Open Access
ARTICLE
An Investigation into the Effects of Oil-Well Cement Expansion Agent on the Integrity of Cement Sheath
1 Sinopec Research Institute of Petroleum Engineering, Beijing, 100101, China
2 Key Laboratory of Unconventional Oil & Gas Development (China University of Petroleum (East China)), Ministry of Education, Qingdao, 266580, China
3 School of Petroleum Engineering, China University of Petroleum (East China), Qingdao, 266580, China
4 E&D Research Institute of Liaohe Oilfield Company, Panjin, 124000, China
* Corresponding Author: Shenglai Guo. Email:
Fluid Dynamics & Materials Processing 2023, 19(5), 1291-1300. https://doi.org/10.32604/fdmp.2022.022233
Received 28 February 2022; Accepted 15 April 2022; Issue published 30 November 2022
Abstract
Generally, the so-called expansion agent is very effective in eliminating all the micro-annuli that exist between the casing and the cement sheath or between the cement sheath and the formation. However, this approach can detrimentally affect the sealing ability of cement sheath if the expansion agent is used in an unreasonable way. For these reasons, in the present work, numerical simulations have been conducted to analyze the effect of elasticity modulus of cement sheath, the elasticity modulus of formation, the expansion rate of cement, the geo-stress on the micro-annulus caused by cement expansion, and the cement sheath expansion on the integrity of cement sheath and formation. The micro-annulus between the casing and the cement sheath has been found to decrease according to the ratio between the elasticity modulus of formation and the elasticity modulus of cement sheath. A positive correlation has been observed between the micro-annulus and the cement expansion ratio. The micro-annulus decreases as the geo-stress increases, but the effect of the geo-stress on the micro-annulus is much smaller. In conclusion, the expansion agent is suitable for the formation in which the elasticity modulus is higher than the cement sheath.Keywords
Nomenclature
σr, | Radial stress |
σθ, | Tangential stress |
σz, | Axial stress |
τrz, | Shear stress |
T, | Temperature |
εr, | Radial strain |
εθ, | Tangential strain |
εz, | Axial strain |
γrz, | Shear strain |
E, | Elasticity modulus |
μ, | Poisson ratio |
Er/Ec, | Elastic modulus ratio between formation and cement stone |
With the development of drilling and completion technologies, the wellbore integrity of oil and gas wells has attracted increasing attention from both academia and the industry itself. Since the loss of wellbore integrity seriously threatens the service life of oil wells and the environment, numerous research studies have so far been carried out in this field to solve these issues [1–8]. The results have suggested that features like micro-annuli existed between the casing and the cement sheath or between the cement sheath and the formation due to poor performance of cement slurry, low displacement efficiency, or change in density of the fluid in the wells during cement operations are reasons of which can induce unqualified cementing quality and annular channeling [9]. In general, the introduction of cement expansion agents in oil wells can eliminate micro-annulus, thereby improving cementing quality and preventing annular channeling [10–12]. In general, the ring-shaped objects will expand under the action of thermal force, and the inner and outer diameters of it will increase simultaneously during the expansion process [13]. Similarly, both the inner and outer diameters of cement sheath will increase when the expansion occurred in the presence of expansion agent, which is beneficial to improving the sealing ability of the cement sheath-formation interface (the second cementing interface). However, this may damage the integrity of the casing-cement sheath interface (the first cementing interface). Fortunately, Beirute et al. [7,14] have demonstrated the phenomena mentioned above. Beirute et al. [14] observed that the expansion of cement sheath formed interfacial micro- annulus at the first interface with the logging tool. Bu et al. [7] studied the effect of expansion agents on the bonding strength of the casing-cement sheath interface and found that the introduction of expansion agents reduced the bonding strength. Both studies indicated that the improper use of expansion agents would harm the sealing quality of the first cementing interface. Yang et al. [15] combined experiments with theory to investigate the changes in radial stress at the annular interface as the expansion of cement sheath. Since the elastic modulus of the simulated formation was larger than that of the cement sheath, micro-annulus forming at the first interface was not observed.
Although the inner and outer diameters of cement sheath are both enhanced upon expansion of cement sheath under in-lab conditions, the elasticity modulus of the formation under downhole conditions are different. This makes it difficult to determine the actual expansion/contraction direction of the cement sheath.
To gain a better understanding of the effect of oil-well cement expansion agent on the integrity of cement sheath, and for the correct use of an oil-well cement expansion agent, Abaqus finite element software was used to investigate the effects of elastic modulus of cement sheath, formation’s elastic modulus, the expansion ratio of cement sheath, and the geo-stress on the micro-annulus at the cementing interface caused by the expansion of cement sheath. Additionally, the impacts of the cement sheath expansion on the integrity of both cement sheath and formation were studied. To this end, measures were proposed for the proper use of the expansion agent to ensure the cementing sealing integrity. This study would shed light on the practical significance of expansion agents for enhancing the sealing integrity of oil wells.
2 Casing-Cement Sheath-Formation Finite Element Model
2.1 Mechanical Model and Assumptions
To investigate this problem, the equivalent thermal expansion was employed to simulate the expansion of the cement sheath caused by the cement expansion agent.
Several model assumptions were considered. First, all casing, cement sheath, and formation were isotropic, linearly-elastic materials. Secondly, the casing and cement sheath were ideal cylinders and concentric with the wellbore. Third is that tight contact existed between the casing and cement sheath. And fourth, the tensile failure of the cement stone was examined by the tensile failure criterion for rock.
In this model, the cylindrical coordinate was used with the axis of symmetry being the wellbore axis. Thermo-elasticity provides a linear relationship between the strains and stresses, and temperature, as shown in Eq. (1).
εr−αT=σrE−μE(σθ+σz)
εθ−αT=σθE−μE(σr+σz) (1)
εz−αT=σθE−μE(σr+σz)
and γrz=1Gτrz
In this paper, Abaqus finite element software was used to simulate the effects of cement expansion agent on the integrity of cement sheath under the casing-cement sheath-formation interaction. The selected model was based on a 3-D stress model.
The validation of the model could be demonstrated by comparing the simulation result based on this model and the experiment result obtained by Belrate et al. qualitatively [7,14]. Based on this model, the bonding between the casing and cement sheath maybe weaken when the expansion of the cement sheath occurred, which is consistent with the experiment result obtained by Belrate et al. [7,14].
2.2 Initial and Boundary Conditions of Model
Several boundary conditions were considered. First, no initial displacements existed in the casing, cement sheath, and formation. Second, the initial stress state of cement sheath in the wellbore’s annulus was not clear after cementing [16]. Here, no initial stress-induced interactions among the cement sheath, casing, and formation were considered. Third, no pressure load on the casing’s inner boundary existed. Forth, the top, bottom, and two vertical planes of the model adopted symmetrical boundary conditions. When investigating the effect of geo-stress on the integrity of the cement sheath, the remote end face of the formation adopted the pressure load boundary condition. In other cases, the remote end face of the formation adopted the boundary condition for the fixed end face. Fifth, a hard contact model was utilized to describe the contact between the casing and cement sheath, as well as between cement sheath and formation. This did not allow penetration between materials.
2.3 Geometric Parameters and Meshing of the Established Model
The outer diameter of the casing was set to 193.675 mm, the diameter of the wellbore was 240 mm, the diameter of the formation was 2.54 m, and the height of the model was 125 mm. The schematic diagram of the model is shown in Fig. 1. A quarter of the model was taken for finite element simulation due to the model’s axial symmetry. The mesh of the model adopted the linear hexahedral element C3D8R, with 3750 casing meshes, 5984 cement sheath meshes, and 3000 formation meshes. The meshing of the model is provided in Fig. 2.
Figure 1: Schematic diagram for casing-cement sheath-formation
Figure 2: Finite element model for casing-cement sheath-formation
2.4 Material Parameters of the Model
The main material parameters used in this paper were density of casing of 7.8 g/cm3, density of cement stone of 2.0 g/cm3, density of formation rock of 2.3 g/cm3, thermal expansion coefficient of cement stone of 1.2 × 10−5 K−1, elastic modulus of casing of 210 GPa, Poisson’s ratio of casing of 0.3, Poisson’s ratio of cement stone of 0.15, Poisson’s ratio of formation of 0.2, and initial temperature of the model of 313 K. The relationship between the expansion rate of cement stone k and the final temperature of the equivalent cement stone Te can be expressed by Eq. (2). By assuming expansion rates of cement stone at 0.0%, 0.05%, 0.1%, 0.15%, and 0.2%, the final temperatures of the equivalent cement stone can be calculated according to Eq. (2). The results are listed in Table 1.
k=(Te−Ti)∙α (2)
where k denotes the expansion rate of cement stone (dimensionless), Te is the final temperature of cement stone (K), Ti represents the initial temperature of cement stone (K), and α refers to the thermal expansion coefficient of cement stone (K−1).
3 Effects of Cement Sheath Expansion on Micro-Annulus at First Cementing Interface
Since the expansion of cement sheath tended to increase the inner and outer diameters of cement sheath, cement sheath would contact formation more closely to improve the sealing effect of the second cementing interface. However, this may cause debonding between casing and cement sheath, leading to the formation of micro-annulus at the first cementing interface. Therefore, the effects of various influencing factors on the micro-annulus at the first cementing interface were studied.
3.1 Effect of Formation Elastic Modulus on Micro-Annulus at First Cementing Interface
The impacts of different formation elastic moduli (3.0, 4.5, 6.0, 7.5, and 9.0 GPa) on the micro-annulus formed at the first cementing interface were investigated. To this end, the elastic modulus of cement sheath was 6 GPa and the expansion rate of cement stone was set to 0.2%. Fig. 3 shows the micro-annulus conditions of the first cementing interface under different elastic moduli of formation.
Figure 3: Micro-gaps at the first interface with different elastic modulus of formation
As shown in Fig. 3, the micro-annulus at the first cementing interface decreases gradually as the increase in the elastic modulus of the formation. When the formation elastic modulus exceeded the elastic modulus of cement sheath (6 GPa), the micro-annulus at the first interface reduced significantly. When the formation elastic modulus exceeded 7.5 GPa, the number of micro-annulus at the first interface reduced to zero. These variations indicated the expansion agent suitable for the “hard formation” environment, where the elastic modulus of formation was greater than that of the cement stone.
3.2 Influences of Elastic Modulus of Cement Stone on Micro-Gaps at the First Interface
The effects of different elastic moduli of cement stone (3.0, 4.5, 6.0, 7.5, 9.0, and 12 GPa) on the micro-gaps first cementing interface were also investigated. The elastic modulus of formation was set to 6 GPa, and the expansion rate of cement stone was 0.2%. Fig. 4 displays the micro-gaps at the first cementing interface, and how it formed under different elastic moduli of cement stone.
Figure 4: Micro-gaps at the first interface with different elastic modulus of cement sheath
In Fig. 4, the number of micro-gaps at the first cementing interface increased gradually as the rise in the elastic modulus of the cement stone. When the elastic modulus of the cement stone exceeded 4.5 GPa, micro-gap appeared at the first interface. When the elastic modulus of the cement stone exceeded the elastic modulus of the formation (6 GPa), micro-gap at the first interface increased significantly. Thus, the expansion agent was suitable for application upon cement slurry with a low elastic modulus whose elastic modulus of cement stone was less than that of formation.
3.3 Impacts of Er/Ec on Micro-Gaps at the First Cementing Interface
Based on the data shown in Sections 3.1 and 3.2, a series of Er/Ec under the fixed elastic modulus of the stratum was obtained by fixing the elastic modulus of the cement stone and adjusting the elastic modulus of the formation. Correspondingly, a series of Er/Ec under the fixed elastic modulus of the formation was obtained by fixing the elastic modulus of the formation and adjusting the elastic modulus of the cement stone. The effects of two different types of Er/Ec on the micro-gap at the first cementing interface were explored by simulation at the expansion rate of the cement stone set to 0.2%. Fig. 5 shows the effects of different Er/Ec on micro-gaps at the first cementing interface.
Figure 5: Micro-gaps at the first interface with different Er/Ec
As depicted in Fig. 5, the curves looked completely identical under Er/Ec obtained by two different methods, revealing a good correlation between micro-gaps at the first cementing interface and Er/Ec. Moreover, the increase in Er/Ec led to a gradual decline in the micro-gaps at the first cementing interface. According to the actual wellbore conditions, Er/Ec preventing the generation of micro-gaps at the first interface was determined as Er/Ec > 1.25 under the conditions of this paper. During cementing operations in the field, the reasonable elastic modulus of cement stone can be determined according to the elastic modulus of the formation.
3.4 Effects of Cement Stone’s Expansion Rates on Micro-Gaps at the First Interface under High Formation Elastic Modulus
The high formation elastic modulus refers to the elastic modulus of formation greater than that of cement sheath. Here, the effects of different cement stones’ expansion rates (0.0%, 0.05%, 0.1%, 0.15%, and 0.2%) on micro-gaps at the first cementing interface were examined with the elastic modulus of the formation of 9 GPa and elastic modulus of the cement stone of 6 GPa. Fig. 6 gathers the micro-gap conditions of the first interface under different expansion rates of cement stone.
Figure 6: Effect of cement expansion rate on micro-gaps under high formation elastic modulus
As displayed in Fig. 6, the increase in the expansion rate of cement stone under high formation elastic modulus generated no micro-gaps at the first cementing interface. Therefore, the expansion agent was suitable for cement slurry with a low elastic modulus whose elastic modulus of cement stone was lower than that of formation.
3.5 Impacts of Cement Stone’s Expansion Rates on Micro-Gaps at the First Cementing Interface under low Formation Elastic Modulus
The low formation elastic modulus refers to the elastic modulus of formation less than that of cement sheath. Here, the influences of different cement stone expansion rates (0.0%, 0.05%, 0.1%, 0.15%, and 0.2%) on the micro-gaps at the first cementing interface were evaluated with the elastic modulus of formation of 3 GPa and elastic modulus of cement stone of 9 GPa. Fig. 7 gathers the micro-gap conditions at the first cementing interface under different expansion rates of cement stone.
Figure 7: Effect of cement expansion rate on micro-gaps under low formation elastic modulus
In Fig. 7, the increase in the expansion rate of cement stone under the low elastic modulus of the formation led to an enhanced number of micro-gaps at the first cementing interface. Also, a good linear correlation was noticed between the number of micro-gaps at the first interface and the expansion rate of cement stone. Thus, greater expansion rates of cement stone in cementing operation in the circumstance of soft formation would yield a greater possibility of micro-gaps forming at the first cementing interface, which is adverse to the prevention of gas and water channeling in the well.
3.6 Influences of Geo-Stress on Micro-Gaps at First Cementing Interface
In Section 3.4, no micro-gaps were seen at the interface under the high elastic modulus of the formation. Therefore, the effects of the initial geo-stress field on micro-gaps at the first cementing interface were studied under a low elastic modulus of formation. The geo-stress was applied accordingly to the reported ODB import method [17]. Here, the geo-stress field in formation was first calculated according to the far-field geo-stress, and then applied to the casing-cement sheath-formation model to obtain the model with the initial in-situ geo-stress field, while ensuring no initial interaction force between the formation and the cement sheath ocurred. In the study, the far-field geo-stresses were set to 2, 5, 10, 20, 30, and 40 MPa. The expansion rate of cement stone was 0.2%, the elastic modulus of cement stone was 6 GPa, and the elastic modulus of the formation was 3 GPa. The geo-stress field distributions under different far-field geo-stresses are presented in Fig. 8, and the micro-gaps at the first cementing interface under different geo-stress fields are shown in Fig. 9.
Figure 8: Geo-stress distribution under different remote site stresses
Figure 9: Micro-gaps at the first interface with different remote site stresses
As depicted in Fig. 9, the increase in geo-stress led to the gradual decline in the micro-gap at the first cementing interface. However, the effects of geo-stress on the micro-gaps at the first cementing interface were indistinctive.
The expansion of the cement sheath caused by the oil-well cement expansion agent could form micro-gaps at the first cementing interface, and the ratio between formation elastic modulus and cement stone elastic modulus showed a more significant effect on the number of micro-gaps. The gradual increase in ratio led to the gradual reduction in the numbers of micro-gaps at the first cementing interface to zero, indicating the oil-well cement expansion agent was more suitable for “hard formation” environment where the elastic modulus of formation was greater than the elastic modulus of cement sheath.
The expansion rate of cement stone greatly impacted the micro-gaps at the first cementing interface under low formation elastic modulus. The increase in the expansion rate of cement stone rose the number of micro-gaps at the first cementing interface in a linear manner. At high formation elastic modulus, the expansion rate of cement stone showed an insignificant effect on micro-gaps at the first cementing interface. With the increase in geo-stress, the number of micro-gaps at the first cementing interface gradually decreased under low formation elastic modulus. However, the geo-stress displayed an insignificant effect on micro-gaps at the first cementing interface.
Funding Statement: This study was funded by the Sinopec Science and Technology Department Project (P21056).
Conflicts of Interest: The authors declare that they have no conflicts of interest to report regarding the present study.
References
1. Stormont, J. C., Fernandez, S. G., Taha, M. R., Matteo, E. N. (2018). Gas flow through cement-casing micro-annuli under varying stress conditions. Geomechanics for Energy and the Environment, 13, 1–13. DOI 10.1016/j.gete.2017.12.001. [Google Scholar] [CrossRef]
2. Gray, K. E., Podnos, E., Becker, E. (2009). Finite-element studies of near-wellbore region during cementing operations: Part I. SPE Drilling & Completion, 24(1), 127–136. DOI 10.2118/106998-PA. [Google Scholar] [CrossRef]
3. Liu, K., Gao, D., Taleghani, A. D. (2018). Analysis on integrity of cement sheath in the vertical section of wells during hydraulic fracturing. Journal of Petroleum Science & Engineering, 168, 370–379. DOI 10.1016/j.petrol.2018.05.016. [Google Scholar] [CrossRef]
4. Goodwin, K. J., Crook, R. J. (1992). Cement sheath stress failure. SPE Drilling Engineering, 7(4), 291–296. DOI 10.2118/20453-PA. [Google Scholar] [CrossRef]
5. Lv, K., Huang, Z., Ling, X., Xia, X. (2022). Analysis of the weight loss of high temperature cement slurry. Fluid Dynamics & Materials Processing, 18(5), 1307–1318. DOI 10.32604/fdmp.2022.020294. [Google Scholar] [CrossRef]
6. Restrepo, M. M., Teodoriu, C., Salehi, S., Wu, X. (2020). A novel way to look at the cement sheath integrity by introducing the existence of empty spaces inside of the cement (voids). Journal of Natural Gas Science and Engineering, 77, 103274. DOI 10.1016/j.jngse.2020.103274. [Google Scholar] [CrossRef]
7. Bu, Y., Liu, H., Song, W. (2011). Experimental study on effects of lattice expansive agent on cement-casing interfacial bonding quality. Acta Petrolei Sinica, 6, 1067–1071. [Google Scholar]
8. Zou, P., Huang, Z., Tong, Y., Tan, L., Li, R. et al. (2022). Experimental evaluation of the mechanical properties of cement sheath under high-temperature conditions. Fluid Dynamics & Materials Processing, 18(3), 689–699. DOI 10.32604/fdmp.2022.019470. [Google Scholar] [CrossRef]
9. Zhao, B. I., Gao, Y., Tan, W. (2009). Analysis of the influence factor on bonding quality of second cementing interface. Drilling & Production Technology, 32(5), 16–18. [Google Scholar]
10. Xu, P., Zou, J., Zhao, B. (2012). Developments of expanding additives for oil well cementing compositions. Oilfield Chemistry, 29(3), 368–374. [Google Scholar]
11. Zheng, G., Zhu, L., Li, Q. (2013). Study and application of plastic expansion anti-channeling slurry system. Oil Drilling & Production Technology, 35(5), 52–55. [Google Scholar]
12. Liu, H., Dai, L., Xu, X. (2005). Research on no-shrink & micro-expanding cement. Oil Drilling & Production Technology, 27, 22–25. [Google Scholar]
13. Xu, B., Wang, J. (2007). Elastic mechanics. Beijing China: Tsinghua University Press Journal Center. [Google Scholar]
14. Beirute, R. M., Wilson, M. A., Sabins, F. L. (1992). Attenuation of casing cemented with conventional and expanding cement across heavy-oil and sandstone formations. SPE Drilling Engineering, 7(3), 200–206. [Google Scholar]
15. Yang, Z., Meng, Q., Chen, X. (2012). The theoretical radial stress solution and its experimental verification of expansion cement at annulus interfaces. Petroleum Exploration and Development, 39(5), 605–611. [Google Scholar]
16. Saint-Marc, J., Garnier, A., Bois, A. (2008). Initial state of stress: The Key to achieving long-term cement-sheath integrity. SPE Annual Technical Conference and Exhibition, SPE116651. Denver, Colorado. [Google Scholar]
17. Dai, R., Li, Z., Wang, J. (2012). Research on initial geo-stress balance method based on ABAQUS. Journal of Chongqing Technology and Business University (Natural Science Edition), 29(9), 76–81. [Google Scholar]
Cite This Article
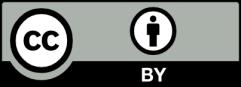
This work is licensed under a Creative Commons Attribution 4.0 International License , which permits unrestricted use, distribution, and reproduction in any medium, provided the original work is properly cited.