Open Access
REVIEW
A Comprehensive Review of the Influence of Heat Exchange Tubes on Hydrodynamic, Heat, and Mass Transfer in Bubble and Slurry Bubble Columns
1 Department of Chemical Engineering, University of Technology-Iraq, Baghdad, Iraq
2 Department of Chemical Engineering and Petroleum Industries, Al-Mustaqbal University College, Babylon, 51001, Iraq
3 Department of Chemical and Biochemical Engineering, Missouri University of Science and Technology, Rolla, MO, USA
* Corresponding Author: Abbas J. Sultan. Email:
(This article belongs to the Special Issue: Recent advancements in thermal fluid flow applications)
Fluid Dynamics & Materials Processing 2023, 19(10), 2613-2637. https://doi.org/10.32604/fdmp.2023.028081
Received 29 November 2022; Accepted 20 February 2023; Issue published 25 June 2023
Abstract
Bubble and slurry bubble column reactors (BCRs/SBCRs) are used for various chemical, biochemical, and petrochemical applications. They have several operational and maintenance advantages, including excellent heat and mass transfer rates, simplicity, and low operating and maintenance cost. Typically, a catalyst is present in addition to biochemical processes where microorganisms are used to produce industrially valuable bio-products. Since most applications involve complicated gas-liquid, gas-liquid-solid, and exothermic processes, the BCR/SBCR must be equipped with heat-exchanging tubes to dissipate heat and control the reactor’s overall performance. In this review, past and very recent experimental and numerical investigations on such systems are critically discussed. Furthermore, gaps to be filled and critical aspects still requiring investigation are identified.Keywords
Nomenclature
XTL | “Natural gas, coal and biomass” to “Liquid” |
GTL | Gas to Liquid |
BTL | Biomass to Liquid |
CTL | Coal to Liquid |
WTL | Waste to Liquid |
FTS | Fischer Tropsch Synthesis |
CFD | Computational Fluid Dynamic |
CSA | Cross Section Area |
BCR | Bubble Column Reactor |
SBCR | Slurry Bubble Column Reactor |
2D | Tow dimension |
DPM | Dynamic Pressure Method |
RCFD | Recirculation and Cross Flow with Desperation |
H/D | Height of dynamic liquid/Column diameter |
L/D | Height of column/Column diameter |
Dc | Bubble column diameter, m |
Hc | Bubble column height, m |
Di | Internal diameter, m |
D° | Outer diameter, m |
Ug | Superficial gas velocity, m.s−1 |
kL | Liquid-side mass transfer coefficient, s−1 |
kLa | Over all volumetric mass transfer coefficient, s−1 |
1.1 Energy Crisis and Environmental Impacts
Since fossil fuels are highly harmful to the environment, an alternative energy source must be discovered [1,2]. This alternative should be a sustainable and eco-friendly generation source that uses advanced techniques that reduce pollution, develop a long-term approach, and satisfy the world’s energy consumption [2–4]. XTL technology is one of the essential technologies for obtaining low-carbon-emission fuels and chemicals from different raw materials, such as coal, natural gas, biomass, or waste [5,6]. Besides this method can convert solid biomass into liquid fuels, natural gas can also be processed with this technology into clean liquid fuels and chemicals [6–8].
Therefore, using XTL technology solves the problem of transporting and marketing natural gas worldwide. Various processes for producing liquid hydrocarbons from non-oil feedstock have been intensively developed over the past years and are still under research and development. These processes, including indirect technologies such as GTL (gas to liquids), CTL (coal to liquids), BTL (biomass to liquids), and WTL (waste to liquids), are examples of such processes [9–11]. These processes begin with the oxidizing conversion of carbon-containing feedstock to obtain synthesis gas, a mixture of carbon monoxide and hydrogen [9,12].
The XTL technologies include catalytic liquefaction, gas-reforming, gasification, water-gas shift converting, syngas-cleaning, methanol-synthesis, Fischer-Tropsch synthesis, and syn-crude refining [5,13,14]. The second step in most XTL processes is the Fischer-Tropsch synthesis, which creates hydrocarbons from carbon monoxide and hydrogen. Because it controls the production, content, and manner of refining hydrocarbon products, this stage of the XTL technology is crucial [15–17].
1.2 Fischer-Tropsch Synthesis (FTS)
FTS is a chemical synthesis process that transforms syngas (i.e., H2 and CO) into synthetic liquid fuels and valuable compound chemicals. Thermal gasification of natural gas, biomass and coal is a practical technology for generating syngas from complex materials, especially those inferred from waste that is not economically feasible to handle for use in bio-catalytic and other rapidly progressive catalyst processes. Developing a newer catalyst with excellent selectivity and activity is desired since it increases the value and performance of FTS products [13,18].
Fischer-Tropsch synthesis is a major chemical process in manufacturing liquid fuels and olefins. The availability of natural gas in recent years and the rising demand for olefins, gasoline, diesel, and waxes have ignited a strong interest in further developing this process [19]. Moreover, FTS is an advanced liquefaction method for solid biomass or natural gas [5,20]. It enables liquid fuel production from different raw materials by catalytic conversion of the synthesis gas (i.e., a mixture of H2 and CO) [21,22]. Controlling heat transfer in FTS is a crucial step since FTS is a highly exothermic process and occurs under high reaction temperatures resulting in increased methane output, carbon deposition, and catalyst deactivation [14,23]. This conversion is carried out in many multiphase reactors, including fluidized bed reactors, fixed bed reactors, and BCR-SBCR, as shown in Fig. 1 [24–28].
Figure 1: Illustration of fischer-tropsch reactors
The fluidized bed and fixed bed reactors are primarily utilized for highly-temperature FTP among these multiphase reactors. In contrast, the BCRs-SBCRs are typically used in low-temperature FTP. BCR-SBCR has been the most preferred reactors for FTS, according to their simplicity of manufacture, providing high interfacial area between reactants materials, offering a high rate of mass and heat transfer, and plug-free operating [29,30].
2 Bubble Column Reactor (BCR) and Slurry Bubble Column (SBCR)
In chemical, biochemical, and petrochemical applications, BCs are commonly used as multiphase reactors [31–34]. This type of reactor has various advantages, including, excellent heat and mass transfer rates, good thermal stability, inexpensive operating costs, and low upkeep requirements. Several variables affect the BC reactor’s efficiency, which also influences the FTS, such as operating parameters (i.e., the physical properties of reactant materials, pressure, temperature, gas and liquid superficial velocities, operating mode, design parameters (i.e., height and diameter of the column and gas distributor design)) [35–37]. It is important to mention that the gas sparger is commonly positioned before the gas distributor plate at the bottom of the column, dispersing the gas phase as bubbles into liquid or suspension [6,38,39].
In almost all SBCR applications, fine solid particles (catalytic) are suspended in a gas-liquid system to catalyze reactions. For handling exothermic reactions by these reactors, heat exchanger tubes must be installed in the BCRs-SBCRs to dissipate heat, control operating temperature and hence regulate the reactor’s performance [40]. Many theoretical and experimental studies have been conducted to facilitate the design, scaleup, and enhancement of these reactors’ performance. However, these studies were conducted in BCRs-SBCRs that were not equipped with a bundle of heat-exchanging tubes despite these reactors being widely used for handling exothermic reactions that require dissipation for the heat generated. Accordingly, the impact of installing a bunch of cooling tubes on the hydrodynamic, heat, and mass transfer of BCR-SBCR is lacking in the literature and still needs to be better understood. A better understanding of the effect of these heat-exchanging tubes can be achieved by conducting comprehensive studies on these reactors when equipped with a bundle of heat-exchanging tubes.
Therefore, this review aims to critically discuss the previous and latest experimental and numerical studies on BCR-SBCR fitted with tubes. Moreover, it analyzes and reports the influence of equipping the BC-SBC with tubes on hydrodynamics, heat, and mass transfer phenomena. Furthermore, it identifies the gap in the literature in this field and establishes further recommendations for future works.
3 Experimental Hydrodynamic Studies on BC-SBC Equipped with a Bundle of Heat Exchange Tubes
Heat exchange tubes have been commonly used in BCR-SBCR to eliminate excess heat and optimize operating conditions by influencing reactant phase distributions; the inclusion of cooling tubes has a major impact and influences fluid dynamics [41,42]. To increase mass/heat transfer rates in these reactors, the design of these cooling tubes must be enhanced. Therefore, it is essential to understand and comprehend the impact of cooling tubes and their configurations on the phase distribution of reactants material. Forret et al. [43] explored mixing liquid and dispersion in a 1 m diameter BC with and without a bunch of vertical tubes using a standard tracer technique. Also, they evaluated one dimensional-axial dispersion model (ADM) that can describe the level of back-mixing and measure the departure from the optimal behavior of plug flow on the column without internals [44,45]. Their study established two-dimensional models to consider internals when calculating the effect of liquid mixing at various superficial gas velocities. The bundle covered 22% of the column’s CSA in this study. Their findings show that the insertion of vertical tubes has an impact on both local and large-scale liquid dispersion. In addition, they found that vertical tubes have the primary effect of reducing radial-dispersion and increasing large-scale recirculation, as illustrated in Fig. 2.
Figure 2: Illustration of liquid recirculating in BC (a) in the absence of vertical tubes (b) with vertical tubes [43]
Zhang et al. [46] investigated two SBCs with 0.5 m diameter. The first one was equipped with vertical internals that blocked 11% (i.e., 40 vertical internals) of the column’s CSA. The other column had vertical internals that equipped 5.3% (i.e., 18 vertical internals) of the CSA. The experiment results demonstrated that the vertical internals would significantly improve gas holdup (i.e., the volume percentage of gas in the overall volume of the gas-liquid phase in the bubble column). It is one of the essential parameters for characterizing the bubble column’s hydrodynamic factors. It is closely related to bubble size and surface gas velocity with large-scale liquid circulation while inhibiting the radial dispersion of both liquid and bubbles.
Youssef et al. [47] measured the local-gas holdup and bubble characteristics (i.e., bubble chord lengths, bubbles velocities distribution, and gas-liquid interfacial area) in the BC fitted with a bunch of vertical rods by utilizing four tips optical probe at various operating superficial gas velocities. Their experimental investigation was conducted in two BC equipped with different occluded CSA by vertical rods. The first column has a bunch of vertical rods that block 5% of the CSA of the column to represent methanol synthesis. In comparison, the second column was equipped with vertical rods that blocked 22% of CSA to simulate the FTP. Their research findings revealed that gas holdup and interfacial area were increased when the BC was equipped densely with rods (i.e., blocking 22% of CSA). In contrast, bubble chord lengths were significantly reduced. In addition, they found that when the BC was equipped with rods that covered 5% of CSA, the gas holdup and large-scale liquid circulation were negligible.
Chen et al. [27] used Computer Automated Radioactive Particle Tracking (CARPT) and Computed Tomography (CT) techniques to quantify the gas-liquid distribution, liquid recirculation, and turbulent stresses for a BC (0.44 m in diameter) equipped with a bunch of vertical rods.
These hydrodynamic parameters were measured at various operating superficial gas velocities. The bunch of vertical rods in their research was designed in a way to block 5% of the column’s CSA to simulate the synthesis of methanol, as shown in Fig. 3. Their investigation showed a significant reduction in turbulent stress and a 10% increase in the gas holdup. Also, they discovered that the internals’ existence does not affect the gas-liquid recirculation.
Figure 3: Configuration of a bundle of vertical rods [30]
Balamurugan et al. [48] examined the impact of using vibrating helical spring rods of various diameters and thicknesses on the total gas holdup in a BC with an inside diameter of 1.5 m at different superficial gas velocities varying from 3.6–54.2 cm/s. Fig. 4 shows the type and configuration of used vibrating helical spring rods. They used vertical rods for comparison purposes against vibrating helical spring rods. The experimental finding presented in their study indicates that gas holdup was enhanced up to 135% by utilizing vibrating helical spring rods in the BC reactor compared to empty BC reactors. They also indicated that the vibrating springs break up the gas bubbles into smaller bubbles, which reduces the gas’s rising velocity and increases its residence time in the column.
Figure 4: Bubble column schematic with spring rods [46]
Consequently, this method provides an easy, economical, and simple technique to improve gas holdup at a high gas flow rate. Despite using a novel design for vertical internals as shown previously, these studies were limited to measuring one parameter (i.e., overall gas holdup), which is a global parameter. Therefore, further investigations are needed to check the new design’s visibility.
Among the simulation studies of a bubble reactor, Abid et al. [38] applied the Eulerian-Eulerian model in their simulation with a constant bubble size (CBSM) and variable bubble size modeling approach (VBSM). According to his work, the proposed approach and CFD-PBM modeling are used to simulate a lab-scale bubble column operating in a heterogeneous regime, and the computing efficiency and accuracy of these two approaches are quantified. Furthermore, in CFD-PBM simulations, numerous combinations of bubble coalescence models and breakage models are employed to investigate the influence of coalescence and breakdown models on simulation outcomes. The effect of the minimum bubble diameter, a critical parameter of the discretization approach, is also investigated. It should be mentioned that the numerical models employed in the developed technique are the same as those used in CFD-PBM modeling, with the difference that the breakdown and coalescence models are not recognized in the developed method. A series of discrete points represent the range of bubble sizes, and the proportion of bubbles of various sizes at the gas inlet is obtained by the results of Computational fluid dynamic balance model (PBM) simulations, with the impact of bubble coalescence and breakup ignored [41,49–55].
Youssef et al. [56] continued the investigation in the field of the hydrodynamics of BCR with vertical internals. They experimentally characterized the bubble properties using an optical probe technique in a large-scale BC with a 0.45 m diameter fitted densely with a bundle of vertical rods at various superficial gas velocities ranging from 0.05–0.45 m/s. In their study, the bundle of rods was designed to cover 5%, 10%, 20%, and 25% of the column’s total CSA, as presented in Fig. 5. Their experimental findings at different superficial gas velocities revealed that the vertical rods increased the overall gas holdup and changed the radial gas holdup profile. In addition, they discovered that the tube bundle’s presence in a large-diameter column caused an improvement in liquid recirculation.
Figure 5: Bundle rods configurations covering (a) 5%, (b) 10%, (c) 15%, (d) 20%, and (e) 25% of the CSA [47]
Kagumba et al. [57] studied the effects of vertical internals on the bubble characteristics in two BCRs with 0.14 and 0.44 m inner diameters using an optical sensor with four tips under operating superficial gas velocity ranging between 0.03 and 0.45 cm/s. Two different configurations were used in this work. The first configuration was made of 30 Plexiglas rods of 2.54 cm in diameter, while the second configuration was made of 8 Plexiglas rods of 1.27 cm in diameter. The rods for both configurations were designed in a triangular pitch occupying 25% of the CSA targeting in their study of the FTP, as shown in Fig. 6. Their experimental findings revealed that the tubes with a diameter of 2.54 cm consistently provided better overall and local gas holdup than tubes with a diameter of 1.27 cm or an empty column. The internal diameter has little impact on the churn turbulent flow regime. Also, they indicated that local and overall gas holdup and bubble properties (bubble passage frequencies, bubble chord lengths, and axial bubble velocity) increase with increasing column diameter for BCR/SBCR with and without vertical internals.
Figure 6: Rods arrangements for both sizes of rods [48]
Al Mesfer et al. [58] examined the effect of inserting a bunch of vertical rods on the gas hold up in a BC with 0.14 m in diameter operated at various flow regimes (i.e., homogeneous and heterogeneous flow regimes) by utilizing gamma ray Computed Tomography (CT) technique. A triangular pitch of 30 vertical rods with a 1.27 cm outer diameter covering 25% of the CSA was used, as shown in Fig. 7. The research showed that the vertical rods gradually increased the local and overall gas holdup. Other impressive effects were noticed, such as the influence of the vertical rods on the form of the gas holdup profiles close to the wall and that the effect of dense tubes became minor at high velocities. Furthermore, they observed that, when employing the same-sized tubes and the same occluded CSA, the vertical rod bundle had a substantial impact on gas holdup over the CSA of the column.
Figure 7: Configuration of the vertical rods [59]
Al Mesfer et al. [59] continued studying the influence of inserting a bunch of vertical rods on the hydrodynamics of BC. They extended experimental work on the velocity of liquid and turbulence variables utilizing the Radioactive Particle Tracking (RPT) technique for the same BC. From experimental analyses, they deduced that the existence of vertical rods with increased superficial gas velocities causes an increase in both axial velocity and liquid centerline. On the other hand, they noticed a substantial reduction in turbulence parameters, whereas an increase in superficial gas velocity in the absence of internals leads to an increase in both. The data acquired from their research are very beneficial for computational fluid dynamics (CFD) simulations and model validation.
Guo et al. [60] simulated the impact of tube-bunch on the hydrodynamics of gas-liquid of BC with 0.14 m diameter under two operating gas flow rates (0.03 and 0.45 m/s). In their simulation, they utilized the dimensions of BC and the layout of vertical internals the same as that used by Kagumba et al. [61] and Al Mesfer et al. [62], as shown in Fig. 8. An Eulerian two-fluid model (TFM) and a population balance method (PBM) were utilized in their simulation. Also, the numerical simulations were conducted fully three-dimensional with ANSYS Fluent.
Figure 8: Geometric configurations of vertical rods [51]
According to the simulation’s findings, a BC with vertical rods included a greater number of smaller-sized bubbles. Also, they reported that the turbulent dissipation rates were dramatically elevated in the spaces between the internal walls, according to the numerical results.
Guan et al. [63] predicted the influence of the installation of a bunch of vertical rods on the hydrodynamic parameters of a pilot-scale BC (0.48 m in diameter) by using 2D CFD (a set of numerical modeling techniques to simulate and forecast the dynamics of single-phase and multi-phase fluid flows related to chemical reactions, hydrodynamics, heat and mass transfer with fundamental principles). In this research, the bundle rods were chosen to block 5% of CSA and arranged in equilateral triangular. Their CFD results show that a bundle of rods has no consequence on gas holdup, and it enhances large-scale liquid circulation by significantly reducing the turbulent velocity. Also, the findings indicate that the bunch of rods reduced the average bubble chord length in the BC while dramatically increasing turbulent dissipation rates in the spaces between the bunch rods and the column wall.
Sultan et al. [64] visualized and quantified in a noninvasive way the impact of inserting a bunch of vertical rods and the design of configurations of rods in a 0.14 m BC on gas holdup distribution utilized an advanced gamma-ray Computed Tomography (CT) technique. Three distinct configurations of vertical rods were designed and used in their experimental work, as shown in Fig. 9. Despite using different configuration designs in their work, the bunch of vertical rods was designed to occupy 22% of the column’s CSA to simulate the cooling tubes used in the industrial FTP. Their CT images in Fig. 10 displayed that the hexagonal configuration led to a notable improvement in gas holdup values and enhanced distribution of the gas dispersed across the whole of the column’s CSA. Gas holdup distribution was asymmetric in the BC, including circular tubes and an additional central tube. The obtained data of CT images for gas-liquid distribution throughout the whole CSA of a BC equipped densely with a bunch of vertical rods would be greatly helpful in developing and validating CFD simulation or even mathematical models. This validation process for simulation or models through benchmark data will advance this reactor’s design and scale-up.
Figure 9: Picture and schematics for different configurations (a) circular, (b) hexagonal, (c) circular with an extra tube in the center [53]
Figure 10: CT images for gas holdup distribution measured in BC with and without vertical rods under a variety operating of superficial gas velocities [53]
Al-Naseri et al. [29] measured the radial profiles of the bubble characteristics in a BC with a diameter of 0.6 m at superficial gas velocities ranging from 0.2 to 0.45 m/s by using four points of optical probes. Twenty-four tubes, each 0.06 m in diameter, were placed in a hexagonal configuration and inserted inside the column, occupying 24% of the CSA of the column shown in Fig. 11. Various available height levels of dynamic liquid to the diameter of the bubble column (aspect ratios H/D) were employed (H/D = 3, 4, and 5) in their experiments to quantify the effect of using different aspects ratio on the bubble properties. According to their findings, the tubes significantly impacted the distribution of bubble characteristics and radial profiles distribution, especially in the fully developed flow zone, and slightly increased overall gas holdup.
Figure 11: Configuration of hexagonal rods [31]
In contrast, reduce the chord length of the bubble and velocities of the bubble rise while increasing both the interfacial bubble area and the bubble pass frequency, particularly at the wall zone. Furthermore, the existence of tubes and an increase in the aspect ratio (H/D) indicate that the fully developing flow zone begins at lower axial locations. Also, an increase in superficial gas velocities conserves the change to a higher axial site.
The summary of investigations based on experiments carried out in SBCR and BCR with a bunch of tubes is described in Table 1. This table includes brief details about the effect of internals (heat exchange tubes) on hydrodynamics.
According to the above discussion of previous studies, a few studies have been done on the hydrodynamics of a bubble column equipped with a bundle of rods. These few studies have contributed a lot to improving the understanding of the effect of installing a tube bundle inside this reactor on the hydrodynamic factors. However, these studies have some limitations. Among these limitations, most previous studies were conducted at atmospheric temperature and pressure, while the real Fischer Tropsch synthesis (FTS) occurs at high temperature and pressure. Also, the past studies were limited to the air-water system, which does not represent the actual material involved in FTS. Moreover, all the bundles used in the previous studies were solid rods, not real heat exchanger tubes. Furthermore, all previous studies were not involved in any chemical reactions. Therefore, further research is required to enhance the fundamental understanding of the impact of inserting a heat exchanger inside these reactors on the hydrodynamics parameters, which affect the performance of these reactors and, ultimately, the productivity of FTS.
4 Heat Transfer in BCR/SBCR Equipped with a Bunch of Vertical Tubes
In order to eliminate extra heat and maintain the proper operating conditions, heat exchange tubes are frequently installed in BCR-SBCR columns. One of the main difficulties in the FTP is the evacuation of significant amounts of the excessive heat produced by exothermic synthesis reactions to protect the catalyst from deactivation and poisoning. Heat generation that produces hot-spots and carbon deposits on the catalyst could cause this catalyst deactivation. Therefore, excess heat must be removed. Studying heat transfer coefficients (HTC) in BCR/SBCR may be helpful when designing, implementing, and augmenting production reactors. It is considered one of the vital factors in the way these reactors work. In gas/liquid and gas/liquid/solid systems, bubbles cause disturbs and mix gases, considerably improving heat/mass transfer. Therefore, bubble-induced turbulence is primarily responsible for the high HTC in the BCR/SBCR [57,61,74,75].
According to the literature on BCR/SBCR, there are tremendous studies on hydrodynamic, heat, and mass transfer in these reactors that are not equipped with a bunch of vertical rods. However, few experimental and numerical studies on BCR/SBCR fitted densely with many tubes. Furthermore, investigation of heat transfers in BCR/SBCR with a bunch of vertical tubes is even scarce. Among these heat transfer investigations:
Abdulmohsin et al. [76] investigated the impact of internals on the HTC in a 0.19 m diameter BC operating under superficial gas velocities ranging from 0.03 to 0.2 m/s by utilizing a fast response HT technique. They examined the effects of cooling tubes that covered 0% (an empty column), 5% (to simulate the synthesis of methanol), and 22% (to simulate the synthesis of FT) of the total CSA. Their study showed that the HTC was enhanced in the column, with a larger percentage of internals covering the CSA (22%).
Jhawar et al. [77] used a fast response probe in a BC with a 0.15 m diameter and operated it under various flow rates (0.03 to 0.35 m/s) to study the effect of vertical rods on the local HTC. Their experimental work was conducted with two types of vertical rods: fifteen tubes arranged in a circular pitch of 12.7 mm and six concentric baffles, as shown in Fig. 12. They found that the presence of the tube bundle enhances HTC in the central region compared to a hollowed BCR.
Figure 12: Design of vertical rods [66]
Jhawar et al. [78] studied the influence of inserting vertical rods inside the BCR on local HTC. This research investigated the local HTC in an SBCR with a 0.15 m diameter equipped with dense vertical internals. This study measured and quantified the influence of using various configurations (i.e., 15 tubes in a circular arrangement of 12.7 mm pitch and 6 concentric baffles) on local HTC at a wide variety of flow rates ranging from (0.03 to 0.35 m/s). He observed that the local HTC with a bundle of vertical internals was increased. Also, he found that the HTC decreased as slurry concentration increased.
Alzamily et al. [79] recently investigated the impact of equipping a BC with a bunch of tubes on instantaneous and local HTC radially and axially operated at a wide variety of gas flow rates ranging from (0.05–0.45 m/s) by using an advanced heat transfer technique. They examined different arrangement designs (square and triangular tube pitch configurations), as illustrated in Fig. 13.
Figure 13: Geometric layouts of square and triangular tubes [68]
Additionally, the axial height’s impact on HTC has been studied. According to their findings, HTC has a uniform-profile due to the square tube’s pitch arrangement. Higher heat transfer values are attained towards the center of the column when equipped with a bundle of tubes. Also, this study showed that the configuration of the tubes has a considerable impact on the shape of the HTC profile. For instance, the triangular tube pitch arrangement induced a high HTC profile.
Heat transfer studies in BCRs/SBCRs with various vertical internal designs are summarized in Table 2. Despite the importance of using a bundle of internals for industrial BCRs/SBCRs, previous literature on heat transfer studies in BCRs equipped with a bundle of vertical internals shows that understanding of the impact of these vertical internal tubes on heat transfer is still limited and lacking in the available literature.
5 Mass Transfer Studies in BC-SBC with a Bunch of Vertical Tubes
One of the most crucial process variables in the fields of chemicals, petrochemicals, and biological engineering is the overall volumetric gas-liquid mass transfer (KLa). It is an important design parameter for BC and SBC, especially in operations like the FTP and methanol synthesis that require absorbing gases into organic liquids. Since mass transfer has been studied over the past few years, experiment values and correlation for KLa at various operating parameters have been collected [66,86]. Unfortunately, these experimental studies were carried out in BCs without vertical tubes. Even though comprehensive efforts have been made in recent decades to help comprehend the mass transfer of BCRs and SBCRs, only a limited number of these experiments have been obtained in BC fitted with a bunch of internals on mass transfer. The following is a summary of the researchers’ study in recent years on the impact of vertical internals on mass transfer in both BCs and SBCs.
Hamed [66] conducted and quantified the effect of vertical rods on the volumetric gas-liquid mass transfer coefficient, KLa; and the gas-liquid mass transfer, KL; in a pilot-scale BC 0.45 m diameter at a variety range of superficial gas velocities from 0.02 to 0.45 m/s, utilized the optical- oxygen probe and an oxygen-enriched air dynamics methods. According to his finding, the KL factor with a bunch of vertical internals was decreased compared with the case without internals from 0.047 to 0.032 s−1. Therefore, the interfacial-area increased. Also, he noticed that the value of KLa in the absence of internals ranged from 0.091 to 0.15 cm/s, which is the same value in the presence of internals, indicating that the KLa values did not affect the inclusion of vertical internals.
Manjrekar et al. [87] studied the impact of vertical rods on the KLa and KL in two pilot-scale BC 0.45 and 0.19 m diameters in the air-water system using dynamic-gas separation technique to calculate the volumetric mass transfer coefficients. Their experimental findings showed that vertical rods had no discernible impact on the KL (0.03 cm/s) in the churn turbulent flow regime. Consequently, the decrease in mass transfer coefficients KLa (0.13 s−1) caused by a decrease in turbulent intensity with the existence of internals is offset by an increase in gas-liquid interfacial- area which is caused by increased bubble separation.
Möller et al. [86,88] recently conducted a study examining the impact of two different tube arrangements (i.e., the triangular pitch of 0.032 m and square pitch of 0.045 m) with U-tube bottom end design on the KLa using an oxygen probe technique in the air-water system. They conducted their experiments in a pilot-scale BC with a diameter of 0.392 m equipped with a bundle of tubes (i.e., blocking 25% of CSA). The KLa was measured under different gas flow rates ranging from 0.01–0.2 m/s (i.e., covering the bubble and churn flow regimes). Both tube layouts and specifications are illustrated in Fig. 14. From experimental work, the results from narrow and pilot-scale columns have been compared, deduced that internals reduces volumetric mass transfer approximately from (0.18 to 0.1 s−1) and cause flow asymmetries which is consistent with Manjrekar et al. [87].
Figure 14: Tube arrangement inside the bubble column [86]
Möller et al. [89] later suggested a sophisticated recirculation-cell model conduct mass transfer in the same BC (0.39 m diameter) either with or without internals. The model, which assumed the size of the bubbles, was validated using Möller et al. [86] experimental data. Their experiment showed that the mass transfer rate decreased approximately from (1.7 to 1.3 s−1) when inserting a tube bundle of vertical internals.
Table 3 illustrates the summary investigations of the effect of a bunch of tubes based on experiments carried out in the BCR and SBCR on mass transfer. It was noted that no one of the researchers studied the impact of inserting a bunch of vertical cooling internals in SBCRs.
6 Conclusions and Recommendations
The experimental and numerical research findings provide a detailed understanding of the impact of vertical internals; the configurations and diameter of the tube; and the occluded CSA ratio on the hydrodynamic; heat/mass transfer, which are considered to be the most crucial hydrodynamic factors affecting BCR/SBCR efficiency. The effects of inserting heat exchange tubes into BCR/SBCR on flow regime, the intensity of mixing, and overall hydrodynamics are debated. The main conclusions and recommendations for this review are as follows:
1. Bubbles breakage is promoted and smaller bubbles with a tight size distribution are produced by the insertion of vertical tubes for heat exchange, which might significantly enhance gas holdup and interfacial-area while physically reducing turbulence length scales at low superficial velocities.
2. Internals have an effect only if they are present in a significant proportion of the column’s CSA. Large-scale liquid circulations are promoted by vertical tubes for heat exchange, while radial dispersion and bubble chord lengths are limiting. The overall gas holdup and HTC improve while the bubble chord-length reduces as the percentage of the column’s CSA increases.
3. Compared to the circular configuration of vertical tubes for heat exchange, the hexagonal design considerably enhanced the gas holdup values and distribution of the gases throughout the whole column’s CSA.
4. A high percentage of internals enhances the HTC for a given gas velocity, as measured by the flow’s free CSA, compared to the column CSA occupied by 0% “empty column”; 5% “simulated methanol-synthesis”; and 22% “simulated FTS”.
5. In relation to the mass transfer investigations, the local turbulence created by particle transitions to the bubble’s surface due to the collision characteristic caused a large increase in the mass transfer coefficient on the liquid’s side.
6. Future studies should investigate the impact of utilizing finned heat exchange tubes on the heat and mass transfer of BCR-SBCR under high operating conditions.
7. Quantifying the impact of different heat exchange tube diameter on the hydrodynamic and heat/mass transfer of BCR-SBCR using different tube arrangements need to be considered in future studies.
Acknowledgement: The authors would like to acknowledge the Department of Chemical Engineering, University of Technology-Iraq, and the Department of Chemical Engineering and Petroleum Industries, Al-Mustaqbal University College, Babylon, for their guidance and support throughout this study.
Funding Statement: The authors received no specific funding for this study.
Conflicts of Interest: The authors declare that they have no conflicts of interest to report regarding the present study.
References
1. Kumar, S., Panda, A. K., Singh, R. K. (2011). A review on tertiary recycling of high-density polyethylene to fuel. Resources, Conservation and Recycling, 55(11), 893–910. https://doi.org/10.1016/j.resconrec.2011.05.005 [Google Scholar] [CrossRef]
2. Ovchinnikova, S., Borovkov, A., Kukinova, G., Markina, N. (2021). Environmental substantiation for the use of alternative energy sources. E3S Web of Conferences, 244(2), 1–6. https://doi.org/10.1051/e3sconf/202124401007 [Google Scholar] [CrossRef]
3. Sebestyén, V. (2021). Renewable and sustainable energy reviews: Environmental impact networks of renewable energy power plants. Renewable and Sustainable Energy Reviews, 151, 111626. https://doi.org/10.1016/j.rser.2021.111626 [Google Scholar] [CrossRef]
4. Gilbert, A., Bazilian, M. D., Gross, S. (2022). The emerging global natural gas market and the energy crisis of 2021–2022. Brookings. [Google Scholar]
5. Martinelli, M., Gnanamani, M. K., LeViness, S., Jacobs, G., Shafer, W. D. (2020). An overview of Fischer-Tropsch synthesis: XtL processes, catalysts and reactors. Applied Catalysis A: General, 608, 117740. https://doi.org/10.1016/j.apcata.2020.117740 [Google Scholar] [CrossRef]
6. Rahimpour, M. R., Jokar, S. M., Jamshidnejad, Z. (2012). A novel slurry bubble column membrane reactor concept for Fischer-Tropsch synthesis in GTL technology. Chemical Engineering Research and Design, 90(3), 383–396. https://doi.org/10.1016/j.cherd.2011.07.014 [Google Scholar] [CrossRef]
7. Teimouri, Z., Borugadda, V. B., Dalai, A. K., Abatzoglou, N. (2022). Application of computational fluid dynamics for modeling of Fischer-Tropsch synthesis as a sustainable energy resource in different reactor configurations: A review. Renewable and Sustainable Energy Reviews, 160, 112287. https://doi.org/10.1016/j.rser.2022.112287 [Google Scholar] [CrossRef]
8. Gupta, P. K., Kumar, V., Maity, S. (2021). Renewable fuels from different carbonaceous feedstocks: A sustainable route through Fischer-Tropsch synthesis. Journal of Chemical Technology and Biotechnology, 96(4), 853–868. https://doi.org/10.1002/jctb.6644 [Google Scholar] [CrossRef]
9. Loewert, M., Riedinger, M., Pfeifer, P. (2020). Dynamically operated Fischer-Tropsch synthesis in PtL—Part 2: Coping with real PV profiles. ChemEngineering, 4(2), 1–18. https://doi.org/10.3390/chemengineering4020027 [Google Scholar] [CrossRef]
10. Kulikova, M. V. (2019). The new Fischer-Tropsch process over ultrafine catalysts. Catalysis Today, 348(3), 89–94. https://doi.org/10.1016/j.cattod.2019.09.036 [Google Scholar] [CrossRef]
11. Sabri, L. S., Sultan, A. J., Al-Dahhan, M. H. (2017). Assessment of RPT calibration need during microalgae culturing and other biochemical processes. 2017 International Conference on Environmental Impacts of the Oil and Gas Industries: Kurdistan Region of Iraq as a Case Study (EIOGI), Iraq: Koya-Erbil. [Google Scholar]
12. Shamkhi, H. A., Albdiri, A. D. Z., Jabir, F. A., Petruzzelli, D. (2021). Removal of Pb2+, Cu2+, and Cd2+ ions from a saline wastewater using emulsion liquid membrane: Applying response surface methodology for optimization and data analysis. Arabian Journal for Science and Engineering, 47(5), 5705–5719. https://doi.org/10.1007/s13369-021-05624-5 [Google Scholar] [CrossRef]
13. Jahangiri, H., Bennett, J., Mahjoubi, P., Wilson, K., Gu, S. (2014). A review of advanced catalyst development for Fischer-Tropsch synthesis of hydrocarbons from biomass derived syn-gas. Catalysis Science and Technology, 4(8), 2210–2229. https://doi.org/10.1039/c4cy00327f [Google Scholar] [CrossRef]
14. Vogel, A. P., van Dyk, B., Saib, A. M. (2015). GTL using efficient cobalt Fischer-Tropsch catalysts. Catalysis Today, 259(19), 323–330. https://doi.org/10.1016/j.cattod.2015.06.018 [Google Scholar] [CrossRef]
15. Mahmoudi, H., Mahmoudi, M., Doustdar, O., Jahangiri, H., Tsolakis, A. et al. (2017). A review of Fischer Tropsch synthesis process, mechanism, surface chemistry and catalyst formulation. Biofuels Engineering, 2(1), 11–31. https://doi.org/10.1515/bfuel-2017-0002 [Google Scholar] [CrossRef]
16. Shen, J., Ho, W. H., Zhang, Y., Liu, X., Yao, Y., Hildebrandt, D., Ali, H. M. (2022). Design of a Fischer-Tropsch multi-tube reactor fitted in a container: A novel design approach for small scale applications. Journal of Cleaner Production, 362. https://doi.org/10.1016/j.jclepro.2022.132477 [Google Scholar] [CrossRef]
17. dos Santos, R. G., Alencar, A. C. (2020). Biomass-derived syngas production via gasification process and its catalytic conversion into fuels by Fischer Tropsch synthesis: A review. International Journal of Hydrogen Energy, 45(36), 18114–18132. https://doi.org/10.1016/j.ijhydene.2019.07.133 [Google Scholar] [CrossRef]
18. Davis, B. H. (2005). Fischer-Tropsch synthesis: Overview of reactor development and future potentialities. Topics in Catalysis, 32(3–4), 143–168. https://doi.org/10.1007/s11244-005-2886-5 [Google Scholar] [CrossRef]
19. Dancuart, L. P., Steynberg, A. P. (2007). Fischer-Tropsch based GTL technology: A new process? Studies in Surface Science and Catalysis, 163(2), 379–399. https://doi.org/10.1016/S0167-2991(07)80490-3 [Google Scholar] [CrossRef]
20. Tropsch, F., Schurm, L., Kern, C., Jess, A. (2021). Accumulation and distribution of higher hydrocarbons in the pores of a cobalt catalyst during low-temperature Fischer–Tropsch fixed-bed synthesis. Catalysis Science & Technology, 11(18), 6143–6154. https://doi.org/10.1039/d1cy01305j [Google Scholar] [CrossRef]
21. Abusrafa, A. E., Challiwala, M. S., Wilhite, B. A., Elbashir, N. O. (2020). Thermal assessment of a micro fibrous fischer tropsch fixed bed reactor using computational fluid dynamics. Processes, 8(10), 1–22. https://doi.org/10.3390/pr8101213 [Google Scholar] [CrossRef]
22. Karl, J., Pröll, T. (2018). Steam gasification of biomass in dual fluidized bed gasifiers: A review. Renewable and Sustainable Energy Reviews, 98, 64–78. https://doi.org/10.1016/j.rser.2018.09.010 [Google Scholar] [CrossRef]
23. Hu, J., Yu, F., Lu, Y. (2012). Application of Fischer-Tropsch synthesis in biomass to liquid conversion. Catalysts, 2(2), 303–326. https://doi.org/10.3390/catal2020303 [Google Scholar] [CrossRef]
24. Ge, S., Lou, Z., Yang, Y., Huang, Z., Sun, J. et al. (2020). Electrostatic effects on hydrodynamics in the riser of the circulating fluidized bed for polypropylene. AIChE Journal, 66(5), 1–13. https://doi.org/10.1002/aic.16916 [Google Scholar] [CrossRef]
25. Wang, X., Lv, Y., Bu, Y., Zhang, F., Li, Y. et al. (2020). A gas-solid fluidized bed reactor for activating the iron-based Fischer-Tropsch synthesis catalyst. Chemical Engineering Journal, 386, 122066. https://doi.org/10.1016/j.cej.2019.122066 [Google Scholar] [CrossRef]
26. Zimmermann, R. T., Bremer, J., Sundmacher, K. (2022). Load-flexible fixed-bed reactors by multi-period design optimization. Chemical Engineering Journal, 428, 130771. https://doi.org/10.1016/j.cej.2021.130771 [Google Scholar] [CrossRef]
27. Chen, J., Li, F., Degaleesan, S., Gupta, P., Al-Dahhan, M. H. et al. (1999). Fluid dynamic parameters in bubble columns with internals. Chemical Engineering Science, 54(13–14), 2187–2197. https://doi.org/10.1016/S0009-2509(99)00003-2 [Google Scholar] [CrossRef]
28. Fattahi, M., Kazemeini, M., Khorasheh, F., Darvishi, A., Rashidi, A. M. (2013). Fixed-bed multi-tubular reactors for oxidative dehydrogenation in ethylene process. Chemical Engineering and Technology, 36(10), 1691–1700. https://doi.org/10.1002/ceat.201300148 [Google Scholar] [CrossRef]
29. Al-Naseri, H., Schlegel, J. P., Al-Dahhan, M. H. (2019). The effects of internals and low aspect ratio on the fully developed flow region and bubble properties in a pilot-plant bubble column. Experimental Thermal and Fluid Science, 104, 284–301. https://doi.org/10.1016/j.expthermflusci.2019.02.011 [Google Scholar] [CrossRef]
30. Alzamily, A. N., Sultan, A., Abdulrahman, A. A., Al-Naseri, H., Sultan, A. et al. (2022). Study the impact of the tube configurations on the local heat transfer coefficient in mimicked Fischer-Tropsch bubble column reactor. SSRN Electronic Journal, 1–17. https://doi.org/10.2139/ssrn.4043692 [Google Scholar] [CrossRef]
31. Luo, H. P., Kemoun, A., Al-Dahhan, M. H., Sevilla, J. M. F., Sánchez, J. L. G. et al. (2003). Analysis of photobioreactors for culturing high-value microalgae and cyanobacteria via an advanced diagnostic technique: CARPT. Chemical Engineering Science, 58(12), 2519–2527. https://doi.org/10.1016/S0009-2509(03)00098-8 [Google Scholar] [CrossRef]
32. Zhou, S. Z., Xu, Q. J., Zhang, X. B., Luo, Z. H. (2021). Correlations for predicting heat transfer coefficients in bubble columns. Chemical Engineering and Processing—Process Intensification, 162, 108332. https://doi.org/10.1016/j.cep.2021.108332 [Google Scholar] [CrossRef]
33. Sultan, A. J., Sabri, L. S., Shao, J., Al-Dahhan, M. H. (2019). Overcoming the Gamma-Ray computed tomography data processing pitfalls for bubble column equipped with vertical internal tubes. Canadian Journal of Chemical Engineering, 97(11), 2979. https://doi.org/10.1002/cjce.23529 [Google Scholar] [CrossRef]
34. Papari, S., Kazemeini, M., Fattahi, M., Fatahi, M. (2014). Dme direct synthesis from syngas in a large-scale three-phase slurry bubble column reactor: Transient modeling. Chemical Engineering Communications, 201(5), 612–634. https://doi.org/10.1080/00986445.2013.782292 [Google Scholar] [CrossRef]
35. Möller, F., Lau, Y. M., Seiler, T., Hampel, U., Schubert, M. (2018). A study on the influence of the tube layout on sub-channel hydrodynamics in a bubble column with internals. Chemical Engineering Science, 179, 265–283. https://doi.org/10.1016/j.ces.2018.01.008 [Google Scholar] [CrossRef]
36. Mahmoudi, S., Hlawitschka, M. W. (2022). Effect of solid particles on the slurry bubble columns behavior—A review. ChemBioEng Reviews, 9(1), 63–92. https://doi.org/10.1002/cben.202100032 [Google Scholar] [CrossRef]
37. Marchini, S., Schubert, M., Hampel, U. (2022). Analysis of the effect of uncertainties in hydrodynamic parameters on the accuracy of the gas flow modulation technique for bubble columns. Chemical Engineering Journal, 434(November 2021), 133478. https://doi.org/10.1016/j.cej.2021.133478 [Google Scholar] [CrossRef]
38. Abid, B. A., Abdulmohsin, R. S. (2010). Heat transfer characteristics in a large-scale bubble column operating in a semi—batch mode. Engineering and Technology Journal, 28(3), 562–578. [Google Scholar]
39. Möller, F., Kipping, R., Lavetty, C., Hampel, U., Schubert, M. (2019). Two-bubble class approach based on measured bubble size distribution for bubble columns with and without internals. Industrial and Engineering Chemistry Research, 58(8), 2759–2769. https://doi.org/10.1021/acs.iecr.8b05784 [Google Scholar] [CrossRef]
40. Li, L., Zhao, Y., Lian, W., Han, C., Zhang, Q. et al. (2021). Review on the effect of gas distributor on flow behavior and reaction performance of the bubble/slurry reactors. Industrial & Engineering Chemistry Research, 60(30), 10835–10853. https://doi.org/10.1021/acs.iecr.1c00609 [Google Scholar] [CrossRef]
41. Bhusare, V. H., Dhiman, M. K., Kalaga, D. V., Roy, S., Joshi, J. B. (2017). CFD simulations of a bubble column with and without internals by using OpenFOAM. Chemical Engineering Journal, 317, 157–174. https://doi.org/10.1016/j.cej.2017.01.128 [Google Scholar] [CrossRef]
42. Li, L., Zhao, Y., Lian, W., Han, C., Liu, Y. et al. (2022). Insight into the effect of particle density and size on the hydrodynamics of a particular slurry bubble column reactor by CFD-PBM approach. Powder Technology, 400, 117264. https://doi.org/10.1016/j.powtec.2022.117264 [Google Scholar] [CrossRef]
43. Forret, A., Schweitzer, J., Gauthier, T., Krishna, R., Schweich, D. (2003). Liquid dispersion in large diameter bubble columns, with and without internals. The Canadian Journal of Chemical Engineering, 81, 360–366. [Google Scholar]
44. Basha, O. M., Sehabiague, L., Abdel-Wahab, A., Morsi, B. I. (2015). Fischer-Tropsch synthesis in slurry bubble column reactors: Experimental investigations and modeling—A review. International Journal of Chemical Reactor Engineering, 13(3), 201–288. https://doi.org/10.1515/ijcre-2014-0146 [Google Scholar] [CrossRef]
45. Abdulmohsin, R., Dissertation, A. (2013). Gas dynamics and heat transfer in a packed pebble-bed reactor for the 4th generation nuclear energy. https://www.proquest.com/openview/2e2f4d9e03e611232ae95f3e47aae65f/1?pq-origsite=gscholar&cbl=18750 [Google Scholar]
46. Zhang, Y., Lu, J., Wang, L., Li, X. (2009). Studies on hydrodynamics of turbulent slurry bubble column (III) Effect of vertical pipe bundles. Journal of the Chemical Industry and Engineering Society of China, 60, 1135–1140. [Google Scholar]
47. Youssef, A. A., Al-Dahhan, M. H. (2009). Impact of internals on the gas holdup and bubble properties of a bubble column. Industrial and Engineering Chemistry Research, 48(17), 8007–8013. https://doi.org/10.1021/ie900266q [Google Scholar] [CrossRef]
48. Balamurugan V., Subbarao D., Roy S. (2010). Enhancement in gas holdup in bubble columns through use of vibrating internals. The Canadian Journal of Chemical Engineering, 88, 1010–1020. https://doi.org/10.1002/cjce.20362 [Google Scholar] [CrossRef]
49. Guan, X., Yang, N. (2021). CFD simulation of bubble column hydrodynamics with a novel drag model based on EMMS approach. Chemical Engineering Science, 243, 116758. https://doi.org/10.1016/j.ces.2021.116758 [Google Scholar] [CrossRef]
50. Zhang, X., Luo, Z. (2022). Bubble size modeling approach for the simulation of bubble columns. Chinese Journal of Chemical Engineering, 53(20), 194–200. https://doi.org/10.1016/j.cjche.2022.02.005 [Google Scholar] [CrossRef]
51. Li, L., Lian, W., Bai, B., Zhao, Y., Li, P. et al. (2021). CFD-PBM investigation of the hydrodynamics in a slurry bubble column reactor with a circular gas distributor and heat exchanger tube. Chemical Engineering Science: X, 9, 100087. https://doi.org/10.1016/j.cesx.2020.100087 [Google Scholar] [CrossRef]
52. Gaurav, T. K., Prakash, A., Zhang, C. (2022). CFD modeling of the hydrodynamic characteristics of a bubble column in different flow regimes. International Journal of Multiphase Flow, 147, 103902. https://doi.org/10.1016/j.ijmultiphaseflow.2021.103902 [Google Scholar] [CrossRef]
53. Zhang, X., Luo, Z. (2023). Bubble size modeling approach for the simulation of bubble columns. Chinese Journal of Chemical Engineering, 53(20), 194–200. https://doi.org/10.1016/j.cjche.2022.02.005 [Google Scholar] [CrossRef]
54. Gupta, A., Roy, S. (2013). Euler-Euler simulation of bubbly flow in a rectangular bubble column: Experimental validation with radioactive particle tracking. Chemical Engineering Journal, 225, 818–836. https://doi.org/10.1016/j.cej.2012.11.012 [Google Scholar] [CrossRef]
55. Guan, X., Li, Z., Wang, L., Cheng, Y., Li, X. (2014). CFD simulation of bubble dynamics in bubble columns with internals. Industrial and Engineering Chemistry Research, 53(42), 16529–16538. https://doi.org/10.1021/ie502666y [Google Scholar] [CrossRef]
56. Youssef, A. A., Hamed, M. E., Grimes, J. T., Al-dahhan, M. H., Dudukovic, M. P. (2013). Hydrodynamics of pilot-scale bubble columns: Effect of internals. Industrial & Engineering Chemistry Research, 52(1), 43–55. [Google Scholar]
57. Kagumba, M., Al-Dahhan, M. H. (2015). Impact of internals size and configuration on bubble dynamics in bubble columns for alternative clean fuels production. Industrial and Engineering Chemistry Research, 54(4), 1359–1372. https://doi.org/10.1021/ie503490h [Google Scholar] [CrossRef]
58. Al Mesfer, M. K., Sultan, A. J., Al-Dahhan, M. H. (2016). Impacts of dense heat exchanging internals on gas holdup cross-sectional distributions and profiles of bubble column using gamma ray Computed Tomography (CT) for FT synthesis. Chemical Engineering Journal, 300(2–4), 317–333. https://doi.org/10.1016/j.cej.2016.04.075 [Google Scholar] [CrossRef]
59. Al Mesfer, M. K., Sultan, A. J., Al-Dahhan, M. H. (2017). Study the effect of dense internals on the liquid velocity field and turbulent parameters in bubble column for Fischer-Tropsch (FT) synthesis by using Radioactive Particle Tracking (RPT) technique. Chemical Engineering Science, 161, 228–248. https://doi.org/10.1016/j.ces.2016.12.001 [Google Scholar] [CrossRef]
60. Guo, X., Chen, C. (2017). Simulating the impacts of internals on gas–liquid hydrodynamics of bubble column. Chemical Engineering Science, 174, 311–325. https://doi.org/10.1016/j.ces.2017.09.004 [Google Scholar] [CrossRef]
61. Kagumba, M., Al-Naseri, H., Al-Dahhan, M. H. (2019). A new contact time model for the mechanistic assessment of local heat transfer coefficients in bubble column using both the four-optical fiber probe and the fast heat transfer probe-simultaneously. Chemical Engineering Journal, 361, 67–79. https://doi.org/10.1016/j.cej.2018.12.046 [Google Scholar] [CrossRef]
62. Al Mesfer, M. K., Sultan, A. J., Al-Dahhan, M. H. (2016). Impacts of dense heat exchanging internals on gas holdup cross-sectional distributions and profiles of bubble column using gamma ray Computed Tomography (CT) for FT synthesis. Chemical Engineering Journal, 300(2–4), 317–333. https://doi.org/10.1016/j.cej.2016.04.075 [Google Scholar] [CrossRef]
63. Guan, X., Yang, N. (2017). CFD simulation of pilot-scale bubble columns with internals: Influence of Interfacial forces in the present study, influence of interfacial forces, including drag force and. Chemical Engineering Research and Design, 126, 109–122. https://doi.org/10.1016/j.cherd.2017.08.019 [Google Scholar] [CrossRef]
64. Sultan, A. J., Sabri, L. S., Al-Dahhan, M. H. (2018). Influence of the size of heat exchanging internals on the gas holdup distribution in a bubble column using gamma-ray computed tomography. Chemical Engineering Science, 186(4), 1–25. https://doi.org/10.1016/j.ces.2018.04.021 [Google Scholar] [CrossRef]
65. Larachi, F., Desvigne, D., Donnat, L., Schweich, D. (2006). Simulating the effects of liquid circulation in bubble columns with internals. Chemical Engineering Science, 61(13), 4195–4206. https://doi.org/10.1016/j.ces.2006.01.053 [Google Scholar] [CrossRef]
66. Hamed, M. (2012). Hydrodynamics, mixing, and mass transfer in bubble columns with internals. Washington University, St. Louis. [Google Scholar]
67. Jhawar, A. K., Prakash, A. (2013). Chemical engineering research and design bubble column with internals: Effects on hydrodynamics and local heat transfer. Chemical Engineering Research and Design, 92(1), 25–33. https://doi.org/10.1016/j.cherd.2013.06.016 [Google Scholar] [CrossRef]
68. George, K. (2015). Investigations in hydrodynamics and mixing Pattern in the bubble column equipped with internals. Electronic Thesis and Dissertation Repository, 3167. https://ir.lib.uwo.ca/etd/3167 [Google Scholar]
69. Jasim, A. (2016). The impact of heat exchanging internals on hydrodynamics of bubble column reactor, (Masters Theses). [Google Scholar]
70. Jasim, A. A., Sultan, A. J., Al-Dahhan, M. H. (2019). Influence of heat-exchanging tubes diameter on the gas holdup and bubble dynamics in a bubble column. Fuel, 236, 1191–1203. https://doi.org/10.1016/j.fuel.2018.09.049 [Google Scholar] [CrossRef]
71. Jasim, A. A., Sultan, A. J., Al-Dahhan, M. H. (2019). Impact of heat exchanging internals configurations on the gas holdup and bubble properties in a bubble column. International Journal of Multiphase Flow, 112, 63–82. https://doi.org/10.1016/j.ijmultiphaseflow.2018.11.008 [Google Scholar] [CrossRef]
72. Agahzamin, S., Pakzad, L. (2019). CFD investigation of the gas dispersion and liquid mixing in bubble columns with dense vertical internals. Chemical Engineering Science, 203(5), 425–438. https://doi.org/10.1016/j.ces.2019.03.048 [Google Scholar] [CrossRef]
73. Guan, X., Xu, Q., Yang, N., Nigam, K. D. P. (2021). Hydrodynamics in bubble columns with helically-finned tube internals: Experiments and CFD-PBM simulation. Chemical Engineering Science, 240(5), 116674. https://doi.org/10.1016/j.ces.2021.116674 [Google Scholar] [CrossRef]
74. Kouzbour, S., Gourich, B., Stiriba, Y., Vial, C., Gros, F. et al. (2021). Experimental analysis of the effects of liquid phase surface tension on the hydrodynamics and mass transfer in a square bubble column. International Journal of Heat and Mass Transfer, 170. https://doi.org/10.1016/j.ijheatmasstransfer.2021.121009 [Google Scholar] [CrossRef]
75. Jhawar, A. K., Prakash, A. (2012). Heat transfer in a slurry bubble column reactor: A critical overview. Industrial & Engineering Chemistry Research, 51(4), 1464–1473. https://doi.org/10.1021/ie201108b [Google Scholar] [CrossRef]
76. Abdulmohsin, R. S., Al-Dahhan, M. H. (2012). Impact of internals on the heat-transfer coefficient in a bubble column. Industrial and Engineering Chemistry Research, 51(7), 2874–2881. https://doi.org/10.1021/ie2018096 [Google Scholar] [CrossRef]
77. Jhawar, A. K. (2011). Effects of internals configurations on heat transfer and hydrodynamics in bubble columns-with and without solid particles. The University of Western Ontario London, Ontario, Canada. [Google Scholar]
78. Jhawar, A. K., Prakash, A. (2007). Analysis of local heat transfer and hydrodynamics in a bubble column using fast response probes. Chemical Engineering Science, 62(24), 7274–7281. https://doi.org/10.1016/j.ces.2007.08.026 [Google Scholar] [CrossRef]
79. Alzamily, A., Sultan, A., Abdulrahman, A., Majdi, H. (2022). Study of the impact of tube configurations on the local heat transfer coefficient in mimicked Fischer-Tropsch bubble column reactor. Processes, 10(5), 976. https://doi.org/10.3390/pr10050976 [Google Scholar] [CrossRef]
80. Saxena, S. C. (1991). Hydrodynamic and heat transfer investigations conducted column with fine powders and a viscous liquid. Powder Technology, 67, 265–275. [Google Scholar]
81. Westermeyer, B. H. (1992). Heat transfer and gas holdup in two and three phase bubble column reactors with longitudinal internals (Ph.D. Thesis). University of Dortmund, Germany. [Google Scholar]
82. Taha, M. M., Nosier, S. A., Abdel-Aziz, M. H., El-Naggar, M. A. (2021). Solid-liquid mass transfer in a bubble column reactor with tube bank internals. Experimental Heat Transfer, 34(5), 461–473. https://doi.org/10.1080/08916152.2020.1776420 [Google Scholar] [CrossRef]
83. Muroyama, K., Imai, K., Oka, Y. (2013). Mass transfer properties in a bubble column associated with micro-bubble dispersions. Chemical Engineering Science, 100(1), 464–473. https://doi.org/10.1016/j.ces.2013.03.043 [Google Scholar] [CrossRef]
84. Béliard, P., Schweich, D., Clément, P., Gauthier-Maradei, P., Dromard, N. (2010). Heat transfer metrology issues in two-phase bubble column reactors. The Canadian Journal of Chemical Engineering, 88(4), 543–550. [Google Scholar]
85. Odongo, M., Kagumba, O. (2013). Scholars’ Mine Scholars’ Mine Doctoral Dissertations Student Theses and Dissertations Spring 2013 Heat transfer and bubble dynamics in bubble and slurry bubble Heat transfer and bubble dynamics in bubble and slurry bubble columns with internals for Fische. https://scholarsmine.mst.edu/doctoral_dissertations/2032. [Google Scholar]
86. Möller, F., Lavetty, C., Schleicher, E., Löschau, M., Hampel, U. et al. (2019). Hydrodynamics, mixing and mass transfer in a pilot-scale bubble column with dense internals. Chemical Engineering Science, 202, 491–507. https://doi.org/10.1016/j.ces.2019.03.001 [Google Scholar] [CrossRef]
87. Manjrekar, O. N., Hamed, M., Dudukovic, M. P. (2018). Chemical engineering research and design gas hold-up and mass transfer in a pilot scale bubble column with and without internals. Chemical Engineering Research and Design, 135, 166–174. https://doi.org/10.1016/j.cherd.2018.05.008 [Google Scholar] [CrossRef]
88. Möller, F., MacIsaac, A., Lau, Y. M., Schleicher, E., Hampel, U. et al. (2018). Advanced analysis of liquid dispersion and gas-liquid mass transfer in a bubble column with dense vertical internals. Chemical Engineering Research and Design, 134, 575–588. https://doi.org/10.1016/j.cherd.2018.04.018 [Google Scholar] [CrossRef]
89. Möller, F., Dehmelt, T., Schmidt, N., Lau, Y. M., Hampel, U. et al. (2020). A recirculation cell approach for hydrodynamic and mass transfer modeling in bubble columns with and without internals. Chemical Engineering Journal, 383(8), 123197. https://doi.org/10.1016/j.cej.2019.123197 [Google Scholar] [CrossRef]
90. Chen, P., Qin, G., Huang, Y. J., Wu, H. (1989). A heat and mass transfer model for thermal and hydraulic calculations of indirect evaporative cooler performance. ASHRAE Transactions, 97, 852–865. [Google Scholar]
91. Kang, Y., Kim, D. (1990). Mass transfer in continuous bubble columns with floating bubble breakers. AIChE Journal, 36(8), 1255–1258. [Google Scholar]
92. Karamanev, D. G., Nagamune, T., Endo, I. (1992). Hydrodynamic and mass transfer study of a gas-liquid-solid draft tube spouted bed bioreactor. Chemical Engineering Science, 47(13–14), 3581–3588. [Google Scholar]
93. Nosier, S. A., Mohamed, M. M. (2004). Mass transfer at helical coils in bubble columns. Chemical and Biochemical Engineering Quarterly, 18(3), 235–240. [Google Scholar]
94. Al-Shahrani, S. S., Nosier, S. A., El-Shazly, A. H., Abdel-Aziz, M. H. (2020). Effect of surfactants on mass transfer in a bubble column equipped with a horizontal tube bundles. International Communications in Heat and Mass Transfer, 113, 104548. https://doi.org/10.1016/j.icheatmasstransfer.2020.104548 [Google Scholar] [CrossRef]
Cite This Article
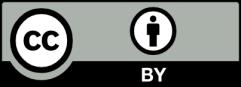
This work is licensed under a Creative Commons Attribution 4.0 International License , which permits unrestricted use, distribution, and reproduction in any medium, provided the original work is properly cited.