Open Access
ARTICLE
Development of a High-Temperature Thixotropic Cement Slurry System
1
Institute of Petroleum Engineering Technology, Sinopec Northwest Oil Field Company, Urumqi, 830000, China
2
Xinjiang Branch of CNPC Chuanqing Drilling Engineering Company Limited, Korla, 841000, China
3
School of Petroleum Engineering, China University of Petroleum (East China), Qingdao, 266580, China
4
Sinopec Shengli Petroleum Engineering Co., Ltd., Dongying, China
5
Henan Science and Technology Innovation Promotion Center, Zhenzhou, 450003, China
* Corresponding Author: Mengran Xu. Email:
Fluid Dynamics & Materials Processing 2023, 19(11), 2907-2921. https://doi.org/10.32604/fdmp.2023.029304
Received 12 February 2023; Accepted 25 April 2023; Issue published 18 September 2023
Abstract
Cementing carbonate reservoirs is generally a difficult task. The so-called thixotropic cement slurry has gained considerable attention in this regard as it can help to fix some notable problems. More precisely, it can easily fill the leakage layer; moreover, its gelling strength can grow rapidly when pumping stops, thereby increasing the resistance to gas channeling, effectively preventing this undesired phenomenon in many cases. High-temperature thixotropic cement slurry systems, however, are still in an early stage of development and additional research is needed to make them a viable option. In the present study, using a self-developed composite high-temperature thixotropic additive as a basis, it is shown that the compressive strength can be adjusted by tuning the proportion of silica sand, the high-temperature retarder, fluid loss additive and dispersant (compatible with the thixotropic additive). According to the tests, the developed high-temperature thixotropic cement slurry system has a 14 d compressive strength of 29.73 MPa at 150°C, and a thickening time of 330 min when the dosage of retarder is 2%. At the same time, the rheological property, water loss, permeability, water separation rate, and settlement stability of the cement slurry system meet the requirements of cementing construction.Keywords
At present, carbonate gas reservoirs play an important role in proven gas reservoirs. In recent years, the exploration and development of carbonate gas reservoirs has also shown a trend of rapid development [1], and there are more and more marine sedimentary reservoirs in the exploration and development areas [2]. However, the cementing operation on carbonate reservoirs generally has the following difficulties [3–7]: ① the bottom hole temperature is high. High temperature can make the functional admixture of cement slurry fail, the rheological properties and stability of cement slurry change, the viscosity of cement slurry decreases, and the gas channeling resistance decreases, which can cause gas channeling and difficulty with preventing gas channeling; ② the gas reservoir pressure is high, and the safety window is narrow. In the borehole where the high-pressure gas reservoir is drilled, there are also low-pressure easy-to-leak or even fractured-vuggy serious leakage-prone layers. If the high-pressure gas reservoir is to be stabilized, there is a danger of leaking of the low-pressure layer. To sum up, the contradiction between pressure stability and leakage prevention is very prominent. Therefore, how to effectively prevent gas channeling and formation of pressure leakage has become an urgent problem to be solved in exploration and development. At present, at home and abroad, latex and liquid silicon are mainly used to cement high temperature and high pressure gas reservoirs, but once the well temperature exceeds 170°C, this kind of cement slurry system is no longer applicable [8]. Because of its good thixotropy, the thixotropic cement slurry system can easily fill the leakage layer, and its gel strength can develop rapidly when pumping stops, thus increasing the gas channeling resistance, preventing the occurrence of gas channeling, and also solving the problem of poor plugging of the leakage interval. Therefore, the thixotropic cement slurry system has attracted increasing attention from cementing engineers and technicians.
The thixotropic cement slurry system is a kind of special cement slurry obtained by adding thixotropic additive to ordinary Portland cement. It has the characteristics that the gel structure is destroyed under shear and quickly recovered after being static, i.e., shear thinning and static thickening. During the cementing operation, the thixotropic cement slurry system can quickly form a network structure in the slurry after being pumped to the target layer, which can effectively avoid the migration of bubbles in the slurry, thus achieving the purpose of preventing gas channeling [9–12]. When it enters the leakage-prone stratum, the network structure is rapidly formed in the cement slurry under the static state, and then the consistency of the cement slurry increases rapidly, which makes the cement slurry lose its fluidity, thereby achieving the purpose of plugging the leakage-prone stratum [13–15]. Therefore, the thixotropic cement slurry system is an effective means of preventing leakage and gas channeling. At present, research on the thixotropic cement slurry system has greatly progressed, with some reports on field application, but the application temperature is mostly at normal and moderate temperature, while the research on high temperature thixotropic cement slurry system needs to be deepened.
To solve this problem, this paper takes the self-developed high temperature thixotropic additive as the core additive, and optimizes the cement slurry admixture compatible with the thixotropic additive under the condition of ensuring the compressive strength performance of the high temperature thixotropic cement slurry system to meet the requirements of field construction. Thus, constructing a set of high temperature thixotropic cement slurry systems with good thixotropic performance without affecting the conventional cement slurry performance, which provides a new solution for cementing in carbonate gas reservoirs.
The experimental materials used in this study are listed in Table 1. The thixotropic additive used in this study is a self-developed composite high temperature thixotropic additive [16], which consists of 62.5% xanthan gum + 6.25% konjac gum + 31.25% KCl.
The preparation of cement slurry and the routine test of performance of cement slurry are carried out in accordance with the method of the American Petroleum Institute 10B-2-2013.
The method of evaluation of the high temperature thixotropy of cement slurry used in this study is the consistency increment method, and its test process is as follows [17]: place the prepared cement slurry in the thickener, after reaching the target temperature, test the consistency increase after stopping and starting, at stopping times of 10, 20, and 30 min. The evaluation of thixotropic performance of cement slurry by this method must be carried out on a stable consistency section during the thickening of the cement slurry, and the stable section of the cement slurry is kept for more than 60 min to ensure the accuracy and operability of the test.
Considering that the current thixotropic evaluation methods generally test at normal temperature and medium-high temperature, the thixotropy of cement slurry obtained from the evaluation of high temperature cement slurry by the consistency increment method was not classified according to the common/usual consistency difference. Therefore, an evaluation standard for thixotropy of cement slurry at high temperature was established, and the thixotropy of the cement slurry was judged according to the consistency increment. The evaluation standard is presented in Table 2.
3.1 Control of Compressive Strength of High Temperature Thixotropic Cement Slurry System
The compressive strength of cement slurry will decline at high temperature, which is not conducive to the sealing integrity of wellbores [18]. At present, the problem of strength decline at high temperature is mostly solved by adding sand to cement, and the general amount of added silica sand is 30%–50%. To ensure that the strength performance of high temperature thixotropic cement slurry system meets the requirements of field construction, two kinds of silica sand, with 180 and 80 mesh, and nano-liquid silicon were selected to control the compressive strength of the high temperature thixotropic cement slurry system, in which the ratio of silica sand was 7:3 [19].
To determine the amount of composite silica sand and nano-liquid silicon, the compressive strength of cement stone with different amounts of silica sand and nano-liquid silicon was tested. The curing temperature of cement stone specimens was 150°C, and curing time was 1 and 2 d. The consistency of the cement slurry increases due to the addition of silica sand, hence the water-cement ratio was adjusted to 0.5. The experimental formula is presented in Table 3.
3.1.2 Experimental Results and Analysis
The test results of the compressive strength of the cement slurry formed by each cement slurry formula are shown in Fig. 1. The addition of silica sand and liquid silicon at high temperature improves the compressive strength of the cement slurry system. Under the same condition of thixotropic addition, comparing the compressive strength of cement slurry with different amounts of silica sand and liquid silicon, it is observed that the compressive strength of cement slurry with 50% silica sand and 10% liquid silicon is the highest, which is 35.6 MPa. When comparing Formula 8 with Formula 9, the 1-day strength of Formula 8 decreased 0.8 MPa, the 2-day strength decreased 0.5 MPa, and the 7-day strength decreased 0.6 MPa. This shows that the addition of the composite thixotropic agent slightly decreased the compressive strength, but with the compressive strength still being much higher than the industry standard requirements. Therefore, silica sand and liquid silicon are selected as system strength enhancers, with the addition of 50% silica sand (180 and 80 mesh, with the ratio of 7:3) and 10% nano-liquid silicon.
Figure 1: Compressive strength of cement stone
3.2 Optimization of Additives for the High Temperature Thixotropic Cement Slurry System
3.2.1 Optimization of Retarder
With the increase of temperature, the thickening time of the cement slurry shows a decreasing trend. To meet the safety requirements for cementing construction, it is necessary for the cement slurry to have enough thickening time under the condition of circulating temperature at the bottom of the well, so the retarder is optimized. Through investigation [20], GH-9 and DZH-3 which are widely used retarders have been known to impart good retarding effect at medium and high temperature and are selected for testing. The basic formula is: Akzo G cement + 2% thixotropic additive + 0.5% dispersant SCD + 10% liquid silicon + 35% silica sand (180 mesh) + 15% silica sand (80 mesh) + water cement ratio of 0.5, and the test temperature is 90°C.
The experimental results of retarder optimization are presented in Table 4. The thickening time of GH-9 with 1% dosage is 80 min, which fails to reflect the retarding performance, and the thickening time does not meet the requirements of the consistency increment method. However, the thickening time of the 2% retarder DZH-3 is 420 min, which meets the requirements of the consistency increment method, so retarder DZH-3 is selected as the retarder in the cement slurry system.
3.2.2 Optimization of Dispersant
The rheological property of cement slurry is related to the flow resistance of cement slurry injection during cementing [21,22]. The decline of the rheological property of cement slurry will seriously affect the displacement efficiency of the cement slurry and cementing quality [23,24]. According to an investigation, SCD and BZGF-1 can effectively improve the rheology [25] of cement slurry at high temperature, and the dosage ranges from 1% to 2%. Therefore, SCD and BZGF-1 are selected as the best dispersants. The basic formula is: Akzo G cement + 2% thixotropic additive + 2% retarder DZH-3 + 10% liquid silico + 35% silica sand (180 mesh) + 15% silica sand (80 mesh) + water cement ratio of 0.5.
The rheological test results of SCD and BZGF-1 are presented in Table 5. The average rheological properties of the dispersants SCD and BZGF-1 meet the API standards when the dosage is 1% and 1.5%, and the rheological index is the largest when the dosage of dispersant SCD is 1.5%, thus SCD is selected as the dispersant in this system.
3.2.3 Optimization of Fluid Loss Additives
Water loss is an important index used to evaluate the performance of cement slurry. A large water loss will lead to poor fluidity of the cement slurry, which will further affect the field cementing construction. A fluid loss additive can effectively control the water loss from cement slurry and is an important additive to ensure the safety of cementing construction.
At present, DZJ-Y, BXF-200L, FS-23L, BH-F201 and D400-I are widely used fluid loss additives. They have a wide range and good high temperature resistance, and its dosage is generally 1%–3% [26]. To make the high-temperature thixotropic cement system meet the standard of water loss, five fluid loss additives, DZJ-Y, BXF-200L, FS-23L, BH-F201 and D400-I, are selected for optimization. The basic formula is: Akzo G cement + 2% thixotropic additive + 2% DZH-3 retarder + 10% liquid silicon + 35% silica sand (180 mesh) + 15% silica sand (80 mesh) + 1% dispersant SCD + water cement ratio 0.5.
The fluid loss additives DZJ-Y, BXF-200L, FS-23L and BH-F201 are solution-type, which can be directly used for cement slurry preparation. The water loss reducer D400-I is a microsphere, which will absorb water and swell in solution. If the filtrate reducer D400-I is directly mixed with slurry, during the thickening process of the cement slurry it will absorb water and cause the consistency of the cement slurry to increase for a short time, which is not conducive to the pumping of cement slurry. Therefore, it is necessary to pre-hydrate D400-I to avoid the problem of poor rheology in the process of slurry pumping.
The effects of temperature and pH on the water absorption characteristics of the filtrate additive D400-I were tested experimentally, and the experimental results are shown in Fig. 2. By comparison, it was found that temperature and pH contribute to the water absorption of the fluid loss additive D400-I, and the higher the temperature and pH, the better its water absorption characteristics. Finally, it was determined that the filtrate additive D400-I should be pre-hydrated at 75°C and pH = 12 when preparing the cement slurry.
Figure 2: Effect of temperature and pH on water absorption characteristics of fluid loss additive D400-I
According to the basic formula, five kinds of fluid loss additives BXF-200L, DZJ-Y, FS-23L, BH-F201 and D400-I, were added into the cement slurry system, and the API water loss was measured at 150°C. The experimental results are presented in Table 6.
As given in Table 6, the water loss of BH-F201, FS-23L, BXF-200L and D400-I all exceeded the water loss specified in the API standard at 150°C, with the water loss of D400-I at 2.5% dosage being 26 mL, indicating that the water loss of all the fluid loss additives met the API requirements.
3.3 Influence of Additives on Thixotropy of Cement Slurry
As additives such as fluid loss additive and dispersant are introduced into the cement slurry system, it is necessary to evaluate whether the selected cement slurry additives affect the thixotropy of the cement slurry system. To study the influence of additives on the thixotropy of cement slurry, the thixotropy of the cement slurry was tested by the consistency increment method at 150°C.
The experimental results of the influence of cement slurry additives on thixotropy of the cement slurry system are presented in Table 7. The results indicate that there were gains and losses. The consistency difference of the water-based slurry is 51.9 Bc when it is stopped for 20 min, and the consistency alarm is started when it is stopped for 30 min; The consistency difference of the cement slurry with dispersant is 56.3 Bc when it is stopped for 20 min, and the consistency alarm is started when it is stopped for 30 min; When the mud is shut down for 20 min, the consistency difference of the cement slurry with retarder is 53.6 Bc, and when it is shut down for 30 min, the consistency alarm is started.
According to the classification standard of the thixotropy performance of cement slurry, the consistency difference of cement slurry with these three additives is more than 50 Bc when it is stopped for 20 min, and the thixotropy performance of cement slurry is excellent, so its influence on thixotropy performance can be ignored. Therefore, D400-I is selected as the fluid loss additive, SCD as the dispersant, and DZH-3 as the retarder of this system.
3.4 Construction and Performance Evaluation of High Temperature Thixotropic Cement Slurry System
By adjusting the strength performance of the cement slurry system at high temperature (150°C) and optimizing and evaluating the additives, the types and dosages of cement slurry additives such as silica sand, liquid silicon, dispersant, fluid loss additive, and retarder were determined. Finally, a set of high temperature thixotropic cement slurry system was constructed, and its initial formula was: Akzo G cement + 2% composite thixotropic agent + 10% liquid silicon + 35% silica sand (180 mesh) + 15% silica sand (80 mesh) + retarder DZH-3 + filtrate reducer D400-I + dispersant SCD + water. To ensure that the comprehensive performance of high-temperature thixotropic cement slurry system attains the optimal level, the dosage of retarder DZH-3, filtrate reducer D400-I, dispersant SCD, and other materials were reasonably optimized, and the resulting comprehensive performance of the system was evaluated.
3.4.1 Optimization of High Temperature Thixotropic Cement Slurry System
Optimization of High Temperature Thixotropic Cement Slurry System
Because 50% silica sand, 10% liquid silica, and fluid loss aadditiveD400-I are added to the cement slurry, the rheology of the cement slurry is negatively impacted. Therefore, the formula of the cement slurry is optimized by adjusting the water-cement ratio of the cement slurry and the amount of dispersant, so that the cement slurry has good rheology. The basic formula is: Akzo G cement + 2% composite thixotropic agent + 10% liquid silicon + 35% silica sand (180 mesh) + 15% silica sand (80 mesh) + 2%DZH-3 retarder + 2.5% fluid loss aadditiveD400-I, and the test temperature is 150°C.
The optimized experimental results of water-cement ratio and dispersant dosage are presented in Table 8. The reading of ϕ300 in the rheological data for a dispersant dosage of 1% and water-cement ratio of 0.50 is out of range, and the rheological properties of the other three groups of experiments are all in line with API standards, indicating that the rheological properties of the cement slurry are easy to adjust. Because the rheological indexes of dispersant dosage of 1.5% and water-cement ratio of 0.58 are greater than those of the other two formulas, the water-cement ratio and dispersant dosage of this formula are selected as the water-cement ratio and dispersant dosage of this system, where the water-cement ratio is 0.58, and the dosage of dispersant SCD is 1.5%.
Optimization of the Dosage of Fluid Loss Additive
To determine the optimal dosage of filtrate reducer, the dosage of filtrate reducer was varied and evaluated. The basic formula is Akzo G cement + 2% composite thixotropic agent + 10% liquid silicon + 35% silica sand (180 mesh) + 15% silica sand (80 mesh) + 2% DZH-3 retarder + 1.5% dispersant SCD + water cement ratio of 0.58. The test temperature is 150°C.
The experimental results of optimizing the dosage of filtrate reducer are shown in Fig. 3. It can be seen from Fig. 3 that when the dosage of filtrate reducer D400-I is 1.5%, the water loss is 78 mL, which does not meet the API standard. When the dosage of D400-I is 2.0%, 2.5% and 3%, the water loss meets the API standard. Because the addition of D400-I will increase the initial consistency of cement slurry to a certain extent, the dosage of D400-I is relatively large, and the water loss of cement slurry should be controlled at the same time. Therefore, D400-I with the dosage of 2.5% is selected as the final optimization result of bulk fluid loss agent.
Figure 3: Experiment on the effect of fluid loss agent on the water loss performance of cement slurry
To determine the optimal dosage of the retarder, varying dosages were used and the thickening time of the cement slurry at different temperatures and dosages was evaluated. The basic formula is: Akzo G cement + 2% composite thixotropic agent + 10% liquid silicon + 35% silica sand (180 mesh) + 15% silica sand (80 mesh) + 2.5% fluid loss additive D400-I + 1.5% dispersant SCD + water cement ratio of 0.58.
The experimental results of thickening time control are shown in Fig. 4. The thickening time of cement slurry has a linear relationship with the addition of retarder at the same temperature; when the amount of retarder is constant, the thickening time decreases with the increase of temperature. Therefore, the thickening time of high temperature thixotropic cement slurry system can be adjusted by adjusting the amount of retarder.
Figure 4: Experiment on the effect of retarder on the thickening time of cement slurry
Finally, the formula of the high temperature thixotropic cement slurry system is: Akzo G cement + 2% composite thixotropic agent + 10% liquid silicon + 35% silica sand (180 mesh) + 15% silica sand (80 mesh) + 2% retarder DZH-3 + 2.5% filtrate reducer D400-I + 1.5% dispersant SCD + water cement ratio of 0.58.
3.4.2 Comprehensive Performance Evaluation of High-Temperature Thixotropic Cement Slurry System
Compressive Strength Evaluation
For carbonate gas reservoir wells, the cement slurry is in a high temperature environment for a long time, so it is required that the cement slurry has strong high temperature resistance. The compressive strength of the final high temperature thixotropic cement slurry system formula was evaluated at a curing temperature of 150°C. The experimental results of the evaluation of the compressive strength of the cement slurry are shown in Fig. 5.
Figure 5: Cement slurry compressive strength evaluation test
The strength of cement slurry is 22.44 MPa at 1 d and 29.73 MPa at 14 d, which shows that the system has excellent high temperature resistance and can meet the strength requirements of cement slurry for carbonate gas reservoirs. However, the strength of 7 and 14 d declined compared with that of 5 d, and the reason for this phenomenon may be the insufficient amount of silica sand addition resulting in a decrease in compressive strength of cement stone, but still meeting the cementing strength requirements. It is recommended to increase the amount of silica sand addition and conduct further research.
Rheological Property Evaluation
According to the optimization results in 3.4.1, the rheological properties of the high-temperature thixotropic cement slurry system were evaluated. The experimental results are presented in Table 9. The fluidity index of the cement slurry is 0.814, and the consistency coefficient is 0.504, which meets the rheological requirements of cement slurry in field construction.
The final formulation of the high temperature thixotropic cement slurry system was evaluated for water loss. The experimental results showed that the water loss was 16 mL, which met the requirements of field construction for water loss of cement slurry.
Permeability is an important metric used to evaluate the performance of cement slurry. Excessive permeability may lead to problems such as air channeling. The national standard SY/T-5480-92 stipulates that the permeability of cement slurry should be less than or equal to 0.01 × 10−3 μm2. This section is about the final high-temperature thixotropic permeability evaluation of the cement slurry system at a curing temperature of 150°C. The test results are shown in Fig. 6, and the maximum permeability of cement stone of 14 d was 6.1 × 10−6 μm2. The permeability of the cement stone was less than 0.01 × 10−3 μm2, which meets the industry requirements.
Figure 6: Cement stone permeability evaluation test
The thickening time of cement slurry is an important construction parameter of cementing cement slurry, which is directly related to the success or failure of construction. The thickening time of the final high temperature thixotropic cement slurry system was evaluated at a test temperature of 150°C. The thickening time of the cement slurry was 330 min, the thickening curve is shown in Fig. 7, which can meet the construction requirements. If there are special requirements for the thickening time of cement slurry system, the amount of retarder can be adjusted to achieve the required thickening time.
Figure 7: High temperature thixotropic cement slurry system thickening curve
Water Separation Rate Evaluation
The final formulation of the high temperature thixotropic cement slurry system was evaluated for its water separation rate. After evaluation, no water separation occurred in the cement slurry, and the water separation rate was 0, which can meet the requirements of field construction.
Settlement Stability Evaluation
The settling stability of cement slurry directly affects the cementing quality. The settling stability is mainly manifested in the longitudinal density difference of the cement column, and the difference between the upper and lower density of the cement column was less than 0.02 g/cm3, which indicates that the cement slurry system has good stability. This section evaluates the settlement stability of the final high-temperature thixotropic cement slurry system. The experimental results are shown in Fig. 8. The difference in densities between the uppermost section and the lowermost section of the cement column formed by the high temperature thixotropic cement slurry system is 0.01 g/cm3, which indicates that the cement slurry system has good settlement stability and can meet the requirements of field cementing construction.
Figure 8: Test of cement slurry sedimentation stability
Thixotropic Performance Evaluation
The thixotropic performance of a cement slurry system is the key to pressure stability and leakage prevention, so the thixotropic performance of the final high temperature thixotropic cement slurry system was evaluated. The test temperature was 150°C. Table 10 presents the test results of the thixotropic evaluation of the cement slurry. The starting consistency difference was greater than 50 Bc when the machine was stopped for 20 min, indicationg that the thixotropic performance of the cement slurry is excellent, so this system has good thixotropic performance.
After testing, the density of high-temperature thixotropic cement slurry system was 1.88 g/cm3.
The fluidity of high-temperature thixotropic cement slurry system was 20 cm, which can meet the requirements of field construction.
(1) By optimizing the additives suitable for high-temperature thixotropic cement slurry system, a set of high-temperature thixotropic cement slurry system formula is finally constructed: Akzog cement + 2% composite thixotropic agent + 10% liquid silicon + 35% silica sand (180 mesh) + 15% silica sand (80 mesh) + 2% DZH-3 retarder + 2.5% filtrate reducer D400-I + 1.5% dispersant SCD + water cement ratio of 0.58.
(2) The high-temperature thixotropic cement slurry system has good thixotropic performance, high-temperature resistance, and adjustable thickening time. When the dosage of composite thixotropic agent is 2%, stop for 30 min and start consistency alarm. The 14 d compressive strength of the cement slurry is 29.73 MPa, and the thickening time is 330 min when the retarder is 2%. It can meet the requirements of carbonate gas reservoirs for cement slurry performance, and at the same time, the rheological properties, water loss, permeability, water separation rate, and settlement stability of cement slurry system can meet the requirements of cementing construction.
Funding Statement: This study was funded by the National Natural Science Foundation of China (51974355). Initials of author who received the grant is Bu Y., and the URLs to sponsors’ websites is: https://www.nsfc.gov.cn/.
Conflicts of Interest: The authors declare that they have no conflicts of interest to report regarding the present study.
References
1. Grishchenko, V. A., Mukhametshin, V. S., Rabaev, R. U. (2022). Geological structure features of carbonate formations and their impact on the efficiency of developing hydrocarbon deposits. Energies, 15(23), 9002. https://doi.org/10.3390/en15239002 [Google Scholar] [CrossRef]
2. Filipe, G. V., Lucas, V. W., Marcello, G. S., Luis, A. B., Gabriela, M. et al. (2021). Mixed siliciclastic-carbonate sedimentation in an evolving epicontinental sea: Aptian record of marginal marine settings in the interior basins of North-Eastern Brazil. Sedimentology, 68(5), 2125–2164. https://doi.org/10.1111/sed.12846 [Google Scholar] [CrossRef]
3. Ding, S., Zhou, S., Chen, L. (2009). Cementing technology for high temperature, high pressure and high sulfur gas wells in Northeast Sichuan. Natural Gas Industry, 29(2), 58–60. [Google Scholar]
4. Ribeiro, S., Naccache, M. F. (2022). Finite element model of oil well cement curing process in the presence of fluid loss zone. Journal of the Brazilian Society of Mechanical Sciences and Engineering, 44(11), 551. https://doi.org/10.1007/s40430-022-03851-x [Google Scholar] [CrossRef]
5. Niu, X., Zhang, K., Ding, S., Chen, Z. (2008). High pressure gas channeling prevention cementing technology in Northeast Sichuan. Petroleum Drilling Technology, 36(3), 10–15. [Google Scholar]
6. Ji, G. (2017). Study on cementing slurry system in anaco oilfield of Venezuela (Master Thesis). Northeast Petroleum University, Daqing, China. [Google Scholar]
7. Bu, Y., Ma, R., Du, J., Guo, S., Liu, H. et al. (2020). Utilization of metakaolin-based geopolymer as a mud-cake solidification agent to enhance the bonding strength of oil well cement-formation interface. Royal Society Open Science, 7(2), 191230. https://doi.org/10.1098/rsos.191230 [Google Scholar] [PubMed] [CrossRef]
8. You, J. (2010). Study on thixotropic cement slurry system and application (Master Thesis). China University of Petroleum, Qingdao, China. [Google Scholar]
9. Fabrício, C. V., Jo, D., Liberato, F., Romildo, D. T. F. (2020). Effect of plain and carboxylated styrene-butadiene rubber on the rheological behavior of silica fume-class G Portland cement slurries. Journal of Materials Research and Technology, 9(3), 5364–5377. https://doi.org/10.1016/j.jmrt.2020.03.063 [Google Scholar] [CrossRef]
10. You, J., Bu, Y., Jiang, L. (2011). Experimental study on optimization of new thixotropic agent for oil and gas well cementing slurry. Drilling and Production Technology, 34(1), 75–77, 118. [Google Scholar]
11. Jiang, L., Wang, R., Bu, Y. (2009). Development of a new thixotropic agent for thixotropic cement slurry. Drilling and Production Technology, 32(6), 103–106, 145. [Google Scholar]
12. Jiang, L., Wang, R., Bu, Y. (2009). Experimental study on a new method for evaluating the thixotropy of cement slurry. Petroleum Drilling Technology, 37(5), 62–65. [Google Scholar]
13. Anjuman, S. (2012). Rheological properties of oil well cement slurries. Proceedings of the Institution of Civil Engineers—Construction Materials, 165(1), 25–44. https://doi.org/10.1680/coma.2012.165.1.25 [Google Scholar] [CrossRef]
14. Xu, Z., Gao, S., Wang, J. (2006). Development and application of TC-1 thixotropic cement plugging agent. Drilling and Production Technology, 29(1), 93–95, 128. [Google Scholar]
15. Lu, H., Zhang, W., Xiong, C., Tang, S., Liu, Y. et al. (2016). Review of thixotropic cement slurry system. Progress in Fine Petrochemical Industry, 17(3), 21–26. [Google Scholar]
16. Guo, S., Bu, Y., Zhou, A., Du, J., Cai, Z. (2020). A three components thixotropic agent to enhance the thixotropic property of natural gas well cement at high temperatures. Journal of Natural Gas Science and Engineering, 84, 103699. https://doi.org/10.1016/j.jngse.2020.103699 [Google Scholar] [CrossRef]
17. Bu, Y., Wang, Q., Cai, Z., Shen, S., Zhao, Q. et al. (2020). A new evaluation method for thixotropic performance of cement slurry based on pressurized consistometer. Research and Exploration in Laboratory, 39(4), 37–41. [Google Scholar]
18. Liu, H., Bu, Y., Zhou, A., Du, J., Zhou, L. et al. (2021). Silica sand enhanced cement mortar for cementing steam injection well up to 380°C. Construction and Building Material, 308(2), 125142. https://doi.org/10.1016/j.conbuildmat.2021.125142 [Google Scholar] [CrossRef]
19. Bu, Y., Cai, Z., Guo, S., Liu, H. (2021). A high-temperature thixotropic cement paste system and its preparation method. CN108658516B. [Google Scholar]
20. Su, R., Li, Q. (2005). Research and application of high temperature retarder GH-9. Drilling Fluid and Completion Fluid, 22(5), 89–92, 127. [Google Scholar]
21. Aiad, I., El-Sabbagh, A. M., Adawy, A. I., Shafek, S. H., Abo-EL-Enein, S. A. (2018). Effect of some prepared superplasticizers on the rheological properties of oil well cement slurries. Egyptian Journal of Petroleum, 27(4), 1061–1066. https://doi.org/10.1016/j.ejpe.2018.03.011 [Google Scholar] [CrossRef]
22. Elahifar, B., Hosseini, E. (2022). Improving the rheological and mechanical properties of oil well cement slurries using multiple chemical admixtures for enhancing zonal isolation: A laboratory evaluation. Journal of Energy Resources Technology, 144(11), 207. https://doi.org/10.1115/1.4054355 [Google Scholar] [CrossRef]
23. Xia, X., Yu, Y., Jin, J., Liu, S., Xu, M. et al. (2020). Performance evaluation of polycarboxylic acid dispersant for oil well cementing. Materials Science Forum, 993, 1341–1350. https://doi.org/10.4028/www.scientific.net/MSF.993.1341 [Google Scholar] [CrossRef]
24. Jedadiah, F. B., Jason, W., John, E. H. (2019). Influence of high volumes of silica fume on the rheological behavior of oil well cement pastes. Construction and Building Materials, 203(2), 401–417. https://doi.org/10.1016/j.conbuildmat.2019.01.027 [Google Scholar] [CrossRef]
25. Gong, R., Li, J., Wang, L., Qiao, X., Yang, Y. (2003). Study on the relationship between the structure of water-soluble comb copolymer hyperdispersant and its dispersion performance for cement slurry. Fine Petrochemical, 19(1), 50–54. [Google Scholar]
26. Ding, S., Zhang, W. (2002). Gas channeling prevention cementing technology at home and abroad. Petroleum Drilling Technology, 30(5), 35–38. [Google Scholar]
Cite This Article
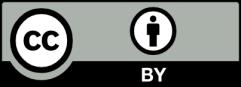
This work is licensed under a Creative Commons Attribution 4.0 International License , which permits unrestricted use, distribution, and reproduction in any medium, provided the original work is properly cited.