory.
3.3.1 Temperature Rise Characteristics of Asphalt Concrete
The temperature rise test was carried out in a low-temperature laboratory, and the carbon fiber heating cable was energized and heated for 6 h at ambient temperatures of 0°C, −5°C, and −10°C, respectively. The temperature change was recorded by a temperature sensor arranged in the center of the specimen (Fig. 4). The temperature-time curves of TCAC and OAC during heating are shown in Fig. 10.
Figure 10: Time-temperature curves of asphalt mixes during heating at different ambient temperatures
In the temperature rise test at three different ambient temperatures, the trend of changes in the surface temperatures of asphalt concretes was that temperature first increased, and then stabilized. When the ambient temperature was 0°C, the temperature of the TCAC increased to 17.7°C in the first 180 min with a near linear change trend. After 180 min, the temperature of the asphalt concrete began to increase at a slow rate, and the temperature stabilized at about 22°C at 300 min. The heating rates of TCAC and OAC at different ambient temperatures are presented in Table 6. In the early stage of heating, the ambient temperature was negatively correlated with the heating rate of asphalt concrete. This was because some of the heat transferred to the road surface was convectively exchanged with the surrounding air. As the ambient temperature decreased, the energy loss increased and the heating rate decreased. When the thermal gain of the asphalt concrete surface and the heat loss caused by convection began to balance out, the temperature began to stabilize. The stable temperature was positively correlated with the ambient temperature. This was because the lower the ambient temperature, the more the heat being transferred to the asphalt concrete surface needed to overcome the heat loss caused by convection, resulting in a lower temperature after stabilization. At the three different ambient temperatures, the heating rate of TCAC increased in comparison with OAC by 62.5%, 68.8%, and 140%, respectively, when it reached 3°C. The thermally conductive specimen showed a higher surface temperature than the control specimen, indicating that the TCAC was more efficient/faster in transferring the heat generated by the carbon fiber heating cable to the pavement surface.
3.3.2 TCAC Surface Temperature Distribution Characteristics
The temperature distribution in the horizontal direction plays a vital role in the application of snow melting and ice melting pavement in practical engineering, which means that not only the heat generated by the carbon fiber heating cable should be transferred to the surface layer of the pavement in the shortest possible heating time, but also the uniformity of the temperature distribution should be satisfied to achieve the effect of effectively removing ice and snow from driving surfaces. The TCAC surface was heated for 6 h at different ambient temperatures and Fig. 11 shows the temperature-time curve of the asphalt concrete surface during the heating process.
Figure 11: Time-temperature curves of TCAC surface at different ambient temperatures
The results showed that the surface temperature of the specimen was positively correlated with the ambient temperature. Among them, the temperatures of No. 2, No. 3 and No. 4 temperature measurement points were similar. The temperature of No. 3 temperature measurement point located in the center of the specimen was the highest, and the temperatures of No. 1 and No. 5 temperature measurement points located at the edges were similar, and slightly lower than the temperature at the center. This was because the temperature superposition effect caused the surface temperature of the No. 3 temperature measurement point to be slightly higher than the nearby points and yield the highest surface temperature. Using the data obtained from the location of the temperature measurement line, it was proved that SiC powder and CF had good distribution uniformity in the asphalt mixture. When the temperature was stable, even in the-10°C environment, the minimum temperature recorded on the TCAC surface edge was still 3.59°C, which met the temperature required for snow/ice melting. This indicated that using CF-SiC two-phase composite as a thermally conductive filler had a positive effect on the surface temperature distribution of the mixture, and the temperature distribution on the surface of TCAC could achieve the purpose of melting snow and ice. It must be noted that the two-phase composite of SiC micropowder and CF with 0.2% of aggregate mass as thermal conductive filler was used to make TCAC.
After the field snow and ice melting test, the changes in the respective ice layer between TCAC and OAC during the experiment are shown in Fig. 12. The ice layer images covered on the surface of the specimen under different heating time were processed, and the area was quantified to provide the ice melting law of each asphalt concrete more accurately, to verify the reliability of the test conditions. The area of the remaining ice layer was plotted in the form of a histogram, as shown in Fig. 13. Under the same working conditions, there was an obvious difference in the ice change on the surface of both asphalt concretes. The ice melting efficiency of TCAC was superior to that of the OAC. In the first 80 min, there was almost no change in the ice layer on the surface of the OAC specimens, while in contrast, a dark area on the surface of the TCAC had begun to appear due to the melting of the ice layer. With the passage of time, as the surface temperature of the asphalt mixtures reached the melting temperature of ice, the melting speed of the ice layer was significantly accelerated, and the size of the dark colored area gradually increased on both specimens. First, the ice layer at the vertical edge of the specimen and the carbon fiber heating cable melted, followed by the ice layer directly above the carbon fiber heating cable. Because the ice layer above the temperature measurement line was not in direct contact with the surface of the specimen, the ice layer above the K-type thermocouple finally melted. After heating for 180 min, the ice layer on the TCAC specimen was almost completely melted, while there was still some residual ice layer above the control OAC specimen.
Figure 12: Ice layer changes during ice melting test of TCAC (a–d) and OAC (e–h)
Figure 13: Changes in the ice layer area on different asphalt concrete specimens over a period of heating
During the heating of the ice layer, the K-type thermocouple recorded the surface temperature of the asphalt concrete, and the results are shown in Fig. 14. Before heating, 56–88 min, the surface temperature of the asphalt concrete specimens was linear with the heating time of the carbon fiber heating cable. The surface temperature of the specimens increased at a nearly constant rate, and the heating rates of the TCAC and OAC were about 0.13°C/min and 0.094°C/min, respectively. When the surface temperatures of the asphalt concretes reached 2°C–3°C, a temperature platform appeared. When the ice layer was completely melted, the surface temperatures of the asphalt concretes began to rise again, and the heating rate of the TCAC was better than that of the OAC. The ice melting times of the two specimens were 188 min and 243 min, respectively. Compared with the control group, the ice melting time of the TCAC specimen was shorter by 55 min, and the ice melting efficiency was increased by 29.3%. This confirmed that in practical application, the ice melting efficiency of asphalt concrete made of CF-SiC two-phase composite thermal conductive filler was markedly improved.
Figure 14: Asphalt concrete surface temperature during ice melting
In this study, the feasibility of using SiC powder, instead of mineral powder, and CF in a two-phase composite as a thermal conductive filler in asphalt concrete was assessed. The optimal CF content for compounding with SiC micronized powder was determined based on thermal conductivity and engineering properties, and was further determined to be of practical engineering significance through the study of temperature rise characteristics and surface temperature changes. Then, the heating characteristics and surface temperature were studied to determine its practical engineering significance. Finally, the ice melting process was studied using an electric heating system for verification. The conclusions are summarized as follows:
(1) TPS is an effective method to test the thermal conductivity of asphalt mixes. With SiC micronized powder replacing mineral powder, the thermal conductivity of asphalt concrete increased and then decreased with the increase of CF admixture. When the CF content was 0.2% of the aggregate mass, the thermal conductivity reached a peak of 1.368 W/(m·K), which was 65.4% higher than that of ordinary asphalt concrete.
(2) The TCAC made of single-doped CF and CF-SiC two-phase composites can meet the engineering performance requirements of standard specifications. TCAC made of CF-SiC two-phase composite have better residual stability and low-temperature stability than TCAC and OAC made of single doped CF. The freeze-thaw splitting strength and high temperature stability of TCAC made of CF-SiC two-phase composite was slightly lower than that of OAC. Considering its good thermal conductivity and its ability to meet the requirements of standard specifications, it is recommended to use SiC micron powder instead of mineral powder and aggregate mass 0.2% CF two-phase composite as the thermally conductive filler in making TCAC.
(3) The threshold temperature of TCAC made of CF-SiC two-phase composite as thermal conductive filler was much higher than that of OAC, and the surface temperature in the horizontal direction reached the temperature required for melting snow and ice.
(4) The ice/snow melting efficiency of TCAC in an electric heating pavement system was analyzed. The electrothermal ice melting time of the TCAC specimen was shortened by 55 min, and the snow melting efficiency was increased by 29.3%.
Acknowledgement: We would like to express our heartfelt thanks to Mr. Yang Zhiyong, Mr. Xi Lei and Mr. Chen Zhi. We would like to express our heartfelt gratitude to the three teachers for their great help and support in completing this research paper. In addition, we would like to thank the academic staff and experts who provided feedback on their work and constructive comments for this study. This study would not have been possible without their assistance.
Funding Statement: The authors acknowledge the support of the Joint Funds of the Natural Science Foundation of Hubei Province (2022CFD130), the Technology Innovation Project of Hubei Province (Key Program, No. 2023BEB010), the Key Research and Development Program of Hubei Province (No. 2021BGD015), the Knowledge Innovation Project of Wuhan (No. 2022010801010259).
Author Contributions: The authors confirm contribution to the paper as follows: study conception and design: Zhiyong Yang, Enjie Hu, Lei Xi; data collection: Feng Xiong, Chuanhai Zhan; analysis and interpretation of results: Zhiyong Yang, Enjie Hu; draft manuscript preparation: Zhiyong Yang, Enjie Hu, Zhi Chen. All authors reviewed the results and approved the final version of the manuscript.
Availability of Data and Materials: The datasets generated during and/or analyzed during the current study are available from the corresponding author on reasonable request.
Conflicts of Interest: The authors declared that they had no conflicts of interest to report regarding the present study.
References
1. Slebi-Acevedo, C. J., Lastra-Gonzalez, P., Pascual-Munoz, P., Castro-Fresno, D. (2019). Mechanical performance of fibers in hot mix asphalt: A review. Construction and Building Materials, 200, 756–769. [Google Scholar]
2. Medina, V. A. (2013). Review on China’s road engineering research: 2013. China Journal of Highway and Transport, 26(3), 1–36. [Google Scholar]
3. Rao, R., Fu, J., Chan, Y., Tuan, C. Y., Liu, C. (2018). Steel fiber confined graphite concrete for pavement deicing. Composites Part B: Engineering, 155, 187–196. [Google Scholar]
4. Han, S., Wei, H., Jiang, B., Wang, H., Chen, J. (2023). Numerical and outdoor experimental study on active snow melting of conductive rubber composites in roads. Road Materials and Pavement Design, 24(7), 1748–1764. [Google Scholar]
5. Notani, M. A., Arabzadeh, A., Ceylan, H., Kim, S., Gopalakrishnan, K. (2019). Effect of carbon-fiber properties on volumetrics and ohmic heating of electrically conductive asphalt concrete. Journal of Materials in Civil Engineering, 31(9), 04019200.1–04019200.9. [Google Scholar]
6. Xie, X. M., Su, J. F., Guo, Y. D., Wang, L. Q. (2020). Evaluation of a cleaner de-icing production of bituminous material blending with graphene by electrothermal energy conversion. Journal of Cleaner Production, 274, 1–9. [Google Scholar]
7. Wang, X., Zhu, Y., Zhu, M., Zhu, Y., Fan, H. et al. (2017). Thermal analysis and optimization of an ice and snow melting system using geothermy by super-long flexible heat pipes. Applied Thermal Engineering, 112, 1353–1363. [Google Scholar]
8. Ozsoy, A., Yildirim, R. (2016). Prevention of icing with ground source heat pipe: A theoretical analysis for turkey’s climatic conditions. Cold Regions Ence and Technology, 125, 65–71. [Google Scholar]
9. Ullah, S., Yang, C., Cao, L., Wang, P., Zhang, B. (2021). Material design and performance improvement of conductive asphalt concrete incorporating carbon fiber and iron tailings. Construction and Building Materials, 303(6), 1–13. [Google Scholar]
10. Kim, H. S., Ban, H., Park, W. J. (2020). Deicing concrete pavements and roads with carbon nanotubes (CNTs) as heating elements. Materials, 13(11), 1–24. [Google Scholar]
11. Alireza, S., Ali, A., Halil, C., Sunghwan, K., Sajed, S. S. M. et al. (2018). Carbon fiber-based electrically conductive concrete for salt-free deicing of pavements. Journal of Cleaner Production, 203, 799–809. [Google Scholar]
12. Woo, B. H., Yoo, D. H., Kim, S. S., Lee, J. B., Ryou, J. S. et al. (2021). Effects of thermal conductive materials on the freeze-thaw resistance of concrete. Materials, 14, 1–15. [Google Scholar]
13. Jiao, W., Sha, A., Liu, Z., Jiang, W., Li, X. (2020). Utilization of steel slags to produce thermal conductive asphalt concretes for snow melting pavements. Journal of Cleaner Production, 261, 121–136. [Google Scholar]
14. Chen, J., Zhang, M., Wang, H., Li, L. (2015). Evaluation of thermal conductivity of asphalt concrete with heterogeneous microstructure. Applied Thermal Engineering, 84, 368–374. [Google Scholar]
15. Wang, S., Shi, Q., Du, Y. (2015). Bidirectional heat induced structure of asphalt pavement for reducing pavement temperature. Applied Thermal Engineering: Design, Processes, Equipment, Economics, 75, 298–306. [Google Scholar]
16. Gulisano, F., Gallego, J. (2021). Microwave heating of asphalt paving materials: Principles, current status and next steps. Construction and Building Materials, 278(3), 1–12. [Google Scholar]
17. Arai, K. (2007). Aspects and prospects of sic R&D in Japan. IEICE Technical Report Electron Devices, 107, 169–172. [Google Scholar]
18. Ministry of Transport of the People’s Republic of China (2017). JTG D50-2017, Specifications for Design of Highway Asphalt Pavement. Beijing, China: People’s Transportation Press. [Google Scholar]
19. Stempihar, J. J., Pourshams-Manzouri, T., Kaloush, K. E., Rodezno, M. C. (2012). Porous asphalt pavement temperature effects for urban heat island analysis. Transportation Research Record: Journal of the Transportation Research Board, 2293(1), 123–130. [Google Scholar]
20. Ministry of Transport of the People’s Republic of China (2011). JTG E20-2011, Standard Test Methods of Bitumen and Bituminous Mixtures for Highway Engineering. Beijing, China: People’s Transportation Press. [Google Scholar]
21. Yin, F., Arambula, E., Lytton, R., Martin, A. E., Cucalon, L. G. (2014). Novel method for moisture susceptibility and rutting evaluation using hamburg wheel tracking test. Transportation Research Record Journal of the Transportation Research Board, 2446(1), 1–7. [Google Scholar]
22. Guo, R., Feng, Z., Li, P., Hong, G., Ding, H. (2013). Experimental analysis of influence factors on anti-rutting property of sma mixture. Journal of Guangxi University, 38(1), 55–61. [Google Scholar]
23. Karimi, M., Amani, S., Jahanbakhsh, S., Jahangiri, B., Alavi, A. (2021). Induced heating-healing of conductive asphalt concrete as a sustainable repairing technique: A review-sciencedirect. Cleaner Engineering and Technology, 4, 1–25. [Google Scholar]
Cite This Article
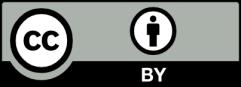
This work is licensed under a Creative Commons Attribution 4.0 International License , which permits unrestricted use, distribution, and reproduction in any medium, provided the original work is properly cited.