Open Access
ARTICLE
Characterization of Unsaturated Polyester Filled with Waste Coconut Shells, Walnut Shells, and Carbon Fibers
Department of Materials Engineering, University of Technology-Iraq, Baghdad, Iraq
* Corresponding Author: Reem Alaa Mohammed. Email:
(This article belongs to the Special Issue: Recent advancements in thermal fluid flow applications)
Fluid Dynamics & Materials Processing 2023, 19(10), 2449-2469. https://doi.org/10.32604/fdmp.2023.027750
Received 13 November 2022; Accepted 18 January 2023; Issue published 25 June 2023
Abstract
This study aims to evaluate the erosion behavior and the hardness of hybrid composites made of varying amounts of coconut shells, walnut shells, and carbon fibers dispersed in a polyester matrix. MINITAB (L16) Taguchi experiments were used to determine the optimal combination of parameters. In particular, an erosion device consisting of a motor with a constant flow rate of 45 L/min, a pump with a diameter of 40 mm, a nozzle with a diameter of 5 mm, and a tank made of “perspex glass” 55 cm long, 30 cm tall, and 25 cm wide was used. The tests were conducted by varying the sample-to-nozzle distance, the pattern angle, and the sand particle size. The results have revealed that the presence of 7.5% by weight of waste coconut shell, for conditions corresponding to 90° angle, sand size 425 μm, stand distance 30 cm, gives the best wear resistance (3.04 × 10−5 g/g). The filler content and sand particle size affect the erosive rate, with the angle playing a secondary role. The distance between the sample and the nozzle has a weaker effect on erosive wear. The hardness results show that the models (UP-5% carbon fiber-2.5-3.5-4.5-5.5-6.5-7.5 wt.% waste coconut shell) give the best values for prayer compared to the samples (UP-5 wt.% carbon fiber-2.5-3.5-4.5-5.5-6.5-7.5 wt.% waste walnut shell).Graphic Abstract
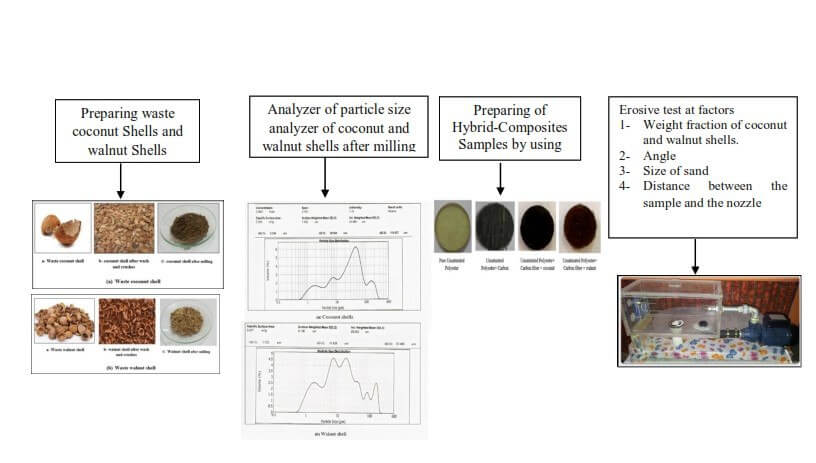
Keywords
Environmental awareness today drives researchers worldwide to develop environmentally friendly solutions for all aspects of life. The availability of waste and natural fibers and ease of manufacturing have tempted researchers to try out locally available inexpensive threads and study their feasibility for reinforcement purposes and to what extent they satisfy the required characteristics of a well-reinforced polymer composite for various applications [1,2]. Due to its low cost and high specific mechanical properties, natural fiber has already displayed its potential to be a promising renewable and biodegradable replacement for the most common synthetic reinforcement, i.e., jute, coconut shell, eggshell, and walnut shell [3]. Fibers and natural waste have received significant attention as reinforcing materials with polymers. The most commonly used thermoset polymers include epoxy resin, unsaturated polyester resins, and vinyl ester. Various polymers, such as thermosetting solids and thermoplastic matrices, can be used when preparing the composites [4]. When subjected to heat, a thermoset is a complex, interconnected substance that loses its mechanical and chemical characteristics and becomes immutable. With a carbon-to-carbon bond in its polymer chain and good mechanical and physical properties, unsaturated polyester resin is a thermosetting polymer created by reacting with an unsaturated monomer or pre-polymer [5]. As a result, it is appropriate for applications requiring high resistance, corrosion resistance, moisture resistance, thermal insulation, and good electrical properties [6]. One of the most widespread issues faced by businesses is wear caused by solid particle erosion. Studies of erosion often focus on the progressive loss of material that occurs during the eroding process. This occurs whenever solid particles are carried by air and then impinge on the surface of the sample at a variety of angles [7]. The erosive particles impact the surface during relative velocity at the component. Standardized techniques are mimicked using an erosion test rig [8]. Many papers have looked at erosion and other properties and tried to figure out what factors affect the highest levels of erosion resistance. Arun et al. [9] illustrated the mechanical and erosive performance of 40 wt.% glass-epoxy hybrid composites under four factors (0-5-10-15 wt.% rice husk); (45, 60, 75, 90 angles); (40, 60, 80, 100 erodent size); and (30, 40, 50, 60 velocities of impact). The samples (Epoxy-40 wt.% glass, 15 wt.% rice husk) performed better than expected in terms of density, hardness, impact, and erosive rate. The tensile and flexural strength decline with adding rice husk into epoxy-40 wt.% glass. Ashish et al. [10] examination of some properties of two groups of hybrid composites: the first: (Ep.-0-5-15-20-25-30 wt.% short of glass fiber) and the second: (Ep.-0-5-15-20-25-30 wt.% short of banana fiber). Used Taguchi’s test design approach to select a parametric analysis of the variable impact velocity, filler content, erodent temperature, impingement angle, stand-off distance, and erodent size. The samples (Ep.-30 wt.% short of glass fiber and 30 wt.% short of banana fiber) have the best properties. Hemalata et al. [11] examined the erosive tests for two groups of samples (Ep.-1.8-2.8-3.3-4.3 wt.% bamboo fiber) and (Ep.-3.3-1.5-3-4.5-6 wt.% cenosphere) under the impact of factors (30, 45, 60, 90 degrees, 33, 48, 70 m/s velocities, 10 mm nozzle to sample distance). The results indicate that composites filled with the cenosphere enhance the erosion wear resistance of the bamboo-epoxy composite. Chellaganesh et al. [12] hybrid composite material both with and without filler (Ep.-60 wt.% hemp fiber-40 wt.% kevlar) and (Ep.-60 wt.% hemp fiber-40 wt.% kevlar-5 wt.% palm and coconut shell) is used for the study of erosive under the influence of variables (45, 90 angles, 2.5 m/s rate flow, 5, 10, 15 times). The samples (Ep.-60 wt.% hemp fiber-40 wt.% kevlar-5 wt.% coconut and palm husk) demonstrated dramatically enhanced erosion behavior. This study aims to verify the erosive behavior and hardness of two groups of samples of hybrid composites. This work differs from the rest of the work of other researchers in the comparison between the composites filled with two types of waste (coconut and walnut shell) reinforced by carbon fiber and polyester, and the study of the erosive wear behavior of these composites under the influence of 4 factors and determining the hardness values for them as well.
The unsaturated polyester resin as a matrix used in this work has (tensile strength of 55–65 MPa, a flexural strength of 182–192 MPa, a density of 1.10–1.11 gm/cm3, elongation at break 1.9–2.3%) equipped by the Company, United Arab Emirates Dubai. Carbon fiber was used as a reinforcement material with properties (tensile strength 2.6 GPa, tensile modulus 240 GPa, density of 1.81 gm/cm3, elongation at break 0.8%) and supplied by the Company, Tenax, USA. In the present work, waste coconut and walnut shells were collected to be recycled and used as fillers with polymer. Initially, waste coconut shells and walnut were washed with distilled water to remove dirt and suspended matter and then dried at room temperature. Grind the coconut husks and walnut husks for 4 h, Figs. 1a and 1b show the steps to obtain shells of coconut and walnut particles, Figs. 2a and 2b show the average particle size of coconut shell particles, where the average particle size of the coconut shell was (43.469 μm), and the average particle size of the walnut shell was (29.053 μm).
Figure 1: (a–b) Steps for preparing coconut and walnut shell
Figure 2: (a and b) Analyzer of particle size analyzer of coconut and walnut shells after milling
2.2 Preparing of Hybrid-Composites Samples
Used The hand lay-up approach to prepare hybrid composite matrix materials samples. First, a layer of nylon must be placed over the glass preparation mold with the dimensions (50 cm3 × 50 cm3 × 0.5 cm3) until adhesion between the specimens and the mold to avoid. Hybrid composites fabricated consisting of 5 wt.% carbon fibers, polyester, waste coconut shells, and waste walnut shells by varying the filler content (2.5-3.5-4.5-5.5-6.5-7.5 wt.%). Use a glass rod to mix the unsaturated polyester resin with the fillers to reach a uniform consistency, gradually add the hardener (FARAPOL O 115) to the mixture and continue mixing for 15 min. Pour part of the mixture into the mold and put carbon fibers (5% weight ratio); the remaining mixture was poured into the mold and set for 24 h at room temperature. To eliminate residual tensions and achieve better bonding, the samples are placed in an oven at 55°C for 1 h [13]. Fig. 3 shows some of the samples that were executed in this paper. The samples were cut using a machine (CNC) according to a test for each ASTM (erosive and hardness shore).
Figure 3: Samples of the composites (UP-5 wt.% carbon fiber-coconut and walnut shells)
To estimate the erosion rate of all manufactured samples using a (jet) type erosion device according to ASTM G76 [14]. According to Fig. 4, prepared the erosion device locally, consists of a motor with a constant flow rate of 45 L/min, a pump with a diameter of 40 mm, a nozzle with a diameter of 5 mm, and a tank made of “perspex glass” 55 cm long, 30 cm tall, and 25 cm wide. According to ASTM G76, the test samples had the following measurements: 40 mm width and 5 mm thickness. The dimensions of the test samples are 40 mm in width and 5 mm in thickness, as specified by ASTM G76. An electronic scale was used with an accuracy of (0.0001) digits to measure the weight of the samples before and after the erosion experiments. As shown in Eq. (1), the wear behavior rate can be determined [15].
where:
E.R: Erosive wear rate (g)
Figure 4: Erosive test device used in this wor
The hardness of the composites was measured using a shore D hardness tester according to AS2240 [16]. This test takes five measurements for each sample and then calculates the average hardness of the models, which dimensions were (40 mm wide and 5 mm thick).
2.3.3 Taguchi Experimental Design
Implemented Taguchi’s experimental design to achieve the best possible results in terms of efficiency, quality, and cost [17]. It is necessary to reduce the number of parameters affecting optimization before using this strategy to ignore non-essential parameters. According to published research, the erosion behavior of composite samples is determined primarily by the impingement angle, particle size, the distance between the model and the nozzle, and filler content [18]. This study uses the L16 orthogonal array design to explore the effects of these four factors, as shown in Table 1. Convert experimental data into signal-to-noise (SN) ratios. In the tests, there are different S/N (Convert experimental data into signal-to-noise) ratios selecting “smaller is better” properties in this work to have the least amount of wear, as shown in Eq. (2) [19].
where:
N = Number of observations
Y = Erosive rate
Tables 2 and 3 display the findings of erosion tests performed on polyester-carbon fiber/different weight content of coconut and walnut shells by the planned design. The last column indicates the signal-to-noise ratio of each test run in the Tables. The erosion rate’s S/N ratio has an overall mean of (−9.6575 db) for samples (UP-5 wt.% carbon fiber-7.5 wt.% coconut shell) in Table 2. The erosion rate’s S/N ratio has an overall mean of (−13.6969 db) for samples (UP-5 wt.% carbon fiber-7.5 wt.% walnut shell) in Table 3. The high ratio of (S/N) values gives the best resistance to erosion rate. Because the presence of fibers, coconut husks, and walnuts has provided a better bonding interface to the erosion resistance behavior when compared with the composites without the reinforcement with fillings [20]. The effect of control parameters for the erosive rate of samples of unsaturated polyester-carbon fiber-weight coconut shell and walnut shell samples are shown in Figs. 5 and 6. The possible interactions between the control factors must be considered before any attempt is made to use this straightforward model as a predictor for the performance measure. Therefore, the factorial design includes a specific testing method for the presence of the interaction effects. The analysis of the results shows from Figs. 5a and 5b the conclusion that the combination of factors A4 (3.5 wt.%, 7.5 wt.% coconut shell), B4 (90°, 30°), C1 (425 μm), and D3 (30, and 25 cm) gives the minimum of the erosive rate. The analysis of the results shows from Figs. 6a and 6b the conclusion that the combination of factors A4 (3.5 and 7.5 wt.% walnut shell), B4 (90°), C1 (425 μm), and D3 (30 cm) gives the minimum of the erosive rate.
Figure 5: (a–b) Control variables S/N for the coconut shell-filled samples
Figure 6: (a–b) Control variables S/N for the walnut shells-filled samples
The results of the experiments in Figs. 7a and 7b show the effect of the added weight fractions of coconut and walnut shells of unsaturated polyester resin-carbon fiber on the wear behavior. The erosion rate of unreinforced polyester samples was (111.45 × 10−5 g/g) and improved by (45%) when adding the carbon fibers because the fibers’ presence improved the bonding between the resin and the fibers. The experiments showed that weight loss in the erosive test decreases with increased fraction weight of both the coconut and the walnut shells. The erosive resistance of samples filled (2.5-3.5-4.5-5.5-6.5-7.5 wt.% coconut shell) (3.04 × 10−5 g/g) was better compared to samples filled (2.5-3.5-4.5-5.5-6.5-7.5 wt.% walnut shell) (4.62 × 10−5 g/g) at the same variables (90° angle, 425 μm size sand particle, 30 cm stand-off distance). Because the hardness of the material and chemical composition nature of coconut shells was better than the hardness and chemical composition nature of walnut shells, and thus it gave a better relationship with the carbon-fiber resin matrix and improved the erosive resistance. Also, this confirms the bonding quality of the composite material with filler to enhance the mechanical and erosive properties of the material [21].
Figure 7: (a–b) Effect weight fraction on erosive behavior of polyester-carbon fiber-coconut and walnut shells
The collision angle impact on the erosive wear behavior was studied by conducting experiments under specific operating conditions, as shown in Figs. 8a and 8b. The erosion wear behavior for polymer composites is classified as ductile or brittle; however, this classification is not definite because erosion properties are affected by experimental conditions and target material composition [22]. Commonly recognized that impingement angle is one of the most critical elements in the erosion process, with ductile materials experiencing peak erosion at a (15°–20°) grade and brittle materials seeing peak erosion at standard impact, i.e., at a (90°) impingement angle [23]. The results in Fig. 8 showed that the erosive wear peak was at an impact angle of 45 for the composites filled with carbon and unsaturated polyester resin filled with coconut and walnut husks. In this work, the effect of the solid particles was not purely ductile nor strictly brittle.
Figure 8: (a–b) Effect of impact angle on erosive behavior of polyester-carbon fiber-coconut shells, walnut shells
Figs. 9a and 9b illustrate the correlation between the sand particle size and the erosive rates. The erosive rate of the composites-polymeric reinforced with coconut, walnut shells, and carbon fibers at different sand sizes 425, 525, 625, and 725 μm was studied. The increase in the sand particle size gradually leads to material loss increase, regardless of the filler content. Still, the loss weight of the composites reinforced with (coconut shells) was less than the composites reinforced with (walnut shells). Smaller particles of sand suffer from particle retardation before impact resulting in lower erosion efficiency of the particles. This will also lead to lower kinetic energy dissipation at the mark and automatically decrease the erosion rate [24]. The highest erosive rate was (3.60 × 10−5, 6.50 × 10−5) at the sand grain size (725 μm), and the best wear resistance was (3.04 × 10−5, 4.62 × 10−5) at the sand grain size (425 μm) for the composites filled with (coconut shells and walnut shell), respectively.
Figure 9: (a–b) Effect of size sand particles on erosive behavior of polyester-carbon fiber coconut, walnut shells
The distance between the sample and the nozzle significantly affects the composite’s erosive behavior. The relationship distance between a sample and the nozzle on the erosion behavior of all models display in Figs. 10a and 10b. It is clear from the figure rate of erosive composites increases with the reduction of distance between the sample and the nozzle. This work shows the highest erosive rate at a distance (20 and 25 cm) and the lowest erosive rate at a distance (30 and 35 cm). Because the lower the distance, the greater the water movement within the system, thus increasing the erosion process and losing weight, these results are consistent with [25].
Figure 10: (a–b) Effect of sand off-distance on erosive behavior of polyester-carbon fiber-coconut, walnut shells
Tables 4 and 5 show the value of ANOVA, statistical analysis, the degree of freedom (DF), the adjusted sum of squares (AdjSS), the adjusted sum of mean squares (AdjMS), Fisher’s value (F), and the probability value (p) for erosion value. The ANOVA analysis for samples (UP-UP-5% carbon fiber, UP-5 wt.% carbon fiber, 2.5-3.5-4.5-5.5-6.5-7.5 wt.% coconut shell) showed the (p-value of filler content A) (0.001), (the p value of angle B) (0.04), (p value of sand grain size C) (0.002), and (p value of Off Distance D) (0.035), all value less than (0.05) and this means that these factors have a more significant influence on the rate of erosive behavior. The ANOVA analysis for samples (UP-UP-5 wt.% carbon fiber, UP-5 wt.% carbon fiber, 2.5-3.5-4.5-5.5-6.5-7.5 wt.% walnut shells) showed the (p-value of filler content A) (0.002), (p-value of size sand particles C) (0.001), and (p-value of standoff distance D) (0.04) all value less than (0.05) and this means that these factors have a more significant influence on the rate of erosive behavior. In contrast, the (p value of the angle B) (0.05) has less effect on the erosion behavior rate. Among all the significant variables, filler content (A) and size of sand particles (C) contributed significantly compared to other factors towards increasing the erosive-resistant property of the composites.
Shore hardness (D) was measured for all composite material samples after an average of five readings was taken to obtain higher accuracy results, as shown in Tables 6 and 7. Figs. 11a–11b show the values of hardness shore (D) for the prepared specimens (unsaturated polyester resin, unsaturated polyester +5 wt.% carbon fiber, 2.5-3.5-4.5-5.5-6.5-7.5 wt.% walnut, and coconut shell). It is evident from the Figures that there is an apparent effect in the hardness values after adding 5 wt.% carbon fibers. The increase in hardness values is because it is a property of the surface, and the addition of fibers to the polymeric substrate increases flexibility and reduces the resistance of the matrix surface to the indentation [26]. The stiffness improves by adding different weight fractions (walnut and coconut shell) to the polyester resin and carbon fibers. The hardness values of the samples (unsaturated polyester resin, unsaturated polyester +5 wt.% carbon fiber, 2.5-3.5-4.5-5.5-6.5-7.5 wt.% coconut shell ash) were better when compared with the samples (unsaturated polyester resin, unsaturated polyester +5 wt.% carbon fiber, 2.5-3.5-4.5-5.5-6.5-7.5 wt.% walnut shell ash), the reason is that coconut shell contains more solid ash than walnut shell ash, adding to improved stacking and cross-linking that reduces movement polymer particles and makes them more resistant to scratch penetration [27]. The results of the ANOVA test for the unsaturated polyester resin, carbon fiber, and coconut and walnut husk waste samples are shown in Tables 8 and 9. It is clear from the ANOVA analysis that the hardness results have improved positively due to the value of (Sig. less than 0.05) meaning that the added reinforcement materials gave positive properties.
Figure 11: (a–b) Hardness shore D of polyester-carbon fiber-coconut, walnut shells
The conclusion from the research is that the presence of coconut and walnut shells in an unsaturated polyester resin filled (5 wt.% carbon fiber) significantly reduced the erosive loss and obtained the best erosion rate at (7.5 wt.% of coconut and walnut shells). The samples (UP+5 wt.% carbon fiber +7.5 wt.% coconut shells) and (UP+5 wt.% carbon fiber +7.5 wt.% walnut shells) give erosive rate resistance (3.04 × 10−5 g/g) and (4.62 × 10−5 g/g) respectively at factors (90° angle, sand size 425 μm, stand distance 30 cm). In contrast, the sample (UP) gives a higher erosive rate (111.45 × 10−5 g/g) at a 90° angle, size of sand 725 μm, sand off-distance 35 cm). The filler content and size of the sand particles were the major significant factors influencing the erosive rate, followed by angle. In contrast, the distance between the sample and the nozzle had less effect on the erosive wear. The S/N ratio found that the variables (A4, B1, C1, D2) and (A4, B4, C1, D3) gave the best erosion rate for the reinforced composites. The hardness results showed that the samples (UP-5 wt.% carbon fiber-2.5-3.5-4.5-5.5-6.5-7.5 wt.% waste coconut shell) gave the best values for prayer compared to the samples (UP-5 carbon fiber-2.5-3.5-4.5-5.5-6.5-7.5 wt.%) waste walnut shell. It is possible that future work will include adding other waste, for example (egg shells, banana peels, pomegranate peels, sunflower seed peels, etc.) to epoxy resin, vinyl ester, glass fibers, and Kevlar fiber.
Funding Statement: The authors received no specific funding for this study.
Conflicts of Interest: The authors declare that they have no conflicts of interest to report regarding the present study.
References
1. Anu, G., Ajit, K., Amar, P., Sandhyarani, B. (2012). Effect of filler content and alkalization on mechanical and erosion wear behavior of CBPD filled bamboo fiber composites. Journal of Surface Engineered Materials and Advanced Technology, 2, 149–157. https://doi.org/10.4236/jsemat.2012.23024 [Google Scholar] [CrossRef]
2. Vera-Cardenas, E. E., Mendoza-Mendoza, J. C., Martinez-Perez, A. I., Ledesma-Ledesma, S., Rubio-González, C. et al. (2021). Solid particle erosive wear study of polymer composite materials for wind turbine applications. Polymer Composites, 42(4). https://doi.org/10.1002/pc.25950 [Google Scholar] [CrossRef]
3. Sandhyarani, B., Alok, S. (2009). Tribo-performance analysis of red mud-filled glass-epoxy composites using taguchi experimental design. Materials and Design, 30, 2841–2853. https://doi.org/10.1016/j.matdes.2009.01.018 [Google Scholar] [CrossRef]
4. Harper, C., Petrie, E. (2003). Plastics materials and processes: A concise encyclopedia. John Wiley & Sons, Inc. [Google Scholar]
5. Marwah, S., Reem, A. (2019). Flexural, compressive and thermal characterization of hybrid composite materials. AIP Publishing Conference Proceedings, 2123, 020084-1–020084-12. https://doi.org/10.1063/1.5117011 [Google Scholar] [CrossRef]
6. Jeetendra, M., Sanjeev, D., Brijesh, G., Lalit, R., Shubham, S. (2021). Comparative analysis of erosive wear behaviour of epoxy, polyester and vinyl esters based thermosetting polymer composites for human prosthetic applications using taguchi design. Polymers, 3607(13), 1–21. https://doi.org/10.3390/polym13203607 [Google Scholar] [PubMed] [CrossRef]
7. Adam, K., Manikandan, E. (2019). Solid particle erosion studies on fiber composite with eggshell as filler materials. International Journal of Surface Science and Engineering, 13(1), 1–13. https://doi.org/10.1504/IJSURFSE.2019.097910 [Google Scholar] [CrossRef]
8. Hemalata, J. (2018). Study of solid particle erosion wear behavior of bamboo fiber reinforced polymer composite with cenosphere fille. Advances in Polymer Technology, 37(3), 1–9. https://doi.org/10.1002/adv.21718 [Google Scholar] [CrossRef]
9. Arun, K., Alok, S. (2012). Study on mechanical and tribo-performance of rice-husk filled glass–epoxy hybrid composites. Materials and Design, 41, 131–141. https://doi.org/10.1016/j.matdes.2012.05.002 [Google Scholar] [CrossRef]
10. Ashish, K., Rupesh, K., Abhishek, C. (2014). Mechanical and tribological characterization of short fibers reinforced polymer composites. IOSR Journal of Mechanical and Civil Engineering, 11(3), 32–43. https://doi.org/10.9790/1684 [Google Scholar] [CrossRef]
11. Hemalata, J., Arun, K., Mihir, K. (2016). Study of solid particle erosion wear behavior of bamboo fiber reinforced polymer composite with cenosphere filler. Advances in Polymer Technology, 1(1). https://doi.org/10.1002/adv.21718 [Google Scholar] [CrossRef]
12. Chellaganesh, D., Adam, K., Mohamed, A., Ragul, S., Nachiappan, J. et al. (2018). Hybrid composite material and solid particle erosion studies. IOP Conference Series: Materials Science and Engineering, 346 (012014). https://doi.org/10.1088/1757-899X/346/1/012014 [Google Scholar] [CrossRef]
13. Oleiwi, J., Mohammed, R. A. (2021). Comparison of the wear behavior and hardness of vinylester resin reinforced by glass fiber and nano ZrO2 and Fe3O4. Revue des Composites et des Matériaux Avancés-Journal of Composite and Advanced Materials, 31(6), 325–333. https://doi.org/10.18280/rcma.310603 [Google Scholar] [CrossRef]
14. Annual Book of ASTM (2013). Standard standard test methods for conducting erosion tests by solid particle impingement using gas jets G76-13. https://doi.org/10.1520/G0076-13 [Google Scholar] [CrossRef]
15. Mishra, P., Acharya, S. (2010). Solid particle erosion of bagasse fiber reinforced epoxy composite. International Journal of Physical Sciences, 5, 1–7. [Google Scholar]
16. Annual Book of ASTM Standard (1988). Standard test method for plastics properties-durometer hardness D 2240, 09.01. [Google Scholar]
17. Reem, A. (2019). Tensile strength, impact strength and experimental analysis wear behavior of modified zinc nitrate filled polymer. Materials Research Express, 6, 1–10. https://doi.org/10.1088/2053-1591/ab5492 [Google Scholar] [CrossRef]
18. Jnanaranjan, K., Arun, K., Alekha, K. (2018). Physical, mechanical, and erosion characterization of palm leaf stalk fiber reinforced epoxy composites filled with palm leaf stem stalk (PLSS) powder. BioResources, 13(4), 7212–7231. [Google Scholar]
19. Patnaik, A. (2008). Taguchi approach for investigation of erosion of glass fiber–polyester composites. Journal of Reinforced Plastics and Composites, 27(8), 1–18. https://doi.org/10.1177/0731684407085728 [Google Scholar] [CrossRef]
20. More, S., Bhatta, D., Menghani, J. (2017). Study of the parametric performance of solid particle erosion wear under the slurry Pot test Rig. Tribology in Industry, 39(4), 471–481. https://doi.org/10.24874/ti.2017.39.04.06 [Google Scholar] [CrossRef]
21. Harsha, A., Tewari, U., Venkatraman, B. (2003). Solid particle erosion behaviour of various polyaryletherketone composites. Wear, 254, 693–712. https://doi.org/10.1016/S0043-1648(03)00143-1 [Google Scholar] [CrossRef]
22. Niharika, M., Samir, K. (2015). Mechanical and tribological performance of luffa cylindrica fibre-reinforced epoxy composite. BioResources, 10(4), 8364–8377. [Google Scholar]
23. Mohanta, N., Acharya, S. (2013). Tensile, flexural and interlaminar shear properties of luffa cylindrica fibre reinforced epoxy composites. International Journal of Macromolecular Science, 3, 6–10. [Google Scholar]
24. Tej, S., Sachin, T., Amar, P., Vedant, S., Ibolya, Z. et al. (2019). Fabrication of waste bagasse fiber-reinforced epoxy composites: Study of physical, mechanical, and erosion properties. Polymer Composites, 40(9), 3777–3786. https://doi.org/10.1002/pc.25239 [Google Scholar] [CrossRef]
25. Mohammed, R. A. (2018). Study of some mechanical properties and erosive behavior by taguchi method for hybrid nano composites. Engineering and Technology Journal, 36(4), 471–479. https://doi.org/10.30684/etj.36.4A.15 [Google Scholar] [CrossRef]
26. Reem, A., Ruaa, H., Marwah, S. (2021). Investigation the effect of nano silica dioxide additives on the properties of epoxy resin for using in industrial applications. Materials Science Forum, 1050, 103–113. [Google Scholar]
27. Mudradi, S., Ravikantha, P., Kandavalli, R., Thirumaleshwara, B. (2014). Effect of filler content on the performance of epoxy/PTW composites. Advances in Materials Science and Engineering, 2014, 11. https://doi.org/10.1155/2014/970468 [Google Scholar] [CrossRef]
Cite This Article
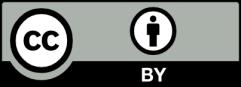
This work is licensed under a Creative Commons Attribution 4.0 International License , which permits unrestricted use, distribution, and reproduction in any medium, provided the original work is properly cited.