Open Access
ARTICLE
Numerical Simulation of Gas-Solid Flow Processes in an Ash Conveying Pipeline with Multiple Feeds
1 College of Transportation, Ludong University, Yantai, 264025, China
2 School of Energy and Power Engineering, Northeast Electric Power University, Jilin, 132012, China
* Corresponding Author: He Wang. Email:
Fluid Dynamics & Materials Processing 2024, 20(12), 2721-2739. https://doi.org/10.32604/fdmp.2024.055174
Received 19 June 2024; Accepted 13 September 2024; Issue published 23 December 2024
Abstract
Pneumatic conveying technology, as an efficient material transportation method, has been widely used in various industrial fields. To study the powder transportation in horizontal ash conveying pipes, this study relies on the Computational Particle Fluid Dynamics (CPFD) numerical method. The characteristics of the gas-solid two-phase flow under continuous air supply conditions are analyzed, and the effects on particle movement of factors such as feed port spacing, inlet air velocity, and the number of discharge ports are explored accordingly. The research results show that when the inlet velocity is 5 m/s, adjacent discharged particles come into contact after 8 s. As the inlet air velocity increases, the contact time between adjacent discharge ports is shortened. When the feed port spacing increases from 0.5 to 2 m, the dust accumulation thickness decreases by about 0.6 times. Additionally, when the spacing reaches a certain value, the rate of decrease in dust accumulation thickness begins to diminish.Keywords
Cite This Article
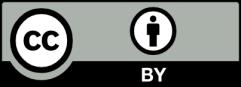
This work is licensed under a Creative Commons Attribution 4.0 International License , which permits unrestricted use, distribution, and reproduction in any medium, provided the original work is properly cited.