Open Access
ARTICLE
Optimization of Anti-Collapse Drilling Fluid Systems with High Potassium Content
1
School of Petroleum Engineering, Yangtze University, Wuhan, 430100, China
2
Key Laboratory of Drilling and Production Engineering for Oil and Gas, Wuhan, 430100, China
3
School of Petroleum Engineering, Yangtze University: National Engineering Research Center for Oil & Gas Drilling and
Completion Technology, Wuhan, 430100, China
4
Engineering Technology Research Institute of PetroChina Great Wall Drilling Engineering Co., Ltd., Panjin, 124000, China
5
PetroChina Fushun Petrochemical Branch, Fushun, 113006, China
* Corresponding Author: Shanfa Tang. Email:
Fluid Dynamics & Materials Processing 2023, 19(6), 1609-1622. https://doi.org/10.32604/fdmp.2023.025263
Received 01 July 2022; Accepted 03 September 2022; Issue published 30 January 2023
Abstract
The ash mudstone in some oil formations is highly water-sensitive. The oil formation is fractured, and the risk of well leakage and collapse is not negligible. This study presents a countermeasure for well collapse prevention, based on a “force-chemistry synergistic balance” approach and the utilization of environmentally friendly and efficient hydration inhibitors. The relevance of this approach is demonstrated considering a drilling fluid system with the high potassium content. The analysis shows that the system can maintain good rheological properties, filtration loss and suspension stability even after aging at 130°C for 16 h. The primary roll recovery of rock chips is better than 98%. The secondary rolling recovery rate is 89%. The rapid water loss is close to zero. The effects of carrying rock, sand, hydration inhibition and dispersion of drill chips are all noticeable.Keywords
Following the shale gas revolution, tight oil development has gradually become the focus of unconventional oil and gas exploration and development worldwide. Tight oil resources are rich in reserves and widely distributed [1]. In recent years, tight oil exploration has been carried out in some oil fields, and specific results have been achieved. Tight oil resources have been discovered successively in the Ordos Basin, the Luchaogou Formation in the Junggar Basin, the Middle and Lower Jurassic in the Sichuan Basin, and the Sha 4 section in the Bohai Bay Basin. However, based on the late start of tight oil exploration and development. The knowledge of this type of reservoir and geology is relatively shallow. There are still some difficulties in tight oil’s safe and rapid drilling [2–6].
The Sha 4 section in the Leijia area is dominated by shallow lakeshore-semi-deep Hu subphase sedimentation. It forms a set of sedimentary assemblages of lacustrine carbonates and mudstones. Two oil formations, Dujiatai and Gaosheng, have been developed. It is one of the leading oil and gas producing areas in the Liaohe oilfield [1,7–9]. Sand 4 section is developed with soft mudstone and oil shale, with strong hydration ability and heavy slurry. It is easy to have complicated working conditions such as well diameter reduction, downhole obstruction, well leakage, and well collapse. The site construction mainly adopts an organosilicon drilling fluid system and a standard water-based potassium chloride drilling fluid system. Many times there were accidents such as well collapse and well filling in large sections, and the construction was tough [10]. Through literature research and analysis of relevant construction data. The main reasons for well wall instability are: (1) The drilling fluid system has a wide variety of agents and low content of inhibiting agents. Therefore, inhibiting the degree of hydration dispersion is not enough. As a result, the drilling fluid and its filtrate invade the formation, resulting in well wall instability. (2) The design density is low (average density is less than 1.3 g/cm³), which is insufficient to balance the pore and collapse pressure. Malignant results include formation stress release, repeated scribing of the hole, and prolonged drilling cycles [11].
In response to such problems, the technical countermeasures of “force-chemistry combined with synergistic collapse prevention” are adopted. Mechanically, the design density of drilling fluid is increased to balance the formation collapse pressure. Chemically, the agents are selected to be highly inhibitory, temperature resistant, and environmentally friendly to mitigate the deterioration of drilling fluid performance caused by high-temperature thickening. An environmentally friendly drilling fluid system with high potassium content and strong inhibition against collapse was constructed and evaluated to help the safe and efficient development of the tight oil in the Sha4 section of the Leijia area.
The materials and source institutions used in the article can be found in Tables 1 and 2.
(1) Basic performance test of drilling fluid
Refer to “Field Test of Drilling Fluid for Oil and Gas Industry” (GB/T16783.1-2014) for testing.
(2) Mud shale swelling test
The test is conducted by SY/T5613-2000 of the Physical and Chemical Properties Test Methods for Mud Shale of the Oil and Gas Industry Standard of the People’s Republic of China.
(3) Settling stability test
Prepare the drilling fluid with the required specific gravity, use the particular stainless steel tank, age at 130°C and leave it for some time (2–24 h), and determine the density specific gravity (r1) at the top of the weighted drilling fluid column and the density specific gravity (r2) at the bottom of the column, respectively; then calculate the static settling factor (SF) according to Eq. (1), if SF = 0.50, then no static settling occurs; if SF > 0.52, then It means that the static settlement stability is poor
(1)
where SF-static settling factor; r1-density of the upper part of drilling fluid column, g/cm³; r2-density of the lower part of drilling fluid column, g/cm³.
(4) Inhibition performance test
A certain amount of core particle sample was weighed and dried to constant weight in an oven at 105°C ± 3°C. Weigh the core particles of mass m and place them in a high-temperature aging tank containing the drilling fluid to be tested. After the high-temperature rolling is completed, all the liquid and rock samples in the jar are transferred to a 0.42 mm pore size sieve. Wet sieve in a tank of tap water. Replace the tap water and continue sieving until the tap water is clear. The rock sample was transferred to a weighing bottle (m1) that had been dried and weighed, and excess water was gently poured out. Put the weighing bottle with the sample into a blast oven at 105°C ± 3°C and dry to a constant weight (accurate to 0.1 g). Remove and cool to room temperature in the desiccator, weigh and record the mass as m2 and calculate the heat roll recovery according to Eq. (2).
(2)
where ω-thermal roll recovery, %; m-initial core particle mass, g; m1-mass of the empty weighing bottle, g; m2-mass of core particles and weighing bottle after drying, g.
(5) Biotoxicity test
According to the Chinese oil and gas industry standard SY/T6788-2010 “Technical evaluation method for environmental protection of water-soluble oilfield chemical agents”, the semi-effective concentration EC50 of each treatment agent was detected by the bioluminescent bacterial method.
3.1 Well Wall Destabilization Analysis
The results of the analysis of mineral composition and clay content in the rocks of the Sha IV formation in the Leijia block are shown in Tables 3 and 4. As can be seen from Table 3, the clay minerals (>50%) in the Sha IV formation are much higher than the content of other minerals, while the range of sodium feldspar and quartz is low. Among the clay minerals, except for containing about 10% montmorillonite, kaolinite, chlorite, and illite. It is mainly rich in mixed-layer illite, including disordered mixed-layer illite and ordered mixed-layer illite, and the total proportion is as high as 75.6%. Among them, the disordered mixed-layer illite is more than 40%, and the ordered mixed-layer illite is more than 75% (Table 4). This creates conditions for the well wall rocks and drill chips to hydrate, swell and disperse, resulting in well wall instability.
3.1.2 Use of Used Drilling Fluid Systems
The current drilling fluid systems used in the sand section of the Leijia area are shown in Figs. 1, 2, and Table 5. As can be seen from Fig. 1, the drilling fluid system in the sand section of the Leijia block is mostly an organosilicon drilling fluid system (about 50%) and an ordinary water-based KCl system (about 20%), which together account for more than 70% of the total. However, during the drilling period of the Sand IV section with the existing drilling fluid system, many complicated situations such as well leakage, well collapse, and large area scratching were encountered. The average density was ≤1.3 g/cm3, and the average drilling period was ≥40 d (Fig. 2). Therefore, only the organosilicon drilling fluid system was applied relatively well (average drilling cycle of 40 d, the average density of 1.308 g/cm3). According to the analysis of drilling fluid formulation agent composition and drilling effect, it is known. Insufficient inhibitory agents in the formulation to effectively inhibit the hydration and swelling of the mud shale and low design density from balancing the collapse pressure are the two key factors causing the well wall instability.
Figure 1: Distribution of used drilling fluid system in the Sha 4 section
Figure 2: Average density and drilling cycle of drilling fluid system in Sand 4
To sum up, the rock clay mineral content in the sand section of the Leijia block is high and rich in mixed-layer illite. It is easy to hydrate and swell and disperse. The existing drilling fluid has poor inhibition, which is difficult to meet the demand of inhibiting hydration performance. At the same time, the low density of drilling fluid is challenging to balance the collapse pressure of the well wall. The combined effect of the two causes the well wall instability. In response to these two problems, this paper establishes the “ force-chemistry synergistic balance to prevent collapse” strategy. An environmentally friendly, robust collapse prevention drilling fluid system was developed for the Sha4 section in the Leijia area, considering environmental protection.
3.2 Development of High Potassium Content Strong Inhibition Anti-Collapse Drilling Fluid
A core swelling experiment was used to screen and evaluate the available inhibitors. The inhibitors provided for screening were: NH4Cl, KCl, HCOONa, polyamines, and polymeric alcohols. The experimental data are shown in Fig. 3.
Figure 3: Comparison of the inhibition effect of hydration swelling by different KCl content
From Fig. 3, it can be seen that 2% polymeric alcohol did not inhibit the hydration of the core, and its core swelling rate was higher than that of clear water (26.23%). 0.5% polyamine had almost no inhibitory effect (26.22%). 5% HCOONa and 3% HCOONa had a certain inhibitory effect, and the swelling rates were 24.89% and 21.43%, respectively. 5% KCl (15.27%) had better inhibitory effect than 3% KCl (16.81%). The inhibition effect of 5% KCl (15.27%) was better than that of 3% KCl (16.81%). The inhibition effect of 3% NH4Cl was the best, and the swelling rate was stable at 11.68% for 480 min.
In summary, 3% NH4Cl has the best inhibition effect, and 5% KCl is the second best. However, combined with the bottom boundary of the sand section 3850 m, the formation temperature is higher than 100°C, and NH4Cl starts to volatilize and release irritating gas significantly above 100°C, which cannot meet the needs of high-temperature stability of drilling fluid and environmental protection. Therefore, choosing 5% KCl as the inhibitor is more reasonable.
3.2.2 Preferred Filter Loss Reduction Agent
The high filtration loss of drilling fluid is likely to cause swelling and collapse of mud shale, resulting in unstable well walls. After drilling fluid and filtrate invade the formation, it will cause clay swelling. It will block the oil flow channel of the formation and damage the producing layer. It also thickens the filter cake, causing difficulties such as well diameter reduction, a high torque of drilling tools, start-up suction, down-drilling obstruction, and poor cementing quality. Adding filter loss reducers is an effective way to improve the filter loss performance of drilling fluids. And try to use non-sulfonated water loss reduction agents, such as KH-931 and emulsified asphalt to enhance or improve the environmental friendliness of the developed drilling fluid.
(1) KH-931 dosage optimization
KH-931 is a kind of lignite, acrylamide, and acrylonitrile as raw materials. It is a non-fluorescent anti-collapse water loss agent that integrates inhibition and filtration loss by grafting alkene monomer copolymer on natural modified materials. Its non-fluorescence and high-temperature resistance can perfectly adapt to this anti-collapse drilling fluid system research. Therefore, KH-931 was identified as the preferred filter loss reducer and inhibitor for the anti-collapse drilling fluid system. The formula 3% bentonite slurry + 5% KCl was used as the base slurry. The system filtration loss performance was measured by adding 3% KH-931, 4% KH-931, 5% KH-931, 6% KH-931, and 7% KH-931, respectively. The experimental results are shown in Fig. 4.
Figure 4: Water loss reduction performance of KH-931 with different contents
From Fig. 4, it can be seen that with the increase of KH-931 addition, the drilling fluid filtration loss showed a gradual reduction trend, and the water loss reduction effect of 6%/7% KH-931 was the most obvious, and 7% KH-931 had the highest water loss reduction rate (44%). Thus, 7% is the best dosage of KH-931.
(2) Compounding of filter loss reduction agent
DSP is a copolymer filter loss reduction agent. It can increase viscosity slightly in the brine slurry. It can effectively reduce the amount of filtration loss and improve the quality of mud cake. It has good resistance to temperature and salt, and is especially suitable for deep well and ultra-deep well drilling fluids. It can be well adapted to this anti-collapse drilling fluid system. DSP is selected as the preferred objects with PAC-Lv and emulsified asphalt, commonly used in water-based drilling fluids to reduce filtration loss. A 3% bentonite slurry + 5% KCl + 7% KH-931 was used as the base slurry to measure the filtration loss performance. The experimental results are shown in Fig. 5.
Figure 5: Performance of KH-931 in combination with filter loss reduction agent
As seen in Fig. 5, DSP and emulsified asphalt reduce the water loss effect (5%) is comparable; PAC-Lv, on the contrary, makes water loss rise. The filter cake of PAC-Lv is rougher (Fig. 6a), with small particles visible to the naked eye all around the cake; the filter cake of emulsified asphalt and DSP is dense and smooth (Figs. 6b and 6c). The filter loss reduction mechanism analysis shows that PAC-Lv is an organic polymer filter loss reduction agent. Its molecular size is beyond the range of the colloidal particles of the drilling fluid, so when this treatment agent is added, on the one hand, it cannot block the micro-pores of the filter cake. On the other hand, because PAC-Lv has a specific effect of dispersing and diluting, it forms certain damage to the reticular structure of the drilling fluid, resulting in a decrease in the structural viscosity of the drilling fluid, which produces the effect of not reducing but increasing the filter loss. In contrast, DSP and emulsified asphalt can fill the microporosity better and reduce the filtration loss effect. Therefore, DSP and emulsified asphalt were selected for compounding to study their water loss performance.
Figure 6: Filter cake diagram of PAC-Lv and DSP/emulsified asphalt formulation
The 3% bentonite slurry + 5% KCl + 7% KH-931 was selected as the base slurry. The water loss performance of the emulsified asphalt with a DSP compounding system was examined, as shown in Fig. 7. As seen from Fig. 7, as the concentration of emulsified asphalt increases, the system water loss shows a “U” shaped trend. DSP + 3.5% emulsified asphalt drops the highest rate of water loss (32%). Therefore, the combination of 7% KH-931 + DSP + 3.5% is chosen as the compounding system to reduce water loss.
Figure 7: DSP and emulsified asphalt compounding system filter loss
3.2.3 Preferred Viscosity Enhancers
Viscosity enhancers are generally composed of polymeric macromolecules, which can enhance the sand suspension and chip-carrying ability to drill fluid by entangling polymer molecules to form a mesh structure and encapsulating free water [12].
CMP is a chelated metal-polymer inclusion inhibitor with solid viscosity and filtration loss reduction capabilities, as well as a strong ability to accommodate drilling fluid solid phase and inhibit chip slurry formation, with temperature resistance up to 150°C. FA-367 is an amphoteric strong inclusion agent, which combines inhibition and excellent compatibility, and is suitable for deep and ultra-deep wells, with temperature resistance higher than 180°C [13–16]. FA-367 and CMP were selected as the preferred viscosity enhancers. The performance was preferred by adding two agents through 3% bentonite slurry + 5% KCl + 6% KH-931 + 0.3% DSP + 3.5% emulsified asphalt as the base slurry, as shown in Table 6.
From Table 6, it can be seen that: the CMP viscosity increasing effect is more prominent, plastic viscosity increased by 46%, the dynamic plastic ratio increased by 125%, and water loss is reduced to a small extent. Therefore, CMP is selected as the viscosity-increasing agent for anti-collapse drilling fluid to enhance the structural strength of drilling fluid at high downhole temperature (130°C) and achieve a better sand suspension effect.
3.2.4 Viscosity Reducer Preferred
Viscosity reducers were introduced to solve the high-temperature thickening of anti-collapse drilling fluid. Two viscosity reducers provided by the site, viscosity reducer A and viscosity reducer B, were selected and tested for performance. The experimental results are shown in Tables 7 and 8.
As seen in Table 7, viscosity reducer A has a more obvious viscosity reduction effect, with a 33% reduction in plastic viscosity and a 28% reduction in water loss. Further optimization of viscosity reducer A dosage (Table 8) shows that 0.8% viscosity reducer A can better control the thermal stability of the anti-collapse drilling fluid after aggravation and the rate of reduction of plastic viscosity is 22%. Furthermore, the rate of decline of water loss is 76% after aging at 130°C, which indicates that changing the dosage of viscosity reducer A can improve the rheological properties and wall-building properties of the high temperature thickened anti-collapse drilling fluid at 130°C. Therefore, viscosity reducer A was selected as the viscosity reducer for the anti-collapse drilling fluid, and the optimal dosage was 0.8%.
In summary, in this paper, the inhibitor, viscosity builder, filter loss reduction agent, and viscosity reducer were preferentially selected and the formulation was optimized. Finally, an environmentally friendly high potassium-containing strong inhibitor anti-collapse drilling fluid system [16–19] was developed, and its all-around performance was evaluated. The formulation was as follows: 2.5% bentonite slurry + 0.2% NaOH + 5% KCl + 7% KH-931 + 0.3% DSP + 0.25% CMP + 3.5% emulsified asphalt + 2.5% CaCO3 + 2% lubricant + 2% graphite powder + barite + 1.0% viscosity reducer A (r = 1.54 g/cm3).
3.3 Performance Evaluation of High Potassium Content Strong Inhibition Anti-Collapse Drilling Fluid Development
The recovery rate of this high potassium content anti-collapse drilling fluid was measured after rolling and aging at 130°C for 16 h, and the results are shown in Table 9. As can be seen from Table 9, this drilling fluid has excellent high-temperature inhibition. The primary recovery is higher than 98% after hot rolling. The secondary recovery is ≥89%, which shows that this drilling fluid can still effectively inhibit hydration dispersion under the condition of Sand 4 ground temperature (130°C) [18–20].
3.3.2 Settlement Stability Evaluation
The anti-collapse drilling fluid was weighted to the target density (r = 1.54 g/cm³), and the rheological properties and filtration loss performance of this drilling fluid were tested before and after weighting, respectively, as shown in Table 10. As can be seen from Table 10, the anti-collapse drilling fluid has good weight ability, the flow pattern index is 0.7, and the dynamic plastic ratio is 0.3 after weighting. The water loss is effectively controlled (about 4 mL) to meet the construction requirements.
Settlement stability reflects the ability of the weighting agent particles in the weighted drilling fluid to maintain uniform distribution in the drilling fluid. The settlement stability test results of this anti-collapse drilling fluid are shown in Table 11. From Table 11, it can be seen that the weighted drilling fluid has excellent settlement stability performance. There is almost no change in the specific gravity of the upper and lower layers when it is left for 24 h. The static settling factor SF = 0.50 shows that the anti-collapse drilling fluid has good weight ability and settling stability before and after high temperature. Therefore, it can meet the need for well wall stabilization in the sand section and extend the well wall collapse cycle.
Further study on the variation of borehole collapse pressure with borehole drilling open time in Leijia area (shown in Fig. 8) shows that when the density reaches 1.54 g/cm³, the borehole open time/collapse cycle can reach more than 20 d.
Figure 8: Variation pattern of collapse pressure (equilibrium density) with drilling opening time of borehole in Leijia block
3.3.3 Evaluation of Transient Water Loss
Instantaneous water loss is the moment (t < 2 s) when drilling fluid starts to contact the new free surface from the moment the drill bit breaks the rock at the bottom of the well to form a new free surface. The free water in the drilling fluid penetrates into the pore space of the rock. The amount of filtration loss during this time until the solid phase particles and polymers in the drilling fluid start to appear as mud cake on the well wall. For sandstone and mud shale reservoirs with large pores and fractures, a larger rapid water loss will cause more filtrate to enter the reservoir, resulting in a decrease in reservoir permeability and collapse of the well wall [21]. The filtrate output and dripping process within 1 min were photographed and recorded to evaluate the transient water loss performance of the anti-collapse drilling fluid, as shown in Fig. 9.
Figure 9: First drop of filtrate output and drop of high potassium content anti-collapse drilling fluid
As seen from Fig. 9, no filtrate was produced or ejected from the discharge orifice at the time of pressure and water loss timing. 58 s later, the first drop of filtrate was seen at the orifice. The first drop of filtrate fell in 70 s. In other words, it took a total of 58 s from the time of pressurization and water loss to the first drop of filtrate output. This indicates that the anti-collapse drilling fluid cannot lose water quickly and instantaneously at the beginning. In other words, the high potassium content anti-collapse drilling fluid can quickly form filter cake or mud cake in the well wall. Thus, it is conducive to its ability to stabilize the well wall.
1. We analyzed that the main causes of well wall destabilization in the Sha 4 section of Leijia area were poor inhibition and low design density. A “force-chemistry synergistic balance” countermeasure was developed to prevent the collapse of the well wall. Combined with the environmental protection needs, the environmentally friendly and efficient inhibitor was selected and the formulation was optimized. An environmentally friendly high potassium content strong collapse inhibitor drilling fluid system was constructed for the Sha Section 4 formation in the Leijia area. 2.5% bentonite slurry + 0.2% NaOH + 5% KCl + 7% KH-931 + 0.3% DSP + 0.25% CMP + 3.5% emulsified asphalt + 2.5% CaCO3 + 2% lubricant + 2% graphite powder + barite + 0.8% viscosity reducer A (r = 1.540 g/cm3).
2. The primary recovery rate of the drilling fluid system (130°C, 16 h) is ≥98%. Secondary recovery rate ≥89%. The rheological performance of high-temperature aging for 16 h is stable. The API water loss is 3.1 mL. The gravity of the upper and lower layers does not change significantly when the drilling fluid is left for 24 h, and there is no transient water loss formation. It has good high-temperature inhibition, weight ability, and drilling fluid settlement stability.
3. The newly developed environmentally friendly high potassium content strong inhibition anti-collapse drilling fluid meets the demand for high-temperature stabilization of tight oil drilling fluid in the Sha-4 section. In addition, it provides a reference for the selection of drilling fluids in the Sha-4 section of Leijia area and has application potential.
Funding Statement: The authors received no specific funding for this study.
Conflicts of Interest: The authors declare that they have no conflicts of interest to report regarding the present study.
References
1. Kleinberg, R. L., Paltsev, S., Ebinger, C. K. E., Hobbs, D. A., Boersma, T. (2018). Tight oil market dynamics: Benchmarks, breakeven points, and inelasticities. Energy Economics, 70(2), 70–83. DOI 10.1016/j.eneco.2017.11.018. [Google Scholar] [CrossRef]
2. Hughes, J. D. (2013). A reality check on the shale revolution. Nature, 494(7437), 307–308. DOI 10.1038/494307a. [Google Scholar] [CrossRef]
3. Arthur, M. A., Cole, D. R. (2014). Unconventional hydrocarbon resources: prospects and problems. Elements, 10(4), 257–264. DOI 10.2113/gselements.10.4.257. [Google Scholar]
4. Skogdalen, J. E., Utne, I. B., Vinnem, J. E. (2011). Developing safety indicators for preventing offshore oil and gas deepwater drilling blowouts. Safety Science, 49(8–9), 1187–1199. DOI 10.1016/j.ssci.2011.03.012. [Google Scholar] [CrossRef]
5. Fershee, J. P. (2012). The oil and gas evolution: Learning from the hydraulic fracturing experiences in North Dakota and West Virginia. Texas Wesleyan Law Review, 19, 23. DOI 10.2139/ssrn.2175798. [Google Scholar] [CrossRef]
6. Kondash, A. J., Lauer, N. E., Vengosh, A. (2018). The intensification of the water footprint of hydraulic fracturing. Science Advances, 4(8), eaar5982. DOI 10.1126/sciadv.aar5982. [Google Scholar] [CrossRef]
7. Wang, H., Ma, F., Tong, X., Liu, Z., Zhang, X. et al. (2016). Assessment of global unconventional oil and gas resources. Petroleum Exploration and Development, 43(6), 925–940. [Google Scholar]
8. Kondash, A., Vengosh, A. (2015). Water footprint of hydraulic fracturing. Environmental Science & Technology Letters, 2(10), 276–280. DOI 10.1021/acs.estlett.5b00211. [Google Scholar] [CrossRef]
9. Patterson, L. A., Konschnik, K. E., Wiseman, H., Fargione, J., Maloney, K. O. et al. (2017). Unconventional oil and gas spills: Risks, mitigation priorities, and state reporting requirements. Environmental Science & Technology, 51(5), 2563–2573. DOI 10.1021/acs.est.6b05749. [Google Scholar] [CrossRef]
10. Wang, W. (2019). Application of high-performance water-based drilling fluid technology in the Leijia Block of Liaohe Oilfield (Ph.D. Thesis). Northeast Petroleum University, China. [Google Scholar]
11. Godhavn, J. M. (2010). Control requirements for automatic managed pressure drilling system. SPE Drilling & Completion, 25(3), 336–345. DOI 10.2118/119442-PA. [Google Scholar] [CrossRef]
12. Hu, Z. B., Zhang, J. Q., Wang, Q. C., Meng, F. J., Hou, B. et al. (2021). Water base drilling fluid technology for ultra-long horizontal drilling in a tight gas well in Changqing Oilfield. Drilling Fluid & Completion Fluid, 38(2), 183–188. [Google Scholar]
13. Zhang, G., Chen, R., Hu, G., Huang, W. (2019). Low-cost drilling technology for horizontal wells with atmospheric shale gas in the outer margin of Sichuan Basin. 2019 5th International Conference on Energy Materials and Environment Engineering, vol. 295, pp. 042098. Kuala Lumpur, Malaysia. [Google Scholar]
14. Wang, Y., Wang, Y., Ran, B., Xing, P., Xin, X. et al. (2018). Research on high density oil-based drilling fluid and application in the Southern Edge of Junggar Basin, China. Open Journal of Yangtze Oil and Gas, 3(4), 253–262. DOI 10.4236/ojogas.2018.34022. [Google Scholar] [CrossRef]
15. Jiang, G., Ni, X. X., Li, W. Q., Quan, X. H., Luo, X. W. (2020). Super-amphiphobic, strong self-cleaning and high-efficiency water-based drilling fluids. Petroleum Exploration and Development, 47(2), 421–429. DOI 10.1016/S1876-3804(20)60059-3. [Google Scholar] [CrossRef]
16. Cheng, R., Lei, Z., Bai, Y., Zhang, J., Hao, H. et al. (2022). Preparation of the tetrameric poly (VS-St-BMA-BA) nano-plugging agent and its plugging mechanism in water-based drilling fluids. ACS Omega, 7(32), 28304–28312. [Google Scholar]
17. Jiang, G., Sun, J., He, Y., Cui, K., Dong, T. et al. (2021). Novel water-based drilling and completion fluid technology to improve wellbore quality during drilling and protect unconventional reservoirs. Engineering. DOI 10.1016/j.eng.2021.11.014. [Google Scholar] [CrossRef]
18. Ni, X., Jiang, G., Yang, L., Li, W., Wang, K. et al. (2019). Synthesis of superhydrophobic nanofluids as shale inhibitor and study of the inhibition mechanism. Applied Surface Science, 484(22), 957–965. DOI 10.1016/j.apsusc.2019.04.167. [Google Scholar] [CrossRef]
19. Zhang, J., Hu, Z., Zhang, Q., Wang, Q., Ni, H. et al. (2022). Water-based drilling fluid for ultra-long horizontal intervals in Changqing oil and gas field, pp. 1–19. Petroleum Science and Technology, Taylor & Francis. [Google Scholar]
20. Jie, H. (2016). Performance evaluation and field application of new water-based drilling fluid system in protecting shale gas reservoir. Electronic Journal of Geotechnical Engineering, 21, 4567–4575. [Google Scholar]
21. Huang, X., Shen, H., Sun, J., Lv, K., Liu, J. et al. (2018). Nanoscale laponite as a potential shale inhibitor in water-based drilling fluid for stabilization of wellbore stability and mechanism study. ACS Applied Materials & Interfaces, 10(39), 33252–33259. DOI 10.1021/acsami.8b11419. [Google Scholar] [CrossRef]
Cite This Article
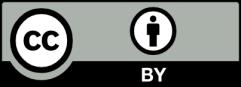
This work is licensed under a Creative Commons Attribution 4.0 International License , which permits unrestricted use, distribution, and reproduction in any medium, provided the original work is properly cited.