Open Access
ARTICLE
Enhancing Heavy Crude Oil Flow in Pipelines through Heating-Induced Viscosity Reduction in the Petroleum Industry
1 Petroleum Technology Department, University of Technology-Iraq, Baghdad, Iraq
2 Department of Chemical Engineering, University of Technology-Iraq, Baghdad, Iraq
* Corresponding Author: Ramzy S. Hamied. Email:
(This article belongs to the Special Issue: Recent advancements in thermal fluid flow applications)
Fluid Dynamics & Materials Processing 2023, 19(8), 2027-2039. https://doi.org/10.32604/fdmp.2023.027312
Received 24 October 2022; Accepted 10 January 2023; Issue published 04 April 2023
Abstract
The process of transporting crude oil across pipelines is one of the most critical aspects of the midstream petroleum industry. In the present experimental work, the effect of temperature, pressure drop, and pipe diameter on the flow rate of heavy crude oil have been assessed. Moreover, the total discharge and energy losses have been evaluated in order to demonstrate the improvements potentially achievable by using solar heating method replacing pipe, and adjusting the value of the initial pressure difference. Crude oil of API = 20 has been used for the experiments, with the studied pipelines sections connecting the separator unit to the storage tank operating at a temperature of 25°C–100°C, pressure drop of 3, 4, 5, and 6 kg/cm2, and with pipe diameter of 4, 6, and 8 in. The results show that on increasing the temperature and/or the pressure drop, the flow rate through the pipeline becomes higher, thus raising the total pumping energy (as the pipe diameter increase), while energy losses increase from the last separator to the storage tank in the field. A pipe diameter increase can also produce a growth of the total pumping energy (i.e., energy losses increase). The results of the present analysis suggest that employing an optimal temperature (50°C) is needed to ensure good performance.Graphic Abstract
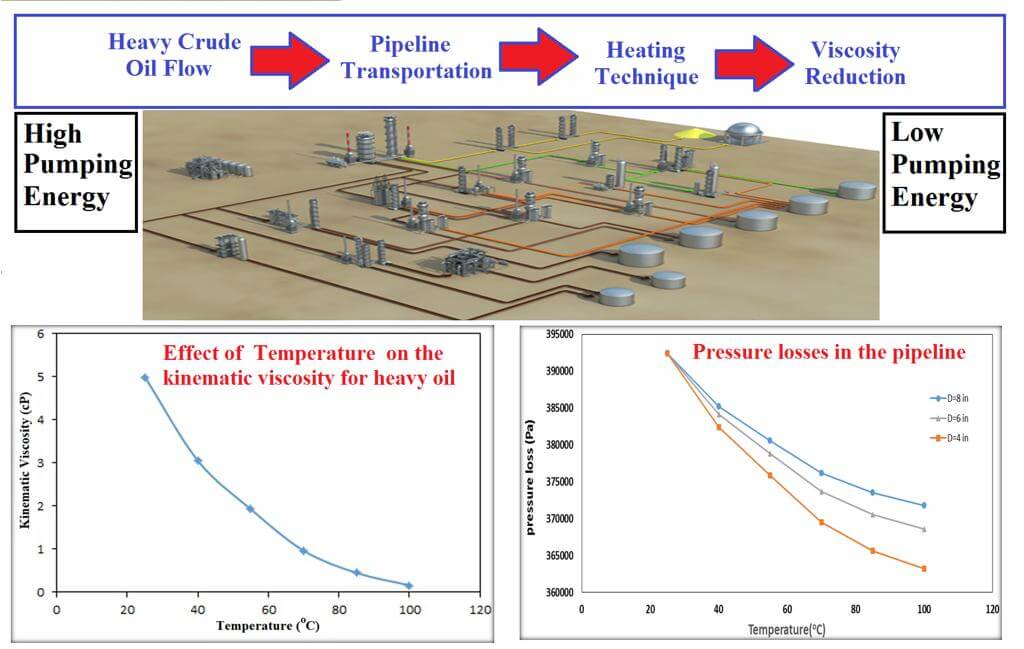
Keywords
Nomenclature
API | American Petroleum Institute (-) |
D | Pipe diameter (m) |
dp | Pressure deference (kg/cm2) |
f | Friction factor of pipe (-) |
g | Gravitational acceleration (m/s2) |
HC | Hydrocarbon (-) |
hf | Head of loss (m) |
L | Length of pipe (m) |
P | Pressure (Pa) |
Q | Flow rate (bbl/day) |
Re | Reynolds number (-) |
Sp.gr | Specific gravity (-) |
V | Fluid velocity (m2/s) |
ε/D | Relative roughness (-) |
μ | Dynamic viscosity (Cp) |
ν | Kinematic viscosity (cSt) |
In the last few decades, the continuous growth in world energy needs driven by economic growth and the enormous population expansion have caused a decrease in the availability of petroleum resources with characteristics that are amenable to refining and effective production [1,2]. Heavy crude oil transportation through pipelines is a problem because of the oil’s inability to flow freely [3,4]. Heavy oil transportation through pipelines is much more complicated without reducing the viscosity because a massive energy demand is needed to offset the higher drop in pressure through the pipeline due to high viscosity [5]. Heavy crude oil contains a higher molecular weight of hydrocarbon (HC), with much more than 50 atoms of carbon, which makes the process of refining complicated and expensive [6–8].
Lowering the consumption of power is one of the keys to remedying the existing concern. Transportation fluids in pipelines and other similar transportation channels tend to consume much power because in a moving fluid, energy is squandered due to fundamental drag friction. About 70% of the total worldwide resources of petroleum have an API grade lower than 20 for heavy oil. Heavy crude oil transportation using pipelines may cause many drops in pressure because of higher viscosity values, which raises the energy needed to pump and also impedes the capability to flow through pipelines [9–11].
From an engineering point of view, numerical models have been widely applied to predict the flow behavior of heavy crude oil [12–15]. Newly proposed technologies in heavy crude oil transport must decrease the impedance to lower the values of the pump requests, and this process should be made more economical [16,17]. Crude oil liquid or product pipelines are handled similarly, with stations of pumps and stations of block valves along the length of the pipelines. Models of the entire pipeline can help to calculate the flow, temperature, and pressure at the main checkpoints. Then, an administrative system can be implemented based on these models [18,19].
To reduce transportation costs and the higher pressure drop, various technologies have been suggested to improve the flow of heavy crude oil and extra heavy oil through pipelines, thus meeting the projected volume production. These technologies include reducing viscosity emulsification during the formation of an oil-in-water emulsion and reducing the oil’s pour point by using pour point depressants (PPDs), blending and dilution with light oils or organic solvents, preheating the heavy crude oil, and adding bitumen and later heating the pipeline [20–22]. Crude oil preheating is the most attractive method due to a rapid reduction in the oil viscosity [23,24]. Therefore, the objective of this work is to investigate the influence of the temperature, pressure drop, and pipe diameter of heavy crude oil flow rate to estimate the improvement in the total discharge and energy (pump and energy loss) of crude oil in horizontal pipelines in order to demonstrate the feasibility of using solar heating methods, replacing pipes, and adjusting the value of the initial pressure difference, employed in the petroleum industry.
2.1 Properties of Heavy Crude Oil
Crude oil is classified as light, medium, heavy, and extra heavy according to its measured API gravity, whereas oil viscosity is a measure of the resistance to the flow of the fluid. This study used Iraqi heavy crude oil from the East Baghdad Oil Field. Heavy oil characteristics (i.e., relative density, API grade, water content, sulfur content, sediment content, viscosity, and density) were evaluated in the Department of Petroleum Technology Laboratory at the University of Technology-Iraq, with the data listed in Table 1.
2.2 Measuring the Heavy Crude Oil Viscosity
All the experiments were tested in the Petroleum Researcher Unit of the Petroleum Technology Department at the University of Technology-Iraq. We studied the effect of temperature variations on the viscosity of Iraqi heavy crude oil at various temperatures (i.e., 25°C, 40°C, 55°C, 70°C, and 100°C) and pressure drop (dp) values (i.e., 3, 4, 5, and 6 kg/cm2) for three pipe diameters (i.e., 4, 6 and 8 in.).
The liquid flow rate is generally studied through viscosity measurements using a computerized viscometer (HB-Brookfield Viscometer, Model DV-11+ Pro, USA). The procedure for testing the viscosity of heavy crude oils entailed placing it in a 250-ml container (cylindrical glass) with the temperature controlled using a magnetic stirrer with a thermometer until the computerized viscometer was read for each temperature and pipe diameter, as shown in Fig. 1.
Figure 1: Computerized viscosity measuring device
3 Programming Method (Fortran 90)
Fortran 90 is a newer software program that can identify the characteristics significant to oil flow through a pipeline. The East Baghdad Oil Field was used as a case study for pipelines starting from the last separator to the storage tank in the field by evaluating the total length and pressure drop from the pumps to storage and the pipe diameter for horizontal flow.
In modeling pipe flow problems, the known properties of the crude oil that flows through the pipeline and the equations governing the flow were used to determine the crude oil flow characteristics [25]. Kinematic viscosity measurements based on Eq. (1) were calculated, which depend on the dynamic viscosity and density. Additionally, the Reynolds number can be estimated using Eq. (2). The volumetric flow rate (synonymous with the flow rate of the mass) can be estimated using Eq. (3):
where
The velocity of crude oil can be calculated with Eq. (4), using the value as the average velocity along the pipe since all parameters exist.
The friction factor in the above equation can be calculated by the iteration method, as shown in Table 2, using the following procedure:
1. Calculate the relative roughness (ε/D).
2. Choose f and suppose that the flow is turbulent with perfect roughness: f(i) = f(0).
3. Calculate the velocity using Eq. (4).
4. Calculate the Reynolds number from Eq. (2).
5. Calculate f from Steps 1 and 4 [f(i + 1)] using Eq. (5) or a Moody chart.
6. Check to see if f(i + 1) = f(i).
7. If no, return to Step 3.
8. If yes, continue.
9. Calculate V.
The friction factor can be obtained from a Moody chart or be determined using Eq. (5).
3.2 Head Loss Determination and Power
Head losses encompass all he numerous losses incurred by flowing liquids, including inlet and outlet losses, friction, etc. The main losses result from the frictional resistance of the pipes, which depends on their internal coarseness. Darcy’s law, Eq. (6) is the general form for estimating the head loss based on the friction and power use calculated according to Eq. (7) [26].
4.1 Effect of Temperature on the Viscosity of Crude Oil
The effect of temperatures ranging from 25°C–100°C on the viscosity of crude oil in the East Baghdad Oil Field is shown in Fig. 2. Increasing the temperature caused the value of the kinematic viscosity for the crude oil to decrease rapidly [27]. The kinematic viscosity results indicated the importance of the heating process as an efficient method for improving the flow properties of heavy crude oils [28]. Moreover, solar heating methods can be applied successfully to provide the required energy. Such type of energy is considered one of the renewable energy sources with relatively low costs.
Figure 2: Effect of the temperature on the kinematic viscosity for the heavy oil
The results showed that a temperature of 50°C can be employed because the viscosity decreased to 53.9%. In comparison with other research, there is research using the dilution method (adding 20 wt. % of acetone) and the percentage of viscosity decrease was about 21.98%, as well as the use of changing the electric current, the percentage of viscosity decrease was 35.61%, and the two methods were also used together in combination (Dilution and Electrical Field), achieving an optimum viscosity reduction of about 61.856% [6].
4.2 Effect of Temperature on the Flow Rate and Reynolds No.
The effect of the kinematic viscosity of heavy crude oil on the flow rate for three pipe diameters (i.e., 4, 6, and 8 in.) and the effect of a constant pressure drop are presented in Table 3 and Fig. 3. When the temperature increased (and the viscosity decreased), the flow rate of the crude oil increased and reached 21.60837, 62.69048, and 133.261 L/s for the three pipe diameters (i.e., 4, 6, and 8 in.), respectively. This occurred because high viscosity heavy crude oils cannot be produced, transported, and pumped with conventional pipelines. Instead, heavy crude oils require additional treatments that reduce the viscosity of the crude oil because a more viscous fluid has a lower tendency to flow [28].
Figure 3: Effect of the temperature of the crude oil on the flow rate for pipe diameters of 4, 6, and 8 in.
Moreover, the results in Fig. 4 and Table 3 show that the Reynolds number (Re) is integrally related to the temperature of the crude oil. As the viscous forces are proportional to the viscosity of the fluid, the Reynolds number is inversely proportional to the viscosity. Therefore, the Reynolds number increased as the viscosity of the heavy crude oil decreased. The flow arrangement with minimum resistance to crude oil flow makes the transport of crude oil more rapid. Additionally, it can be concluded that when the pipe diameter increased from 4 to 6 to 8 in., the flow rate and Reynolds number of the crude oil increased in direct proportion, as shown in Eq. (2) [6,25].
Figure 4: Effect of the temperature of the crude oil on the Reynolds number for pipe diameters of 4, 6, and 8 in.
4.3 Effect of the Temperature on the Power Losses and Pressure Losses
Power consumption is a major problem for energy in pipeline conveyances [29]. The relationship between the pumping power (w), power losses, and pressure losses with temperature for three (i.e., 4, 6, and 8 in.) pipe diameters of heavy crude oil are illustrated in Table 4 and Figs. 5 and 6. Fig. 5 shows that the pumping power rose with increasing temperature because the flow rate of the crude oil increased. This also occurs in Eq. (7) for the constant pressure drop because the kinematic viscosity decreases as the temperature rises. While the amount of energy (power losses) displayed in Fig. 6 demonstrates an increase in power losses with increasing viscosity and pipe diameter because of increasing friction loss between the crude oil and the pipe. Since heavy oil becomes more viscous, the pressure head suffers, and the pump consumes more power [30,31].
Figure 5: Effect of the temperature of the crude oil on the pump power for pipe diameters of 4, 6, and 8 in.
Figure 6: Effect of the temperature of the crude oil on the power losses for pipe diameters of 4, 6, and 8 in.
Fig. 7 presents the relationship between the pressure losses and the temperature for various pipe diameters (i.e., 4, 6, and 8 in.) transporting heavy crude oil. The pressure losses increased with decreasing temperature because the kinematic viscosity increased. There is an inverse relationship between the crude oil viscosity and the pressure drop because a higher viscosity causes power to disperse as the fluid flows. Also, Fig. 7 illustrates that the pressure losses rose as the pipe diameter increased from 4 to 6 to 8 in. Eq. (6) shows the effect of increasing the velocity more than decreasing the friction factor, which is inversely affected by increasing the diameter.
Figure 7: Effect of the temperature for crude oil on the pressure losses in the pipe diameter (4, 6, and 8 in.)
4.4 Effect of the Pressure Drop on the Flow Rate and Reynolds No. of Heavy Crude Oil
Table 4 and Figs. 8–11 illustrate the effect of the pressure drop on the flow rate, Reynolds number, pump power, power losses, and difference in pressure in relation to heavy crude oil in a 4-in. diameter pipe. The flow rate and Reynolds number rose as the pressure drop increased, as shown in Figs. 8 and 9. When the pressure drop increased (meaning there was an increase in the differential pressure), there was more flow, reaching 14392.7980 bbl/day at a pressure drop of 6 kg/cm2, while for 10163.2833 bbl/day, it was 3 kg/cm2. The flow rate is directly proportional to the pressure differential. Higher pressure differences will drive greater flow rates [32].
Figure 8: Effect of the pressure difference of the crude oil on the flow rate for a pipe diameter of 4 in.
Figure 9: Effect of the pressure difference of the crude oil on the Reynolds number for a pipe diameter of 4 in.
Figure 10: Effect of the pressure difference of the crude oil on the power pump for a pipe diameter of 4 in.
Figure 11: Effect of the pressure difference of the crude oil on the power loss for a pipe diameter of 4 in.
Results related to the pump power and power losses with pressure drop are described in Figs. 9 and 10. When the pressure drop in the line is high, the rate of energy consumption to maintain the desirable flow process must also be large, which requires a higher motor horsepower. Inversely, by lowering the drop in pressure at the pipeline, less energy is consumed, which provides the potential to using a lower value motor horsepower [33].
The heating method was successfully applied to reduce the viscosity of heavy crude oil to enhance their flow rate and consumed pumping energy through horizontal pipelines in the petroleum industry. This was achieved using a heating method to demonstrate the feasibility of using solar heating methods, replacing pipes, and adjusting the value of the initial pressure difference. It was found that the operating temperature plays a major role in determining the viscosity of heavy crude oil. The effect of temperature (25°C–100°C) on the viscosity of heavy crude oil indicated a clear reduction in viscosity in the range of 4.9892 to 0.16059 cSt. The results showed that a temperature of 50°C can be employed because the viscosity decreased to 53.9%, the flow rate increased to 3.8%, the power losses decreased to 3.7%, and the pressure drop decreased to 3.7%. Additionally, this temperature retained the light components in heavy crude oil. Also, when increasing the pressure drop from 4 to 6 kg/cm2 for a pipe diameter of 4 in. and reaching a temperature of 50°C, the results show that the viscosity decreased by 53.9% and enhanced the flow rate by 3.31%, the Reynolds number was 136.2%, and the power losses decreased to 3.2%. Therefore, the effect of temperature decreases when the pressure drop increases. Also, when increasing the pipe diameter from 4 to 8 in. for a pressure drop of 4 kg/cm2 and a temperature of 50°C, the viscosity decreased by 53.9% and enhanced the flow rate by 2.69%, and the Reynolds number by 134.5%, while the power losses decreased by 2.62% and the pressure drop decreased by 2.62%. Therefore, the effect of temperature decreases when the pipe diameter increases.
Acknowledgement: The authors are thankful to the staff of the Petroleum Technology Department, University of Technology-Iraq for supporting this work.
Funding Statement: The authors received no specific funding for this study.
Conflicts of Interest: The authors declare that they have no conflicts of interest to report regarding the present study.
References
1. Douglas, L. D., Rivera-Gonzalez, N., Cool, N., Bajpayee, A., Udayakantha, M. et al. (2022). A materials science perspective of midstream challenges in the utilization of heavy crude oil. ACS Omega, 7(2), 1547–1574. https://doi.org/10.1021/acsomega.1c06399 [Google Scholar] [PubMed] [CrossRef]
2. Shah, A., Fishwick, R., Wood, J., Leeke, G., Rigby, S. et al. (2010). A review of novel techniques for heavy oil and bitumen extraction and upgrading. Journal of Energy Environmental Science, 3, 700–714. https://doi.org/10.1039/B918960B [Google Scholar] [CrossRef]
3. Costalonga, L., Michell, B., Loureiro, V., Soares, E. J. (2018). Drag reducing flows by polymer solutions in annular spaces. Journal of Fluids Engineering, 140(5), 051101. https://doi.org/10.1115/1.4038531 [Google Scholar] [CrossRef]
4. Jin, F., Jiang, T., Yuan, C., Varfolomeev, M. A., Wan, F. et al. (2022). An improved viscosity prediction model of extra heavy oil for high temperature and high pressure. Journal of Fuel, 319, 123852. https://doi.org/10.1016/j.fuel.2022.123852 [Google Scholar] [CrossRef]
5. Alwasiti, A. A., Shneen, Z. Y., Ibrahim, R. I., Al Shalal, A. K. (2021). Energy analysis and phase inversion modeling of two-phase flow with different additives. Ain Shams Engineering Journal, 12, 799–805. https://doi.org/10.1016/j.asej.2020.07.004 [Google Scholar] [CrossRef]
6. Noor, I., J, Raheek, I., I, Manal, K. O. (2022). Flow improvement and viscosity reduction for crude oil pipelines transportation using dilution and electrical field. Engineering and Technology Journal, 40(1), 66–75. https://doi.org/10.30684/etj.v40i1.2192 [Google Scholar] [CrossRef]
7. Farid, S., Ahmed, S., Eddine, M. (2022). Drag reduction in single-phase crude oil flow: A mini-review. Journal of Pipeline Science and Engineering, 2(4), 100088. https://doi.org/10.1016/j.jpse.2022.100088
8. Santos, R. G., Loh, W., Bannwart, A. C., Trevisan, O. V. (2014). An overview of heavy oil properties and its recovery and transportation methods. Brazilian Journal of Chemical Engineering, 31(3), 571–590. https://doi.org/10.1590/0104-6632.20140313s00001853 [Google Scholar] [CrossRef]
9. Abdulrazak, A. A., Al-Khatieb, M., Faris, H. A. (2015). Problems of heavy oil transportation in pipelines and reduction of high viscosity. Iraqi Journal of Chemical and Petroleum Engineering, 16(3), 1–9. [Google Scholar]
10. Beloglazov, I., Morenov, V., Leusheva, E., (2021). Flow modeling of high-viscosity fluids in pipeline infrastructure of oil and gas enterprises. Egyptian Journal of Petroleum, 30(4), 43–51. https://doi.org/10.1016/j.ejpe.2021.11.001
11. Saad, N. S., Thamer, J. M., Huda, K. H., Shahzad, B. (2021). CFD investigation on characteristics of heavy crude oil flow through a horizontal pipe. Egyptian Journal of Petroleum, 30, 13–19. https://doi.org/10.1016/j.ejpe.2021.06.003 [Google Scholar] [CrossRef]
12. Poole, R. J., Ridley, B. S. (2007). Development-length requirements for fully developed laminar pipe flow of inelastic non-newtonian liquids. Journal of Fluids Engineering, 129, 1281–1287. https://doi.org/10.1115/1.2776969 [Google Scholar] [CrossRef]
13. Shnain, Z. Y., Ali, J. M., Sukkar, K. A., Alsaffar, M. A., Abid, M. F. (2022). A computational fluid dynamics study of liquid–solid nano-fluid flow in horizontal pipe. Arabian Journal for Science and Engineering, 47(5), 5577–5585. https://doi.org/10.1007/s13369-021-05512-y [Google Scholar] [CrossRef]
14. Zambrano, H., Sigalotti, L., Klapp, J., Polo, F., Bencomo, A. (2017). Heavy oil slurry transportation through horizontal pipelines: Experiments and CFD simulations. International Journal of Multiphase Flow, 91, 130–141. https://doi.org/10.1016/j.ijmultiphaseflow.2016.04.013 [Google Scholar] [CrossRef]
15. Kumar, R., Banerjee, S., Banik, A., Bandyopadhyay, T. K., Kumar, T. N. (2017). Simulation of single phase non-newtonian flow characteristics of heavy crude oil through horizontal pipelines. Journal of Petroleum Science and Technology, 35(6), 615–624. https://doi.org/10.1080/10916466.2016.1266365 [Google Scholar] [CrossRef]
16. Wang, Y., Lu, J. (2015). Optimization of China crude oil transportation network with genetic ant colony algorithm. Information, 6(3), 467–480. https://doi.org/10.3390/info6030467 [Google Scholar] [CrossRef]
17. Sarkar, A., Arya, A. K. (2022). A survey on optimization parameters and techniques for crude oil pipeline transportation. In: Das, B., Patgiri, R., Bandyopadhyay, S., Balas, V. E. (Eds.Smart innovation, systems and technologies, vol. 292. Singapore: Springer. https://doi.org/10.1007/978-981-19-0836-1_43 [Google Scholar] [CrossRef]
18. Håvard, D. (2015). Oil and gas production handbook: An introduction to oil and gas production, transport, refining and petrochemical industry. Edition 3.0Oslo. https://Lulu.com [Google Scholar]
19. Bekibayev, T., Zhapbasbayev, U., Ramazanova, G. (2022). Optimal regimes of heavy oil transportation through a heated pipeline. Journal of Process Control, 115, 27–35. https://doi.org/10.1016/j.jprocont.2022.04.020 [Google Scholar] [CrossRef]
20. Emad, S. (2019). Flow of heavy oils at low temperatures: Potential challenges and solutions. Processing of Heavy Crude Oils-Challenges and Opportunities. https://doi.org/10.5772/intechopen.82286 [Google Scholar] [CrossRef]
21. Ke, H., Yuan, M., Xia, S. (2022). A review of nanomaterials as viscosity reducer for heavy oil. Journal of Dispersion Science and Technology, 43(9), 1271–1282. https://doi.org/10.1080/01932691.2020.1851246
22. Muñoz, J. A., Ancheyta, J. (2022). Techno-economic analysis of heating techniques for transportation of heavy crude oils by pipeline. https://doi.org/10.2139/ssrn.4040989 [Google Scholar] [CrossRef]
23. Henaut, I., Argillier, J., Pierre, C., Moan, M. (2003). Thermal flow properties of heavy oils. Offshore Technology Conference, Houston, Texas. OTC-15278-MS. https://doi.org/10.4043/15278-MS [Google Scholar] [CrossRef]
24. Antonio, J. C., Koptjaev, E. (2022). Electrical heating system for oil pipelines. International Conference on Industrial Engineering, Applications and Manufacturing (ICIEAM), pp. 368–373. Sochi, Russian Federation. https://doi.org/10.1109/ICIEAM54945.2022.9787254 [Google Scholar] [CrossRef]
25. White, F. M. (2011). Fluid mechanics. Americas: McGraw-Hill, 7th Published a Business Unit of the McGraw-Hill Companies, Inc. https://docs.google.com/file/d/0B9JtpWUzKcwkNC11OC1mQ0NzZjg/edit?pli=1 [Google Scholar]
26. Hibberler, R. C. (2021). Fluid mechanics. UK: Pearson Education, Inc. https://ebookyab.com/fluid-mechanics-hibbeler [Google Scholar]
27. Yaghi, B. M., Al-Bemani, A. (2002). Heavy crude oil viscosity reduction for pipeline transportation. Journal of Energy Sources, 24(1), 93–102. https://doi.org/10.1080/00908310252774417 [Google Scholar] [CrossRef]
28. Saniere, A., Hénaut, I., Argillier, J. F. (2004). Pipeline transportation of heavy oils, a strategic, economic and technological challenge. Journal of Oil & Gas Science and Technology–revue De L Institut Francais Du Petrole, 59(5), 455–466. [Google Scholar]
29. Peter, G. (2018). How viscosity affects pumping. Hydraulic Institute. https://www.pumpsandsystems.com/how-viscosity-affects-pumping [Google Scholar]
30. Almukhtar, R., Hammoodi, S. I., Majdi, H. S., Sukkar, K. A. (2022). Managing transport processes in thermal cracking to produce high-quality fuel from extra-heavy waste crude oil using a semi-batch reactor. Journal of Processes, 10(10), 2077. https://doi.org/10.3390/pr10102077 [Google Scholar] [CrossRef]
31. Majeed, E. M., Eynas, M., Tariq, M. (2020). Viscosity reduction of Iraqi crude oil by different additives. AIP Conference Proceedings, 2213, 020142. https://doi.org/10.1063/5.0000229 [Google Scholar] [CrossRef]
32. Brian, S., Freeman, M. D. (2014). Flow and velocity. In: Anesthesiology core review: Part one basic exam. USA: McGraw-Hill Education. https://accessanesthesiology.mhmedical.com/book.aspx?bookID=974 [Google Scholar]
33. Abbas, A. D., Sukkar, K. A. (2022). Rheological behaviour modification of basrah crude oil by graphene additions at different temperatures in petroleum pipeline. AIP Conference Proceedings, 2443(1), 030048. https://doi.org/10.1063/5.0091896 [Google Scholar] [CrossRef]
Cite This Article
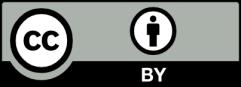
This work is licensed under a Creative Commons Attribution 4.0 International License , which permits unrestricted use, distribution, and reproduction in any medium, provided the original work is properly cited.