Open Access
ARTICLE
Influence of the Blade Bifurcated Tip on the Correlation between Wind Turbine Wheel Vibration and Aerodynamic Noise
1
Mechanical College, Shanghai Dianji University, Shanghai, 201306, China
2
College of Energy Engineering, Xinjiang Institute of Engineering, Urumqi, 830091, China
* Corresponding Author: Yuanjun Dai. Email:
Fluid Dynamics & Materials Processing 2023, 19(12), 3033-3043. https://doi.org/10.32604/fdmp.2023.029583
Received 27 February 2023; Accepted 05 May 2023; Issue published 27 October 2023
Abstract
To reduce the vibration and aerodynamic noise of wind turbines, a new design is proposed relying on a blade with a bifurcated apex or tip. The performances of this wind turbine wheel are tested at the entrance of a DC (directaction) wind tunnel for different blade tip angles and varying centrifugal force and aerodynamic loads. The test results indicate that the bifurcated apex can reduce the vibration acceleration amplitude and the vibration frequency of the wind wheel. At the same time, the bifurcated apex can lower the maximum sound pressure level corresponding to the rotating fundamental frequency of the wind wheel. According to all these findings, the tip angle of the bifurcated apex is the main factor enhancing the effect of the modification.Keywords
Considering the rapid development of economy, traditional energy sources present challenges, including environmental pollution and insufficient supply of raw materials, among others; thus, the development of renewable energy is garnering more attention. Wind energy is a form of renewable energy, whereby a wind turbine converts wind energy into electrical energy. A major component of wind turbines is the blades; however, the aerodynamic noise resulting from the vibrations caused by the blade movement has had a substantial negative effect on people. As such, reduction in wind turbine blade vibration and the associated aerodynamic noise, while maintaining power generation capacity and minimizing environmental harm, is a priority in wind turbine research.
To study the vibration and aerodynamic noise caused by wind turbines, Wang et al. assessed the correlation between the number of blades and modal parameters of wind turbines [1]; Xu et al. explored the influence of the use of asymmetric airfoil on the aerodynamic performance of the wind turbine [2]; Ma et al. explored the influence of airfoil and blade installation methods on the natural frequency of each order of wind turbine [3]; Dai et al. modified the V-shaped apex of the wind turbine blade to study the influence of modified design on the vibration and noise of the wind turbine [4,5]; Gao et al. installed S-shaped winglets at the tip of the wind turbine blade to assess the influence of winglets on the noise caused by the wind turbine [6]; Haghdoust et al. added shape memory alloy to the material of the wind turbine blade to suppress vibration of the wind turbine [7]; Chen et al. designed a tuned liquid damper to suppress the vibration of wind turbines [8]; Maizi et al. studied the influence of three different blade tip shapes on the aerodynamic noise of wind turbines [9]; Kim et al. used a semi-empirical formula combined with numerical simulation to analyze the influence of blade flexibility on aerodynamic noise of wind turbines [10]; and Moreau et al. experimentally investigated the noise reduction capability of a trailing edge serrated wind turbine blade at low to medium Reynolds numbers [11]. It is evident from the literature that the research to date has focused individually on either vibration or on aerodynamic noise of wind turbine blades, with research on the correlation between vibration and noise reduction being limited.
It is evident that wind turbine blade design affects the vibration and noise outputs of wind turbines. Therefore, this study assessed the vibration and aerodynamic noise resulting from a small wind turbine comprising a bifurcated apex.
In this study, the vibration and noise coupling characteristics of a wind turbine wind wheel were tested to assess the influence of the bifurcated apex design. The tests on the dynamic vibration and aerodynamic noise characteristics of the wind turbine were performed at the entrance of the DC wind tunnel at different blade tip angles and under different centrifugal force and aerodynamic loads.
2.1 Wind Wheel Vibration Design and Noise Coupling Characteristics Test Scheme
Three small 100 W wind turbine blades of varying dimensions were tested in the experiment. Fig. 1 provides a three-dimensional representation of the original blade and the modified double forked tip blade. The rated inlet wind speed was set at 8 m/s and the rated turbine rotation speed at 600 r/min. The blade parameters are shown in Table 1.
Figure 1: (a) Original blade; (b) bifurcated apex blade
The modified design focused on the tip of wind turbine blade because this is where the variation in the load and sound pressure is highest. The design of the bifurcated apex was derived from the twin-apex of the Boeing airliner. The twin-apex of the airfoil can reduce the intensity of the wing tip vortex and thus enhance the aerodynamic performance of the wing. The bifurcated apex includes tip angle
Figure 2: Bifurcated apex design
A low-speed direct current wind tunnel with a maximum wind speed of 15 m/s and a size of 3 m × 3 m at the open end was used in the experiment. A three-way accelerometer (B&K; 4524-B) and a microphone (BSWA; MPA416) were used to measure the data. The instrument sampling frequency is 400 Hz. A laser speed probe was connected to the system to obtain speed signals, which would facilitate later data processing (B&K; 2981). An electronic load meter was used to adjust the speed of the wind turbine to enable the observation of responses under varying experimental conditions (ADEX; IT8512A+). The test equipment is shown in Fig. 3.
Figure 3: (a) Data measurement system; (b) laser speed probe; (c) three-way accelerometer; and (d) acoustic array test system
The vibration and noise coupling characteristics tests of the wind turbines were carried out in accordance with the GB/T 19068.3-2003 Off Grid Wind Turbine-Part 3: Wind Tunnel Test Method and the GB/T 6882-2008 Acoustics Sound Pressure Method for Determination of Sound Power Level of Noise Sources. In this experiment, spectral analysis was used to comprehensively explore the influence of a bifurcated apex on the vibration and noise coupling characteristics of a wind turbine. Wind wheel vibration and noise data were measured under the same conditions and at the same time for each blade type. The wind tunnel wind speed parameter was set, and measurements were taken while the wind turbine was rotating. The acoustic array testing system comprised a pneumatic loading with 30 BK connect three-way accelerometer channels and the vibration and vibration noise testing system comprised seven acoustic sensors. The rotor vibration frequency, vibration acceleration amplitude, and the noise pressure level were obtained through a combination of data processing and spectrum analysis.
The accelerometer was placed close to the wind wheel at the front and middle ends of the generator. The dynamic vibration spectrum captured by the accelerometer was combined with the static vibration spectrum measured by the modal experiment. The dynamic frequency of the wind wheel was identified using the spectrum analysis method [12]. By comparing the static and dynamic vibration spectra, it was observed that the dynamic vibration spectrum of the accelerometer located at the front end of the generator was more similar to the static vibration spectrum. Thus, the data measured at the front end of the generator were used for analysis.
Noise measuring points are placed as shown in Fig. 4 and clustered around the wind turbine blade tip where the local noise sound pressure level is the highest. A total of seven microphones were placed beginning at 30 cm from the rotor center moving outward in a horizontal direction along the rotor plane. The reference points assigned include the origin (O) at the center, the x-axis (X) parallel to the flow direction, and the measuring point spacing on the y-axis (Y). The measuring points are set in line 20 cm from, and parallel to, the rotating plane of the wind wheel, with measuring point 7 located 10 cm to the left of the x-axis. The interval between each measuring point is 10 cm.
Figure 4: Placement of noise measuring points
3.1 Influence of the Bifurcated Apex on Wind Turbine Vibration Characteristics
3.1.1 Unchanging Centrifugal Force and Increasing Aerodynamic Load
When conducting an experiment on the vibration and noise coupling characteristics of wind turbines, an electronic load meter should be connected to the power generation system of the wind turbine so that the speed of the wind turbine can be adjusted. A constant centrifugal force load regulates electronic load, which ensures that the rotating speed of the rotor is constant. The aerodynamic load rule considers wind speed relative to the centrifugal force constant. The influence of the bifurcated apex on the rotor vibration characteristics became evident when fatigue damage was observed following the aerodynamic load increase. First- and second-order vibrations were prioritized in the data analysis because fatigue damage occurred when the wind turbine rotor speed and resonance were low. In the experiment, the rated speed was 600 r/min, and the incoming wind speeds were 6, 7, 8, and 9 m/s.
The fundamental vibration frequency of the wind turbine is indicated in Table 3. With the increase in aerodynamic load, the variation amplitude was less than 1 Hz, indicating no major difference between the fundamental vibration frequencies of the original wind turbine and the bifurcated apex wind turbine. It is therefore evident that the aerodynamic load has little influence on the fundamental vibration frequency of the wind turbine, and the bifurcated apex has little influence on the fundamental frequency.
As indicated in Fig. 5, the aerodynamic load increases and the fundamental vibration acceleration amplitude changes for the original blade; however, in the bifurcated apexs, the change was hardly noticeable at less than 0.1 m/s. The instability of the data was as a result of the margin of error of the sensor in the range of allowable accuracy, and as a result, the fundamental vibration acceleration amplitude of the aerodynamic load of the wind turbines was less affected. When comparing the three modified bifurcated tip wind turbines, the fundamental vibration acceleration amplitude decreased in the bifurcated apex 1 by 8.33%, 17.95%, 8.11%, and 15.38%; in the bifurcated apex 2 by 25.00%, 28.21%, 16.22%, and 30.77%; and in the bifurcated apex 3 by 41.67%, 41.03%, 35.14% and 41.03%, respectively. The comparative analysis indicates that the bifurcated apex can reduce the fundamental amplitude of the vibration acceleration. The best reduction effect was observed in the bifurcated apex 3 wind wheel.
Figure 5: Amplitude of the fundamental vibration acceleration of the wind wheel under increasing aerodynamic load
In addition, the second-order vibration frequency and the amplitude of vibration acceleration were analyzed. It was observed that the second-order vibration frequency was concentrated in the range of 59–61 Hz and the regularity was like that of the fundamental vibration. It is evident from the analysis of the second-order vibration frequency and vibration acceleration amplitude, known by centrifugal load constant, the aerodynamic load increase, the wind turbine rotor vibration frequency, and vibration acceleration amplitude were small. It could not be proven that the aerodynamic load influenced the wind turbine rotor vibration frequency and change in vibration acceleration amplitude, because the rotor diameter was small and very stiff, as such the aerodynamic load was therefore small, and there was a smaller effect on the vibration frequency amplitude and vibration acceleration. However, compared with the original wind turbine blades, the vibration acceleration amplitude of the wind turbine could be significantly reduced. It is therefore evident that the bifurcated apex can improve the vibration characteristics of wind turbines, and more specifically, the bifurcated apex 3 wind turbine improved the most.
3.1.2 Unchanging Aerodynamic Load and Increasing Centrifugal Force Load
The influence of the bifurcated apex on the vibration characteristics of the wind turbine was analyzed under a constant aerodynamic load, that is, a constant inlet wind speed, and an increasing centrifugal force load, where an electronic load meter was adjusted to increase the wind wheel tip speed ratio. The wind speed was maintained at a rated wind speed of 8 m/s and the pointed speed ratios were 4.5, 5.0, 5.5, and 6.0, respectively.
The fundamental vibration frequency of the different wind turbines is shown in Table 4. With the increase in centrifugal force load, the fundamental vibration frequency of the original wind turbine and the bifurcated apex wind turbines increased, indicating that the centrifugal force load has a large influence on the fundamental vibration frequency of the wind turbines. It is evident from the comparative analysis that the bifurcated apex can adjust the fundamental vibration frequency of the wind turbine.
As shown in Fig. 6, the amplitude of the fundamental vibration acceleration increased with the increase in centrifugal force load in both the original wind turbine and the bifurcated apex wind turbines. The comparative analysis demonstrated that the amplitude of the fundamental vibration acceleration of the bifurcated apex wind turbine was lower than that of the original wind turbine. When comparing the different bifurcated apex wind turbines at four different tip speed ratios in the fundamental vibration; acceleration amplitude decreased in the bifurcated apex 1 wind turbines by 12.50%, 10.26%, 12.77%, and 12.96%; in the bifurcated apex 2 wind turbines by 21.88%, 20.51%, 19.15%, and 24.07%; and in the bifurcated apex 3 wind turbines by 34.38%, 30.77%, 27.66%, and 27.78%, respectively. It is therefore evident that the bifurcated apex can reduce the fundamental vibration acceleration amplitude of wind turbines. The best reduction effect was observed in the bifurcated apex 3 wind turbine.
Figure 6: Amplitude of the fundamental vibration acceleration of the wind wheel under increasing centrifugal force load
In addition, the second-order vibration frequency and vibration acceleration amplitude were analyzed, and it was observed that the regularity was like that of the fundamental vibration. The second-order vibration frequency and vibration acceleration amplitude were analyzed under an increasing aerodynamic load and increasing centrifugal force load. The wind turbine rotor vibration frequency and vibration acceleration amplitude increased because as the tip speed ratio increased, the centrifugal force also increased with increased rotor speed, resulting in greater distortion of the wind turbines. Therefore, the centrifugal force load is directly proportional to the vibration frequency and vibration acceleration amplitude of the wind turbine. It is evident that the vibration frequency of the wind turbine can be adjusted by the bifurcated apex to reduce the vibration acceleration amplitude of the wind turbine. The highest reduction effect was observed in the bifurcated apex 3 wind turbine.
3.2 Bifurcated Apex Influence on Wind Turbine Aerodynamic Noise
3.2.1 Wind Turbine Aerodynamic Noise Spectrum Analysis
Fig. 7 indicates the noise spectrum at measuring point 3 (x = 20 cm) at a wind speed of 8 m/s and a rated turbine speed of 600 r/min. The noise spectrum diagram indicates that the sound pressure level is highest at the fundamental frequency, the rotated harmonic relationship between the peak frequency of the sound pressure level, the blade tip vortex shedding frequency of the peak sound pressure level, and the corresponding peak sound pressure level of the ambient noise. In this study, the variation of the maximum pressure level corresponding to the rotational fundamental frequency was used as the observation value for the aerodynamic noise generated by the bifurcated apex.
Figure 7: Noise spectrum at measuring point 3 at a wind speed of 8 m/s and rated turbine speed of 600 r/min
3.2.2 Unchanging Centrifugal Force Load and Increasing Aerodynamic Load
Considering noise measuring point 3 near the blade tip as an example, the centrifugal force load of the wind turbine remained unchanged, but the aerodynamic load increased. In other words, the rated speed was maintained at 600 r/min in the experiment, with varying incoming wind speeds of 6, 7, 8, and 9 m/s, respectively.
As shown in Fig. 8, when the aerodynamic load increased, the maximum pressure level corresponding to the fundamental frequency of the rotor rotation remained unchanged while the continued to increase. It is evident from comparative analysis, and not retrofitted wind turbines, that the rotation of the bifurcated apex rotor base frequency corresponds to the loudest level at a fundamental frequency of 30 Hz. The rotation of the rotor blade base frequency corresponding to the loudest level decreased in the bifurcated apex 1 by 4.20%, 4.07%, 4.06%, and 3.86%; in the double fork structure 2 by 6.80%, 6.69%, 6.57%, and 6.49%; and in the bifurcated apex 3 by 8.70%, 8.46%, 8.41%, and 8.22%, respectively. The theoretical analysis indicates that when the rotating speed was constant and the rotating fundamental frequency was constant, the corresponding loudest level remained unchanged. The reason for these small changes is that wind speed fluctuations during the process of the experiment pose limitations to the data. The bifurcated apex could reduce the noise corresponding to the fundamental frequency of the rotor rotation. The bifurcated apex 3 wind turbine demonstrated the best noise reduction effect. The noise reduction effect of the wind turbine also gradually improved with the increase in the angle between the blade tips.
Figure 8: Aerodynamic load increase: Loudest pressure level corresponding to the fundamental frequency of wind wheel rotation
3.2.3 Unchanging Aerodynamic Load and Increasing Centrifugal Force
Considering noise measuring point 3 near the blade tip as an example, the aerodynamic load of the wind turbine remained unchanged, but the centrifugal force load increased, that is, the experimental wind speed remained at the rated wind speed of 8 m/s, and the tip speed ratios were 4.5, 5.0, 5.5, and 6.0, respectively. The aim was to assess the influence of the bifurcated apex on the aerodynamic noise of the wind turbine. As shown in Fig. 9, when the aerodynamic load remained unchanged and the centrifugal force load increased, the maximum pressure level corresponding to the fundamental frequency of wind wheel rotation also increased consistently, while the remained unchanged. With a constant incoming wind speed, the rotor tip speed ratio increased and the rotational speed increased, and as a result, the aerodynamic noise of the wind turbine increased. Meanwhile, ambient noise remained unchanged because the incoming wind speed remained unchanged. It is evident through comparative analysis, and not retrofitted wind turbines, that the rotation of the bifurcated apex rotor base frequency corresponds to the loudest level, at fundamental frequencies of 26.40, 29.35, 32.30, and 35.25 Hz. The base frequency of the rotation of the rotor corresponding to the loudest level decreased in bifurcated apex 1 by 4.03%, 4.33%, 4.01%, and 3.56%; in double fork apex 2 by 7.68%, 7.73%, 6.51%, and 6.21%; and in double fork tip blade structure 3 by 8.70%, 9.28%, 9.24%, and 9.17%, respectively. It is therefore evident that the modified bifurcated tip turbine can reduce the noise corresponding to the rotating fundamental frequency of the wind turbine. The bifurcated apex 3 wind turbine demonstrated the best noise reduction effect.
Figure 9: Loudest pressure level corresponding to the fundamental frequency of the wind wheel with the increase in centrifugal force load
In this study, the vibration and noise coupling characteristics of the original blade wind turbine and the bifurcated apex wind turbine were tested simultaneously, and the following conclusions have been drawn:
(1) Through the analysis of vibration characteristics under different operational conditions, it was evident that the variation of aerodynamic load has no noticeable effect on the fundamental or second-order vibration of the wind turbine, whereas the change in centrifugal force load had a noticeable influence on the fundamental and second-order vibration of the wind turbine, with the change being proportional to the relation.
(2) By analyzing the aerodynamic noise generated by a wind turbine under different operational conditions, it was observed that the aerodynamic load had no noticeable influence on the noise change corresponding to the rotational fundamental frequency of the wind turbine, while the centrifugal force load had a large influence on the variation in noise corresponding to the rotating fundamental frequency of the wind turbine, with the variation being proportional to that of the wind turbine. Meanwhile, it was observed that the bifurcated apex could reduce aerodynamic noise of wind turbines.
(3) Through comparative analysis, it was observed that the bifurcated apex could improve the vibration and aerodynamic noise performance of a wind turbine, with a higher angle within the angle range of 0°–90° between blade tips being the primary factor enhancing the effect. Among the different bifurcated apex assessed, the bifurcated apex 3 wind turbine demonstrated the best vibration and noise reduction effect.
Funding Statement: This work was supported by the National Natural Science Foundation Project under Grant Numbers [51966018, 51466015].
Conflicts of Interest: The authors declare that they have no conflicts of interest to report regarding the present study.
References
1. Wang, J. W., Yan, J. X., Liu, J. P., Zhang, Z. H. Y. (2008). Experimental modal analysis of multi-blade wind turbine. Journal of Solar Energy, 29(12), 1460–1464. [Google Scholar]
2. Xu, Z. H., Zhang, Y., Yang, B., Wang, J. M., Shen, Z. H. H. (2013). Effects of installation method of asymmetric airfoils on performance of H-type wind turbine. Journal of Solar Energy, 34(6), 933–937. [Google Scholar]
3. Ma, J. L., Wang, J. W., Liu, B., Che, F., Liu, X. F. (2013). Research on impact of airfoil changes and blade installation on each order natural frequency of wind wheel. Journal of Engineering Thermophysics, 34(6), 1069–1073. [Google Scholar]
4. Dai, Y. J., Zhang, J. W., Ma, J. H. Z. H. (2018). Experimental study of effect of V-type blade on vibration characteristics of wind turbine. Journal of Engineering Thermophysics, 39(11), 95–99. [Google Scholar]
5. Dai, Y. J., Ren, C. H. Z., Xu, L. J., Li, B. H. (2017). Experimental study of effect of V-type blade tip structure on aerodynamic noise at tip region of wind turbine. Journal of Solar Energy, 38(2), 472–477. [Google Scholar]
6. Gao, Z. H. Y., Wang, J. W., Dong, X. Q., You, Z. H. G., Li, Y. Z. H. (2014). Experimental study on sound radiation effects near wake of the rotor by S tip vane. Journal of Engineering Thermophysics, 35(9), 1749–1752. [Google Scholar]
7. Haghdoust, P., Conte, A. L., Cinquemani, S. (2018). Investigation of shape memory alloy embedded wind turbine blades for the passive control of vibrations. Smart Materials and Structures, 27(10), 105012. [Google Scholar]
8. Chen, J. L., Georgakis, C. T. (2018). Spherical tuned liquid damper for vibration control in wind turbines. Journal of Vibration and Control, 21(10), 1875–1885. [Google Scholar]
9. Maizi, M., Mohamed, M. H., Dizene, R., Mihoubi, M. C. (2018). Noise reduction of a horizontal wind turbine using different blade shapes. Renewable Energy, 117(8), 242–256. [Google Scholar]
10. Kim, H., Lee, S., Son, E., Lee, S. M., Lee, S. G. (2012). Aerodynamic noise analysis of large horizontal axis wind turbines considering fluid-structure interaction. Renewable Energy, 42, 46–53. [Google Scholar]
11. Moreau, D. J., Doolan, C. J. (2013). Noise-reduction mechanism of a flat-plate serrated trailing edge. AIAA Journal, 51(10), 2513–2522. [Google Scholar]
12. Lv, W. C. H., Ma, J. L., Wang, J. W., Li, P. L., Zhang, Y. Q. (2016). Indirect test and identification method of dynamic frequencies of typical vibrations on wind wheel. Transactions of the Chinese Society of Agricultural Engineering, 32(23), 233–238. [Google Scholar]
Cite This Article
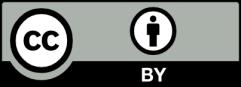
This work is licensed under a Creative Commons Attribution 4.0 International License , which permits unrestricted use, distribution, and reproduction in any medium, provided the original work is properly cited.