Open Access
ARTICLE
Analysis of a Strong-Inhibition Polyamine Drilling Fluid
Engineering Technology Research Institute, Petro China Southwest Oil & Gas Field Company, Chengdu, 610000, China
* Corresponding Author: Rui Wang. Email:
Fluid Dynamics & Materials Processing 2023, 19(9), 2431-2447. https://doi.org/10.32604/fdmp.2023.027604
Received 05 November 2022; Accepted 14 December 2022; Issue published 16 May 2023
Abstract
Drilling technologies based on oil-based drilling fluids and strong inhibitory saltwater fluids are affected by drawbacks such as downhole accidents where sticking and wellbore instabilities occur. Existing polyamine drilling fluids also exhibit problems such as easy decomposition and poor inhibition performances. In order to mitigate these issues, additives can be used, such as polyamine inhibitors and the synthesis of nanometer filtrate reducers. Tests conducted in the frame of this study with a polyamine drilling fluid and such additives show that this fluid has the same inhibitory, plugging, lubricating, and wellbore-stability performances as oil-based drilling fluids. However, it has long-term anti-wear performances even better than those of oil-based drilling fluids. The outcomes of a series of comparisons with other sample cases (other wells) are reported and the advantages related to the proposed fluid discussed in detail.Graphic Abstract
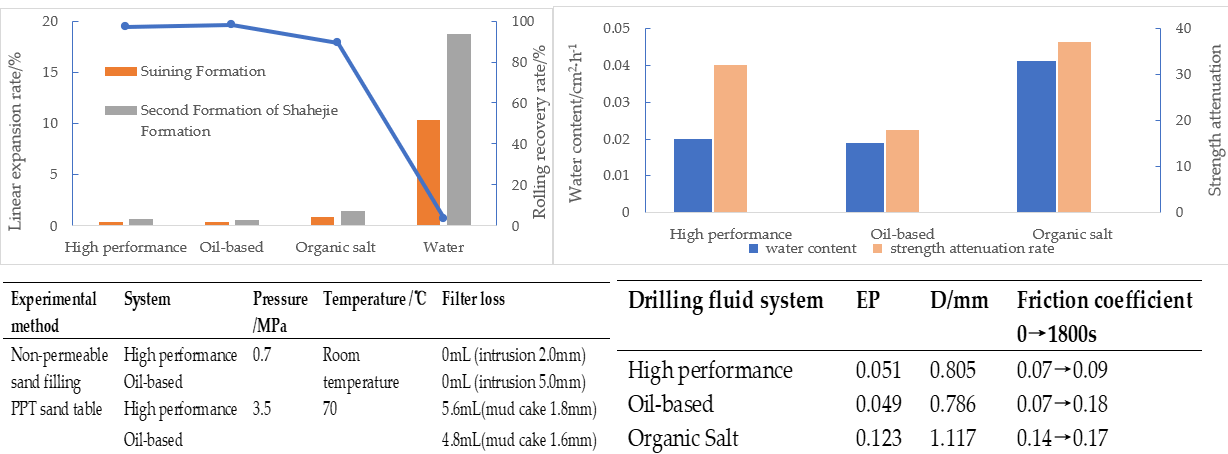
Keywords
Nomenclature
AV | Apparent viscosity |
PV | Plastic viscosity |
YP | Yield point |
Φ6 | Six-speed rotating viscometer for a 6-rpm reading |
Φ3 | Six-speed rotating viscometer for a 3-rpm reading |
EP | Lubrication coefficient |
HTHP | High temperature and high pressure |
CMC | Carboxymethyl cellulose |
FLHTHP | High temperature and high pressure filtration loss |
D | Diameter |
In recent years, with the continuous reduction of drilling construction costs, the scope of using oil-based drilling fluids has been greatly limited. The strong inhibition of water-based drilling fluids developed for shale formations has also achieved good application results at the same time, such as strong inhibition of amine drilling fluid, silicate drilling fluid, and organic or inorganic salt water drilling fluid. The above-mentioned water-based drilling fluids have good shale inhibition and plug-ging performance to a certain extent. However, the lubricating effect of water-based drilling fluids is poorer than that of oil-based drilling fluids, which cannot reduce the drilling friction. The polyamine and silicate inhibitors used in these water-based drilling fluids have a poor inhibitory effect and are mostly polymers that are not easy to decompose, while the high concentration of chloride salts (KCl, NaCl, CaCl2) used will have a serious impact on soil and water bodies [1–3]. Therefore, it is urgent to develop a set of high-performance water-based drilling fluids with low cost and performance com-parable to oil-based drilling fluids [4,5].
High-performance water-based drilling fluid technology has become increasingly mature and widely used worldwide. It has been applied on-site in many countries and regions and has achieved good results [6–8], such as in the Gulf of Mexico, the North Sea, Canada, and Australia. It is also applied in many blocks in China, and the application effect is generally better than that of oil-based drilling fluid in the same block, such as Changqing Sulige, Xinjiang Mahu, Sichuan-Chongqing region [9–12]. The high-performance water-based drilling fluid developed by Baker Hughes with polyamine as shale inhibitor does not contain salt substances, and its inhibition and lubricity are equivalent to those of oil-based drilling fluids. It has been tested in the U.S. Gulf of Mexico, Arabian Gulf, and Bahrain onshore oil fields, and is widely used in onshore drilling, continental shelf drilling, offshore deep-water drilling, etc. The strongly inhibited water-based drilling fluid HYDRO-GUADR, developed by Halliburton, has good wellbore stability and rheology in deep-water low temperature wells. It is mainly used in deep water operations in the Gulf of Mexico. The strongly inhibited water-based drilling fluid ULTRADRILL, developed by MI, has been applied on a large scale in the United States and Australia. Field tests show that the drilled well sections have regular diameter, no leakage, and the casing runs smoothly. Good results have been achieved when applied in oilfields such as Dagang, Jidong, Zhanjiang and other oilfields in China. The environment-friendly strong inhibitive drilling fluid technology developed by Wen [13] was successfully used in Well Rong 18-3X. In addition, many scientific research institutions and oilfield enterprises, such as China University of Petroleum, Hubei Hanke Company, Liaohe Oilfield, and Qinghai Oilfield, have also carried out relevant research and achieved certain results in the field application. However, these high-performance water-based drilling fluids are not suitable for Well Jinqian XX (Well JQXX for short), which is located in Sichuan, China.
This paper takes Well JQXX as the research object and the target formation is No. 6 sand body of the second section of Shaximiao formation. According to the analysis of the data of the drilled ad-jacent wells, it can be seen that the mudstone content in this block is high, the average clay mineral content is above 33%, and the content in some parts is as high as 51.6%, which leads to a high risk of bit balling and difficulty in maintaining the rheological properties of drilling fluids. When oil-based drilling fluid and strongly inhibited KCL organic salt drilling fluid were used in the adjacent wells of Well JQXX, there were sticking and jamming phenomena. In some wells, wellbore instability also occurred, which could not meet the requirements of drilling construction in this block. Therefore, aiming at the problems of sticking and wellbore instability in this block, a polyamine inhibitor and micro/nano fluid loss reducer were developed indoor, and a set of polyamine drilling fluid system with high performance and strong inhibition (referred to as high-performance drilling fluid in the following diagrams) was introduced. This system has strong reservoir protection ability, which is comparable to the inhibition, plugging and lubrication performance of oil-based drilling fluid, and superior to the long-term wear resistance of oil-based drilling fluid; The system has a good application effect in Well JQXX. There was no sticking during drilling, and tripping was smooth as a whole, which is of great practical significance for high-quality and efficient exploration and development in this area.
2 Technical Difficulties and Countermeasures of Drilling Fluid
The target formation of Well JQXX is No. 6 sand body of the second section of Shaximiao formation. The reservoir rocks are mainly feldspar quartz sandstone, feldspar sandstone, and feldspar lithic sandstone. The mineral composition analysis is shown in Fig. 1. Analysis of the statistics of the complex situation from the data of drilled adjacent wells (see Table 1) shows that the complex situation mainly occurred in No. 6 sand body of the second section of Shaximiao formation, where adhesion sticking occurred with both oil-based and water-based drilling fluids. There were also some wells with borehole wall instability. The technical difficulties and related countermeasures of drilling fluids are as follows:
i) Borehole instability and block drop.
According to the analysis of the causes of wellbore instability and block drop [14], it may be related to the fact that Penglaizhen formation is a long section of mudstone and the second section of Shaximiao formation is interbedded with sandstone and mudstone. The thin mudstone layer has low mechanical strength, and the formation microfractures are then developed. It is necessary to strengthen the drilling fluid inhibition performance and plugging performance of the drilling fluid.
ii) Pressure differences in the whipstock section and horizontal section are prone to ad-hesion sticking.
With the change of well deviation azimuth and long horizontal extension, the tripping friction is large. The high gamma mudstone formation in the Shaximiao formation is easy to collapse and diameter extension. The decreased sand carrying efficiency in the whipstock and horizontal section may form a cuttings bed, resulting in borehole obstruction and sand plug. The depth of the adjacent well 4# is 3260 m, and the vertical depth is 2157 m. When the salt water drilling fluid was used for drilling in the third spud, the average well diameter expansion rate was 19.75%, the maximum frictional resistance during tripping was 20–38 T, and the maximum frictional resistance during drill-down was 40 t. The acid soak method was used for stuck freeing, and the loss time was 145.07 h, which seriously increased the drilling cost. It is suggested to improve the lubrication performance of the drilling fluid, which is beneficial to the extension of long horizontal sections and prevents the sticking of pressure differential [15].
iii) The drill bit balling in a large section of mudstone.
The mudstone content of the well is high, with an average clay mineral content of more than 33% and as high as 51.6% in some parts. Therefore, the risk of bit balling is high, and the maintenance of drilling fluid rheology is difficult. This requires improving the inhibition performance of drilling fluid and reducing the drilling fluid filtration, reducing chemical instability, controlling the drilling fluid filtration, improving the rheological control capa-bility of drilling fluid, and preventing bit mud inclusion during rapid drilling [16,17].
Figure 1: Mineral composition analysis of Shaximiao mudstone (a) all rock mineral content (b) relative content of clay minerals
3 Selection and Synthesis of Main Additives
3.1.1 Synthesis of the Polyamine Inhibitors
In order to improve the inhibitory performance of high-performance and strong-inhibiting polyamine drilling fluids [18,19], a polyamine inhibitor was developed in the laboratory.
In the first step, 60 g maleic anhydride and 130 g ethylene glycol amine were mixed uniformly and then transferred to the reactor. After 4 h of reaction under vacuum at 180°C, the temperature is lowered to 90°C;
In the second step, 40 g of citric acid was added to react with the amine bond for 2 h, and the product obtained after cooling to room temperature was polyamine inhibitor WQ-N.
The infrared spectrum of the polyamine inhibitor WQ-N is shown in Fig. 2. The wavenumber of 600∼750 cm−1 is the oscillating vibration absorption band of -NH2, and 3370.64 cm−1 is the non-association contraction vibration absorption peak of -NH. The increase of the number of the two groups can enhance the adsorption of amine functional groups and mud shale, and improve the inhibition ability of polyamine inhibitors in mud shale. 1270 cm−1 is the stretching vibration of C-N bond, and 1690 cm−1 is the strong absorption peak of C-N. 3987.63 cm−1 is the stretching vibration absorption peak of -CH2. Its mechanism is mainly based on its long-chain macromolecular structure and various hydration and adsorption groups, which can strongly adsorb on the surface of clay and drilling cuttings, coat the drilling cuttings, plug the micro-cracks on the drilling cuttings and prevent free water from entering the interior of drilling cuttings, slow down the hydration expansion and spalling speed of drilling cuttings.
Figure 2: The infrared spectrum of polyamine inhibitor WQ-N
In this way, the growth of low-density solid content in the drilling fluid can be effectively controlled, and the interlayer hydration can be inhibited to achieve the purpose of inhibiting the hydration expansion of shale.
3.1.2 Evaluation of the Inhibition Performance
40% bentonite powder was added into fresh water in the laboratory to compare and evaluate the inhibitory effects of common inhibitors PF-UHIB and WQ-N in the market (see Table 2, the rheological data were measured by a six-speed rotating viscometer according to API standards). The experimental conditions were as follows: 80°C * 16 h. It shows that the blank slurry was too thick to be beyond the measurement value range of the instrument. The viscosity of WQ-N and PF-UHIB was low, and both of them have good inhibition effect. The WQ-N has lower viscosity and stronger inhibition ability, and can better inhibit the hydration and dispersion of bentonite.
The clay mineral content of this well is as high as 27.8%, which requires the drilling fluid to have a strong ability to inhibit the hydration and expansion of clay. In order to further evaluate the inhibitory ability of the polyamine inhibitor WQ-N, the inhibitor’s ability to prevent hydration and swelling of bentonite was evaluated indoors. 3%PF-UHIB, 7%KCl, 3%WQ-N, 5%WQ-N and 7%WQ-N were added into fresh water and fresh water with 25% bentonite, respectively. The experimental results of anti-inflation rate are shown in Fig. 3. It shows that the anti-swelling effect of 3%WQ-N is comparable to that of 7%KCl. With the increase of the concentration of WQ-N, the anti-swelling effect increases from 92.8% to 97.6%, which can effectively inhibit the hydration and dispersion of bentonite.
Figure 3: Evaluation of the ability of the inhibitor to prevent hydration and dispersion of cuttings
The reservoir rocks of Well JQXX are mainly feldspar quartz sandstone, feldspar sandstone, and feldspar lithic sandstone. And wellbore instability and block dropping exist in the drilling operation. Therefore, the influence of drilling fluid on shale in drilling process is simulated through immersion test indoors. Put rock samples from the second section of Shaximiao formation in Well JQXX in fresh water + 3%PF-UHIB, water + 7%KCl, water + 3%WQ-N, and water + 5%WQ-N, respectively. Observe the changes of rock samples immersed in a 90°C constant temperature oven for 12, 24 and 48 h, and evaluate the shale hydration expansion performance of several inhibitors. The 48 h rock sample state is shown in Fig. 4. It shows that the rock samples soaked in 3%PF-UHIB and 7%KCl solutions showed more obvious cracks than the 3%WQ-N. The rock samples in 3%WQ-N solution showed a small crack, and the rock samples in 5%WQ-N solution showed no change. The results show that WQ-N can effectively enhance the strength of field rock samples and inhibit the hydration and dispersion of field rock samples.
Figure 4: Effect of inhibitor on on-site rock samples: (a) 3%PF-UHIB; (b) 7%KCl; (c) 3%WQ-N; (d) 5%WQ-N
3.2 Synthesis of Nanometer Filtrate Reducer
The laboratory has developed a micro-nano-size degradable material filtrate reducer [19–22] MZ was developed in the laboratory. The specific production steps are as follows: first, add 200 g of isopropanol and 20 g of ethyl cellulose into the round bottom flask, stir them until dissolved, and ultrasonically disperse it in an ultrasonic cell grinder for 1.5 h. Second, the pH value was adjusted to 8 with an aqueous NaOH solution with a concentration of 30%; nitrogen was introduced and heated to 30°C, continued to stir for 20 h, and then heated to 80°C. In the third step, 40 g of chloroacetic acid is dissolved in 3 g of isopropanol and slowly added dropwise to the liquid in the above-mentioned round bottom flask at a rate of one drop for 30 s to carry out an etherification reaction for 3 h. The mixture was cooled to room temperature and centrifuged and the centrifuged precipitate was washed with ethanol for three times. The fourth step was to dry the obtained solid product at 60°C for 24 h, and the crushed powder is the nanometer filtrate reducer MZ. The enlarged molecular morphology is shown in Fig. 5, and the particle size distribution is shown in Fig. 6, the function mechanism is shown in Fig. 7.
Figure 5: Molecular morphology of MZ
Figure 6: Particle size distribution of MZ
Figure 7: Mechanism action of MZ
Because of a certain amount of hydroxyl and carboxyl groups in the molecular structure, the nanomembrane filtrate reducer has strong surface electricity and hydration ability and strong dispersion stability. The nano cellulose has excellent characteristics such as a large specific surface area, strong stiffness, and strong surface activity, and it is easier to form a stable adsorption layer on the clay surface through hydrogen bonding, to forma spatial network structure, to improve the colloidal stability of drilling fluid, and preventing bentonite from coalescing. It is conducive to forming a dense filter cake, thereby greatly reducing the filtration loss of drilling fluid.
Through the use of micro-nano-size degradable material MZ, it can maintain the uniformity of polyamine drilling fluid slurry with high performance and strong inhibition, op-timize the rheological property of drilling fluid, improve the rapid migration ability of particles in drilling fluid and the instant plugging of filtration channel, further improve the fil-tration effect, block the shale micro fractures and pores, and prevent the invasion of drilling fluid filtrate and the transmission of pore pressure.
The sulfonated lignite resin and sodium carboxymethyl cellulose (CMC), which are commonly used as filtration reducers for water-based drilling fluids in the market. The apparent viscosity and API filtration amount of the three filtrate reducers at 25°C were evaluated, which reflect the filtration reduction ability. Prepare the base slurry (400 ml distilled water + 0.64 g Na2CO3 + 16 g bentonite). Then 2 g MZ, 2 g sulfonated lignite resin and 2 g CMC were added to the base slurry respectively. The experimental data are shown in Fig. 8. As can be seen from Fig. 8, the apparent viscosity of the three filtrate reducers is 6 mPa⋅s, and the addition of the three filtrate reducers will not increase the viscosity of the base slurry. Among the three filtrate reducers, MZ has the strongest filtrate reduction ability, and the API filtrate loss decreases from 125 to 30 ml.
Figure 8: Comparison of apparent viscosity and filtration reduction ability of three filtrate reducers
3.3 Optimization of Environmentally-Friendly Lubricants
The conventional physical and chemical properties of four environmentally friendly lubricants [23–26] were compared. Experimental methods: add lubricant 3g1#, 3g2#, 3g3#, 3g4# to the base slurry in 3.2, respectively. After stirring 1200 r/min for 20 min, the lubrication coefficient was measured by FANN extreme pressure lubricator, and the NF-1 mud cake adhesion coefficient tester was used to measure the lubrication coefficient (EP), adhesion coefficient of mud cake and calculate the reduction rate. The results are shown in Table 3. It shows that the physical and chemical properties of the four lubricants are all up to the standard, and the 3# lubricant with the reduction rate of the viscosity coefficient of the mud cake and the reduction rate of the lubrication coefficient above 85% is select as the lubricant for high-performance and strong inhibitory polyamine drilling fluid.
4.1 Performance Evaluation of the System
The basic formula of high-performance and strong-inhibiting polyamine drilling fluid: 1% bentonite slurry + 0.1% NaOH + 0.15% Na2CO3 + 0.1% coating agent (FA367) + 0.3% viscosifier (low viscosity polyanionic cellulose) + 3% nanometer filtrate reducer (MZ) + 3% lubricant (3# environmentally friendly lubricant) + 6% KCl + 5% polyamine inhibitor (WQ-N) + 3% micro-nano plugging agent + barite (weighted to 1.60 sg).
4.1.1 Evaluation of Temperature Resistance
Polyamine and other inhibitors are not resistant to high temperature, cannot inhibit the hydration dispersion of high montmorillonite content formation, and have poor compatibility. In order to ensure the performance in drilling, it is necessary to evaluate the temperature resistance performance of the high-performance and strong inhibition polyamine drilling fluid system. The specific temperature resistance performance is shown in Fig. 9. It shows that the rheological properties, the high temperature and high pressure filtration loss and lubricating properties of the system have no significant change with the increase of temperature, indicating that the system still has good rheological properties and lubricating properties at 90°C.
Figure 9: Evaluation of temperature resistance (a) Viscosity (AV, PV) (b) Dynamic shear (YP) before and after 6 rpm (c) API filtration loss and EP; filtration loss at 60°C, 70°C, 80°C, 90°C and psi500 (FLHTHP)
4.1.2 Evaluation of Resistance to Density Change
In the process of drilling, with the increase of drilling depth, it is necessary to increase the density of the drilling fluid system to balance the pressure between the formations, which will increase the pressure difference between the drilling fluid system and the formation, leading to an increase in the filtration of the drilling fluid and a thickening of the mud cake, thereby increasing the frictional resistance between the drilling tool and the mud cake, and increasing the friction between the borehole wall and drill pipe, causing downhole accidents such as support pressure, differential pressure sticking [23–25]. Under an aging temperature of 70°C, the effect of density change on high-performance and strong-inhibition polyamine drilling fluid was evaluated in the laboratory. The specific data are shown in Fig. 10. It shows that when the density gradually increases from 1.50 to 1.70 sg, the viscosity of the system gradually increases within a controllable range, and the HTHP filtration loss changed slightly. Furthermore, it has good lubricating performance under the density of 1.50∼1.70 sg, indicating that the drilling fluid performs well at the density of 1.70 sg.
Figure 10: Effect of density change on system performance (a) Viscosity (AV, PV) (b) Dynamic shear (YP) and before and after 6 rpm (c) API filtration loss, EP and filtration loss at 90°C and psi500 (FLHTHP)
4.1.3 Evaluation of Anti-Pollution Performance
The evaluation of salt resistance and calcium resistance was carried out indoors, and the experimental results are shown in Fig. 11. It shows that with the increase of NaCl concentration, the viscosity and filtration loss of the system had no significant change, and the lubrication coefficient increased slightly. The lubricant can be supplemented in time according to the actual situation to improve the lubrication performance of the system. When the amount of CaSO4 increased from 0% to 3%, the viscosity and shear force of the system increased, the lubrication coefficient increased, and the HTHP filtration loss changed little. In general, the high performance and strong inhibition polyamine drilling fluid system has strong salt and calcium resistance, up to 8% salt and 3% calcium resistance.
Figure 11: Evaluation of anti-pollution performance (a) Viscosity (AV, PV) (b) Dynamic shear (YP) before and after 6 rpm (c) API filtration loss and EP; Filtration loss at 90°C and psi500 (FLHTHP)
4.2 Performance Comparison of Different Drilling Fluid Systems
Considering the complex downhole conditions that are prone to occur in this block, the high-performance and strong-inhibiting polyamine drilling fluid, the oil-based drilling fluid, and organic salt water drilling fluid used in adjacent wells and water have been tested for inhibition performance, plugging performance, lubrication performance, and wellbore stability. The formulas of oil-based drilling fluid and organic salt water drilling fluid are as follows:
The formula of oil-based drilling fluid: Oil-water phase (3# white oil: water = 85:15, the water is an aqueous solution of CaCl2 with a concentration of 25%) + 3% main emulsifier + 1% auxiliary emulsifier + 3% alkalinity regulator + 1.5% wetting agent + 3% organic soil + 3% filtrate reducer + 2% plugging agent + 1% flow pattern regulator + barite (weighted to 1.60 sg).
The formula of organic salt water drilling fluid: 2% bentonite slurry + 0.1% NaOH + 0.15% Na2CO3 + 0.3% viscosifier (low viscosity polyanionic cellulose) + 0.4% coating inhibitor (polyacrylamide) + 0.1% tackifier (biopolymer) + 3% lubricant + 2% polyamine + 3% filtrate reducer + 3% plugging agent + 6% KCL + barite (weighted to 1.60 sg).
4.2.1 Comparison of Inhibition
The content of clay minerals in this well is as high as 27.8%. The second section of Shaximiao is prone to adhesion sticking, which requires the drilling fluid to inhibit clay hydration expansion strongly and has good lubrication. The cuttings of the Suining formation and the second section of the Shaximiao formation and the inhibition performance of the three drilling fluid systems was compared by evaluating the rolling recovery rate and the linear expansion rate of the cuttings. The experimental results are shown in Fig. 12. It can be seen form the figure that the rolling recovery rate of the high-performance and strong-inhibiting polyamine drilling fluid is as high as 97%. The linear expansion rates of the Suining formation and the second section of the Shaximiao formation are 0.43% and 0.68%, respectively, showing the excellent inhibition of the high-performance drilling fluid, which is comparable to oil-based drilling fluid.
Figure 12: Comparison results of inhibition performance of three drilling fluid systems: linear expansion rates (left) and rolling recovery rate (right) of the three drilling fluid systems and water
According to the porosity and permeability of the formation, 16 artificial cores were made from the mudstone cuttings of Weizhou formation in combination with epoxy resin cement. The artificial mudstone core mechanical-chemical coupling experiment was carried out on the obtained cores in the laboratory and tested the strength parameters and attenuation rate of the test cores after soaking them in different drilling fluids for 24, 48, and 72 h. The least square method was applied to fit the characteristic equation of mudstone adsorbed water with the measured water adsorption data to obtain the water absorption diffusion coefficients of rocks immersed in different drilling fluids and to evaluate the inhibition performance of the three drilling fluids. The experimental results are shown in Fig. 13. It shows that with the increase of immersion time, the parameters such as compressive strength, elastic modulus, and internal friction angle of the rock decrease significantly. The strength attenuation rate of oil-based drilling fluid is 18%, and the water content is 0.018896 cm2/h; the attenuation rate of salt water drilling fluid is about 37%, and the water content is 0.041224 cm2/h; the attenuation rate of high-performance strong inhibition polyamine drilling fluid is about 32%, and the water content is 0.02004 cm2/h. It shows that the inhibition of drilling fluid from strong to weak is organic drilling fluid > high-performance strong inhibition polyamine drilling fluid > organic salt water drilling fluid.
Figure 13: Comparison results of inhibition performance of three drilling fluid systems: water content (left) and strength attenuation rate (right) of the three drilling fluid systems
4.2.2 Evaluation of Plugging Performance
In the laboratory, the plugging ability of the two systems was evaluated by comparing the penetration depth of oil-based drilling fluid and high-performance strong inhibition polyamine drilling fluid into the sand layer with the non-permeable sand filling experiment method (60∼80 mesh sand bed, 0.7 MPa) and PPT sand table experiment method (sand table permeability was 4.5D, 70°C, 3.5 MPa). The experimental results are shown in Table 4. In the non-permeable sand filling experiment and PPT sand table experiment, the loss and intrusion depth data of high performance and strong inhibition polyamine drilling fluid system and oil-based drilling fluid have little difference, indicating that the high-performance drilling fluid system has the same excellent plugging performance as the oil-based drilling fluid.
4.2.3 Lubrication Performance Evaluation
The extreme pressure lubrication coefficient (EP) and four ball antiwear spot diameter (D) of three systems (high performance and strong inhibition polyamine drilling fluid, oil-based drilling fluid and organic salt drilling fluid) were measured with FANN extreme pressure lubrication instrument and micro control full-automatic four ball friction tester, and the extreme pressure lubrication performance, antiwear performance and long-term antiwear performance of the three systems were compared and evaluated salt water. The experimental results are shown in Table 5, which shows that the extreme pressure lubrication performance and anti-wear performance of high-performance and strongly inhibited polyamine drilling fluid are comparable to those of oil-based drilling fluid and significantly better than those of organic salt water drilling fluid. In the long-time anti-wear test from 0 to 1800 s, the friction coefficient of oil-based drilling fluid increased significantly with the increase of friction time, and the friction coefficient of high-performance strong inhibition polyamine drilling fluid did not change significantly with the increase of friction time. It shows that the lubricating film in the drilling fluid system is strong and tough and has good long-term anti-wear performance, and the lubricating effect in the long-term drilling process is better than that of the oil-based drilling fluid.
4.2.4 Evaluation of Wellbore Stability
Shale of the second section of Shaximiao formation was soaked in water, high-performance strong inhibitory polyamine drilling fluid, oil-based drilling fluid, and orgainic salt water drilling fluid for 36 h. The changes of shale micro-fractures before and after soaking is observed by scanning electron microscope, see Fig. 14. The experimental results show that the shale fractures in water, high performance, and strong inhibition polyamine drilling fluid, oil-based drilling fluid, and organic salt water drilling fluid are increased by 285%, 138%, 106%, and 240%, respectively. Shale has the highest stability in oil-based drilling fluid and the minimum change after 36 h. The second is high-performance and strong-inhibitory polyamine drilling fluid.
Figure 14: Microcracks in shale after soaking for 36 h (a) Water (b) High-performance strong inhibitory polyamine drilling fluid (c) Oil-based drilling fluid (d) Organic salt water drilling fluid
The design depth of Well JQXX is 3641 m, the completion depth is 3620 m with an open hole length of 3218 m, and a horizontal length of 1000 m. In the initial drilling stage, the amount of environmentally friendly lubricant was small, and the lubricity coefficient was slightly large. During the drilling process, the amount of environmentally friendly lubricant was increased, and the lubricity coefficient of the drilling fluid was maintained below 0.08, the drilling torque was stable, and the tripping and tripping out were relatively smooth. The HTHP filtrate loss was less than 8.5 ml, and the solid content was less than 30%. The upper formation has been soaked for more than 50 days, and the borehole wall remains stable. There was no sticking during the drilling process, and the tripping is smooth as a whole, which proves that the high-performance and strong-inhibiting polyamine drilling fluid has good plugging and anti-sloughing performance and lubricating performance, which is suitable for drilling operations in the formation in this area.
i) The high-performance and strong-inhibiting polyamine drilling fluid system still has good plugging and lubricating performance at 90°C. The density range is wide, and the drilling fluid maintains good rheological properties under the density of 1.60∼1.75 g⋅cm−³; the salt resistance can reach 8%, the calcium resistance can reach 3%, and it has strong salt and calcium resistance ability. It can effectively inhibit the hydration and expansion of the cuttings of Suining formation and the second section of Shaximiao formation and the bentonite powder and maintain a low lubrication coefficient.
ii) The comparison experiments with oil-based drilling fluids and organic salt water drilling fluids used in adjacent wells show that the inhibition performance, plugging performance, lubrication performance, and wellbore stability performance of the high-performance and strong-inhibiting polyamine drilling fluid system are comparable to those of the oil-based drilling fluid, and the long-term wear resistance is superior to the oil-based drilling fluid.
iii) The high-performance and strong-inhibiting polyamine drilling fluid system had stable performance in the drilling process of Well JQXX in Sichuan, and there was no sticking and wellbore instability during, which proves that the system is suitable for application in this block. The comprehensive promotion will positively promote the developing of drilling fluid treatment agents and new drilling fluid systems, showing good social benefits.
Funding Statement: The authors received no specific funding for this study.
Conflicts of Interest: The authors declare that they have no conflicts of interest to regarding the present study.
References
1. Abdo, J., AL-Sharji, H., Hassan, E. (2016). Effects of nano-sepiolite on rheological properties and filtration loss of water-based drilling fluids. Surface and Interface Analysis, 48(7), 522–526. https://doi.org/10.1002/sia.5997 [Google Scholar] [CrossRef]
2. Bakke, T., Klungsøyr, J., Sanni, S. (2013). Environmental impacts of produced water and drilling waste discharges from the Norwegian offshore petroleum industry. Marine Environmental Research, 92, 154–169. https://doi.org/10.1016/j.marenvres.2013.09.012 [Google Scholar] [PubMed] [CrossRef]
3. Balaban, R. D. C., Vidal, E. L. F., Borges, M. (2015). Design of experiments to evaluate clay swelling inhibition by different combinations of organic compounds and inorganic salts for application in water base drilling fluids. Applied Clay Science, 105, 124–130. https://doi.org/10.1016/j.clay.2014.12.029 [Google Scholar] [CrossRef]
4. Gautam, S., Guria, C., Rajak, V. K. (2022). A state of the art review on the performance of high-pressure and high-temperature drilling fluids: Towards understanding the structure-property relationship of drilling fluid additives. Journal of Petroleum Science and Engineering, 213(6), 110318. https://doi.org/10.1016/j.petrol.2022.110318 [Google Scholar] [CrossRef]
5. Konate, N., Salehi, S. (2020). Experimental investigation of inhibitive drilling fluids performance: Case studies from United States shale basins. Energies, 13(19), 5142. https://doi.org/10.3390/en13195142 [Google Scholar] [CrossRef]
6. Morton, E. K., Bomar, B. B., Schiller, M. W., Gallet, J. D., Azar, S. J. et al. (2005). Selection and evaluation criteria for high-performance drilling fluids. SPE Annual Technical Conference and Exhibition, pp. 2671–2683. Dallas, Texas. https://doi.org/10.2118/96342-MS [Google Scholar] [CrossRef]
7. Leaper, R., Anderson, D., Dye, W. M., Hansen, N. A., Al-Ansari, A. et al. (2005). Diverse application of unique high performance water based mud technology in the Middle East. SPE/IADC Middle East Drilling Technology Conference and Exhibition, Dubai, United Arab Emirates. https://doi.org/10.2118/97314-MS [Google Scholar] [CrossRef]
8. Alemdar, A., Öztekin, N., Güngör, N., Ece, Ö. I., Erim, F. B. (2005). Effects of polyethyleneimine adsorption on the rheological properties of purified bentonite suspensions. Colloids and Surfaces A: Physicochemical and Engineering Aspects, 252(2–3), 95–98. https://doi.org/10.1016/j.colsurfa.2004.10.009 [Google Scholar] [CrossRef]
9. Wang, Z. H., Liu, Y. X., Liu, X. G., Xia, C. P. (2020). Research on high performance water-based drilling fluid system with polyamine temperature resistance and environmental protection. Cleaning World, 36(8), 103–104. [Google Scholar]
10. Hou, J., Liu, Y. G., Li, H. (2015). Application of high-performance water-based drilling fluid for horizontal wells in tight reservoirs of daqing oilfield. Petroleum Drilling Techniques, 43(4), 59–65. https://doi.org/10.11911/syztjs.201504011 [Google Scholar] [CrossRef]
11. Qiu, Z. S., Zhong, H. Y., Huang, W. A. (2005). Review and prospect of water-based drilling fluid formula combination. Acta Petrolei Sinica, 22(3), 35–39. [Google Scholar]
12. Chen, Z. H., Lan, L., Yang, W. J., Xia, H. Y. (2013). Application of polyamine imitation oil-based drilling fluids in the long horizontal section in Western Sichuan. Chemical Engineering of Oil & Gas, 42(5), 501–505. [Google Scholar]
13. Wen, L. (2021). Application of environment-friendly strong inhibition drilling fluid technology in rong 18-3X well. Liaoning Chemical Industry, 50(7), 1009–1011+1105. https://doi.org/10.14029/j.cnki.issn1004-0935.2021.07.021 [Google Scholar] [CrossRef]
14. Gholami, R., Elochukwu, H., Fakhari, N., Sarmadivaleh, M. (2018). A review on borehole instability in active shale formations: Interactions, mechanisms and inhibitors. Earth-Science Reviews, 177, 2–13. https://doi.org/10.1016/j.earscirev.2017.11.002 [Google Scholar] [CrossRef]
15. Perumalsamy, J., Gupta, P., Sangwai, J. (2021). Performance evaluation of esters and graphene nanoparticles as an additives on the rheological and lubrication properties of water-based drilling mud. Journal of Petroleum Science and Engineering, 204, 108680. https://doi.org/10.1016/j.petrol.2021.108680 [Google Scholar] [CrossRef]
16. Rana, A., Arfaj, M. K., Saleh, T. A. (2019). Advanced developments in shale inhibitors for oil production with low environmental footprints–A review. Fuel, 247, 237–249. https://doi.org/10.1016/j.fuel.2019.03.006 [Google Scholar] [CrossRef]
17. Ezeakacha, C., Salehi, S., Hayatdavoudi, A. (2017). Experimental study of drilling fluid’s filtration and mud cake evolution in sandstone formations. Journal of Energy Resources Technology, 139(2), 022912. https://doi.org/10.1115/1.4035425 [Google Scholar] [CrossRef]
18. Ranaa, A., Saleh, T. A. (2022). An investigation of polymer-modified activated carbon as a potential shale inhibitor for water-based drilling muds. Journal of Petroleum Science and Engineering, 216, 110763. https://doi.org/10.1016/j.petrol.2022.110763 [Google Scholar] [CrossRef]
19. Jain, R., Mahto, V. (2015). Evaluation of polyacrylamide/clay composite as a potential drilling fluid additive in inhibitive water based drilling fluid system. Journal of Petroleum Science and Engineering, 133, 612–621. https://doi.org/10.1016/j.petrol.2015.07.009 [Google Scholar] [CrossRef]
20. Karakosta, K., Mitropoulos, A. C., Kyzas, G. Z. (2021). A review in nanopolymers for drilling fluids applications. Journal of Molecular Structure, 1227, 129702. https://doi.org/10.1016/j.molstruc.2020.129702 [Google Scholar] [CrossRef]
21. Abdullah, A. H., Ridha, S., Mohshim, D. F., Yusuf, M., Kamyab, H. (2022). A comprehensive review of nanoparticles: Effect on water-based drilling fluids and wellbore stability. Chemosphere, 308, 136274. https://doi.org/10.1016/j.chemosphere.2022.136274 [Google Scholar] [PubMed] [CrossRef]
22. Balaga, D. K., Kulkarni, S. D. (2022). A review of synthetic polymers as filtration control additives for water-based drilling fluids for high-temperature applications. Journal of Petroleum Science and Engineering, 215, 110712. https://doi.org/10.1016/j.petrol.2022.110712 [Google Scholar] [CrossRef]
23. Hasan, M. L., Abidin, N. A. Z., Singh, A. (2018). The rheological performance of guar gum and castor oil as additives in water-based drilling fluid. Materials Today: Proceedings, 5(10), 21810–21817. https://doi.org/10.1016/j.matpr.2018.07.036 [Google Scholar] [CrossRef]
24. William, J. K. M., Gupta, P., Sangwai, J. S. (2021). Interaction of lubricants on the rheological and filtration loss properties of water-based drilling fluids. Petroleum Science and Technology, 39(7–8), 235–248. https://doi.org/10.1080/10916466.2021.1892757 [Google Scholar] [CrossRef]
25. Sonmez, A., Kok, M. V., Bal, B., Bagatir, G., Gucuyener, I. H. (2021). Comprehensive approach to torque and lost circulation problems in geothermal wells in terms of drilling fluid. Geothermics, 95, 102126. https://doi.org/10.1016/j.geothermics.2021.102126 [Google Scholar] [CrossRef]
26. Saffari, H. R. M., Soltani, R., Alaei, M., Soleymani, M. (2018). Tribological properties of water-based drilling fluids with borate nanoparticles as lubricant additives. Journal of Petroleum Science and Engineering, 171, 253–259. https://doi.org/10.1016/j.petrol.2018.07.049 [Google Scholar] [CrossRef]
Cite This Article
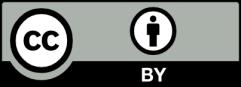
This work is licensed under a Creative Commons Attribution 4.0 International License , which permits unrestricted use, distribution, and reproduction in any medium, provided the original work is properly cited.