Open Access
ARTICLE
New Nano Polymer Materials for Composite Exterior-Wall Coatings
Faculty of Urban Construction, Eastern Liaoning University, Dandong, 118001, China
* Corresponding Author: Yue Yu. Email:
Fluid Dynamics & Materials Processing 2023, 19(10), 2681-2694. https://doi.org/10.32604/fdmp.2023.028250
Received 07 December 2022; Accepted 20 February 2023; Issue published 25 June 2023
Abstract
A triethylenetetramine epoxy mixture was synthesized through the reaction of a low-molecular-weight liquid epoxy resin with triethylenetetramine (TETA). Then triethyltetramine (TETA) was injected dropwise into a propylene glycol methyl ether (PM) solution for chain extension reaction. A hydrophilic and flexible polyether segment was introduced into the hardener molecule. The effects of TETA/DGEPG, reaction temperature and reaction time on the epoxy conversion of polyethylene glycol diglycidyl ether (DGEPG) were studied. In addition, several alternate strategies to add epoxy resin to the high-speed dispersion machine and synthesize MEA DGEBA adduct (without catalyst and with bisphenol A diglycidyl ether epoxy resin) were compared. It was found that the higher the molecular weight of triethylenetetramine, the longer the chain segment of the surface active molecule. When the equivalence ratio of amine hydrogen and epoxy group is low, the stability of lotion is good. When the ratio of amine hydrogen to epoxy group is large, the content of triethylenetetramine is small. The main objective of this study is the provision of new data and knowledge for the development of new materials in the coating and electronic industry.Keywords
Epoxy resin has excellent physical and chemical properties and is widely used in coating, adhesive, composite materials, and many other fields. Traditional epoxy coatings are insoluble in water. A large number of organic solvents need to be added for dilution during construction, which will harm the ecological environment and the health of construction workers. Therefore, water-based epoxy resins with low volatile organic compound content, high efficiency, energy saving and environmental protection are attracting more and more attention from the market [1]. Since epoxy resins are insoluble in water by themselves, they cannot be dispersed directly in water and must be water-based by physical or chemical means [2]. The waterborne method of epoxy resin can be divided into additive emulsifiers, curing agent emulsification, and chemical modification. Additional emulsifier methods can be divided into mechanical and reverse rotation methods [3]. According to the type of emulsifier, they can be divided into anionic type, cationic type and nonionic type 3. The curing agent emulsification method refers to the water-based epoxy curing agent emulsifying epoxy resin to make it waterborne . The curing agents can be divided into the anionic curing agent emulsification method, cationic agent emulsification method, and nonionic agent emulsification method. The chemical modification method has hydrophilic and self-emulsifying functions [4]. It can be dispersed in water. Self-emulsifying water-based epoxy resins can be divided into anionic, cationic and nonionic types according to surface-active hydrophilic groups introduced [5].
2 Additional Nonionic Emulsifier Method
2.1 Mechanical Emulsification of Epoxy Resin with the Addition of a Nonionic Emulsifier
The mechanical emulsification with additional non-ionic emulsifier refers to the addition of emulsifier to the epoxy resin under heating and high-speed mechanical stirring, so that the water-soluble epoxy resin is dispersed in the water in the form of particles or droplets to form lotion. The advantage of this method is that it is easy to handle. However, the particle size of epoxy resin dispersion phase in lotion is large, the particle shape is irregular, the particle size distribution is comprehensive, and the stability is poor. The typical surfactants are sorbitol anhydride polyformaldehyde sorbitol fatty acid ester series and many long-chain alkylphenol polyethylene glycol. Hydrophilic and lipophilic groups fixed in substances with surfactant that can significantly reduce the surface tension of epoxy resin solution can be oriented on the surface of the solution. It has a positive effect on the improvement of epoxy conversion rate. Generally, the appropriate amount of this surface activity is large, easy to precipitate and adhere to the dry surface of the paint film, affecting the corrosion resistance of the paint film. Some scholars will add epoxy resin into high-speed dispersion machine, add surfactant, defoamer and 2-butoxyethanol, and completely decompose. Preheat the water to 40°C~45°C and slowly add it into the resin solution under high shear force. After adding 60%~70% water, the dispersion rate will be reduced. Slowly add the remaining water to form a stable lotion. Generally, the appropriate amount of this kind of surface activity is large, easy to precipitate and adhere to the dry surface of the paint film, affecting the corrosion resistance of the paint film. Some scholars will add epoxy resin into high-speed dispersion machine, add surfactant, defoamer and 2-butoxyethanol, and completely decompose. Preheat the water to 40~45°C and slowly add it into the resin solution under high shear force. After adding 60%~70% water, the dispersion rate will be reduced. Slowly add the remaining water to form a stable lotion [6].
2.2 Polyethylene Glycol Preparation Emulsifier Emulsion Epoxy Resin by the Reverse Rotation Method
Polyethylene glycol has the characteristics of long-chain helical conformation, environmental friendliness and good compatibility with epoxy resins. Usually, polyethylene glycol is introduced into the epoxy resin chain segment to make a nonionic emulsifier, which emulsifies the epoxy resin and turns it in reverse, from oil-in-water to oil-in-water, to achieve water-based. This process, on the one hand, introduces hydrophilic groups. On the other hand, it retains the epoxy structure, enhances compatibility, and makes emulsification easier. The emulsification diagram is shown in Fig. 1 below.
Figure 1: Preparation of polyethylene glycol emulsifier emulsion epoxy resin by the reverse rotation method
This emulsifier can be divided into the following two types: First, the hydroxyl group on polyethylene glycol reacts directly with the epoxy group on the epoxy resin, and the hydrophilic chain segment of polyethylene glycol is connected to the epoxy resin to form the emulsifier. Second, polyethylene glycol reacts with other functional groups, then grafts epoxy resin to comprise an emulsifier.
2.2.1 Polyethylene Glycol Reacts Directly with Epoxy Resin
Polyethylene glycol was directly reacted with epoxy resin, and the hydrophilic chain segment was used to synthesize emulsifier and emulsifier epoxy resin by the hydroxyl group of polyethylene glycol and epoxy resin. The hydroxyl and epoxide groups barely react at room temperature and need heating and a catalyst. The reaction diagram is shown in Fig. 2 below.
Figure 2: The process of direct reaction of PEG, BPA and ECH
2.2.2 Polyethylene Glycol Reacts with Other Functional Groups and Then Grafts Epoxy Resin
The reaction of polyethylene glycol with epoxy resin is difficult to control under a strong corrosive Lewis acid catalyst. The added motivation should be diluted with a large amount of solvent and added slowly. Otherwise, it is easy to gel and not easy for large-scale industrial production. The highly corrosive Lewis’s acid can also adversely affect reaction equipment and operation. However, the catalytic efficiency of peroxide and amine catalysts is low. Therefore, it has been reported that other methods have been used to prepare emulsifiers for nonionic epoxy emulsions. Some scholars used bisphenol A diglyceryl ether epoxy resin (DGEBA) to expand the chain reaction on ethanolamine (MEA) to synthesize MEA-dgeba addition under the condition of no catalyst. The appropriate technological conditions are n(MEA):n(DGEBA) = 2:1. The reaction temperature was 55°C, and the reaction time was 4 h. MEA-DGEBA adjunct was used for the chain extension reaction of PEGGE. The nonionic chemical-modified aqueous epoxy emulsifier Pepegge-MEADGEBA addition was synthesized. The new emulsifier can disperse nicely in water and has good film performance.
2.3 Nonionic Curing Agent Emulsifies Epoxy Resin
Type 1 water-based epoxy resin system, composed of low relative molecular weight liquid epoxy resin (usually the epoxy equivalent of 175~240) and water-based epoxy curing agent. Generally, low molecular weight epoxy resins are not pre-emulsified. Still, they are emulsified by a curing agent, which requires the curing agent to have the dual functions of curing and emulsifying. Studies on this aspect are relatively early. Most mature technologies are ionic salt-modified aliphatic amine epoxy curing agents, while nonionic emulsifying curing agents are relatively few. Some scholars reacted polyethylene glycol diglyceryl ether with octa decamines to synthesize an epoxy group with two ends. Intermediate nitrogen atoms are attached to long-chain alkyl admixtures. A latent nonionic self-emulsifying water-based epoxy curing agent was prepared by sealing the enamine by reacting the secondary amine with the epoxide group. The curing agent has a good emulsifying effect on liquid epoxy resin. The prepared waterborne coatings have excellent properties.
Nonionic curing agent emulsified liquid epoxy resin film is relatively dense, has high hardness, high crosslinking density, and good solvent resistance. Because the liquid epoxy resin’s relative molecular weight is low, the functional groups’ content is high, so the activation period of this system is generally short, and the high gloss duration is scarce [7]. It is necessary to prolong the activation period by reducing the active hydrogen of the curing agent. In addition, the curing agent emulsifies the liquid epoxy resin generally has a larger viscosity. It must be thoroughly mixed evenly and is not as easy to construct as the double water system.
3 Molecular Dynamics Simulation of Epoxy Resin Coatings
3.1 Coefficient of Thermal Expansion
The coefficient of thermal expansion (CTE) calculates the internal stress caused by thermal expansion inside a material. It is an important index to measure the thermal stability of materials [8]. The change rate of the book with temperature under different states can be obtained by fitting the volume and temperature data before and after the glass transition (Fig. 3).
Figure 3: CTE fitting curve
The specific calculation formula of CTE is
β=1V0(∂V∂T)pβ=1V0(∂V∂T)p (1)
ββ is the coefficient of thermal expansion. V0V0 is the volume of the initial system. p=1.01325×105 pap=1.01325×105 pa is one standard atmosphere.
3.2 Static Mechanical Properties
The static constant strain method is used to calculate the mechanical properties of the crosslinked system. A tiny strain is applied to the crosslinked epoxy system that has reached equilibrium. The stiffness matrix CijCij can be obtained by the response of the system to strain:
Cij=[λ+2μλλ0000λ+2μλ00000λ+2μ00v000μ000000μ000000μ] (2)
λ and μ are elastic constants. It can be obtained from the stiffness matrix
{λ=16(C12+C13+C21+C23+C31+C32)μ=13(C44+C55+C66) (3)
According to λ and μ , mechanical property parameters of the system such as volume modulus K , shear modulus G and Young’s modulus E can be obtained
{K=λ+23μG=μK=μ3λ+2μλ+μ (4)
3.3 Molecular Chain Movement Analysis
Mean azimuth shift (MSD) is used to characterize the system’s motility of molecular chain segments. Its definition is
SMSD=13NN−1∑i=0(|Ri(t)−Ri(0)|2) (5)
SMSD stands for mean azimuth shift. Ri(t) and Ri(0) represent the displacement vector of any atom i in the system at time t and at the beginning, respectively. The trajectory files of each ratio model after annealing simulation at room temperature were extracted, and their MSD values were calculated (Fig. 4).
Figure 4: MSD curves of systems with different molar ratios
Free volume is a vital microstructure parameter of materials. It is an important index affecting the crosslinked system’s glass transition temperature and mechanical properties. Since the volume of different polymer systems is different, the free volume ratio (FFV) is introduced to represent the relative size of free volume. Its expression is
RFFV=VfV0+Vf×100% (6)
RFFV is the free volume proportion. V0 and Vf represent the volume occupied by the molecule and the free volume, respectively.
Epoxy 618(E-51): Epoxy value 0.51, Shanghai Resin Factory. Triethylenetetraamine: Chemical pure, Shanghai Chemical Reagent Company (Shanghai, China). TETA: Chemical pure, Shanghai Dyeing and Chemical Factory No. 14. Butylepoxy-propyl ether (BGE): Chemical pure, Shanghai Chemical Reagent Company (Shanghai, China). Glacial acetic acid (HAc): Analytically pure, Shanghai Chemical Reagent Company (Shanghai, China).
4.2.1 Centrifugal Stability of the Emulsion
In this paper, a certain amount of emulsion was loaded into the matching test tube of type 80-2B bench centrifuge, and a centrifuge test was carried out. Control a certain speed and observe the emulsion stratification and demulsification phenomenon. Record the corresponding time.
4.2.2 Determination of Epoxy Value and Emulsion Viscosity
The epoxy value was determined by the acetone hydrochloride method. An NDJ-79 rotary viscometer measured the thickness of the emulsion.
According to GB1730-79, the film hardness was measured by a QTX-I film elasticity tester, namely the pendulum rod hardness tester [9]. According to GB1727-79, “coating general preparation method” for bottom plate treatment and coating preparation. The hardness of the film was measured continuously for 7 days and observed. Obtain the hardness of the film X: X = t/t0. Where: t is the average swing time of the pendulum rod on the film from 6° to 3°. t0 is the average swing time of the pendulum rod on the standard glass plate from 6° to 3°.
4.3 Synthesis of Triethylenetetramine (TETA)
1) Reaction process of triethylenetetramine and epoxy resin
Epoxy-618 and triethylenetetramine were reacted in the presence of a catalyst at 90°C~110°C. The epoxy equivalent was measured every 1 h. The reaction stops when the epoxy equivalent reaches the theoretical value. Both temperature and stirring speed should be controlled throughout the whole reaction process. Especially in the initial stage of the reaction, the temperature will rise significantly due to the release of a large amount of heat. Cooling should be managed to avoid gelation.
2) Synthesis of epoxy-polyamine addition
The above product was taken and reacted with 2 equivalent epoxy-618 and a specific equivalent of triethylenetetramine at 60°C~80°C for 3~5 h. After the reaction, add water and dilute to 80% solid content. Continue stirring for 0.5 h.
3) End sealing process
Control reaction temperature of 60°C. A certain amount of butyl epoxy-propyl ether (BGE) was added with a dropper funnel. After about 0.5 h, the reaction was continued at 60°C for 1 h.
4) Salt formation
Add acetic acid slowly at room temperature. The salt formation rate is 20%. As a result of the exothermic reaction, the temperature will rise and then gradually decrease. Wait until the temperature drops to 50°C before applying heat [10]. Control the reaction temperature at 60°C. The reaction was maintained for 1 h and then diluted to about 50.0% solid content with water at 60°C. Continue stirring for 0.5 h and stop heating and stirring.
4.4 Preparation of Type 1 Waterborne Epoxy Curable Emulsion Coating
In this article, triethylenetetramine (TETA) is poured into a beaker. Add epoxy 618 slowly at high speed. Continue stirring for 5 min after adding. Type 1 waterborne epoxy curable emulsion coating was prepared. The equivalent ratio of amine hydrogen to the epoxy group is 1:1.
5.1.1 Influence of Molecular Weight of Triethylenetetramine in Curing Agent on Centrifugal Stability of the Emulsion
In this paper, the emulsion prepared by triethylenetetramine and epoxy resin was tested for centrifugal strength. The rotational speed was 1000 r/min.Temperature set in this paper is 60°C, the results are shown in Table 1.
It can be seen from Table 1 that the higher the molecular weight of triethylenetetramine, the better the centrifugal stability of the emulsion prepared. The higher the molecular weight of the triethylenetetramine, the longer the chain segment of the surface-active molecule. When mixing with epoxy resin, if the equivalent ratio of maintenance curing agent and epoxy resin is the same (1:1), the mass ratio of triethylenetetramine in the hybrid system is higher [11]. The emulsification effect is vital to form a stable oil-in-water emulsion, and the stability of the emulsion is improved.
5.1.2 Influence of Equivalent Ratio of Amine Hydrogen to the Epoxy Group on Emulsion Stability during Synthesis of Triethylenetetramine
In this paper, triethylenetetramine with a molecular weight of 1000 was synthesized with different amine hydrogen and epoxy equivalent ratios. The stability of the epoxy emulsion prepared by these curing agents is shown in Table 2.
It can be seen from Table 2 that if the equivalent ratio of amine hydrogen to the epoxy group is low, the emulsion has good stability. There are six active hydrogens in triethylenetetramine. Epoxy resins contain two epoxy groups. When the equivalent ratio of amine hydrogen to the epoxy group is 6:1, the molar ratio of triethylenetetramine to epoxy resin is 2:1. An amount of the additive containing only an epoxy resin chain segment with an amine end group is formed. Therefore, it is not only the epoxy resin curing agent but also the emulsifier of epoxy resin. When the equivalent ratio of amine hydrogen to the epoxy group is higher than 6:1, the admixture formed contains partial excess triethylenetetramine. The higher the yield ratio, the lower the amine hydrogen yield of the resulting admixture. If the equivalent ratio of epoxy resin and curing agent is the same, the mass ratio of the curing agent is lower. The amount of triethylenetetramine in the hybrid system is correspondingly less. The emulsification is weak, so it is not enough to form a stable emulsion.
5.2 Curing and Film Forming of Type 1 Water-Based Epoxy System
Water-based epoxy coating is a kind of emulsion coating. Still, its film-forming mechanism is not only very different from that of general polymer emulsion coating but also very different from the solvent-based epoxy system [12]. The film-forming process of polymer emulsion coatings is either physical or physical-chemical. The polymer particles in the polymer emulsion have a low glass transition temperature and form a compact packed structure after the evaporation of water, which aggregates and creates a film under the action of capillary pressure. Epoxy resin coating is a reactive two-component coating whose film-forming process includes both physical and chemical processes.
The water-based epoxy system is a multiphase system in which the epoxy resin is the dispersing phase, and the amine curing agent is the continuous phase [13]. Therefore, the curing reaction occurs at the interface, and the curing agent gradually diffuses into the dispersing phase of the epoxy resin to further the epoxy curing. Assuming that the particle size of a dispersed phase in the epoxy emulsion is 500 nm, the density is 1.16 g/mL, the molecular weight of epoxy is 1000, and ignoring its dissolution in water, it can be calculated that each epoxy particle contains about 4.6 × 107 molecules. Therefore, the curing of a water-based epoxy system is controlled by a diffusion process, which is a complex process compared with a solvent-based epoxy system. Curing time is long and less complete and incomplete. The degree of solidification depends on the following factors: (1) The particle size of the dispersed phase. (2) The viscosity and glass transition temperature of dispersing phase epoxy particles. The dispersing phase resin of Type 1 water-based epoxy is in a liquid sta. Still, with the progress of the curing reaction, the viscosity of the surface layer of epoxy particles continues to rise and even becomes. Then the glass transition temperature will also gradually increase.
At this time, the epoxy particles are still liquid, the glass transition temperature is still lower than room temperature, the compatibility of epoxy and curing agent is good, and the homogeneous transparent and glossy film can be formed [14]. On the contrary, if it is used for too long, the glass transition temperature of epoxy particles will rise, and incomplete homogeneous film may be formed, with low transparency and gloss, or even film formation.
5.2.1 Influence of Molecular Weight of Triethylenetetramine on Curing Properties of the Water-Based Epoxy System
Fig. 5 shows the viscosity curve over time of the aqueous epoxy system obtained by mixing triethylenetetramine with epoxy resin. The equivalent ratio of amine-hydrogen/epoxy was 6.4:1. It can be seen from Fig. 5 that the higher the molecular weight of triethylenetetramine, the faster the curing rate of the emulsion [15]. The larger the molecular weight of triethylenetetramine is, the longer the chain segment with surface activity is, and the larger the proportion is in the hybrid system. After the curing reaction occurs on the surface of the epoxy resin dispersed phase, the curing agent is conducive to the diffusion of epoxy latex particles. The corresponding curing rate also increases, which shows that the system’s viscosity rises rapidly on the macro level.
Figure 5: Effect of relative molecular weight of triethylenetetramine on curing rate under different conditions of catalyst EP/A-Nips
5.2.2 Influence of Amine Hydrogen to Epoxy Equivalent Ratio on the Curing Rate of the Water-Based Epoxy System
Triethylenetetraamine was synthesized with the equivalent ratio of amine hydrogen to epoxide group of 6.4: 1,8: 1,10 :1 and the molecular weight of triethylenetetramine of 1000. The viscosity curve of the curing system prepared with epoxy resin over time is shown in Fig. 6. Fig. 6a is 1:1; Fig. 6b shows 6.4:1; Fig. 6c shows 8:1; Fig. 6d shows 10:1.
Figure 6: Effect of the molar ratio of amine hydrogen to epoxy group on curing rate at different temperatures and SCR conditions
Under the same conditions, the higher the equivalent ratio of amine hydrogen to the epoxy group, the slower the curing rate of emulsion and the longer the curing time. When the equivalent of amine hydrogen and epoxy group is large, there are polyamine epoxy admixtures without triethylenetetramine chain segments and some free polyamines. At the same time, the chain segments with surface activity in the emulsion account for a small proportion, and the emulsification is weak, resulting in a larger latex particle size. The curing agent needs a longer time to spread into the epoxy latex particle, so the curing rate of the emulsion is slower [16]. At the same time, the free polyamines are mainly dispersed in the aqueous phase, incompatible with the epoxy-dispersed degree. First, it needs to crosslink the link curing reaction with the epoxy resin through the “film” coated on the surface of the epoxy latex particle, so the diffusion rate to the dispersed phase is slow.
5.3.1 Influence of Molecular Weight of Triethylenetetramine on Film Hardness
Fig. 7 shows the hardness curve of the aqueous epoxy system prepared when the molecular weight of triethylenetetramine is 1000 and 4000, and the equivalent ratio of amine hydrogen to epoxy is 6.4:1.
Figure 7: Effect of the relative molecular weight of triethylenetetramine on hardness under four conditions
It can be seen from Fig. 7 that R2, R2adj and R2pred refer to the molecular weight of different triethylenetetramine structures, and the three parameters have a greater impact on the molecular weight of triethylenetetraaniline. After drying, the membrane contains more chain segments with surface activity. The smaller the hardness of the film [17]. In other words, the content of emulsifier is relatively high. Because it plays an internal plasticizing role in the system, the hardness of the film is low. In addition, if the content of emulsifier is too high, the film will quickly absorb water from the air, thus reducing the hardness of the film.
5.3.2 Influence of Equivalent Ratio of Amine Hydrogen to the Epoxy Group on Film Hardness
Fig. 8 shows the hardness curve of the aqueous epoxy system prepared when the equivalent ratio of amine hydrogen to epoxy is 6.4:1, 8:1, and 10:1.
Figure 8: Influence of amine hydrogen to epoxy equivalent ratio on the hardness cross-linking density
It can be seen from Fig. 8 that when the equivalent ratio of amine hydrogen to the epoxy group is small, the curing rate of the film is faster, and it can be hardened in a short time [18]. The hardness of the system is higher after 7 days. It can reach more than 0.6. At this time, the polyamine epoxy addition curing agent diffused into the latex particle at a slower rate, and the curing reaction was not complete, so the hardness was low.
The water resistance, gloss, flexibility and chemical resistance of waterborne epoxy were also preliminarily investigated. The results are shown in Table 3. Triethylenetetraamine 1000 was synthesized, and the equivalent ratio of amine hydrogen to epoxy was 6.4:1. The equal balance of curing agent and epoxy resin was 1:1.
It can be seen from Table 3 that the synthesized Type 1 water-based epoxy has good water resistance and flexibility. Because the triethylenetetramine chain segment has been combined into the curing agent molecule, the cured epoxy resin contains the triethylenetetramine chain segment, which plays a particular role in internal toughening, thus improving the brittleness of epoxy. But correspondingly, its hardness is lower than that of solvent-based epoxy. It also has a lower gloss than the solvent-based version. This indicates that the compatibility between water-based epoxy and its curing agent needs to be improved, and the acid-base resistance needs to be further enhanced.
By introducing the surface-active molecular chain segment into the amine curing agent molecule and using the method of sealing and salting, the triethylenetetramine with both curing and emulsifying effect and good compatibility can be obtained. The curing agent synthesized was used to emulsify epoxy resin. The emulsion has good stability, but its film performance is poor, and its hardness is small. The emulsion prepared with low molecular weight triethylenetetramine curing agent emulsified epoxy resin has general stability but good film performance. From this point of view, triethylenetetramine 1000 is a useful monomer. It is better to control the equivalent ratio of amine hydrogen to the epoxy group between 6.4 and 8. The proportion of trim ethylene tetramine molecular chain segment is more significant. The emulsion has better stability, and the film also has better mechanical properties. The synthesized aqueous epoxy system has good emulsion stability, film hardness, water resistance and flexibility, but its acid and alkali resistance need further improvement.
Funding Statement: This work is financially supported by a University-Level Doctoral Research Start-Up Fund in 2019.
Conflicts of Interest: The author declares that they have no conflicts of interest to report regarding the present study.
References
1. Zhang, J., Wang, D., Wang, L., Zuo, W., Ma, X. et al. (2021). Thermomechanical properties of silica-epoxy nanocomposite modified by hyperbranched polyester: A molecular dynamics simulation. High Performance Polymers, 33(10), 1153–1164. https://doi.org/10.1177/09540083211032383 [Google Scholar] [CrossRef]
2. Sahoo, S. K., Kannan, S. (2022). Investigation on curing kinetics, water diffusion kinetics and thermo-mechanical properties of functionalized castor oil based epoxy copolymers. Journal of Polymer Research, 29(7), 1–24. [Google Scholar]
3. Haridharan, N., Sundar, D., Kurrupasamy, L., Anandan, S., Liu, C. H. et al. (2022). Oil spills adsorption and cleanup by polymeric materials: A review. Polymers for Advanced Technologies, 33(5), 1353–1384. https://doi.org/10.1002/pat.5636 [Google Scholar] [CrossRef]
4. Fredi, G., Dorigato, A., Fambri, L., Pegoretti, A. (2020). Detailed experimental and theoretical investigation of the thermomechanical properties of epoxy composites containing paraffin microcapsules for thermal management. Polymer Engineering & Science, 60(6), 1202–1220. https://doi.org/10.1002/pen.25374 [Google Scholar] [CrossRef]
5. Yi, H., Hu, M., Yao, D., Lin, H., Zheng, B. (2020). Tribological and thermomechanical properties of epoxy-matrix nanocomposites containing montmorillonite nanoclay intercalated with polybutadiene-based quaternary ammonium salt. Plastics, Rubber and Composites, 49(9), 389–399. https://doi.org/10.1080/14658011.2020.1776921 [Google Scholar] [CrossRef]
6. Gouda, K., Bhowmik, S., Das, B. (2020). Synergetic effect of micro-bamboo filler and graphene nanoplatelets on thermomechanical properties of epoxy-based hybrid composite. JOM, 72(12), 4466–4476. https://doi.org/10.1007/s11837-020-04125-4 [Google Scholar] [CrossRef]
7. Li, J., Bi, Y., Zhao, B., Zu, L., Yang, Q. et al. (2022). Thermomechanical properties of epoxy resin/basalt fiber/hydrotalcite composites and influence of hydrotalcite particle size on their properties. Polymer Composites, 43(2), 955–963. https://doi.org/10.1002/pc.26425 [Google Scholar] [CrossRef]
8. Bagherzade, A., Jamshidi, M. (2020). Thermo-mechanical properties of epoxy nanocomposites incorporating amino acid and acid functionalized multi-walled carbon nanotubes. Journal of Composite Materials, 54(14), 1847–1861. https://doi.org/10.1177/0021998319886631 [Google Scholar] [CrossRef]
9. Poutrel, Q. A., Blaker, J. J., Soutis, C., Tournilhac, F., Gresil, M. (2020). Dicarboxylic acid-epoxy vitrimers: Influence of the off-stoichiometric acid content on cure reactions and thermo-mechanical properties. Polymer Chemistry, 11(33), 5327–5338. https://doi.org/10.1039/D0PY00342E [Google Scholar] [CrossRef]
10. Orselly, M., Devemy, J., Bouvet-Marchand, A., Dequidt, A., Loubat, C. et al. (2022). Molecular simulations of thermomechanical properties of epoxy-amine resins. ACS Omega, 7(34), 30040–30050. https://doi.org/10.1021/acsomega.2c03071 [Google Scholar] [PubMed] [CrossRef]
11. Babu, M. S., Velmurugan, R., Sarathi, R., Imai, T. (2021). Influence of water ageing on variation in space charge and thermo-mechanical properties of epoxy micro-nano composites. IET Science, Measurement & Technology, 15(1), 44–60. https://doi.org/10.1049/smt2.12005 [Google Scholar] [CrossRef]
12. Alsenafi, A., Bég, O. A., Ferdows, M., Bég, T. A., Kadir, A. (2021). Numerical study of nano-biofilm stagnation flow from a nonlinear stretching/shrinking surface with variable nanofluid and bioconvection transport properties. Scientific Reports, 11(1), 1–21. https://doi.org/10.1038/s41598-021-88935-9 [Google Scholar] [PubMed] [CrossRef]
13. Joy, J., George, E., Thomas, S., Anas, S. (2020). Effect of filler loading on polymer chain confinement and thermomechanical properties of epoxy/boron nitride (h-BN) nanocomposites. New Journal of Chemistry, 44(11), 4494–4503. https://doi.org/10.1039/C9NJ05834F [Google Scholar] [CrossRef]
14. Gioia, C., Colonna, M., Tagami, A., Medina, L., Sevastyanova, O. et al. (2020). Lignin-based epoxy resins: Unravelling the relationship between structure and material properties. Biomacromolecules, 21(5), 1920–1928. https://doi.org/10.1021/acs.biomac.0c00057 [Google Scholar] [PubMed] [CrossRef]
15. Shuvo, I. I. (2020). Fibre attributes and mapping the cultivar influence of different industrial cellulosic crops (cotton, hemp, flax, and canola) on textile properties. Bioresources and Bioprocessing, 7(1), 1–28. https://doi.org/10.1186/s40643-020-00339-1 [Google Scholar] [CrossRef]
16. Barba, B. J. D., Madrid, J. F., Penaloza Jr, D. P. (2020). A review of abaca fiber-reinforced polymer composites: Different modes of preparation and their applications. Journal of the Chilean Chemical Society, 65(3), 4919–4924. https://doi.org/10.4067/s0717-97072020000204919 [Google Scholar] [CrossRef]
17. Konuray, A. O., di Donato, F., Sangermano, M., Bonada Bo, J., Fernández Francos, X. et al. (2020). Dual-curable stereolithography resins for superior thermomechanical properties. Express Polymer Letters, 14(9), 881–884. https://doi.org/10.3144/expresspolymlett.2020.72 [Google Scholar] [CrossRef]
18. Thakur, T., Jaswal, S., Gaur, B., Singha, A. S. (2021). Thermo-mechanical properties of rosin-modified o-cresol novolac epoxy thermosets comprising rosin-based imidoamine curing agents. Polymer Engineering & Science, 61(1), 115–135. https://doi.org/10.1002/pen.25562 [Google Scholar] [CrossRef]
Cite This Article
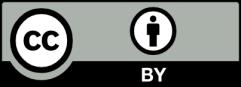
This work is licensed under a Creative Commons Attribution 4.0 International License , which permits unrestricted use, distribution, and reproduction in any medium, provided the original work is properly cited.