Open Access
ARTICLE
Exergy Analysis of Organic Rankine Cycles with Zeotropic Working Fluids
Department of Engineering DI, Università della Campania “Luigi Vanvitelli” Aversa (CE), Caserta, 81031, Italy
* Corresponding Author: Biagio Morrone. Email:
(This article belongs to the Special Issue: Materials and Energy an Updated Image for 2021)
Fluid Dynamics & Materials Processing 2023, 19(3), 593-601. https://doi.org/10.32604/fdmp.2022.022524
Received 14 March 2022; Accepted 28 March 2022; Issue published 29 September 2022
Abstract
Waste heat recovery is one of the possible solutions to improve the efficiency of internal combustion engines. Instead of wasting the exhaust stream of an energy conversion system into the environment, its residual energy content can be usefully recovered, for example in Organic Rankine Cycles (ORC). This technology has been largely consolidated in stationary power plants but not yet for mobile applications, such as road transport, due to the limitations in the layout and to the constraints on the size and weight of the ORC system. An ORC system installed on the exhaust line of a bus powered by a natural gas spark ignition engine has been investigated. The thermal power available at engine exhaust has been evaluated by measuring gas temperature and mass flow rate during real driving operation. The waste thermal power has been considered as heat input for the ORC plant simulation. A detailed heat exchanger model has been developed because it is a crucial component for the ORC performance. The exergy analysis of the ORC was performed comparing different working fluids: R601, R1233zd(E) and two zeotropic blends of the two organic pure fluids. The model allowed the evaluation of the ORC produced energy over the driving cycle and the potential benefit on the engine efficiency.Graphic Abstract
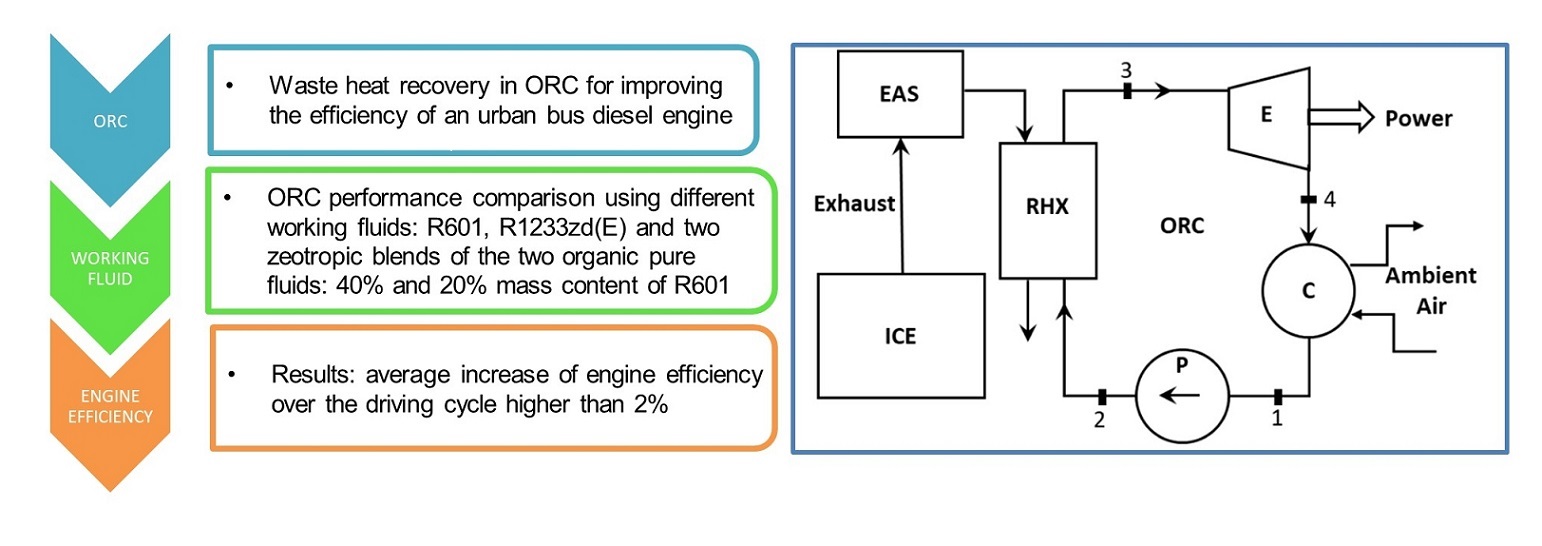
Keywords
Nomenclature
Symbol | Quantity SI unit |
CAC | Charge air cooling − |
EAS | Exhaust aftertreatment − |
GWP | Global warming potential − |
mfr | Mass flow rate kg/h |
n | Engine speed rpm |
ODP | Ozone depletion potential − |
ORC | Organic Rankine Cycle − |
P | Power kW |
pmax | Maximum ORC pressure bar |
RHX | Recovery heat exchanger − |
Teng | Engine torque Nm |
Tex | Exhaust temperature K |
UA | Overall conductance W/K |
v | Vehicle speed km/h |
η | Engine efficiency % |
τ | Percent residence time % |
τ’ | Normalized residence time % |
The exhaust streams of energy conversion systems are at temperatures higher than the ambient one. Exploiting the residual energy and exergy contents of the exhaust stream would maximize the efficiency of energy conversion systems, with consequent reduction of greenhouse gases and pollutant emissions [1]. Transport is responsible for 33% of primary energy consumption in the European Union, mainly coming from oil [2], with negative effects on air quality and human health, particularly in urban areas. Internal combustion engine efficiency can attain a maximum value of around 40%, but the values are usually lower in real operating conditions as the engine often operates at part load [3,4]. The heat wasted by the exhaust gases is about 34%–45% of the chemical fuel energy for spark ignition (SI) engines and 22%–35% for diesel engines. Organic Rankine Cycles (ORC) could recover this heat for additional power generation: the pressurized working fluid evaporates into a recovery heat exchanger, expands producing mechanical power and then it is condensed, returning to the initial conditions. ORC plants are a well-established solution but their use in road vehicles is still difficult due to installation problems. Considering the stringent regulations in the automobile industry, ensuring the safety of equipment is crucial. Size and mass constraints, very rigorous for cars, are less severe for marine propulsion [5], buses and trucks [6]. To reduce ORC cost, weight and size and to improve efficiency and reliability, the system design should be optimized [7–10]. The integration of an ORC plant on the exhaust pipe increases the complexity and weight of the system, causing additional backpressure, and consequently a performance deterioration. The selection of the working fluid has important effects on cycle efficiency, system safety and environmental impact [11]. Working fluids are classified according to the slope of the saturation curve in the Temperature-Entropy diagram, with dry and isentropic fluids expanding with no condensation [12]. Working fluids are classified in accordance with the National Fire Protection Association (NFPA) 704 Standard [13] and by a global warming potential index (GWP) [14]. Energy can be recovered in internal combustion engines from distinct heat sources at different temperatures [15]. Usually alcohols (e.g., ethanol, methanol), water steam and hydrocarbons are well suited to recover waste heat from exhaust gases, even though some fluids show flammability issues. Refrigerant fluids are generally more convenient for low temperature heat, such as coolant and CAC. Hot exhaust gas has significant changes in temperature in the heat exchanger with large exergy destruction because of the finite temperature difference between hot and cold fluids. The use of mixtures as ORC working fluid in place of pure fluids makes variable temperature heat transfer possible, diminishing the temperature difference between hot and cold streams, which consequently reduces the exergy destruction [16]. However, the selection process to choose the mixture components and their concentrations is very complicated, requiring research to adopt such solutions [17]. ORC systems also require a convenient control strategy: the superheating at the evaporator outlet must be controlled by adjusting the pump speed and the expander energy output monitored by regulating the mass flow rate at the expander inlet to stabilize the operation during transients [18]. This study deals with the performance evaluation of an ORC system bottoming a spark ignition natural gas engine installed on a bus, using experimental data acquired during road tests. Aim of the paper is to estimate the mechanical power recovered by the ORC system and the consequent increase in engine efficiency. For this purpose, a detailed heat exchanger model has been developed. The exergy efficiency using different working fluids has been compared.
The ORC system integration with the engine is represented in Fig. 1: energy is recovered from the exhaust gas into a recovery heat exchanger (RHX) specifically designed for this purpose. There is no regeneration and low-temperature heat sources were not exploited, preferring a simple system layout. Table 1 shows engine characteristics. Engine torque and speed, exhaust flow rate and temperature have been measured over the road test by the engine control unit (ECU) at a frequency of 1 Hz; vehicle speed profile is represented in Fig. 2. The RHX is crossflow type, composed of two units in series of length L1 and L2, as sketched in Fig. 3. The fluid attains the saturated liquid condition in the first unit and leaves the second one as dry saturated vapour. The RHX design has been performed considering the engine operating condition of point 6 in Table 2.
Figure 1: Sketch of the integrated ORC-ICE system for exhaust energy recovery
Figure 2: Vehicle speed vs. time over the entire driving cycle
Figure 3: Sketch of the RHX
A limited number of exhaust flow rate and temperature conditions have been chosen as input for the ORC model by considering a 10-point grid on the engine torque-speed plane in Table 2. The reduction of the real engine operating conditions to a limited number of grid nodes in the engine torque-speed plane is performed assigning each operating condition to the adjacent grid nodes. Residence time is inversely proportional to the distance between actual operating points and grid nodes. Engine work in the operating point is imposed equal to the sum of work in the adjacent grid points [19]. The effects of load transient on fuel consumption have been neglected. In the present study, the tested ORC working fluids are n-pentane (R601), trans-1-chloro-3,3,3-trifluoroprop-1-ene (R1233zd(E)), and two zeotropic mixtures of the previous fluids. The adoption of zeotropic fluids allows a reduction of the thermodynamic irreversibility, with a consequent increase of the exergy efficiency [6,16]. R601 is a hydrocarbon with excellent thermodynamic properties but with a high flammability index. It shows a low health hazard, with no chemical instability; it does not have Ozone Depletion Potential while the GWP 100 is 5 [6,20]. R1233zd(E) is a hydrofluoroolefin (HFO). HFOs have been developed for replacing flammable fluids with high ODP and GWP in refrigerant applications. Both R601 and R1233zd(E) belong to the dry fluid class in Table 3.
The ORC performance over the road test is evaluated considering the heat recovered from the exhaust gases of the internal combustion engine in operating conditions corresponding to the grid nodes listed in Table 4, in which the ORC is active for energy recovery. The table shows the residence time spent by the engine at each operating condition over the driving cycle. The normalized residence times (τ’) are used for calculating the average ORC delivered power, calculated by Eq. (1). The available heat in the exhaust gases is dependent on engine operating conditions: exhaust flow rate and temperature increase with engine load and speed, therefore the ORC power is higher.
Fig. 4 shows the effect of the maximum cycle pressure on the ORC power, in the range 10–30 bar, for all the working fluids. The power produced by the Rankine cycle is higher when using R601 as working fluid, at all operating conditions. The ORC power increases with the maximum cycle pressure for all the fluids due to the resulting increase of the average temperature of heat adduction. The cycle thermodynamic efficiency improves consequently, see Fig. 5.
Figure 4: ORC power vs. maximum cycle pressure, for the evaluated working fluids
Figure 5: ORC thermodynamic efficiency vs. maximum cycle pressure, for the evaluated working fluids
For maximum cycle pressure close to the critical pressure value, superheating is required for avoiding condensation during the expansion. This constraint is unnecessary in case a volumetric expander is adopted. The performance for the two zeotropic mixtures is similar and close to the performance of R1233zd(E), which is always the main constituent of the fluids. The zeotropic mixture with higher n-pentane mass content shows slightly better performance. A maximum ORC power of 2 kW can be produced using R601, and 1.65 kW with the mixture 60% R1233zd(E)-40% R601. The corresponding thermodynamic efficiencies are 14.5% and 13.4%, respectively. The exergy efficiency, defined as:
reproduces the trend of the cycle thermodynamic efficiency, see Fig. 6, with values higher than ηORC for all the working fluids, since its maximum theoretical value is 1.
Figure 6: ORC exergy efficiency as a function of the maximum cycle pressure, for all the working fluids
The ORC power produces an increase of the overall internal combustion engine efficiency, according to the following equation:
It was assumed that the engine operated at steady state conditions at the grid node’s points, neglecting the effect of transients on engine and ORC performance. Although the increase in engine efficiency is below 2% at the maximum pressure of 30 bar with the zeotropic mixture 60% R1233zd(E) and 40% R601, the available ORC power can still be exploited for supplying energy to auxiliary devices, see Fig. 7.
Figure 7: Variation of engine efficiency due to the recovered ORC power, as a function of the maximum cycle pressure, for all the working fluids
A numerical investigation has been presented for an Organic Rankine Cycle bottoming an internal combustion engine to estimate the recoverable mechanical power and the resulting engine efficiency increase. Data for exhaust mass flow rate and temperature have been obtained from experimental tests. Results have been achieved considering two pure fluids, R601 and R1233zd, and their zeotropic mixtures. The best performance is attained using pure R601, but the fluid shows a very high flammability index. Thus, its zeotropic mixtures with 40% and 20% mass content of R601 show worse thermodynamic performance, but are still comparable with the pure R601, reducing the flammability risk. In fact, the recoverable ORC power ranges between 1 and 2 kW. The exergy efficiency has been estimated between 15% and 25%, showing a large recovery of the exhaust energy stream.
Funding Statement: The authors gratefully acknowledge Università degli studi della Campania “L. Vanvitelli” for funding the research project CHIMERA with V:ALERE 2019 grant.
Conflicts of Interest: The authors declare that they have no conflicts of interest to report regarding the present study.
References
1. United Nations (1998). Kyoto protocol to the united nations framework convention on climate change. https://unfccc.int/resource/docs/convkp/kpeng.pdf. [Google Scholar]
2. He, C., Liu, C., Gao, H., Xie, H., Li, Y. et al. (2012). The optimal evaporation temperature and working fluids for subcritical organic Rankine cycle. Energy, 38(1), 136–143. DOI 10.1016/j.energy.2011.12.022. [Google Scholar] [CrossRef]
3. Heywood, J. (1989). Internal combustion engine fundamentals. New York: Mc Graw-Hill. [Google Scholar]
4. Stuhldreher, M., Kargul, J., Barba, D., McDonald, J., Bohac, S. et al. (2018). Benchmarking a 2016 honda civic 1.5-Liter L15B7 turbocharged engine and evaluating the future efficiency potential of turbocharged engines. SAE International Journal of Engines, 11(6), 1273–1305. DOI 10.4271/2018-01-0319. [Google Scholar] [CrossRef]
5. Lion, S., Michos, C. N., Vlaskos, I., Rouaud, C., Taccani, R. (2017). A review of waste heat recovery and Organic Rankine Cycles (ORC) in on-off highway vehicle Heavy Duty Diesel Engine applications. Renewable and Sustainable Energy Reviews, 79, 691–708. DOI 10.1016/j.rser.2017.05.082. [Google Scholar] [CrossRef]
6. Lion, S., Michos, C. N., Vlaskos, I., Taccani, R. (2017). A thermodynamic feasibility study of an Organic Rankine Cycle (ORC) for heavy-duty diesel engine waste heat recovery in off-highway applications. International Journal of Energy and Environmental Engineering, 8(2), 81–98. DOI 10.1007/s40095-017-0234-8. [Google Scholar] [CrossRef]
7. Xu, B., Rathod, D., Yebi, A., Filipi, Z. (2020). A comparative analysis of real-time power optimization for organic Rankine cycle waste heat recovery systems. Applied Thermal Engineering, 164, 114442. DOI 10.1016/j.applthermaleng.2019.114442. [Google Scholar] [CrossRef]
8. Nazari, N., Heidarnejad, P., Porkhial, S. (2016). Multi-objective optimization of a combined steam-organic Rankine cycle based on exergy and exergo-economic analysis for waste heat recovery application. Energy Conversion and Management, 127, 366–379. DOI 10.1016/j.enconman.2016.09.022. [Google Scholar] [CrossRef]
9. Valencia, G., Fontalvo, A., Cárdenas, Y., Duarte, J., Isaza, C. (2019). Energy and exergy analysis of different exhaust waste heat recovery systems for natural gas engine based on ORC. Energies, 12(12), 2378. DOI 10.3390/en12122378. [Google Scholar] [CrossRef]
10. Valencia, G., Fontalvo, A., Forero, D. J. (2021). Optimization of waste heat recovery in internal combustion engine using a dual-loop organic Rankine cycle: Thermo-economic and environmental footprint analysis. Applied Thermal Engineering, 182, 116109. DOI 10.1016/j.applthermaleng.2020.116109. [Google Scholar] [CrossRef]
11. Xu, W., Zhao, L., Mao, S. S., Deng, S. (2020). Towards novel low temperature thermodynamic cycle: A critical review originated from organic Rankine cycle. Applied Energy, 270(9), 115186. DOI 10.1016/j.apenergy.2020.115186. [Google Scholar] [CrossRef]
12. Chen, H., Goswami, D. Y., Stefanakos, E. K. (2010). A review of thermodynamic cycles and working fluids for the conversion of low-grade heat. Renewable and Sustainable Energy Reviews, 14(9), 3059–3067. DOI 10.1016/j.rser.2010.07.006. [Google Scholar] [CrossRef]
13. NFPA (2022). Codes & standards. https://www.nfpa.org/. [Google Scholar]
14. EPA Greenhouse Gas Emissions. https://www.epa.gov/ghgemissions/understanding-global-warming-potentials. [Google Scholar]
15. Hountalas, D. T., Mavropoulos, G. C., Katsanos, C., Knecht, W. (2012). Improvement of bottoming cycle efficiency and heat rejection for HD truck applications by utilization of EGR and CAC heat. Energy Conversion and Management, 53(1), 19–32. DOI 10.1016/j.enconman.2011.08.002. [Google Scholar] [CrossRef]
16. Chys, M., van den Broek, M., Vanslambrouck, B., de Paepe, M. (2012). Potential of zeotropic mixtures as working fluids in organic Rankine cycles. Energy, 44(1), 623–632. DOI 10.1016/j.energy.2012.05.030. [Google Scholar] [CrossRef]
17. Scaccabarozzi, R., Tavano, M., Invernizzi, C. M., Martelli, E. (2017). Thermodynamic optimization of heat recovery ORCs for heavy duty internal combustion engine: Pure fluids vs. zeotropic mixtures. Energy Procedia, 129, 168–175. DOI 10.1016/j.egypro.2017.09.099. [Google Scholar] [CrossRef]
18. Enayatollahi, H., Fussey, P., Nguyen, B. K. (2021). Control of Organic Rankine Cycle, a neuro-fuzzy approach. Control Engineering Practice, 109(12), 104728. DOI 10.1016/j.conengprac.2021.104728. [Google Scholar] [CrossRef]
19. Mariani, A., Morrone, B., Unich, A. (2012). Numerical evaluation of internal combustion spark ignition engines performance fuelled with hydrogen–Natural gas blends. International Journal of Hydrogen Energy, 37(3), 2644–2654. DOI 10.1016/j.ijhydene.2011.10.082. [Google Scholar] [CrossRef]
20. ASHRAE (2015). Update on new refrigerants designations and safety classifications. https://www.ashrae.org/technical-resources/standards-and-guidelines/ashrae-refrigerant-designations. [Google Scholar]
Cite This Article
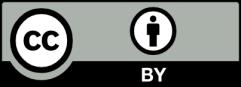
This work is licensed under a Creative Commons Attribution 4.0 International License , which permits unrestricted use, distribution, and reproduction in any medium, provided the original work is properly cited.