Open Access
ARTICLE
A Gel-Based Solidification Technology for Large Fracture Plugging
1 Tianjin Branch of CNOOC (China) Co., Ltd., Tianjin, 300450, China
2 Jingzhou Jiahua Technology Co., Ltd., Jingzhou, 434001, China
* Corresponding Author: Kan Chen. Email:
Fluid Dynamics & Materials Processing 2024, 20(3), 563-578. https://doi.org/10.32604/fdmp.2023.030152
Received 24 March 2023; Accepted 27 June 2023; Issue published 12 January 2024
Abstract
Fault fractures usually have large openings and considerable extension. Accordingly, cross-linked gel materials are generally considered more suitable plugging agents than water-based gels because the latter often undergo contamination via formation water, which prevents them from being effective over long times. Hence, in this study, a set of oil-based composite gels based on waste grease and epoxy resin has been developed. These materials have been observed to possess high compressive strength and resistance to the aforementioned contamination, thereby leading to notable increase in plugging success rate. The compressive strength, thickening time, and resistance to formation water pollution of these gels have been evaluated indoors. The results show that the compressive strength of the gel can reach 11 MPa; additionally, the related gelation time can be controlled to be more than 3 h, thereby providing a safe construction time; Invasion of formation water has a small effect on the gel strength and does not shorten the thickening time. All considered performance indicators of the oil-based gel confirm its suitability as a plugging agent for fault fractures.Keywords
Natural fractures encountered during drilling are the primary cause of mud loss [1,2]. Studies have shown that proximity of formation fractures to faults, mechanism and geometry of folds, and rock properties are the main factors that affect fracture density and pore size [3–8]. In the Bozhong block, such fractured formations with severe leakage are often found during drilling owing to the relatively developed faults. Currently, research on plugging in this kind of seriously leaky and fractured formations can be summarized vis-à-vis two aspects. First, the leakage and control mechanisms of drilling fluid should be clarified to provide a basis for scientific plugging. The second is to develop corresponding plugging materials for different loss types and formation conditions. This includes gel-type plugging materials that can be compatible with various fracture sizes, strong filling plugging materials, and different granular plugging materials for bridge slurry plugging [9–14]. Various types of plugging materials have satisfactory application effects in the process of indoor evaluation and field application [15–19]; however, the most widely used plugging material is still traditional bridge slurry plugging. For example, Amanullah [20] developed a series of bridge plugging materials (ARC) based on jujube stone, and the pressure could reach 8 MPa when plugging 2-mm cracks. Kang et al. [21] evaluated the sealing effect of different types of granular materials on cracks when used alone or in combination. The results showed that when used in combination, rigid particles, elastic particles, and fiber materials achieve a sealing pressure capacity of up to 13 MPa for 2-mm cracks. A plugging agent with high water loss [22] also increases the filtration rate of the plugging slurry depending upon the bridge plugging material, as the plugging material can rapidly accumulate in the fracture to form a plugging. However, this kind of granular plugging formula suffers several shortcomings: ① Granular plugging materials are often find it difficult to effectively match the formation fracture size, which easily causes plugging failure; ② When drilling large fractures, fracture width and longitudinal depth are large, and it is difficult for granular materials to effectively accumulate and stay and in such fractures. Even for the rapidly accumulating, high water loss plugging formula, we must add bridging particles that match the size of the fracture to achieve a rapid accumulation effect. Therefore, when plugging large fractures, the granular plugging method often suffers low pressure bearing capacity and is prone to repeated loss.
Gel materials offer a number of advantages when used for plugging cracks [23,24]. Accordingly, researchers have developed various types of gel materials to resolve different types of leakage. For example, a weak gel-type plugging agent [25–28] usually has satisfactory flow ability and deformation ability. It can effectively squeeze into microfractures with complex shapes. Relying on the structural strength of the gel, the leakage rate undergoes considerable decline; however, this kind of gel suffers low pressure-bearing capacity. A gel plugging agent [29–31], which expands upon encountering oil or water, can be more effectively supported in the fracture after a certain period of foam invasion upon entering the fracture. However, the expansion time of the gel is not easy to control, and the strength after expansion considerably decreases, which is more suitable for microporous leakage. A cross-linked solidified plugging gel [32–34], mostly a temperature-sensitive gel, can achieve high strength at a certain temperature after a certain reaction time, which has a satisfactory effect on plugging and pressure bearing of large fractures. However, such gel is easily damaged by downhole fluid before the cross-linking reaction, considerably reducing the gel strength and affecting its filling state in the fractures, thereby leading to insufficient sealing density and weakened plugging effect.
Many kinds of gel were developed by researchers. In this study, we select some typical gel types and analyze their applicability. The thixotropic self-healing gel, represented by ZND gel developed by Academician Luo Pingya, is a weak gel. Although it was observed to be less affected by simulated formation water, it suffers low strength and struggles in meeting the plugging requirements of some large fractures. Guo et al. [35] studied a high-temperature-resistant chemical gel, and Li et al. [36] studied a high-temperature-resistant plugging gel for plugging of malignant leakage in a reservoir. This kind of gel belongs to the category of water-based gels that can be solidified via the cross-linking reaction, and the strength after curing mostly exceeds 2 MPa. However, this kind of water-based gel is either affected by formation water in formation fractures, which considerably reduces the gel’s strength, or even cannot be solidified; hence, the plugging effect is not ideal in application. Li et al. [37] studied the plugging agent YDLJ-1, which can expand four to six times but needs to be used in combination with other plugging particles, similar to particle bridging for sealing small cracks. Although the sealing effect was satisfactory, the pressure-bearing capacity was insufficient when sealing large cracks. Ji et al. [38] studied a gel plugging system that used water as the base fluid; addition of binders and plugging agents caused physical and chemical reactions to solidify the gel system. With increase in dosage, the system considerably thickened when simulating the invasion of formation water. There was also a risk of gel curing in advance after slurry mixing, which made it difficult to meet the plugging requirements of large fractures.
With an aim to meet the plugging requirements of such fault fractures, we study an oil-based gel plugging system to resist the damage by downhole fluid and enhance the plugging effect of the gel in large fractures. After indoor investigation, the concept of interpenetrating network gel [39,40] was introduced. Using an emulsifier and an oil-based suspension agent, the resin was evenly dispersed in the waste grease base fluid under high-speed stirring, forming an oily gel system suitable for fault fracture plugging. Before the reaction, it was in the pure liquid state. After addition of a fat saponifying agent and a resin curing agent, the resulting composite oily gel solid formed via a reaction gained high compressive strength; the performance of the oil-based gel system was systematically evaluated in the laboratory, and the field application was also accomplished.
Experimental raw materials comprised waste oil (mainly comprising peanut oil, castor oil, rapeseed oil, animal oil, among others), a saponification agent (calcium hydroxide), saponification activator (sodium hydroxide), epoxy resin E54, a resin curing agent (diethyltoluene diamine), a resin emulsifier (EMUL150, provided by Jingzhou Jiahua Technology Co., Ltd., Jingzhou City, Hubei Province, China), and an oil-based suspension agent (B38, SA-05, provided by Jingzhou Jiahua Technology Co., Ltd., Jingzhou City, Hubei Province, China).
The main materials were waste grease and epoxy resin. The waste grease is a mixture of various animal oils and vegetable oils, mainly comprising triglyceride fatty acid ester (C6H5O6(C18H37NO3)3), linoleic acid (CH3(CH2)4CH=CHCH2CH=CH(CH2)7COOH), oleic acid (C18H34O2), arachidonic acid (C20H32O2), and cholesterol (C27H46O), among others.
Epoxy resin is a type of polymer with a molecular formula of (C11H12O3)n and contains more than two epoxy groups in its molecules. It is a condensation product of epichlorohydrin with bisphenol A or polyols.
The experimental instruments comprised an electronic balance, a high-speed mixer, an atmospheric curing kettle (Shenyang Taige Petroleum Equipment Manufacturing Co., Ltd., Shenyang City, Liaoning Province, China), a high-temperature, high-pressure thickening-time tester (Shenyang Taige Petroleum Equipment Manufacturing Co., Ltd., Shenyang City, Liaoning Province, China), a uniaxial compressive strength testing machine (Jinan Zhongluchang Testing Machine Manufacturing Co., Ltd., Jinan City, Shandong Province, China), and a natural fracture plugging simulation experimental device (Jingzhou Talin Electromechanical Equipment Manufacturing Co., Ltd., Jingzhou City, Hubei Province, China).
2.2.1 Preparation Method of Composite Oily Gel
(1) Use an electronic scale to measure 500 mL of waste grease (convert volume to mass on the basis of density). Add in the epoxy resin, suspension agent, and emulsifier in proportion based on the volume of the waste oil.
(2) Under stirring at 3000 rpm, add in calcium hydroxide, activator (10% sodium hydroxide aqueous solution), fresh water, and barite in sequence.
(3) The specific dosage of all materials is determined based on the experimental situation. After all materials are added, continue to stir for 30 min to obtain a composite oily gel base liquid.
2.2.2 Stability Evaluation of Compound Oily Gel
(1) Prepare 500 mL of the compound oily gel according to the formula, and weigh it to 1.6 g/cm3.
(2) Different gel formulations are obtained by adjusting the dosage of the resin, suspending agent, and emulsifier. The pumpability and stability of the composite oily gel are tested using a Marsh funnel. As the pumpability standard, the funnel viscosity is less than 75 s.
(3) Let the gel paste to stand at room temperature for 3 h; thereafter, measure the density difference between the top and bottom of the paste, and if it is less than 0.03 g/cm3, it is qualified.
2.2.3 Thickening Time Test of the Composite Oily Gel
(1) Prepare more than 600 mL of the composite oily gel; place it into a high-temperature, high-pressure thickening cup, and attempt to fill it to avoid air from entering it.
(2) Use high-temperature, high-pressure thickening to test the thickening time of the gel. Observe the change in thickening curve with time at 80°C, 90°C, 100°C, and 110°C, respectively. If the consistency exceeds 40 Bc, it is deemed that the gel cannot be effectively pumped, with the corresponding time being the thickening time.
2.2.4 Triaxial Compressive Strength Test of the Oily Gel
(1) After preparing the gel, pour it into the mold and demold it after curing to form a gel module with 10 mm diameter and 25 mm height.
(2) Use a triaxial compressive strength tester to test the compressive strength (MPa) of different formulations.
2.2.5 Evaluation of Antipollution Ability of the Oily Gel
(1) Prepare more than 600 mL of the composite oil-based gel, and mix different amounts of simulated formation water according to the experimental requirements; thereafter, use a high-speed mixer, and mix at 3000 rpm for 30 min.
(2) Next, thickening time test and compressive strength test (the method is the same as previously stated) shall be performed for the mixed liquid in a bid to evaluate the change in gel performance under different simulated formation water invasion amounts and study the gel’s antipollution ability.
3 Determination of Basic Formula of the Oil-Based Gel
3.1 Formula Composition of the Oil-Based Gel
The composite oil-based gel should have the following characteristics when plugging in a bid to effectively plug fault fractures:
(1) The ability to intrude into the micropores of the fracture wall: Because there is a large fracture surface in the fault fracture, the gel must invade the micropores of the fracture wall to ensure it can effectively stay in the fracture, which helps enhance the adhesion between the gel and fracture wall.
(2) Compressive strength: Because the fault fracture is in a continuous open state, the plugging layer must maintain resistance to the leakage pressure of drilling fluid, which requires that the plugging gel possesses certain pressure-bearing capacity after plugging formation. Under continuous fluid column pressure and formation pressure, the plugging section will not be damaged. The pressure bearing capacity after plugging must be up to 10 MPa per the requirements for plugging and pressure bearing in the Bozhong block.
3.1.1 Composition of the Oil-Based Gel Basic Formula
Oil and alkaline substances undergo a chemical reaction, changing from a liquid state to a solid state. The reaction time can be adjusted by screening for alkaline substances and modifying their dosage. Accordingly, the author considers using waste grease to make gel to plug the lost circulation when drilling. Waste grease is widely available and has low price. Upon reasonable use, it is not only beneficial for environmental protection but can also solve the lost-circulation problem. Considering the low strength of single waste grease after curing, we attempt to introduce a small amount of epoxy resin. The epoxy resin needs a specific curing agent for curing. The epoxy resin and waste grease will not negatively affect each other, and a solid gel with high strength will be formed after mixed curing, which can effectively meet on-site plugging requirements.
Waste grease and resin cannot be effectively mixed under normal conditions. There is obvious stratification phenomenon in the mixture, which is neither conducive to development of gel strength nor is convenient for field application.
The solution can be uniformly dispersed by addition of the emulsifier and suspension agent. The rheology and suspension of the plugging slurry can be evaluated at room temperature. Table 1 presents the experimental evaluation results. The experimental formula is as follows: 500 mL of waste oil + epoxy resin + suspending agent + emulsifier + 30% calcium hydroxide + 3% activator (10% sodium hydroxide aqueous solution) + 5% fresh water + barite to 1.6 g/cm3.
From the experimental results, it can be observed that a certain amount of suspending agent and emulsifier can effectively make the emulsify the resin and successfully disperse it in the oil solution and maintain a stable state. According to the data on funnel viscosity and sedimentation stability, it is recommended to select SA-05 as the suspending agent (with dosage in the range of 0.5%–1%) and EMUL150 as the emulsifier (with dosage in the range of 2%–3%).
From Table 2, it can be seen that with increase in resin dosage, the funnel viscosity will increase and suspension stability decrease. We must increase the amount of emulsifier. According to the different resin dosages, the overall performance of the gel system can be ensured by adjusting the dosage of the suspending agent. Taken together, we suggest that the dosage of resin be in the range of 10%–30%, that of suspending agent SA-05 be in the range of 0.8%–1%, and that of emulsifier EMUL150 be 3%.
From Fig. 1, it can be seen that the resin will rapidly settle when not fully emulsified and dispersed, causing a large density difference between the top and bottom of the slurry, thereby resulting in poor overall curing strength. The particle size of the lotion of stable slurry is approximately 25 μm, as shown in Fig. 2. The emulsion dispersion is satisfactory.
Figure 1: Resin is not fully dispersed and mixed with waste oil
Figure 2: Fully disperse and mix the resin and waste oil
3.1.2 Effect of Resin Dosage on Gel Thickening Time and Strength
The curing of the composite oily gel involves the double reaction of saponification of oil and resin curing; therefore, the effect of resin on thickening time and curing strength should be considered. The following is the evaluation formula in the laboratory: 500 mL of waste oil + 0%–40% epoxy resin + 1% suspending agent + 3% emulsifier + 30% calcium hydroxide + barite to 1.6 g/cm3 + 3% activator (10% sodium hydroxide aqueous solution). The thickening time and curing strength of the gel at different resin dosages were evaluated using a high-temperature, high-pressure thickening-time tester, and the experimental conditions were 80°C and 40 MPa. Fig. 3 shows the experimental results.
Figure 3: Effect of resin dosage on gel thickening time and curing strength
From Fig. 3, it can be seen that the thickening time of the composite oily gel considerably increases with increasing resin dosage, and that 10%, 20%, 30% and 40% dosages correspond to thickening time of 375, 347, 273, and 208 min, respectively. This is because the resin curing reaction will release heat, which will facilitate the saponification reaction, and the viscosity of the resin becomes high upon thickening, which considerably affects the consistency of the entire system. Therefore, the thickening time is considerably affected by the resin when reacting to the data. The gel strength considerably increases with increasing resin dosage during drilling, which is 6.5, 9.1, 13, and 14.4 MPa, respectively. This is because the resin has high strength, so it performs a strength-supporting role in the entire system. According to site requirements and cost consideration, it is recommended to control the resin dosage in the range of 20%–30%.
Overall, the following is the basic formula of the compound oily gel: 500 mL of waste oil + 20%–30% epoxy resin + 1% suspending agent + 3% emulsifier + 30% calcium hydroxide + 3% activator (10% sodium hydroxide aqueous solution) + 5% fresh water + barite to 1.6 g/cm3.
3.2 Application-Performance Evaluation of the Oil-Based Gel
3.2.1 Temperature-Adaptability Evaluation of the Oil-Based Gel
Because both resin curing and oil saponification are temperature-sensitive reactions, we must evaluate the thickening time of the system at different temperatures in the laboratory. According to requirements of field application, the experimental temperature is set at 80°C, 90°C, 100°C, and 110°C and the resin dosage at 20%, 23%, 26%, and 30%. Fig. 4 shows the experimental results.
Figure 4: Corresponding thickening times at different resin dosages and temperatures
The results showed that the thickening time of the composite oily gel was considerably shortened with increasing temperature. Within the range of 80°C–110°C, the thickening time was reduced by 20–30 min for every 10°C increase in temperature. Within the range of 20%–30% resin dosage, the thickening time was >3 h, essentially meeting the requirements of on-site construction. An appropriate dosage could be selected according to an actual situation.
3.2.2 Change in Strength of the Oil-Based Gel with Time
The basic formula of the composite oil-based gel was determined in the preliminary experiment, and the pressure-holding time, i.e., the strength-development time of the gel, must be considered in the field application. In the laboratory, we evaluated the change trend of gel strength with time at 90°C (see Fig. 5).
Figure 5: (a) Change in trend of gel strength with waiting time (b) Damaged state of gel with different strengths
From the experimental results shown in Fig. 5a, it is clear that the gel strength gradually develops after 12 h. When the resin dosage becomes 23% or more, the final strength can exceed 10 MPa, which can meet the requirements of field application. Based on these data as reference, the pressure-holding time is recommended to be in the range of 12–16 h for field applications.
The gel is very easy to break and fall off when the compressive strength is low, while only some cracks will be produced in the gel when the compressive strength is high (see Fig. 5b).
3.2.3 Evaluation of Antipollution Ability of the Oil-Based Gel
We must evaluate the effect of simulated formation water dosage on the gel’s thickening time and strength to avoid safety accidents during field application. This is because the gel will encounter formation water pollution in the formation. The experimental formula gives a composite oily gel with a resin dosage of 20%, 23%, 26%, and 30%. The simulated formation water dosage is 5%, 10%, 15%, and 20%. The effect on thickening time was evaluated at 90°C (see Fig. 6).
Figure 6: Effect of simulated formation water dosage on thickening time
The results show that the invasion of simulated formation water will prolong the thickening time, which is inversely proportional to amount of resin added and directly proportional to amount of simulated formation water invasion. The pollution of formation water will not result in early thickening of gel, which indicates low risk in field application. Considering the cost and effect, the recommended resin dosage is 23%. The effect of formation water pollution on gel strength was also evaluated at 90°C. Fig. 7 shows the experimental results.
Figure 7: Effect of amount of simulated formation water on gel strength
In the experimental formula shown in Fig. 7, the resin content is 23% with the contamination levels of formation water being 5%, 10%, and 15%. Clearly, with increasing invasion amount of simulated formation water, the gel strength considerably decreases, and the curing time is relatively prolonged. When the pollution amount reaches 15%, the gel strength clearly decreases; however, the gel can still maintain a strength of 2.7 MPa after curing for 24 h. This indicates that simulated formation water has a limited effect on gel strength. The gel squeezed into cracks can still maintain high strength by increasing the amount of slurry on site and reducing the mixing by engineering means.
In theory, when waste oil reacts with alkalies, the concentration of the latter will decrease after invasion of formation water, decreasing the reaction rate. However, the curing reaction of resin will intensify upon encountering a small amount of water but decelerate upon encountering water exceeding a certain amount. In this composite oily gel system, water may preferentially participate in the reaction of oil, following which the overall thickening time would be extended. Regarding strength, water negatively affects the curing of oils and resins, considerably decreasing the curing reaction rate and strength after curing.
3.2.4 Evaluation of Pumpability of the Oil-Based Gel
Fig. 8 shows the state of gel at different stages. By observing the thickening state of the oil-based gel, it can be said that it maintains a satisfactory fluidity at 20–30 Bc, and this state can still squeeze into the formation fractures under pressure. At 40 Bc, a certain gel structure is still exhibited, and the process can last for approximately 30 min. In this state, the gel is not easy to damage by the formation fluid; therefore, it can effectively fill the leaks during the pressure-holding process, and the plugging effect is enhanced after later curing. Therefore, we determine the pumpable time to be in the range of 180–210 min, which is also the pumping construction time.
Figure 8: Different flow states of the gel
3.2.5 Evaluation of Plugging Ability of the Oil-Based Gel
(1) Evaluating the oil-based gel’s ability to penetrate microcracks
The oil-based gel delivers satisfactory flow performance and can effectively penetrate micropores on the surface of formation fractures. This helps the gel to stay in the formation fracture, following which it can effectively form a stable plugging barrier in the fracture, thus enhancing the pressure-bearing capacity after plugging. In the laboratory, we used a fine sand bed to simulate the formation micropore state and observe the invasion ability of the gel. Figs. 9 and 10 show the experimental results.
Figure 9: The state of gel invasion into micropores
Figure 10: Consolidation state formed by the gel and sand bed
A transparent sand filling tube was used to observe the invasion depth of the gel in the sand bed, as shown in Fig. 9. The experimental results show that the developed oil-based gel can effectively invade micropores formed by an 80–100-mesh sand bed, with a depth of approximately 4–5 cm; therefore, it can effectively invade micropores on the formation wall in formation fractures. The high-temperature, high-pressure simulation sand bed plugging instrument was used to simulate the high-temperature, high-pressure state at the bottom of the well, as shown in Fig. 10. Clearly, the composite oily gel can consolidate the sand bed together after reaction and solidification, which is conducive to enhancing the cohesive force of the gel in fractures.
(2) Evaluating the oil-based gel’s ability to plug large fractures
In the laboratory, we used fractures processed from natural rocks to further evaluate the plugging ability of the oil-based gel for large fault fractures. The depth of the fractures was 200 mm, width 50 mm, and opening 5 mm (see Fig. 11). According to the abovementioned test method 4, the pressure-bearing capacity test can be performed after the gel reaches the reaction strength. In the laboratory, we used a drilling fluid for testing the pressure-bearing capacity. Table 3 presents the experimental results.
Figure 11: Plugging state of gel to fault fracture
The following is the formula of the gel used in the experiment: 500 mL of waste oil + 23% epoxy resin + 1% suspending agent + 3% emulsifier + 30% calcium hydroxide + 3% activator (10% sodium hydroxide aqueous solution) + 5% fresh water + barite to 1.6 g/cm3.
From the experimental data in Table 3, it can be seen that the gel has a satisfactory effect in plugging of large cracks with 5 mm opening. The pressure-bearing capacity after plugging is related to the waiting time. A solidification waiting time of 8 h is not sufficient to make the gel reach a higher strength. Therefore, during the pressure-bearing test, the gel will be damaged to a certain extent owing to high-pressure squeezing, resulting in a small loss. Although the curing time of the gel is shortened when the temperature is higher, considering the reliability of field application, it is still recommended to control the solidification waiting time to be more than 10 h.
(1) The composite oily gel takes waste grease as the base liquid and introduces use of epoxy resin. Among them, oil saponification reaction occurs and resin solidification reaction occurs, forming an interpenetrating network gel structure, thereby enhancing the overall gel strength, allowing it to possess a high pressure bearing capacity, effectively plugging large fault fractures and improving the formation pressure.
(2) It is determined through indoor gel performance evaluation that for a resin dosage in the range of 23%–30%, the compressive strength of the composite oil-based gel can be in the range of 10.3–13 MPa, which meets the requirements of plugging and pressure bearing. At 80°C–110°C, the thickening time is in the range of 206–347 min, and no early thickening is observed after the simulated formation water invasion. A small amount of invasion has a limited effect on the strength, which still meets the site construction requirements.
(3) The gel has a satisfactory microfracture invasion ability and can form effective plugging in the fractures. The evaluation results of the gel’s microfracture invasion capability showed that the invasion depth can be in the range of 4–5 cm for a 80–100-mesh sand bed, and that the gel can form a consolidated state with the sand bed, which is conducive to solidification and filling of the gel in the fractures.
(4) The plugging experiment showed that the system can effectively seal large formation fractures. After the strength of gel exceeded 9 MPa, the gel body was not damaged under the experimental pressure. This shows that the gel can effectively resist damage by fluid column pressure and formation pressure after undergoing solidification in formation fractures.
(5) The composite oil-based gel developed in this study is mainly an oil-based material. Meanwhile, some water-based gels thicken oil-based drilling fluids, which would considerably affect the gel’s performance. However, because of its lipophilic nature, the oil-based gel has a small effect on the fluidity of oil-based drilling fluids, which can inspire a novel technical idea for plugging of oil-based drilling fluid. In this regard, we must further optimize and adjust the gel formula. Additionally, research on compatibility of drilling fluid for plugging of oil-based drilling fluid is also needed in future in a bid to determine the effect of oil-based drilling fluid on the performance of gel vis-à-vis gel strength and other aspects.
Acknowledgement: The author would like to thank the Engineering Technology Center of CNOOC, Tianjin Branch, for all the technical discussions and scientific input during the research period. The author also wishes to thank Jingzhou Jiahua Technology Co., Ltd., Jingzhou City, Hubei Province, China, for its support in the experiment.
Funding Statement: “Research and Application of Key Techniques for Drilling and Completion of Bozhong 19-6 Condensate Gas Field Development-Phase I” sub topic 4 “Research on Leakage Prevention and Plugging Techniques for Fault and Buried Hill Reservoirs”, a Project of China National Offshore Oil (China) Co., Ltd. (Project No. YXKY-2020-TJ-03).
Author Contributions: The authors confirm contribution to the paper as follows: Research ideas and scheme design of oil-based gel: Kunjian Wang, Ruibin He; Collection and analysis of relevant research literature: Qianhua Liao; Suggestions and guidance for on-site application parameters: Kun Xu, Wen Wang; Experimental operation and analysis of experimental results: Kan Chen; Draft manuscript preparation: KunJian Wang, Ruibin He, Kan Chen. All authors reviewed the results and approved the final version of the manuscript.
Availability of Data and Materials: The authors confirm that the data supporting the findings of this study are available within the article.
Conflicts of Interest: The authors declare that they have no conflicts of interest to report regarding the present study.
References
1. Iñigo, J. F., Laubach, S. E., Hooker, J. N. (2012). Fracture abundance and patterns in the suband ean fold and thrust belt, Devonian Huama mpampa formation petroleum reservoirs and outcrops, Argentina and Bolivia. Marine and Petroleum Geology, 35(1), 201–218. [Google Scholar]
2. Pireh, A., Alavi, S. A., Ghassemi, M. R., Shaban, A. (2015). Analysis of natural fractures and effect of deformation intensity on fracture density in Garau formation for shale gas development within two anticlines of Zagros fold and thrust belt, Iran. Journal of Petroleum Science and Engineering, 125(4), 162–180. [Google Scholar]
3. Ghosh, S., Galvis-Portilla, H. A., Klockow, C. M., Slatt, R. M. (2018). An application of outcrop analogues to understanding the origin and abundance of natural fractures in the woodford Shale. Journal of Petroleum Science and Engineering, 164, 623–639. [Google Scholar]
4. Wang, X. H., Ding, W. L., Cui, L., Wang, R., He, J. et al. (2018). The developmental characteristics of natural fractures and their significance for reservoirs in the Cambrian Niutitang marine shale of the Sangzhi block, Southern China. Journal of Petroleum Science and Engineering, 165, 831–841. [Google Scholar]
5. Brudy, M., Zoback, M. (1999). Drilling-induced tensile wall-fractures: Implications for determination of in-situ stress orientation and magnitude. International Journal of Rock Mechanics and Mining Sciences, 36(2), 191–215. [Google Scholar]
6. Haghi, A. H., Kharrat, R., Asef, M. R., Rezazadegan, H. (2013). Present-day stress of the central Persian Gulf: Implications for drilling and well performance. Tectonophysics, 608, 1429–1441. [Google Scholar]
7. Nelson, R. (2001). Geological analysis of naturally fractured reservoirs, 2nd editionNetherlands: Elsevier Inc. [Google Scholar]
8. Gutmanis, J. C., i Oró, L. A. (2010). Application of pyrenean fractured carbonate outcrops for subsurface reservoir characterisation. 72nd EAGE Conference and Exhibition Incorporating, Barcelona, Spain, SPE EUROPEC. [Google Scholar]
9. Abrams, A. (1977). Mud design to minimize rock impairment due to particle invasion. Journal of Petroleum Technology, 29(5), 586–592. [Google Scholar]
10. Nayberg, T. M. (1987). Laboratory study of lost circulation materials for use in both oil-based and water-based drilling muds. SPE Drilling Engineering, 2(3), 229–236. [Google Scholar]
11. Chellappah, K., Aston, M. (2012). A new outlook on the ideal packing theory for bridging solids. Proceedings of the SPE International Symposium and Exhibition on Formation Damage Control, Lafayette, LA, USA. [Google Scholar]
12. Sun, J. S., Bai, Y. R., Cheng, R. C., Lyu, K., Liu, F. et al. (2021). Research progress and prospect of plugging technologies for fractured formation with severe lost circulation. Petroleum Exploration and Development, 48(3), 732–743. [Google Scholar]
13. Xu, C. Y., Yan, X. P., Kang, Y. L., You, L., Zhang, J. (2020). Structural failure mechanism and strengthening method of plugging zone in deep naturally fractured reservoirs. Petroleum Exploration and Development, 47(2), 399–408. [Google Scholar]
14. Jia, L. C., Chen, M., Hou, B., Sun, Z., Jin, Y. (2014). Drilling fluid loss model and loss dynamic behavior in fractured formations. Petroleum Exploration and Development, 41(1), 95–101. [Google Scholar]
15. Xu, M. B., Zhao, M. K., Hou, S. S. (2018). Research and application of oil-based bridge plugging agent. Fault-Block Oil and Gas Field, 25(6), 799–802. [Google Scholar]
16. van Oort, E., Vargo, R. (2008). Improving formation-strength tests and their interpretation. SPE Drilling and Completion, 23(3), 284–294. [Google Scholar]
17. Aston, M. S., Alberty, M. W., McLean, M. R., De Jong, H. J., Armagost, K. (2004). Drilling fluids for wellbore strengthening. Texas, USA: SPE. [Google Scholar]
18. Loloi, M., Zaki, K. S., Zhai, Z., Abou-Sayed, A. (2010). Borehole strengthening and injector plugging-the common geomechanics thread. Egypt: SPE Cairo. [Google Scholar]
19. Kang, Y. L., Xu, C. Y., Tang, L., Li, S., Li, D. (2014). Constructing a tough shield around the wellbore: Theory and method for lost-circulation control. Petroleum Exploration and Development, 41(4), 473–479. [Google Scholar]
20. Amanullah, M. (2016). Characteristics, behavior and performance of arc plug: A date seed-based sized particulate LCM. Saudi Arabia: SPE Damman. [Google Scholar]
21. Kang, Y. L., Yu, H. F., Xu, C. Y. (2014). An optimal design for millimeter-wide fracture-plugged zones. Natural Gas Industry, 34(11), 88–94. [Google Scholar]
22. Hou, S. L., Liu, G. Y., Huang, D. Q., Tang, C., Shu, R. et al. (2018). Lost circulation control with high filtration lost circulation materials. Drilling Fluid & Completion Fluid, 35(1), 53–56. [Google Scholar]
23. Whitfill, D. L., Wang, M., Jamison, D., Angove-Rogers, A. (2007). Preventing lost circulation requires planning ahead. Proceedings of the International Oil Conference and Exhibition in Mexico, Veracruz, Mexico. [Google Scholar]
24. Lecolier, E., Herzhaft, B., Rousseau, L., Neau, L., Quillien, B. et al. (2005). Development of a nanocomposite gel for lost circulation treatment. Proceedings of the SPE European Formation Damage Conference, Sheveningen, The Netherlands. [Google Scholar]
25. Hashmat, M. D., Sultan, A. S., Rahman, S., Hussain, S. M., Ali, S. A. (2017). Flowing gels for loss circulation prevention. Saudi Arabia: SPE Damman. [Google Scholar]
26. Huang, B., Zhang, W. S., Zhou, Q., Fu, C., He, S. (2020). Preparation and experimental study of a low-initial-viscosity gel plugging agent. ACS Omega, 5(25), 15715–15727 [Google Scholar] [PubMed]
27. Jia, H., Yang, X., Li, S., Yu, P., Zhang, J. (2020). Nanocomposite gel of high-strength and degradability for temporary plugging in ultralow-pressure fracture reservoirs. Colloids and Surfaces A: Physicochemical and Engineering Aspects, 585, 124108. [Google Scholar]
28. Nie, X. Y., Wang, P. Q., Luo, P. Y. (2010). A study of the yield stress of a viscoelastic gel applied in severe lost circulation control. Natural Gas Industry, 30(3), 80–82. [Google Scholar]
29. Bai, Y. R., Dai, L. Y., Sun, J. S., Jiang, G. C., Lv, K. H. et al. (2022). Plugging performance and mechanism of an oil-absorbing gel for lost circulation control while drilling in fractured formations. Petroleum Science, 19, 2941–2958. [Google Scholar]
30. Wang, Z., Bai, B. J. (2018). Preformed-particle-gel placement and plugging performance in fractures with tips. SPE Journal, 23(6), 2316–2326. [Google Scholar]
31. Imqam, A., Wang, Z., Bai, B. J. (2017). The plugging performance of preformed particle gel to water flow through large opening void space conduits. Journal of Petroleum Science and Engineering, 156, 51–61. [Google Scholar]
32. Li, Z. Y., Li, X. G., Du, K., Liu, H. K. (2020). Development of a new high-temperature and high-strength polymer gel for plugging fractured reservoirs. Upstream Oil and Gas Technology, 5, 100014. [Google Scholar]
33. Qiu, J. X., Bai, Y. R., Sun, J., Dai, L., Lei, S. et al. (2021). Experimental study on an oil-based polymer gel for lost circulation control in high-temperature fractured formation. Applied Ploymer, 139(10), 51763. [Google Scholar]
34. Fan, X. Y., Zhao, P. F., Zhang, Q. G., Zhang, T., Zhu, K. et al. (2018). A polymer plugging gel for the fractured strata and its application. Materials, 11(5), 856 [Google Scholar] [PubMed]
35. Guo, X. J., Yu, P. Z. (2019). Controlling mud losses in well Shunbei 52X with high temperature chemical gels. Drilling Fluid and Completion Fluid, 36(2), 189–193. [Google Scholar]
36. Li, H., Liu, H. K., He, Z., Li, Z., Zhang, S. et al. (2019). Use gel to control severe mud losses in carbonate reservoir formations in Tahe oilfield. Drilling Fluid & Completion Fluid, 36(1), 25–28. [Google Scholar]
37. Li, H. M., Shen, F., Wu, J. J., Li, W., Ma, Z. (2016). Study on performance of a new oil base mud lost circulation material. Drilling Fluid and Completion Fluid, 33(2), 41–44. [Google Scholar]
38. Ji, W. J., Yang, Y., Yan, Y. S., Tang, G. (2021). Gel plugging system for oil-based drilling fluid and its application. Drilling Fluid and Completion Fluid, 38(2), 196–200. [Google Scholar]
39. Dhand., A. P., Galarraga., J. H., Burdick, J. A. (2021). Enhancing biopolymer hydrogel functionality through interpenetrating networks. Trends in Biotechnology, 39(5), 519–538 [Google Scholar] [PubMed]
40. Myung, D., Waters, D., Wiseman, M., Duhamel, P. E., Noolandi, J. et al. (2008). Progress in the development of interpenetrating polymer network hydrogels. Polymers for Advanced Technologies, 19(6), 647–657 [Google Scholar] [PubMed]
Cite This Article
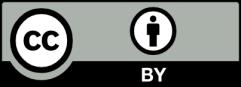
This work is licensed under a Creative Commons Attribution 4.0 International License , which permits unrestricted use, distribution, and reproduction in any medium, provided the original work is properly cited.