Open Access
ARTICLE
Implementation of a Nesting Repair Technology for Transportation Pipeline Repair
1 School of Civil & Resource Engineering, University of Science and Technology Beijing, Beijing, 100083, China
2 Anhui Magang Luohe Mining Industry Co., Ltd., Hefei, 231500, China
* Corresponding Author: Yong Wang. Email:
Fluid Dynamics & Materials Processing 2024, 20(11), 2443-2458. https://doi.org/10.32604/fdmp.2024.051385
Received 04 March 2024; Accepted 21 June 2024; Issue published 28 October 2024
Abstract
Filling methods in the mining industry can maximize the recovery of mineral resources and protect the underground and surface environments. In recent years, such methods have been widely used in metal mines where pipeline transportation typically plays a decisive role in the safety and stability of the entire filling system. Because the filling slurry contains a large percentage of solid coarse particles, the involved pipeline is typically eroded and often damaged during such a process. A possible solution is the so-called nesting repair technology. In the present study, nesting a 127 mm outer diameter pipeline in 151 mm inner diameter borehole is considered to meet the repair objective. First, by using the rheological theory, the pipeline transmission resistance and self-flow conveying range are calculated under different working conditions. It is shown that the pipeline transmission resistance is larger when the inner diameter of casing is 80 mm, and the limit flow rate of vertical pipeline self-flow is 120 m3/h; moreover, when the pipeline diameter is 100 mm and the flow rate is 140 m3/h, the self-flow conveying can be satisfied in most of the underground −455 m stage. Accordingly, a plan is presented for the nesting repair strategy, based on the installation of a drill bit under the casing and lowering the casing into the borehole as if it were a drill pipe. Finally, the outcomes of such a strategy are verified. The filling flow rate range using the new pipelines is found to be in the range from 188.60 to 224.39 m3/h, and its average filling flow rate reaches 209.83 m3/h when conveying 2319.6 m long-distance quarry.Keywords
Cite This Article
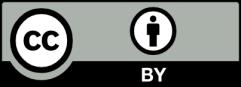
This work is licensed under a Creative Commons Attribution 4.0 International License , which permits unrestricted use, distribution, and reproduction in any medium, provided the original work is properly cited.