Open Access
ARTICLE
The Conversion of Non-Dispersed Polymers into Low-Potassium Anti-Collapse Drilling Fluids
1 School of Petroleum Engineering, Yangzte University, Wuhan, 430100, China
2 Hubei Key Laboratory of Oil and Gas Drilling and Production Engineering, Yangtze University, Wuhan, 430100, China
3 School of Petroleum Engineering, Yangtze University, National Engineering Research Center for Oil & Gas Drilling and Completion Technology, Wuhan, 430100, China
4 Engineering Technology Research Institute of PetroChina Great Wall Drilling Engineering Co., Ltd., Panjin, 124000, China
* Corresponding Author: Shanfa Tang. Email:
Fluid Dynamics & Materials Processing 2024, 20(2), 325-335. https://doi.org/10.32604/fdmp.2023.042055
Received 30 March 2023; Accepted 14 July 2023; Issue published 14 December 2023
Abstract
Different drilling fluid systems are designed according to mineral composition, lithology and wellbore stability of different strata. In the present study, the conversion of a non-dispersed polymer drilling fluid into a low potassium anti-collapsing drilling fluid is investigated. Since the two drilling fluids belong to completely different types, the key to this conversion is represented by new inhibitors, dispersants and water-loss agents by which a non-dispersed drilling fluid can be turned into a dispersed drilling fluid while ensuring wellbore stability and reasonable rheology (carrying sand—inhibiting cuttings dispersion). In particular, the (QYZ-1) inhibitors and (FSJSS-2) dispersants are used. The former can inhibit the hydration expansion capacity of clay, reduce the dynamic shear force and weaken the viscosity; the latter can improve the sealing effect and reduce the filtrate loss. The results have shown that after adding a reasonable proportion of these substances (QYZ-1: FSJSS-2) to the non-dispersed polymer drilling fluid, while the apparent viscosity, plastic viscosity, structural viscosity and fluidity index underwent almost negligible changes, the dynamic plastic ratio increased, and the filtration loss decreased significantly, thereby indicating good compatibility. According to the tests (conducted in the Leijia area), the density was 1.293 g/cm3, and after standing for 24 h, the SF (static settlement factor) was 0.51. Moreover, the filtration loss was reduced to 4.0 mL, the rolling recovery rate reached 96.92%, with excellent plugging and anti-collapse performances.Keywords
As an important part of unconventional oil and gas, tight oil has gradually gained a higher position in the world energy supply structure and has gradually become an important part of the world oil and gas [1–4]. Leijia-lacustrine carbonate rock is one of the PetroChina Liaoning Liaohe Oilfield Company (Panjin, China) key exploration and development in the future [5–9]. Early due to the formation research is not thorough, drilling fluid performance and wall stability matching is not perfect, easy to cause quaternary thick mud cake and shrink diameter card, designed two sets of drilling fluid system, higher drilling costs, seriously affected the economic benefits of tight oil development. Based on the complex and diverse mineral composition of terrestrial mud shale in Shahejie Section of Leijia area and the obvious chemical composition differences among different lithologic combinations, non-dispersive polymer drilling fluid and low potassium anti-collapsing drilling fluid were designed in S2 and S3 intervals, respectively, but the conversion of drilling fluid types and systems was not achieved, resulting in the problem of low drainage and reuse rate of drilling fluid. It also increases environmental safety risks and drilling fluid costs [10–16].
In order to realize low economic cost, safety and environmental protection in Leijia area, a systematic study was conducted on the geology of tight oil in Leijia area and the supporting technology of drilling fluid [17–19], using the technical idea of the transformation of non-dispersed to dispersed drilling fluid type, the reasonable ratio of inhibitor QYZ-1 and dispersant FSJSS-2 was developed [20–24]. Based on this, this study constructed a set of low-potassium anti-collapsing drilling fluid system transformed by non-dispersible polymer drilling fluid, and tested its rheological properties, inhibition properties, enhanced suspension properties and thermal stability. Rheological properties, filtration loss, rolling recovery rate and suspension stability all met the requirements of drilling fluid field use [25,26]. The effects of changes in soil loading, density, rheology and salt content on the conversion of non-dispersed polymer drilling fluid were tested [27–29]. It was concluded that the system was not affected by the above factors and met the needs of different strata and different lithology, and was successfully converted into S3 formation, providing a feasible low-potassium anti-collapse drilling fluid scheme, which greatly improved the repeated utilization rate of drilling fluid and helped to ensure the effective green development of Shahe Street section [30].
2.1 Experimental Materials and Apparatus
The materials and equipment used are shown in Tables 1 and 2.
(1) Non-dispersed polymers drilling fluid preparation
Preparation of non-dispersed polymer drilling fluid preparation in accordance with the Drilling fluid Material Code (GB/T 5005-2010). Configuration process: Firstly, 150 mL base slurry with a density of 1.06 g/cm3 was added to the drilling fluid cup and stirred at high speed for 5–10 min; Under high speed stirring, 10 mL of 10% NaOH solution was added to increase the dispersity of drilling fluid. Then 7.5 g of NH4Cl, 50 ml of FA-367 with a concentration of 2%, 7.5 g of NH4PAN, 5 mL of PAC-Lv (10%), 17.5 g of emulsified asphalt, 12.5 g of ultra-fine CaCO3 were added successively, and finally 500 mL of water was added.
(2) Drilling fluid basic performance test
The measurement of rheology, shear force, density and filtration loss at room temperature was carried out according to “Oil and Gas Industry—Drilling Fluid Field Test” (GB/T 16783.1-2014). Rheology property: Use D6B six-speed rotary viscometer at 3, 6, 100, 200, 300, 600 rpm to measure shear force and calculate rheology. API filtration: The filtration vector of drilling fluid filtrate at 1 MPa was measured by NS-1 medium pressure filtration analyzer; Density: The density of drilling fluid was measured by YYM liquid densimeter. Based on the horizontal scale, the drilling fluid was filled in one end of the liquid cup until it spilled into the hole of the lid, wiped the lid, adjusted to balance, and finally the density value was read.
(3) Core soak test
The S3 core powder from Shahe Street in Leijia area of Liaohe Oilfield was crushed through an 80-mesh sieve, and three 8 g core powder were taken out. Core slices were formed after pressing at 10 MPa for 15 min. The size of core was 3.026 cm × 0.575 cm. The core pieces were placed into clean water and low potassium anti-collapsing drilling fluids respectively, and the changes of core pieces morphology in different soaking fluids at different times within 24 h were observed and recorded, so as to determine the anti-collapsing effect of different soaking media.
(4) Rolling recovery rate measurement
The rolling recovery rate was determined by reference to the Standard of the Oil and Gas Industry of the People’s Republic of China—Test Method for Physical and Chemical Properties of Mud Shale (SY-T 5613-2018). Certain core particles are dried and weighed, and the core particles with mass m are placed in a high-temperature aging tank containing drilling fluid to be measured and rolled at a high temperature. After rolling, the liquid and rock samples in the tank are transferred to a sampling screen with a diameter of 0.42 mm for screening and washing, and then the rock samples are transferred to a weighing bottle (m1) that has been dried and weighed. The weighing bottle containing the sample was put into a blast oven at 105°C ± 3°C for drying to constant weight, and then taken out and put into the dryer for cooling to room temperature before weighing. The mass was recorded as m2, and the hot roll recovery rate was calculated according to formula (1).
ω=m2−m1m×100% (1)
(5) Settlement stability measurement
The settlement factor is calculated in accordance with the Specification for Drilling Fluid Materials (GB/T 5005-2010). The drilling fluid with the required specific gravity was prepared, aged at 130°C in a stainless steel tank and left for a period of time (2–24 h). The density specific gravity (r1) at the upper part of the heavy drilling fluid column and the density specific gravity (r2) at the bottom of the liquid column were determined respectively, and then the static settlement factor was calculated according to formula (2).
SF=r2r1+r2 (2)
3.1 Experimental Thinking of System Transformation
According to the characteristics of wellbore instability, difficulty in carrying drilling cuttings and high difficulty in reservoir protection in S3 interval, Combined with the non-dispersive polymer drilling system (3% bentonite + 0.1% NaOH + 1.5% NH4Cl + 0.25% FA − 367 + 0.1% PAC − lv + 1.5% NH4PAN + 3.5% + 2.5% CaCO3 + white asphalt + barite (r = 1.20∼1.22 g/cm3), Low potassium anti-collapsing drilling fluid belongs to coarse dispersive drilling fluid, necessary to use a heat-resistant inhibitor. Finally, QYZ-1 inhibitor with rheological improvement and FSJSS-2 dispersant with strong sealing performance were selected.
3.2 Study on the Influence of Different Factors Change on Transformation
3.2.1 Effect of Bentonite Content on Inter-System Conversion
Test 6 groups of non-dispersed polymer drilling fluids with different bentonite content (2%∼4.5%), and select the flow index and apparent viscosity, plastic viscosity change smaller 2 groups (3% and 3.5% of bentonite content), its performance before and after the transformation of such as shown in Table 3.
As can be seen from Table 3, the apparent viscosity, plastic viscosity and structural viscosity all increase with the increasing of bentonite content before conversion, and the changes of fluidity index, dynamic plastic ratio and filter vector are minimal. After conversion, compared with before conversion, the apparent viscosity and plastic viscosity increased at 3% bentonite content, and decreased at 3.5% bentonite content. The changes of viscosity parameters were within a reasonable range, while the filter vector decreased to 4.2 mL at 3% bentonite content, indicating that the dispersive fluid loss reducer FSJSS-2 was introduced into the non-dispersive polymer drilling fluid. Its filter vector reducer has the effect of greatly reducing water loss; Moreover, the effect of filter vector and rheology is very small according to the change of soil content.
3.2.2 Effect of Weighted Density on Inter-System Transition
Six groups of non-dispersed polymer drilling fluids with different density weights (ρ = 1.0203∼1.310 g⋅cm−3) were tested. Two groups of drilling fluids with densities of 1.0203 and 1.206 g⋅cm−3 with better rheology and lower filter vector were selected. The performance pairs before and after conversion were shown in Table 4.
Table 4 shows that when the drilling fluid density is 1.020 g⋅cm−3, the apparent viscosity, plastic viscosity, structural viscosity and fluidity index change little before and after conversion, the dynamic plastic ratio increases from 0.30 to 0.40, and the filter vector decreases to 4.4 mL. When the drilling fluid density was 1.020 g⋅cm−3, the apparent viscosity and fluidity index still changed little, the plastic viscosity decreased to 29 mPa⋅s, the structural viscosity increased to 20.5 mPa⋅s, the dynamic plastic ratio increased from 0.61 to 0.72, and the filter vector also decreased to 4.4 mL. Before and after the conversion, the rheology was stable and the fluid loss decreased significantly, all of which met the target range of drilling demand.
3.2.3 Effect of Rheology on Inter-System Conversion
Four groups of non-dispersed polymer drilling fluids with different rheological properties were prepared, and the properties before and after conversion were compared, as shown in Table 5.
The data in Table 5 show that the rheological properties of the two drilling fluids do not fluctuate much before and after conversion, and the fluid loss decreases significantly. Therefore, both drilling fluids can be successfully converted into low-potassium anti-collapsing drilling fluids. Among them, the filter vector of the first group is reduced to 4.2 mL, which has strong sealing performance, and the fourth group, especially the dynamic plastic, reaches 0.72, which has the ability of suspension and sand carrying. Therefore, adding 1%QYZ-1 + 3%FSJSS-2 non-dispersed drilling fluid viscosity or dynamic plastic ratio does not affect the conversion, can smoothly implement the conversion of drilling fluid system and type, improve its water loss performance, and rheological properties are stable.
3.2.4 Effect of Salt Content on Intersystem Transformation
Water, 1% NaCl and 2% NaCl were added to the drilling fluid system before and after conversion, and the specific experimental results were shown in Table 6.
The results in Table 6 show that after NaCl was introduced into the non-dispersed polymer drilling fluid, the apparent viscosity and filter vector decreased, the plastic viscosity and fluidity index increased, and the dynamic plastic ratio decreased significantly to below 0.2. With the increase of NaCl concentration in the converted low-potassium anti-collapse drilling fluid, the apparent viscosity and plastic viscosity are increased, the dynamic plastic ratio and flow index change little, the water loss decreases, and the water loss reduction effect is better, which meets the application requirements of the field drilling fluid.
Pressed core pieces (S3 interval) were implanted with clean water, 1%NaCl and 2%NaCl respectively to convert low-potassium anti-collapsing drilling fluids. As shown in Fig. 1 below.
Figure 1: Effect of salt content on inhibition of conversion of low potassium anti-collapsing drilling fluid
As shown in Fig. 1, S3 interval core pieces showed no significant change after soaking in clean water for 2 h, and 1 cm cracks appeared in the upper layer 24 h later, and cracks appeared in the upper edge 24 h later. S3 interval core pieces were immersed in the transformed low-potassium anti-collapsing drilling fluid with 1% NaCl added. After soaking for 2 h, a tiny crack of 0.1 cm appeared at the edge of S3 core pieces. After 24 h, the edge crack deepened and no collapse occurred. S3 core pieces were immersed in converted low-potassium anti-collapsing drilling fluid with 2% NaCl added. After soaking for 2 h, 0.6 cm cracks appeared at the edge of S3 core pieces, and no significant changes were found at the cracks 24 h later. No collapse occurred in the rest parts, indicating that the converted low-potassium anti-collapsing drilling fluid had excellent anti-collapsing effect.
3.3 Performance Evaluation of Converted Drilling Fluid
3.3.1 Basic Performance Evaluation
Take an appropriate amount of prepared drilling fluid and add barite powder according to the national standard GB/T 16783.1-2014 “Oil and Gas Industry Drilling Fluid Field Test Part 1: Water-Based Drilling Fluid”. The experimental results are shown in Table 7.
As shown in Table 7, after the introduction of barite powder, the viscosity of the low-potassium anti-collapse drilling fluid system increased by half, the dynamic-plastic ratio and flow index remained basically unchanged, the filtration loss wall-building performance was greatly improved, and the filtration loss was as low as 4 mL, which met the basic requirements of on-site drilling construction (≤4 mL). It can be seen that the new inhibitor QYZ-1, dispersant FSJSS-2 and aggravating agent introduced in this system have good compatibility.
3.3.2 Evaluation of Inhibition
An appropriate amount of S3 interval shale cuttings and four kinds of low-potassium anti-collapsing drilling fluids of different densities were taken from the Middle Shahejie Formation in the Leijia area of Liaohe Oilfield (2.2.2 section), and the rolling recovery rate of shale cuttings was determined according to standard SY/T56133-2016 “Test Method for Testing Physical and Chemical Properties of Mud Shale by Drilling Fluids”, as shown in Fig. 2 below.
Figure 2: Rolling recovery rate test at different densities
As shown in Fig. 2, the 16-h rolling recovery rate of drilling fluid system No. 1 (r = 1.020 g/cm3) was 94.38%, and that of drilling fluid system No. 2 (r = 1.150 g/cm3) was 96.40%. The rolling recovery rate of drilling fluid system No. 3 (r = 1.206 g/cm3) for 16 h was 96.80%, and that of drilling fluid system No. 4 (r = 1.210 g/cm3) for 16 h was 96.92%, both of which had excellent ability to inhibit core dispersion and good inhibition performance of low-potassium anti-collapsing drilling fluid. The thermal roll recovery rate is higher than 93%, which fully meets the drilling requirements of complex formation in tight oil and gas reservoirs.
3.3.3 Evaluation of Sedimentation Suspension Performance
The settlement stability reflects the ability of the weighting agent particles in the weighted drilling fluid to maintain uniform distribution in the drilling fluid. The low potassium anti-collapse drilling fluid was weighted to the target density (r = 1.293 g/cm³). The settlement and suspension performance of the transformed low potassium anti-collapse drilling fluid was tested, and the results are shown in Table 8.
The experimental data in Table 8 show that the fluid suspension stability of the converted low-potassium anti-collapsing drilling fluid not only has good weighting performance and high weighting density, but also fully meets the general weighting requirements of the bottom boundary at a depth of 3500 meters. Moreover, it has very good weight stability (SF is 0.50) and suspended cuttings stability. After 24 h of static drilling, the upper and lower densities of drilling fluid are identical, and the SF values are both 0.50, reflecting excellent suspension stability, which can meet the needs of wellbore stability in S3 interval and prolong the wellbore collapse period.
(1) After applying a reasonable proportion of agent (QYZ-1: FSJSS-2) to the S3 interval, the non-dispersed polymer drilling fluid can be successfully converted into low potassium anti-collapsing drilling fluid, successfully adapting to the S3 interval. The system is almost unaffected by bentonite, density, rheology and salt, and the introduction of NaCl reduces rheology, which can appropriately reduce the amount of dispersant FSJSS-2.
(2) Laboratory experiments show that the viscosity, flow resistance and power consumption of the converted low-potassium anti-collapsing drilling fluid decrease. The filtration loss is as low as 4 mL, and the filtration wall building performance is greatly improved. There were no significant changes in the flow pattern index and the dynamic plastic ratio. The rolling recovery is 96.92%, which has excellent inhibition performance. The low-potassium anti-slumping drilling fluid (r = 1.293 g/cm3) was weighted and stood for 24 h, and the SF (static settling factor) was 0.50, which had excellent weighted suspension performance and sand carrying performance.
(3) Through the joint action of inhibitor QYZ-1 and dispersant FSJSS-2, not only the moderate dispersion of drilling fluid is controlled, but also the temperature resistance of drilling fluid is improved, fully meeting the needs of rheology, water-loss wall building and anti-collapse of drilling fluid at high temperature. The new system forms the technology of converting drilling fluids to each other for reuse in different sections or runs of the same well, greatly improving the reuse rate of drilling fluids and saving economic costs.
Acknowledgement: None.
Funding Statement: The authors received no specific funding for this study.
Author Contributions: The authors confirm contribution to the paper as follows: study conception and design: Hao Hu, Jian Guan, Shanfa Tang; data collection: Hao Hu, Jialuo Rong; analysis and interpretation of results: Hao Hu, Jialuo Rong; draft manuscript preparation: Hao Hu, Shanfa Tang, Yuanpeng Cheng. All authors reviewed the results and approved the final version of the manuscript.
Availability of Data and Materials: The two agents, named QYZ-1 and FSJSS-2, were developed with the support of Yangtze University and Liaohe Oil Field, and were prepared by Yangtze University laboratories, and their formulations were kept secret.
Conflicts of Interest: The authors declare that they have no conflicts of interest to report regarding the present study.
References
1. Yan, J. N. (2013). Drilling fluid technology, pp. 210–225. Beijing, China: China University of Petroleum Press. [Google Scholar]
2. Yin, B. T. (2022). Development history of drilling fluid technology in tight reservoir in Daqing oilfield. Western Exploration Engineering, 34(10), 103–105+108. [Google Scholar]
3. Deng, H. T., Liu, M. T. (2017). Analysis on drilling fluid technology of horizontal well in Leijia tight reservoir. China Petroleum and Chemical Standards and Quality, 37(15), 181–182. [Google Scholar]
4. Song, C. (2017). Application of strong inhibition polymer drilling fluid to horizontal wells in daqing tight oil reservoirs. Western Exploration Engineering, 29(8), 101–105. [Google Scholar]
5. Liu, R. T. (2020). Research and application of environmentally friendly drilling fluid system for tight oil horizontal wells. Xi’an, China: Xi’an Petroleum University. [Google Scholar]
6. Li, M. B., Sun, M. J., Yang, X. F., Jiang, Q. (2021). Performance evaluation of strong inhibition water-based drilling fluid in longfengshan gas field. Cleaning the World, 37(9), 30–31. [Google Scholar]
7. Yu, M., Wang, J., Wang, F. (2020). High performance drilling fluid technology suitable for liaohe tight oil formation. Drilling and Completion Fluids, 37(5), 578–584. [Google Scholar]
8. Yang, Z. Z., Liu, F. C., Zhou, C., Li, J. C., Yang, P. et al. (2018). Study on the performance of new ultra-high temperature high density oil base mud thinners. Drilling Fluid & Completion Fluid, 35(2), 35–39. [Google Scholar]
9. Guo, Y. B., Guan, S., Liu, Z. Q. (2017). Solid free organic salt drilling fluid for horizontal wells in the Weizhou 12-1 oilfield. Petroleum Drilling Techniques, 45(6), 31–36. [Google Scholar]
10. Gu, S. (2017). Experimental study on high performance water-based drilling fluid for shale gas horizontal wells in Western Hubei. Wuhan, China: China University of Geosciences. [Google Scholar]
11. Sun, C. (2021). Development analysis of high performance water-based drilling fluid technology. Chemical Management, 2021(18), 107–108. [Google Scholar]
12. Yu, D. S., Xu, H., Wu, X. Z., Chen, Y. W., Xu, J. Y. (2020). High performance anti sloughing water-based drilling fluid technology of Ordovician Sangtamu Formation in Manshen 1 well. Petroleum Drilling Technology, 48(5), 49–54. [Google Scholar]
13. Lin, S. Y., Li, Z., Huang, Y., Luo, M., Guo, W. (2018). The development and application of high performance water base muds for HTHP wells in Yinggehai basin. Drilling Fluid & Completion Fluid, 35(2), 44–48. [Google Scholar]
14. Huang, W. A., Niu, X., Shen, Q. Y., Zhou, W., Yang, Z. S. et al. (2016). Anti-sloughing drilling fluid technology for deep sidetracking wells in the Tahe oil fied. Petroleum Drilling Techniques, 44(2), 51–57. [Google Scholar]
15. Lei, Z. Y., Chen, Q., Zhang, P., Liu, X. D., He, B. (2018). Study on optimization of water-based drilling fluid system in Bohai oilfield. Tianjin Science and Technology, 45(9), 22–24+28. [Google Scholar]
16. Li, S. W., Li, Y., Cai, D. S., Li, L. H. (2018). Inhibitory evaluation and research of drilling fluid. China Petroleum and Chemical Standard and Quality, 38(1), 114–115. [Google Scholar]
17. Wang, X. D. (2019). Research and application of a high performance and environment-friendly drilling fluid. Shandong Chemical Industry, 48(11), 74–75. [Google Scholar]
18. Zhang, G. B., Gao, Q. L., Ma, Q. Y. (2019). Discussion on the enhancement of the inhibitive capacity of oil base drilling fluids in shale gas drilling. Drilling Fluid & Completion Fluid, 36(2), 141–147. [Google Scholar]
19. Sheng, Y., Ye, Y., Zhou, Z. S., Zhou, G. X., Wei, L. et al. (2021). Study on wellbore instability mechanism and drilling fluid optimization of Yingsha block in Southwest Tarim basin. E3S Web of Conferences, 252, 03045. [Google Scholar]
20. Basfar, S., Bageri, B., Elkatatny, S. (2023). Effect of Qusaiba shale formation on high-pressure high-temperature drilling fluids properties. Geoenergy Science and Engineering, 224, 211608. [Google Scholar]
21. Paulo, C. F., Liszt, Y. C., Nívia, N. M., Rosangela, C. B. (2021). Evaluation of polymer/bentonite synergy on the properties of aqueous drilling fluids for high-temperature and high-pressure oil wells. Journal of Molecular Liquids, 327, 114808. [Google Scholar]
22. Naeimavi, M., Khazali, F., Abdideh, M., Saadati, Z. (2021). Potassium sorbate as substitute for KCl to shale inhibition in water-base drilling fluids. Energy Sources, Part A: Recovery, Utilization, and Environmental Effects, 43(14), 1691–1705. [Google Scholar]
23. Zhou, J., Nasr-El-Din, H. A. (2017). A new application of potassium nitrate as an environmentally friendly clay stabilizer in water-based drilling fluids. SPE International Conference on Oilfield Chemistry, D021S006R008. [Google Scholar]
24. Balaga, D. K., Mondal, J., Mondal, J., Tatke, V., Bandal, R. et al. (2023). Degradation kinetics of synthetic acrylamide polymers as a viscosity and filtration control additives in the low-density water-based drilling fluid systems. Geoenergy Science and Engineering, 222, 211453. [Google Scholar]
25. Al-Jaberi, J., Bageri, B., Elkatatny, S., Patil, S. (2023). Primary investigation of barite-weighted water-based drilling fluid properties. ACS Omega, 8(2), 2155–2163. [Google Scholar] [PubMed]
26. Davoodi, S., Al-Shargabi, M., Woodc, D. A., Rukavishnikov, V. S., Minaev, K. M. (2022). Thermally stable and salt-resistant synthetic polymers as drilling fluid additives for deployment in harsh sub-surface conditions: A review. Journal of Molecular Liquids, 371, 121117. [Google Scholar]
27. Fan, J. W., Ebadat, A., Metwally, A. S. M. (2022). An experimental study to evaluate the efficiency of silicate drilling fluids on the stabilization of shale layers. Applied Water Science, 12(9), 225. [Google Scholar]
28. Lalji, S. M., Ali, S. I., Haneef, J., Quraishi, R., Kapadia, A. et al. (2022). Changes in Pakistan crude oil properties contaminated by water-based drilling fluids with varying KCL concentrations. Chemical Papers, 76(7), 4189–4201. [Google Scholar]
29. Metwally, M., Nguyen, T., Wiggins, H., Saasen, A., Gipson, M. (2022). Experimental lab approach for water based drilling fluid using polyacrylamide friction reducers to drill extended horizontal wells. Journal of Petroleum Science and Engineering, 212, 110132. [Google Scholar]
30. Rodrigues, R. K., Martins, S. F. C., Naccache, M. F., Naccahe, M. F., Mendes, P. S. (2020). Rheological modifiers in drilling fluids. Journal of Non-Newtonian Fluid Mechanics, 286, 104397. [Google Scholar]
Cite This Article
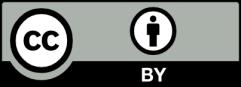
This work is licensed under a Creative Commons Attribution 4.0 International License , which permits unrestricted use, distribution, and reproduction in any medium, provided the original work is properly cited.