Open Access
ARTICLE
Analysis of a Composite Admixture Based on Ready-Mixed Concrete Waste Residuals
1 Wuhan Energy Conservation Office, Wuhan, 430000, China
2 China Construction Ready Mixed Concrete Co., Ltd., Wuhan, 430000, China
* Corresponding Author: Zihan Zhou. Email:
(This article belongs to the Special Issue: Advances in Solid Waste Processing and Recycling Technologies for Civil Engineering Materials)
Fluid Dynamics & Materials Processing 2023, 19(8), 1983-1995. https://doi.org/10.32604/fdmp.2023.026023
Received 10 August 2022; Accepted 25 October 2022; Issue published 04 April 2023
Abstract
Reasonable treatment and utilization of waste residuals discharged during the production of ready-mixed concrete is an important problem in the cement industry. In this study, a composite admixture was prepared by using ready-mixed concrete waste residuals, furnace slag, and water granulated slag. The grinding characteristics of such material were investigated. Moreover, the effect of such admixture on cement hydration and pore structure was analyzed by X-ray diffraction, thermogravimetric-differential scanning calorimetry, scanning electron microcopy and mercury intrusion porosimetry. As shown by the results: The grinding characteristics of the waste residuals can be improved significantly by mixing them with furnace slag and water granulated slag. Furthermore, the composite admixture does not change the composition of hydration products; rather it contributes to refine the pore structure of the matrix, thus improving the mechanical properties of these cement-based materials.Graphic Abstract
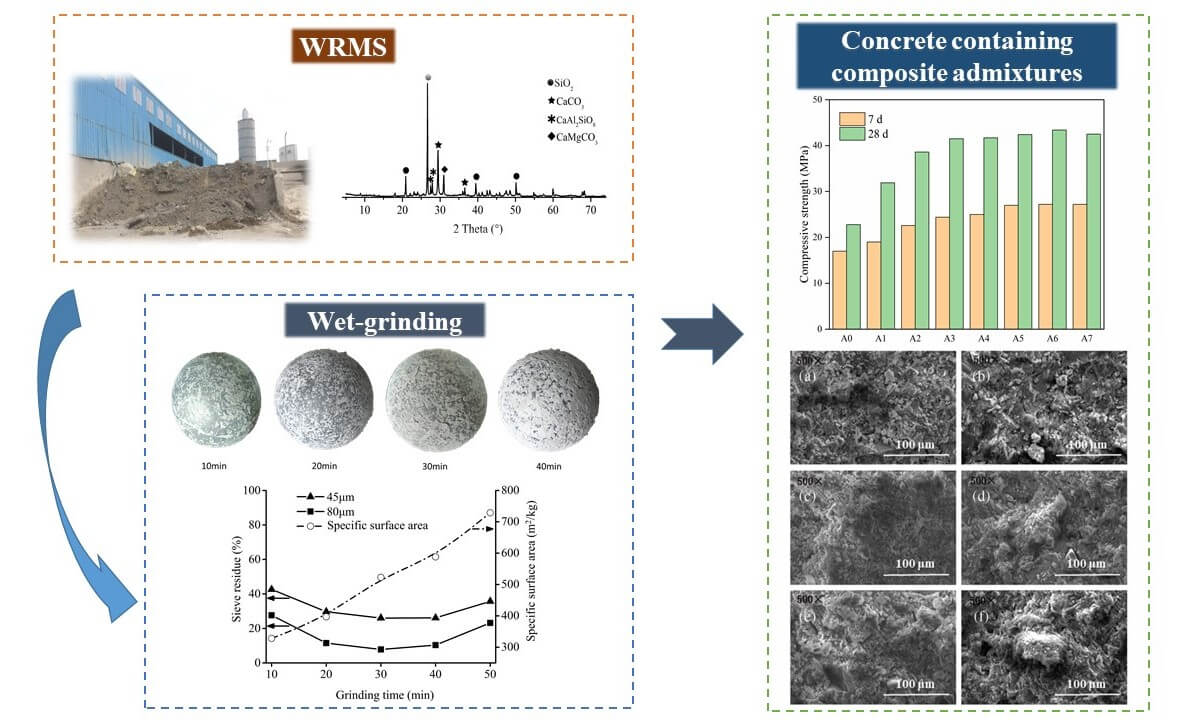
Keywords
Due to a large amount of pollutants and wastes generated in the production process of ready-mixed concrete [1–3], the industry is considered to be highly polluting and energy-consuming [4,5]. Generally, for every 1 m3 of concrete manufactured, 0.02 t of the waste residue of a ready-mixed concrete station (WRMS) will be produced [6–8]. As shown in Fig. 1, WRMS is difficult to be treated and utilized, and it is mainly landfilled and stacked at present, which has caused huge environmental pollution and waste of resources [9–11]. Under the background of green and clean production, increasing attention has been paid to the utilization of WRMS.
Figure 1: Waste residue of ready-mixed concrete station
Audo et al. [12] replaced cement and sand with WRMS. They found that the working performance of concrete decreased, which is consistent with the research results of Shi et al. [13]. Sun et al. [14] believed that replacing cement with WRMS had an adverse impact on concrete strength. Hossain et al. [15] prepared concrete by replacing river sand and mechanized sand with WRMS. The result showed that the replacement amount of WRMS should be limited to 15%. de Brito Prado Vieira et al. [16] found that the recycled aggregate crushed by WRMS can be used within 48 h after production, and its pumpability was no different from that of normal aggregate.
In addition, some researchers used recycled aggregate and WRMS to produce partition wall blocks and unfired bricks [17,18], which has good economic benefits. However, the application scope of block bricks is narrow, so their ability to absorb WRMS is limited. Considering the composition characteristics of calcium and silicate rich in WRMS and its performance characteristics of high water absorption, it is also an important application direction of WRMS as carbon capture medium [19,20], solid adsorbent [21], soil stabilizer [22] and other functional applications.
Although scholars have carried out a lot of research works on the utilization of WRMS, the low hydration activity of WRMS leads to its low utilization rate. As a result, its efficient utilization technology has not been broken through and lacks large-scale engineering application [20–22]. On the other hand, mineral admixtures are an important part of concrete, but at present, high-quality concrete admixtures such as fly ash and mineral powder are increasingly scarce. Therefore, improving the hydration activity of WRMS to prepare high-quality concrete admixtures can not only realize the self-absorption of WRMS, so as to meet the production requirements of green composite, but also can meet the increasing demand of high-quality mineral admixtures.
Aiming at the key problem of improving the hydration activity of WRMS, this study analyzed the activity and grinding characteristics of composite admixtures prepared by WRMS, furnace slag and water granulated slag. In addition, the influence mechanism on hydration products and pore structure of cement-based materials was studied. This research is of great significance for promoting the efficient utilization of WRMS and the green development of ready mixed concrete.
The cement used was P⋅O 42.5 ordinary Portland cement produced by Huaxin Cement Co., Ltd., Wuhan, China. The WRMS used was solid waste separated by sand and gravel separator. Furnace slag was from ethylene power plant, and water granulated slag was from Wuhan Iron and Steel Co., Ltd., Wuhan, China. The chemical compositions of raw materials are shown in Table 1. The basic performance indexes of cement and the WRMS were listed in Tables 2 and 3, respectively.
The fine aggregate used was ISO 679 sand, river sand and machine-made sand in line with the standard GB/T 14684. The coarse aggregate used was 5–25 mm continuous graded gravel. Polycarboxylic acid water-reducing agent, with a solid content of 20%, was used to obtain the required slump.
According to the standard GB/T 17671-1999, the cement mortars were prepared for strength test with a size of 40 mm × 40 mm × 160 mm. All specimens were cured to the specified age at the condition of 20°C ± 2°C and RH > 95%.
2.2.2 Fineness Test of Admixture
The specific surface area and fineness of admixtures were tested with reference to the brinell method in GB/T 8074-2008 and the sieve analysis method in GB/T 1345-2005, respectively.
2.2.3 Microstructure Characterization
X-ray diffraction analysis (XRD; D8 advance, Bruker, Germany) was carried out to study the phase composition of WRMS and cement-based materials. The scanning range was 5°–70° and the scanning rate was 4°/min.
Thermogravimetric-Differential scanning calorimetry (TG-DSC) analysis was measured by a synchronous thermal analyzer produced by Netzsch company of Germany. The powder for TG-DSC was put in a ceramic pallet and heated from 30°C to 1000°C at a heating rate of 10 °C/min with nitrogen protection.
Scanning electron microscope (SEM; JSM-5610LV, JEOL, Japan) was conducted to observe the surface morphology of the specimens. To prepare SEM samples, cement hydration must be stopped via immersing broken pieces in an alcohol solution for 24 h.
The porosity and pore size distribution of the specimens were measured by Mercury intrusion porosimetry (MIP). The instrument used was the Auto Pore IV 9510 Mercury porosimeter produced by MIC company in the United States.
3.1 Performances of Concrete Admixture Prepared by Waste Residue of Ready-Mixed Concrete Station
The XRD pattern of the WRMS is shown in Fig. 2. The main mineral compositions of the WRMS are SiO2 and CaCO3 [23]. Fig. 3 shows the TG-DSC analysis result of the WRMS. It can be seen clearly that there is weight loss of the WRMS near 450°C and 700°C, which is attributed to the decomposition of Ca(OH)2 and CaCO3, respectively [24,25]. Combined with the analysis results of XRD and TG-DSC, it can be determined that there is no component harmful to cement in the WRMS, so the WRMS can be used to prepare concrete admixture.
Figure 2: XRD analysis of the WRMS
Figure 3: Thermal analysis of the WRMS
In order to investigate the variation of 45 and 80 μm sieve residue and specific surface area of the WRMS with grinding time, the WRMS was grinded for 10, 20, 30, 40 and 50 min, respectively. The result is presented in Fig. 4. In addition, the powder adhesion on the surface of steel ball in ball mill is shown in Fig. 5.
Figure 4: Effect of grinding time on sieve residue and specific surface area of the WRMS
Figure 5: Adhesion of powder on steel ball during ball milling of the WRMS
As can be seen from Fig. 4, although the specific surface area increases with the grinding time, the 45 and 80 μm sieve residue decreases rapidly at first and then increases after 30 min. This may be because there are many fine particles in the WRMS. After grinding for 30 min, the fine particles are bonded and agglomerated, resulting in the increase of sieve residue, which is consistent with the phenomenon shown in Fig. 5, that is, the ball inclusion and ball sticking phenomenon occur due to the extension of grinding time.
After the WRMS was ground for 30 min, the cement was replaced by the WRMS with the substitution rates of 10%, 20%, 30%, 40%, 50% and 60%, respectively. The influence of the WRMS on the strength of cement mortar was studied under different dosage conditions. The results are shown in Fig. 6. It can be seen from Fig. 6 that the strength of mortars decreases with the increase of the WRMS, which is consistent with the conclusion of Vaičiukynienė et al. [26]. Compared to the pure cement mortar system, the strength of the cement mortars with 10% content of the WRMS at 7, 28 and 90 d is reduced by 7.6%, 5.0% and 1.5%, respectively. When the content of the WRMS reaches 30%, the 7, 28 and 90 d strength of cement mortar is reduced by 19.5%, 18.0%, and 8.9%, respectively. Overall, the strength of pure cement mortar develops rapidly in the early stage, while that of the mortar incorporated with the WRMS develops slowly. This is because the activity of the WRMS in the early stage does not increase much after mechanical activation, and its incorporation is mainly the effect of micro-aggregate filling and dilution, which reduces the strength of the matrix. However, the development rate of the mortar incorporated with the WRMS increases in the later stage, which indicates that the pozzolanic activity of the WRMS gradually releases in the later stage.
Figure 6: Effect of the WRMS on mortar strength
3.2 Performances of Mortars Prepared by Composite Admixture
From the above study, it can be seen that the WRMS can be used as concrete admixture, but the strength of cement-based materials will be significantly reduced if the content of the WRMS exceeds 30%. Considering the excellent grindability of furnace slag and high activity of water granulated slag, the two materials can be combined with the WRMS to prepare concrete admixture.
Fig. 7 shows the mineral compositions of the WRMS, water granulated slag, furnace slag and the composite admixture. It can be seen that there is less amorphous SiO2 in the WRMS, which may be the main reason for its insufficient activity. The WRMS is mainly derived from the cementitious components in concrete, which can be used in concrete production after being activated after mechanical activation. From the perspective of the low-carbon design concept, the single use of WRMS can meet the requirements of the first level, but its usage is limited. The complementarity between different admixtures can not only solve the problem of insufficient activity of WRMS, but also improve the functionality and economy of composite admixture. For example, there is less amorphous SiO2 in slag, while there is more amorphous SiO2 in water slag. Therefore, a composite low-carbon admixture with outstanding economy and excellent environmental performance can be prepared theoretically through mineral complementarity in different industrial waste residue.
Figure 7: XRD analysis of different admixtures
The cementitious system design of ternary industrial waste residue is shown in Table 4. The WRMS, furnace slag and water granulated slag were grinded for 40 min, and the prepared composite admixture was fixed at 50% of the cement content. The compressive strength of cement mortar prepared by different proportions of composite admixture is shown in Fig. 8. Compared with the cement mortar in group A0, which is only mixed with 50% of the WRMS, the strength of the specimen in A1 at 7, 28 and 90 d increases by 11.8%, 39.9% and 10.5%, respectively. The strength of cement mortar in group A5 increases by 60.0%, 90.4% and 71.0% at 7, 28 and 90 d, respectively. In particular, the 28 d strength of cement mortar in A4, A5 and A6 increases by more than 80% compared with that in A0. The results show that the activity of admixtures can be significantly increased by the composite preparation of the WRMS, furnace slag and water granulated slag. In addition, the activity of water granulated slag is higher than that of furnace slag and the WRMS, and its dosage plays a key role in mortar strength. Moreover, the mixture of the WRMS, furnace slag and water granulated slag has a synergistic effect, which makes the particle grading more reasonable, and can further improve the filling effect of the admixture.
Figure 8: Influence of different ternary composite admixtures on mortar strength
Groups A4, A5 and A6 were selected to study the grinding characteristics of the composite admixtures. The influence of different ball milling time on sieve residue and specific surface area of ternary admixtures is shown in Fig. 9. Overall, the sieve residue of the admixtures in A4, A5 and A6 decreases with grinding time, and begins to increase after 40 min, indicating that the composite admixtures appear balling phenomenon after 40 min of grinding, and the mutual bonding effect of fine particles exceeds the dispersion effect of grinding. In addition, when the grinding time is more than 50 min, the sieve residue of A4 and A6 groups increases significantly, but the trend does not appear in A5 group. According to the comprehensive results of activity and grinding characteristics, the admixture of group A5 (WRMS:furnace slag:water granulated slag = 3:3:4) exhibits the best performance.
Figure 9: Effect of milling time on sieve residue and specific surface area of ternary admixture
3.3 Influence of Composite Admixture on Cement Hydration and Pore Structure
Cement mortars were prepared by fixing the admixture content as 50% and the water to binder ratio as 0.4. E0 was set as pure cement group, E1 as the WRMS group, and E2 as the composite admixtures group (WRMS:furnace slag:water granulated slag = 3:3:4). The influence of composite admixture on cement hydration and pore structure was studied.
XRD was used to characterize the variation of unhydrated cement particles and hydration products in the specimens cured for 7 and 28 d, and the results are shown in Fig. 10.
Figure 10: XRD analysis of cement mortars
It can be seen from Fig. 10 that the hydration products of each group of samples at different ages are composed of Ca(OH)2, CACH, AFt, etc., of which the main hydration product is Ca(OH)2 [27,28]. Compared with the mortars in group E0, the characteristic peak of SiO2 appear in E1 and E2 groups. The WRMS and composite admixture contain a small amount of fine sand, which does not participate in hydration, but can fill the voids of hardened slurry to make the structure more compact. In addition, the content of Ca(OH)2 in the samples in groups E1 and E2 is significantly reduced. On the one hand, the substitution of cement by composite admixture reduces the content of hydration products; on the other hand, the composite admixture exerts pozzolanic activity and consumes part of Ca(OH)2. In particular, the XRD analysis shows that the content of Ca(OH)2 in E2 is lower than that in E1, indicating that the pozzolanic activity of E2 is higher than that of E1.
The TG and DSC analysis results of each group of samples are shown in Figs. 11 and 12. It can be found that all samples have an obvious mass loss in the temperature range of 30°C–400°C, 400°C–550°C and 550°C–1000°C, which is due to dehydration of C-S-H gel/AFt, the dehydration of Ca(OH)2 and the decomposition of CaCO3, respectively [24,25]. Compared with the specimens of E0 group, the WRMS and composite admixtures do not change the types of hydration products. After curing for 7 d, the composite admixture greatly reduces the amount of C-S-H gel due to its low hydration activity. In addition, it also significantly reduces the content of Ca(OH)2 in the sample, which is consistent with the XRD analysis results.
Figure 11: TG analysis of cement mortars: (a) 7 d; (b) 28 d
Figure 12: DSC analysis of cement mortars: (a) 7 d; (b) 28 d
The surface morphology of each sample at different ages is shown in Fig. 13. As can be seen from Fig. 13, the samples of group E0 have a high degree of hydration at 7 d, and the hydration products are distributed on the surface of unhydrated particles, but the connection between hydration products is not very tight. In general, flocculent C-S-H gel, hexagonal calcium hydroxide and needle-rod shaped ettringite can be observed on the surface [29,30]. In the early stage, the cement hydration is rapid, and a large amount of hydration products are generated, but the matrix structure is not dense enough.
Figure 13: SEM analysis of cement mortars: (a) E0-7 d; (b) E0-28 d; (c) E1-7 d; (d) E1-28 d; (e) E2-7 d; (f) E2-28 d
For the samples cured for 7 d in groups E1 and E2, although the hydration products grow in the pores or cover the surface of unhydrated particles, the overall hydration degree of the samples is low, and there are many pores in the matrix, especially for the samples with WRMS alone, a large number of smooth unhydrated particles can be observed on its surface. The results show that for cement-based materials cured for 7 d, the WRMS and composite admixture basically do not hydrate, resulting in less hydration products in the sample. When the curing age reaches 28 d, with the increase of hydration degree, the surface of the all samples tends to be flat and the structure has become dense. In addition, compared with the mortar of group E1, there are more hydration products on the surface of the sample of group E2, and its matrix structure is more compact, indicating that the composite admixture has higher activity than the WRMS.
It is generally believed that the pores with a size larger than 50 nm are harmful and have a significant effect on the strength and permeability of cement-based materials, while the pores with a size less than 50 nm are less harmful and mainly affect the shrinkage and creep of the matrix [31]. In this study, MIP was employed to analyze the pore characteristics of the specimens. The differential curve of mercury injection and pore size distribution of each sample cured for 28 d are shown in Figs. 14 and 15, respectively.
Figure 14: Pore size distribution of cement mortars
Figure 15: Pore differential curve of cement mortars
It can be found that the proportion of pores larger than 50 nm in the sample with composite admixture is lower than that in the E0 group. In addition, the critical pore size of the pure cement sample is 62.7 nm, while the critical pore size of the E2 sample is only 40.6 nm. Compared with the pure cement sample, some harmful pores in the sample incorporated with the composite admixture turn into less harmful pores, which may be due to the pozzolanic reaction of the admixture to generate a large amount of hydration products to fill the pores of the matrix, thus improving the performance of cement-based materials [32].
In this study, concrete composite admixture was prepared by the WRMS, furnace slag and water granulated slag, and its grinding characteristics and activity were systematically investigated. The main conclusions are as follows:
• The WRMS has the feasibility to be used as concrete admixture, but it is easy to agglomerate during grinding and has low activity. In addition, the amount of the WRMS cannot exceed 30% when used as a single admixture. Composite admixture prepared by the WRMS, furnace slag and water granulated slag exhibits excellent grinding characteristics and activity. The results show that the optimum ratio of the composite admixture is WRMS: furnace slag: water granulated slag = 3:3:4. Compared with the pure cement sample, the 28 d strength of the sample incorporated with 50% composite admixture increased by 90.4%.
• The composite admixture does not change the mineral composition of the cement-based material, but reduces the content of Ca(OH)2 in the sample, and optimizes the pore structure of the matrix to make the structure closer, so as to improve the properties of cement-based material.
Funding Statement: This work was supported by the project of China State Construction Engineering Corporation (CSCEC-2020-Z-39; Zhao, R. X.; https://www.cscec.com.cn/).
Author Contributions: Conceptualization, Jinfa Jiang; methodology, Jinfa Jiang; investigation, Jinfa Jiang; resources, Long Xiong; data curation, Long Xiong; writing—original draft preparation, Jinfa Jiang; writing—review and editing, Zihan Zhou; visualization, Zihan Zhou; supervision, Zihan Zhou; project administration, Ming Bao; funding acquisition, Ming Bao. All authors have read and agreed to the published version of the manuscript.
Conflicts of Interest: The authors declare that they have no conflicts of interest to report regarding the present study.
References
1. de Paula, H. M., de Oliveira Ilha, M. S., Andrade, L. S. (2014). Concrete plant wastewater treatment process by coagulation combining aluminum sulfate and moringa oleifera powder. Journal of Cleaner Production, 76, 125–130. https://doi.org/10.1016/j.jclepro.2014.04.031 [Google Scholar] [CrossRef]
2. Raupp-Pereira, F., Silva, L., Segadães, A. M., Paiva, H., Labrincha, J. A. (2007). Effects of potable water filtration sludge on the rheological behaviour of one-coat plastering mortars. Journal of Materials Processing Technology, 190(1–3), 12–17. https://doi.org/10.1016/j.jmatprotec.2007.03.120 [Google Scholar] [CrossRef]
3. Prošek, Z., Trejbal, J., Nežerka, V., Goliáš, V., Faltus, M. et al. (2020). Recovery of residual anhydrous clinker in finely ground recycled concrete. Resources, Conservation and Recycling, 155, 104640. https://doi.org/10.1016/j.resconrec.2019.104640 [Google Scholar] [CrossRef]
4. Abed, M., Nemes, R., Lublóy, É. (2020). Performance of self-compacting high-performance concrete produced with waste materials after exposure to elevated temperature. Journal of Materials in Civil Engineering, 32(1), 05059004. https://doi.org/10.1061/(ASCE)MT.1943-5533.0002989 [Google Scholar] [CrossRef]
5. Kluge, M., Gupta, N., Watts, B., Chadik, P. A., Ferraro, C. et al. (2018). Characterisation and management of concrete grinding residuals. Waste Management & Research, 36(2), 149–158. https://doi.org/10.1177/0734242X17744040 [Google Scholar] [PubMed] [CrossRef]
6. Letelier, V., Ortega, J., Muñoz, P., Tarela, E., Moriconi, G. (2018). Influence of waste brick powder in the mechanical properties of recycled aggregate concrete. Sustainability, 10(4), 1037. https://doi.org/10.3390/su10041037 [Google Scholar] [CrossRef]
7. Martins, J. V., Garcia, D. C. S., Aguilar, M. T. P., dos Santos, W. J. (2021). Influence of replacing portland cement with three different concrete sludge wastes. Construction and Building Materials, 303. https://doi.org/10.1016/j.conbuildmat.2021.124519 [Google Scholar] [CrossRef]
8. Vieira, L. B. P., de Figueiredo, A. D., Moriggi, T., John, V. M. (2019). Waste generation from the production of ready-mixed concrete. Waste Management, 94, 146–152. https://doi.org/10.1016/j.wasman.2019.05.043 [Google Scholar] [PubMed] [CrossRef]
9. Sealey, B. J., Phillips, P. S., Hill, G. J. (2001). Waste management issues for the UK ready-mixed concrete industry. Resources Conservation and Recycling, 32(3–4), 321–331. https://doi.org/10.1016/S0921-3449(01)00069-6 [Google Scholar] [CrossRef]
10. Tam, V. W. Y. (2008). Economic comparison of concrete recycling: A case study approach. Resources, Conservation and Recycling, 52(5), 821–828. https://doi.org/10.1016/j.resconrec.2007.12.001 [Google Scholar] [CrossRef]
11. Fraile-Garcia, E., Ferreiro-Cabello, J., Lopez-Ochoa, L. M., Lopez-Gonzalez, L. M. (2017). Study of the technical feasibility of increasing the amount of recycled concrete waste used in ready-mix concrete production. Materials, 10(7), 817. https://doi.org/10.3390/ma10070817 [Google Scholar] [PubMed] [CrossRef]
12. Audo, M., Mahieux, P. Y., Turcry, P. (2016). Utilization of sludge from ready-mixed concrete plants as a substitute for limestone fillers. Construction and Building Materials, 112, 790–799. https://doi.org/10.1016/j.conbuildmat.2016.02.044 [Google Scholar] [CrossRef]
13. Shi, Z., Lu, H. M., Yu, X. (2018). Characteristic analysis of waste slurry from mixing plant and its influence on cement paste performance. Jiangsu Architecture, (1), 109–111. [Google Scholar]
14. Sun, C. J., Zhang, X. Y., Wang, X. L. (2015). Experimental study on waste sand in concrete. Ready Mixed Concrete, (11), 64–65. [Google Scholar]
15. Hossain, M. U., Xuan, D., Poon, C. S. (2017). Sustainable management and utilisation of concrete slurry waste: A case study in Hong Kong. Waste Management, 61, 397–404. https://doi.org/10.1016/j.wasman.2017.01.038 [Google Scholar] [PubMed] [CrossRef]
16. de Brito Prado Vieira, L., Domingues de Figueiredo, A., John, V. M. (2020). Evaluation of the use of crushed returned concrete as recycled aggregate in ready-mix concrete plant. Journal of Building Engineering, 31, 101408. https://doi.org/10.1016/j.jobe.2020.101408 [Google Scholar] [CrossRef]
17. Kou, S. C., Zhan, B. J., Poon, C. S. (2012). Properties of partition wall blocks prepared with fresh concrete wastes. Construction and Building Materials, 36, 566–571. https://doi.org/10.1016/j.conbuildmat.2011.08.063 [Google Scholar] [CrossRef]
18. Xuan, D. X., Zhan, B. J., Poon, C. S., Zheng, W. (2016). Carbon dioxide sequestration of concrete slurry waste and its valorisation in construction products. Construction and Building Materials, 113, 664–672. https://doi.org/10.1016/j.conbuildmat.2016.03.109 [Google Scholar] [CrossRef]
19. Abed, M., de Brito, J. (2020). Evaluation of high-performance self-compacting concrete using alternative materials and exposed to elevated temperatures by non-destructive testing. Journal of Building Engineering, 32, 101720. https://doi.org/10.1016/j.jobe.2020.101720 [Google Scholar] [CrossRef]
20. Sasaki, T., Sakai, Y., Hongo, T., Iizuka, A., Yamasaki, A. (2012). Preparation of a solid adsorbent derived from concrete sludge and its boron removal performance. Industrial and Engineering Chemistry Research, 51(16), 5813–5817. https://doi.org/10.1021/ie2024646 [Google Scholar] [CrossRef]
21. Mohammadhosseini, H., Yatim, J. M. (2017). Microstructure and residual properties of green concrete composites incorporating waste carpet fibers and palm oil fuel ash at elevated temperatures. Journal of Cleaner Production, 144, 8–21. https://doi.org/10.1016/j.jclepro.2016.12.168 [Google Scholar] [CrossRef]
22. Kou, S. C., Zhan, B. J., Poon, C. S. (2012). Feasibility study of using recycled fresh concrete waste as coarse aggregates in concrete. Construction and Building Materials, 28(2), 549–556. https://doi.org/10.1016/j.conbuildmat.2011.08.027 [Google Scholar] [CrossRef]
23. Yoo, D. H., Lee, J. B., Lee, H., Kim, H. G. (2022). Investigation of newly developed PCM/SiC composite aggregate to improve residual performance after exposure to high temperature. Materials, 15(5), 1959. https://doi.org/10.3390/ma15051959 [Google Scholar] [PubMed] [CrossRef]
24. He, X., Zheng, Z., Yang, J. (2020). Feasibility of incorporating autoclaved aerated concrete waste for cement replacement in sustainable building materials. Journal of Cleaner Production, 250, 119455. https://doi.org/10.1016/j.jclepro.2019.119455 [Google Scholar] [CrossRef]
25. Park, B., Choi, Y. C. (2021). Self-healing products of cement pastes with supplementary cementitious materials, calcium sulfoaluminate and crystalline admixtures. Materials, 14(23), 7201. https://doi.org/10.3390/ma14237201 [Google Scholar] [PubMed] [CrossRef]
26. Vaičiukynienė, D., Pundienė, I., Kantautas, A., Augonis, A., Janavičius, E. et al. (2020). Synergistic effect of dry sludge from waste wash water of concrete plants and zeolitic by-product on the properties of ternary blended ordinary portland cements. Journal of Cleaner Production, 244, 118493. https://doi.org/10.1016/j.jclepro.2019.118493 [Google Scholar] [CrossRef]
27. Yang, J., Zeng, J., He, X. (2022). Sustainable clinker-free solid waste binder produced from wet-ground granulated blast-furnace slag, phosphogypsum and carbide slag. Construction and Building Materials, 330, 127218. https://doi.org/10.1016/j.conbuildmat.2022.127218 [Google Scholar] [CrossRef]
28. Ahad, M. Z., Ashraf, M., Kumar, R., Ullah, M. (2018). Physico-chemical, and mechanical behaviour of mass concrete with hybrid blends of bentonite and fly ash. Materials, 12(1), 60. https://doi.org/10.3390/ma12010060 [Google Scholar] [PubMed] [CrossRef]
29. Yang, J., Zeng, J., He, X. (2021). Eco-friendly UHPC prepared from high volume wet-grinded ultrafine GGBS slurry. Construction and Building Materials, 308, 125057. https://doi.org/10.1016/j.conbuildmat.2021.125057 [Google Scholar] [CrossRef]
30. Khan, K., Ishfaq, M., Amin, M. N., Shahzada, K., Wahab, N. et al. (2022). Evaluation of mechanical and microstructural properties and global warming potential of green concrete with wheat straw ash and silica fume. Materials, 15(9), 3177. https://doi.org/10.3390/ma15093177 [Google Scholar] [PubMed] [CrossRef]
31. Mehta, P. K. (2006). Concrete structure, properties, and materials. Preticehall International. [Google Scholar]
32. He, X., Zheng, Z., Ma, M., Su, Y., Yang, J. et al. (2020). New treatment technology: The use of wet-milling concrete slurry waste to substitute cement. Journal of Cleaner Production, 242, 118347. https://doi.org/10.1016/j.jclepro.2019.118347 [Google Scholar] [CrossRef]
Cite This Article
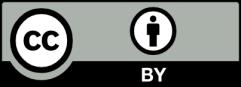
This work is licensed under a Creative Commons Attribution 4.0 International License , which permits unrestricted use, distribution, and reproduction in any medium, provided the original work is properly cited.