Open Access
ARTICLE
Numerical Analysis of Dynamical Effects Associated with a Plugging String in a Horizontal Well
1 Oil and Gas Technology Research Institute Changqing Oilfield Company, PetroChina, Xi’an, 710018, China
2 National Engineering Laboratory for Exploration and Development of Low Permeability Oil and Gas Fields PetroChina, Xi’an, 710018, China
3 Shunan Gas Mine, PetroChina Southwest Oil and Gas Field Company, Luzhou, 646000, China
4 College of Engineering, Southwest Petroleum University, Nanchong, 637001, China
* Corresponding Author: Wei Lin. Email:
Fluid Dynamics & Materials Processing 2023, 19(5), 1203-1214. https://doi.org/10.32604/fdmp.2023.022022
Received 17 February 2022; Accepted 25 July 2022; Issue published 30 November 2022
Abstract
The finite element method has been applied to simulate the dynamics of a water plugging string in a complex horizontal well of a low-permeability oilfield. The force associated with the pipe string and the packer has been determined under the sucking action of the oil well pump. Such analysis has been conducted for a real drilling well, taking into account the process of lifting, lowering, unblocking and water plugging. Comparison between field measured data and simulation data indicates that the model is reliable and accurate. The packer creep effect under different pressure differences has also been investigated in the framework of the same model.Keywords
Compared with traditional drilling technology, horizontal well drilling has obvious advantages with high economic value, which has been widely used in China [1–3]. According to the production data of Changqing Oilfield, 2300 horizontal wells had been put into operation in the oilfield by the end of December 2018, with a total production water content of 58%. With the increasing of production time, the liquid production of horizontal wells decreased significantly, while the water content increased gradually. Due to the complex wellbore trajectory of a horizontal well, particularly in water plugging, the process operation string is affected by collective action, including the pressure of the water outlet point, the indirect contact force between the horizontal section string and casing and axial force associated with the string. Therefore, the packer cannot be taken out normally, and the string is seriously deformed, failing water plugging [4–6].
To improve the success rate and efficiency of water plugging in low permeability oilfield, many Scholars have carried out relevant researches on stresses of process string. Cui [7] introduced significance of mechanical one-trip string with water finding and plugging techniques, a string structure, principle of supporting tool, operation process, problems, and solutions in field construction. To accurately analyze the dynamic mechanical properties and creep phenomenon of multi-stage and multi-stage water injection string under different working conditions, Huang et al. [8] established a three-dimensional mechanical model of water injection pipe string to analyze the dynamic mechanical properties accurately, and creep behavior of multi-stage and multi-segment water injection pipe under different working conditions. The three-dimensional trajectory of the wellbore and the spatial force associated with the multi-stage and multi-segment water injection pipe string were considered, and the creep mechanism of the packer was studied, and corresponding suggestions were put forward. Zhao et al. [9] analyzed the column axial stress state to establish a two-dimensional computational model with forced packer column and educed deblocking calculation formula to provide packer wellhead deblocking method.
To investigate the deformation of oil pipes in complex wells, Lubinski [10] established a analytical model of rotary drilling strings, and the critical helical load of the drill string was solved. Then Mitchell [11–13] investigated the lateral buckling of pipe with connectors in curved wellbores, and the new buckling solutions for extended reach wells were analyzed. Taking into account the well trajectory, drillstring/wellbore friction and cress section, Hajianmaleki et al. [14–17] studied the critical buckling load of the tubular strings.
Although there are a series of previous studies on the mechanical of plugging string in horizontal well, the complex contact state between the string and the well wall/casing is not considered, resulting in a particularly prominent problem in the process of horizontal well, that is, there is a large gap between the stress state of the string and the actual working condition. Therefore, this paper established the nonlinear finite element of three-dimensional full well process string and carried out the mechanical analysis of water plugging string in a horizontal well.
2 Water Plugging String Assembly
2.1 Mechanical Analysis of Water Plugging String
In the wellbore, the process string, tools and packer are affected by fluid pressure. The pressure may be unequal when the packer blocks in different sections, resulting in pressure differences at both ends of the packer [18,19]. Here, the pressure distributions of each section of the packer are supposed as P1, P2 and P3 (in Fig. 1).
Figure 1: Pressure field of mechanical water finding and plugging string
The pressure on packer 1 can be expressed as:
F1=P1∗Aext−P2∗Aint (1)
The pressure on packer 2 can be expressed as:
F2=(P2−P3)∗Aext (2)
where,
P1 is the hydrostatic pressure, P1=ρ0gH ;
ρ0 is the annular liquid density;
H is the height from moving liquid level to well bottom;
Aext is the annular cross-sectional area;
Aint is the cross-sectional area of borehole.
2.2 Mechanical Analysis of Packer
When the packer setting is finished, the displacement of the casing interface is constrained so that the casing can only move along the axial direction of the string, that is, UX = 0; UY = 0 as shown in Fig. 2; when the axial external force (the packer suffered) F > fmax, the packer begins to slide, where, the fmaxis the maximum static friction between the packer rubber and the casing.
Figure 2: Mechanical boundary of the string packer
In water plugging, the pressure of each section changes with the sucking of the oil well pump. Axial pressure on packer can be expressed as:
F=(P3−P2)∗(πD2/4)−f2 (3)
The up-lift force associated with the string can be expressed as:
F1=P3∗πD2/4−P1∗π(D2−d2)/4 (4)
where, D is the diameter of the casing;
d is the outer diameter of tube;
f2 is the friction between packer 2 and casing.
ΔF1=F1−F (5)
ΔF2=F2−F (6)
{ΔF>fmaxcreepΔF<fmaxnocreep (7)
where, ΔF is the axial external force on the packer. When the creep occurred in the trial, the upper pressure on packer 1 was greater than the lower pressure, which is easy to damage the rubber when unpacking the packer or even cannot unpack the packer.
In water plugging, the packer is downhole tool, and plays a vital role in the operation. To normally pull the water plugging packer out of the hole normally, this paper studies the unblocking force of the water plugging string packer. The finite element simulation model of water plugging string is first established according to the beam element theory. Then, the model is verified by the hook load in the lowering process of a practical well logging. Finally, the forces associated with the packer under different pressure conditions are carried out.
3 Modeling of Mechanical Plugging String in Horizontal Well
When water output happens in the toe of the horizontal well, the water plugging string is a catchable bridge plug without complex string assembly. Therefore, this paper mainly focuses on condition 3: the finite element modeling and analysis of unblocking force characteristic of the multi-interval water plugging string assembly in the horizontal section. To improve the simulation efficiency and convergence, the water plugging string model [20] is simplified as follows:
(1) The plugging string is simulated by a beam element;
(2) The casing is a rigid body without elastic deformation;
(3) The mathematical model of packer is based on the boundary condition of water plugging string.
In the stress analysis of water plugging string, the contact state between string and casing should be considered. In this paper, the water plugging string is simulated by beam element. The contact judgment between the string and the borehole is shown in Fig. 3.
Figure 3: The contact forms between the drill string and borehole
Based on the above geometric relationship, to study the contact friction between beam elements, the vector of gap function dv which is between a pair of nearest points can be obtained:
dv=(xmn−xsn) (8)
The normal gap function dv and two tangential gap functions dn2 and dn3 can be obtained by projecting the gap function vector dv to the normal n1 and tangential directions n2,n3 at the contact respectively so that the resultant gap function in the tangential direction can be calculated as:
{dn2=dv⋅n2dn3=dv⋅n3dT=√d2n2+d2n3 (9)
The cross-section radii of the beam elements are Dh/2 and D/2 , respectively. According to the value of the normal gap function dn , the criterion for judging whether the contact occurs is:
{dn=‖xmn−xsn‖−Dh/2−D/2>0⇒No Contactdn=‖xmn−xsn‖−Dh/2−D/2<0⇒Contact (10)
The algorithm is used to judge the contact state between the string and the borehole, which is shown in Fig. 4.
Figure 4: Contact between plugging string and borehole
4 Numerical Analysis of Plugging String in Horizontal Well
According to an actual well in Western China, the force analysis the string under different processes at different test positions in Table 1 are carried out, including running in, tripping out, unblocking, and water plugging. The well (shown in Fig. 5) is perforated and fractured into ten sections which are divided into five combined sections for conducting the water finding and water plugging tests with double-sealing drag sucking action.
Figure 5: Double packer drag water finding string
The size of the casing is 5 1/2 with a thickness of 7.72 mm;
Parameter of the work-over fluid is 970 kg/m3, 39 mPa.s;
Downhole temperature is 65°C; operating speed is 6 m/min;
Tubing type is 2 7/8 ordinary tubing with a thickness of 5.5 mm.
Test procedure
(1) During the lowering process, the first combined section (Sections 1 and 2) is tested when the upper end of water finding packer is set between the second and third sections, the bottom of the packer is set at the lower part of the first section;
(2) During the lifting process, the second combined section (Sections 3 and 4) is tested when the upper end of water finding packer is set between the Sections 4 and 5, the bottom of the packer is set between the Sections 2 and 3;
(3) During the lifting process, the third combined section (Sections 5 and 6) is tested when the upper end of water finding packer is set between the Sections 6 and 7, the bottom of the packer is set between the Sections 3 and 4;
(4) During the lifting process, the fourth combined section (Sections 7 and 8) is tested when the upper end of water finding packer is set between the Sections 8 and 9, the bottom of the packer is set between the Sections 6 and 7;
(5) During the lifting process, the fifth combined section (Sections 9 and 10) is tested when the upper end of water finding packer is set at the upper part of Section 10, the bottom of the packer is set between the Sections 8 and 9;
The force analyses are carried out for the first test and the third test positions.
4.1 Force Analysis During Lifting in the Real Drilling Well
Based on the established force analysis of water finding and plugging string, the stress analyses are studied on the axial force, contact force, and friction force associated with the string in the process of lifting, lowering and unblocking.
The test type of the well is with a vertical section–the first oblique section-a steady inclined section–the second oblique section-a horizontal section. When the string is lifted at 6 m/min, the axial force associated with the string is shown as Fig. 6.
Figure 6: Axial force during lifting (in the first position and third position)
It can be shown from the Fig. 6 that the axial force associated with the string is distributed nonlinearly along the wellbore trajectory at the first test position and the third test position, and the whole well string is in the tensile state. The axial force in the second oblique section changes more stable than that in the first oblique section. The field test shows that the hook loads of the first and third positions are 25.6 and 24.3 tons in the lifting, respectively. The error between the test results and the simulation results is less than 10%.
The contact force between string and casing during lifting is shown in Fig. 7:
Figure 7: The contact force during lifting (in the first position and third position)
It can be seen from the Fig. 7 that the contact force associated with the string at the entrance of the two oblique sections is significantly higher than that of other sections, and the contact force in the horizontal section is relatively stable.
4.2 Force Analysis of the Lowering Process in the Real Drilling Well
When the string is lowering at 6 m/min, the axial force associated with the string is shown in Fig. 8.
Figure 8: The axial force during lowering (in the first position and third position)
It can be seen from the Fig. 8 that the axial force associated with the string is distributed nonlinearly along the wellbore trajectory at the first test position and the third test position, and the string is under pressure at the second oblique section. The axial force in the second oblique section changes more stable than that in the first oblique section. The field test shows that in the lowering process, the hook loads of the first position and the third positions are 18.2 and 17.4 tons, respectively. The error between the test results and the simulation results is within 10%.
It can be seen from the Fig. 9 that during lowering, the contact forces associated with the string in the oblique entrance section and the lower part of the second oblique section are significantly higher than that of other sections. Moreover, the contact force in the horizontal section changes significantly at the end of the string.
Figure 9: The contact force during lowering (in the first position and third position)
From the force analyses of the string in lifting and lowering, it is shown that the axial force associated with the string is non-linear distributed along the string, and it in the second oblique section changes obviously during tripping. During the lowering process, the pressure on the string in the first oblique section is more severe. At the same time, compared with the measurement of hook load, the error is less than 10%, which shows that the simulation result is reliable.
4.3 Force Analysis of Unblocking in the Real Drilling Well
In the actual drilling well, the water finding is obtained using double packers with drag sucking function. The unblocking process of the packer is simulated and analyzed, and the rated unblocking force is set as 3 tons. During the packer unblocking process, the variation of wellhead load and axial force at packer 1 and packer 2 is shown in Fig. 10.
Figure 10: Force analysis of packer at the first test position
It can be seen from the Fig. 10 that packer 1 and packer 2 are unblocking step by step. When they are completely unblocking, the wellhead load is greatly reduced. The variation of contact force at packer with displacement is shown in Fig. 11.
Figure 11: Force analysis of packer at the third test position
After unblocking the packer 1 and packer 2, the contact force between packer and casing increases significantly, indicating that the axial freedom of the packer has been released.
The force analysis of the packer shows that the packer in the bottom hole has been completely unblocked when the wellhead load changes significantly.
4.4 Analysis of Packer Creep during Water Plugging in Real Drilling Well
The annulus pressures of casing in these sections are P1, P2, and P3, respectively. Packer 1 is 168 m away from the bottom hole, while packer 2 is 37 m. During the water finding test, the sucking action of the oil well pump produces interval differential pressure. Therefore, the force associated with the packer in the wellbore is analyzed to ensure the safety and reliability of the packer in the working process, which is shown in Fig. 12.
Figure 12: The integrated string of the well shanping 8–11
The force associated with the water plugging packer during operation is analyzed. The unblocking force of the packer is 8 tons. The variation of the axial force and displacement of the string with the differential pressure is shown in Fig. 13.
Figure 13: Relationship between axial force and displacement of a string with differential pressure (the setting force is 8 tons)
Fig. 13 shows that when F2 ≤ fmax = 8t (F2 is the axial force of packer,) there is no creep; when the pressure difference is greater than 7 MPa, packer 2 begins to creep; when the differential pressure is 12 MPa, the creep of packer is 0.45 m.
The mechanical analysis of the water plugging packer shows that the packer will eventually creep with the increasing of differential pressure. The string close to the bottom packer mainly occurs creep.
In this paper, the force associated with the water plugging string with the bottom hole packer is studied. Firstly, the finite element model of the whole well string is established based on the beam element. Then the model is verified by the field test data of a real drilling well. According to the established numerical simulation model of the real drilling well and the mechanical characteristics of string and packer in the process of lifting, lowering, unblocking and water plugging, the following conclusions are obtained:
(1) By comparing and analyzing the measured data and simulation data, it is shown that the model of the water plugging string established in this research has high accuracy;
(2) During lifting and lowering, the axial force of the string is distributed nonlinearly along the string, and the axial force in the second build-up section has changed significantly. The contact on the string during the lowering process is obviously more serious in the first build-up section;
(3) The wellhead unblocking load increases with the step-by-step unblocking of the packer. After unblocking the packer, the contact length between the string and the borehole changes so that leads to the friction loss of axial force increase;
(4) The force analysis of water plugging packer shows that the packer will eventually creep with the increasing of differential pressure, and the string close to the bottom packer mainly occurs creep.
Funding Statement: This research received no specific grant from any funding agency in the public, commercial, or not-for-profit sectors.
Conflicts of Interest: The authors declare that they have no conflicts of interest to report regarding the present study.
References
1. Li, W., Nie, H., Cheng, Y., Yang, L. (2007). Integration of mechanical water finding and plugging string. Process String China Petroleum Machinery, 7, 52–54. [Google Scholar]
2. Kong, L. W. (2016). WDP technology without pulling the strings for horizontal wells. Petroleum Geology & Oilfield Development in Daqing, 35(5), 100–103. [Google Scholar]
3. Zhu, H., Lv, Y. M., Wang, B., Guo, J., Chang, L. (2017). Integrated technique for hydrophobic-lipophilic water finding and plugging. Petroleum Geology & Oilfield Development in Daqing, 36(1), 90. [Google Scholar]
4. Lin, W. (2016). Simulated study on workover string dynamics in workover operations of highly-deviated well (Mater Thesis). Southwest Petroleum University, China. [Google Scholar]
5. Lin, W., Dong, Z. Z., Zhang, L. M., Zhang, J. Z., Wang, H. J. (2017). Simulation study on affect factors of workover string buckling in horizontal well. Journal of Mechanical Strength, 39(5), 1245–1250. [Google Scholar]
6. Liu, Z. (1988). New progress of packer separate-layer water plugging technique. Oil Drilling & Production Technology, 1, 48. [Google Scholar]
7. Cui, F. (2000). Application of mechanical water finding and plugging one trip string operation in well S6 of Shanshan oilfield. Oil Drilling & Production Technology, 1, 86–88. [Google Scholar]
8. Huang, Z., Wang, H., Ma, Z., Bao, R., Liu, Y. et al. (2019). Study on dynamic mechanical analysis and creep law of multi-stage segmental subdivision water injection pipe string. Journal of China University of Petroleum (Edition of Natural Science), 43(6), 144–150. [Google Scholar]
9. Zhao, X. W., Wang, B. A., Zhu, H. Z. (2013). Analysis of the packer reopened force in the horizontal segment. Oil Field Equipment, 42(7), 35–38. [Google Scholar]
10. Lubinski, A. (1950). A study of the buckling of rotary drilling strings. In: Drilling & production practice. OnePetro. [Google Scholar]
11. Mitchell, R. F. (2003). Lateral buckling of pipe with connectors in curved wellbores. SPE/IADC Drilling Conference, OnePetro. [Google Scholar]
12. Mitchell, R. F. (2002). New buckling solutions for extended reach wells. Society of Petroleum Engineers. [Google Scholar]
13. Mitchell, R. (2003). The twist and shear of helically buckled pipe. SPE/IADC Drilling Conference. [Google Scholar]
14. Daily, J. S., Ring, L., Hajianmaleki, M., Gandikota, R. A. (2013). Critical buckling load assessment of drill strings in different wellbores using the explicit finite element method. SPE Offshore Europe Oil and Gas Conference and Exhibition. [Google Scholar]
15. Jaculli, M. A., Mendes, J. R. P., Miura, K. (2017). Dynamic buckling with friction inside directional wells. Journal of Petroleum Science & Engineering, 153, 145–156. DOI 10.1016/j.petrol.2017.03.040. [Google Scholar] [CrossRef]
16. Walker, B. H., Friedman, M. B. (1977). Three-dimensional force and deflection analysis of a variable cross section drill string. Journal of Pressure Vessel Technology, 99(2), 367–373. DOI 10.1115/1.3454543. [Google Scholar] [CrossRef]
17. Kyllingstad, A. (1995). Buckling of tubular strings in curved wells. Journal of Petroleum Science & Engineering, 12(3), 209–218. DOI 10.1016/0920-4105(94)00046-7. [Google Scholar] [CrossRef]
18. Wang, B., Lv, Y., Gan, Q., Li, D., Zhu, H. et al. (2014). Mechanical water plugging technology of the horizontal wells in changqing low-permeability oilfield. Petroleum Geology & Oilfield Development in Daqing, 1, 111–115. DOI 10.3969/J.ISSN.1000. [Google Scholar] [CrossRef]
19. Mu, L., Zhu, H., Lv, Y., Bai, W., Li, D. et al. (2014). Design and application of water detecting and plugging pipe string for low production horizontal wells. Petroleum Drilling Techniques, 42(1), 91–94. DOI 10.3969/j.issn.1001-0890.2014.01.018. [Google Scholar] [CrossRef]
20. Kuang, Y., Lin, W., Liu, Y., Wang, Q., Zhang, J. (2019). Numerical modelling and field experimental validation of the axial load transfer on the drill-strings in deviated wells. Journal of Natural Gas Science and Engineering, 75, 103124. DOI 10.1016/j.jngse.2019.103124. [Google Scholar] [CrossRef]
Cite This Article
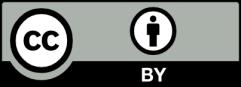
This work is licensed under a Creative Commons Attribution 4.0 International License , which permits unrestricted use, distribution, and reproduction in any medium, provided the original work is properly cited.