Open Access
ARTICLE
Numerical Simulation of Turbulent Swirling Pipe Flow with an Internal Conical Bluff Body
1 Khalifa University of Science and Technology, Abu Dhabi, United Arab Emirates
2 National Polytechnic School of Constantine, Constantine, Algeria
* Corresponding Author: Nabil Kharoua. Email:
Fluid Dynamics & Materials Processing 2021, 17(2), 455-470. https://doi.org/10.32604/fdmp.2021.014370
Received 22 September 2020; Accepted 11 February 2021; Issue published 02 April 2021
Abstract
Turbulent swirling flow inside a short pipe interacting with a conical bluff body was simulated using the commercial CFD code Fluent. The geometry used is a simplified version of a novel liquid/gas separator used in multiphase flow metering. Three turbulence models, belonging to the Reynolds averaged Navier-Stokes (RANS) equations framework, are used. These are, RNG k-ε, SST k-ω and the full Reynolds stress model (RSM) in their steady and unsteady versions. Steady and unsteady RSM simulations show similar behavior. Compared to other turbulence models, they yield the best predictions of the mean velocity profiles though they exhibit some discrepancies in the core region. The influence of the Reynolds number on velocity profiles, swirl decay, and wall pressure on the bluff body are also presented. For Reynolds numbers generating a Rankine-like velocity profile, the width and magnitude of flow reversal zone decreases along the pipe axis disappearing downstream for lower Reynolds numbers. The tangential velocity peaks increase with increasing Reynolds number. The swirl decay rate follows an exponential form in accordance with the existing literature. These flow features would affect the performance of the real separator and, thus, the multiphase flow meter, noticeably.Keywords
Cite This Article
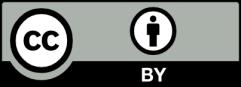
This work is licensed under a Creative Commons Attribution 4.0 International License , which permits unrestricted use, distribution, and reproduction in any medium, provided the original work is properly cited.