Open Access
ARTICLE
Fluid-Dynamics Analysis and Structural Optimization of a 300 kW MicroGas Turbine Recuperator
Shanghai University of Electric Power, Shanghai, 201306, China
* Corresponding Authors: Weiting Jiang. Email: ; Tingni He. Email:
Fluid Dynamics & Materials Processing 2023, 19(6), 1447-1461. https://doi.org/10.32604/fdmp.2023.025269
Received 02 July 2022; Accepted 13 September 2022; Issue published 30 January 2023
Abstract
Computational Fluid Dynamics (CFD) is used here to reduce pressure loss and improve heat exchange efficiency in the recuperator associated with a gas turbine. First, numerical simulations of the high-temperature and low-temperature channels are performed and, the calculated results are compared with experimental data (to verify the reliability of the numerical method). Second, the flow field structure of the low-temperature side channel is critically analyzed, leading to the conclusion that the flow velocity distribution in the low-temperature side channel is uneven, and its resistance is significantly higher than that in the high-temperature side. Therefore, five alternate structural schemes are proposed for the optimization of the low-temperature side. In particular, to reduce the flow velocity in the upper channel, the rib length of each channel at the inlet of the low-temperature side region is adjusted. The performances of the 5 schemes are compared, leading to the identification of the configuration able to guarantee a uniform flow rate and minimize the pressure drop. Finally, the heat transfer performance of the optimized recuperator structure is evaluated, and it is shown that the effectiveness of the recuperator is increased by 1.5%.Graphic Abstract
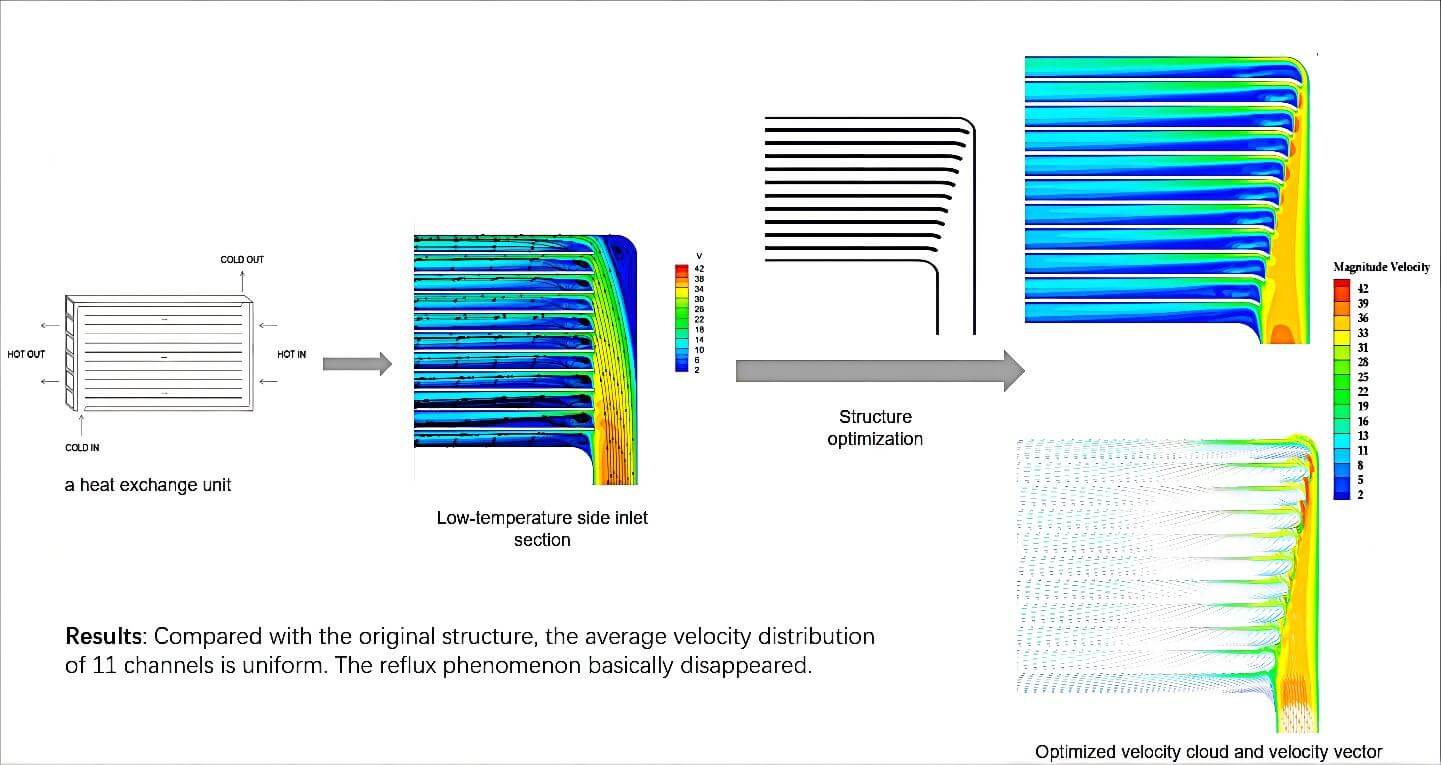
Keywords
Cite This Article
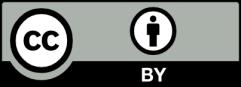
This work is licensed under a Creative Commons Attribution 4.0 International License , which permits unrestricted use, distribution, and reproduction in any medium, provided the original work is properly cited.