Open Access
ARTICLE
Water Stability Improvement of Acid Fine Aggregate-Based Asphalt Concrete
1 Zhejiang Scientific Research Institute of Transport, Hangzhou, 310023, China
2 Zhejiang Key Laboratory of Road and Bridge Detection and Maintenance Technology, Hangzhou, 310023, China
3 Huzhou Administration of Highway and Transportation, Huzhou, 313000, China
4 China University of Geosciences (Wuhan), Wuhan, 430074, China
* Corresponding Author: Yudong Cheng. Email:
(This article belongs to the Special Issue: Advances in Solid Waste Processing and Recycling Technologies for Civil Engineering Materials)
Fluid Dynamics & Materials Processing 2023, 19(8), 2171-2180. https://doi.org/10.32604/fdmp.2023.026892
Received 01 October 2022; Accepted 14 December 2022; Issue published 04 April 2023
Abstract
In general, acid aggregates are not used in combination with asphalt concrete because of their poor compatibility with the asphalt binder, which typically results in a scarce water stability of the concrete. In the present study, the feasibility of a new approach based on the combination of acid granite fine aggregate with alkaline limestone coarse aggregate and Portland cement filler has been assessed. The mineral and chemical compositions of these three materials have first been analyzed and compared. Then, the effect of different amounts of Portland cement (0%, 25%, 50%, 75% and 100% of the total filler by weight) on the mechanical performance and water stability of the asphalt concrete has been considered. Asphalt concrete has been designed by using the Marshall method, and the mechanical performance indexes of this material, including the Marshall stability and indirect tensile strength (ITS), have been measured together with the related water stability indexes (namely the Marshall stability (RMS) and tensile strength ratio (TSR)). The results indicate that the alkaline limestone coarse aggregate and Portland cement filler can balance the drawback caused by the acid granite fine aggregate. The asphalt concrete has good mechanical performances and water stability when the amount of common limestone powder filler replaced by cement is not less than 75%.Keywords
Asphalt pavement and cement pavement are the two most widely used forms of pavement at present. Asphalt pavement was widely used in the construction of high-grade express because of its characteristics such as comfortable driving, low noise and skid resistance [1]. Besides, Asphalt pavement was made of asphalt concrete, with the aggregate accounting for more than 90% of the volume of asphalt concrete [2]. Therefore, the massive construction of asphalt pavement was accompanied by astonishing consumption of resources, and the shortage of high-quality road construction materials has become more and more serious. To reduce the reliance on natural high-quality resources for asphalt pavement construction, developing a technology for the use of low-grade natural resources in asphalt concrete is an important research direction at present. Low-grade aggregate referred to these acid rocks, such as granite, gneiss, etc., because they showed bad adhesion performance with asphalt binder [3], which adversely affected the performance of asphalt concrete, especially the water stability. Therefore, to realize the application of acid aggregate in asphalt concrete, it was crucial to improve the adhesion performance between acid aggregate and asphalt binder.
The current work mainly focuses on the utilization of acid coarse aggregate in asphalt concrete. The common method to improve the bonding performance of asphalt concrete containing acid coarse aggregate was by adding alkaline fine aggregate [3–7]. For example, Chen et al. [5] prepared asphalt concrete by using acid gneiss coarse aggregate with alkaline steel slag fine aggregate. Wu et al. [7] prepared asphalt concrete by using acid gneiss coarse aggregate with alkaline limestone fine aggregate. Sun et al. [8] prepared asphalt concrete by using acid granite coarse aggregate and recycled concrete fine aggregate. These operations can improve the moisture stability of asphalt concrete containing acid coarse aggregate. However, it was difficult to improve the engineering performance of asphalt concrete to an ideal level only by combining acid coarse aggregate and alkaline fine aggregate. Asphalt concrete mainly consists of aggregate, filler and asphalt binder [9]. The aggregate formed an embedded bone structure, the asphalt mastic which was composed of filler and asphalt was bonds the bone structure, so the bonding behavior between asphalt mastic and aggregate was very important for the engineering performance of asphalt concrete.
To strengthen the bonding performance between aggregate and asphalt mastic, three methods were suggested. The first method was to use some alkaline powders as asphalt fillers. Research shown that partial or total replacement of common mineral powder fillers in asphalt mastic by alkaline powders, such as steel slag powder [3], flue gas desulfurization residues [4], hydrated lime [7,10–12], cement [11,12], etc. can strengthen the bonding and hence improve the engineering performance of asphalt concrete containing acid coarse aggregate, especially the water damage resistance. Hesami et al. [13] prepared asphalt concrete by using acid granite coarse aggregate and hydrated lime as anti-strip additives, the results showed that hydrated lime increases the wettability of asphalt binder on the aggregate and improves the adhesion between the asphalt binder and aggregate. Cui et al. [14] found that the interfacial adhesion in wet conditions could be improved by mixing a silane, amine or rubbery polymer into the bitumen. Strokova et al. [15] explored the feasibility of using the fines of aluminosilicate sedimentary rocks as fillers, and the results showed that such treatment provided sufficient structural stability of obtained materials and resulted in the reduction of water absorption of asphalt, improved water resistance (up to 2.5 times) and also, in reduced swelling (up to 9 times). The second method was to modify the asphalt binder. Shivani et al. [16] found that the use of warm-mix additive (WMA) to modify the asphalt can enhance the bonding strength between the asphalt binder and granite aggregate. Consequently, the resistance of asphalt concrete containing WMA to moisture-induced damage had improved. Singh et al. [17] used SBS to modify the asphalt, and the results showed that there was a significant improvement in the strength characteristics, rutting resistance and moisture susceptibility of SBS modified mixes. Foxworthy et al. [18] investigated the feasibility of using phosphogypsum-based slag aggregate in asphaltic concrete binder course mixes. The results of the study indicated that phosphogypsum-based slag aggregate could be successfully employed in asphaltic concrete binder course mixtures and improved the moisture susceptibility of asphalt concrete obviously. Hirato et al. [19] developed a hybrid binder consisting of polymer modified asphalt and a special additive, it had high oil and flow resistance as well as water and abrasion resistance comparable to semi-flexible pavement and epoxy asphalt pavement. Ye et al. [20] used amines and organic polymers as anti-stripping agents to modify the asphalt, which showed that these anti-stripping agents could significantly improve the adhesion between granite and asphalt. The third method was to modify the acid aggregate. The silane coupling agent (SCA) was frequently used to modify the surface of granite aggregate. Yang et al. [21] found that the SCA grafts onto the aggregate surface via chemical interactions, which helped to raise the contact angle and reduce the hydrophilicity of granite greatly. Ding et al. [22] modified the surface of granite aggregate by SCA graded KH-560. Experimental results also suggested that the SCA could improve the adhesion between asphalt and granite aggregate efficiently.
However, the acid coarse aggregate and fine aggregate were produced simultaneously when preparing aggregate by crushing stones. Only applying acid coarse aggregate to asphalt concrete was not conducive to the full use of acid aggregate. Considering that the proportion of fine aggregate in asphalt concrete was also very large, we evaluated the applicability of acid fine aggregate in asphalt concrete, focusing on the mechanical performance and moisture damage resistance of asphalt concrete containing acid fine aggregate. The scheme was to prepare asphalt concrete by combining alkaline coarse aggregate and acid fine aggregate. At the same time, alkaline filler was used to improve the engineering performance of asphalt concrete.
In this study, alkali limestone coarse aggregate, acidic granite fine aggregate and alkaline Portland cement filler were used. The work included three main aspects: revealing the mineral and chemical compositions of the raw materials used; designing asphalt concrete composed of limestone coarse aggregate, granite fine aggregate and cement filler; determining the influence of cement content on the mechanical performance and water stability of asphalt concrete.
The coarse aggregate used in this research was alkaline limestone, and the fine aggregate was acid granite. Two types of fillers, common limestone powder and Portland cement, were also used. The common limestone powder was used as the control group. The strength grade of the cement was 42.5 MPa. The asphalt binder was AH-70 base asphalt. The basic performance indexes of aggregates, fillers and asphalt were tested in accordance with Chinese standard methods [23,24]. The test results were presented in Tables 1–4, which showed that the basic performance indexes of raw materials selected in this study met the requirements of Chinese specifications [25].
2.2.1 Raw Material Characteristics
To reveal the acid and alkaline performance, the mineral and chemical compositions of raw materials were investigated. The mineral composition was analyzed by a polarizing microscope, and the chemical composition was analyzed by an X-ray fluorescence spectrometer.
2.2.2 Design of Asphalt Concrete
The gradation of asphalt concrete selected in this study was Asphalt Concrete-13 Coarse (AC-13C). The contents of alkaline limestone coarse aggregate, acid granite fine aggregate and filler were 52%, 44% and 4%. According to the different amounts of cement and common limestone powder filler, five kinds of asphalt concrete were designed, as detailed in Table 5. All asphalt concretes were designed according to the standard Marshall method. Marshall specimens with air void of 4% and 6% were prepared, respectively, which was used to test the mechanical performance and water stability of each asphalt concrete.
2.2.3 Mechanical Performance and Water Stability of Asphalt Concrete
In this research, the mechanical performance indexes of asphalt concrete including Marshall stability and indirect tensile strength (ITS) were tested, the water stability indexes of asphalt concrete including retained Marshall stability (RMS) and tensile strength ratio (TSR) were calculated.
The determination of stability and RMS. For each asphalt concrete, Marshall specimens with air void of 4% were divided into four groups, each group had no less than four specimens. All four groups of specimens were kept in a water bath at 60°C for 30 min, 24, 48 and 72 h, respectively. The first group was the control group and the last three groups were the conditioned groups. The Marshall stability of all specimens were measured by the Marshall stability meter, and the RMS was calculated according to Eq. (1). The test was performed in triplicate.
The determination of ITS and TSR. For each asphalt concrete, Marshall specimens with air void of 6% were also divided into four groups, each group had no less than four test specimens. One group was used as the control group and the other three groups were subjected to freeze-thaw damage for 1, 2 and 3 cycles respectively. All specimens were soaked in a water bath at room temperature for 2 h, then they were tested by splitting instrument to obtain the ITS, and the TSR was calculated according to Eq. (2). The test was performed in triplicate.
RMS=MSiMS0×100% (1)
TSR=TStTS0×100% (2)
where MS0 was the average Marshall stability of specimens in the control group, kN; MSi was the average Marshall stability of specimens in the conditioned group after immersing in water bath at 60°C for i h, kN; TS0 was the average ITS of specimens in the control group, MPa; TSt was the average ITS of specimens in the conditioned group after subjecting to freeze-thaw damage for t cycles, MPa.
3.1 Raw Material Characteristics
The polarizing microscope analysis results of limestone and granite were shown in Fig. 1. Based on the unique shape and color of some minerals under polarizing microscope, it was adjudged that limestone mainly contains calcite minerals while granite was dominated by quartz minerals. This conclusion agreed with the results of the chemical composition analysis. As detailed in Table 6, the CaO content of limestone was very high, more than 50%, and the amount of burning loss is also very large. It indicated that CaO was mainly derived from the decomposition of calcite minerals in X-ray fluorescence spectrometer analysis. The content of SiO2 in granite was very high, close to 70%, which mainly participated in the formation of quartz minerals. The high content of CaO and SiO2 contributed to the alkalinity of limestone and acidity of granite. As we all know, Portland cement mainly contained high alkaline tricalcium silicate, dicalcium silicate and other minerals, which were also confirmed by the results of the chemical composition analysis in Table 6. Its main chemical compositions were CaO and SiO2, with the content of CaO being the highest. The alkaline raw materials had good adhesion with the weak acidic asphalt, so the alkaline limestone coarse aggregate and alkaline cement filler were used together with the acid fine aggregate in this study, with the aim of enhancing the adhesion between acid fine aggregate and asphalt.
Figure 1: Polarizing microscope images: (a) limestone; (b) granite
3.2 Design of Asphalt Concrete
The different asphalt concrete detailed in Table 5 was designed according to the standard Marshall design method. Under the premise that the volume parameters of each type of asphalt concrete meet the design requirements, the optimum asphalt-aggregate ratios of the five asphalt concretes were shown in Fig. 2. With the increase in cement dosage, although the optimum asphalt-aggregate ratio of asphalt concrete increased slightly, the increment was quite small. Even if the limestone powder was replaced by cement completely, the changes in the optimum asphalt-aggregate ratio did not exceed 0.1%, indicating that the cement dosage had little influence on the asphalt consumption of asphalt concrete, which was mainly due to the small amount of filler in asphalt concrete systems.
Figure 2: Asphalt-aggregate ratio of each asphalt concrete
3.3 Mechanical Performance and Water Stability of the Asphalt Concrete
The initial Marshall stability of each asphalt concrete (without water damage) was shown in Fig. 3. The stability of asphalt concrete was improved to some extent by replacing some or all limestone powder fillers with cement. When the amount of limestone powder replaced by cement increased to 75%, the stability of asphalt concrete was improved by 35%, which was the most stable among these five asphalt concretes. According to the requirements of Chinese specification [25], the Marshall stability of asphalt concrete shall not be less than 8 kN. Therefore, in terms of the stability of asphalt concrete, the suitable amount of limestone powder replaced by cement shall not be less than 75%, although the Marshall stability decreased slightlywhen the amount of cement was further increased.
Figure 3: Initial marshall stability of each asphalt concrete
The relationship between RMS of each asphalt concrete and hot water immersion time was shown in Fig. 4. The RMS of each asphalt concrete decreased with the extension of hot water immersion time. However, with the increasing of cement content, the attenuation speed of RMS slowed down. According to the requirements of Chinese specifications [25], the RMS of asphalt concrete shall not be lower than 80% after being immersed in a water bath at 60°C for 48 h. Fig. 4 showed that this requirement was met when the amount of limestone powder replaced by cement was 75% or 100%, even if the hot water immersion time was extended to 72 h. Therefore, in terms of the RMS of asphalt concrete, it was also suggested that the amount of limestone powder replaced by cement should not be less than 75%.
Figure 4: Retained marshall stability (RMS) of each asphalt concrete
The ITS values of each asphalt concrete were shown in Fig. 5. The ITS did not show a change rule with the increase in cement dosage. The ITS of asphalt concrete containing cement was not obviously different from that of asphalt concrete prepared with pure limestone powder, which varied from 0.65 to 0.70 MPa. Meanwhile, the Chinese specification did not set a limitation on the ITS of asphalt concrete [25]. Therefore, in terms of the ITS of asphalt concrete, any amount of cement can be added.
Figure 5: Indirect tensile strength (ITS) of each asphalt concrete
The relationship between the TSR of each asphalt concrete and the freeze-thaw cycles was shown in Fig. 6. The TSR of each asphalt concrete showed a trend to decrease with the increase in the number of freeze-thaw cycles. After three cycles of freeze-thaw damage, the ITS loss of each asphalt concrete exceeded 25%. Similar to the change rule of RMS, with the increasing of cement dosage, the attenuation speed of TSR slowed down, especially when the amount of limestone powder replaced by cement reached 50% or more. According to the Chinese specification [25], the TSR of asphalt concrete shall not be lower than 75% after being subjected to freeze-thaw damage for one cycle. Fig. 6 showed that when the amount of limestone powder replaced by cement reached 50% or more, this requirement can be met. And the larger the amount of cement, the more obvious the effect will be. When the amount of cement replacing limestone powder reached 100%, the TSR was still higher than 75% even after being subjected to the two cycles of freeze-thaw damage. In terms of the TSR of asphalt concrete, the amount of limestone powder replaced by cement was 50% or more.
Figure 6: Tensile strength ratio (TSR) of each asphalt concrete
Therefore, for asphalt concrete composed of alkaline limestone coarse aggregate, acid granite fine aggregate and alkaline cement, after a comprehensive consideration of the influence of cement dosage on the mechanical performance and water stability of asphalt concrete, the suitable amount of common limestone powder replaced by cement was suggested to be not less than 75%.
In this research, in order to promote the application of acidic granite fine aggregate in asphalt concrete, the feasibility of using alkaline limestone coarse aggregate and alkaline Portland cement to balance the drawback caused by acid granite fine aggregate in asphalt concrete was evaluated. The influence of cement dosage in total filler on the mechanical performance and water stability of asphalt concrete composed of limestone coarse aggregate and granite fine aggregate was mainly studied. The following conclusions were obtained:
1) Limestone mainly contained calcite minerals while granite was dominated by quartz minerals. Therefore, the amount of CaO in limestone and the amount of SiO2 in granite were very high, which contributed to the alkalinity of limestone and acidity of granite.
2) The Marshall stability of asphalt concrete increased to more than 8 kN when the proportion of cement in filler reached 75% or more. The influence of cement dosage on the ITS of asphalt concrete was not as obvious as which on Marshall stability. In terms of Marshall stability, the amount of cement replacing limestone powder filler must not be less than 75% in accordance with the requirements of the Chinese specification.
3) The introduction of cement in asphalt concrete can reduce its sensitivity to hot water and freeze-thaw cycle damage. The attenuation speed of RMS and TSR of asphalt concrete slowed down with the dosage increase of cement in filler. In terms of RMS and TSR, the amount of cement replacing limestone powder filler must not be less than 75% in accordance with the requirements of the Chinese specification.
Funding Statement: This work was supported by the Science and Technology Planning Project of Zhejiang Provincial Department of Transportation (2021012) and Zhejiang Provincial Natural Science Foundation of China under Grant (No. LGG21E080002).
Conflicts of Interest: The authors declared that they had no conflicts of interest to report regarding the present study.
References
1. Chen, Z. W., Leng, Z., Jiao, Y. Y., Xu, F., Lin, J. T. et al. (2022). Innovative use of industrially produced steel slag powders in asphalt mixture to replace mineral fillers. Journal of Cleaner Production, 344, 131124. https://doi.org/10.1016/j.jclepro.2022.131124 [Google Scholar] [CrossRef]
2. Ahmedzade, P., Sengoz, B. (2009). Evaluation of steel slag coarse aggregate in hot mix asphalt concrete. Journal of Hazardous Materials, 165(1), 300–305. https://doi.org/10.1016/j.jhazmat.2008.09.105 [Google Scholar] [PubMed] [CrossRef]
3. Chen, Z. W., Jiao, Y. Y., Wu, S. P., Tu, F. B. (2018). Moisture-induced damage resistance of asphalt mixture entirely composed of gneiss and steel slag. Construction and Building Materials, 177, 332–341. https://doi.org/10.1016/j.conbuildmat.2018.05.097 [Google Scholar] [CrossRef]
4. Chen, Z. W., Wu, S. P., Li, F. Z., Chen, J. Y., Qin, Z. H. et al. (2014). Recycling of flue gas desulfurization residues in gneiss based hot mix asphalt: Materials characterization and performances evaluation. Construction and Building Materials, 73, 137–144. https://doi.org/10.1016/j.conbuildmat.2014.09.049 [Google Scholar] [CrossRef]
5. Chen, Z. W., Wu, S. P., Wen, J., Zhao, M. L., Yi, M. W. et al. (2015). Utilization of gneiss coarse aggregate and steel slag fine aggregate in asphalt mixture. Construction and Building Materials, 93, 911–918. https://doi.org/10.1016/j.conbuildmat.2015.05.070 [Google Scholar] [CrossRef]
6. Pang, L., Wu, S. P., Xie, J., Hu, D. M. (2010). Investigate of performance of asphalt concrete with gneiss. Key Engineering Materials, 417, 497–500. [Google Scholar]
7. Wu, S. P., Hu, D. M., Pang, L., Wang, H. (2009). Utilization of gneiss in asphalt concrete mixtures. Materials Science Forum, 620(622), 1–4. https://doi.org/10.4028/www.scientific.net/MSF.620-622.1 [Google Scholar] [CrossRef]
8. Sun, Y. H., Wu, S. P., Zhu, J. Q., Zhong, J. J. (2011). Investigation on properties of granite asphalt mixtures prepared using fine recycled concrete aggregate. Advanced Materials Research, 211–212, 1066–1071. https://doi.org/10.4028/www.scientific.net/AMR.211-212.1066 [Google Scholar] [CrossRef]
9. Airey, G. D., Collop, A. C., Zoorob, S. E., Elliott, R. C. (2008). The influence of aggregate, filler and bitumen on asphalt mixture moisture damage. Construction and Building Materials, 22(9), 2015–2024. https://doi.org/10.1016/j.conbuildmat.2007.07.009 [Google Scholar] [CrossRef]
10. Huang, S. C., Robertson, R. E., Branthaver, J. F., Claine Petersen, J. (2005). Impact of lime modification of asphalt and freeze–thaw cycling on the asphalt–aggregate interaction and moisture resistance to moisture damage. Journal of Materials in Civil Engineering, 17(6), 711–718. https://doi.org/10.1061/(ASCE)0899-1561(2005)17:6(711) [Google Scholar] [CrossRef]
11. Guo, D. D. (2013). Study on water stability of granite asphalt mixture. Advanced Materials Research, 724–725, 1555–1559. https://doi.org/10.4028/www.scientific.net/AMR.724-725.1555 [Google Scholar] [CrossRef]
12. Zeng, M. L., Luo, L. W., Liu, T. (2005). Improving moisture susceptibility of granite asphalt mixture using different additives. Hunan Daxue Xuebao/Journal of Hunan University Natural Sciences, 32, 119–122. [Google Scholar]
13. Hesami, S., Roshani, H., Hamedi, G. H., Azarhoosh, A. (2013). Evaluate the mechanism of the effect of hydrated lime on moisture damage of warm mix asphalt. Construction and Building Materials, 47, 935–941. https://doi.org/10.1016/j.conbuildmat.2013.05.079 [Google Scholar] [CrossRef]
14. Cui, S., Blackman, B. R., Kinloch, A. J., Taylor, A. C. (2014). Durability of asphalt mixtures: Effect of aggregate type and adhesion promoters. International Journal of Adhesion and Adhesives, 54, 100–111. https://doi.org/10.1016/j.ijadhadh.2014.05.009 [Google Scholar] [CrossRef]
15. Strokova, V., Lebedev, M., Potapova, I., Sobolev, K. (2014). New alumosilicate fillers based on sedimentary rocks for asphalt concrete. MRS Online Proceedings Library, 1611(1), 81–87. https://doi.org/10.1557/opl.2014.762 [Google Scholar] [CrossRef]
16. Shivani, R., Rouzbeh, G., Syed Ashik, A., Musharraf, Z., Edgar, A. O. (2017). Effect of warm-mix additive on interfacial energy of an asphalt binder and a granite aggregate. 15th International Conference of the International Association for Computer Methods and Advances in Geomechanics, pp. 803–810, Wuhan, Hubei Province, China. [Google Scholar]
17. Singh, M., Kumar, P., Maurya, M. R. (2013). Strength characteristics of SBS modified asphalt mixes with various aggregates. Construction and Building Materials, 41, 815–823. https://doi.org/10.1016/j.conbuildmat.2012.12.062 [Google Scholar] [CrossRef]
18. Foxworthy, P. T., Nadimpalli, R. S., Seals, R. K. (1996). Phosphogypsum slag aggregate-based asphaltic concrete mixes. Journal of Transportation Engineering, 122(4), 300. https://doi.org/10.1061/(ASCE)0733-947X(1996)122:4(300) [Google Scholar] [CrossRef]
19. Hirato, T., Murayama, M., Sasaki, H. (2014). Development of high stability hot mix asphalt concrete with hybrid binder. Journal of Traffic and Transportation Engineering, 1(6), 424–431. [Google Scholar]
20. Ye, Y. L., Hao, Y., Zhuang, C. Y., Shu, S. Q., Lv, F. L. (2022). Evaluation on improvement effect of different anti-stripping agents on pavement performance of granite-asphalt mixture. Materials, 15(3), 915. https://doi.org/10.3390/ma15030915 [Google Scholar] [PubMed] [CrossRef]
21. Yang, M., Huang, T., Lv, S. T., Zheng, J. L. (2021). Effect and mechanism of acidic aggregate surface silane modification on water stability of asphalt mixture. Road Materials and Pavement Design, 22(7), 1654–1666. https://doi.org/10.1080/14680629.2020.1730229 [Google Scholar] [CrossRef]
22. Ding, G. Y., Yu, X., Dong, F. Q., Ji, Z. Z., Wang, J. Y. (2020). Using silane coupling agent coating on acidic aggregate surfaces to enhance the adhesion between asphalt and aggregate: A molecular dynamics simulation. Materials, 13(23), 1–16. https://doi.org/10.3390/ma13235580 [Google Scholar] [PubMed] [CrossRef]
23. Ministry of Transport of the People’s Republic of China. Test methods of aggregate for highway engineering. JTG E42 (2005) (in Chinese). [Google Scholar]
24. Ministry of Transport of the People’s Republic of China. Standard test methods of bitumen and bituminous mixtures for highway engineering. JTG E20 (2011) (in Chinese). [Google Scholar]
25. Ministry of Transport of the People’s Republic of China. Technical specifications for construction highway asphalt pavements. JTG F40 (2004) (in Chinese). [Google Scholar]
Cite This Article
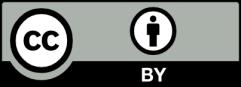
This work is licensed under a Creative Commons Attribution 4.0 International License , which permits unrestricted use, distribution, and reproduction in any medium, provided the original work is properly cited.