Open Access
ARTICLE
An Experimental Study on the Reinforcement of Weakly-Consolidated Shallow Formation in Deep Water Using an Epoxy Resin-Based Fluid
1 School of Petroleum Engineering, China University of Petroleum (East China), Qingdao, 266555, China
2 Key Laboratory of Unconventional Natural Gas Evaluation and Development in Complex Tectonic Areas, Ministry of Natural Resources, Guiyang, 550000, China
3 Guizhou Engineering Research Institute of Oil & Gas Exploration and Development, Guiyang, 550000, China
* Corresponding Authors: Yuhuan Bu. Email: ; Huajie Liu. Email:
Fluid Dynamics & Materials Processing 2023, 19(5), 1215-1226. https://doi.org/10.32604/fdmp.2022.022219
Received 27 February 2022; Accepted 23 May 2022; Issue published 30 November 2022
Abstract
The mechanical properties of Portland cement differ from the weakly consolidated shallow formation in deep water. This results in undesired abrupt changes in the compressive strength and elastic modulus at the cement–formation interface. In this study, a water-borne epoxy resin was applied as a strengthening material to reinforce the weakly consolidated shallow formation and protect the cement sheath from potential failure. The mechanical properties of the unconsolidated clay were tested, including their changes with increases in the temperature and curing time. In addition, the effects of the seawater, cement slurry alkaline filtrate, and saltwater drilling fluid were evaluated. As confirmed by the results, the strengthening fluid was excellent at reinforcing the unconsolidated clay, with a compressive strength of 2.49 MPa (after curing for 7 days), even at a dosage of 5%. A cement slurry filtrate with a high pH was suitable to produce the required strengthening of the formation, especially its early age strength. It should also be pointed out that the used fluid exhibited good compatibility with the saltwater drilling fluid and seawater behaved well as a diluent for the strengthening fluid.Keywords
A cement sheath can protect a wellbore from being crushed by formations and also isolate fluids (oil, gas, and water) underground [1–4]. Cementing quality is an essential factor in the safe, efficient, and long-term production of oil and gas wells, particularly in the ocean. Accidents caused by cementing and cement sheath failures are usually severe and expensive to deal with [5–8].
However, several difficulties threaten cement quality in the weakly consolidated shallow formation in deep water, including brittle cement sheath failure and sunken wellheads. The consolidated shallow formation is usually very weak, and its elastic modulus is lower than that of a cement sheath, differing significantly from that found with Portland cement. Consequently, there are abrupt changes in the mechanical properties at the cement–formation interface [9]. Under this condition, the cement sheath is similar to a boat floating in the weakly consolidated shallow formation, providing limited strength to support the long-term stable service of the wellbore. Many methods have been applied to address these cementing problems, such as improving the cement slurries [10–15], reinforcing the mud cake [16], enhancing the bonding strength of the cement–formation interface [17], and using self-healing cement technology [18,19]. However, the cement–formation interface and mud cake are too thin to prevent the failure of the brittle cement sheath. Significant differences remain between the mechanical properties of Portland cement and those of the weakly consolidated shallow formation.
The main components of the weakly consolidated shallow formation in deep water are unformed-rock silt and sand [7]. The structure of the weakly consolidated shallow formation is very loose and can extend hundreds of meters below the mud line [20]. Hence, it is difficult for the cement slurry to bond with the weakly consolidated shallow formation and form a single unit as it does in the normal formation. Therefore, a novel method for application in oil and gas wells in deep water was proposed to improve the wellbore and protect the cement sheath from brittle failure [20,21]. Strengthening materials were applied to penetrate the formation and stabilize the poorly consolidated clays. Subsequently, the mechanical property differences between the cement stone and adjacent formation decreased, and the stabilized formation formed a strength transition layer for the cement sheath, which could be adopted as a buffer to protect the cement sheath. Accordingly, the strength of the cement–formation interface was enhanced and the cementing quality was improved.
In this study, a water-borne epoxy resin (ER) was applied as the strengthening material, and its reinforcement properties for unconsolidated clays were studied. The effects of the effective penetration dosage, temperature, curing time, and formation fluid on the stabilization were evaluated. The results of this study provide a guide for building the strength transition layer in wellbores [22].
The ER adopted in this work was the E-51 type (colorless, epoxy equivalent: 180–190 g/eq, viscosity: 12,000–14,000 mPa⋅s at 25°C, internal code: NPEL-128) produced by NANYA Electronic Materials Co., Ltd., Kunshan, China. The hardener, a waterborne-type modified aliphatic polyamine, was purchased from SHANGHAI HANZHONG Paint Co. (Shanghai, China). The defoamer (SN-154) was obtained from SAN NOPCO Ltd. (Shanghai, China). Coupling agent KH-560 was obtained from Sinopharm Chemical Reagent Co., Ltd. (Shanghai, China). In addition, instant Na2SiO3 powder with a purity of 99% was purchased from Guangzhou Julan Chemical Technology Co., Ltd. (Guangzhou, China).
Class G oil well cement (OPC) was purchased from Jiahua Special Cement Co., Ltd. (Leshan, China). The dispersant JZ-1 was purchased from Shandong Linju Wei Sheng Special Cement Co., Ltd. (Dongying, China). Furthermore, colloidal nano silica was purchased from the Zhejiang Yuda Chemical Company (Shangyu, China).
2.2.1 Mechanical Property Tests
(1) Compressive strength (API, 2013)
The distribution of the strengthening fluid around a wellbore progresses gradually in a radial direction. The mechanical properties of the weakly consolidated shallow formation after reinforcement are difficult to test. Therefore, the compressive strength and elastic modulus were obtained from standard blocks. The dimensions of the mold adopted in this experiment were 50 mm × 50 mm × 50 mm. The curing times were 3 and 7 days. The 3-day strength demonstrated the early age properties, while the 7-day strength showed the final properties, as 7 days of curing were sufficient for the ER to reach its final properties. The samples were loaded using hydraulic compression test equipment until they failed, and the maximum compressive stress was recorded.
(2) Elastic modulus (ASTM E111-97)
The elastic modulus was tested and calculated according to the ASTM E111-97 standard. The mold adopted in this experiment was φ50 mm × 100 mm. The hydraulic compression test equipment was employed to record the stress-strain curves.
2.2.2 Preparation of Weakly Consolidated Shallow Formation Clay
It is difficult and expensive to mine the clay of weakly consolidated shallow formations in deep water. Hence, as an alternative, we utilized coastal soft clay collected from the Jiaozhou and Tangdaowan Bays in Qingdao, China. These two types of raw clays were stored after drying and sieving. Water was added during the experiment to restore them to their initial state.
2.2.3 Preparation of Slurries and Blocks
(1) ER slurries
The ER and hardener were mixed at a ratio of 1:1.3 (by weight) and manually stirred for ∼1 min. Subsequently, additives were supplemented into the mixture and blended for 3 min with a blender to achieve a homogeneous mixture. Water was adopted as a diluent, and its dosage varied from 0% to 60%, according to the experimental requirement. The dosage of the defoamer and coupling agent was 0.1 wt%.
(2) Cement slurries in evaluation experiment
The cement slurry formulation and its additives in this study have been reported in the literature [23]. The water/solids ratio in this work was 0.44. The slurry was mixed according to the API Spec. 10B-2-2013 (API, 2013) standard. Table 1 presents the cement slurry formula adopted in this study.
3.1 Weakly Consolidated Shallow Formation Particle Size Analysis
To formulate a substitute clay that was as close as possible to an actual formation for the experiment, we solicited the assistance of CNOOC (China) Co., Ltd. (China) and obtained some logging cuttings. The logging cuttings were produced while drilling in the South China Sea. Subsequently, we analyzed the chemical composition and particle size of the logging cuttings via X-ray fluorescence (XRF) and a laser particle size analyzer. The chemical composition and particle size are presented in Table 2 and Fig. 1, respectively. Moreover, a literature review was conducted; the particle sizes obtained in the 1998 National Marine Special Survey of the China State Oceanic Administration [24] are presented in Fig. 1 for comparison and reference. The chemical composition may affect the curing reaction of the ER [21], while the particle size primarily influences the penetration, structure, and porosity of the shallow formation [22]. Therefore, we took the chemical composition and particle size as the main properties required to ensure the properties of the substitute clay.
Figure 1: Particle sizes from the literature as well as those of logging cuttings and substitute clay used in the experiments
The D50 value from the literature was 6.67 μm, while that of the logging cuttings was 7.12 μm. The XRF data demonstrated that the top three elements of the logging cuttings were Si, Al, and Ca. After analyzing the chemical compositions and particle sizes of the two types of raw clay, they were mixed at a ratio of 7:3 to approximate the chemical composition and particle size of a weakly consolidated shallow formation. The chemical composition and particle size of the raw clay after mixing are presented in Table 2 and Fig. 1, respectively. In addition, the D50 value of the substitute clay was 6.26 μm. The primary difference between the chemical elements of the substitute clay and logging cuttings was Ca. It seems plausible that the shells and carapaces from marine life influenced the data, because before sieving, the clay possessed some shells and carapaces, which were too large to pass through the mesh. Moreover, some of the sand also failed for the same reason. Although some differences remained, the characteristics of the substitute clay were very close to those of the logging cuttings and data in the literature.
3.2 Mechanical Properties of Reinforced Weakly Consolidated Shallow Formation
The moisture content of the weakly consolidated shallow formation is significant [21], and the pores of a shallow formation are completely saturated with the formation fluid, which has physical and chemical properties that are close to those of seawater. The mechanical properties of a shallow formation after reinforcement depend on the amount of strengthening fluid that has penetrated. The moisture contents of weakly consolidated formations vary from 30% to 50% [21,22]. Therefore, the penetration amount in a stabilized formation cannot exceed 50% even under ideal conditions. Given the replacement efficiency, the actual penetration amount would be lower. Hence, the strengthening fluid dosage in this work varied from 5% to 30%. Fig. 2 presents the compressive strength and elastic modulus values of the unconsolidated substitute clay after being reinforced with different strengthening fluid dosages. It is evident in Fig. 2 that the compressive strength and elastic modulus had positive correlations with the strengthening fluid dosage. The reinforcing effect was excellent, with a strengthening fluid dosage of even 5% significantly increasing the compressive strength of the unconsolidated substitute clay to 2.49 MPa. The compressive strength exceeded 10 MPa (after 7 days of curing) when the dosage was 30%.
Figure 2: Mechanical properties of substitute clay after being reinforced with different strengthening fluid dosages (cured at 20°C)
3.2.1 Compressive Strength Growth with Curing Time
The unconsolidated substitute clay was mixed with the strengthening fluid at a dosage of 15% and 30% moisture. Fig. 3 presents the increase in the compressive strength with the curing time. It can be deduced from Fig. 3 that the compressive strength increased with the curing time and temperature. However, the growth rate of the strength was lower at 7°C than at 20°C and 30°C. The compressive strength increased rapidly in the first few days, and then the growth rate slowed down. The compressive strengths at 20°C and 30°C peaked at ∼6 days, while that at 7°C peaked at ∼11 days. Fig. 4 presents the variation curve of the elastic modulus with time, from which we can deduce that the elastic modulus increased with the curing time. The growth rate of the elastic modulus decreased with the curing time and was steady at ∼9–11 days. Moreover, the growth rate of the elastic modulus at 7°C was significantly lower than those at 20°C and 30°C during the first 5 days. A low elastic modulus is beneficial in counteracting part of the load by plastic deformation and protecting the cement sheath. Figs. 3 and 4 indicate that the mechanical properties of the unconsolidated substitute clay increased significantly after being stabilized by the strengthening fluid. The compressive strength was 4.71 MPa at 11 days and 7°C, and increased to 8.5 MPa at 30°C. The elastic modulus values were ∼110 and ∼293 MPa at 7°C and 30°C, respectively.
Figure 3: Compressive strength growth with time (15% strengthening fluid)
Figure 4: Variation curve of elastic modulus with time
The temperature of the weakly consolidated shallow formation in deep water is usually less than 10°C because it is near the seabed. In some places, the temperature can even be as low as 2°C [21,22]. The mechanical properties of most curable materials, including Portland cement, are significantly influenced by a low temperature. It has been reported that the hydration reaction of Portland cement is slower in a shallow formation in deep water because of the low temperature [13,21–23]. Therefore, the strengthening effect of the strengthening fluid on the weakly consolidated shallow formation requires further research.
Fig. 5 presents the effect of temperature on the compressive strength. It indicates that a low temperature exerts a significant effect on the compressive strength, especially at the early stages and ages. The compressive strength at 30°C (7.06 MPa after curing for 3 days) was twice that at 7°C (3.47 MPa after curing for 3 days). In addition, the compressive strength after 7 days (4.48 MPa, 7°C) was 29.1% greater than that after 3 days. Fig. 6 presents the effect of temperature on the elastic modulus. It shows that the elastic modulus of the stabilized clay had a positive correlation with the temperature. The test blocks indicated strong plasticity, and it was also determined in the experiments that the destructive deformation of the blocks was significantly large (25%–35% when the temperature was below 20°C).
Figure 5: Effect of temperature on compressive strength
Figure 6: Effect of temperature on elastic modulus
3.3 Effects of Formation Water on Mechanical Properties
3.3.1 Effect of Formation Moisture Content
Fig. 7 presents the effect of the moisture content of a shallow formation on the reinforcement of the unconsolidated shallow formation clay. It is evident in Fig. 7 that an increase in the moisture content significantly decreased the compressive strength and elastic modulus of the shallow formation. The compressive strength with a moisture content of 40% was 62.9% lower than that with 25% (a decrease from 7.52 to 2.79 MPa). The elastic modulus dropped by 80.2% (after 7 days of curing) when the moisture content increased from 25% to 40%. The stabilization property of the strengthening fluid significantly decreased with a higher moisture content. The close-packed solid particles in the formation were the most stable. The free water in the formation altered its packing structure, and the particles became sparse; consequently, the compressive strength dropped significantly.
Figure 7: Effect of moisture content on the formation (curing at 20°C)
3.3.2 Effect of Formation Fluid Mixed in Strengthening Fluid Curing Product
When an ER-based strengthening fluid penetrates a weakly consolidated shallow formation, it is inevitable for it to mix with seawater [21,22]. Moreover, the strengthening fluid employed in this work was a water-borne ER, and water could be adopted as a diluent to adjust the viscosity of the strengthening fluid. Fig. 8 illustrates the effect of the formation fluid mixture content on the strengthening fluid product. In addition, seawater was employed as a substitute for the formation fluid. Fig. 8 demonstrates that the compressive strength (7 days) increased when the mixture dosage was less than 40% and decreased when the dosage exceeded 40%. Water can be applied as a diluent in a water-borne ER system to reduce the viscosity and cost. This experiment suggested that the water that was applied as a diluent should not exceed 40%.
Figure 8: Effect of formation fluid mixture content on strengthening fluid product
3.3.3 Effect of Alkaline Filtrate from Cement Slurry on Strengthening Fluid Curing Product
The density of a cement slurry is greater than the formation fluid during cementing to avoid kick and blowout [10,21]. This density difference would cause a pressure differential at the borehole. During the setting of a cement slurry, the cement slurry filtrate, which is alkaline, can penetrate a formation under this pressure differential [9,21]. The alkaline filtrate may influence the curing performance of the strengthening fluid. Fig. 9 illustrates the effects of the pH value on the mechanical properties of strengthening fluid products, where the curing water in this experiment was the same as the mixed one. Fig. 9 shows that the compressive strength after 3 days decreased significantly with an increase in the pH value, while the compressive strength after 7 days decreased slightly. In addition, the elastic modulus decreased with an increase in the pH value. Hence, we can conclude that a lower pH value could increase the early age strength of the strengthening fluid product. In this experiment, the pH value of the curing water in the curing box was measured every day, and it was determined that the pH value of the curing water would always increase to 8.7–9.0. The ER was produced in an alkaline environment, and it could be inferred that the ER could release leachable alkaline during curing. The early age strength is important for oil and gas wells to prevent channeling. The results suggested that adopting low pH water as a diluent would be beneficial towards further improving the early age strength.
Figure 9: Effect of pH value on mechanical properties of strengthening fluid products. (curing at 15°C; 30% fluid mixture)
3.4 Effects of Salinity on Mechanical Properties
Inorganic salt is usually applied as an additive to the drilling fluid in deep water, and a saltwater drilling fluid is the most common type of drilling fluid for shallow formation in deep water. It is very probable for the strengthening fluid to mix with the drilling fluid and obtain high salinity when pumping or penetrating the formation. A group of experiments was designed to test the effects of the salinity on the strengthening fluid. The mechanical properties of the strengthening fluid products are illustrated in Fig. 10. Artificial seawater was utilized as a substitute for a saltwater drilling fluid in this experiment (to minimize the cost, seawater is usually employed when preparing the drilling fluid, which is applied in shallow formation drilling in deep water). The X-axis of Fig. 10 represents multiples of the standard seawater salinity (3.5%), while the control group adopted distilled water. The results in Fig. 10 indicate that the salt in the fluid that was mixed with the strengthening fluid had a positive effect on the product’s compressive strength. The elastic modulus increased with the salinity. In combination with 3.3.2, we can infer that the salt in the mixed fluid is beneficial for the early age compressive strength of the strengthening fluid. However, the benefit is minimal for the final strength. Therefore, the strengthening fluid exhibited an optimal compatibility with the saltwater drilling fluid. Moreover, seawater is an optimal choice as a diluent for the strengthening fluid as well.
Figure 10: Effects of salinity on mechanical properties of strengthening fluid products (curing at 15°C; 20 wt% fluid mixture)
First, the particle size of a weakly consolidated shallow formation was investigated via literature research and tests using logging cuttings. The D50 particle size in the literature was 6.67 μm and that in the tested logging cuttings was 7.12 μm, while the substitute clay used in this work had a value of 6.26 μm. The XRF results indicated that the top three elements of the logging cuttings were Si, Al, and Ca. The main differences in the element contents were Fe and Ca. The shells and carapaces from marine life that were too large to pass through the mesh seemed to be a plausible explanation for the difference in Ca.
Second, an experiment in which an ER-based strengthening fluid was used to reinforce the unconsolidated substitute clay indicated that even adding 5% of the strengthening fluid could significantly increase the compressive strength of the unconsolidated substitute clay to 2.49 MPa (after 7 days of curing), and the compressive strength exceeded 10 MPa when the dosage was 30%. The strength of the unconsolidated clay after reinforcement increased rapidly during the first 5 days, and then the growth rate slowed down. The maximum compressive strengths of the unconsolidated clay after being reinforced were ∼4.71 and 8.56 MPa at 7°C and 30°C after 9 days of curing, respectively. These strengths had a positive correlation with the temperature. The effects of the strengthening fluid dosage, curing time, and temperature on the compressive strength were the same. The substitute clay after reinforcement had a low elastic modulus of less than 500 MPa and a large destruction deformation of more than 20%, which was beneficial in counteracting part of the load by plastic deformation.
Third, the moisture of a weakly consolidated shallow formation had a negative effect on the compressive strength, and a high moisture content would also trigger a lower elastic modulus. An experiment where the formation fluid was mixed with the strengthening fluid indicated that a mixture of formation water would increase the compressive strength when the mixture dosage was less than 40%. In addition, a mixture dosage of more than 20% would cause a decrease in the early age strength. The pH experiments indicated that a lower pH value was beneficial for the compressive strength, especially the early age strength. The salinity experiments indicated that a higher salinity could slightly increase the compressive strength of the curing product, which implied that seawater is an optimal choice as a diluent for the strengthening fluid.
Acknowledgement: We thank the editor and the reviewers for their useful feedback that improved this paper.
Funding Statement: This work was supported by the Natural Science Foundation of China (51804332, 51974355), Major Scientific and Technological Projects of CNPC (ZD2019-184-003), Provincial Geological Exploration Fund of Guizhou Province (208-9912-JBN-UTS0), and Shandong Provincial Natural Science Foundation (ZR2017LEE005).
Conflicts of Interest: The authors declare that they have no conflicts of interest to report regarding the present study.
References
1. Mangadlao, J. D., Cao, P., Advincula, R. C. (2015). Smart cements and cement additives for oil and gas operations. Journal of Petroleum Science and Engineering, 129, 63–76. DOI 10.1016/j.petrol.2015.02.009. [Google Scholar] [CrossRef]
2. Guo, S., Bu, Y., Liu, H., Guo, X. (2014). The abnormal phenomenon of class G oil well cement endangering the cementing security in the presence of retarder. Construction & Building Material, 54, 118–22. DOI 10.1016/j.conbuildmat.2013.12.057. [Google Scholar] [CrossRef]
3. Liu, H., Bu, Y., Sanjayan, J. G., Nazari, A., Shen, Z. (2016). The application of coated superabsorbent polymer in well cement for plugging the microcrack. Construction & Building Material, 104, 72–84. DOI 10.1016/j.conbuildmat.2015.12.058. [Google Scholar] [CrossRef]
4. Zou, P., Huang, Z., Tong, Y., Tan, L., Li, R. et al. (2022). Experimental evaluation of the mechanical properties of cement sheath under high-temperature conditions. Fluid Dynamics & Materials Processing, 18(3), 689–699. DOI 10.32604/fdmp.2022.019470. [Google Scholar] [CrossRef]
5. Scientific American, How BP’s blowout ranks among top 5 oil spills in 1 graphic. https://www.scientificamerican.com/article/how-bp-s-blowout-ranks-among-top-5-oil-spills-in-1-graphic/. [Google Scholar]
6. Pan, G., Qiu, S., Liu, X., Hu, X. (2015). Estimating the economic damages from the Penglai 19-3 oil spill to the Yantai fisheries in the Bohai Sea of Northeast China. Marine Policy, 62, 14–24. DOI 10.1016/j.marpol.2015.08.007. [Google Scholar] [CrossRef]
7. Lavasani, S. M. M., Yang, Z., Finlay, J. (2011). Fuzzy risk assessment of oil and gas offshore wells. Process Safety and Environmental Protection, 89, 277–294. DOI 10.1016/j.psep.2011.06.006. [Google Scholar] [CrossRef]
8. Brannock, P. M., Sharma, J., Bik, H. M., Thomas, W. K., Halanych, K. M. (2017). Spatial and temporal variation of intertidal nematodes in the Northern Gulf of Mexico after the deepwater horizon oil spill. Marine Environmental Research, 130, 200–212. DOI 10.1016/j.marenvres.2017.07.008. [Google Scholar] [CrossRef]
9. Du, J., Bu, Y., Shen, Z., Cao, X. (2019). Maximum penetration depth and penetration time predicting model of cementing fluid flow through wellbore into weakly consolidated formation. Fractals, 27(8), 1950132. DOI 10.1142/S0218348X19501329. [Google Scholar] [CrossRef]
10. Wang, S., Jian, L., Shu, Z., Wang, J., Hua, X. et al. (2019). Preparation, properties and hydration process of low temperature nano-composite cement slurry. Construction and Building Materials, 205, 434–442. DOI 10.1016/j.conbuildmat.2019.02.049. [Google Scholar] [CrossRef]
11. Liu, H., Bu, Y., Nazari, A., Sanjayan, J. G., Shen, Z. (2016). Low elastic modulus and expansive well cement system: The application of gypsum microsphere. Construction and Building Materials, 106, 27–34. DOI 10.1016/j.conbuildmat.2015.12.105. [Google Scholar] [CrossRef]
12. Ribeiro, D., Souza, L., Paredes, J. L., Michon, P., Szakolczai, C. (2019). Applying a foamed cement operation for surface casing in a deepwater well: Case study, French Guiana. Abu Dhabi International Petroleum Exhibition & Conference, Abu Dhabi, UAE. [Google Scholar]
13. Diarra, R., Bogaerts, M., Andrews, H., Lehr, J., Osteen, N. et al. (2017). Low-temperature dispersant improves cement slurry properties in deepwater operations. Offshore Technology Conference, vol. 5, pp. 3641–3650. Houston, Texas, USA. DOI 10.4043/27534-MS. [Google Scholar] [CrossRef]
14. Pang, X., Maxson, J. K., Jimenez, W. C., Singh, J. P., Ronnie, G. M. (2017). Microscale characterization of field and laboratory foamed cement by use of X-ray microcomputed tomography. SPE Journal, 22(5), 1690–1703. DOI 10.2118/180278-PA. [Google Scholar] [CrossRef]
15. Liu, H., Li, Z., Huang, Y., Fang, M., Liu, Z. (2017). Ultra deepwater cementing development and field applications in Western South China Sea. SPE Middle East Oil & Gas Show & Conference, Manama, Kingdom of Bahrain. [Google Scholar]
16. Hao, H., Jun, G., Huang, J., Wang, Z., Wang, Q. et al. (2016). Comparative study on cementation of cement-mudcake interface with and without mud-cake-solidification-agents application in oil & gas wells. Journal of Petroleum Science & Engineering, 147, 143–153. DOI 10.1016/j.petrol.2016.05.014. [Google Scholar] [CrossRef]
17. Liu, H., Bu, Y., Guo, Q., Sanjayan, J. G. (2017). Converting hydration heat to achieve cement mixture with early strength and low hydrating-thermal dissipation. Construction and Building Materials, 151, 113–118. DOI 10.1016/j.conbuildmat.2017.06.098. [Google Scholar] [CrossRef]
18. Lu, Z., Kong, X., Yang, R., Zhang, Y., Jiang, L. et al. (2016). Oil swellable polymer modified cement paste: Expansion and crack healing upon oil absorption. Construction and Building Materials, 114, 98–108. DOI 10.1016/j.conbuildmat.2016.03.163. [Google Scholar] [CrossRef]
19. Wang, C., Bu, Y., Guo, S., Lu, Y., Sun, B. et al. (2018). Self-healing cement composite: Amine- and ammonium-based pH-sensitive superabsorbent polymers. Cement and Concrete Composites, 96, 154–162. DOI 10.1016/j.cemconcomp.2018.11.023. [Google Scholar] [CrossRef]
20. Skogdalen, J. E., Vinnem, J. E. (2012). Quantitative risk analysis of oil and gas drilling, using deepwater horizon as case study. Reliability Engineering & System Safety, 100, 58–66. DOI 10.1016/j.ress.2011.12.002. [Google Scholar] [CrossRef]
21. Du, J., Bu, Y., Shen, Z., Cao, X. (2019). A novel fluid for use in oil and gas well construction to prevent the oil and gas leak from the wellbore. Construction and Building Materials, 217, 626–637. DOI 10.1016/j.conbuildmat.2019.05.100. [Google Scholar] [CrossRef]
22. Tian, L., Bu, Y., Liu, H., Guo, S. (2022). Study on the penetration of strengthening material for deep-water weakly consolidated shallow formation. Journal of Petroleum Science and Engineering, 210, 109862. DOI 10.1016/j.petrol.2021.109862. [Google Scholar] [CrossRef]
23. Bu, Y., Hou, X., Wang, C., Du, J. (2018). Effect of colloidal nanosilica on early-age compressive strength of oil well cement stone at low temperature. Construction and Building Materials, 171, 690–696. DOI 10.1016/j.conbuildmat.2018.03.220. [Google Scholar] [CrossRef]
24. Zhang, F., Zhang, W., Yang, Q. (2003). Characteristics of grain size distributions of surface sediments in the Eastern South China Sea. Acta Sedimentologica Sinica, 21, 452–460. [Google Scholar]
Cite This Article
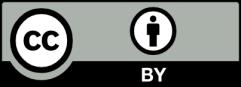
This work is licensed under a Creative Commons Attribution 4.0 International License , which permits unrestricted use, distribution, and reproduction in any medium, provided the original work is properly cited.