Open Access
REVIEW
Numerical Analysis of the Mixed Flow of a Non-Newtonian Fluid over a Stretching Sheet with Thermal Radiation
1 Maritime Department-Marine Engineering, International Maritime College Oman (IMCO), Suhar, 322, Sultanate of Oman
2 Department of Mathematics, Faculty of Science, Benha University, Benha, 13518, Egypt
* Corresponding Author: Nourhan I. Ghoneim. Email:
Fluid Dynamics & Materials Processing 2023, 19(2), 407-419. https://doi.org/10.32604/fdmp.2022.020508
Received 27 November 2021; Accepted 07 March 2022; Issue published 29 August 2022
Abstract
A mathematical model is elaborated for the laminar flow of an Eyring-Powell fluid over a stretching sheet. The considered non-Newtonian fluid has Prandtl number larger than one. The effects of variable fluid properties and heat generation/absorption are also discussed. The balance equations for fluid flow are reduced to a set of ordinary differential equations through a similarity transformation and solved numerically using a Chebyshev spectral scheme. The effect of various parameters on the rate of heat transfer in the thermal boundary regime is investigated, i.e., thermal conductivity, the heat generation/absorption ratio and the mixed convection parameter. Good agreement appears to exist between theoretical predictions and the existing published results.Keywords
List of symbols
| Component of velocity in the x-direction |
| Component of velocity in the y-direction |
| The reference temperature |
| The temperature in the surroundings |
| The characteristics of Powell-Eyring Model |
| The permeability of the porous medium |
| The gravitational acceleration |
| The ambient fluid density |
| The stream function |
| The fluid temperature |
| The heat sources coefficient |
| The radiative heat flux |
| The specific heat at constant pressure |
| The positive dimensional constants |
| The Stefan-Boltzman constant |
| The absorption coefficient |
| The non-dimensional stream function |
| The similarity variable |
| The dimensionless fluid temperature |
| The dimensionless Powell-Eyring fluid parameters |
| The porous parameter |
| The heat generation (absorption) parameter |
| The thermal stratification parameter |
| The Prandtl number |
| The local skin-friction |
| The local Nusselt number |
| The local Reynolds number |
Many neoteric engineering applications require control of both the cooling mechanism and the high-speed transfer of fluid flow, particularly the flow produced by stretching the sheet. Abundant examples can be cited in chemical engineering and particularly in the manufacturing of plastic and rubber sheets, crystal growing, food processing, solidification of liquid crystals, glass blowing, hot rolling, continuous cooling, fiber spinning, exotic lubricants, and several other areas of technology. Many assumptions regarding the nature of fluid flow over a stretching sheet, along with properly chosen boundary conditions, result in accurate and numerical solutions to the conservation equations that describe flow velocity, heat transfer mechanisms, and mass transfer processes [1–6]. While the prediction of cooling phenomena is extremely useful, certain other information such as suction or injection, thermal radiation and heat flux is also valuable [7–10]. A reasonably straightforward correlation between proper physical circumstances and some physical assumptions, in particular, becomes useful in predicting model performance or setting cooling parameters [11–13]. Because of its biological, geological, and engineering applications in purification processes, liquid film evaporation, filtration processes, petroleum industries, and subsurface water resources, the topic of fluid flow within a porous medium has recently gotten a lot of interest. As shown in the diagram, the porous medium can be classified into two types based on its porosity: porous medium with high porosity and porous medium with low porosity (Fig. 1).
Figure 1: (a) Porous medium with low porosity (b) Porous medium with high porosity
The flow and temperature fields are considered over linear and non-linear stretching sheets in all of the preceding investigations. Theoreticians have been less enthusiastic to study the non-Newtonian Powell-Eyring fluid because they believe that this sort of boundary-layer fluid is unsuitable for industrial use. However, they observed that non-Newtonian fluids caused by stretching sheets provide a significant engineering and technological problem because of their widespread engineering and technological applications in a variety of industrial and engineering processes [14–19]. In references [20–38], you can find some additional interesting contributions on Newtonian and non-Newtonian nanofluid flow and its applications in manufacturing.
The fundamental purpose of this research is to look at the heat transfer properties of an Eyring-Powell fluid flow caused by a stretching sheet immersed in a porous media and influenced by thermal radiation. Our focus here is on two fundamental physical phenomena: mixed convection and thermal stratification, both of which have significant effects on cooling rates. The results of the current analysis were obtained after employing the efficient Chebyshev spectral method.
A layer of finite thickness is constrained on one side by a stretched wall in the physical model. This surface is assumed to has a temperature
Figure 2: A schematic representation of the model
In order to be as precise as possible, the number of governing parameters for this physical model is introduced by assuming that there are heat sources with a coefficient
The temperature distribution and energy transfer across the thermal layer can be predicted using the thermal characteristics and boundary conditions. The shear stress relation, which describes the Powell-Eyring model, is [39]:
where
Considering
For the above physical situation, basic equations for mass, momentum and energy after using the appropriate boundary layer approximations are thus:
where
with the band of physical model and application of simplification for
where
in which
For mathematical convenience, viscosity of the fluid
The following rigorous transformation for both the flow and heat transfer fields (3) and (4) could be obtained by using Eqs. (9) and (10) along with the boundary conditions (7) and (8) as follows:
where
Apart from the preceding system that governs our physical problem and allows us to quickly recognize flow features and heat transfer mechanisms, it is very serious to study the following significant physical quantities, the local skin-friction coefficient (
where
To validate the reliability and precision of the numerical process utilized here via the Chebyshev spectral method, calculations for the values of the skin-friction coefficient are done below. The data obtained is compared to Bilal and Ashbar’s previously published findings [43]. From our observations of the tabular data in Table 1, we have found that our results are in good accord.
The preceding considerations and assumptions lead to the current results and discussion section. As a result, while describing the physical problem of hydrodynamics, a system of ordinary differential equations with novel governing parameters emerges, giving us the opportunity to choose which of them is required to develop the suggested model. The Chebyshev spectral approach [44] is appealing because it achieves more precision than other numerical methods for solving the system that regulates our situation. It is also worth noting that all of the results produced utilizing the Chebyshev spectral approach, as well as other associated published results, are mutually supportive. The results of the fully developed velocity and temperature profiles for governing parameter runs in the laminar flow region are plotted in Figs. 3–11. Fig. 3 depicts the numerical result of the present analysis, which offers a close examination of the impact of the porous parameter
Figure 3: (a)
Figure 4: (a)
Figure 5: (a)
Figure 6: (a)
Figure 7: (a)
Figure 8: (a)
Figure 9: (a)
Figure 10: (a)
Figure 11: (a)
Figs. 4a and 4b show how the velocity and temperature fields vary as the
The velocity and temperature profiles in Figs. 5a and 5b indicate the impact of the dimensionless Powell-Eyring parameter
The curves in Figs. 6a and 6b show that for low viscosity parameter
Regarding the mixed convection parameter
Figs. 8a and 8b show the effect of the radiation parameter
Further, a typical steady flow and heat transfer pattern for different values of the thermal conductivity parameter
Figs. 10a and 10b show the variations in velocity
In order to illustrate the effect of the thermal stratification parameter
Now, both the physical quantities
The current investigation’s overall goal is to determine the velocity distribution, temperature distribution, heat transfer rate, and drag properties of Powell-Eyring fluid flow in the boundary layer region. The material presented in this research is limited to the measurement of the flow and heat transfer of the Powell-Eyring fluid with mixed convection and heat generation and the determination of their effect on the cooling mechanism through a porous medium. This data would contribute considerably to the understanding of the mixed-convection heat transfer phenomena. Numerically, a solution to the present physical problem using the Chebyshev spectral method was introduced. The main findings of our study are summarized as follows:
1. It is even possible that with large values of the first Powell-Eyring parameter and smaller values of the porous parameter, the boundary layer thickness will be totally increased.
2. Another interesting situation is that in which both the porous parameter and the thermal conductivity parameter increase significantly, the temperature distribution may be regarded as being enhanced uniformly.
3. Thermal radiation and heat generation have another important effect insofar as they can establish a thicker thermal layer with the thermal stratification phenomenon.
4. It is interesting to note that the thickness of the fluid layer depends very little on the second Powell-Eyring parameter, the thermal conductivity parameter, and the thermal stratification parameter.
5. A strong relationship between the cooling mechanism and both of the thermal stratification parameters and the radiation parameter is found.
Acknowledgement: The authors wish to express their sincere thanks to the editor and referees for their valuable time spent reading this paper and for their valuable comments and suggestions, which improved the quality of this paper.
Funding Statement: The authors received no specific funding for this study.
Conflicts of Interest: The authors declare that they have no conflicts of interest to report regarding the present study.
References
1. Ali, M. E. (1995). On thermal boundary layer on a power-law stretched surface with suction or injection. International Journal of Heat and Mass Transfer, 16, 280–290. DOI 10.1016/0142-727x(95)00001-7. [Google Scholar] [CrossRef]
2. Andersson, H. T., Aarseth, J. B., Dandapat, B. S. (2000). Heat transfer in a liquid film on an unsteady stretching surface. International Journal of Heat and Mass Transfer, 43(1), 69–74. DOI 10.1016/S0017-9310(99)00123-4. [Google Scholar] [CrossRef]
3. Afzal, N. (1993). Heat transfer from a stretching surface. International Journal of Heat and Mass Transfer, 36, 1128–1131. DOI 10.1016/s0017-9310(05)80296-0. [Google Scholar] [CrossRef]
4. Chen, C. K., Char, M. (1988). Heat transfer on a continuous stretching surface with suction or blowing. Journal of Mathematical Analysis and Applications, 35(2), 568–580. DOI 10.1016/0022-247X(88)90172-2. [Google Scholar] [CrossRef]
5. Grubka, L. J., Bobba, K. M. (1985). Heat transfer characteristics of a continuous stretching surface with variable temperature. ASME Journal of Heat Transfer, 107(1), 248–260. DOI 10.1115/1.3247387. [Google Scholar] [CrossRef]
6. Magyari, E., Keller, B. (1999). Heat transfer characteristics of the separation boundary flow induced by a continuous stretching surface. Journal of Physics D: Applied Physics, 32(22), 2876–2881. DOI 10.1088/0022-3727/32/22/308. [Google Scholar] [CrossRef]
7. Carragher, P., Crane, L. J. (1982). Heat transfer on a continuous stretching sheet. Journal of Applied Mathematics and Mechanics, 62, 564–573. DOI 10.1002/(ISSN)1521-4001. [Google Scholar] [CrossRef]
8. Elbashbeshy, E. M. A. (2001). Heat transfer over an exponentially stretching continuous surface with suction. Archives of Mechanics, 53, 643–651. [Google Scholar]
9. Ishak, A., Nazar, R., Pop, I. (2008). Heat transfer over an unsteady stretching surface with prescribed heat flux. Canadian Journal of Physics, 86(6), 853–855. DOI 10.1139/p08-005. [Google Scholar] [CrossRef]
10. Mahapatra, T. R., Gupta, A. S. (2003). Stagnation-point flow towards a stretching surface. The Canadian Journal of Chemical Engineering, 81(2), 258–263. DOI 10.1002/cjce.5450810210. [Google Scholar] [CrossRef]
11. Liu, I. C., Megahed, A. M. (2012). Numerical study for the flow and heat transfer in a thin liquid film over an unsteady stretching sheet with variable fluid properties in the presence of thermal radiation. Journal of Mechanics, 28(2), 291–297. DOI 10.1017/jmech.2012.32. [Google Scholar] [CrossRef]
12. Megahed, A. M. (2012). Variable viscosity and slip velocity effects on the flow and heat transfer of a power-law fluid over a non-linearly stretching surface with heat flux and thermal radiation. Rheologica Acta, 51(9), 841–874. DOI 10.1007/s00397-012-0644-8. [Google Scholar] [CrossRef]
13. Megahed, A. M. (2014). Variable heat flux effect on MHD flow and heat transfer over an unsteady stretching sheet in the presence of thermal radiation. Canadian Journal of Physics, 92(1), 86–91. DOI 10.1139/cjp-2012-0543. [Google Scholar] [CrossRef]
14. Eldabe, N. T. M., Hassan, A. A., Mohamed, M. A. A. (2003). Effect of couple stresses on the MHD of a non-Newtonian unsteady: Flow between two parallel porous plates. Zeitschrift für Naturforschung, 58(4), 204–210. DOI 10.1515/zna-2003-0405. [Google Scholar] [CrossRef]
15. Hayat, T., Iqbal, Z., Qasim, M., Obaidat, S. (2012). Steady flow of an Eyring Powell fluid over a moving surface with convective boundary conditions. International Journal of Heat and Mass Transfer, 55(7–8), 1817–1822. DOI 10.1016/j.ijheatmasstransfer.2011.10.046. [Google Scholar] [CrossRef]
16. Khader, M. M., Megahed, A. M. (2016). Numerical treatment for flow and heat transfer of Powell-Eyring fluid over an exponential stretching sheet with variable thermal conductivity. Meccanica, 51(8), 1763–1770. DOI 10.1007/s11012-015-0336-4. [Google Scholar] [CrossRef]
17. Mahmoud, M. A. A., Megahed, A. M. (2016). Slip flow of Powell-Eyring liquid film due to an unsteady stretching sheet with heat generation. Brazilian Journal of Physics, 46(3), 299–307. DOI 10.1007/s13538-016-0412-9. [Google Scholar] [CrossRef]
18. Mushtaq, A., Mustafa, M., Hayat, T., Rahi, M., Alsaedi, A. (2013). Exponentially stretching sheet in a Powell-Eyring fluid. Zeitschrift für Naturforschung A, 68, 791–798. DOI 10.5560/ZNA.2013-0063. [Google Scholar] [CrossRef]
19. Patel, M., Timol, M. G. (2009). Numerical treatment of Powell-Eyring fluid flow using method of satisfaction of asymptotic boundary conditions (MSABC). Applied Numerical Mathematics, 59(10), 2584–2592. DOI 10.1016/j.apnum.2009.04.010. [Google Scholar] [CrossRef]
20. Ramzan, M., Gul, N., Chung, J. D., Kadry, S., Chu, Y. M. (2020). Numerical treatment of radiative Nickel-Zinc ferrite-Ethylene glycol nanofluid flow past a curved surface with thermal stratification and slip conditions. Scientific Reports, 10(1), 16832. DOI 10.1038/s41598-020-73720-x. [Google Scholar] [CrossRef]
21. Ramesh, K., Khan, S. U., Jameel, M., Khan, M. I., Chu, Y. M. et al. (2020). Bioconvection assessment in Maxwell nanofluid configured by a Riga surface with nonlinear thermal radiation and activation energy. Surfaces and Interfaces, 21(18), 100749. DOI 10.1016/j.surfin.2020.100749. [Google Scholar] [CrossRef]
22. Ramzan, M., Rafiq, A., Chung, J. D., Kadry, S., Chu, Y. M. (2020). Nanofluid flow with autocatalytic chemical reaction over a curved surface with nonlinear thermal radiation and slip condition. Scientific Reports, 10(1), 18339. DOI 10.1038/s41598-020-73142-9. [Google Scholar] [CrossRef]
23. Qayyum, S., Khan, M. I., Masood, F., Chu, Y. M., Kadry, S. et al. (2020). Interpretation of entropy generation in Williamson fluid flow with nonlinear thermal radiation and first-order velocity slip. Mathematical Methods in the Applied Sciences, 44, 1–10. DOI 10.1002/mma.6735. [Google Scholar] [CrossRef]
24. Zhao, T. H., Khan, M. I., Chu, Y. M. (2021). Artificial neural networking (ANN) analysis for heat and entropy generation in flow of non-Newtonian fluid between two rotating disks. Mathematical Methods in the Applied Sciences, 44, 1–19. DOI 10.1002/mma.7310. [Google Scholar] [CrossRef]
25. Akram, S., Razia, A., Afzal, F. (2020). Effects of velocity second slip model and induced magnetic field on peristaltic transport of non-Newtonian fluid in the presence of double-diffusivity convection in nanofluids. Archive of Applied Mechanics, 90(7), 1583–1603. DOI 10.1007/s00419-020-01685-4. [Google Scholar] [CrossRef]
26. Akram, S., Afzal, Q., Aly, E. (2020). Half-breed effects of thermal and concentration convection of peristaltic pseudoplastic nanofluid in a tapered channel with induced magnetic field. Case Studies in Thermal Engineering, 22(2), 100775. DOI 10.1016/j.csite.2020.100775. [Google Scholar] [CrossRef]
27. Song, Y. K., Khan, S. A., Imran, M., Waqas, H., Khan, S. U. et al. (2021). Applications of modified Darcy law and nonlinear thermal radiation in bioconvection flow of micropolar nanofluid over an off centered rotating disk. Alexandria Engineering Journal, 60(5), 4607–4618. DOI 10.1016/j.aej.2021.03.053. [Google Scholar] [CrossRef]
28. Khan, M. I., Waqas, H., Khan, S. U., Imran, M., Chu, Y. M. et al. (2021). Slip flow of micropolar nanofluid over a porous rotating disk with motile microorganisms, nonlinear thermal radiation and activation energy. International Communications in Heat and Mass Transfer, 22(10), 105161. DOI 10.1016/j.icheatmasstransfer.2021.105161. [Google Scholar] [CrossRef]
29. Waqas, H., Khan, M. I., Khan, S. U., Khan, M. I., Kadry, S. et al. (2021). Falkner-Skan time-dependent bioconvrction flow of cross nanofluid with nonlinear thermal radiation, activation energy and melting process. International Communications in Heat and Mass Transfer, 120(2), 105028. DOI 10.1016/j.icheatmasstransfer.2020.105028. [Google Scholar] [CrossRef]
30. Ramzan, M., Riasat, S., Kadry, S., Chu, Y. M., Ghazwani, H. A. S. et al. (2021). Influence of autocatalytic chemical reaction with heterogeneous catalysis in the flow of Ostwald-de-Waele nanofluid past a rotating disk with variable thickness in porous media. International Communications in Heat and Mass Transfer, 128(6), 105653. DOI 10.1016/j.icheatmasstransfer.2021.105653. [Google Scholar] [CrossRef]
31. Chu, Y. M., Ahmad, F., Khan, M. I., Nazeer, M., Hussain, F. et al. (2021). Numerical and scale analysis of non-Newtonian fluid (Eyring-Powell) through pseudo-spectral collocation method (PSCM) towards a magnetized stretchable Riga surface. Alexandria Engineering Journal, 60(2), 2127–2137. DOI 10.1016/j.aej.2020.12.017. [Google Scholar] [CrossRef]
32. Afzal, Q., Akram, S. (2021). Impact of double-diffusivity convection in nanofluids and induced magnetic field on peristaltic pumping of a Carreau fluid in a tapered channel with different waveforms. Journal of Thermal Analysis and Calorimetry, 143(3), 2291–2312. DOI 10.1007/s10973-020-09776-8. [Google Scholar] [CrossRef]
33. Akram, S., Athar, M., Saeed, K., Umair, M. Y. (2021). Double-diffusivity convection on Powell-Eyring nanofluids in non-uniform inclined channel under the impact of peristaltic propulsion and induced magnetic field. The European Physical Journal Plus, 136(5), 1–14. DOI 10.1140/epjp/s13360-021-01506-9. [Google Scholar] [CrossRef]
34. Akram, S., Saleem, N., Umair, M. Y., Munawar, S. (2021). Impact of partial slip and lateral walls on peristaltic transport of a couple stress fluid in a rectangular duct. Science Progress, 104(2), 1–17. DOI 10.1177/00368504211013632. [Google Scholar] [CrossRef]
35. Afzal, Q., Akram, S., Ellahi, R., Sait, S. M., Chaudhry, F. (2021). Thermal and concentration convection in nanofluids for peristaltic flow of magneto couple stress fluid in a nonuniform channel. Journal of Thermal Analysis and Calorimetry, 144(6), 2203–2218. DOI 10.1007/s10973-020-10340-7. [Google Scholar] [CrossRef]
36. Akram, S., Athar, M., Saeed, K. (2021). Hybrid impact of thermal and concentration convection on peristaltic pumping of Prandtl nanofluids in non-uniform inclined channel and magnetic field. Case Studies in Thermal Engineering, 25(2), 100965. DOI 10.1016/j.csite.2021.100965. [Google Scholar] [CrossRef]
37. Akram, S., Razia, A. (2021). Hybrid effects of thermal and concentration convection on peristaltic flow of fourth grade nanofluids in an inclined tapered channel: applications of double-diffusivity. Computer Modeling in Engineering & Sciences, 127(3), 901–922. DOI 10.32604/cmes.2021.014469. [Google Scholar] [CrossRef]
38. Akram, S., Athar, M., Saeed, K., Razia, A. (2021). Crossbreed impact of double-diffusivity convection on peristaltic pumping of magneto Sisko nanofluids in non-uniform inclined channel: A bio-nanoengineering model. Science Progress, 104(3), 1–23. DOI 10.1177/00368504211033677. [Google Scholar] [CrossRef]
39. Powell, R. E., Eyring, H. (1944). Mechanism for relaxation theory of viscosity. Nature, 154(3909), 427–428. DOI 10.1038/154427a0. [Google Scholar] [CrossRef]
40. Prasad, K. V., Vajravelu, K., Datti, P. S., Raju, B. T. (2013). MHD flow and heat transfer in a power-law liquid film at a porous surface in the presence of thermal radiation. Journal of Applied Fluid Mechanics, 6, 385–395. DOI 10.36884/jafm.6.03.19563. [Google Scholar] [CrossRef]
41. Raptis, A. (1998). Flow of a micropolar fluid past a continuously moving plate by the presence of radiation. International Journal of Heat and Mass Transfer, 41(18), 2865–2866. DOI 10.1016/S0017-9310(98)00006-4. [Google Scholar] [CrossRef]
42. Mahmoud, M. A. A., Megahed, A. M. (2009). MHD flow and heat transfer in a non-Newtonian liquid film over an unsteady stretching sheet with variable fluid properties. Canadian Journal of Physics, 87(10), 1065–1071. DOI 10.1139/P09-066. [Google Scholar] [CrossRef]
43. Bilal, M., Ashbar, S. (2020). Flow and heat transfer analysis of Eyring-Powell fluid over stratified sheet with mixed convection. Journal of the Egyptian Mathematical Society, 28(1), 40. DOI 10.1186/s42787-020-00103-6. [Google Scholar] [CrossRef]
44. El-Gendi, S. E. (1969). Chebyshev solution of differential, integral and integro-differential equations. The Computer Journal, 12(3), 282–287. DOI 10.1093/comjnl/12.3.282. [Google Scholar] [CrossRef]
Cite This Article
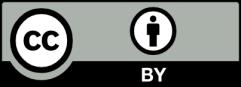
This work is licensed under a Creative Commons Attribution 4.0 International License , which permits unrestricted use, distribution, and reproduction in any medium, provided the original work is properly cited.