Open Access
ARTICLE
Analysis of Fluid-Structure Interaction during Fracturing with Supercritical CO2
1 Xi’an Key Laboratory of Wellbore Integrity Evaluation, Xi’an Shiyou University, Xi’an, 710065, China
2 CCDC Changqing Downhole Technology Company, China National Petroleum Corporation, Xi’an, 712042, China
* Corresponding Author: Jiarui Cheng. Email:
Fluid Dynamics & Materials Processing 2024, 20(12), 2887-2906. https://doi.org/10.32604/fdmp.2024.057056
Received 07 August 2024; Accepted 25 September 2024; Issue published 23 December 2024
Abstract
During the implementation of CO2 fracturing for oil and gas development, the force transfer effect caused by the unsteady flow of high-pressure CO2 fluid can lead to forced vibration of the tubing and ensuing structural fatigue. In this study, a forced vibration analysis of tubing under CO2 fracturing conditions is carried out by taking into account the fluid-structure coupling and related interaction forces by means of the method of characteristics (MOC). The results show that for every 1 m3/min increase in pumping displacement, the fluid flow rate increases up to 3.67 m/s. The flow pressure in the pipe tends to be consistent with the pumping pressure at the initial stage and then decreases with an increase in the pump starting time. When the pumping pressure increases by 10 MPa, the additional stress in the tubing increases by 11.8%, and the peak value of the additional stress at the bottom of the well is the largest. The temperature in the tubing grows with well depth, which causes a phase change in CO2 due to heat absorption. At this time the pressure in the tubing decreases, the fluid flow rate increases by about 1.12 m/s, and the additional stress grows by about 1.5 MPa.Graphic Abstract
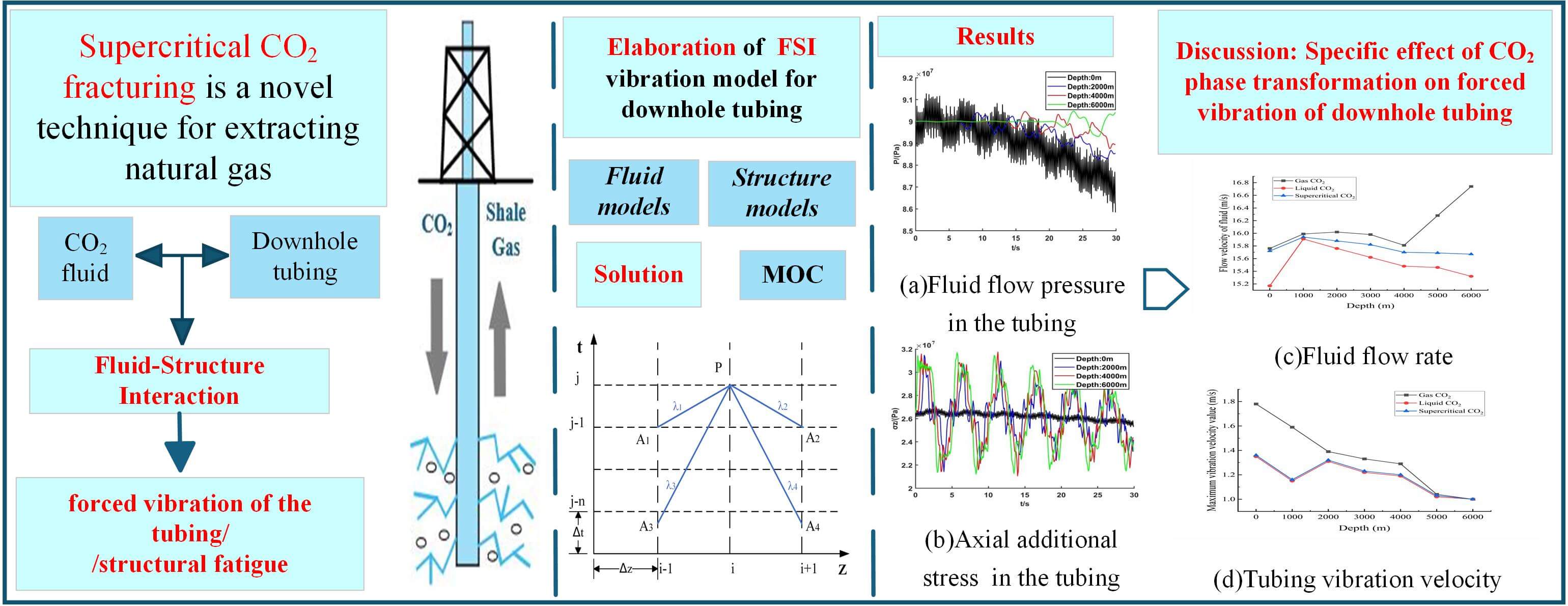
Keywords
Cite This Article
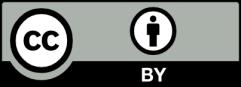
This work is licensed under a Creative Commons Attribution 4.0 International License , which permits unrestricted use, distribution, and reproduction in any medium, provided the original work is properly cited.