Open Access
ARTICLE
Performance Analysis of a Profile Control Agent for Waste Drilling Fluid Treatment
Hubei University of Technology, Wuhan, 430000, China
* Corresponding Author: Xueyu Zhao. Email:
Fluid Dynamics & Materials Processing 2023, 19(7), 1897-1905. https://doi.org/10.32604/fdmp.2023.025247
Received 30 June 2022; Accepted 25 October 2022; Issue published 08 March 2023
Abstract
A method for the treatment of hazardous waste drilling fluids, potentially leading to environmental pollution, is considered. The waste drilling fluid is treated with an inorganic flocculant, an organic flocculant, and a pH regulator. The profile control agent consists of partially hydrolyzed polyacrylamide, formaldehyde, hexamethylenetetramine, resorcinol, phenol, and the treated waste drilling fluid itself. For a waste drilling fluid concentration of 2500 mg/L, the gelling time of the profile control agent is 25 h, and the gelling strength is 32,000 mPa.s. Compared with the profile control agent prepared by recirculated water under the same conditions, the present profile control agent displays better stability, salt-resistance, and performance.Keywords
Waste drilling fluid from the drilling process contains a huge quantity of treatment agents, additives, and conditioners which, if left untreated, would cause severe pollution to the atmosphere, soil, and surface water [1–6]. To safeguard the environment and decrease the treatment cost of waste drilling fluids, therefore, it is necessary to study the waste drilling fluids treatment technology [7–13].
At present, the most prevalent drilling fluid system in China’s oil fields is water-based drilling fluid, a mixing solution of suspension and colloid with water as the dispersion medium and clay (bentonite), weighing agents, and other chemical treatment agents as the dispersing phase [14]. Water-based drilling fluids have experienced natural drilling fluid, fine dispersion drilling fluid, coarse dispersion drilling fluid, non-dispersion low solid phase drilling fluid, solid-free drilling fluid, and polymer drilling fluid. The main oilfields in China employ polymer drilling fluid; thus, treatment technology is an urgent need [15–23].
Solidification treatment is the predominant method for waste drilling fluids, but it has several drawbacks: the addition of a large amount of solidification agent increases solid waste; long-term storage poses a danger of leakage, and the treatment cost to meet standard discharge is high [24–30]. In response to these drawbacks, this study suggests waste drilling fluid as a material to prepare a profile control agent, therefore realizing the recycling and utilization of waste drilling fluid and contributing to environmental protection.
Polymeric aluminum chloride, sodium hydroxide, formaldehyde (aqueous solution with a mass concentration of 37%), hexamethylenetetramine, resorcinol, sodium chloride, anhydrous calcium chloride, magnesium chloride, potassium chloride, sodium sulfate, and sodium bicarbonate were all analytically pure and purchased without further purification from Chengdu Kelong Chemical Co. (China); the organic flocculants were prepared in the laboratory; partially hydrolyzed polyacrylamide (HPAM) is purchased from Beijing Hengju Chemical Group Co. (China), with a relative molecular mass of 1.9 × 107 and the degree of hydrolysis of 25%.
The waste drilling fluid from well XA722 in the Bohai A oilfield was a polymer drilling fluid system; the experimental water was the formation water and recirculated water from the Bohai A oilfield, with the ionic composition shown in Table 1; and the simulated core was made by core powder from the Bohai A oilfield.
Quanta 450 environmental scanning electron microscope (SEM, EFI), Brookfield DV-II viscometer (Brookfield), and multifunctional core replacement experimental equipment (Hai’an Petroleum Scientific Research Instrument Co., China) were the main experiment instruments.
2.2 Treatment of Waste Drilling Fluid
To obtain treated waste drilling fluid, solid phase particles in the waste drilling fluid were removed using an 80 mesh (0.198 mm pore size) screen, 15 g of inorganic flocculant polymeric aluminum chloride, and 0.2 g of organic flocculant were added to 1000 g of filtrate and stirred until completely dissolved, and sodium hydroxide was then added to adjust the pH of the solution to 7–7.5.
2.3 Preparation of Waste Drilling Fluid Profile Control Agent
The waste drilling fluid profile control agent is formulated with the treated waste drilling fluid, partially hydrolyzed polyacrylamide (HPAM), formaldehyde, hexamethylenetetramine, resorcinol, and phenol, with the dosage of each agent detailed in Table 2. The waste drilling fluid profile control agent is prepared as follows: add partially hydrolyzed polyacrylamide (HPAM) to a certain amount of treated waste drilling fluid and stir to dissolve it completely; add formaldehyde, hexamethylenetetramine, resorcinol, and phenol to the polymer solution in turn and stir to dissolve it completely.
2.4 Performance Evaluation of Waste Drilling Fluid Profile Control Agent
The waste drilling fluid profile control agents with 2500 and 4500 mg/L concentrations were prepared, placed in glass bottles with stoppers, sealed, and baked in an oven at a constant temperature of 65°C to create a gel. Every ten days, a Brookfield DV3T viscometer is used to determine the apparent viscosity of the waste drilling fluid profile control agents was determined at 65°C with a Brookfield DV3T viscometer.
To examine how sodium chloride impacts the performance of the profile control agent, different concentrations of sodium chloride are added to waste drilling fluid or treated waste drilling fluid to adjust the mineralization of the solution, which is then used to formulate the profile control agent. The waste drilling fluid profile control agent is then formulated with a solution of sodium chloride, put in a glass with a stopper, sealed, and placed in a constant temperature oven with a constant temperature of 65°C to form a gel. After gelatinization, the apparent viscosity of the waste drilling fluid profile control agents was evaluated at 65°C with a Brookfield DV3T viscometer.
2.4.3 Performance of Profile Improvement
The Sandpack model is used to examine the profile improvement performance of the waste drilling fluid profile control agent. As shown in Fig. 1, the experiment is carried out as follows: The sandpack model is saturated with formation water at an injection rate of 0.5 mL/min, followed by the injection of a profile control agent of 0.5 times the pore volume (PV); After 72 h, the sandpack model is injected by recirculated at the rate of 0.5 mL/min until the injection pressure stabilizes, and then measure the fractional flow at the exit of the parallel core during the experiment.
Figure 1: Flow chart of the parallel core plugging experiment
The performance of the profile control agent is characterized by the profile improvement rate, whose formula is as follows:
f=Qhb/Qlb−Qha/QlaQhb/Qlb (1)
where f—profile improvement rate of profile control agent, %;
Qhb—the percentage of Water absorption of high permeability core before profile improvement (after flow stabilization), %;
Qha—the percentage of Water absorption of high permeability core after profile improvement (after flow stabilization), %;
Qlb—the percentage of Water absorption of low permeability core before profile improvement (after flow stabilization), %;
Qla—the percentage of Water absorption percentage of low permeability core after profile improvement (after flow stabilization), %.
3.1 Apparent Viscosity of Polymer Solution
As shown in Fig. 2, the viscosity of polymer solution made with treated waste drilling fluid is somewhat lower than that of polymer solution made with recirculated water, but the polymer still has excellent viscosity increasing performance. After flocculant and sodium hydroxide treatment, the water quality of the waste drilling fluid was improved, primarily because the flocculant can provide a large number of complex ions, which can strongly adsorb the colloidal particles in the waste drilling fluid and coagulate the colloids via adsorption, bridging, and cross-linking, thereby reducing the influence of various treatment agents and additives in the drilling fluid on viscosity and enhancing the performance of the polymer. It is evident from the viscosity data of the polymer solution that the treated waste drilling fluid may be substituted for the recirculated water in the preparation of the profile control agent.
Figure 2: Effect of water quality on the viscosity of polymer solutions under varying concentrations. ◼ 2500-RW; ○ 2500-TWDF; ▲ 4500-RW; ▽ 4500-TWDF
3.2 Microstructure of Profile Control Agents
The microstructure of profile control agents made with treated waste drilling fluid and recirculated water was observed by scanning electron microscope (SEM). From Fig. 3, it is evident that both kinds of profile control agents have a spatial mesh structure, which is advantageous for locking the water molecules and maintaining the strength and stability of the profile control agents. Compared to the profile control agents made with recirculated water, the profile control agents made with treated waste drilling fluid have a more uniform and fine spatial mesh structure, which is advantageous for maintaining the binding ability of water molecules.
Figure 3: SEM images of 2500-PCAWDF and 2500-PCARW. (a) PCAWDF, 200×; (b) PCAWDF, 500×; (c) PCAWDF, 1000×; (d) PCARW, 200×; (e) PCARW, 500×; (f) PCARW, 1000×
3.3 Gelling Strength of Profile Control Agent
The apparent viscosity characterizes the gelling strength of the profile control agent, and Fig. 4 depicts the curve of the apparent viscosity of the profile control agent at various concentrations and place time. The gelatinization time of 500-PCAWDF and 2500-PCARW is about 25 h, and the viscosity after gelatinization is 18,000 mPa.s. While the gelatinization period for 4500-PCAWDF and 4500-PCARW is about 15 h and the viscosity after gelatinization is 32,000 mPa.s. This suggests that the apparent viscosity of the profile control agent generated with treated waste drilling fluid and recirculated water is comparable.
Figure 4: Effect of place time on the apparent viscosity of profile control agents. ◼ 2500-PCARW; ○ 2500-PCAWDF; ▲ 4500-PCARW; ▽ 4500-PCAWDF
The apparent viscosity of the profile control agent produced with treated waste drilling fluid and recirculated water reduced as the place time after gelatinization, as shown in Fig. 5. In the first 200 days, the apparent viscosity of 2500-PCARW was somewhat greater than that of 2500-PCAWDF, but as the place time was extended, 2500-PCAWDF demonstrated superior temperature resistance. Both 4500-PCARW and 4500-PCAWDF showed the same trend. This might be related to the microstructure of the profile control agent. The water quality of the waste drilling fluid was improved by the addition of flocculants and sodium hydroxide, and the spatial mesh structure of the profile control agent became more uniform and finer, resulting in a stronger binding force on water molecules and a lower likelihood of dehydration, resulting in stable performance.
Figure 5: Effect of place time on the apparent viscosity of profile control agents. ◼ 2500-PCARW; ○ 2500-PCAWDF; ▲ 4500-PCARW; ▽ 4500-PCAWDF
3.5 Performance of Salt-Resistance
When sodium chloride is introduced to the profile control agent, the molecular chain of partially hydrolyzed polyacrylamide (HPAM) curls, resulting in a significant decrease in the agent’s strength. As shown in Fig. 6, the curve of apparent viscosity and sodium chloride concentration reveals that sodium chloride has a greater effect on the apparent viscosity of profile control agents after gelatinization, and the higher the sodium chloride concentration, the lower the apparent viscosity of profile control agents. As sodium chloride concentration increases, the apparent viscosity of the conditioning agent decreases. The profile control agents made with the treated waste drilling fluid have increased salt-resistance and viscosity under the same circumstances.
Figure 6: Effect of NaCl concentration on the apparent viscosity of profile control agents. ◼ 2500-PCARW; ○ 2500-PCAWDF; ▲ 4500-PCARW; ▽ 4500-PCAWDF
Table 3 demonstrates that the profile control agents formulated with treated waste drilling fluids and recirculated water have excellent profile improvement performance. After the injection of profile control agents, the fractional flow rate of the relatively high permeability sandpack model decreases, and the water absorption profile is significantly improved. As the concentration of the profile control agent increases, so does the pace of profile improvement. Under the same experimental settings, the profile improvement was greater when profile control agents were made with treated waste drilling fluid compared to recirculated water.
(1) This paper devises a treatment method for waste drilling fluid. After the removal of the solid phase particles from the waste drilling fluid, inorganic and organic flocculants were added, and the pH was adjusted with sodium hydroxide to 7–7.5 to create the treated waste drilling fluid that can be utilized to prepare the profile control agent.
(2) A waste drilling fluid conditioning agent system was created using partially hydrolyzed polyacrylamide (HPAM), formaldehyde, hexamethylenetetramine, resorcinol, phenol, and treated waste drilling fluid.
(3) The profile control agent created with treated waste drilling fluid has equivalent strength to the profile control agent formulated with recirculated water but has superior stability, temperature resistance, and profile improvement performance.
(4) Using treated waste drilling fluid to prepare the profile control agent not only solves the waste drilling fluid environmental pollution issue and decreases treatment costs but also supplies water for profile control and realizes recycling and utilization.
Funding Statement: The author received no specific funding for this study.
Conflicts of Interest: The author declares that they have no conflicts of interest to report regarding the present study.
References
1. Zhang, S. X., Pei, T., Yuan, M., Wang, D. D., Ma, T. Q. et al. (2021). Classification and treatment of waste drilling fluid and its efficiency analysis. Applied Chemical Industry, 50(9), 2453–2456. [Google Scholar]
2. Zhou, B. G., Ma, M. L., Yang, X. X., Wang, H., Liu, H. Y. (2021). Research on efficient treatment technology of waste water-based drilling fluid without landing. Drilling and Production Technology, 44(3), 108–111. [Google Scholar]
3. Ismail, A. R., Alias, A. H., Sulaiman, W. R. W., Jaafar, M. Z., Ismail, I. (2017). Drilling fluid waste management in drilling for oil and gas wells. Chemical Engineering Transactions, 56, 1351–1356. [Google Scholar]
4. Pereira, L. B., Sad, C. M., Castro, E. V., Filgueiras, P. R., Lacerda, V. (2022). Environmental impacts related to drilling fluid waste and treatment methods: A critical review. Fuel, 310, 122301. [Google Scholar]
5. Jones, T. G., Trevor, L. H. (1996). Drilling fluid suspensions. USA: American Chemical Society. [Google Scholar]
6. Al-Hameedi, A. T., Husam, H. A., Shari, D., Nawaf, A. A., Abdullah, F. A. et al. (2019). Environmental friendly drilling fluid additives: Can food waste products be used as thinners and fluid loss control agents for drilling fluid? SPE Symposium: Asia Pacific Health, Safety, Security, Environment and Social Responsibility, 195410. Kuala Lumpur, Malaysia. [Google Scholar]
7. Ren, W., Liu, X., Li, S., Wang, F., Tong, K. et al. (2020). Electric adsorption treatment method for recycling waste high-performance water-based drilling fluid. Petroleum Drilling Technology, 48(4), 50–55. [Google Scholar]
8. Zhang, J., Liu, X. X., Li, Y. F., Chang, X. F., Zhang, J. J. et al. (2021). Study of COD removal from the waste drilling fluid and its application chad oilfield. Journal of Water Chemistry and Technology, 43(1), 60–67. [Google Scholar]
9. He, Y., Long, Z., Lu, J. S., Shi, L. L., Yan, W. et al. (2021). Investigation on methane hydrate formation in water-based drilling fluid. Energy & Fuels, 35(6), 5264–5270. [Google Scholar]
10. Ye, B. (2020). Research on harmless treatment method of offshore waste drilling fluid. Petrochemical Technology, 27(4), 42–43. [Google Scholar]
11. Getliff, J. M., Silverstone, M. P., Shearman, A. K., Lenn, M., Hayes, T. (1998). Waste management and disposal of cuttings and drilling fluid waste resulting from the drilling and completion of wells to produce Orinoco very heavy oil in Eastern Venezuela. SPE International Conference on Health, Safety, and Environment in Oil and Gas Exploration and Production, SPE-46600-MS. Caracas, Venezuela. [Google Scholar]
12. Page, P. W., Greaves, C., Lawson, R., Hayes, S., Boyle, F. (2003). Options for the recycling of drill cuttings. SPE Exploration and Production Environmental Conference, 80583. San Antonio, Texas. [Google Scholar]
13. Tuncan, A., Tuncan, M., Koyuncu, H. (2000). Use of petroleum-contaminated drilling wastes as sub-base material for road construction. Waste Management & Research, 18(5), 489–505. [Google Scholar]
14. Zhang, Y. N. (2020). Synthesis of thermosensitive polymer and its flocculation in waste drilling fluid. China: Yangtze University. [Google Scholar]
15. Dong, W. X., Pu, X. L., Zhai, Y. F., Yi, Q. X. (2020). Treatment of waste drilling fluid with high heavy metal content by β-cyclodextrin/bentonite. Industrial Water Treatment, 40(3), 27–30. [Google Scholar]
16. Wang, C. W., Chen, Z. H., Chen, E. D., Liu, J. Y., Xiao, F. F. et al. (2021). Ultrasonic-assisted removal of undesirable submicron-sized particulates to realize sustainable and eco-friendly circulation of drilling fluid. SPE Journal, 26, 2516–2526. [Google Scholar]
17. Yang, S. S., Tong, S. Y., Li, D. S., Li, P., Sun, M. Y. et al. (2019). Research progress of harmless treatment technology of waste drilling fluid. Applied Chemical Industry, 48(12), 3037–3041. [Google Scholar]
18. Wang, Q. Y. (2019). Research on technology of waste water-based drilling fluid used in profile control and water plugging of oil well. China: China University of Geosciences (Beijing). [Google Scholar]
19. Caenn, R., George, V. C. (1996). Drilling fluids. State of the art. Journal of Petroleum Science and Engineering, 14(3–4), 221–230. [Google Scholar]
20. Steiger, R. P. (1982). Fundamentals and use of potassium/polymer drilling fluids to minimize drilling and completion problems associated with hydratable clays. Journal of Petroleum Technology, 34(8), 1661–1670. [Google Scholar]
21. Chaineau, C. H., Vidalie, J. F., Hamzah, U. S., Suripno, P., Asmaradewi, G. et al. (2003). Bioremediation of oil-based drill cuttings under tropical conditions. Middle East Oil Show, 81562. Bahrain. [Google Scholar]
22. Antle, G., Gower, P., Pruett II, J. O. (2003). Integrated waste management: Successful implementations of thermal phase separation technology for oil-and synthetic-based cuttings and drilling fluid waste. SPE/EPA/DOE Exploration and Production Environmental Conference, 80595. San Antonio, USA. [Google Scholar]
23. Barbosa, M. I. R., Amorim, L. V., Barboza, K. R. A., Ferreira, H. C. (2007). Bentonite/polymers composites development to application in drilling fluids. Asian Chemical News, 12(2), 367–372. [Google Scholar]
24. Li, J. M., Chen, Z. J., Chen, L., Wang, Y. Q., Lei, J. (2018). Study on solid-liquid separation and reuse of waste drilling fluid in sulige gas field. Drilling and Production Technology, 41(4), 89–91. [Google Scholar]
25. Li, X. G. (2018). Solidification treatment of waste drilling fluid and research on low toxicity drilling fluid. China: Northeast Petroleum University. [Google Scholar]
26. Chen, G., Wang, P., Zhao, Y., Tong, K., Zhang, J. et al. (2020). Research and application progress of waste drilling fluid treatment technology. Drilling Fluid and Completion Fluid, 37(1), 1–8. [Google Scholar]
27. Wang, Y. N., Liu, Q. W., Fan, Z. Z., Sun, A., Liang, T. et al. (2020). Synthesis of cationic rare earth-aluminum polymer hybrid flocculant and its application in waste drilling fluid treatment. Petroleum Chemical Industry, 49(5), 484–489. [Google Scholar]
28. Conner, J. R., Hoeffner, S. L. (1998). A critical review of stabilization/solidification technology. Critical Reviews in Environmental Science and Technology, 28(4), 397–462. [Google Scholar]
29. Dermatas, D., Meng, X. G. (2003). Utilization of fly ash for stabilization/solidification of heavy metal contaminated soils. Engineering Geology, 70(3–4), 377–394. [Google Scholar]
30. Cowan, K. M., Hale, A. H., Nahm, J. J. (1992). Conversion of drilling fluids to cements with blast furnace slag: Performance properties and applications for well cementing. SPE Annual Technical Conference and Exhibition, 24575. Wasinghton DC, USA. [Google Scholar]
Cite This Article
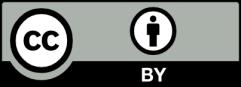
This work is licensed under a Creative Commons Attribution 4.0 International License , which permits unrestricted use, distribution, and reproduction in any medium, provided the original work is properly cited.