Open Access
ARTICLE
On the Combination of Silica Fume and Ceramic Waste for the Sustainable Production of Mortar
1 Civil Engineering Department, Faculty of Technology, M’sila University, M’sila, 28000, Algeria
2 Institute of Technical Urban Management, M’sila University, M’sila, 28000, Algeria
* Corresponding Author: Zine El Abidine Rahmouni. Email:
(This article belongs to the Special Issue: Materials and Energy an Updated Image for 2021)
Fluid Dynamics & Materials Processing 2023, 19(5), 1083-1090. https://doi.org/10.32604/fdmp.2022.021970
Received 23 February 2022; Accepted 24 June 2022; Issue published 30 November 2022
Abstract
The combined use of silica fume (SF) and ceramic waste (CW) for the production of mortar is studied. Sand is replaced by 5%, 10%, 15% and 20% of CW while a fixed 5% percentage (% wt of cement) of SF is used. The results show that the best results are obtained by using silica fume and ceramic waste sand with 15% weight of sand and 5% wt of cement. With the addition of sand ceramic waste (SCW), the mortar compressive strength and density increase, while the porosity displays an opposite trend. The experimental analysis is complemented with theoretical considerations on the matrix strength and related improvements in mechanical behavior. It is shown that the agreement between the experimental values and the estimated values is good.Graphic Abstract
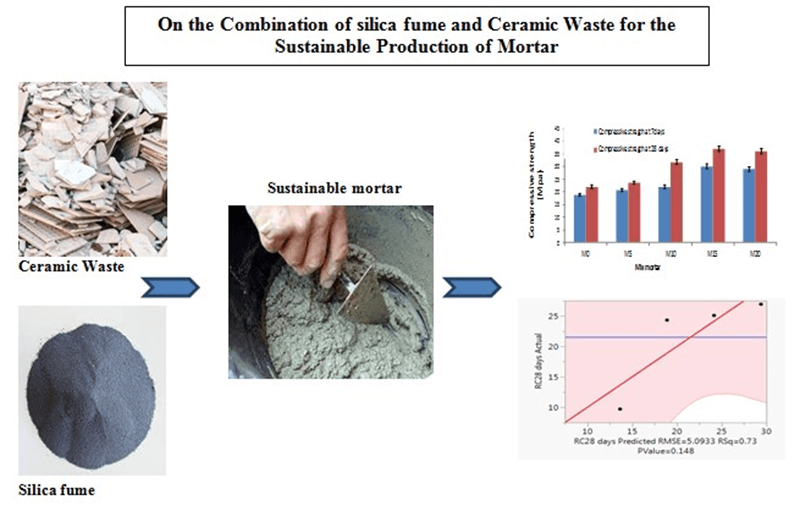
Keywords
The big topic of importance today in cement and concrete technology is the recycling and reuse of industrial waste and by-products, like ceramic and brick wastes [1]. Some recent studies have proven that the use of the remnants of inorganic industrial produces in the production of concrete can make sustainable ceramics industry range from 3% to 7% of daily production [2]. Therefore, recycling it allows it to be used in the construction of many different buildings [3]. After recycling this waste, it was considered to be coarser than the cement particles, which is usually as fine and coarse aggregate in the concrete mixture, up to 35% of tile waste [4].
According to research by Kannan et al. (2017), replacing part of the cement with micro-ceramic powder led to the good improvement of the outstanding mechanical properties of high-performance concrete [5]. MCP has been classified as a material rich in aluminum silicate which indicates significant activity of pozzolanic [5]. The (C-S-H) and (C-AS-H), as the two major strength transfer phases in Portland cement (PC), formed as a result of the consumption of Ca(OH)2 by the reaction of aluminosilicates inside ceramic waste [6].
Cement consumes a large proportion of carbon dioxide is emitted into the atmosphere during its production, which causes many environmental problems [7]. The silica fume (SF) is one of the cementitious additions (SCMs) used due to its improvement concrete/mortar properties [8].
Shubbar et al. [9] showed that SF can considerably growth the hydration level of the paste and the compressive strengths of hardened pastes, mortars and concretes. This improvement in strength comes from bonding the interface between the hardened cement paste and the aggregate. It is evident that the degree of crystal orientation, crystal size and calcium hydroxide content at the interface were decreased by the addition of SF.
Zhang et al. [10] studied the effect of replacing aggregates with ceramic tiles on the properties of concrete. The results indicated that the mechanical strength was improved with replacement of 25%–50% sand and 10%–20% coarse aggregate. Most of the research carried out in such studies used the waste in the form of a powder, and the results were different in terms of their impact on the different properties of mortar and concrete [11].
In this study, the impacts of ceramic wastes used as sand on the properties of mortar were investigated. The combination of SF and CW and their effects as sand aggregates in a sustainable mortar were examined.
The Portland cement (C) type CEM II/A 42.5 was used, with 3.1 g/cm3 values of absolute density, 28% consistency and fineness of 4000 cm2/g, respectively.
The silica fume (SF) is obtained from GRANITEX (Algeria region) with specific surface >15 m2/gr. The properties of cement are shown in Table 1.
The dune sand (DS) used with particles ranging from 0.08 to 5 mm in size and fineness modulus Mf of 2.44. Granular analysis was carried out NF EN 933-1 [12].
Ceramic waste aggregates (CW): floor and wall ceramics were the material used in this study (obtained from construction and demolitions sites). It was added as aggregates witha grain size of 0.08 to 5 mm .The granulometric distribution of SF and CW used are shown in Figs. 1 and 2.
Figure 1: Particle size distribution of SF
Figure 2: Granular analysis of DS and the CW
The admixture used in the preparation of our concrete to ensure satisfactory processing fluidity is the super plasticizer “Medaplast SP40” belonging to the family of superplasticizers/high water reducers. It density equal to 1.22.
2.2 Preparation of Mortar Samples
Four mixtures were produced: a reference mortar (M0) formulated and three mortars containing 5%, 10%, 15% and 20% respectively of CW by weight. These mixtures took the following names (M5, M10, M15 and M20).
The prisms (4 × 4 × 16) cm3 of mortars were prepared according to EN 196-1 [13]. The final compositions of mortars are presented on Table 2.
Porosity test: the protocol of porosity accessible to water conform the recommendations of AFREM group [14,15].
Based on standard NF EN 196-1, the fresh mortars density was evaluated [13]. From the Fig. 3, it was found that the fresh density increased with increasing of CW content. The elevation in fresh density can be explained by the fact of silica fume and cement density, which contributed to the increase in the density of the mortar. On the other hand, incorporating CW led to an increase in mortar density due to the fact that the density of the SCW used was considerably higher than that of the DS. For example, the fresh density of the M0 was 527 g/cm3, whereas this value for M15 was 540 g/cm3.
Figure 3: Density of different mortar formulated
As explained in the Fig. 4, the compressive strength increased as the % of SCW increased in mortar until 15% SCW, after this % the compressive strength decreased as the % of CW increased in mortar. Whereas, 15% SWC expressed an improvement in the properties of the mortars, which confirms other research [16].
Figure 4: Variation of mortar compressive strength as a function of different percentage of CW at 7 days and 28 days
After 15% we notice a drop in compression (M20), this decrease explained by the development of C-S-H gel influenced by the elements in CW [17,18]. As for the increase in the bonding between the aggregate and the cement paste, it is due primarily to the angular shape and the rough surface of CW. The rough surface of CW provided a physical anchor while its higher porosity compared to DS increased anchoring between hydrated products and the aggregate (chemical anchoring).
3.3 Effect of Binary Combination of SF and CW
The best result for compressive strength was appeared in 28 days with SF and without SCW is illustrated in Fig. 4.
The compressive increased as the content of SF combined with CW in the mixture. The range of compressive strength at 7th day was between 19 and 30 MPa, while at 28th day was between 22 and 37 MPa. The presence of 25% SF in the mixture explained by the improvement of the resistance. It presents a pozzolanic reaction with clinker hydration products to form dense C-S-H [19].
3.4 Effect of Porosity of Binary Sand on the Mechanical Strength
Fig. 5 indicated that increasing of porosity of SCW influences significantly the compressive of mortar tested but such decreasing was found limited, principally for mortar prepared with binary sand.
Figure 5: Porosity and compressive strength of mortars as a function of different percentage of CW
In general, the reducing of porosity binary sand results in increasing the compressive of mortar. It is noted that the texture of the sand as well as its porosity have an effect on the resistance of the hardened mortar. From the sample incorporation with different % SCW replacement has minor % of porosity of the mixtures M5, M10, M15 and M20 compared with the reference mortar. This is due to the lower volume of voids inside the binary sand.
3.5 Modeling the Compressive Strength
When plotting the observed values of the quadratic model as a function of the predicted values (that is, the relationship between the predicted area and the actual area measured, it is found that the points are placed above the first arithmetic that is desirable (Fig. 6).
Figure 6: (1a, 1b) Graphs of the values observed according to the expected values (compressive strength at 7 days and 28 days)
The evolution of the compressive strengths as a function of the dosages of ceramic waste has been presented in Fig. 7. It can clearly be stated that the dosage of the ceramic strongly influences the compressive strength. A rise in compressive strength has been observed with the increase in dosage up to 15% beyond 15% of ceramic resistance considerably reduced.
Figure 7: Evolution of compression strength at 7 days and 28 days (2a, 2b)
According to the results of estimate of coefficients drawn: the dosage of ceramic effect is larger than the effect of the percentage interaction of E/L. To simplify the model, we will eliminate this term from the equation. Therefore the compressive strength response can be summarized in the following empirical model:
• Compressive strength at 7 days = 19.1475 + 1.5435 [ceramic-7.5]/7.5
• Compressive strength at 28 days = 21.5225−7.8645 [ceramic-7.5]/7.5
From the above experimental results, the following conclusions are drawn:
• The substitution of C with 5% to 15% CWS leads to increase in compressive strength beyond 15% a drop in resistance has been noticed;
• The addition of SF with CWS increase density of mortar;
• The porosity of mortar decreased with an increase of ceramic sand;
• The possibility of using the CW residue as an effective compound in the mortar at rates not exceeding 15% of sand;
• The improvements in mechanical behavior allow a good agreement between the experimental values and the estimated values.
Acknowledgement: The authors thank the Geo-Materials Development Laboratory (M’sila University) and (DGRSDT-MESRS, Algeria) for the assistance and support to complete this paper.
Funding Statement: The authors received no specific funding for this study.
Conflicts of Interest: The authors declare that they have no conflicts of interest to report regarding the present study.
References
1. Puertas, F., Blanco-Varela, M. T., Vazquez, T. (1999). Behaviour of cement mortars containing an industrial waste from aluminium refining: Stability in Ca(OH)2 solutions. Cement and Concrete Research, 29(10), 1673–1680. DOI 10.1016/S0008-8846(99)00157-X. [Google Scholar] [CrossRef]
2. Fernandes, M., Sousa, A., Dias, A. (2004). Environmental impact and emissions trade. In: Ceramic industry. A case study. Portuguese Association of Ceramic Industry APICER. [Google Scholar]
3. Medina, C., de Rojas, M. S., Frías, M. (2012). Reuse of sanitary ceramic wastes as coarse aggregate in eco-efficient concretes. Cement and Concrete Composites, 34(1), 48–54. DOI 10.1016/j.cemconcomp.2011.08.015. [Google Scholar] [CrossRef]
4. Senthamarai, R. M., Manoharan, P. D. (2005). Concrete with ceramic waste aggregate. Cement and Concrete Composites, 27(9–10), 910–913. DOI 10.1016/j.cemconcomp.2005.04.003. [Google Scholar] [CrossRef]
5. NF EN 196-1. Méthodes d’essais des ciments-Partie 1: Détermination des résistances mécaniques (2016). [Google Scholar]
6. Kannan, D. M., Aboubakr, S. H., El-Dieb, A. S., Taha, M. M. R. (2017). High performance concrete incorporating ceramic waste powder as large partial replacement of portland cement. Construction and Building Materials, 144, 35–41. DOI 10.1016/j.conbuildmat.2017.03.115. [Google Scholar] [CrossRef]
7. Pacheco-Torgal, F., Jalali, S. (2010). Reusing ceramic wastes in concrete. Construction and Building Materials, 24(5), 832–838. DOI 10.1016/j.conbuildmat.2009.10.023. [Google Scholar] [CrossRef]
8. Grmasha, R. A., Al-sareji, O. J., Salman, J. M., Hashim, K. S. (2020). Polycyclic aromatic hydrocarbons (PAHs) in urban street dust within three land-uses of Babylon governorate, Iraq: Distribution, sources, and health risk assessment. Journal of King Saud University-Engineering Sciences, 34(4), 231–239. [Google Scholar]
9. Shubbar, A. A. F., Sadique, M. M., Nasr, M. S., Al-Khafaji, Z. S., Hashim, K. S. (2020). The impact of grinding time on properties of cement mortar incorporated high volume waste paper sludge ash. Karbala International Journal of Modern Science, 6(4), 394–403. DOI 10.33640/2405-609X.2149. [Google Scholar] [CrossRef]
10. Zhang, Z., Zhang, B., Yan, P. (2016). Comparative study of effect of raw and densified silica fume in the paste, mortar and concrete. Construction and Building Materials, 105, 82–93. DOI 10.1016/j.conbuildmat.2015.12.045. [Google Scholar] [CrossRef]
11. Tavakoli, D., Heidari, A., Karimian, M. (2013). Properties of concretes produced with waste ceramic tile aggregate. Asian Journal of Civil Engineering, 14(3), 369–382. [Google Scholar]
12. Kubba, H. Z., Nasr, M. S., Al-Abdaly, N. M., Dhahir, M. K., Najim, W. N. (2020). Influence of incinerated and non-incinerated waste paper on properties of cement mortar. IOP Conference Series: Materials Science and Engineering, vol. 671, no. 1, 012113. Kerbala, Iraq, IOP Publishing. [Google Scholar]
13. NF EN 933-1: Essais pour déterminer les caractéristiques géométriques des granulats–Partie 1: Détermination de la granularité–Analyse granulométrique par tamisage (2016). [Google Scholar]
14. EN 196-1:2018. Methods of testing cement–Part 1: Determination of strength (2016). [Google Scholar]
15. AFPC-AFREM (1998). Groupe de travail durabilité des bétons. Recommended test methods for measur-ing the parameters associated to durability. Proceedings des Journées Techniques AFPC-AFREM : Durabilité des Bétons, Toulouse, France. [Google Scholar]
16. Lasseuguette, E., Burns, S., Simmons, D., Francis, E., Chai, H. K. et al. (2019). Chemical, microstructural and mechanical properties of ceramic waste blended cementitious systems. Journal of Cleaner Production, 211, 1228–1238. DOI 10.1016/j.jclepro.2018.11.240. [Google Scholar] [CrossRef]
17. Heidari, A., Tavakoli, D. (2013). A study of the mechanical properties of ground ceramic powder concrete incorporating nano-SiO2 particles. Construction and Building Materials, 38, 255–264. DOI 10.1016/j.conbuildmat.2012.07.110. [Google Scholar] [CrossRef]
18. Tebbal, N., Rahmouni, Z. E. A. (2019). Recycling of brick waste for geopolymer mortar using full factorial design approach. The Eurasia Proceedings of Science Technology Engineering and Mathematics, 7, 44–47. [Google Scholar]
19. Tawfik, T. A., Abd EL-Aziz, M. A., Abd El-Aleem, S., Serag Faried, A. (2018). Influence of nanoparticles on mechanical and nondestructive properties of high-performance concrete. Journal of the Chinese Advanced Materials Society, 6(4), 409–433. DOI 10.1080/22243682.2018.1489303. [Google Scholar] [CrossRef]
Cite This Article
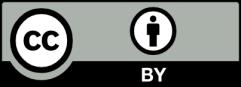
This work is licensed under a Creative Commons Attribution 4.0 International License , which permits unrestricted use, distribution, and reproduction in any medium, provided the original work is properly cited.