Open Access
ARTICLE
The Influence of Chemical Admixtures on the Fluidity, Viscosity and Rheological Properties of Ultra-High Performance Concrete
1 School of Civil Engineering, Architecture and Environment, Hubei University of Technology, Wuhan, 430068, China
2 Building Waterproof Engineering and Technology Research Center of Hubei Province, Hubei University of Technology, Wuhan, 430068, China
* Corresponding Author: Xingyang He. Email:
Fluid Dynamics & Materials Processing 2024, 20(10), 2163-2181. https://doi.org/10.32604/fdmp.2024.055448
Received 27 June 2024; Accepted 19 August 2024; Issue published 23 September 2024
Abstract
To achieve higher strength and better durability, ultra-high performance concrete (UHPC) typically employs a relatively small water-binder ratio. However, this generally leads to an undesired increase in the paste viscosity. In this study, the effects of liquid and powder polycarboxylate superplasticizers (PCE) on UHPC are compared and critically discussed. Moreover, the following influential factors are considered: air-entraining agents (AE), slump retaining agents (SA), and defoaming agents (DF) and the resulting flow characteristics, mechanical properties, and hydration properties are evaluated assuming UHPC containing 8‰ powder PCE (PCE-based UHPC). It is found that the spread diameter of powder PCE is 5% higher than that of liquid PCE. Among the chemical admixtures studied, AEs have the best effect on improving UHPC workability, while DFs have the worst effect. When the addition of AE and SA is 1.25‰ and 14.7% of PCE, paste viscosity reduces by 35% and 19%, respectively compared to the paste with only 8‰ PCE. A low AE dosage (1.25‰) decreases compressive strength by 4.1%, while SA (8.1%) increases UHPC compressive strength by 9.1%. Both AE and SA significantly delay the UHPC hydration process, reducing the hydration heat release peaks by 76% and 27%, respectively.Keywords
List of Abbreviations
UHPC | Ultra-high performance concrete |
PCE | Polycarboxylate superplasticizer |
AE | Air-entraining agent |
SA | Slump retention agent |
DF | Defoamer agent |
PCE-based UHPC | UHPC with 8‰ powdered PCE |
VMA | Viscosity-reducing admixture |
WP | Liquid PCE |
PP | Powder PCE |
Concrete was an essential and highly sought-after building material in the construction and civil engineering sectors [1,2]. However, as construction engineering advances, the performance of traditional concrete no longer satisfies the requirements for certain applications [3]. In response, ultra-high performance concrete (UHPC) was developed as a new type of concrete with extremely high compressive strength (exceeding 120 MPa), flexural strength (exceeding 10 MPa), and excellent durability [3]. UHPC has a porosity of less than 1% and typically includes steel fibers to enhance its mechanical properties [4]. These attributes made UHPC an ideal material for long-span bridges [5], high-rise buildings [6], marine engineering [7], railway engineering [8], and structures with specific functions [9,10]. Compared to conventional concrete, UHPC’s low water-binder ratio (800 kg/m3) and its multi-scale fine-grained mixture design (with a bulk density of 0.825 to 0.855 N/m3) ensure a dense microstructure, thereby reducing matrix porosity [11–13]. The difference in UHPC’s material composition resulted in significantly higher viscosity than that of conventional concrete [14].
The rheological properties of UHPC significantly affected the dispersion and arrangement of matrix particles, influencing their mechanical properties and durability [15]. These properties determined the ease with which cement-based materials can be pumped, formed, and consolidated [16]. UHPC paste typically exhibited shear-thickening behavior [1]. An increase in viscosity can lead to poor UHPC consolidation, resulting in pore defects and affecting overall performance [15]. Semendary et al. [17] demonstrated that when the plastic viscosity was less than 200 Pa·s and the dynamic yield stress was less than 400 Pa, the mixture exhibited good fluidity and pumpability. Yahia [18] evaluated the rheological behavior of high-performance paste mixtures and found a nonlinear relationship between shear stress and strain rate.
Existing research on UHPC indicates that paste rheological properties can be adjusted by modifying the amount of admixture [19–23]. The type of admixture also has an effect on the flow performance of UHPC paste [23–27]. Table 1 shows the influence of different admixture types on concrete flow performance. Polycarboxylate ether (PCE) can improve UHPC paste flow ability, rheology and workability by reducing the water-binder ratio [3]. Compared to other liquid admixtures, PCE has a high water-reducing capacity and excellent dispersibility [28]. Additionally, PCE’s molecular structure allows more stable adsorption on cement particle surfaces and good compatibility with different binder materials [29]. Studies found combining two PCEs can reduce the required PCE dose to achieve the same fluidity [28]. Notably, gradually adding PCE can significantly improve its dispersion effect, increasing UHPC fluidity [4]. Some studies have also used viscosity-modifying admixtures (VMAs) to adjust UHPC matrix rheological properties [30]. VMAs maintain low flow resistance by increasing cement pore solution zero shear viscosity and forming associative structures [31]. Sonebi et al. [32] showed that VMAs exhibit shear thinning behavior at low shear rates but shear thickening behavior at high shear rates. However, at a certain PCE amount, increasing VMA dosages can significantly improve UHPC fluidity [32].
The synergistic effect between chemical admixtures was an important consideration [33]. Nehdi et al. [34] observed that adding admixtures further improves the rheological properties of cementitious materials mixed with PCE, compared to those prepared with PCE alone. When PCE and VMA in combination for UHPC, their concentrations needed optimization to obtain the best rheological properties [35]. Additionally, the combination of VMA and PCE can provide varying degrees of robustness [36]. Fares et al. [37] found that the effect of PCE and VMA in the cement matrix depended on their order of addition and the critical PCE/VMA ratio. When VMA was added first, paste fluidity mainly depended on the water-binder ratio. When VMA was added after PCE, the paste flow affected significantly improved. Yin et al. [38] discussed the feasibility of grouting with waste glass powder (WGP), PCE, and VMA. The fresh state of cement-based materials was closely related to the WGP, PCE, and VMA dosages. When the WGP, PCE, and VMA dosages were 15%, 0.115%, and 0.03%, respectively, the pseudoplastic index was the smallest. Huang et al. [39] introduced a rosin resin-type air-entraining agent based on PCE and VMA. With increasing PCE and AE dosages, the plastic viscosity of self-compacting concrete gradually decreases. Lazniewska-Piekarczyk [40] analyzed the effects of air-entraining admixtures, PCE, and VMA, highlighting that the VMA type affects the fluidity of high-performance self-compacting concrete. Although different admixture types can improve the rheological properties of cement-based materials, a research gap exists in their application effects and synergistic improvement effects on UHPC [41,42].
In this study, the effects of powder and liquid PCE on UHPC paste rheological properties were compared and powder PCE was selected to prepare low-viscosity and high flow UHPC with air-entraining agents (AE), defoaming agents (DF) and slump retaining agents (SA), respectively. The effects of PCE, AE, SA and DF dosages and mixed types on flow properties, viscosity, rheological properties, mechanical properties and hydration process were studied. This study is expected to provide a theoretical reference for designing and preparing low-viscosity and high-flow UHPC admixtures.
2 Raw Materials and Test Methods
The cementitious material employed in this study was sourced from Wuhan Huaxin Cement Co., Ltd.(China), and its chemical composition is detailed in Table 2. The aggregate used was quartz sand, acquired from Wuhan, Hubei. The superplasticizer utilized in this study was a polycarboxylate superplasticizer (PCE), purchased in Wuhan, Hubei Province. Two forms of PCE are depicted in Fig. 1. The water-reducing rates of the PCE is presented in Table 3, with the liquid PCE exhibiting a water-reducing rate of 30.1% and the powder PCE achieving a rate of 52%. The air-entraining agents (AE), slump retaining agents (SA), and defoaming agents (DF) used in this study were all manufactured in Wuhan City, Hubei Province. The AE was anionic surfactant; the SA was polycarboxylate-based slump retaining agent; and the DF was polyether-based defoaming agent.
Figure 1: Two different forms of PCE. (a) Powder and (b) Liquid
2.2 Mix Proportion Design of PCE and Admixture System
The quality of the solid and UHPC admixtures used in this study is presented in Tables 4 and 5. For all mixtures, the mass ratios of water to binder (w/b) and binder to quartz sand were maintained at 0.175 and 1.1, respectively [43,44]. The total water used consisted solely of tap water. The w/b ratio was kept at 0.175 to investigate the diffusion flow, slump, hydration kinetics, and strength of the paste [45]. The dosage of PCE was determined based on the binder mass, while the dosages of the other additives were based on the PCE mass [46]. The paste was mixed for approximately 8 min using a 5-liter mixer. The mixing procedure included 30 s of dry mixing, followed by 180 s for adding the chemical admixtures and water, then 150 s of mixing at low speed, and finally 120 s at medium speed [45].
1) The UPHC mix proportion design of different forms of PCE
To assess the impact of different forms of PCE on the viscosity and strength of UHPC, we initially investigated the influence of powder and liquid PCE on the properties of UHPC paste. The specific ratios are detailed in Table 4. The dosages of powdered PCE were established at 6‰, 8‰, and 10‰ of the cement mass, while the dosages of liquid PCE were set at 6‰, 8‰, and 11‰ of the water mass. An experimental group with an 8‰ dosage of PCE was designated as the control group.
2) The UPHC mix proportion design of chemical admixtures
Based on the PCE tests, we carried out chemical admixture tests, with specific combinations shown in Table 5. We selected the air-entraining agent (AE), slump retaining agents (SA) and defoaming agents (DF) for this study. The AE dosages were set at 1.25‰, 3.75‰ and 6.25‰ of the PCE mass. The SA was added to replace the PCE, with substitution masses of 0.425, 0.6, 0.825 and 1.025 g, respectively. The DF was mixed internally to replace the PCE, with masses of 0.05, 0.1 and 0.15 g, respectively. The experimental group with an 8‰ powder PCE dosage served as the control group.
2.3 Specimen Preparation Methods
The concrete block forming method adhered to the Chinese standard GB/T 50080-2016 [47]. The paste test block preparation followed the requirements of GB/T 8007-2000 [48]. All test blocks were placed in a standard curing room (20°C, 95% humidity) for 24 h. Subsequently, the molds were removed and the blocks continued curing until the designated testing age.
For the compressive strength test, specimens measured 100 mm × 100 mm × 100 mm, with a loading rate of 1.2 to 1.4 MPa/s. Six specimens with the same mix ratio were tested for compressive strength, with the average value taken as the final result [49]. The deviation between the measured and average values did not exceed 15% and the final result was accurate to 0.1 MPa.
The slump test was conducted using a slump cylinder with a base diameter of 100 mm, a top diameter of 200 mm and a height of 300 mm [19]. The test site was ensured to be dry and debris-free. Concrete was filled in three layers, each compacted by vibrating 25 times with a rod from the outside to the inside along the cylinder wall. The surface was flattened using a funnel to ensure smoothness. Afterward, the cylinder was lifted, allowing the concrete to collapse. The slump was calculated by subtracting the height of the highest concrete point from the cylinder height (300 mm).
Due to the high viscosity characteristics of UHPC, this study innovatively applied the asphalt viscosity test method, using Brookfield viscosity as the characterization index. The largest rotor (No. 6) was selected and the speed was fixed at 20 rpm to ensure test accuracy and comparability.
The rheological properties were tested using an RST-SST touchscreen rheometer (Bolefeld Company, USA). Instrument parameters were: torque 100 mN·m, torque resolution 0.15 μN·m and a rate range of 0.01–1300 rpm. The paste was tested at a constant shear rate, sheared at 100 s−1 for 480 s and then stopped [50]. Results were fitted using the Herschel-Bulkley model, as shown in Eq. (1).
τ=τ0+K⋅γn (1)
where τ represents the shear stress, τ0 denotes the yield stress, K is the consistency coefficient, γ is the shear rate and n is the flow index.
Isothermal calorimetry analysis of the mixture was performed at 20°C using a TAM Air isothermal calorimeter. A total of 8 g of paste samples were uniformly stirred and injected into a sealed plastic ampoule, then measured for 120 h.
3.1.1 Different Forms and Dosage of PCE
Fig. 2 depicts the effects of different types and concentrations of polycarboxylate Ether (PCE) on the fluidity of UHPC paste. It can be observed from Fig. 2 that powder PCE (PP) significantly improved the fluidity of fresh UHPC paste compared to liquid PCE (WP), suggesting that powder PCE was more suitable for the UHPC material system studied. When the flow time was 30 s, the fluidity measurements for the PP-6‰, PP-8‰, PP-10‰, WP-6‰, WP-8‰ and WP-11‰ paste was 280, 287, 295, 265, 271 and 285 mm, respectively. It was evident that increasing the PCE dosages gradually enhanced the fluidity of UHPC. Both excessively low and high fluidity can negatively impact the performance of building structures. Therefore, for further studies on the influence of air-entraining agents (AE), slump retaining agents (SA) and defoaming agents (DF) on the basic properties of UHPC, PP-8‰ was chosen as the control group.
Figure 2: The influence of different forms and dosages of PCE on the fluidity of UHPC paste
3.1.2 Different Dosages of AE, SA and DF
Fig. 3 depicts the effect of AE on the fluidity of UHPC paste. Upon adding AE, the fluidity initially increased and then decreased, but all experimental groups exhibited higher fluidity than the control group, particularly AE-1, which increased by 9.4% in fluidity. Low-dosage AE significantly enhanced the fluidity of the paste by introducing tiny bubbles, reducing direct particle contact and facilitating flow [24]. However, excessive AE can cause paste agglomeration, reducing fluidity.
Figure 3: The influence of air-entraining agents (AE) on (a) fluidity and (b) fluidity loss ratio of UHPC paste
Fig. 4 demonstrates the effect of SA on the fluidity of UHPC paste. After adding SA, fluidity initially decreased and then increased. Compared to the control group, the fluidity of SA-2 decreased by 4.3%. With increased SA dosages, fluidity rose, particularly in SA-4, which was 6% higher than the control group. Both SA and PCE operate in a similar manner in cementitious materials, facilitating the dispersion of cement particles and inhibiting aggregation through electrostatic repulsion, steric hindrance, and hydration control [51–53]. Additionally, slump retaining agents commonly include retarders that prolong concrete setting time [52].
Figure 4: The influence of slump retaining agents (SA) on (a) fluidity and (b) fluidity loss ratio of UHPC paste
Fig. 5 depicts the effect of DF on the fluidity of UHPC paste. The fluidity progressively decreased with the addition of DF. The fluidity measurements for the control, DF-1, DF-2 and DF-3 were 235, 230, 224 and 217 mm, respectively. DF-3 exhibited a 7.7% decrease in fluidity compared to the control group, indicating a significant negative effect. The low surface tension of DF reduced the air content and enhanced the friction between paste particles, thereby diminishing fluidity [54].
Figure 5: The influence of defoaming agents (DF) on (a) fluidity and (b) fluidity loss ratio of UHPC paste
Based on these findings, DF had the most substantial negative impact on UHPC paste performance. Lower dosages of AE were found to improve fluidity, while higher dosages of SA had an effect similar to that of lower dosages of AE. Consequently, in subsequent work, we focused on the effects of the AE and SA on the basic properties of UHPC.
3.2 Viscosity Properties of UHPC Paste
3.2.1 Different Dosages of PCE and AE
To assess the effect of additives on UHPC viscosity, we tested the viscosity of UHPC paste. Fig. 6 illustrates the impact of PCE and AEs on UHPC viscosity. Fig. 6a indicates that powder water reducers markedly decrease UHPC viscosity. Fig. 6b demonstrates that increasing the dosage of AE initially led to a decrease in viscosity, followed by an increase. All experimental groups exhibited lower viscosity than the control group, with AE-1 achieved a 35% reduction. Zhang et al. [55] reported that incorporating 10% of 4 μm limestone powder decreased UHPC plastic viscosity by 22.8%, while Li et al. [56] found that adding 15 wt% bentonite increased it by 16%. The dosage of AE enhanced surface adsorption and foam height, thereby improving dispersibility. Nonetheless, excessive AE increased paste air content, raising viscosity due to increased contact area between paste particles [31].
Figure 6: The influence of (a) PCE and (b) air-entraining agents (AE) on the viscosity of UHPC
3.2.2 Different Dosages of SA and DF
Fig. 7 displays the influence of SA and DF on the viscosity of UHPC paste. As shown in Fig. 7a after adding SA, the viscosity of UHPC paste showed a trend of increasing first and then decreasing [51]. The viscosity of SA-2 increased by 7.5% compared with the control group, while the viscosity of SA-4 decreased by 18.7% compared with the control group. The addition of higher dosages of SA significantly reduced the viscosity of UHPC paste. This effect can be attributed to the high dosages of SA, which facilitate the redispersion and dilution of fine powder agglomerates in the concrete, thereby lowering the viscosity of the UHPC paste. This observation aligns with the trend of paste fluidity changes observed after the addition of SA [57]. As shown in Fig. 7b, the viscosity of UHPC paste increased after adding DF and the viscosity values of all test groups were higher than those of the control group. With the increase of DF dosages, the viscosity of UHPC paste continued to increase, especially in the DF-3, where the viscosity reached 14,526 Pa·s, which was 51% increase over the control group. The addition of DF had a pronounced negative effect on the viscosity of the paste. The primary function of DF was to reduce the air content in the concrete, which increased the contact surface between the paste, enhanced the cohesion between the paste and increased the viscosity of the paste [58].
Figure 7: The influence of (a) slump retaining agents (SA) and (b) defoaming agents (DF) on the viscosity of UHPC
3.3 Rheological Properties of UHPC Paste
To assess the viscosity reduction effect of AE, we conducted rheological tests on UHPC paste. Fig. 8 depicts the impact of AEs on the rheological properties of UHPC. The test results for the groups were well-fitted to the H-B model, with correlation coefficients exceeding 0.99. Specific rheological parameters are shown in Table 6. Fig. 8a indicates that with increasing AE dosages, the shear stress of UHPC paste initially decreases and then increases. Table 6 shows that the yield stress increases as the AE dosage is increased. Fig. 8b indicates that UHPC viscosity follows the similar trend, with AE-2 exhibiting the lowest apparent viscosity. High AE dosages reduced viscosity by increasing air content and bubble volume proportion, enhancing plastic viscosity [59]. Fig. 8c demonstrates a strong correlation between static yield strength and apparent viscosity after adding AE.
Figure 8: Air-entraining agents (AE) effect on UHPC (a) yield stress, (b) apparent viscosity and (c) correlation between static yield strength and apparent viscosity
Fig. 9 shows the effect of SA on UHPC rheology. Fig. 9a reveals that increasing SA dosages initially increases and then decreases shear stress. Under the same shear rate, SA-2 exhibited the highest shear stress, while SA-4 showed the lowest. Fig. 9b indicates that both control and experimental groups exhibited increased apparent viscosity with shear rate. SA-2 had the highest apparent viscosity, while SA-4 had the lowest. Rheological data fitting results aligned with the H-B model, with correlation coefficients exceeding 0.99. Specific rheological parameters are shown in Table 7. The yield stress of SA-2 was the lowest, while SA-4’s was the highest. Fig. 9c shows a strong correlation between static yield strength and apparent viscosity after adding SA.
Figure 9: Slump retaining agents (SA) effect on UHPC (a) yield stress, (b) apparent viscosity and (c) correlation between static yield strength and apparent viscosity
3.4 Hydration Heat of UHPC Paste
Fig. 10 demonstrates the impact of AE on the hydration heat of ultra-high-performance concrete (UHPC). The incorporation of AE resulted in a rightward shift of the hydration exothermic peak for UHPC, markedly delaying the hydration exothermic process. As depicted in Fig. 10a, the control group’s hydration exothermic peak occurred at 24 h, whereas the AE group’s peak was observed at 90 h. Kubissa et al. [60] reported a 33% delay in the peak of hydration heat release when 0.1 and 0.2 wt% AE were added to concrete. Similarly, Qin et al. [61] found that both PCE and AE delayed the hydration reaction time by approximately 35%. Zhang et al. [62] observed that AE dosages ranging from 0 to 0.2 wt% inhibited the hydration reaction time of cement. With AE addition, the peak value of hydration heat release in UHPC significantly decreased. For the control group, the peak was 1.65 mW/g, while for the AE group, it was 0.4 mW/g. Increasing AE dosages further reduced the peak value, though the differences were minimal. According to Fig. 10b, AE addition also drastically reduced the cumulative heat release of UHPC, with the AE group’s cumulative heat release being one-third that of the control group. Increasing AE dosages had little effect on cumulative heat release. AE reduced the surface tension of the concrete system, introducing more tiny bubbles, which buffered the cement hydration process [63].
Figure 10: The influence of air-entraining agents (AE) on the (a) Heat flow and (b) cumulative heat of UHPC
Fig. 11 depicts the effect of SA on the hydration heat of UHPC. Fig. 11a showed that increasing SA dosages decreased the exothermic peak and delayed the hydration process. The control group’s peak appeared at 24 h, whereas the SA group’s peak appeared at 48 h, with SA-4 peaking at 60 h. Massarweh et al. [64] found that using 0.03, 0.05 and 0.08 wt% SA delayed the water exothermic peak by 23%, 31% and 46%, respectively. The peak values of hydration heat release for SA-1, SA-2 and SA-3 were similar, but they decreased significantly for SA-4, possibly due to the negative effect of excessive SA on UHPC hydration performance. From Fig. 11b, it is evident that SA incorporation reduced the cumulative heat release of UHPC. All SA groups had lower cumulative heat release than the control group, with SA-2 having a relatively high cumulative heat release. Compared to Fig. 10a, the hydration exothermic peak of UHPC with SA addition was relatively higher, possibly due to the chemical composition and effect of SA being similar to PCE [46].
Figure 11: Effect of slump retaining agents (SA) on the (a) Heat flow and (b) cumulative heat of UHPC
3.5 Hydration Heat of UHPC Paste
3.5.1 Different Dosages of PCE and AE
Fig. 12 shows the effects of PCE and AE on the compressive strength of UHPC. In Fig. 12a, the compressive strength of UHPC with powder PCE was higher than that with liquid PCE. Notably, when the powder PCE dosage was 8‰, the 28-day compressive strength of UHPC reached 117.2 MPa. However, further increasing the powder PCE dosage reduced compressive strength. Fig. 12b indicates that the compressive strength of UHPC at various ages was lower than that of the control group after AE addition. As AE dosages increased, UHPC strength further decreased. The 28-day compressive strength of AE-1 was 112.4 MPa, 4% lower than the control group, while AE-3 was 89.7 MPa, 23% lower. This suggested that AE significantly influenced UHPC compressive strength, with higher AE dosages weakening mechanical properties [65]. The effect was mainly due to AE altering the pore structure of concrete, including pore size and distribution, affecting compressive strength.
Figure 12: Effect of (a) PCE and (b) air-entraining agents (AE) on the compressive strength of UHPC
3.5.2 Different Dosages of AE and SA
The effect of SA and DF on the compressive strength of UHPC is shown in Fig. 13. It can be found from Fig. 13a that the compressive strength of UHPC increased first and then decreased after the addition of SA. The compressive strength of UHPC was improved when an appropriate amount of SA was added. Good fluidity made UHPC paste uniformly hydrated, thus forming a more uniform microstructure [24]. When the dosages of SA were too high, the compressive strength began to decrease. When the quality of the SA was controlled at about 1‰ of the cementitious material, the mechanical properties of UHPC could be improved. The main function of the SA was to maintain the slump of the concrete and it will also have a certain impact on the final strength development of the concrete. Some studies have pointed out that the SA may have a certain adverse effect on the early strength of concrete, but it had little effect on the strength after 28 days or longer.
Figure 13: Effect of (a) slump retaining agents (SA) and (b) defoaming agents (DF) on the compressive strength of UHPC
Fig. 13b demonstrated that increasing DF dosages initially increases and then decreases UHPC compressive strength. DF-1 exhibited the best mechanical properties, with a 28-day compressive strength of 127.9 MPa, 9% higher than the control group. However, excessive DF dosages decrease compressive strength, with DF-3 being 18% lower than the control group. Studies indicate a correlation between bubble content and concrete strength [54]. DF reduces bubble content, enhancing strength, but excessive DF causes supersaturation, negatively affecting UHPC strength [58].
This study compared the effects of liquid and powder polycarboxylate superplasticizer (PCE) and evaluated the impact of air-entraining agents (AE), slump retaining agents (SA) and defoaming agents (DF) on the flow characteristics, mechanical and hydration properties of PCE-based UHPC. The following conclusions were drawn:
1. Under the same dosage, UHPC with powder PCE exhibited higher flow and mechanical properties than with liquid PCE. At 8‰ powder PCE, the 28-day compressive strength reached 117.2 MPa, 31% higher than with liquid PCE.
2. AE significantly improved the flow and mechanical properties of PCE-based UHPC paste, though this effect diminished with increased dosage. At 1.25‰ AE dosages, UHPC exhibited fluidity of 257 mm, viscosity of 6274 Pa·s and 28-day compressive strength of 112.4 MPa.
3. Increasing SA dosages initially decreased and then increased the flow characteristics of PCE-based UHPC paste. At 14.69% PCE (SA-4), UHPC fluidity was 249 mm and viscosity was 7836 Pa·s. Although DF improved compressive strength, it reduced paste fluidity.
4. Both AE and SA delayed the hydration heat release process of PCE-based UHPC paste, with AE having a more significant effect. The hydration heat peak for AE was about 0.4 mW/g, whereas for SA, it was about 1.2 mW/g. AE and SA dosages had minimal effects on the hydration process.
5. For high early strength, reduce AE and SA dosages while increasing powder PCE. For high fluidity, moderately increase AE and SA, controlling powder PCE dosages.
Acknowledgement: The authors express their gratitude to the editors and reviewers for their insightful comments that helped to raise the caliber of our manuscript.
Funding Statement: The authors would like to acknowledge the Key Research and Development Program of Hubei Province (2022BCA082 and 2022BCA077).
Author Contributions: The authors confirm contribution to the paper as follows: study conception and design: Xingyang He, Jin Yang; data collection: Ying Su, Jin Yang; analysis and interpretation of results: Hailong Zhao, Mengdi Zhu, Jingyi Zeng; draft manuscript preparation: Hailong Zhao, Mengdi Zhu, Jin Yang. All authors reviewed the results and approved the final version of the manuscript.
Availability of Data and Materials: The data used to support the findings of this study are available from the corresponding author upon request.
Ethics Approval: Not applicable.
Conflicts of Interest: The authors declare that they have no conflicts of interest to report regarding the present study.
References
1. Shi CJ, Wu ZM, Xiao JF, Wang DH, Huang ZY, Fang Z. A review on ultra high performance concrete: part I. Raw Mat Mix Design Constr Build Mater. 2015;101:741–51. [Google Scholar]
2. Emad W, Mohammed AS, Kurda R, Ghafor K, Cavaleri L, Qaidi SMA, et al. Prediction of concrete materials compressive strength using surrogate models. Structures. 2022;46:1243–67. doi:10.1016/j.istruc.2022.11.002. [Google Scholar] [CrossRef]
3. Meng W, Valipour M, Khayat KH. Optimization and performance of cost-effective ultra-high performance concrete. Mater Struct. 2017;50(1):16. [Google Scholar]
4. Wang C, Yang CH, Liu F, Wan CJ, Pu XC. Preparation of ultra-high performance concrete with common technology and materials. Cem Concr Compos. 2012;34(4):538–44. doi:10.1016/j.cemconcomp.2011.11.005. [Google Scholar] [CrossRef]
5. Honarvar E, Sritharan S, Rouse JM, Aaleti S. Bridge decks with precast UHPC waffle panels: a field evaluation and design optimization. J Bridge Eng. 2016;21(1):13. [Google Scholar]
6. Cao X, Xie XD, Zhang TY, Du GF. Bond-slip behavior between high-strength steel tube and ultra-high performance concrete. Structures. 2022;47:1498–510. [Google Scholar]
7. Fang H, Zhu HD, Li AJ, Liu HC, Luo SL, Liu YL, et al. A multiscale material-structure-hydroelasticity coupled analytical model for floating sandwich structures with hierarchical cores. Mar Struct. 2021;79:28. [Google Scholar]
8. Bae Y, Pyo S. Ultra high performance concrete (UHPC) sleeper: structural design and performance. Eng Struct. 2020;210:14. [Google Scholar]
9. Zeyad AM, Hakeem IY, Amin M, Tayeh BA, Agwa IS. Effect of aggregate and fibre types on ultra-high-performance concrete designed for radiation shielding. J Build Eng. 2022;58:15. [Google Scholar]
10. Jung M, Lee YS, Hong SG, Moon J. Carbon nanotubes (CNTs) in ultra-high performance concrete (UHPC): dispersion, mechanical properties, and electromagnetic interference (EMI) shielding effectiveness (SE). Cem Concr Res. 2020;131:15. [Google Scholar]
11. Wang SW, Wang B, Zhu HT, Chen G, Li ZZ, Yang L, et al. Ultra-high performance concrete: mix design, raw materials and curing regimes—a review. Mater Today Commun. 2023;35:20. [Google Scholar]
12. Liu Q, Andersen LV, Wu M. Prediction of concrete abrasion depth and computational design optimization of concrete mixtures. Cem Concr Compos. 2024;104:538–44. [Google Scholar]
13. Yin TY, Yu R, Liu KN, Wang ZY, Fan DQ, Wang SY, et al. Precise mix-design of Ultra-High Performance Concrete (UHPC) based on physicochemical packing method: from the perspective of cement hydration. Constr Build Mater. 2022;352:16. [Google Scholar]
14. Ahmad J, Majdi A, Elhag AB, Deifalla AF, Soomro M, Isleem HF, et al. A step towards sustainable concrete with substitution of plastic waste in concrete: overview on mechanical, durability and microstructure analysis. Crystals. 2022;12(7):23. doi:10.3390/cryst12070944. [Google Scholar] [CrossRef]
15. Meng WN, Khayat KH. Improving flexural performance of ultra-high-performance concrete by rheology control of suspending mortar. Compos Pt B-Eng. 2017;117:26–34. doi:10.1016/j.compositesb.2017.02.019. [Google Scholar] [CrossRef]
16. Yoo DY, Yoon YS. A review on structural behavior, design, and application of ultra-high-performance fiber-reinforced concrete. Int J Concr Struct Mater. 2016;10(2):125–42. doi:10.1007/s40069-016-0143-x. [Google Scholar] [CrossRef]
17. Semendary AA, Svecova D. Bond characterization and interfacial coefficients at precast UHPC and cast-in-place UHPC interface. J Mater Civ Eng. 2021;33(7):20. doi:10.1061/(ASCE)MT.1943-5533.0003755. [Google Scholar] [CrossRef]
18. Yahia A. Shear-thickening behavior of high-performance cement grouts—Influencing mix-design parameters. Cem Concr Res. 2011;41(3):230–5. doi:10.1016/j.cemconres.2010.11.004. [Google Scholar] [CrossRef]
19. Shui LL, Sun ZP, Yang HJ, Yang X, Ji YL, Luo Q. Experimental evidence for a possible dispersion mechanism of polycarboxylate-type superplasticisers. Adv Cem Res. 2016;28(5):287–97. doi:10.1680/jadcr.15.00070. [Google Scholar] [CrossRef]
20. Li PP, Yu QL, Brouwers HJH. Effect of PCE-type superplasticizer on early-age behaviour of ultra-high performance concrete (UHPC). Constr Build Mater. 2017;153:740–50. doi:10.1016/j.conbuildmat.2017.07.145. [Google Scholar] [CrossRef]
21. Teng L, Zhu J, Khayat KH, Liu JP. Effect of welan gum and nanoclay on thixotropy of UHPC. Cem Concr Res. 2020;138:12. doi:10.1016/j.cemconres.2020.106238. [Google Scholar] [CrossRef]
22. Yoo DY, Banthia N, Yoon YS. Effectiveness of shrinkage-reducing admixture in reducing autogenous shrinkage stress of ultra-high-performance fiber-reinforced concrete. Cem Concr Compos. 2015;64:27–36. doi:10.1016/j.cemconcomp.2015.09.005. [Google Scholar] [CrossRef]
23. Han J, Fang H, Wang KJJ. Design and control shrinkage behavior of high-strength self-consolidating concrete using shrinkage-reducing admixture and super-absorbent polymer. J Sustain Cen-Based Mater. 2014;3(3–4):182–90. doi:10.1080/21650373.2014.897268. [Google Scholar] [CrossRef]
24. Yoo SW, Kwon SJ, Jung SH. Analysis technique for autogenous shrinkage in high performance concrete with mineral and chemical admixtures. Constr Build Mater. 2012;34:1–10. doi:10.1016/j.conbuildmat.2012.02.005. [Google Scholar] [CrossRef]
25. Wu ZM, Shi CJ, He W, Wu LM. Effects of steel fiber content and shape on mechanical properties of ultra high performance concrete. Constr Build Mater. 2016;103:8–14. doi:10.1016/j.conbuildmat.2015.11.028. [Google Scholar] [CrossRef]
26. Zhang YY, Duan L, Xin HH, Wang CS. Shrinkage behavior of ultra-high-performance concrete (UHPC) in cold winter conditions with shrinkage reducing agent (SRA) and expansive agent (EA). Constr Build Mater. 2024;436:15. [Google Scholar]
27. Khan M, Chu SH, Deng XW, Wang YH. Protection of steel tube against corrosion using self-prestressing UHPC prepared with expansive agent and steel fibers. Structures. 2022;37:95–108. doi:10.1016/j.istruc.2021.12.076. [Google Scholar] [CrossRef]
28. Plank J, Schroefl C, Gruber M, Lesti M, Sieber R. Effectiveness of polycarboxylate superplasticizers in ultra-high strength concrete: the importance of PCE compatibility with silica fume. J Adv Concr Technol. 2009;7(1):5–12. doi:10.3151/jact.7.5. [Google Scholar] [CrossRef]
29. Hanehara S, Yamada K. Interaction between cement and chemical admixture from the point of cement hydration, absorption behaviour of admixture, and paste rheology. Cem Concr Res. 1999;29(8):1159–65. doi:10.1016/S0008-8846(99)00004-6. [Google Scholar] [CrossRef]
30. Gonzalez-Avina JV, Hosseinpoor M, Yahia A, Durran-Herrera A. New biopolymers as viscosity-modifying admixtures to improve the rheological properties of cement-based materials. Cem Concr Compos. 2024;146:18. [Google Scholar]
31. Bessaies-Bey H, Khayat KH, Palacios M, Schmidt W, Roussel N. Viscosity modifying agents: key components of advanced cement-based materials with adapted rheology. Cem Concr Res. 2022;152:20. [Google Scholar]
32. Sonebi M. Rheological properties of grouts with viscosity modifying agents as diutan gum and welan gum incorporating pulverised fly ash. Cem Concr Res. 2006;36(9):1609–18. doi:10.1016/j.cemconres.2006.05.016. [Google Scholar] [CrossRef]
33. Yuan Q, Liu WT, Wang C, Deng DH, Liu ZQ, Long GC. Coupled effect of viscosity enhancing admixtures and superplasticizers on rheological behavior of cement paste. J Cent South Univ. 2017;24(9):2172–9. doi:10.1007/s11771-017-3626-2. [Google Scholar] [CrossRef]
34. Nehdi M, Al-Martini S. Coupled effects of high temperature, prolonged mixing time, and chemical admixtures on rheology of fresh concrete. ACI Mater J. 2009;106(3):231–40. [Google Scholar]
35. Meng WN, Khayat KH. Effect of graphite nanoplatelets and carbon nanofibers on rheology, hydration, shrinkage, mechanical properties, and microstructure of UHPC. Cem Concr Res. 2018;105:64–71. doi:10.1016/j.cemconres.2018.01.001. [Google Scholar] [CrossRef]
36. Qin WH, Zhang ZC, Xi Z, Wang DF. Experimental investigation on the progressive collapse resistance of UHPC-RC composite beam-column structures. Eng Struct. 2023;284:13. [Google Scholar]
37. Fares G, Al-Negheimish A, Alhozaimy AMM, Khan MI. Polycarboxylate superplasticizer and viscosity modifying agent: mode of addition and its effect on cement paste rheology using image analysis. J Build Eng. 2022;48:17. [Google Scholar]
38. Yin WS, Li XP, Sun T, Chen YZ, Xu F, Yan G, et al. Utilization of waste glass powder as partial replacement of cement for the cementitious grouts with superplasticizer and viscosity modifying agent binary mixtures: rheological and mechanical performances. Constr Build Mater. 2021;286:12. [Google Scholar]
39. Huang FL, Li HJ, Yi ZL, Wang Z, Xie YJ. The rheological properties of self-compacting concrete containing superplasticizer and air-entraining agent. Constr Build Mater. 2018;166:833–8. doi:10.1016/j.conbuildmat.2018.01.169. [Google Scholar] [CrossRef]
40. Lazniewska-Piekarczyk B. The influence of admixtures type on the air-voids parameters of non-air-entrained and air-entrained high performance SCC. Constr Build Mater. 2013;41:109–24. doi:10.1016/j.conbuildmat.2012.11.086. [Google Scholar] [CrossRef]
41. Yang J, Zeng JY, He XY, Su Y, Tan HB, Min HP, et al. Utilization of submicron autoclaved aerated concrete waste to prepare eco-friendly ultra-high performance concrete by replacing silica fume. J Clean Prod. 2022;376:13. doi:10.1016/j.jclepro.2022.134252. [Google Scholar] [CrossRef]
42. Yang J, Zeng JY, He XY, Hu HC, Su Y, Bai H, et al. Eco-friendly UHPC prepared from high volume wet-grinded ultrafine GGBS slurry. Constr Build Mater. 2021;308:13. doi:10.1016/j.conbuildmat.2021.125057. [Google Scholar] [CrossRef]
43. Shah HA, Yuan Q, Photwichai N. Use of materials to lower the cost of ultra-high-performance concrete—A review. Constr Build Mater. 2022;327:29. doi:10.1016/j.conbuildmat.2022.127045. [Google Scholar] [CrossRef]
44. Su X, Ren ZG, Li PP. Review on physical and chemical activation strategies for ultra-high performance concrete (UHPC). Cem Concr Compos. 2024;149:35. doi:10.1016/j.cemconcomp.2024.105519. [Google Scholar] [CrossRef]
45. Mosaberpanah MA, Eren O. Effect of quartz powder, quartz sand and water curing regimes on mechanical properties of UHPC using response surface modelling. Adv Concr Constr. 2017;5(5):481–92. [Google Scholar]
46. Mendonca F, Hu J. Impact of chemical admixtures on time-dependent workability and rheological properties of ultra-high-performance concrete. ACI Mater J. 2021;118(6):383–94. [Google Scholar]
47. Ministry of Housing and Urban-Rural Development People’s Republic of China. Standard for test method of performance on ordinary fresh concrete; 2016. GB/T 50080-2016. https://www.chinesestandard.net/PDF/English.aspx/GBT50080-2016 [Accessed 2024]. [Google Scholar]
48. American Standard test methods. Standard specification for chemical admixtures for concrete; 2012. C494/C494M. [Google Scholar]
49. Standard for test method of ultra-high performance concrete; 2021. ASTM Standard C1856/C1856M. [Google Scholar]
50. Wang YB, Xu L, He XY, Su Y, Miao WJ, Strnadel B, et al. Hydration and rheology of activated ultra-fine ground granulated blast furnace slag with carbide slag and anhydrous phosphogypsum. Cem Concr Compos. 2022;133:12. doi:10.1016/j.cemconcomp.2022.104727. [Google Scholar] [CrossRef]
51. Zhang XS, Yu RG, Chen JP. Preparation and properties of controlled compacting filling material based on admixture technique. Emerg Mater Res. 2018;7(1):47–51. doi:10.1680/jemmr.16.00021. [Google Scholar] [CrossRef]
52. Zeng FK, Zhang JC, Wei XN, Li BP. Preparation and properties study of a low-cost Ammonia Carboxylate concrete superplasticizer. Nanosci Nanotechnol Lett. 2019;11(11):1603–6. doi:10.1166/nnl.2019.3045. [Google Scholar] [CrossRef]
53. Ye QQ, Han YF, Liu T, Bai Y, Chen YJ, Li JZ, et al. Magnesium oxychloride cement reinforced via D-gluconic acid sodium salt for slow-curing, with enhanced compressive strength and water resistance. Constr Build Mater. 2021;280:10. doi:10.1016/j.conbuildmat.2021.122487. [Google Scholar] [CrossRef]
54. Puthipad N, Ouchi M, Rath S, Attachaiyawuth A. Enhanced entrainment of fine air bubbles in self-compacting concrete with high volume of fly ash using defoaming agent for improved entrained air stability and higher aggregate content. Constr Build Mater. 2017;144:1–12. doi:10.1016/j.conbuildmat.2017.03.049. [Google Scholar] [CrossRef]
55. Zhang C, Wang JW, Zhang XZ, Hou J, Huang JL, Feng SX, et al. Influence of limestone powder on water film thickness and plastic viscosity of UHPC. Case Stud Constr Mater. 2024;20:13. doi:10.1016/j.cscm.2024.e03036. [Google Scholar] [CrossRef]
56. Li K, Leng Y, Xu LL, Zhang JJ, Liu KN, Fan DQ, et al. Rheological characteristics of Ultra-High Performance Concrete (UHPC) incorporating bentonite. Constr Build Mater. 2022;349:21. [Google Scholar]
57. Bhattacherjee S, Jain S, Santhanam M. A method to increase the workability retention of concrete with limestone calcined clay based cementitious system using a dispersing agent containing sodium hexametaphosphate. Cem Concr Compos. 2022;132:11. doi:10.1016/j.cemconcomp.2022.104624. [Google Scholar] [CrossRef]
58. Wang SX, Zhang GF, Wang ZJ, Huang TY, Wang PM. Effect of defoaming agent on the properties of cement mortars with hydroxyethyl methyl cellulose through adjusting air content gradient. Cem Concr Compos. 2023;139:13. doi:10.1016/j.cemconcomp.2023.105024. [Google Scholar] [CrossRef]
59. Cao L, Shi FT, Qiu MZ, Chen W, Cao P, Zhou CJ. Effects of air entraining agent on the rheological properties and electrochemical parameters of cement mortar. Constr Build Mater. 2022;344:10. [Google Scholar]
60. Kubissa W, Jaskulski R, Grzelak M. Torrent air permeability and sorptivity of concrete made with the use of air entraining agent and citric acid as setting retardant. Constr Build Mater. 2021;268:15. doi:10.1016/j.conbuildmat.2020.121703. [Google Scholar] [CrossRef]
61. Qin L, Gao XJ, Li QY. Influences of coal fly ash containing ammonium salts on properties of cement paste. J Environ Manage. 2019;249:9. doi:10.1016/j.jenvman.2019.109374. [Google Scholar] [PubMed] [CrossRef]
62. Zhang RL, Hao ZF, Ma LN, Guo HZ, Xiong ZY, Xu L. Research on concrete strength growth and micromechanism under negative temperature curing based on equal strength theory. J Mater Civ Eng. 2021;33(10):9. doi:10.1061/(ASCE)MT.1943-5533.0003877. [Google Scholar] [CrossRef]
63. Lazniewska-Piekarczyk B. The influence of chemical admixtures on cement hydration and mixture properties of very high performance self-compacting concrete. Constr Build Mater. 2013;49:643–62. doi:10.1016/j.conbuildmat.2013.07.072. [Google Scholar] [CrossRef]
64. Massarweh O, Maslehuddin M, Al-Dulaijan SU, Shameem M. Performance evaluation of heavy oil fly ash as a retarder of Portland cement hydration. J Build Eng. 2021;34:15. doi:10.1016/j.jobe.2020.101881. [Google Scholar] [CrossRef]
65. Puthipad N, Ouchi M, Attachaiyawuth A. Effects of fly ash, mixing procedure and type of air-entraining agent on coalescence of entrained air bubbles in mortar of self-compacting concrete at fresh state. Constr Build Mater. 2018;180:437–44. doi:10.1016/j.conbuildmat.2018.04.138. [Google Scholar] [CrossRef]
Cite This Article
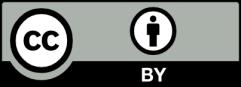
This work is licensed under a Creative Commons Attribution 4.0 International License , which permits unrestricted use, distribution, and reproduction in any medium, provided the original work is properly cited.