Open Access
ARTICLE
CFD-Based Optimization of Hot Primary-Air Pipe Networks in Power Plant Milling Systems
1 Jiangxi Vocational and Technical College of Electricity, Nanchang, 330032, China
2 North China Electric Power University, Baoding, 071003, China
3 Power China Jiangxi Electric Power Engineering Co., Ltd., Nanchang, 330096, China
* Corresponding Author: Xuemin Ye. Email:
(This article belongs to the Special Issue: High-Speed and High-Temperature Flows)
Fluid Dynamics & Materials Processing 2020, 16(3), 623-636. https://doi.org/10.32604/fdmp.2020.09669
Received 14 January 2020; Accepted 08 April 2020; Issue published 25 May 2020
Abstract
A hot primary-air pipe system is the bridge connecting an air-preheater with a coal mill in power generation stations. The effective geometrical configuration of the pipe network greatly affects the air flow distribution and consequently influences the safe and economic operation of milling systems in power stations. In order to improve the properties of the air flow, in the present work the SIMPLEC method is used to simulate numerically the flow field for the original layout of the system. As a result, the internal mechanisms influencing the uneven pressure drop in each branch are explored and three optimization schemes are proposed accordingly. The numerical results indicate that, for the original layout, the local pressure drop of the tee section accounts for approximately 74% of the total drop of the system, with other pressure drops depending on the specific branch considered. It is shown that after optimization, a roughly balanced flow resistance and flow rate can be obtained. Compared with the original layout, the pressure drop relating to different branches is significantly reduced.Keywords
Cite This Article
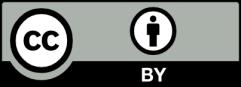
This work is licensed under a Creative Commons Attribution 4.0 International License , which permits unrestricted use, distribution, and reproduction in any medium, provided the original work is properly cited.