Open Access
ARTICLE
On the Preparation of Low-Temperature-Rise and Low-Shrinkage Concrete Based on Phosphorus Slag
China Construction Ready Mixed Concrete Co., Ltd., Wuhan, 430000, China
* Corresponding Author: Peng Zeng. Email:
(This article belongs to the Special Issue: Advances in Solid Waste Processing and Recycling Technologies for Civil Engineering Materials)
Fluid Dynamics & Materials Processing 2024, 20(4), 803-814. https://doi.org/10.32604/fdmp.2023.027311
Received 24 October 2022; Accepted 20 February 2023; Issue published 28 March 2024
Abstract
The effects of different contents of a MgO expansive agent and phosphorus slag on the mechanical properties, shrinkage behavior, and the heat of hydration of concrete were studied. The slump flow, setting time, dry shrinkage, and hydration heat were used as sensitive parameters to assess the response of the considered specimens. As shown by the results, in general, with an increase in the phosphorus slag content, the hydration heat of concrete decreases for all ages, but the early strength displays a downward trend and the dry shrinkage rate increases. The 90-d strength and dry shrinkage of concrete could be improved with a phosphorus residue content between 0%–20%, with the best performances in terms of mechanical properties and shrinkage characteristics being achieved for a content of 20 kg/m3. On the basis of these results, it can be concluded that appropriate amounts of phosphorus slag and MgO expansive agent can be used to improve the compressive strength of concrete in the later stage by reducing the hydration heat and dry shrinkage rate, respectively.Graphic Abstract
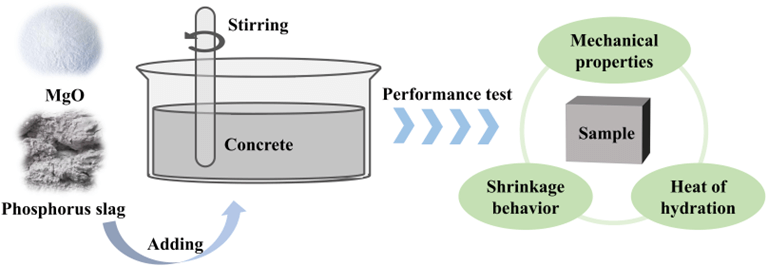
Keywords
In recent years, with the continuous development of infrastructure and water conservancy and hydropower facilities, the source of fly ash has become difficult to guarantee. At the same time, the regional lack of fly ash resources and long-distance transportation of uneconomical problems have become increasingly prominent. Inferior fly ash even appeared in the market. Phosphorus slag is the by-product of yellow phosphor production. The annual output of phosphorus slag is 0.81 million tons, and the main treatment method is stacking method with a low utilization rate [1]. Studies have shown that [2] the ground phosphorus slag powder has high activity and the secondary hydration reaction is relatively complete. It can be used as a mineral admixture, which has similar characteristics to fly ash, increasing the number of concrete cementing products, refines the pore size, reducing the porosity, improving the strength of cement paste, and improving the structure of the concrete interface transition zone. Allahverdi et al. [3] found that adding phosphorus slag to concrete can improve the matrix’s density and reduce the power and hydration heat of the concrete. Chang et al. [4] studied the application of phosphorus slag powder in hydraulic concrete. The results show that the incorporation of phosphorus slag powder can effectively prevent stress cracks caused by excessive temperature rise in large-volume hydraulic concrete, which is conducive to the development of tensile and compressive mechanical properties and the durability of concrete. The early strength of phosphorus slag concrete is low, but the later strength of concrete with phosphorus slag content between 15% and 30% is close to or even better than that of ordinary fly ash concrete. Qi et al. [5] found that when the content of phosphorus slag reached 50%, the 28 d strength of concrete was about 15% lower than that of ordinary concrete.
A large number of studies have shown that [6,7] phosphorus slag powder has a certain retarding effect, which can effectively delay the hydration process of cement, thereby reducing the hydration heat release rate of cementitious materials. At present, there are three main explanations for the retarding mechanism of phosphorus slag powder: (1) The soluble phosphorus and fluorine in the phosphorus slag are combined with Ca2+ to form soluble P and F, covering the surface of cement particles and delaying the hydration of cement. (2) P2O5 in phosphorus slag has a certain retarding effect, so that the hydration of C3A stays in the ‘hexagonal hydration product’ layer stage, resulting in neither AFt nor C3AH3 formation. (3) The semi-permeable hydration product membrane formed in the early hydration stage of Portland cement has a certain adsorption effect on the phosphorus slag particles, which increases the membrane’s compactness, reduces the passing rate of ions and water molecules, and delays the hydration process. Due to the slow hydration rate of phosphorus slag and large water demand, the early water evaporation of phosphorus slag concrete is large, and the early drying shrinkage rate is greater than that of ordinary concrete. Li et al. [8] studied the effect of phosphorus slag on the shrinkage performance of concrete. The results show that the shrinkage rate of concrete mixed with phosphorus slag will increase in the early stage, and the shrinkage rate will gradually approach that of the reference concrete in the later stage. Studies have also shown that the shrinkage of phosphorus slag powder concrete in the early and late stages is consistently larger than that of the reference concrete.
To solve the problem of the large early drying shrinkage rate of phosphorus slag concrete, the method of adding MgO can be considered. MgO has controlled delayed micro-expansion characteristics [9,10]. MgO is added to bulk concrete to compensate for the volume shrinkage generated during the temperature drop process through controlled autogenous volume expansion, thereby inhibiting the generation of temperature cracks in the dam and breaking through traditional temperature control measures [11,12]. At present, there are many types of research on the application of phosphorus slag in concrete, but there are few on the combination of phosphorus slag and MgO, which are basically in the state of indoor experimental research. Therefore, this paper is to study the effect of phosphorus slag powder instead of fly ash on the working performance, mechanical properties, drying shrinkage characteristics, and hydration heat of concrete, explore the influence of MgO on the autogenous volume deformation and mechanical properties of phosphorus slag concrete and comprehensively analyze the mechanism of the influence of phosphorus slag and MgO on the performance of concrete.
The cement is an ordinary Portland cement conforming to 42.5, the main performance indexes are listed in Table 1 and the chemical composition analysis is listed in Table 2. The X-ray diffraction (XRD) and particle size distribution (PSD) of cement are shown in Figs. 1 and 2, respectively.
Figure 1: XRD analysis of cement
Figure 2: PSD analysis of cement
Phosphorus slag is produced by Shimian Kangrui New Material Co., Ltd. (China), the chemical composition of phosphorus slag is listed in Table 3, and the XRD, PSD, and Microstructure of phosphorus slag are shown in Figs. 3–5, respectively.
Figure 3: XRD pattern of phosphorus slag
Figure 4: PSD of phosphorus slag
Figure 5: Microstructure of phosphorus slag
The hydraulic activity was evaluated by the mass coefficient K through the chemical composition of phosphorus slag. The mass coefficient K is the ratio of CaO, MgO, and Al2O3 content to SiO2 and P2O5 content in the composition. The larger the ratio, the higher the activity of phosphorus slag powder. The mass coefficient K of phosphorus slag powder used in this paper is 1.21 > 1.10.
Fig. 3 shows the XRD pattern of phosphorus slag powder. The characteristic peaks of the minerals in the phosphorus slag are not obvious, and there is no sharp crystal mineral peak, but there is a slight uplift at the diffraction angle 2θ of 25°~35°, which is characteristic of the glassy state. This shows that the phosphorus slag is mainly composed of a vitreous body, which is also the basis for the potential activity of phosphorus slag.
The physical activation method can further stimulate the activity of cement and mineral admixtures, further improving the material’s performance. The wet grinding process ground the phosphorus slag to a certain fineness, and its particle size distribution is shown in Fig. 4. The particle size range of ground phosphorus slag is 0.09–120 μm and the average particle size is 12.4 μm, D v (10) = 2.7 μm.
The phosphorus slag selected in this paper is granular after water quenching. The research shows that only the phosphorus slag after quenching has a vitreous structure, and will be active, and the phosphorus slag after natural cooling will be massive and hard. Fig. 5 shows the microstructure of phosphorus slag powder. The phosphorus slag powder is composed of irregular particles of several microns to tens of microns, with different sizes and smooth surfaces. The phosphorus slag powder exhibits a dense structure of the skeleton in the grain size composition. There are both a certain number of large-sized particles and a sufficient number of small-sized particles in the whole structure. The materials with this particle size distribution favor dense packing systems when used as admixtures. This system structure favors overall strength and stability.
Class II fly ash source from Wuhan Yangluo Thermal Power Station (China). The main indexes and chemical composition are listed in Tables 4 and 5.
Manufactured sand is processed from broken pebbles and coarse aggregate between 5–31.5 mm continuous graded crushed stone, the main indexes are listed in Table 6.
MgO Expansive Agent is produced by Wuhan Sanyuan Special Building Materials Co., Ltd. (China). The main indexes are listed in Table 7.
Coarse aggregate adopts continuous graded crushed stone with a 5–31.5 mm particle size.
Water reducer is a polycarboxylate superplasticizer (PCA-1) produced by Subote New Materials Co., Ltd., China, the water reduction rate can reach 30%.
In this paper, when studying the influence of phosphorus slag content on the properties of concrete, eight groups of test proportions are adopted (G-1~G-8), the amount of cementitious material is controlled to 410 kg/m3, and phosphorus slag is used to replace part of cement in the concrete cementitious material. When studying the influence of MgO expansive agent content on the properties of concrete, four different contents are set to replace phosphorus slag (G-9~G-12). The specific mix proportion is listed in Table 8.
2.3.1 Test of Slump Flow and Setting Time
The Slump Flow and Setting Time Test of the concrete mixture are referred to GB/T 50080-2016, where the flow performance is measured by a slump meter, and the slump meter should meet the requirements of JG/T248. The penetration resistance method is used to test the condensation time. The test equipment is a penetration resistance instrument. The maximum measurement value is 1000 N and the accuracy is 10 N. Finally, the initial setting time and final setting time are obtained by referring to the calculation method in GB/T 50080-2016.
The dry shrinkage test is conducted according to the ‘Standard for test methods of long-term performance and durability of ordinary concrete’, and the specimen size is 100 mm × 100 mm × 515 mm, with a probe embedded at both ends. The drying shrinkage experiment is used to test the shrinkage rate at different ages.
2.3.3 Test of Compressive Strength and Splitting Tensile Strength
The concrete samples for the test of Compressive Strength and Splitting Tensile Strength are cube specimens with a size of 150 mm, and the test equipment is a 2000 KN compressive testing machine. Cube specimens were tested for compressive strength and splitting tensile strength test according to GB/T50081-2019 at the ages of 3, 7, 28, 90 days. The reported results were the average of three concrete samples.
The hydration heat is analyzed by using an eight-channel TAM air microcalorimeter produced using the American TA instrument. The temperature fluctuation of the constant temperature device is controlled at ± 0.02°C. The measurement temperature ranges from 5°C to 90°C, and the accuracy is 10 μW. After the sample preparation is completed, water is added outside the device and stirred until the stirring is uniform and moved to the corresponding test channel. The whole test process is completed independently by the instrument. After the specified age, the sample is taken out and the test data is exported.
3.1 Effect of Phosphorus Slag on the Performance of Concrete
3.1.1 Effect of Phosphorus Slag on Mechanical Properties and Workability of Concrete
It can be seen from Fig. 6 that with the increase of phosphorus slag content, the slump and expansion of concrete gradually increase, and both the initial setting time and final setting time are prolonged. With the increase of phosphorus slag content, the working performance of concrete is improved. It can be seen from G-7 and C40-8 that when the content of fly ash and phosphorus slag is 43.4% of the total amount of cementitious materials, the expansion of the G-8 group with phosphorus slag is greater than that of the G-7 group with fly ash, and its water consumption is decreased by 5 kg/m3. On the one hand, the phosphorus slag contains a large amount of vitreous body with a low hygroscopic rate, which can be filled in the pores of the cement particles and the flocculation structure, occupying the water filling space between the particles, releasing the water in the flocculation structure, and increasing the fluidity of the concrete. On the other hand, the specific surface area of phosphorus slag is large, the water demand is less, and its apparent density is smaller than that of cement, increasing in both slurry volume and fluidity of the concrete [13–15]. From the change rule of setting time shown in Fig. 6, it can be seen that the setting time is prolonged with the increase of phosphorus slag content. This is mainly because the combined action of P2O5 and gypsum in phosphorus slag delays the hydration of C3A, and P2O5 and F- react with Ca(OH)2 in the cement slurry to form an insoluble protective film covering the surface of the particles and inhibiting hydration [16,17].
Figure 6: Workability of concrete
It can be seen from Fig. 7 that the compressive strength and splitting tensile strength of concrete for 90 d are greater than those of the G-1 group with 0% phosphorus slag, but the compressive strength for 7 d and 28 d are slightly lower. This is mainly due to the late hydration of the cementitious materials (90 d), the content of Ca(OH)2 in the cement slurry decreased, the vitreous body in the phosphorus slag continued to disintegrate, and the new C-S-H gel polymer intersected with the AFt grains, filling the blocked pores, making the structure of cement rock more compact [18,19]. When the content of phosphorus slag increases from 20% to 50%, the compressive strength and splitting tensile strength of concrete are significantly reduced at 7 d and 28 d. However, when the cementitious materials are hydrated to 90 d, the compressive strength of each group is relatively close. Compared with the G-7, the compressive strength for 7 d and 28 d in the G-8 were reduced by 3.8 and 6.4 MPa, respectively, but the compressive strength of the 90 d was 1.4 MPa higher. These indicate that although the incorporation of phosphorus slag hurts the early strength of concrete, the late strength of concrete incorporated with phosphorus slag is the same or even higher than that of plain concrete. It can be seen from the above tests that when the phosphorus slag content reaches 43.4%, its mechanical properties and working performance perform best.
Figure 7: Mechanical properties of concrete
3.1.2 Effect of Phosphorus Slag on Drying Shrinkage of Concrete
As Fig. 8 shows, the drying shrinkage values of Groups 2 and 3 concrete with a phosphorus slag content of 10% and 20% are lower than thoese of G-1 reference concrete with 0% phosphorus slag content. When the content of phosphorus slag increases from 10% to 50%, the drying shrinkage of concrete increases, especially in the early stage (28 d), the drying shrinkage growth rate of concrete increases with the increase of phosphorus slag content, but the drying shrinkage in the later stage is the same as in G-1. Compared with G-1, the drying shrinkage of concrete with 30%, 40% and 50% phosphorus slag increased by 9.5%, 13.4%, 26.2% for 28 days, and increased by 2.3%, 4.8% and 10.5% in the later period (90 d), respectively. This indicates that phosphorus slag will lead to an increase in early drying shrinkage of concrete, while a smaller increase in shrinkage in the later stage. According to G-7 and G-8, it can be seen that phosphorus slag leads to a significant increase in the early shrinkage of concrete, with a 46.9% increase in drying shrinkage at 28 d and a 21.1% increase in drying shrinkage at 360 d. When the phosphorus slag content is low (0%–20%), the drying shrinkage rate of concrete decreases. At this time, the proportion of cement in the cementitious materials is relatively large, the phosphorus slag mainly acts as a filling material, and the shrinkage of the concrete is mainly due to the reduction of the volume of the cementitious materials caused by the hydration of the cement. With the increase of phosphorus slag content, the hydration process slows down, the early water evaporation of phosphorus slag concrete increases, and the early drying shrinkage rate increases.
Figure 8: Effect of phosphorus slag content on drying shrinkage of concrete
3.1.3 Effect of Phosphorus Slag on Hydration Exothermic of Cementitious System
As can be seen from Fig. 9, when the content of phosphorus slag increases from 0% to 50%, there is a large gap between the heat release rate and the heat output. When the content of phosphorus slag increased from 0% to 20%, the time of temperature peak was delayed by 0.7 h, and the heat release rate and total heat output both decreased. When the content of phosphorus slag increases to 30%, the heat release of the cement paste decreases significantly by 27.56% compared with the blank group at 3 days, and the time of the temperature peak is delayed by 2.83 h. This is mainly because the phosphorus slag has a great retarding effect on the cementitious slurry, which leads to the delay of the hydration process of the slurry and the prolongation of the time of the exothermic peak. At the same time, the content of cement clinker in the slurry is relatively reduced, leading to a decrease in the total amount of hydration heat. Moreover, the incorporation of an appropriate amount of phosphorus slag into bulk concrete can reduce the total amount of hydration heat of concrete, delay the time of the temperature peak, and thus reduce the cracking risk of bulk concrete due to excessive temperature difference between the inside and outside [20].
Figure 9: Effect of phosphorus slag on hydration heat release rate and heat output
3.2 Effect of MgO Expansive Agent on the Performance of Mass Concrete
The calcination temperature and holding time of the MgO expansive agent have a great influence on its activity. The lattice size of MgO decreases with the increase in calcination temperature, the lattice distortion decreases, the density of MgO grains increases, and the hydration activity decreases. The longer the holding time, the longer the recrystallized MgO crystals grow at high temperatures, the higher the density of the crystals, and the longer the expansion time [21,22]. From Fig. 10, it is clear that with the increase of MgO expansion agent content, the compressive strength of concrete increases first and then reduces slightly. When the content of the MgO expansion agent is 20 kg/m3, the compressive strength of concrete at 28 d and 90 d is the largest. As the content increased to 25 kg/m3, the compressive strength of each age decreased slightly, suggesting that an appropriate amount of MgO expansive agent can promote the development of strength, but the excessive dosage may cause damage to the internal structure of concrete and have a negative effect on the development of strength [23]. The reason may be that a small amount of expansion agent hydrates to form Mg(OH)2, which fills in the pores and promotes the densification of the microstructure inside the concrete. Excess expansion agents can cause large expansion stresses inside, and induce micro-cracks in cementite under unconstrained conditions, resulting in decreased strength [24]. According to the drying shrinkage rate, when the concrete age reached 7 d, the drying shrinkage of each group of concrete was close. When the hydration continued to 28 d, the drying shrinkage of concrete gradually reduced with the increase of MgO expansion agent content. This indicates that when the hydration for 7 d, the hydration degree of MgO was very low. In early hydration, the cementitious material consumes more water. The diffusion of Mg2+ and the formation of Mg(OH)2 require water. Insufficient water will hinder the formation of crystal expansion pressure. At the same time, the addition of phosphorus slag will reduce the alkalinity of the pore water solution in the slurry and promote the diffusion of Mg2+. The resulting Mg(OH)2 crystal is relatively coarse and dispersed in a large area around the surface of MgO particles, with small expansion. Therefore, the activity of MgO is not high, and the drying shrinkage of concrete is not significantly reduced at 7 days. As the reaction proceeds, the water consumption of cementitious materials decreases, the amount of MgO added increases, the expansion amount per unit of MgO increases, and the drying shrinkage of concrete is greatly improved. With the extension of hydration age, MgO hydration gradually releases its expansion energy, which significantly reduces the drying shrinkage of concrete at 28 d, 90 d and 180 d. When the content of the MgO expansive agent is 10 kg/m3, the drying shrinkage is reduced by 3.3%, 4.9%, and 2.9% for 28 d, 90 d, and 180 d, respectively, compared with the G-8 without MgO bulking agent. When the dosage is increased to 20 kg/m3, the drying shrinkage is reduced by 17.8%, 25.6%, and 25.7% for 28 d, 90 d, and 180 d, respectively. This indicates that MgO expansive agent can greatly reduce the drying shrinkage of mass concrete in the later stage of hydration and improve the crack resistance of mass concrete. Therefore, considering the performance of concrete, the content of the MgO expansive agent should be controlled at 20 kg/m3.
Figure 10: Performance of concrete with MgO expansive agent
In this study, phosphorus slag was used to replace part of the cement in the cementitious material, and the MgO expansion agent was used to reduce the shrinkage of mass concrete. The effects of phosphorus slag and MgO expansion agent on the mechanical properties, shrinkage characteristics, and hydration heat of mass concrete were systematically investigated. The main conclusions are as follows:
(a) Phosphorus slag can significantly increase the slump and expansion of the mixture, prolong the setting time, and reduce the hydration heat within 48 h. In the range of 0%–50% content, the greater the phosphorus slag content, the more obvious the effect.
(b) The early compressive strength and tensile strength of concrete were reduced when phosphorus slag was used to replace cement. However, the compressive strength and tensile strength of concrete will be slightly improved in the range of 0%–20% at 90 days.
(c) In the range of 0%–20%, phosphorus slag can reduce the drying shrinkage rate of concrete. In the range of 20% to 50%, phosphorus slag will increase the drying shrinkage rate of concrete, and the increase in drying shrinkage is particularly obvious before 28 days.
(d) MgO expansion agent can effectively reduce the drying shrinkage rate of phosphorus slag concrete at each age, and the effect of MgO with 20 and 25 kg/m3 on drying shrinkage is essentially consistent.
(e) The compressive strength of concrete with different content of MgO is the same, which is slightly lower than that of G-8. With the increase of age, the strength reduction decreases. When the content of MgO is 20 kg/m3, the compressive strength of concrete increases and is essentially consistent with G-8 at 90 days.
Acknowledgement: None.
Funding Statement: The work presented in this paper was supported by CSCEC Technology Research and Development Plan (CSCEC-2020-Z-39).
Author Contributions: The authors confirm contribution to the paper as follows: study conception and design: Jianlong Jin; data collection: Jingjing Ding; analysis and interpretation of results: Long Xiong and Ming Bao; draft manuscript preparation: Peng Zeng. All authors reviewed the results and approved the final version of the manuscript.
Availability of Data and Materials: The authors confirm that the data supporting the findings of this study are available within the article.
Conflicts of Interest: The authors declare that they have no conflicts of interest to report regarding the present study.
References
1. Peng, Y., Zhang, J., Liu, J., Ke, J., Wang, F. (2015). Properties and microstructure of reactive powder concrete having a high content of phosphorous slag powder and silica fume. Construction and Building Materials, 101, 482–487. [Google Scholar]
2. Allahverdi, A., Abadi, M. M. B. R., Hossain, K. M. A., Lachemi, M. (2014). Resistance of chemically-activated high phosphorous slag content cement against freeze-thaw cycles. Cold Regions Science and Technology, 103, 107–114. [Google Scholar]
3. Allahverdi, A., Pilehvar, S., Mahinroosta, M. (2016). Influence of curing conditions on the mechanical and physical properties of chemically-activated phosphorous slag cement. Powder Technology, 288, 132–139. [Google Scholar]
4. Chang, J. J., Yeih, W., Hung, C. C. (2005). Effects of gypsum and phosphoric acid on the properties of sodium silicate-based alkali-activated slag pastes. Cement and Concrete Composites, 27(1), 85–91. [Google Scholar]
5. Qi, G. H., Peng, X. Q. (2011). Analysis on the pozzolanic effects of phosphorus slag powder in concrete. Paper Key Engineering MaterialsnXiamen, China. [Google Scholar]
6. Sun, H., Peng, Y. Z., Tang, J. F., Li, N. (2013). Preparation of reactive powder concrete having high volume of phosphorous slag powder and Silica Fume. Advanced Materials ResearchQingdao, China. [Google Scholar]
7. Vafaei, M., Allahverdi, A. (2019). Strength development and acid resistance of geopolymer based on waste clay brick powder and phosphorous slag. Structural Concrete, 20(5), 1596–1606. [Google Scholar]
8. Li, D., Shen, J., Mao, L., Wu, X. (2000). The influence of admixtures on the properties of phosphorous slag cement. Cement and Concrete Research, 30(7), 1169–1173. [Google Scholar]
9. Mo, L., Fang, J., Huang, B., Wang, A., Deng, M. (2019). Combined effects of biochar and MgO expansive additive on the autogenous shrinkage, internal relative humidity and compressive strength of cement pastes. Construction and Building Materials, 229, 116877. [Google Scholar]
10. Forero, J. A., Bravo, M., Pacheco, J., De Brito, J., Evangelista, L. (2022). Thermal performance of concrete with reactive magnesium oxide as an alternative binder. Sustainability, 14(10), 5885. [Google Scholar]
11. Cao, F., Yan, P. (2019). The influence of the hydration procedure of MgO expansive agent on the expansive behavior of shrinkage-compensating mortar. Construction and Building Materials, 202, 162–168. [Google Scholar]
12. Li, F. X., Chen, Y. Z., Long, S. Z. (2010). Influence of MgO expansive agent on behavior of cement pastes and concrete. Arabian Journal for Science & Engineering, 35(1), 125–139. [Google Scholar]
13. Peng, Y. Z., Huang, J., Ke, J. (2013). Preparation of ultra-high performance concrete using phosphorous slag powder. Applied Mechanics and Materials. 357–360, 588–591. [Google Scholar]
14. Liu, K., Cui, Y. (2021). Effects of different content of phosphorus slag composite concrete: Heat evolution, sulphate-corrosion resistance and volume deformation. Crystals, 11(11), 1293. [Google Scholar]
15. Pang, M., Sun, Z., Chen, M., Lang, J., Dong, J. et al. (2020). Influence of phosphorus slag on physical and mechanical properties of cement mortars. Materials, 13(10), 2390. [Google Scholar] [PubMed]
16. Wang, L., Luo, R., Zhang, W., Jin, M., Tang, S. (2021). Effects of fineness and content of phosphorus slag on cement hydration, permeability, pore structure and fractal dimension of concrete. Fractals, 29(2), 2140004. [Google Scholar]
17. Yao, H., Liu, D. (2021). In study on the mechanic property of low heat cement admixing phosphorus slag and fly ash. Journal of Physics: Conference Series, 2021, 012090. [Google Scholar]
18. Liu, X. W., Yang, L., Zhang, B. (2013). Utilization of phosphorus slag and fly ash for the preparation of ready-mixed mortar. Applied Mechanics and Materials, 423–426, 987–992. [Google Scholar]
19. Yang, R., Yu, R., Shui, Z., Gao, X., Xiao, X. et al. (2019). Low carbon design of an ultra-high performance concrete (UHPC) incorporating phosphorous slag. Journal of Cleaner Production, 240, 118157. [Google Scholar]
20. Mehdizadeh, H., Kani, E. N. (2018). Modeling the influence of chemical composition on compressive strength behavior of alkali-activated phosphorus slag cement using statistical design. Canadian Journal of Civil Engineering, 45(12), 1073–1083. [Google Scholar]
21. Li, S., Mo, L., Deng, M., Cheng, S. (2021). Mitigation on the autogenous shrinkage of ultra-high performance concrete via using MgO expansive agent. Construction and Building Materials, 312, 125422. [Google Scholar]
22. Kadhum, I., Khalil, Y., Mustafa, H. (2020). Effect of MgO powder on physical and mechanical properties of polyolefin fiber reinforced concrt. IOP Conference Series: Materials Science and Engineering, 928, 022088. [Google Scholar]
23. Zhang, J. (2022). Recent advance of MgO expansive agent in cement and concrete. Journal of Building Engineering, 45, 103633. [Google Scholar]
24. Lu, X., Geng, F., Zhang, H., Chen, X. (2011). Influence of MgO-type expansive agent hydration behaviors on expansive properties of concrete. Journal of Wuhan University of Technology-Materials Science Edition, 26(2), 344–346. [Google Scholar]
Cite This Article
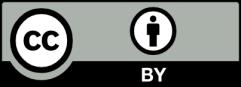
This work is licensed under a Creative Commons Attribution 4.0 International License , which permits unrestricted use, distribution, and reproduction in any medium, provided the original work is properly cited.