Open Access
ARTICLE
A Cementing Technology for Shale Oil Horizontal Wells
1
College of Petroleum Engineering, China University of Petroleum-Beijing, Beijing, 102249, China
2
CNPC Drilling Engineering Technology Research Institute of Daqing Drilling Engineering Company, Daqing, 163413, China
3
College of Petroleum, China University of Petroleum-Beijing at Karamay, Karamay, 834000, China
4
College of Architectural Engineering, Beijing University of Technology, Beijing, 101124, China
* Corresponding Author: Yue Qi. Email:
(This article belongs to the Special Issue: Fluid Flow and Materials Strength related to the Wellbore Safety)
Fluid Dynamics & Materials Processing 2023, 19(11), 2837-2845. https://doi.org/10.32604/fdmp.2023.028805
Received 09 January 2023; Accepted 03 April 2023; Issue published 18 September 2023
Abstract
Organic rich dark shale of Q Formation can be found in many areas (e.g., in the North of S Basin). The shale target stratum is easy to hydrate and often undergoes spallation. Therefore, centering the casing in the horizontal section of the irregular borehole is relatively difficult. Similarly, achieving a good cement flushing efficiency under complex borehole conditions is a complex task. Through technologies such as centralizer, efficient preflushing, multi-stage flushing and ductile cement slurry, better performances can be achieved. In this study, it is shown that the cementing rate in the DY2H horizontal section is 97.8%, which is more than 34% higher than that of adjacent wells. This cementing matching technology for sidetracking horizontal wells can be used to improve the cementing quality of continental shale and provides a reference for future applications in this field.Keywords
The Q Formation in the North of the S Basin is a large lake flood deposit. Organic-rich dark shale is relatively developed and widely distributed, with high overall maturity. The Q2–Q1 section is oil-bearing, and the shale reservoir resource potential is huge. It is preliminarily estimated that the oil resource is about 9.8 billion tons [1–13], and the natural gas resource is about 1 trillion m3. The pure shale reservoir is the crude oil in thick shale, with shale accounting for more than 95% and integrating source and reservoir [1]. Good exploration and development prospects have been seen in horizontal wells where shale with high organic matter abundance and high maturity is mainly put into production. Well DY2H is a key well for exploration in the northern S Basin, but it is difficult to center the casing in the horizontal section of the well’s irregular hole, resulting in a difficulty to ensure the efficiency of cementing flushing and displacement under the complex hole conditions, with a low proportion of high-quality horizontal section, high performance, and requirements of segmented volume fracturing on the cement sheath, as well as common cementing difficulties [14–19]. Through numerical simulation optimization of the scheme, based on simulation numerical simulation analysis combined with field practice, the factors affecting the cementing quality of shale oil horizontal wells, such as the casing centering degree and injection displacement rate, were analyzed, and the cementing construction technical schemes such as centralizer, high-efficiency front fluid, multistage flushing, and ductile cement slurry were optimized and improved. This effectively guaranteed the on-site cementing construction of the sidetracking horizontal wells of DY2H well, greatly improved the cementing quality of shale oil horizontal wells, and achieved the high-quality rate of 97.8% in the horizontal section of Well DY2H, providing a high-quality wellbore environment for achieving exploration purposes and productivity construction.
2.1 Geological Characteristics
The north of Songliao Basin is a continental freshwater sedimentary environment. The clay mineral content of shale in Group Q is in a lamellar structure. The horizontal section of the target layer is mainly gray-black shale, with a small amount of sandstone, siltstone, and limestone. The content of illite in continental pure shale is high, which is prone to interlayer spallation and the formation of “F” [1] shaped complex network fractures, as shown in Fig. 1. Well DY2H consists of Quaternary, Tertiary T group, Upper Cretaceous M group, S group, Lower Cretaceous N group, Y group, Q group, and QT group of strata from top to bottom. Using the data in the block, professional software is used to predict the formation pressure of three items. The average value of the formation pressure coefficient of Group Q is 1.22, the formation pressure of Group Q of Well DY2H is 24.16–29.82 MPa, the average value of the fracture pressure coefficient is 1.9, and the fracture pressure of Group Q of Well DY2H is 35.1–45.5 MPa. In addition, the gas logging of adjacent wells shows different levels of oil and gas. One of the wells has yielded industrial oil flow and produced gas. Due to the uncertainty of the formation pore, fracture, and other three pressures, the density of drilling fluid is determined before cementing according to the aftereffect of gas logging to stabilize the formation. During the actual onsite cementing construction, it is necessary to prevent leakage and other problems, ensure that the cementing quality meets the requirements, and provide a good wellbore environment for subsequent downhole operations.
Figure 1: “F” shaped fracture of shale in the North of S Basin [1]
Well DY2H adopts a three-layer wellbore structure. First, a straight pilot hole is drilled, then the open hole section is backfilled, and the horizontal well is sidetracked with a technical casing. For the first spud in, a drill bit with Ø 444.5 mm is used to a depth of 230 m, and a surface casing with Ø 339.7 mm is run into Group M to isolate the shallow water layer of upper Group T, and the surface layer can be used to install well control devices for the wellhead to ensure the safety of the casing construction. The second spud adopts a Ø 311.2 mm bit to a depth of 2090 m, and a Ø 244.5 mm technical casing is run into the upper part of the target horizon, to ensure the safety of coring in the lower long well section, and to isolate the upper N group of soft mudstone and high-pressure water injection layer that easily shrink. The pilot section of the vertical well was drilled to the upper part of the 2465 m QT formation with Ø 215.9 mm. After the open hole is completed, the cement plug is used to seal the open hole section. The sidetracking horizontal well adopts a Ø 215.9 mm borehole to sidetrack the horizontal well at 1898 m of the technical casing, with a deflection section of 626 m and a horizontal section length of 2020 m. The drilling was completed at 4576 m. A Ø 139.7 mm casing was run into the target formation, and the well was sealed and cemented at once [20].
3 Analysis of Cementing Technical Difficulties and Factors Affecting the Cementing Quality
3.1 Technical Difficulties in Sidetracking Horizontal Well Cementing
Due to the differences between the geological conditions and developed methods of sidetracking horizontal wells and conventional horizontal wells, the shale reservoir sidetracking horizontal wells are characterized by long horizontal sections and Irregular wellbore. Based on the comprehensive analysis of geological and engineering factors, the shale reservoir sidetracking horizontal wells are characterized by irregular horizontal sections where the casing is difficult to be centered, and hence, difficult to guarantee the cementing flushing displacement efficiency under complex wellbore conditions for high performance and requirements of staged volume fracturing on the cement sheath [18].
3.2 Analysis of Factors Affecting the Cementing Quality
Factors affecting the cementing quality of sidetracking horizontal wells include centrality, drilling fluid performance, cementing preflush, cement slurry, cementing technology, construction parameters, well trajectory, well diameter, etc. [14–20]. Among them, the universal factors mainly include the following aspects:
(1) Irregular well diameter and poor centering affect the flushing displacement effect. Using the real borehole conditions of wells GYYP1 and YY1H, the regularity of borehole diameter, centering of the casing, flushing displacement efficiency, etc., were analyzed. The enlargement rate of the horizontal section of Well YY1H is 3.69%, the casing is in the middle of 76%, and the simulated displacement efficiency is 95.72%. The enlargement rate of the horizontal section of GYYP1 well is 17.6%, the casing centering is only 55.3%, and the simulated displacement efficiency is 79.92%. Low centricity, the low flow rate at the narrow side during displacement, and poor flushing displacement effect, affect cementing quality.
(2) Reducing the construction discharge and affecting the flushing displacement effect. As the horizontal section is long and the formation pressure bearing capacity is low, to ensure construction safety and pressure control, leakage prevention construction is adopted, which affects the displacement of flushing. Take Well GYYP1 as an example, the formation pressure is only 2.0 MPa, and the low displacement (0.8–1.2 m3/min) construction is adopted, resulting in the drilling fluid being retained at the narrow side. There is an obvious mixing section at 2700–3500 m, which affects the cementing quality.
(3) The high density of the drilling fluid and the difficulty with designing the flushing spacer affect the flushing displacement effect. Take Well YY1H as an example, the density of the drilling fluid is 1.60 g/cm3, and the density of the low-density cement slurry is 1.60 g/cm3. The density of the flushing isolation fluid does not meet gradient design, which reduces the effect of gravity on the displacement process, and makes it difficult to ensure the cementing quality.
4 Cementing Construction Matching Technology of Sidetracking Horizontal Well
Given the technical difficulties and factors affecting the cementing quality of Group Q sidetracking horizontal wells and relying on the superior resources of the National Engineering Laboratory of Oil and Gas Wells, the numerical simulation optimization of the scheme was focused and the technologies such as centralizer, high-efficiency preflush, and ductile cement slurry were improved.
4.1 Centralizer Casing Centering Technical Measures
As obtained from the electric logging diameter data of Well DY2H, the average diameter of the open hole section is 273.69 mm, and the diameter expansion rate is 26.77%; The average diameter of the deflecting section is 289.62 mm, and the diameter expansion rate is 34.15%; The average diameter of the horizontal section is 267.40 mm, and the diameter expansion rate is 23.85%. Between 0–1790 m, there was one integrated elastic centralizer for every four casings; Each 1790–4576 m casing has an integrated elastic centralizer, as shown in Fig. 2. The simulated average centering degree of the whole well is more than 65%, which effectively reduces the occurrence of wall sticking in the bigbellied well section, improves the displacement efficiency of the narrow edge drilling fluid, and effectively solves the problems of large diameter expansion rate and poor centering degree of the good well casing.
Figure 2: Integrated elastic centralizer
4.2 High-Efficiency Oil Displacement Preflush System
To improve the flushing displacement effect of the oil-based drilling fluid, the high-efficiency oil displacement preflush should have good compatibility and low critical turbulent return velocity. Given this feature, a new composite suspension agent has been developed. At the same time, to improve the ability to facilitate emulsification and water-wetting inversion of oil contamination, silicone surfactants with low surface tension, high-temperature resistance, and salt resistance were developed, while surfactants with different hydrophilic-lipophilic balance (HLB) values were synthesized. To improve the displacement efficiency of the narrow-edge drilling fluid, the performance of drilling fluid, pre-cementing fluid, cement slurry, and cementing operation parameters were optimized. The displacement efficiency of the numerical simulation was 94.2%, and the displacement efficiency of the 2500–3400 m narrow edge was 61.72%. Technical scheme VIII was determined and optimized as presented in Table 1.
Indoor evaluation (see Fig. 3) shows that the flushing effect, turbulence, and compatibility of the high-efficiency oil displacement front fluid system can meet the cementing requirements of the long horizontal section of sidetracking. the matching of appropriate displacement and reasonable displacement flow pattern can effectively avoid the problems of annular mixing and channeling.
Figure 3: Laboratory evaluation of the high-efficiency oil displacement preflush
4.3 Tough Cement Slurry Technology
As obtained from the field gas logging data of Well DY2H, the maximum total hydrocarbon content measured by the 2145–4576 m drill is 10.69%–53.29%, and the aftereffect of drilling and shut-in is obvious. The shut-in is for 49 h, the maximum total hydrocarbon content is 70%, and it is difficult to stabilize the gas reservoir. Given the characteristics of huge difficulty in long-term pressure stability of the horizontal section of the sidetracking horizontal well and the high requirements of fracturing on the mechanical properties of cement stone, the performance of the cement slurry is optimized, and channeling prevention and toughening technologies are applied. Filling the void between cement particles with an anti-gas channeling agent to form film and aggregate and cross-link, reduces the permeability of cement stone, and improves the anti-gas channeling effect of horizontal wells in shale reservoirs. Through the research and development of key additives such as film-forming anti-channeling agent and epoxy resin toughening agent, a new type of anti-channeling toughness cement slurry with “high strength, high channeling resistance, high durability, low permeability, low elastic modulus, and low water loss” has been formed. This solves the bottleneck of increasing toughness and reducing the strength of cement stone, reduces the elastic modulus of cement stone, slows down the damage of skeleton support structure, and improves the impact resistance of cement stone (see Figs. 4 and 5). The elastic modulus can reach 3.9 GPa (70°C × 7 d), and compressive strength 34.5 MPa (70°C × 4 h). Compared with conventional cement slurry, the elastic modulus is reduced by 44.5%, and the strain is increased by 22.8%. In combination with wellhead pressure control technology, the fluid invasion caused by cementing weight loss is avoided, and the mechanical damage to the cement sheath caused by the fracturing operation is improved [4–8], effectively ensuring the wellbore sealing integrity of the cement sheath in the subsequent operation of downhole fracturing.
Figure 4: Curve of stress variation of raw cement
Figure 5: Curve of stress variation of tough cement
The horizontal section of Well DY2H is 2020 m long. Relying on the concept “major completion”, the four key links of smooth wellbore trajectory, good wellbore regularity, good drilling fluid performance, and effective cementing scheme are well grasped. Through the numerical simulation and optimization of the scheme, the technical schemes of cementing pre-fluid and the performance of cement slurry are optimized. The horizontal section is an integrated elastic centralizer, and the pre-fluid is injected on site. The mud pump injects 40 m3 of low-viscosity drilling fluid with a density of 1.63 g/cm3. The cementing pump truck injects 7 m3 of diesel oil in turn, 20 m3 of YJC flushing fluid with a density of 1.55 g/cm3, 20 m3 of YJC flushing fluid with a density of 1.60 g/cm3, and 6 m3 of DOS flushing fluid with a density of 1.60 g/cm3, with an average displacement of 2.0 m3/min. Three cement trucks inject cement slurry into Taihang low density +20% DHL high temperature resistant cement admixture cement slurry 52.18 m3, density 1.63–1.67 g/cm3, displacement 2.0–2.2 m3/min; Then injection of Dalian G grade 1.90 + 25% quartz sand + 1.5% DCR + 4% toughening agent + 1.5% expansion agent + 1.5% high temperature retarder + 20% DHL high temperature resistant cement admixture cement slurry of 54.55 m3, density of 1.88–1.92 g/cm3, and discharge of 2.0–2.2 m3/min was carried out. Finally, injection of Dalian G grade 1.90% + 25% quartz sand + 1.5% DCR + 4% toughening agent + 1.5% expansion agent + 20% DHL high-temperature resistant cement admixture cement slurry of 54.55 m3, density of 1.88–1.92 g/cm3, and displacement 2.0–2.2 m3/min was carried out. Then the rubber plug is pressed within two minutes and an injection of 1.0 m3 of clean water. During the displacement operation, 44.29 m3 of clean water is replaced by a fracturing truck and pump truck. The pump is started stably, and the starting speed is slow to avoid the instability of shale caused by pressure fluctuation during the construction. The displacement can be appropriately increased to 2.0–2.2 m3/min before the pressure is raised. When the pressure rises, the displacement can be slowly reduced to 2.0–1.5 m3/min. The remaining 5 m3 is calculated by one vehicle and completed within five minutes. Attention is paid to the pressure in the later stage of replacement, to properly reduce the displacement, and ensure leak-proof construction. By improving the displacement of injection and displacement construction of the DY2H well by 2.0–2.3 m3/min and adding back pressure at the wellhead by 3.0 MPa, the quality rate of cementing in the horizontal section is 97.8%, and the quality rate of cementing in the horizontal section is 75.6% and 34% higher than that of the adjacent Well DY1H and Well D-YP1, respectively (see Table 2).
(1) The organic-rich dark shale of Group Q in the north of S Basin is relatively developed and widely distributed, with a high overall maturity. The Q2–Q1 section is oil-bearing and has huge potential for oil and gas resources development. In the early stage of exploration and development, the pilot hole is drilled straight first, then the open hole section is backfilled, and horizontal wells are sidetracked by window drilling.
(2) Well DY2H is a pre-exploration well in the North of S Basin. The exploration target layer is continental pure shale. The formation is easy to hydrate and spall. It is difficult to center the casing in the horizontal section of an irregular wellbore, and it is difficult to guarantee the replacement efficiency of cementing flushing under complex wellbore conditions. Therefore, the performance and requirements of segmented volume fracturing on the water mud ring are high. Relying on the superior resources of the National Engineering Laboratory of Oil and Gas Wells, using displacement efficiency system software for numerical simulation, measures such as optimizing cementing preflush and cementing construction parameters, and running an integrated elastic centralizer in the horizontal section have improved the flushing displacement efficiency and greatly improved the cementing quality. The quality rate of cementing in the water level section of Well DY2H is 97.8%, which is more than 34% higher than that of adjacent wells.
(3) The matching cementing technology for shale oil sidetracking horizontal wells in Group Q in the North of S Basin provides a reference for future research and application of relevant measures. It is suggested to strengthen the promotion and application in similar blocks or wells.
Funding Statement: This study was funded by the CNPC Science and Technology Department Project (2021ZZ10-03).
Conflicts of Interest: The authors declare that they have no conflicts of interest to report regarding the present study.
References
1. Sun, L. D., Liu, H., He, W. Y., Li, G. X., Zhang, S. C. et al. (2021). An analysis of major scientific problems and research paths of Gulong shale oil in Daqing Oilfield. Petroleum Exploration and Development, 48(3), 453–463. https://doi.org/10.1016/S1876-3804(21)60043-5 [Google Scholar] [CrossRef]
2. Adams, N. J., Mitchell, R. F., Eustes, A. W., Sampaio, J. H., Antonio, A. O. (2017). A causation investigation for observed casing failures occurring during fracturing operations. Society of Petroleum Engineers, SPE-184868-MS. https://doi.org/10.2118/184868-MS [Google Scholar] [CrossRef]
3. Albawi, A. (2013). Inflfluence of thermal cycling on cement sheath integrity (M.S. Thesis). Norwegian University of Science and Technology, Trondheim, Norway. [Google Scholar]
4. He, W. Y., Meng, Q. A., Zhang, J. Y. (2021). Controlling factors and their classification-evaluation of Gulong shale oil enrichment in Songliao Basin. Petroleum Geology & Oilfield Development in Daqing, 40(5), 1–12. https://doi.org/10.19597/J.ISSN.1000-3754.202107045 [Google Scholar] [CrossRef]
5. Atkinson, G. M., Eaton, D. W., Igonin, N. (2020). Developments in understanding seismicity triggered by hydraulic fracturing. Nature Reviews Earth & Environment, 1(5), 264–277. https://doi.org/10.1038/s43017-020-0049-7 [Google Scholar] [CrossRef]
6. Qi, Y., Chen, S. Y., Li, H., Tian, Y. D., Li, B. et al. (2022). Mechanismf of horizontal wellbore instability for Gulong shale in Songliao Basin. Petroleum Geology & Oilfield Development in Daqing, 41(3), 147–155. https://doi.org/10.19597/J.ISSN.1000-3754.202111077 [Google Scholar] [CrossRef]
7. Xi, Y., Li, J., Zha, C. Q., Guo, B. Y., Liu, G. H. (2019). A new investigation on casing shear deformation during multistage fracturing in shale gas wells based on microseism data and calliper surveys. Journal of Petroleum Science and Engineering, 180, 1034–1045. https://doi.org/10.1016/j.petrol.2019.05.079 [Google Scholar] [CrossRef]
8. Yang, Z. G., Li, J. J., Yang, X. T., Jiang, T., He, C. J. et al. (2020). Technical difficulties and countermeasures of the horizontal well cementing in the shale oil reservoirs. Petroleum Geology & Oilfield Development in Daqing, 39(3), 155–162. https://doi.org/10.19597/J.ISSN.1000-3754.202004049 [Google Scholar] [CrossRef]
9. Saint-Marc, J., Garnier, A., Bois, A. (2008). Initial state of stress: The key to achieving long-term cement-sheath integrity. SPE Annual Technical Conference and Exhibition, SPE116651, Denver, Colorado. https://doi.org/10.2118/116651-MS [Google Scholar] [CrossRef]
10. Goodwin, K. J., Crook, R. J. (1992). Cement sheath stress failure. SPE Drilling Engineering, 7(4), 291–296. https://doi.org/10.2118/20453-PA [Google Scholar] [CrossRef]
11. Zhao, C., Li, J., Liu, G., Zhang, X. (2020). Analysis of well stress with the effect of natural fracture nearby wellbore during hydraulic fracturing in shale gas wells. Journal of Petroleum Science and Engineering, 188, 106885. https://doi.org/10.1016/j.petrol.2019.106885 [Google Scholar] [CrossRef]
12. Restrepo, M. M., Teodoriu, C., Salehi, S., Wu, X. (2020). A novel way to look at the cement sheath integrity by introducing the existence of empty spaces inside of the cement (voids). Journal of Natural Gas Science and Engineering, 77, 103274. https://doi.org/10.1016/j.jngse.2020.103274 [Google Scholar] [CrossRef]
13. Tan, C. Q., Guo, S. L., Huang, J. J. (2023). An investigation into the effects of oil-well cement expansion agent on the integrity of cement sheath. Fluid Dynamics & Materials Processing, 19(5), 1291–1300. https://doi.org/10.32604/fdmp.2022.022233 [Google Scholar] [CrossRef]
14. Wu, Z. Q., Wu, Y., Xie, R. J., Yang, J., Liu, S. J. et al. (2023). Nalysis of the microstructure of a failed cement sheath subjected to complex temperature and pressure conditions. Fluid Dynamics & Materials Processing, 19(2), 399–406. https://doi.org/10.32604/fdmp.2022.020402 [Google Scholar] [CrossRef]
15. Zou, P., Huang, Z., Tong, Y., Tan, L., Li, R. et al. (2022). Experimental evaluation of the mechanical properties of cement sheath under high-temperature conditions. Fluid Dynamics & Materials Processing, 18(3), 689–699. https://doi.org/10.32604/fdmp.2022.019470 [Google Scholar] [CrossRef]
16. Li, H., Yang, Y. X., Tian, Y. D. (2020). Application of floating casing running technology in YH1-6 of shale gas horizontal well in ZJ oilfield. Xinjiang Oil & Gasi, 16(1), 16–20. [Google Scholar]
17. Albawi, A., de Andrade, J., Torsæter, M., Opedal, N., Stroisz, A. et al. (2014). Experimental set-up for testing cement sheath integrity in Arctic wells. OTC Arctic Technology Conference, OTC-24587-MS. https://doi.org/10.4043/24587-MS [Google Scholar] [CrossRef]
18. Boukhelifa, L., Moroni, N., James, S. G., Le Roy-Delage, S., Thiercelin, M. J. et al. (2004). Evaluation of cement systems for Oil and Gas well zonal isolation in a full-scale annular geometry. IADC/SPE Drilling Conference, Dallas, Texas, USA, IADC/SPE 87195. https://doi.org/10.2118/87195-PA [Google Scholar] [CrossRef]
19. Shenold, C., Teodoriu, C. (2016). Development of a structured workflow for enhanced well cement integrity: Lessons learned and the way ahead. Journal of Natural Gas Science and Engineering, 36, 824–836. https://doi.org/10.1016/j.jngse.2016.10.042 [Google Scholar] [CrossRef]
20. Li, J., Xi, Y., Tao, Q., Li, Y., Qu, G. (2020). Experimental investigation and numerical simulation of the emergence and development of micro-annulus in shale gas wells subjected to multistage fracturing. Journal of Natural Gas Science and Engineering, 78, 103314. https://doi.org/10.1016/j.jngse.2020.103314 [Google Scholar] [CrossRef]
Cite This Article
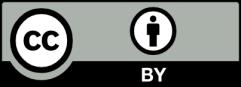
This work is licensed under a Creative Commons Attribution 4.0 International License , which permits unrestricted use, distribution, and reproduction in any medium, provided the original work is properly cited.