Open Access
ARTICLE
Analysis of a Cashew Shell and Fly Ash Rich Brake Liner Composite Material
1 Department of Mechanical Engineering, Saveetha Engineering College, Chennai, Tamilnadu, India
2 Department of Mechatronics, Faculty of Engineering, Tishk International University, Erbil, Iraq
3 Department of Mechanical Engineering, Chouksey Engineering College, Bilaspur, Chhattisgarh
4 Department of Mechanical Engineering, Saveetha School of Engineering, SIMATS, Chennai, India
* Corresponding Authors: R. Selvam. Email: ,
(This article belongs to the Special Issue: Advances in Fluid Dynamics and Functional Materials)
Fluid Dynamics & Materials Processing 2023, 19(3), 569-577. https://doi.org/10.32604/fdmp.2022.022187
Received 12 November 2021; Accepted 12 April 2022; Issue published 29 September 2022
Abstract
Hybrid materials collected from organic and inorganic sources, which are traditionally used as brake lining materials, generally include fly ash, cashew shell powder, phenolic resins, aluminium wool, barites, lime powder, carbon powder and copper powder. The present research focuses on the specific effects produced by fly ash and aims to provide useful indications for the replacement of asbestos due to the health hazards caused by the related fibers. Furthermore, the financial implications related to the use of large-volume use of fly ash, lime stone and cashew shell powder, readily available in most countries in the world, are also discussed. It is shown that many manufacturing and automotive industries, which are currently experiencing difficulties in meeting the increasing demand for brake lining material, may take advantage from the proposed solution.Graphic Abstract
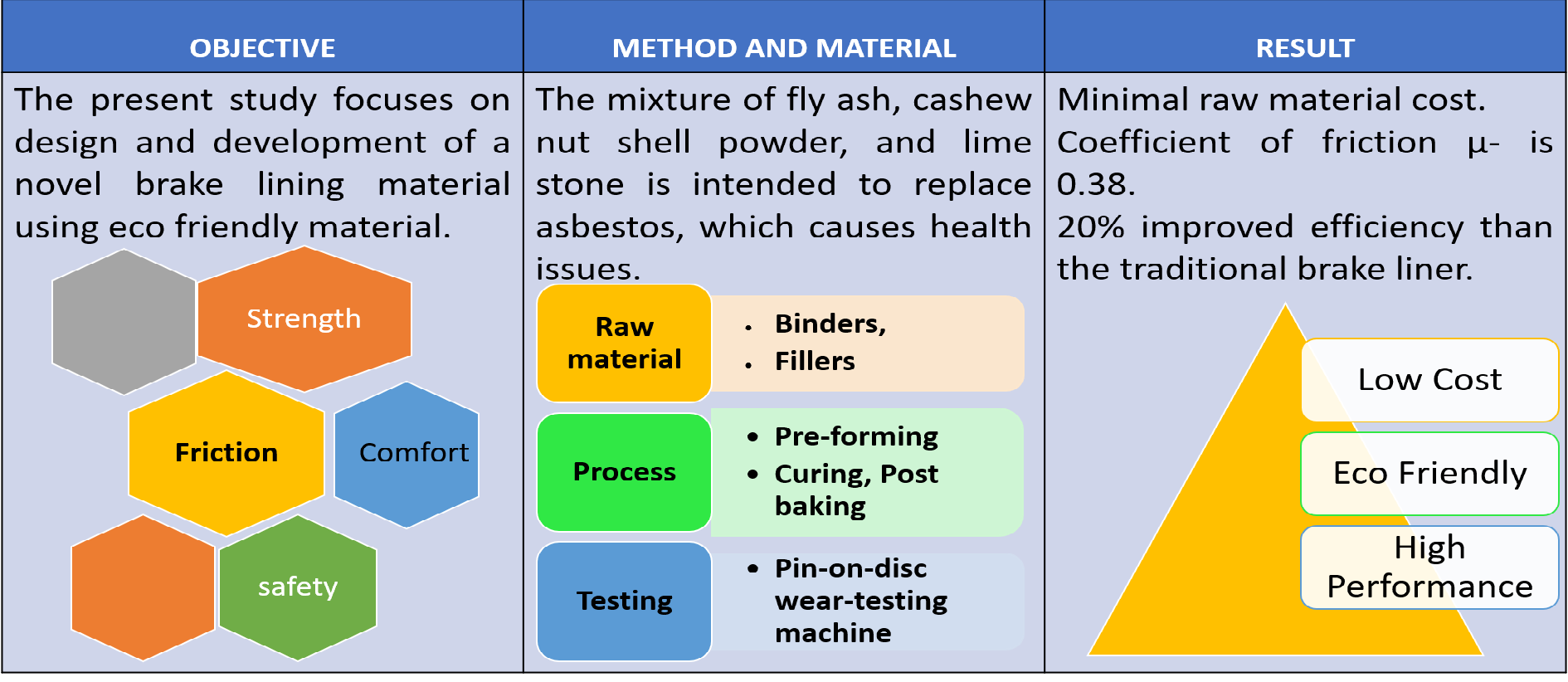
Keywords
A frictional material is designed and developed to control the speed in vehicles by revamping the kinetic energy into warmth, and it is likely to repeat the result under a wide range of temperatures, speeds, and environmental factors. The modern automobile system improves its efficiency as well as its braking geometry. From the liner material and counter shoe, no noise, less wear, and vibration were also noted. Constituent materials were chosen and bound according to individual character requirements. The friction material can be classified according to its characteristics as (i) Binders (ii) Friction modifiers, (iii) Filler, and (iv) Fiber [1].
Many of these materials can serve more than one purpose in these categories, which makes the formulation of new composites more efficient. Although asbestos plays a significant role in brake liners, the government has put a higher tax on its production due to health concerns. The durability and temperature stability of asbestos make it an ideal constituent for friction formulation [2,3].
The present study focuses on the design, development and analysis of a brake lining material using fly ash and cashew shell powder. Composites are reinforced with fly ash to ensure frictional behavior. The mixture of fly ash, cashew nut shell powder, and lime stone is intended to replace asbestos, which causes health issues. Additionally, the production cost of such materials can also be reduced by using large volumes of fly ash readily available in most countries. Thus, the purpose of this project is to develop an improved brake lining frictional material using fly ash [1,2,4].
• To meet the increasing demand for effective brake linings, it is important to develop alternate sources of suppliers for automotive industries.
• Most of the materials used for the brake linings are of high cost and they do not specify the ingredients as these are kept as a trade secret by the suppliers and many of the suppliers have collaborations with foreign firms.
• Low cost and the use of fly ash as a filler material.
• Fly ash is plentifully available [5–7].
2 Hybrid Composite for Brake Lining Requirements
Friction linings have an inexhaustible profile, while safety-relevant aspects merit special attention. In the end, vehicles must be manageable and stoppable under all circumstances, at the same time; there are many requirements in the comfort area that are desirable, but not safety-related. All necessities can be roughly divided into three categories (Table 1).
• Physical/chemical characteristics
• Friction technical behaviour
• Comfort
Society of Automobile Engineering suggests codes and associated friction coefficients as shown in Table 2 [4–6].
3 Selection and Composition of Ingredients
The fundamental materials carefully chosen for this work are primarily used in cars but also have application in commercial vehicles and motorcycles which are given in Table 3. The proportion of material is shown in Tables 3–5.
Pre-forming is the first step in preparing brake liner material. The mixture is generally a combination of dissimilar materials blended together in a specified ratio to produce a new brake liner material. A chemically homogenous material developed by a desired weight/volume with a consistent particle size distribution, color, and texture. In addition to reducing tooling costs and downtime, pre-forming techniques are used to make brake pads.
4.1 Formulation of Non-Asbestos Organic Friction Material Counter Face Material (Disc Material)
One of the most important factors that influences tribological performance is the counter rotor disc. For this study, a grey cast iron rotor disc was used as a counter disc. Therefore, parameters related to it, such as composition, initial surface roughness, microstructure, and hardness, are discussed. Under testing temperature 24.5°C, elements present in the gray cast iron (Tables 6 and 7) with their weight percentage were analyzed by Optical Emission Spectrometry per ASTME 1999–99 (R-04) standard [8–10]. Figs. 1 and 2 give the microstructure of the brake liner.
Figure 1: SEM image of grey cast iron–Couter disc
Figure 2: SEM image of grey cast iron with particle size
Gray cast iron is named for its gray appearance. Gray cast iron contains flake graphite in a matrix of ferrite and pearlite [11–16]. The flake structure is well-defined. SEM image shown in Figs. 1 and 2 indicates uniform spread of particle. The valleys and peek indicate the different sizes of particle.
It is verified that the loading arm movement is free about its horizontal and vertical axis support, and the two pulleys rotate smoothly with an adjustment range of 10–60 mm. Loading pans (1.5 and 2 Kg) are suspended from the wire rope and run over the pulleys. Experiments are conducted in dry conditions without oil. Disc speed is adjusted to 500 rpm, running time is set to 5 min, and the pin is held in its holder refer the Fig. 3. An electronic weighing machine with an accuracy of 10–5 g is used to measure the weight of the pin before and after the experiment. Refer the Tables 8 and 9. Load is added to the iron rope and friction force is initially set to zero in the digital readout system. These two arrangements are important for each experiment.
Figure 3: Testing process in Pin-on-disc testing rig
Friction coefficient is based on friction force and applied load. The direct measurement of efficiency of friction from the pin on disc machine for the duration of 5 min is depicted below for the pin counter to disc material under 1 and 1.5 Kg at wear track radius 15 and 20 mm which is shown in Tables 10 and 11.
The outcomes show that hybrid brake liner material fulfils the necessities of the manufacturing and automotive application. The Hybrid Composite for Brake Lining material formulations with varying fly ash, cashew shell powder and limestone powder content were developed and evaluated. The results of mechanical properties such as elements present in the disc material, hardness, and SEM image captured at different levels of magnification, physical property such as density, carried out showed significant improvement. The tribological evaluation was carried out using Pin-on-disc wear-testing machines (Fig. 3) for brake application, the coefficient of friction was in the range of 0.3 to 0.6 according to its application. In this case, the achieved average value of μ- is 0.38 on associating the varying loads and wear track radius categories and also, the developed composition has 20% improved efficiency than the current brake. Furthermore, the production cost of these developed materials is comparatively less than the commercial friction material.
Acknowledgement: We are very grateful to FDMP Managing Editor, Guest Editor and the reviewers for their suggestions, comments and language editing, which greatly improved the quality of our article.
Funding Statement: This work is self-supported one and not funded by any agency.
Conflicts of Interest: The authors declare that they have no conflicts of interest to report regarding the present study.
References
1. Yu, D. L., Zhu, Z. X., Zhou, J. G., Liao, D. H., Wu, N. X. (2021). On the effect of the rotating chamber reverse speed on the mixing of SiC ceramic particles in a dry granulation process. Fluid Dynamics & Materials Processing, 17(2), 487–500. DOI 10.32604/fdmp.2021.014712. [Google Scholar] [CrossRef]
2. Liu, C. Y., Wu, Y. Y., Gao, Y. Q., Tang, Z. Y. (2021). Experimental and numerical analysis of high-strength concrete beams including steel fibers and large-particle recycled coarse aggregates. Fluid Dynamics & Materials Processing, 17(5), 947–958. DOI 10.32604/fdmp.2021.016283. [Google Scholar] [CrossRef]
3. Ou, Q. R., Ji, P. J., Xiao, J., Wu, L. (2019). A study on the properties of resin transfer molding cyanate ester and its T800 grade carbon fiber composites. Fluid Dynamics & Materials Processing, 15(1), 27–37. DOI 10.32604/fdmp.2019.04787. [Google Scholar] [CrossRef]
4. Unaldi, M., Kus, R. (2017). The effect of the brake pad components to some physical properties of the ecological brake pad samples. IOP Conference Series: Materials Science and Engineering. 2nd International Conference on Mining, Material and Metallurgical Engineering, 191, 012032. Bangkok, Thailand. [Google Scholar]
5. Ungureanu, M., Ungureanu, N. S., Crăciun, I. A. (2017). Study on friction behaviour of brake shoe materials for mining hoist. IOP Conference Series: Materials Science and Engineering, 174, 012016. DOI 10.1088/1757-899X/174/1/012016. [Google Scholar] [CrossRef]
6. Bashir, M., Saleem, S., Bashir, O. (2015). Friction and wear behavior of disc brake Pad material using banana peel powder. International Journal of Research in Engineering and Technology, 4(2), 650–659. DOI 10.15623/ijret.2015.0402091. [Google Scholar] [CrossRef]
7. Kumar, M., Bijwe, J. (2013). Influence of different types of binder in non-asbestos-organic brake lining materials: A case study on inertia brake dynamometer. Journal of Engineering Tribology, 228(5), 584–592. [Google Scholar]
8. Bankar, P. S., Khan, S. N. (2014). A review paper on composite brake friction lining for lining applications on band brake. International Journal of Emerging Engineering Research and Technology, 2(8), 116–122. [Google Scholar]
9. Jaggi, H. S., Satapathy, B. K., Patnaik, A., Mehra, N. C., Tomar, B. S. (2013). Temperature dependence of friction and wear performance and thermomechanical response of fly ash-filled brake composites. Proceedings of the Institution of Mechanical Engineers Part J: Journal of Engineering Tribology, 227(4), 373–384. [Google Scholar]
10. Dow, T. (1985). Friction brakes designing. In: Mechanical design and systems handbook, New York: McGraw-Hill Book Company. [Google Scholar]
11. Dureja, N., Bijwe, J., Gurunath, P. V. (2009). Role of type and amount of resin on performance behavior of non-asbestos organic (NAO) friction materials. Journal of Reinforced Plastic and Composites, 28(4), 489–497. DOI 10.1177/0731684407086588. [Google Scholar] [CrossRef]
12. Yi, G., Yan, F. (2007). Mechanical and tribological properties of phenolic resin-based friction composites filled with several inorganic fillers. Wear, 262(1–2), 121–129. DOI 10.1016/j.wear.2006.04.004. [Google Scholar] [CrossRef]
13. Kim, S. J., Cho, M. H., Bash, R. H., Fash, J. W. (2004). Tribological properties of polymer composites containing barite (BaSO4) or potassium titanate (K2O · 6(TiO2)). Tribology Letters, 17(3), 655–661. DOI 10.1023/B:TRIL.0000044516.75340.25. [Google Scholar] [CrossRef]
14. Fono-Tamo, R. S., Koya, O. A. (2017). Influence of palm karnel shell particle size on fade and recovery behavior of non-asbestos organic friction material. Procedia Manufacturing, 7, 440–451. DOI 10.1016/j.promfg.2016.12.031. [Google Scholar] [CrossRef]
15. Balaji, S., Kalaichelvan, K. (2013). Influence of aramid, cellulose and acrylic fibers in NAO brake pad–effect on thermal stability and frictional characteristics. SAE Technical Paper 2013-26-0081. DOI 10.4271/2013-26-0081. [Google Scholar] [CrossRef]
16. Thiyagarajan, V., Kalaiselvan, V. K. (2013). Influence of steel fiber on thermal stability and thermal conductivity in a semi metallic disc brake pad formulation. Advanced Materials Research, 622–623, 1545–1549. DOI 10.4028/www.scientific.net/AMR.622-623.1545. [Google Scholar] [CrossRef]
Cite This Article
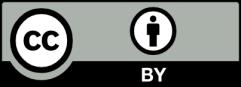
This work is licensed under a Creative Commons Attribution 4.0 International License , which permits unrestricted use, distribution, and reproduction in any medium, provided the original work is properly cited.